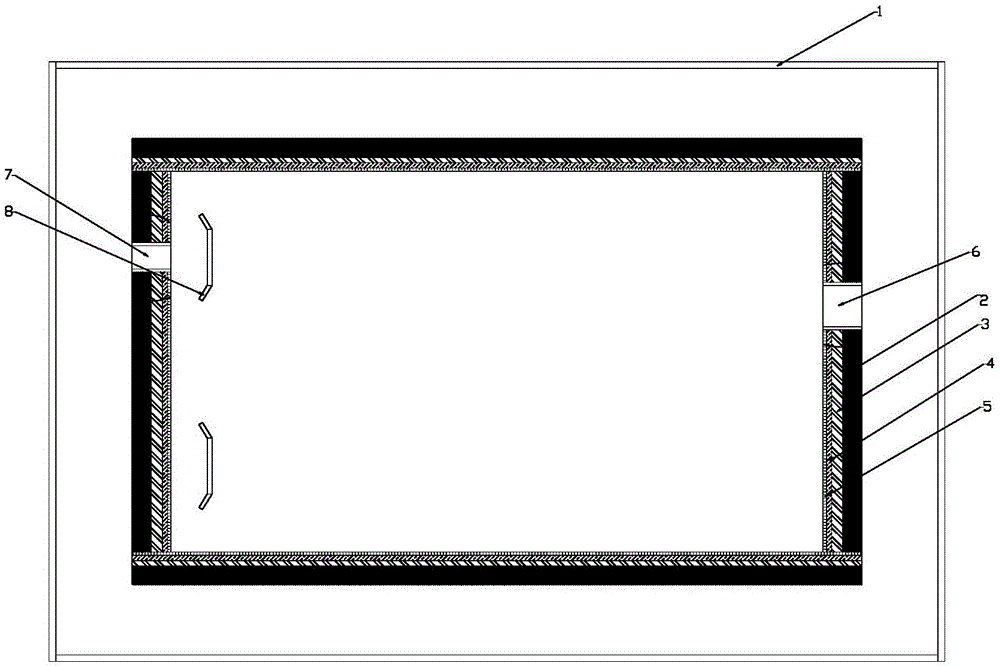
本发明涉及一种合金钢大圆坯的退火装置及其退火方法,属于模具钢的热处理
技术领域:
。
背景技术:
:随着连铸圆坯尺寸的增大和铸坯质量的提高,连铸大圆坯已经能满足高压管、火车车轮、车轴、风电法兰、锚链钢、轴承钢和齿轮钢等的技术要求。与模铸铸锭工艺相比,连铸圆坯不但质量逐步得到提高,而且生产稳定,生产效率大为提高,节约了时间和人力成本,减少了能源和材料的浪费,环境指标也大为改观。总之,采用连铸工艺生产大圆坯,精简了生产工序,降低了加工成本,提高了生产企业的利润。合金含量低的钢种大连铸圆坯,可以通过铸坯缓冷来消除铸坯中的残余应力。但合金含量较大的钢种,传统的缓冷工艺难以消除铸坯中的残余应力,铸坯会因此出现自然脆断、表面开裂等缺陷。因此合金含量较高的连铸坯下线后需要及时退火,但一般退火炉往往距离连铸工序较远,需要用汽车等工具对铸坯进行转运,在转运过程中铸坯热量损失很大,浪费严重,另外,退火炉装入量有限,不适合大批量连铸圆坯退火。技术实现要素:本发明克服了现有技术的不足,提供一种适用于合金钢大圆坯退火的退火装置退及退火方法。为达到上述目的,本发明采用了如下的技术方案:一种用于合金钢大圆坯的退火装置,所述退火装置为池型结构,四周墙壁由内到外依次为绝热层、保温层和耐火层;装置底部由内到外依次为轻质高强层、耐火层和高铝材料层;装置顶盖为钢结构框架形式,内部采用耐火纤维内衬,盖顶部设置吊钩;在一侧墙壁下部布置若干只亚高速烧嘴,烧嘴前设有挡火墙;与设置烧嘴相对的墙壁下部设有若干排烟口,排烟口通过烟道将炉内烟气排出,烟道设有调节阀。优选地,所述绝热层采用硅酸铝纤维板,所述保温层采用轻质保温砖,所述耐火层采用耐火黏土砖,所述轻质高强层采用轻质高强黏土砖,所述高铝材料层采用高铝砖,所述耐火纤维内衬的下层为纤维毯,上层为硅酸铝纤维块。优选地,所述若干只亚高速烧嘴具体为2-4只亚高速烧嘴。本发明中,所述退火装置还包括控制系统以及设置在四周墙壁上的温度传感器,实时检测退火炉内的空气温度,并将温度信号传递给控制系统,控制系统根据设定值进行烟道开口度及烧嘴燃烧强度的控制调节。一种合金钢大圆坯的退火方法,所述退火方法包括如下步骤:连铸圆坯火切后,通过行车直接吊至退火装置内,铸坯间隔10-15cm,排列多层;连铸圆坯装入完毕后,盖上顶盖,开始点火、升温,升温速度≤30℃/h,温度达到700-880℃后开始保温,保温24-48h,保温完成后关闭烧嘴,连铸圆坯在炉内降温,通过调整烟道开口度,控制冷却速度≤20℃/h,炉内温度降至150℃以下后打开顶盖,将连铸圆坯吊出。优选地,在连铸圆坯入炉前,提前将炉内温度加热到550℃以上。本发明中,所述连铸圆坯为:圆坯断面圆坯长度4000mm-9000mm。根据本发明的优选实施例,一种用于合金钢大圆坯的退火装置,为半地下式,池型结构。退火装置四周为混凝土墙壁,墙壁和底部均采用复合耐火材料砌筑。墙壁由内到外依次为硅酸铝纤维板、轻质保温砖和耐火黏土砖,底部由内到外依次为轻质高强黏土砖、耐火黏土砖和高铝砖。退火装置有顶盖,为钢结构框架形式,为了减轻重量,采用耐火纤维内衬,下层为纤维毯,上层为硅酸铝纤维块,具备良好的耐热保温性能,抗震动,密封性好。退火装置一侧墙面下部布置2-4只亚高速烧嘴,烧嘴采用同心射流方式,烧嘴可根据加热工艺的需要,调节燃烧火焰大小。烧嘴前设有挡火墙,烧嘴喷出火焰在挡火墙后(燃烧室空间)燃烧,之后炉气通过挡火墙进入退火装置内,高温炉气沿墙壁和钢件间流动,避免火焰直接烧铸坯。烧嘴喷出的气流,沿装置内壁循环流动,配合烧嘴安装位置角度,对炉气具有搅拌作用,增强了装置内的对流传热,装置底部设有垫铁,铸坯之间堆放时有间隙,提高了铸坯之间温度均匀性。与烧嘴向对的墙面下部设有若干排烟口,排烟口通过烟道将炉内烟气排出,烟道有调节阀,可通过调节各个排烟口开口度大小来控制炉内烟气流动。该退火装置采用一套控制系统实现全炉热工控制功能。设置系统的上位机,缓冷坑旁边设操作柜,可以进行各种参数设定和控制。在退火装置四周的墙壁上设有温度传感器,可实时检测退火装置内的空气温度,并将温度信号传递给控制系统,控制系统可根据设定情况进行烟道开口度及烧嘴燃烧强度的控制调节。本发明具有如下的有益效果:(1)退火装置结构简单,形状、大小与普通的铸坯缓冷坑相当,可以在连铸车间内部建设,铸坯下线后可以通过行车等直接转运至退火装置内,节约了转运时间。(2)铸坯下线后直接转运至退火装置内,铸坯温降少,退火过程中可减少铸坯加热过程中的煤气消耗。(3)退火装置为半地下式,池型结构,铸坯装入量大,可满足连续生产的需求。附图说明图1为本发明退火装置的剖视图一;图2为本发明退火装置的剖视图二;附图标记:1-护栏,2-混泥土墙壁,3-耐火黏土砖,4-轻质保温砖,5-硅酸铝纤维板,6-排烟口,7-烧嘴,8-挡火墙,9-烟道,10-轻质高强黏土砖,11-底部耐火黏土砖,12-高铝砖,13-煤气及空气管道,14-钢结构框架,15-纤维毯,16-炉盖,17-硅酸铝纤维块,18-吊钩。具体实施方式本说明书中公开得任一特征,除非特别叙述,均可被其他等效或具有类似目的的替代特征加以替换。除非特别叙述,每个特征只是一系列等效或者类似特征中的一个例子而已。所述仅仅是为了帮助理解本发明,不应该视为对本发明的具体限制。下面以附图和具体实施方式对本发明作进一步详细的说明。实施例1如图1和图2所示,一种用于合金钢大圆坯的退火装置,为半地下式,池型结构。退火装置四周为混凝土墙壁2,墙壁和底部均采用复合耐火材料砌筑。墙壁由内到外依次为硅酸铝纤维板5、轻质保温砖4和耐火黏土砖3,底部由内到外依次为轻质高强黏土砖10、底部耐火黏土砖11和高铝砖12。退火装置有顶盖16为钢结构框架14,为了减轻重量,采用耐火纤维内衬,下层为纤维毯15,上层为硅酸铝纤维块17,具备良好的耐热保温性能,抗震动,密封性好。盖顶部设置吊钩18。顶盖16外设置有护栏1,防止人员靠近等。退火装置一侧墙面下部布置2-4只亚高速烧嘴7,烧嘴采用同心射流方式,烧嘴可根据加热工艺的需要,调节燃烧火焰大小。烧嘴前设有挡火墙8,烧嘴喷出火焰在挡火墙后(燃烧室空间)燃烧,之后炉气通过挡火墙进入退火装置内,高温炉气沿墙壁和钢件间流动,避免火焰直接烧铸坯。烧嘴7与煤气及空气管道13连接。烧嘴喷出的气流,沿装置内壁循环流动,配合烧嘴安装位置角度,对炉气具有搅拌作用,增强了装置内的对流传热,装置底部设有垫铁,铸坯之间堆放时有间隙,提高了铸坯之间温度均匀性。与烧嘴向对的墙面下部设有若干排烟口6,排烟口6通过烟道9将炉内烟气排出,烟道9有调节阀,可通过调节各个排烟口开口度大小来控制炉内烟气流动。该退火装置采用一套控制系统实现全炉热工控制功能。设置系统的上位机,缓冷坑旁边设操作柜,可以进行各种参数设定和控制。在退火装置四周的墙壁上设有温度传感器,可实时检测退火装置内的空气温度,并将温度信号传递给控制系统,控制系统可根据设定情况进行烟道开口度及烧嘴燃烧强度的控制调节。一种合金钢大圆坯的退火方法,所述方法包括以下步骤:连铸生产7炉断面h13,铸坯定尺5.32m。连铸开浇后,退火装置开始点火预热,预热温度设定为600℃。2.5小时后,第一支铸坯火切完毕,停止预热,打开炉盖,通过行车将铸坯吊运至退火装置内,第一层铸坯间隔10cm,整个吊运过程持续5.6小时,铸坯装入完毕后,盖上炉盖,此时炉内温度显示为480℃,按照25度/h的速度开始升温至780℃,保温25h,保温完成后,关闭烧嘴,烟道开口度调整为25%,开始降温,20h小时后,炉内温度650℃,烟道开口度调整为80%,48h后,炉内温度为145℃。打开炉盖,将铸坯吊运至铸坯存放区,按炉号取样检测硬度。检测数值见下表。表1铸坯硬度检测炉号1234567硬度/hb222218220225216220224从表1可以看出,采用本发明的装置和方法,不同炉的硬度基本一致,方法简单,结果稳定。本发明的工艺参数(如温度、时间等)区间上下限取值以及区间值都能实现本法,在此不一一列举实施例。本发明未详细说明的内容均可采用本领域的常规技术知识。最后所应说明的是,以上实施例仅用以说明本发明的技术方案而非限制。尽管参照实施例对本发明进行了详细说明,本领域的普通技术人员应该理解,对本发明的技术方案进行修改或者等同替换,都不脱离本发明技术方案的精神和范围,其均应涵盖在本发明的权利要求范围当中。当前第1页12