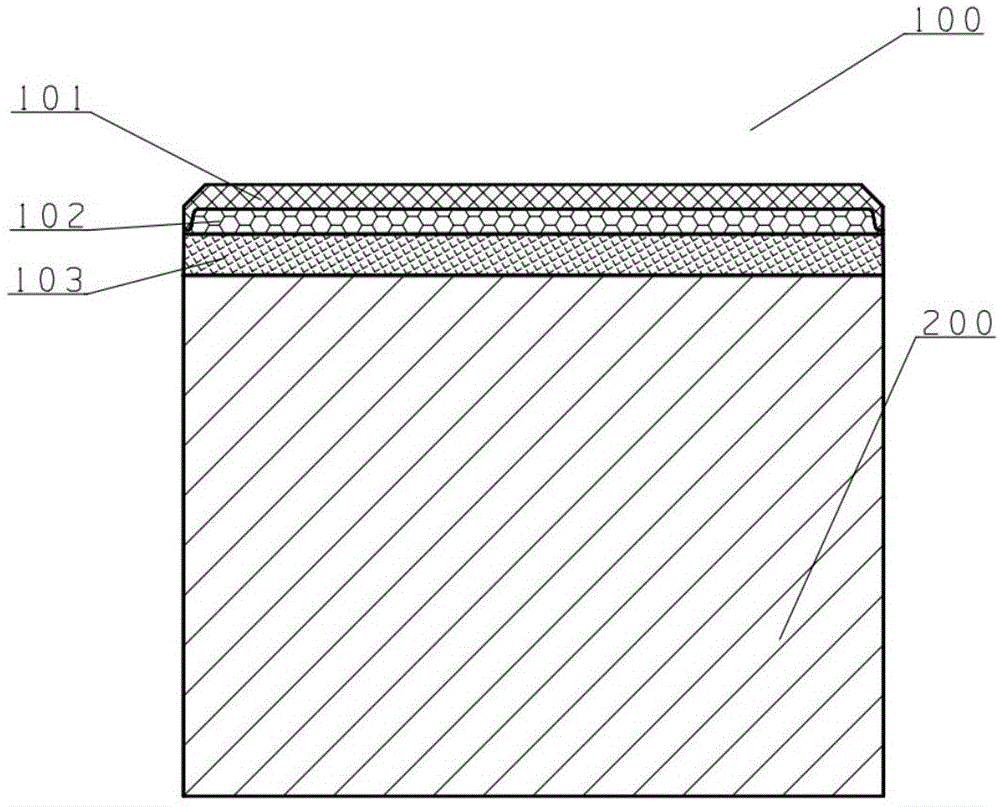
本发明涉及超硬材料
技术领域:
,尤其涉及一种热稳定型高抗冲击的聚晶金刚石复合片及其制备方法。
背景技术:
:聚晶金刚石复合片(pdc)一般由两层材料——上层的聚晶金刚石层和下层的硬质合金基体组成。一般是由金刚石粉末与硬质合金基体在高温高压(hthp)下烧结复合而成。金刚石复合片兼具金刚石层的高耐磨和硬质合金基体的高韧性,是石油天然气的钻采工具上非常重要的切削元件。随着油气开发行业的不断发展和对页岩气、页岩油等非常规能量的开发,开采条件以及对钻采工具的要求也变得越来越苛刻。对切削元件复合片的性能要求也由最初的耐磨性为主逐渐过渡到耐磨/抗冲性兼具,近几年在相当多的复杂难钻地层中对复合片的抗冲击性要求已占主导地位。同时钻采难度的提升使钻采成本日益增加,亟需提高复合片的使用寿命。而使用寿命除了与耐磨性和抗冲击性有关外,还与其热稳定性有着重要而直接的关系。然而,金刚石复合片的抗冲击性及热稳定性的提升却面临着以下三项技术难题。难题一,聚晶金刚石层与硬质合金基体在热膨胀系数和弹性模量上差异显著,如表1所示。这会导致在复合片烧结的冷却过程中硬质合金基体的收缩大于聚晶金刚石层,从而在聚晶金刚石层和硬质合金基体的结合界面处形成有害的残余拉应力,使聚晶金刚石层有脱层趋势,降低其抗冲击性能。表1聚晶金刚石层与硬质合金的物理性能对比材料种类热膨胀系数(10-6/℃)弹性模量(106psi)聚晶金刚石层1.5-3.8132硬质合金4.5-8.572.5-101.5此外,金刚石粉料粒度配比也是影响复合片抗冲击性的重要因素之一。较粗的粉料虽可以保证其抗冲击性,但复合片的耐磨性、热稳定性均会显著下降,因此需要设计一种能提高抗冲击性并同时保证综合性能的配方。难题二,常规复合片聚晶金刚石层的钴含量在12-15%范围内。这部分钴是来自于复合片烧结过程中,硬质合金基体向聚晶金刚石层迁移和扫越的钴。钴是促进金刚石颗粒溶解-析出-成键的重要触媒,在金刚石复合片的烧结中起着不可或缺的重要作用。但同时较高的钴含量会降低聚晶金刚石层的热稳定性和耐磨性,因为钴与金刚石间热膨胀系数的较大差异会使金刚石晶粒的键合间在受热条件下产生微裂纹,从而导致聚晶金刚石层的碎裂和复合片的早期失效。因此,在保证金刚石晶粒成键完整的前提下,钴含量越少其热稳定性越好。难题三,复合片的使用寿命取决于其综合性能的优劣,归根结底取决于金刚石晶粒的烧结质量和d-d键合程度。金刚石粉料本身由于粒度较细,在混配料和组装过程中会不可避免地吸附各种气体及杂质,降低其表面洁净度和活化烧结性,最终影响烧结质量、d-d键合和产品综合性能。技术实现要素:本发明的主要目的在于提供一种热稳定型高抗冲击的聚晶金刚石复合片及其制备方法,旨在保证复合片的耐磨性前提下提升其抗冲击性。为实现上述目的,本发明提出一种热稳定型高抗冲击的聚晶金刚石复合片,包括硬质合金基体和聚晶金刚石层,其中,所述聚晶金刚石层包括靠近硬质合金基体一侧的过渡层以及远离硬质合金基体一侧的表层,聚晶金刚石层的表层和过渡层由不同粒度金刚石粉料配方组成,表层粉料主粒度为5-25微米,过渡层粉料主粒度为25-45微米,表层与过渡层的厚度比为1:1-1:3。优选地,聚晶金刚石层的表层加过渡层的总厚度为2-3mm。优选地,所述硬质合金基体为带平行沟槽状界面的硬质合金基体。优选地,所述聚晶金刚石层的脱触媒金属表层包括以下重量含量的组份:钴1-5%,金刚石95-99%。优选地,所述聚晶金刚石层的未脱触媒金属表层和过渡层均包括以下重量含量的组份:钴8-14%,金刚石86-92%。本发明进一步提出一种基于上述的热稳定型高抗冲击的聚晶金刚石复合片的制备方法,包括以下步骤:混配不同粒度的双层金刚石粉料;将混配好的双层金刚石粉料、带平行沟槽状界面的硬质合金基体以及各种组装元件进行内、外组装,形成外合成模;将外合成模放入六面顶压机,在高温高压下烧结成聚晶金刚石复合片;采用强酸对金刚石复合片的聚晶金刚石层进行脱触媒金属处理。优选地,混配不同粒度的双层金刚石粉料时,对混配好的粉料在氢气气氛下进行650-750℃,时长为30-90min的烧制。优选地,将双层金刚石粉料、硬质合金基体和金属料杯进行内组装时,将组装好的内合成模在氩气气氛下进行500-1200℃,时长为90-150min的热处理。优选地,压制金刚石复合片时所用的温度为1400-1600℃,压力为7.5-8.5gpa。优选地,所述强酸为盐酸、硝酸和氢氟酸的混合物,各酸的体积比为2:1:1-1:1:1。本发明提出的热稳定型高抗冲击聚晶金刚石复合片,由于具有双层不同粒度的金刚石粉料配方,可以在保证复合片的耐磨性前提下提升其抗冲击性;较厚的金刚石层可提升复合片的抗冲击性和抗崩坏能力;带平行沟槽界面的硬质合金基体能有效降低界面有害残余应力,提高复合片的抗冲击性。本发明提出的热稳定型高抗冲击聚晶金刚石复合片,可提高钻进效率、缩短钻采周期、延长使用寿命并有效降低钻采成本。附图说明图1为本发明热稳定型高抗冲击的聚晶金刚石复合片的结构示意图;图2为本发明热稳定型高抗冲击的聚晶金刚石复合片中硬质合金基体的平行沟槽界面的结构示意图;图3为本发明热稳定型高抗冲击的聚晶金刚石复合片的制备方法的流程示意图。图中,100-聚晶金刚石层,101-脱触媒金属表层,102-未脱触媒金属表层,103-过渡层,200-硬质合金基体。本发明目的的实现、功能特点及优点将结合实施例,参照附图做进一步说明。具体实施方式应当理解,此处所描述的具体实施例仅仅用以解释本发明,并不用于限定本发明。本发明提出一种热稳定型高抗冲击的聚晶金刚石复合片。参照图1和图2,本发明提供一种热稳定型高抗冲击的聚晶金刚石复合片,包括硬质合金基体200和聚晶金刚石层100,其中,聚晶金刚石层100包括靠近硬质合金基体200一侧的过渡层103以及远离硬质合金基体200一侧的表层,聚晶金刚石层100的表层和过渡层103由不同粒度金刚石粉料配方组成,表层粉料主粒度为5-25微米,过渡层103粉料主粒度为25-45微米,表层与过渡层103的厚度比为1:1-1:3。表层包括脱触媒金属表层101和未脱触媒金属表层102。进一步地,聚晶金刚石层100的表层加过渡层103的总厚度为2-3mm。常见的聚晶金刚石层100总厚度为1.5-2.0mm;本聚晶金刚石复合片根据性能需求优选的总厚度为2.0-3.0mm。大量试验数据证明较厚的金刚石层也可明显地提升复合片的抗冲击性和抗崩坏能力。进一步地,硬质合金基体200为带平行沟槽状界面的硬质合金基体。通过采用带平行沟槽状界面的硬质合金基体,能有效降低聚晶金刚石层100与硬质合金基体200结合界面处有害的残余拉应力,降低聚晶金刚石层100的脱层风险,提高复合片的抗冲击性。表2对比了3种常见的硬质合金基体界面处的拉应力值,其中平行沟槽界面的拉应力值最低。表23种常见界面结构的拉应力分布及最大拉应力结果对比界面结构名称蜂巢界面平行沟槽界面圆台界面最大拉应力1764mpa1277mpa1395mpa进一步地,聚晶金刚石层100的脱触媒金属表层101包括以下重量含量的组份:钴1-5%,金刚石95-99%。进一步地,聚晶金刚石层100的非脱触媒金属表层102和过渡层103均包括以下重量含量的组份:钴8-14%,金刚石86-96%。即非脱触媒金属表层102和过渡层103中钴含量均为8-14%。现有技术中,聚晶金刚石层100中较多的钴含量(12-15%)会显著降低复合片的热稳定性、耐磨性和使用寿命。本发明通过降低聚晶金刚石层100中的钴含量(1-5%),从而提高了复合片的热稳定性和耐磨性,极大地改善了复合片因微裂纹扩展而引起的早期失效的问题。本发明提出的热稳定型高抗冲击的聚晶金刚石复合片的制备方法步骤如下:第一步,混配不同粒度的双层金刚石粉料;第二步,将混配好的双层金刚石粉料、带平行沟槽状界面的硬质合金基体200以及各种组装元件进行内、外组装,形成外合成模(内组装是指用金属料杯将硬质合金基体200和金刚石粉料包裹起来,形成的小零件叫做内合成模;外组装是指用各种盐零件和叶腊石块将内合成模包裹起来,形成的小零件叫做外合成模);第三步,将外合成模放入六面顶压机,在高温高压下烧结成聚晶金刚石复合片;第四步,采用强酸对金刚石复合片的聚晶金刚石层100进行脱触媒金属处理。第一步混配好不同粒度的双层金刚石粉料后,需将粉料在氢气气氛下进行650-750℃,时长为30-90min的烧制。第二步内组装完成后,需将内合成模在氩气气氛下进行500-1200℃,时长为90-150min的热处理。第三步压制金刚石复合片时所用的温度为1400-1600℃,压力为7.5-8.5gpa。第四步所用的强酸为盐酸、硝酸和氢氟酸的混合酸,各酸的体积比为2:1:1-1:1:1。本发明之所以能解决
背景技术:
中提到的制备一种热稳定性和抗冲击性提升的金刚石复合片所面临的三项技术难题,原因如下。通过采用了“表层粉料主粒度5-25微米的较细配方+过渡层103粉料主粒度25-45微米的较粗配方”的双层粉料设计。该设计既可以通过表层金刚石保证复合片一定的耐磨性,又可以通过过渡层103金刚石实现抗冲击性的提升。同时,通过采用了总厚度为2.0-3.0mm较厚的金刚石层,大量试验数据证明较厚的金刚石层也可明显地提升复合片的抗冲击性和抗崩坏能力。通过采用带平行沟槽状界面的硬质合金基体,能有效降低聚晶金刚石层100与硬质合金基体200结合界面处有害的残余拉应力,降低聚晶金刚石层100的脱层风险,提高复合片的抗冲击性。聚晶金刚石层100中较多的钴含量(12-15%)会显著降低复合片的热稳定性、耐磨性和使用寿命。通过降低聚晶金刚石层100中的钴含量,从而提高了复合片的热稳定性和耐磨性,极大地改善了复合片因微裂纹扩展而引起的早期失效的问题。本发明提供的热稳定型高抗冲击聚晶金刚石复合片,由于具有双层不同粒度的金刚石粉料配方,可以在保证复合片的耐磨性前提下提升其抗冲击性;较厚的金刚石层可提升复合片的抗冲击性和抗崩坏能力;带平行沟槽界面的硬质合金基体200能有效降低界面有害残余应力,提高复合片的抗冲击性。参照图3,本发明进一步提出一种热稳定型高抗冲击的聚晶金刚石复合片的制备方法,包括以下步骤:步骤s10,混配不同粒度的双层金刚石粉料;步骤s20,将混配好的双层金刚石粉料、带平行沟槽状界面的硬质合金基体以及各种组装元件进行内、外组装,形成外合成模(内组装是指用金属料杯将硬质合金基体和金刚石粉料包裹起来,形成的小零件叫做内合成模;外组装是指用各种盐零件和叶腊石块将内合成模包裹起来,形成的小零件叫做外合成模);步骤s30,将外合成模放入六面顶压机,在高温高压下烧结成聚晶金刚石复合片;步骤s40,采用强酸对金刚石复合片的聚晶金刚石层进行脱触媒金属处理。步骤s10中,混配好不同粒度的双层金刚石粉料后,需将粉料在氢气气氛下进行650-750℃,时长为30-90min的烧制。通过采用了对粉料在氢气气氛下的烧制工艺,该工艺可有效去除粉料表面吸附的杂质并还原粉料中的氧化物,提高粉料表面洁净度。步骤s20中,内组装完成后,需将内合成模在氩气气氛下进行500-1200℃,时长为90-150min的热处理。内合成模在氩气气氛下进行更高温度、更长时间的热处理工艺,该工艺不仅能进一步提高粉料表面的洁净程度、活化烧结性和润湿性,增强d-d键合的致密性(超高压也会促进d-d键合致密化),提升复合片的烧结质量,还能一定程度实现金刚石粉料的“预石墨化”,显著提升复合片的综合性能和使用寿命。粉料氢烧工艺、内合成模热处理工艺对粉料洁净度的影响如表3所示,粉料电导率越低,证明粉料上所吸附的杂质含量越少。表3氢烧、内合成模热处理工艺对粉料电导率的影响金刚石粉料粉料电导率值未经处理的粉料2.10us/cm经氢烧处理的粉料1.50us/cm经氢烧及内合成模热处理的粉料1.22us/cm步骤s30中,压制金刚石复合片时所用的温度为1400-1600℃,压力为7.5-8.5gpa。常规复合片的压制压力范围为5-7gpa,技术方案采用了7.5-8.5gpa的超高压力进行压制。合成压力的大幅提升使聚晶金刚石层中的钴在毛细作用下实现了少量且均匀的分布步骤s40所用的强酸为盐酸、硝酸和氢氟酸的混合酸,各酸的体积比为2:1:1-1:1:1。通过采用强酸脱除触媒金属钴的处理工艺,大幅降低了聚晶金刚石层中的钴含量(1-5%),从而提高了复合片的热稳定性和耐磨性,极大地改善了复合片因微裂纹扩展而引起的早期失效的问题。以下以两个实施例进行具体说明。实施例1本实施例为直径15.88,高度13.22mm的热稳定型高抗冲击聚晶金刚石复合片。首先混配好表层及过渡层的金刚石粉料:表层粉料主粒度为10-20mm,过渡层粉料主粒度为25-35mm。将混配好的双层粉料在氢气气氛下进行650-750℃,时长为30-90min的烧制。将烧制好的双层粉料按照表层厚度为1.0mm、过渡层厚度1.5mm的比例与带平行沟槽界面的硬质合金基体依次装入金属料杯中,进行内组装得到内合成模。将内合成模在氩气气氛下进行500-1200℃,时长为90-150min的热处理。将热处理后的内合成模与其他组装元件进行外组装得到外合成模,将外合成模放入六面顶压机中,在1500℃的温度和7.5gpa的压力条件下烧结成聚晶金刚石复合片。最后用体积比为1:1:1的盐酸、硝酸和氢氟酸的混合酸对金刚石复合片的聚晶金刚石层进行脱触媒金属处理,得到最终的产品——热稳定型高抗冲击聚晶金刚石复合片。将此热稳定型高抗冲击聚晶金刚石复合片与常规复合片进行室内性能对比检测。测试结果如表4所示:表4热稳定型高抗冲击复合片1与常规复合片性能对比测试结果显示:热稳定型高抗冲击复合片1相比常规复合片的钴含量降低了74.4%,耐磨性提高了48%,抗冲击性提高了50%,热稳定性/使用寿命提高了50%。实施例2本实施例为直径15.88,高度13.22mm的热稳定型高抗冲击聚晶金刚石复合片。首先混配好表层及过渡层的金刚石粉料:表层粉料主粒度为15-25mm,过渡层粉料主粒度为35-45mm。将混配好的双层粉料在氢气气氛下进行650-750℃,时长为30-90min的烧制。将烧制好的双层粉料按照表层厚度为1.0mm、过渡层厚度2.0mm的比例与带平行沟槽界面的硬质合金基体依次装入金属料杯中,进行内组装得到内合成模。将内合成模在氩气气氛下进行500-1200℃,时长为90-150min的热处理。将热处理后的内合成模与其他组装元件进行外组装得到外合成模,将外合成模放入六面顶压机中,在1550℃的温度和8.0gpa的压力条件下烧结成聚晶金刚石复合片。最后用体积比为1:1:1的盐酸、硝酸和氢氟酸的混合酸对金刚石复合片的聚晶金刚石层进行脱触媒金属处理,得到最终的产品——热稳定型高抗冲击聚晶金刚石复合片。将此热稳定型高抗冲击聚晶金刚石复合片与常规复合片进行室内性能对比检测。测试结果如表5所示:表5热稳定型高抗冲击复合片2与常规复合片性能对比测试结果显示:热稳定型高抗冲击复合片2相比常规复合片的钴含量降低了77.6%,耐磨性提高了39%,抗冲击性提高了75%,热稳定性/使用寿命提高了50%。本发明提出的热稳定型高抗冲击的聚晶金刚石复合片的制备方法,在制备过程中采用了粉料“氢烧”工艺和内模高温热处理工艺,有效提升粉料表面的洁净度、润湿性和烧结活性,从而提高金刚石的烧结质量和d-d键合的致密度。还采用了7.5-8.5gpa超高合成压力和脱触媒金属技术,显著降低了金刚石层中的钴含量,提高了复合片的热稳定性和耐磨性,极大地改善了复合片因微裂纹扩展而引起的早期失效的问题,显著提升了金刚石复合片的综合性能和使用寿命,从而也有效地延长了钻头的使用寿命。以上仅为本发明的优选实施例,并非因此限制本发明的专利范围,凡是利用本发明说明书及附图内容所作的等效结构变换,或直接或间接运用在其他相关的
技术领域:
,均同理包括在本发明的专利保护范围内。当前第1页12