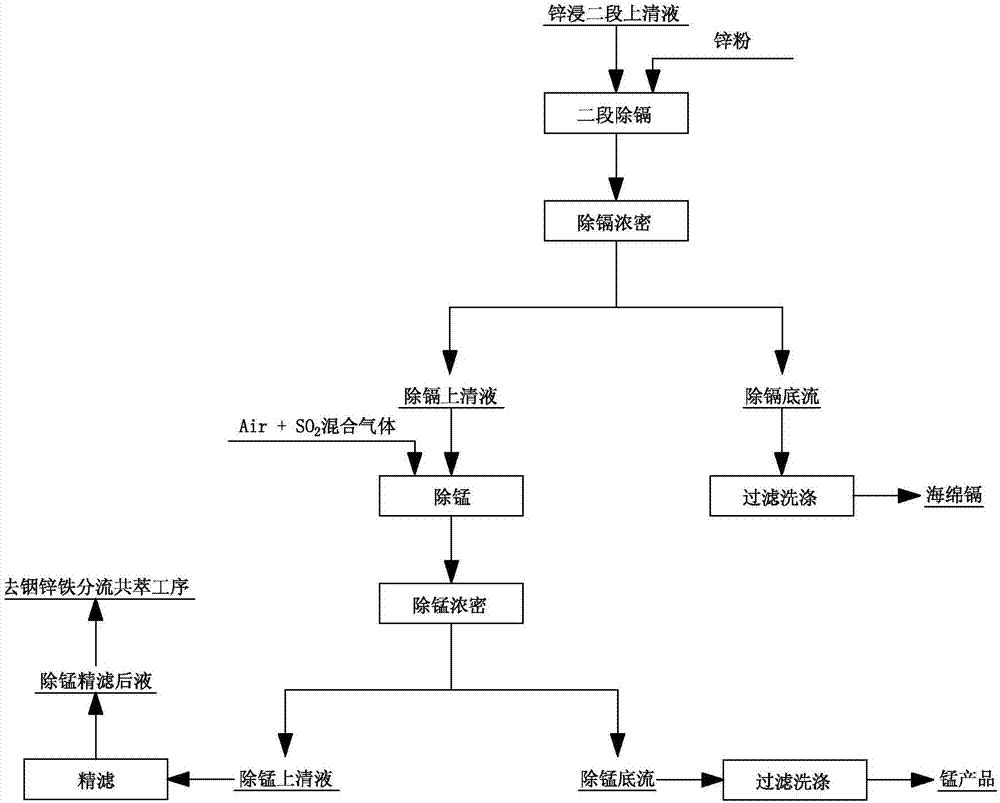
本发明涉及有色金属固体废渣处理领域,具体地说是一种用分流共萃工艺从有色金属固体废渣中回收铟锌铁等有价金属的方法。
背景技术:有色金属固体废渣中的有价金属成份较为复杂,根据其成份的不同,采用的回收方法也不尽相同,但目前国内外对有色固体废渣中铟锌铁的回收方法比较单一,主要有以下两种:(1)酸浸除杂法:该方法采用硫酸作为浸出剂,在高酸下将铟、锌、铁金属浸出,再用铁粉作为还原剂,将溶液中的三价铁离子全部还原成二价铁离子,通过P204萃取后,将铟从溶液中提出,含铟液用锌粉置换变涨成海绵铟,经熔炼后变为粗铟销售;而P204萃取后液则用氧化锌中和,将锌的浓度提高到120~150g/L,采用黄钠铁矾法除铁,再分别除去铜、镉、镍、钴等杂质,如果溶液中含氟离子、氯离子浓度过高还得再将它们分别除去,得到的纯净硫酸锌溶液可以用蒸发结晶的方法生产七水硫酸锌产品或者直接电解生产锌金属。这种方法,一是能耗高、产生的工业废渣种类较多,如:铁渣、铜镉渣、镍钴渣等;二是工业废水排放量大,如:除氟、氯产生的废水;三是收率较低,在铁粉作为还原剂的工序,会损失大量的铟金属到渣中;四是环保问题严重,不适合中国未来环保发展的清洁冶金方向。(2)综合法回收铟镓锗:以富含铟、镓、锗的锌浸出渣为原料,经过浸出、用丹宁沉淀锗和用溶剂萃取提取铟、镓、锗的过程,主要包括预处理、提取铟和提取镓等作业,该法于1975年在中国研究成功。预处理湿法炼锌厂产出的锌浸出渣中,有部分锌和铁形成铁酸锌(nZnO·mFe2O3),而95%左右的铟、锗、镓以类质同象存在于铁酸锌中。用锌电解贫液浸出含铟、锗、镓的锌浸出渣时,铟、锗、镓转入浸出液。过滤所得的滤液加锌粉置换,铟、锗、镓被置换成金属,获得富含铟、锗、镓置换渣。置换渣用硫酸逆流浸出,控制浸出液最终酸度(含游离酸0.6mol/L左右),便可使置换渣中96~100%的铟、锗、镓转入溶液。用盐酸反萃取铟负载有机相,得含铟67~84g/L的反萃液,反萃液加锌粉置换得海绵铟,海绵铟经压团和碱熔铸后送电解,得纯度99.99%的铟,铟的回收率超过90%。而锌粉置换的后液,则用钠碱变为碳酸锌或氢氧化锌的沉淀,沉淀后溶液则排放进入污水处理系统。这个方法对水的污染较为严重,随着日益严厉的环保法的实施,已经不再适合对铟镓锗等金属的综合回收。上述的两种方法,在对有价金属回收的同时,会产生二次污染的渣和工业废水,需要对这些污染物进一步再处理。
技术实现要素:本发明所要解决的技术问题是克服上述现有技术存在的缺陷,提供一种用分流共萃工艺从有色固体废渣中回收铟锌铁等有价金属的方法,其利用金属离子在溶剂萃取中的特征,不断地将浸出金属离子所消耗的酸进行再生;通过控制溶液酸度,对含有不同金属离子的溶液进行分流,形成一个溶液的闭路循环。为此,本发明采用如下的技术方案:用分流共萃工艺从有色固体废渣中回收有价金属的方法,包括依次进行的一段加压浸出和两段常压逆流浸出工序、镉锰净化工序、铟锌铁分流共萃工序、盐酸再生工序及无锰锌电积工序,其特征在于:1)所述的二段常压逆流浸出工序包括锌浸二段和锌浸一段,在锌浸二段中,来自于铟锌铁分流共萃工序的含酸共萃余液、有色固体废渣与空气+SO2的混合气体进行充分混合浸出,pH控制在3-3.5,T=45-55℃,除锌外,铁与其它金属均被抑制浸出,并将铁以FeOOH的形态存在于锌浸二段底流中,锌浸二段上清液进入镉锰净化工序,锌浸二段底流进入锌浸一段中与含酸的萃锌余液充分混合浸出;在锌浸一段中,pH控制在1~2.5,T=45-55℃,锌、铁及铟金属被浸出,锌浸一段底流中锌的浓度控制在15~50g/L,锌浸一段底流进入一段加压浸出工序;在一段加压浸出工序中,加压浸出的工艺控制条件为:有氧条件下,T=150-200℃,P=1.2~1.8Mpa,H2SO4的浓度为100~180g/L,锌浸一段底流与铟锌铁分流共萃工序的含酸共萃余液充分混合浸出;利用此条件选择性浸出In3+、Zn2+离子,除Cd2+、Mn2+离子外,其它杂质被抑制,得到的加压上清液及锌浸一段上清液去铟锌铁分流共萃工序;2)所述的镉锰净化工序中,锌浸二段上清液与锌粉进行两段置换反应,除镉底流经过滤洗涤后得到海绵镉,除镉上清液与空气+SO2的混合气体充分混合除锰,除锰上清液去铟锌铁分流共萃工序,除锰底流经过滤洗涤后得到锰产品;3)所述的铟锌铁分流共萃工序中,加压上清液、锌浸一段上清液及除锰底流分别进入铟铁共萃段、铟锌共萃段和锌萃取段,萃取后形成三种负载有机相和分别产生铟铁共萃余液、铟锌共萃余液和萃锌余液,铟铁共萃余液大部分返回一段加压浸出进行循环,小部分进入锌浸二段,铟锌共萃余液全部返回到锌浸二段,萃锌余液全部返回到锌浸一段;所述的三种负载有机相依次经过水洗段、酸洗段、反萃段、反铟段、反铁二段、反铁一段和洗氯段,负载有机相先经过水洗段洗去负载有机相中机械夹带的氯、氟离子,再经过酸洗段洗下萃上的铜、锰离子。本发明采用一段加压和两段常压逆流浸出和铟锌铁分流共萃新工艺,结合无钠湿法冶金体系,实现了系统内酸和工业废水的循环再生。独创的铟、锌、铁分段浸出与分段萃取技术相结合,使得萃取铟锌铁时产生的酸能够完全被循环利用,比传统工艺节约运行成本70%以上。独创的铟锌铁分流萃取技术,做到了分段浸出与分段萃取技术有机结合,优化与创新了铟锌铁分流共萃工艺。独创的一段加压和两段常压逆流技术实现了铟锌铁选择性的浸出,加压浸出提高了铟锌的浸出率,达到了95%以上。独特的萃取除铁与Air+SO2混合氧化除铁锰技术相结合,解决了传统工艺难以解决的除铁废渣问题。盐酸再生技术解决了萃取工序产生的FeCl3废酸液问题,同时,也将InCl3直接变成了高纯In2O3;盐酸再生技术也解决了反铟富液提取铟后残留的ZnCl2废酸液问题。采用了独特的无锰电积技术,锌电解槽内再无阳极泥沉淀,提高了电解工序的作业率和产品的质量。本发明通过各种独创的和独特的技术组合,集成了一个独创的从有色固废渣中提取铟锌铁等有价金属的湿法冶金体系,比起传统的技术,不但实现了零成本提取铟,无工业除铁废渣的产生,而且实现了真正意义上的工业废水零排放。在一段加压和两段常压逆流浸出工序中,Air+SO2混合氧化除铁锰技术将在常压的条件下,抑制有色固废渣中铁的浸出,并将铁以FeOOH的形态固定在常压浸出渣中;Air+SO2进入水溶液状态后,会立即形成一种FeSO5的物质,这种物质有极强的氧化性,可以将溶液中的Fe2+离子迅速氧化成Fe3+离子,化学反应方程式如下:FeSO5+Fe2++2H+=2Fe3++SO42-+H2O⑴而此时的三价铁离子又会与有色固废渣中含有钙、镁等碱性氧化物发生水解反应,在控制pH保持在3-3.5的状态下,化学反应方程式如下:Fe3++OH-+H2O=FeOOH+2H+⑵经过两段常压逆流浸出,锌的浸出率可以达到85%以上,铟的浸出率在~30%左右,而铁基本被抑制在常压浸出渣中。常压浸出渣中的各种有价金属将会在加压通氧的条件下被大量的浸出,在加压浸出的过程中,温度控制在150~200℃,压力控制在1.2~1.8Mpa,酸度控制在100~180g/L,通入氧气,此时,锌的总浸出率达到95%以上,铟的总浸出率达到92%以上,除已经形成针铁矿的以外,其它的铁则以赤铁矿(Fe2O3)的形式存在于渣中,但加压浸出液中还有不超过5g/L的Fe3+离子,化学反应方程式如下:采用Air+SO2混合氧化除铁锰技术,通过控制其中一段常压浸出的终点PH值在3.0~3.5,可以有效地抑制铟和铁的浸出,同时有色固废渣中含有少量的金属硫化物也可以被氧化浸出;采用高压高酸氧浸可以选择性的强化In3+、Zn2+等离子的浸出,抑制Sn2+、As2+等离子的浸出,使90%的Fe3+离子以Fe2O3形态沉淀(其它5%的Fe3+离子以FeOOH形态沉淀);而通过控制另一段常压浸出的终点PH值1-2.5,则可以让In3+、Zn2+等离子共同浸出。砷则以砷酸根的形式存在,砷酸根极易与其它金属离子形成砷酸盐沉淀,化学方程式如下:2As2-+5O2=2AsO53+⑷3Men++nAsO53+=Me3(AsO5)n⑸在镉锰净化工序中,由于Cd2+、Mn2+离子经过一段加压两段常压逆流浸出后,浸出率高达95%以上,如不及时除去,则会在溶液中循环富集,最后影响到分流共萃工序的正常运行。采用锌粉除镉的方法,也是对溶液中其它离子尽一步净化的过程,其化学反应方程式如下:CdSO4+Zn=Cd+ZnSO4⑹MeSO4+Zn=Me+ZnSO4⑺采用Air+SO2混合氧化除铁锰技术在此工序将Mn2+离子以MnO2或者Mn2O3的形式除去,以消除其在整个系统内的富集,其化学反应方程式如下:当pH<4时,Mn2++SO2+O2+2H2O=MnO2+4H++SO42-⑻当pH=5~7时,2Mn2++SO2+O2+3H2O=Mn2O3+6H++SO42-⑼。在铟锌铁分流共萃工序中,来自于加压浸出液(即加压上清液)中的铟与铁在高酸度下直接共萃,萃取的酸度在100~180g/L,在这个酸度下,In3+优先与P204萃取剂发生反应,其次才是Fe3+与P204萃取剂发生反应,化学反应方程式如下:In3++3HR(org)=InR3(org)+3H+⑽Fe3++3HR(org)=FeR3(org)+3H+⑾来自于常压浸出液(即一段上清液)中的铟与锌在pH=1~3.5时直接共萃,化学反应方程式如下:Zn2++2HR(org)=ZnR2(org)+2H+⑿在反锌段,则用酸度在160~220g/L的电锌贫液(即反锌前液)作为反萃剂将锌反下,变成富锌液,除油后用于锌电积,化学反应方程式如下:ZnR2(org)+H2SO4=ZnSO4+2HR(org)⒀在反铟段,则用酸度为2~4N的HCl和1~2NZnCl2作为反萃剂将铟反下,变成富铟液,这个过程中,也会有少许的三价铁会被反下,因此要经树脂净化提铟后,变为纯净的高含铟溶液,铟含量不低于100g/L,化学反应方程式如下:InR3(org)+3HCl=InCl3+3HR(org)⒁在反铁段,则用5~7N的HCl作为反萃剂采用两段反萃铁的工艺将铁反下,变成富铁液,富铁液中的Fe3+含量不低于70g/L,化学反应方程式如下:FeR3(org)+3HCl=FeCl3+3HR(org)⒂在盐酸再生工序中,纯净的InCl3富铟溶液可以采用盐酸再生技术直接与水反应生成高纯In2O3并再生盐酸,其化学反应方程式如下:2InCl3+3H2O=In2O3+6HCl⒃纯净的FeCl3富铁溶液可以采用盐酸再生技术直接与水反应生成高纯Fe2O3并再生盐酸,其化学反应方程式如下:2FeCl3+3H2O=Fe2O3+6HCl⒄来自于反铟段的富铟液分别用树脂提取In3+和Fe3+等离子后,是纯净的含ZnCl2的溶液,这个溶液在反铟段循环使用后,ZnCl2含量会产生富集,在保持反铟需用的1~2N浓度的ZnCl2含量后,多余的ZnCl2则采用盐酸再生技术生成ZnSO4·7H2O和回收盐酸,化学反应方程式如下:ZnCl2+H2SO4+7H2O=ZnSO4·7H2O+2HCl⒅在无锰锌电积工序中,反锌段产生的富锌液,分别经过一段树脂除油、两段活性碳除油,将溶液中可溶性油控制在1ppm以下,进行电积提锌,其化学反应方程式如下:阴极反应:Zn2++2e=Zn,阳极反应:2OH--2e=1/2O2+H2O⒆锌电积后产生的电锌贫液又返回到分流共萃工序的反锌段用作反萃剂。采用Air+SO2混合氧化除铁锰技术,通过控制其中一段常压浸出的终点pH值在3.0~3.5,可以有效地抑制铟和铁的浸出,同时有色固废渣中含有少量的金属硫化物也可以被氧化浸出;采用高压高酸氧浸可以选择性的强化In3+、Zn2+等离子的浸出,抑制Sn2+、As2+等离子的浸出,使90%的Fe3+离子以Fe2O3形态沉淀(其它5%的Fe3+离子以FeOOH形态沉淀);而通过控制另一段常压浸出的终点pH值~2,则可以让In3+、Zn2+等离子共同浸出。镉锰净化工序中,首先采用锌粉除镉工艺可以除去溶液中的Cd2+离子,同时,也进一步将Cu2+、Ni2+、Co2+、Bi2+、Sn2+等多种金属离子沉淀净化;其次采用Air+SO2混合氧化除铁锰技术能将溶液中的循环Mn2+离子除去70%;此工序的重要作用是将Cd2+、Mn2+等易于浸出却难以消除的金属离子从溶液中分别除去,达到溶液能够不断循环使用,而有害金属离子却不再富集的作用。铟锌铁分流共萃工序中,首先,In3+和Fe3+两种离子共萃的条件是必须控制溶液的酸度[H2SO4]在0~180g/L之间;In3+和Zn2+两种离子或者In3+、Fe3+和Zn2+三种离子共萃的条件必须是控制溶液的pH值在0.5~2.5之间;其次,上述的共萃条件也是不同溶液进行分流的条件,不同的分流溶液按共萃的要求分别进入到萃取系统;第三,分流共萃是由铟铁共萃段、铟锌铁共萃段、水洗段、酸洗段、反锌段、反铟段、反铁段、洗氯段等组成;第四,各种段的萃取、反萃或洗涤的级数根据溶液所含不同金属离子的成份,分别选择在3~8级之间;第五,反铁段采用了两段循环返铁,可以将Fe3+离子浓度富集到70g/L以上。盐酸再生工序中,InCl3、FeCl3在采用盐酸再生技术后,分别生成了In2O3、Fe2O3两种高纯氧化物和再生盐酸;ZnCl2在采用盐酸再生技术后,生成了ZnSO4·7H2O和再生盐酸。盐酸再生工序解决了分流共萃反铟段中的含金属氯化物废水零排放的难题;萃取除铁与盐酸再生技术实现了无缝对接,浸出铁消耗的酸经过铟铁共萃段得以再生循环,而铁也经过盐酸再生技术变成了附加值很高的Fe2O3产品,解决了湿法冶金中形成铁渣污染物的工业化难题。无锰锌电积工序中,首先是来自于分流共萃工序反锌段的反锌富液,除锌以外的各类金属杂质含量均小于1ppm以下;其次是电锌贫液作为反萃剂,不断地与分流共萃工序反锌段进行循环反萃,产生高纯的反锌富液用于锌电积工序;第三是分流共萃工序与无锰锌电积工序之间形成了一个封闭的溶液循环体系,借助这个体系,Zn2+离子则通过分流共萃工序进入,又通过无锰锌电积工序以锌金属的形式析出;第四是有少部分电锌贫液开路至分流共萃工序酸洗段,用以维持在分流共萃工序与无锰锌电积工序之间形成的这个封闭溶液循环体系中的杂质金属含量控制在1ppm以下。本发明中的任何一个工序,均不加入钠碱或钠盐。进一步,在一段加压浸出和两段常压逆流浸出工序中,采用固体原料与液体原料逆流相向的分段浸出方式。逆流分段浸出的优势在于可以完全利用分流共萃时产生的酸,以这些酸作为浸出剂,逐级最大化地实现有色固废渣中的有价金属的浸出率。进一步,所述的负载有机相运行到反锌段,通过反锌前液或电积贫液将负载有机相中的锌全部反萃下来,得到的反锌后液去无锰锌电积工序;在无锰锌电积工序中,所述的反锌后液经过一段树脂除油将可溶性有机物控制在10ppm以内,再经两段活性碳除油将可溶性有机物控制在1ppm以内。进一步,经无锰锌电积工序得到的电锌贫液作为反锌前液,返回到铟锌铁分流共萃工序的反锌段中。进一步,所述的负载有机相运行到反铟段,通过反铟前液将负载有机相中的铟全部反萃下来,得到的反铟后液去盐酸再生工序。进一步,在盐酸再生工序中,反铟后液通过树脂提铟吸附铟离子,用盐酸将吸附铟离子的树脂反洗再生,铟离子进入富铟后液中,富铟后液进行盐酸再生,产出In2O3产品,并再生盐酸,再生的盐酸去反铟前液和用于树脂反洗再生。进一步,通过树脂提铟得到的提铟余液然后进行树脂提铁,用盐酸将吸附铁离子的树脂反洗再生,铁离子进入富铁后液中,富铁后液进行盐酸再生,产出氧化铁产品,并再生盐酸,再生的盐酸去反铁一段后液和洗氯后液。进一步,通过树脂提铁得到的提铁后液加入硫酸,进行盐酸再生,产出高纯ZnSO4·7H2O产品,并再生盐酸,再生的盐酸去反铟前液和用于树脂反洗再生;浓缩的结晶母液大部分循环使用,小部分返回到反铟前液再循环。进一步,所述的负载有机相运行到反铁二段和反铁一段,通过反铁前液将负载有机相中的铁全部反萃下来,得到的反铁二段后液进行盐酸再生,产出氧化铁产品,并再生盐酸,再生的盐酸去反铁一段后液和洗氯后液。进一步,所述的负载有机相运行到洗氯段,洗氯前液将负载有机相中夹带的氯离子全部反萃下来,得到的洗氯后液作为反铁一段前液使用,反铁一段前液经反铁一段后得到的反铁一段后液作用反铁二段前液使用。本发明具有的有益效果:(1)实现了工业水零排放,完全的闭路循环;(2)没有造成污染的工业铁渣(与传统的湿法冶金所产生的大量有污染的工业铁渣相比);(3)零成本提取铟金属;(4)酸的循环再生与利用;(5)相对于传统的湿法冶金生产方式具有辅料消耗低、能耗低、运行成本低、金属收率高等优势。附图说明下面结合说明书附图和具体实施方式对本发明作进一步说明。图1为本发明的一段加压和两段常压逆流浸出工序流程图。图2为本发明的镉锰净化工序流程图。图3为本发明的铟锌铁分流共萃工序流程图。图4为本发明的盐酸再生工序流程图。图5为本发明的无锰锌电积工序流程图。具体实施方式本发明的一段加压和两段常压逆流浸出工序流程如图1所示:在锌浸二段,来自于铟锌铁分流共萃工序的含酸共萃余液与有色固体废渣、Air+SO2混合气体在反应器里进行充分混合,控制pH值3~3.5,T=45~55℃,常压浸出后,将矿浆在锌浸二段浓密设备中进行液固分离,分离出来的锌浸二段上清液去镉锰净化工序;而锌浸二段底流则进入锌浸一段与含酸的萃锌余液在反应器里充分混合浸出,控制pH值1~2.5,T=45~55℃,常压浸出后,将矿浆在锌浸一段浓密设备中进行液固分离,分离出来的锌浸一段上清液进行精滤,要求ss≤1ppm;而锌浸一段底流则进入一段加压浸出,控制T=150~200℃,P=1.2~1.8Mpa,[H2SO4]=100~180g/L,通入氧气,并使锌浸一段底流与铟锌铁分流共萃工序的含酸共萃余液充分混合,保持合适的浸出时间,然后将加压浸出后的矿浆在浓密设备中进行液固分离,分离出的固体经过滤洗涤后变成可销售的铅产品;而分离出的加压上清液进行精滤,要求ss≤1ppm;精滤后的锌浸一段上清液和加压上清液分别进入铟锌铁分流共萃工序的铟锌共萃段段和铟铁共萃。在一段加压和两段常压逆流浸出工序中,(1)利用有色固体废渣中的金属氧化物成分起到了酸度的调节作用;在与Air+SO2混合气体常压浸出的过程中,pH控制在3~3.5,除锌外,铁与其它金属均在这里被抑制浸出,来自于铟锌铁分流共萃工序的共萃余液中的酸得到了很好的利用,但Cd2+、Mn2+等离子开路出来,需要在镉锰净化工序去除;而在另一个常压浸出的过程中,pH控制在1~2.5,锌、铁、铟等金属被浸出,来自于铟锌铁分流共萃工序的共萃余液中的酸再次得到了很好的利用;(2)循环浸出液中锌浓度的控制起到关键的承上启下的作用,P204萃取剂的浓度决定了锌的迁移量,本发明中循环浸出液中锌的浓度控制在15~50g/L;(3)加压浸出的工艺控制条件为:有氧条件下,T=150~200℃,P=1.2~1.8Mpa,[H2SO4]=100~180g/L;这个条件是选择性浸出In3+、Zn2+离子的关键条件,除Cd2+、Mn2+等离子外,其它杂质几乎被抑制住。本发明的镉锰净化工序流程如图2所示:锌浸二段上清液与锌粉进行二段置换反应除镉,将镉等金属离子从溶液中沉淀下来;矿浆经过除镉浓密设备进行液固分离,分离后的除镉底流经过滤洗涤后成为可销售的粗镉产品;而分离后的除镉上清液与Air+SO2混合气体在反应器里充分混合氧化除锰,控制pH值为<4或5~7,T=~50℃,反应一段时间后,将除锰后的矿浆在除锰浓密设备中进行液固分离,分离后的除锰底流经过滤洗涤后成为可销售的锰产品;而分离后的除锰上清液进行精滤,求ss≤1ppm,精滤后的除锰上清液进入铟锌铁分流共萃工序的萃锌段。在镉锰净化工序中,(1)大量的工业化试验已经证明,Cd2+、Mn2+等离子无论在硫酸盐还是氯化盐体系均有良好的浸出率,因此,Cd2+、Mn2+等离子在溶液中循环富集是影响分流共萃技术使用的一个重要因素;(2)Cd2+离子采用锌粉除去是工业化普遍使用的方法,但Mn2+离子在溶液中作为杂质的去除却是非常困难,控制溶液pH值,采用Air+SO2混合气体氧化除锰是本发明中独特的办法,Mn2+离子在这个过程中会被除去~70%,主要工艺控制条件如下:T=30~50℃,pH<4或pH=5~7;(3)经过此工序,Cd2+、Mn2+等离子在溶液中可反复循环但不会富集。本发明的铟锌铁分流共萃工序流程如图3所示:分别来自于一段加压和两段常压逆流浸出工序的三种溶液:精滤后加压上清液、精滤后一段上清液和除锰精滤后液,根据这三种溶液不同的酸度,则依次分别进入铟锌铁分流共萃工序的铟铁共萃段、铟锌共萃段和萃锌段,In3+、Zn2+、Fe3+等离子进入有机相中,分别产生了铟铁共萃余液、铟锌共萃余液和萃锌余液。铟铁共萃余液大部分返回加压浸出进行循环,很少部分进入锌浸二段开路富集的镉、锰等金属离子;铟锌共萃余液则全部返回到锌浸二段;萃锌余液则全部返回到锌浸一段。三种负载有机相汇流到一起,负载有机相先经过水洗段洗去有机相中机械夹带的氯、氟等离子,再经过酸洗段洗下萃上的铜、锰等金属离子;负载有机相运行到反锌段,电解贫液将有机相中的锌全部反萃下来,使锌浓度满足可以进行电积的要求;负载有机相运行到反铟段,反铟前液将有机相中的铟全部反萃下来,富集铟离子的浓度达到100g/L以上;负载有机相运行到反铁段,反铁前液将有机相中的铁全部反萃下来,经过两段循环反铁,使铁离子的浓度达到70g/L以上;负载有机相运行到洗氯段,洗氯前液将有机相中夹带的氯离子全部洗下来,不会在萃取段与分流料液混合时,把氯根带入溶液循环体系。在铟锌铁分流共萃工序中,(1)铟铁共萃的工艺条件如下:Fe3+<40g/L,In3+~5g/L,[H2SO4]=100~180g/L;在这个条件下,Fe3+、In3+离子被同时萃取进入有机相;(2)铟锌共萃的工艺条件如下:Zn2+=15~50g/L,In3+~5g/L,pH=1~3.5;在这个条件下,Zn2+、In3+离子被同时萃取进入有机相;(3)反锌的工艺条件如下:Zn2+30~90g/L,[H2SO4]=160~220g/L;(4)反铟的工艺条件如下:ZnCl2=1~2N,[HCl]=2~4N;(5)反铁的工艺条件如下:[HCl]=5~7N;(6)根据不同的萃取料液情况设计了不同的萃取段,这是分流共萃新工艺的一个核心思想;(7)有机相共用了水洗段、酸洗段、反锌段、反铟段、反铁段、洗氯段;(8)萃取段(铟铁共萃段、铟锌共萃段、锌萃取段等)、水洗段、酸洗段、反锌段、反铟段、反铁段、洗氯段是一个依次不可颠倒的顺序,要实现分流共萃新工艺,缺一不可;(9)反铁段采用的两段反铁结合盐酸再生技术,其目的是利用循环反萃的方法将Fe3+的浓度富集超过70g/L以上。本发明的盐酸再生工序流程如图4所示:反铟后液中含有In3+、Fe3+、Zn2+等金属离子,溶液经过树脂后将In3+吸附后,提铟余液中剩下Fe3+、Zn2+等金属离子;用HCl将吸附In3+离子的树脂反洗再生后,树脂可继续用于反铟后液的处理,而In3+离子全部进入到富铟后液中,富铟后液经盐酸再生技术处理后,产出高纯In2O3产品,并再生盐酸。提铟余液过树脂后将Fe3+吸附后,提铁后液中只剩下Zn2+离子;用HCl将吸附Fe3+离子的树脂反洗再生后,树脂可继续用于提铟余液的处理,而Fe3+离子全部进入到富铁后液中,富铁后液与反铁二段后液混合后经盐酸再生技术处理后,产出高纯Fe2O3产品,并再生盐酸。在提铁后液中加入硫酸,并控制温度,经过盐酸再生技术处理后,产出高纯ZnSO4·7H2O产品,并再生盐酸,浓缩的结晶母液(ZnCl2)大部分返回到SSC盐酸再生技术系统循环使用,小部分返回到反铟前液再循环。再生的盐酸则分别返回到树脂再生、反铟段的反铟前液、反铁一段后液及反铁段的洗氯后液中循环使用。在盐酸再生工序中,(1)形成的FeCl3废酸液通过盐酸再生技术可以生成用于制作软磁材料的高纯Fe2O3产品,并且再生盐酸可以返回到分流共萃工序的反铁段循环使用,这是目前任何一个萃取工艺都无法做到的;(2)传统的高纯In2O3产品都是采用4N的精铟经过电解、真空蒸馏、再电解达到6N的金属铟后,再用酸溶解,并且用碱沉淀后变成氢氧化铟烘干煅烧而成,本发明中使用树脂提铟后的富铟溶液(InCl3溶液)通过盐酸再生技术可以直接生成高纯In2O3,大幅度降低生产成本;(3)提铟后的含氯化锌的废酸液采用盐酸再生技术,生成了高纯的七水硫酸锌产品,再生的盐酸又可返回到反铟前液中使用。本发明的无锰锌电积工序流程如图5所示:反锌后液经过一段树脂除油将可溶性有机物控制在10ppm以内,再经两段活性碳除油将可溶性有机物控制在1ppm以内,此时的溶液可以进入电解槽中进行电解,控制合适的槽电压、电流密度及电流,可以产出0#锌产品,电锌贫液则返回到铟锌铁分流共萃工序的反锌段循环使用。在无锰锌电积工序中,(1)锌电解液中Mn2+离子含量低于1ppm,彻底颠覆了传统锌电解中依靠Mn2+离子保护铅阳极的技术思想;(2)经过锌电积产生的电锌贫液返回到分流共萃工序的反锌段循环使用;(3)锌电解液中的杂质含量均小于1ppm以下;(4)电锌贫液有少许部分会返回到分流共萃工序的酸洗段,以确保锌电解循环液中的杂质含量均小于1ppm以下;(5)采用一段树脂、两段活性碳除油的方式,使锌电解液中的可溶性有机物必须低于1ppm,以防止电解时烧板。