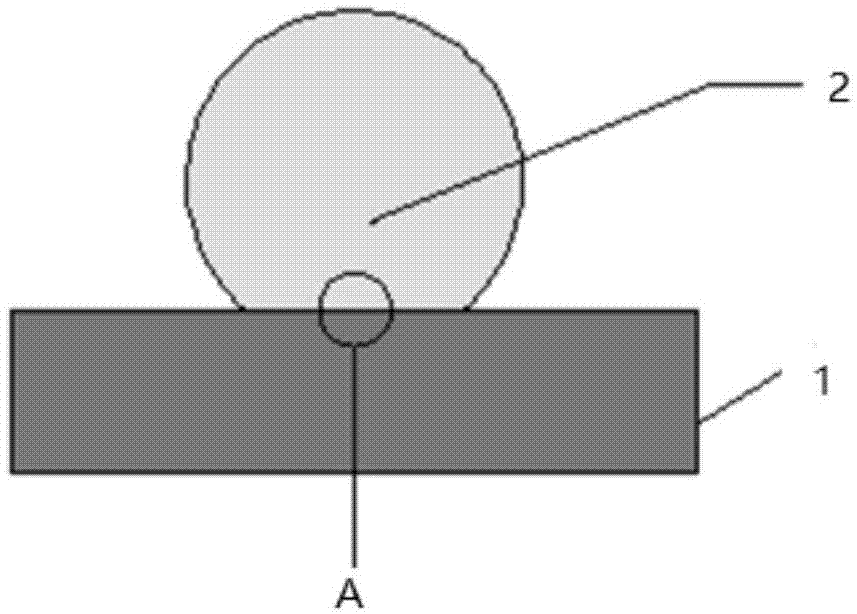
本发明涉及表面处理
技术领域:
,特别涉及一种耐腐蚀铝材的制备方法及耐腐蚀铝材。
背景技术:
:目前工业上用于铝电解电容器生产的阳极引出箔是铝片经过氧化处理后的加压光箔,其表面具有一层较薄的氧化膜,相较于原始光箔,在耐腐蚀性能上有一定改善。但铝电解电容器中存在一定量的水,水与电容器中的cl-会形成hcl溶液,易入侵至氧化膜缺陷处导致阳极引出箔局部酸腐蚀的发生,即h2o+cl-→hcl+ho-→hcl+al+ho-→alcl3+h2o或h2o+cl-→hcl+ho-→hcl+al2o3+ho-→alcl3+h2o,该自催化酸腐蚀反应会恶性发展,最终导致电容器失效。因此,水在铝电解液电容器发生腐蚀现象中是一个关键因素,抑制水参与腐蚀反应过程,可极大地提高铝电解电容器的耐腐蚀性能,延长使用寿命。近年来,现有技术中针对材料超疏水表面的研究也愈加广泛和深入。有研究表明,在金属表面修饰出超疏水表面,可以使得水滴不会在金属表面聚集,并且在非常小的外力作用下便可以使水滴从超疏水的金属表面滚落。例如中国专利cn201610540625.6公开了一种超双疏层表面铝片的制备方法,针对海洋环境对金属腐蚀严重的问题,该专利将铝片打磨、抛光、脱脂、除油、除钝化层后用盐酸溶液浸泡,蚀刻出微米级结构表面,再将铝片浸泡在沸水中后再迅速浸入液氮中,在微米级结构表面上进一步蚀刻出纳米级结构表面,将表面微纳结构铝片浸泡在制备的硬脂酸银中,经烘干后制得超双疏层表面铝片。但是,由于该专利中的铝片使用盐酸溶液进行浸泡,这样将在铝片表面残留cl-,特别是将其用于铝电解电容器时,将会加剧铝电解电容器的腐蚀反应,而且其制备方法复杂,成本较高。综上所述,提供一种提高铝电解电容器耐腐蚀性能、延长使用寿命、制备方法简单、成本低的铝材制备方法是目前亟需解决的问题。技术实现要素:本发明的目的是为了解决现有技术中铝电解电容器耐腐蚀性能差、使用寿命短、制备方法复杂、成本高的问题,而提供了一种耐腐蚀铝材的制备方法及耐腐蚀铝材。为解决上述技术问题,本发明提供了一种耐腐蚀铝材的制备方法,包括如下步骤:将待处理铝材放入有机酸溶液,得到具有微米粗糙结构的铝材;将具有微米粗糙结构的铝材放入低表面能溶液,得到耐腐蚀铝材,其中,耐腐蚀铝材表面的静态接触角不小于150°。与现有技术相比,本发明通过使用有机酸溶液处理待处理铝材,得到具有微米粗糙结构的铝材,有效防止cl-等杂质离子对待处理铝材进行腐蚀,而后将具有微米粗糙结构的铝材放入低表面能溶液,得到超疏水耐腐蚀铝材,即通过对待处理铝材进行表面超疏水化,可以提高待处理铝材在腐蚀过程中的活化位垒,阻缓腐蚀过程,从而达到提高其耐腐蚀性能、延长其使用寿命、提升铝电解电容器品质的目的,与此同时,由于该制备工艺简单,还节约了成本。优选地,有机酸溶液为草酸溶液。优选地,有机酸溶液的浓度不小于2m。优选地,有机酸溶液的浓度范围为2-3m。优选地,低表面能溶液为硬脂酸乙醇溶液、棕榈酸乙醇溶液、十八烯酸乙醇溶液、十八烷基三氯硅烷乙醇溶液中的任一种。优选地,低表面能溶液为十八烯酸乙醇溶液。优选地,在将待处理的铝材放入有机酸溶液中之前,还包括以下步骤:待处理铝材放入碱性溶液。优选地,在将待处理铝材放入碱性溶液之前,还包括以下步骤:将待处理铝材依次放入丙酮溶液、乙醇溶液、去离子水后,再采用超声波清洗。本发明提供了一种由上述耐腐蚀铝材的制备方法制备的耐腐蚀铝材。此外,本发明还提供耐腐蚀铝材在铝电解电容器阳极引出箔上的应用。附图说明一个或多个实施例通过与之对应的附图中的图片进行示例性说明,这些示例性说明并不构成对实施例的限定,附图中具有相同参考数字标号的元件表示为类似的元件,除非有特别申明,附图中的图不构成比例限制。图1是本发明实施例2中的水在超疏水耐腐蚀阳极引出箔表面的示意图;图2是图1的a处局部放大图;图3是样品a、b的极化曲线图。具体实施方式为使本发明实施例的目的、技术方案和优点更加清楚,下面将结合附图对本发明的各实施例进行详细的阐述。本领域的普通技术人员可以理解,在本发明各实施例中,为了使读者更好地理解本申请而提出了许多技术细节。但是,即使没有这些技术细节和基于以下各实施例的种种变化和修改,也可以实现本申请所要求保护的技术方案。本具体实施方式涉及一种耐腐蚀铝材的制备方法,包括如下步骤:将待处理铝材放入有机酸溶液中进行刻蚀,得到具有微米粗糙结构的铝材;将具有微米粗糙结构的铝材放入低表面能溶液进行表面修饰,得到耐腐蚀铝材,耐腐蚀铝材表面的静态接触角不小于150°。优选地,有机酸溶液可以为草酸溶液。在具体实施方式中,有机酸溶液的浓度不小于2m,优选地,有机酸溶液浓度范围为2-3m。优选地,低表面能溶液可以为硬脂酸乙醇溶液、棕榈酸乙醇溶液、十八烯酸乙醇溶液、十八烷基三氯硅烷乙醇溶液中的任一种。需要说明的是,在将待处理的铝材放入有机酸溶液中进行刻蚀之前,还包括以下步骤:待处理铝材放入碱性溶液以去除待处理铝材表面的氧化层。具体地,当待处理铝材为铝电解电容器中的阳极引出箔时,由于阳极引出箔表面有一层较薄的氧化膜,需要在待处理铝材与有机酸溶液反应之前放入碱性溶液以去除待处理铝材表面的氧化层。当然,待处理铝材也可以是表面没有形成氧化层的铝材,当没有形成氧化层时,可以直接将其与有机酸溶液进行反应。另外,在将待处理铝材放入碱性溶液之前,该制备方法还包括以下步骤:将待处理铝材依次放入丙酮溶液、乙醇溶液、去离子水后,再采用超声波清洗5min以去除待处理铝材的表面残余物。具体地,该步骤使用丙酮溶液、乙醇溶液等化学清洗剂去除待处理铝材表面的油脂和其他杂质。具体地,将对耐腐蚀阳极引出箔的制备方法进行详细描述:试验材料:待处理的普通650vf阳极引出箔、丙酮、乙醇、去离子水、氢氧化钠、草酸、硬脂酸。试验仪器:超声波清洗机、烧杯本具体实施方式中,如下将给出12个实施例。将12个待处理的普通650vf阳极引出箔依次置于分别装有丙酮、乙醇、去离子水的干净烧杯中,并放置于超声波清洗机中进行超声波清洗各5min;将经过上述处理后的阳极引出箔取出,自然干燥10min后待用;取一干净烧杯配制1m氢氧化钠溶液200ml,另分别配制浓度2m、2.5m、3m的草酸溶液100ml待用;先将干燥后的阳极引出箔浸入1m氢氧化钠溶液以去除表面氧化层,10min后同时取出并用大量去离子水清洗并自然风干;再将风干后的12个阳极引出箔分成3组,分别浸入2m、2.5m、3m的草酸以构建表面粗糙结构,过程持续5min,完成后用大量去离子水对阳极引出箔清洗并自然风干;分别取一干净烧杯配制质量分数为1%硬脂酸乙醇溶液、棕榈酸乙醇溶液、十八烯酸乙醇溶液、十八烷基三氯硅烷乙醇溶液200ml;将干燥后的每组阳极引出箔分别置于配制好的硬脂酸乙醇溶液、棕榈酸乙醇溶液、十八烯酸乙醇溶液、十八烷基三氯硅烷乙醇溶液中10min,其目的是赋予阳极引出箔表面低表面能的性质;上述步骤完成后取出阳极引出箔,用大量去离子水冲洗以去除残留的溶液,然后风干得到耐腐蚀阳极引出箔。经表面静态接触角测试,12个阳极引出箔的静态接触角及对应的酸处理剂、低表面能溶液如表1所示:表112个实施例的处理条件及静态接触角测试数值序号草酸浓度(m)低表面能物质类别静态接触角数值实施例12硬脂酸155°实施例22棕榈酸152°实施例32十八烯酸164°实施例42十八烷基三氯硅烷162°实施例52.5硬脂酸154°实施例62.5棕榈酸153°实施例72.5十八烯酸165°实施例82.5十八烷基三氯硅烷163°实施例93硬脂酸157°实施例103棕榈酸154°实施例113十八烯酸167°实施例123十八烷基三氯硅烷165°超疏水表面的静态接触角大于等于150°,才具备良好的疏水性能,由上表可知,经过本实施方式12个实施例的方法处理得到的12个阳极引出箔的静态接触角的角度均大于150°,即12个阳极引出箔的表面均已经实现超疏水化,具有良好的耐腐蚀性能。关于耐腐蚀机理,如图1和图2所示,超疏水耐腐蚀阳极引出箔1表面的粗糙结构存在大量孔隙,因此在浸润过程中这些孔隙会捕捉气体,在超疏水耐腐蚀阳极引出箔1表面形成一层类似“空气垫”的膜层,当腐蚀液滴2(如h2o、cl-)经过超疏水耐腐蚀阳极引出箔1表面时,由于其上粗糙孔隙的影响,其表面的气垫3将隔绝与腐蚀物质的接触,提高了耐腐蚀性。在本实施方式中,12个实施例通过使用草酸溶液处理待处理阳极引出箔,得到具有微米粗糙结构的阳极引出箔,有效防止cl-等杂质离子对待处理阳极引出箔进行腐蚀,而后将具有微米粗糙结构的阳极引出箔放入低表面能溶液,得到超疏水耐腐蚀阳极引出箔,即通过对待处理阳极引出箔进行表面超疏水化,可以提升阳极引出箔表面的耐腐蚀性能,从而赋予铝电解电容器在高温高负荷下更优秀的耐腐蚀性能。对比例一关于有机酸的遴选本组对比例分别使用乳酸溶液、甲酸溶液、醋酸溶液、苯甲酸溶液处理阳极引出箔,然后经过相同的低表面能溶液处理后,进行表面静态接触角度的测试,并与实施例1进行对比,具体步骤如下:试验材料:待处理的普通650vf阳极引出箔、丙酮、乙醇、去离子水、氢氧化钠、乳酸、甲酸、醋酸、苯甲酸、硬脂酸。试验仪器:超声波清洗机、烧杯取多段同批次、待处理的普通650vf阳极引出箔,记为对比例1-4,依次置于分别装有丙酮、乙醇、去离子水的干净烧杯中,并放置于超声波清洗机中进行超声波清洗各5min,其目的是通过化学清洗剂去除其表面的油脂和其他杂质;将经过上述处理后的对比例1-4阳极引出箔取出,自然干燥10min后待用;取一干净烧杯配制1m氢氧化钠溶液200ml,另分别配制同浓度2m的乳酸溶液、甲酸溶液、醋酸溶液、苯甲酸溶液各100ml待用;先将干燥后的对比例1-4的阳极引出箔浸入1m氢氧化钠溶液以去除表面氧化层,10min后同时取出并用大量去离子水清洗并自然风干;再将风干后的对比例1阳极引出箔浸入2m乳酸溶液、对比例2阳极引出箔浸入2m甲酸溶液、对比例3阳极引出箔浸入2m醋酸溶液、对比例4阳极引出箔浸入2m苯甲酸溶液以构建表面粗糙结构,过程持续5min,完成后用大量去离子水对比例1-4的阳极引出箔清洗并自然风干;取一干净烧杯配制质量分数为1%硬脂酸的乙醇溶液200ml;将干燥后的对比例1-4的阳极引出箔置于配制好的硬脂酸乙醇溶液中10min,其目的是赋予阳极引出箔表面低表面能的性质;上述步骤完成后取出对比例1-4的阳极引出箔,用大量去离子水冲洗以去除残留的溶液,然后风干。经表面静态接触角测试,对比例1-4的阳极引出箔的接触角及对应酸处理剂以及与实施例1的对比如表2所示:表2对比例1-4与实施例1的静态接触角对比由上表可见,对比例所选取的其余四种有机酸,经其处理后,在阳极引出箔获得的静态接触角均低于150°,可见,并不是所有有机酸都能满足本发明的处理要求。对比例二关于草酸浓度的遴选本组对比例使用不同浓度的草酸溶液对阳极引出箔进行表面处理,然后进行静态接触角度的测试,并与实施例1进行对比,本对比实施例的制备方法与实施例1相同,具体步骤如下:试验材料:待处理的普通650vf阳极引出箔、丙酮、乙醇、去离子水、氢氧化钠、草酸、硬脂酸。试验仪器:超声波清洗机、烧杯试验步骤:取多段同批次、待处理的阳极引出箔,记为对比例5、对比例6,依次置于分别装有丙酮、乙醇、去离子水的干净烧杯中,并放置于超声波清洗机中进行超声波清洗各5min,其目的是通过化学清洗剂去除其表面的油脂和其他杂质;将经过上述处理后的对比例5-6的阳极引出箔取出,自然干燥10min后待用;取一干净烧杯配制1m氢氧化钠溶液200ml,另分别配制不同浓度的草酸溶液各100ml待用,其浓度依次为1m、1.5m。先将干燥后的对比例5-6阳极引出箔浸入1m氢氧化钠溶液以去除表面氧化层,10min后同时取出并用大量去离子水清洗并自然风干;再将风干后的对比例5阳极引出箔浸入1m草酸溶液、对比例6的箔浸入1.5m草酸溶液以构建表面粗糙结构,过程持续5min,完成后用大量去离子水对对比例5-6的箔清洗并自然风干。取一干净烧杯配制质量分数为1%硬脂酸的乙醇溶液200ml;将干燥后的对比例5-6阳极引出箔置于配制好的硬脂酸乙醇溶液中10min,其目的是赋予阳极引出箔表面低表面能的性质;上述步骤完成后取出对比例5-6阳极引出箔,用大量去离子水冲洗以去除残留的溶液,然后风干。经表面静态接触角测试,对比例5-6阳极引出箔的接触角及对应草酸浓度并与实施例1的对比如表3所示:表3对比例5-6与实施例1的静态接触角对比由表中数值可以看出,即便采用草酸进行处理,对其浓度也有较严格的要求,浓度低时,不能解决本发明要解决的问题,其中实施例1的2m的浓度为临界值,低于2m的浓度,达不到本发明要达到的技术效果。对比例三关于低表面能溶液的遴选本组对比例使用不同种类的低表面能溶液对阳极引出箔进行表面处理,然后进行静态接触角度的测试,并与实施例1进行对比,本对比例的制备方法与实施例1相同,具体步骤如下:试验材料:待处理的普通650vf阳极引出箔、丙酮、乙醇、去离子水、氢氧化钠、草酸、月桂酸、棕榈酸、十八烯酸、十八烷基三氯硅烷;试验仪器:超声波清洗机、烧杯;试验步骤:取多段同批次、待处理的阳极引出箔,记为对比例7-10,依次置于分别装有丙酮、乙醇、去离子水的干净烧杯中,并放置于超声波清洗机中进行超声波清洗各5min,其目的是通过化学清洗剂去除其表面的油脂和其他杂质;将经过上述处理后的对比例7-10的阳极引出箔取出,自然干燥10min后待用;取一干净烧杯配制1m氢氧化钠溶液200ml,另一干净烧杯配制2m的草酸溶液100ml待用;先将干燥后的对比例7-10的阳极引出箔浸入1m氢氧化钠溶液以去除表面氧化层,10min后同时取出并用大量去离子水清洗并自然风干;再将风干后的对比例7-10阳极引出箔浸入2m草酸溶液以构建表面粗糙结构,过程持续5min,完成后用大量去离子水对11-15号箔清洗并自然风干;取干净烧杯分别配制质量分数均为1%的月桂酸乙醇溶液100ml,棕榈酸乙醇溶液100ml,十八烯酸乙醇溶液100ml,十八烷基三氯硅烷乙醇溶液100ml;将干燥后的对比例7-10的引出箔分别置于配制好的上述低表面能溶液中10min,其目的是赋予阳极引出箔表面低表面能的性质;上述步骤完成后取出对比例7-10的阳极引出箔,用大量去离子水冲洗以去除残留的溶液,然后风干。经表面静态接触角测试,对比例7-10阳极引出箔的接触角及对应修饰剂以及与实施例1的对比如表4所示:表4对比例7-10与实施例1的静态接触角对比由表4可见,所选低表面能物质均有降低表面能的作用,但因低表面能物质本身所含碳链长度及官能团的不同,其修饰效果也有差别,从结果来看随修饰剂碳链增加,其对阳极引出箔表面的超疏水修饰效果也越好;当碳链长度相同时,含有官能团(如烯基、氯取代基)的低表面能物质如十八烯酸和十八烷基三氯硅烷修饰效果更优,但从避免引入氯离子杂质考虑,优选使用十八烯酸。因此,并非所有低表面能物质的处理均能解决本发明的技术问题测试及比较例分别选取未经处理、经本发明实施例1、实施例3以及现有技术采用无机酸(盐酸)处理的铝电解电容器阳极引出箔组装成电容器后进行寿命试验以及耐腐蚀性验证,具体如下:铝电解电容器的规格尺寸均为420v、680μf、φ35×50mm;同时上述所有的铝电解电容器使用的工作电解液皆为自制,其他材料都相同。采用普通阳极引出箔(未处理)为制作的产品编为p组,使用草酸制备的阳极引出箔所制作的铝电解电容器编为n组,使用盐酸制备的阳极引出箔所制作的铝电解电容器编为s组。p组、n组及s组各选6支产品,测量初始参数后进行直流加纹波负荷寿命试验。试验条件为:105℃,120hz,纹波电流为3.28a/pcs,额定电压满负载投试。参数测试温度为25℃,湿度45%,数据取平均值。首先,如图3所示,通过电化学工作站对上述未处理样品(a)、实施例3样品(b)进行tafel曲线测试,测试溶液为0.5mnacl+0.1mhcl的水溶液。通过比较分析图中两样品箔的极化曲线,可明显看出实施例3样品(b)的自腐蚀电位大于未处理样品(a),其自腐蚀电流也小于未处理样品(a),其孔蚀电位也高于未处理样品(a),从极化曲线图上可以看出实施例3样品(b)比未处理样品(a)更耐电化学腐蚀。其次,产品寿命及腐蚀情况测试结果如表5所示:表5测试及比较例产品寿命及腐蚀情况测试结果由表5可见,经过105℃,5000h寿命试验后,采用未处理阳极引出箔制备的电容器(p组)解体后发现出现腐蚀现象,腐蚀概率高达83.3%,且产品各项参数变化明显;其中在4000h出现一只产品(p3)漏液无容量,解体发现阳极引出箔出现严重腐蚀。采用实施例1的方法处理阳极引出箔制备的电容器(n组)解体后发现出现一只产品(n2)出现轻微腐蚀,其他产品未腐蚀,且产品各项参数变化率明显小于p组。采用草酸制备的阳极引出箔制作的铝电解电容器经过105℃、5000h寿命试验后,产品容量衰减明显减小,损耗和漏电流增幅明显减低。产品腐蚀概率仅为16.7%,相较于普通阳极引出箔产品和盐酸处理的产品均有大幅的减少。采用盐酸制备的阳极引出箔制作的铝电解电容器(s组)经过同样的寿命试验后,有50%产品出现严重腐蚀断裂的情况,且产品腐蚀率也高达83.3%。对于现有技术采用盐酸进行处理的结果,是因为其中含氯的酸处理剂,盐酸的使用不可避免的在阳极引出箔空隙间残留了cl-,而在酸处理过程中,空气中的水也有微量残留在空隙间;虽然阳极引出箔表面经低表面能处理后呈现良好的超疏水性,但内部已然侵入了杂质离子cl-,其与内部的水分共同作用加剧了阳极引出箔内部的腐蚀,进而导致产品漏液无容量的发生。综上所述,使用非含氯的有机酸处理得到的阳极引出箔,对待处理阳极引出箔进行表面超疏水化,能形成更好的耐腐蚀膜层,有效阻隔电解液中的水或其他配套材料中杂质离子(如cl-等)的腐蚀入侵,从而提升阳极引出箔的耐腐蚀性能;采用其制作的铝电解电容器产品耐腐蚀性能有明显的提升,延长铝电解电容器的寿命。以上所述,仅为本发明较佳的具体实施方式,但本发明的保护范围并不局限于此,任何熟悉本
技术领域:
的技术人员在本发明揭露的技术范围内,可轻易想到的变化或替换,都应涵盖在本发明的保护范围之内。因此,本发明的保护范围应以所述权利要求的保护范围为准。当前第1页12