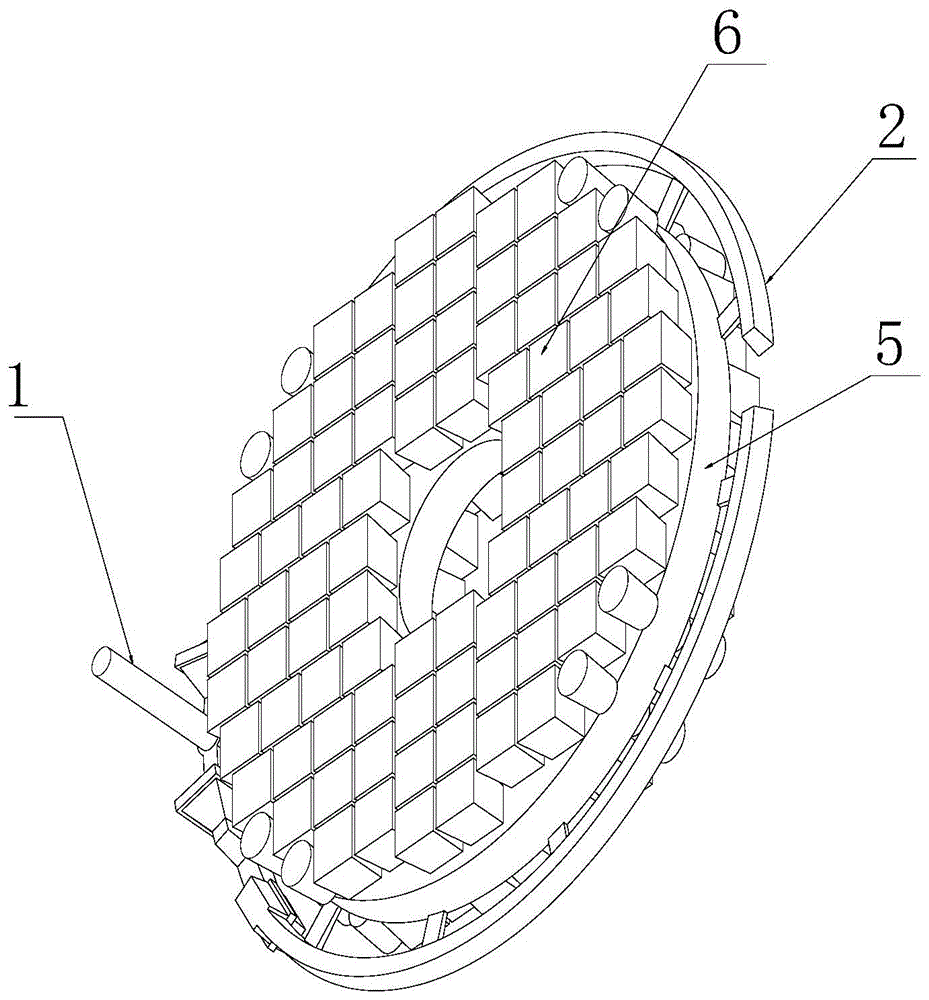
本发明属于球墨铸铁领域,具体涉及一种铸态球墨铸铁磨盘及其浇注系统和生产工艺。
背景技术:
:本申请人在先申请cn201710078216.3公开了一种球墨铸铁轧辊辊身,包括以下重量百分比组分:c:3.85-3.88%;si:1.80-1.90%;mn≤0.10%;p≤0.020%;s≤0.010%;mo:0.35-0.50%;ni:0.70-0.85%;ti≤0.025%;cr+pb+v≤0.020%;re:0.0030-0.0050%;mg:0.030-0.045%以及余量铁和不可除杂质。其解决了现有技术中大尺寸球墨铸铁轧辊辊身容易出现缩松、缩孔、夹渣、夹砂和裂纹等铸造缺陷的问题。在说明书中记载:f直:f横:f内=1:0.95:1。磨盘作为加工可视设备的蓝宝石面板、电子陶瓷和太阳能硅片等产品的一种工具,目前其材料品种较多,有灰铸铁、合金铸铁、球墨铸铁、合金钢、不锈钢等。随着球墨铸铁制造技术不断成熟,且因其具有优异的综合性能,逐步在磨盘上得到广泛应用。上述应用领域对于磨盘的要求需要达到:抗拉强度rm:382-395mpa,断后伸长率a:24-28%,硬度:135-150hb,且硬度差小于5hb。特别是硬度差小于5hb是现在球墨铸铁领域中难于达到的指标。参考本申请人在先专利cn201610824533.0公开了一种合金球墨铸铁轧辊,由以下组分组成:c:3.50~3.60wt%;si:2.1~2.3wt%;mn:0.5~0.8wt%;cr:0.2~0.3wt%;mo:0.4~0.6wt%;cu:0.7~0.8wt%;sb:0.006~0.009wt%;p:≤0.030wt%;s:≤0.010wt%;re:≤0.010wt%;mg:0.035~0.045%,余量铁以及不可除杂质;该专利最大创新点之一是控制轧辊表面硬度任意点间的硬度值相差不大于20hbw。所以,可以理解的,显著的、可靠的提高硬度差是很难的,但是对于上述的应用领域来说又是必须的。这是一个厄待解决的问题。技术实现要素:本发明的目的在于提供一种铸态球墨铸铁磨盘的浇注系统,本浇注系统的最核心的优势在于:所生产的铸铁磨盘硬度差小于5hb。在进一步的改进的技术方案中,进一步的技术效果为:该浇注系统配合传统的配方和工艺,适于生产抗拉强度rm:382-395mpa,断后伸长率a:24-28%,硬度:135-150hb,且硬度差小于5hb的球墨铸铁。同时,本发明还公开了该工艺和该铸态球墨铸铁磨盘。为实现上述目的,本发明提供如下技术方案:一种铸态球墨铸铁磨盘的浇注系统,包括铸模和与铸模配合的浇道单元;所述的浇道单元为环形的浇道单元;所述的铸模内设有位于待加工的磨盘铸件上下表面的冷铁;所述的冷铁的厚度为待加工的磨盘铸件厚度的75%-80%;冷铁之间的间隙为10-15mm。在上述的铸态球墨铸铁磨盘的浇注系统中,所述的冷铁包括方形冷铁和圆形冷铁,所述的圆形冷铁布置在待加工的磨盘铸件的边缘填充方形冷铁不能填充的区域。当磨盘铸件较小时,可以全部采用圆形冷铁。在上述的铸态球墨铸铁磨盘的浇注系统中,所述的浇道单元包括依次连接的直浇道、横浇道、内浇道,所述的横浇道为环形。在上述的铸态球墨铸铁磨盘的浇注系统中,所述的直浇道、横浇道、内浇道的横截面积比为:f直:f横:f内=1:1.55~1.75:1.80~1.90。在上述的铸态球墨铸铁磨盘的浇注系统中,所述的浇道单元还包括位于直浇道两侧的过滤器。二级过滤器的优点在于可以将球化处理后的一次夹渣物和浇注过程产生的夹渣物完全过滤。在上述的铸态球墨铸铁磨盘的浇注系统中,所述的铸模的材料为呋喃树脂砂,砂型强度:2h后达到1.0mpa以上,24h后达到2.5mpa以上。此外,本发明还提供一种铸态球墨铸铁磨盘的生产工艺,采用如上任意所述的浇注系统加工,所述的方法具体为:将铁水和硫氧孕育剂通过浇道单元浇注到铸模中,浇注温度:1355-1375℃,浇注速度:63-68kg/秒;铁水的化学成分的重量百分比(%)组分为:c:3.83-3.88;si:1.57-1.67;mn≤0.12;p≤0.020;s:0.005-0.011;la:0.0045-0.0055;mg:0.030-0.040;硫氧孕育剂占原料总重的0.2%。铸模的加工方法为:a)根据磨盘的厚度制造冷铁,材质为ht150;b)按照磨盘的图纸尺寸和浇注系统比例制作木质模具;c)模具经检验合格后,制作材料为呋喃树脂的铸模,其中冷铁按规定布置。在上述的铸态球墨铸铁磨盘的生产工艺中,浇注时倾斜15-25度。此外,本发明还提供一种铸态球墨铸铁磨盘,采用如上所述的方法制备得到。在上述的铸态球墨铸铁磨盘中,所述的铸态球墨铸铁磨盘的最终化学成分的重量百分比(%)组分为:c:3.83-3.88;si:1.70-1.80;mn≤0.12;p≤0.020;s:0.005-0.011;la:0.0045-0.0055;mg:0.030-0.040。与现有技术相比,本发明的有益效果是:通过本发明的浇注系统加工得到的铸件铸态实体硬度差小于5hb。更进一步改进,通过本发明的浇注系统加工得到的铸件铸态实体达到以下技术要求:基体组织100%铁素体;抗拉强度rm:382-395mpa,断后伸长率a:24-28%,硬度:135-150hb,且硬度差小于5hb;超声波探伤达到en12680-3:2012的1级。附图说明图1为本发明的实施例1的浇注系统的结构示意图;图2为本发明的实施例1的浇道单元的结构示意图;图3为本发明的实施例1的磨盘实体硬度检测点示意图。具体实施方式下面将结合本发明实施例中的附图,对本发明实施例中的技术方案进行清楚、完整地描述,显然,所描述的实施例仅仅是本发明一部分实施例,而不是全部的实施例。基于本发明中的实施例,本领域普通技术人员在没有做出创造性劳动前提下所获得的所有其他实施例,都属于本发明保护的范围。在论述本实施例和对比例之前,先将实施例和对比例所用的浇道单元和浇注系统予以阐述。具体来说,参考图2,所述的浇道单元为环形的浇道单元,包括依次连接的直浇道1、横浇道2、内浇道3,所述的横浇道为环形;所述的浇道单元还包括位于直浇道两侧的过滤器4,过滤器4为两级过滤系统。如图2所示。直浇道1、横浇道2、内浇道3的横截面积比为:f直:f横:f内=1:1.55~1.75:1.80~1.90。具体的数据选择请参考实施例1-4。参考图1,本实施例1-4所述的浇注系统,其包括如上所述的浇道单元以及和浇道单元配合的铸模,所述的铸模(附图未示出)内设有位于待加工的磨盘铸件5上下表面的冷铁6;铸模的材料为呋喃树脂砂,8字形砂型强度:2h后达到1.0mpa以上,24h后达到2.5mpa以上;铸模的加工方法为:a)根据磨盘的厚度制造冷铁,材质为ht150;b)按照磨盘的图纸尺寸和浇注系统比例制作木质模具;c)模具经检验合格后,制作材料为呋喃树脂的铸模,其中冷铁按规定布置。冷铁6的形状根据磨盘铸件5的规格进行设置,冷铁6包括方形冷铁和圆形冷铁,所述的圆形冷铁布置在待加工的磨盘铸件的边缘填充方形冷铁不能填充的区域;冷铁6还需要满足的设计需求为:冷铁的厚度为待加工的磨盘铸件厚度的75%-80%;冷铁之间的间隙为10-15mm。实施例1待加工的磨盘铸件的尺寸为:外圆直径φ1000mm,内孔直径φ226mm,厚度155mm;冷铁厚度为117mm,冷铁间的间隙为15mm;浇注系统的直浇道、横浇道、内浇道的横截面积比为:f直:f横:f内=1:1.55:1.80;按上述尺寸完成铸模,浇注时铸型(即上文所述铸模,下同)倾斜15度;铸态球墨铸铁磨盘的最终化学成分的重量百分比(%)组分为:c:3.83;si:1.70;mn:0.10;p:0.017;s:0.008;la:0.0045;mg:0.030。得到的铸件铸态实体达到以下技术要求:基体组织100%铁素体;抗拉强度rm:382mpa,断后伸长率a:28%,硬度(表1、2所示):138-143hb,硬度差小于5hb;超声波探伤达到en12680-3:2012的1级。加工过程为:将铁水通过浇道单元浇注到铸模中,浇注温度:1355℃,浇注速度:65kg/秒。铁水的组分和上述的铸态球墨铸铁磨盘的最终化学成分基本一致,只是si的用量略微少一些,大致少0.13%,在浇注的过程中还需向铁水中加入占原料总重0.2%的硫氧孕育剂,以致铸铁磨盘的si含量会略高于铁水中的si含量,在浇注过程进行随流孕育,起强化孕育效果,s、o可以增加形核核心,从而达到增加石墨球数量,提高球化率,同时强化孕育可提高基体中铁素体含量。在本实施例中,在球墨铸铁加工领域中任何可选的硫氧孕育剂都是可选的和符合本发明的最终性能要求的,本实施例不做过多的限制,具体到本实施例中,硫氧孕育剂的重量百分比(%)组分为si:74.4;ca:1.12;ce:2.95,al:0.71;s、o适量,余fe;粒度:0.2-0.7mm。磨盘采样位置见图3,每个标号的位置从内而外采样三个点。表1磨盘上面的硬度值(单位:hb)检测位置12345678内139138141142138138143140中138140143141143140141141外142141138140139142141140表2磨盘下面的硬度值(单位:hb)检测位置12345678内143142138141143142141143中138141139140139138141139外140141138140143139142143实施例2待加工的磨盘铸件的尺寸为:外圆直径φ1000mm,内孔直径φ226mm,厚度155mm;冷铁厚度为117mm,冷铁间的间隙为15mm;浇注系统的直浇道、横浇道、内浇道的横截面积比为:f直:f横:f内=1:1.55:1.80;按上述尺寸完成铸模,浇注时铸型倾斜15度;铸态球墨铸铁磨盘的最终化学成分的重量百分比(%)组分为:c:3.83;si:1.70;mn:0.10;p:0.017;s:0.008;la:0.0045;mg:0.030。得到的铸件铸态实体达到以下技术要求:基体组织100%铁素体;抗拉强度rm:385mpa,断后伸长率a:27.5%,硬度(表3、4所示):135-139hb,硬度差小于5hb;超声波探伤达到en12680-3:2012的1级。加工过程为:将铁水通过浇道单元浇注到铸模中,浇注温度:1375℃,浇注速度:63kg/秒。铁水的组分和上述的铸态球墨铸铁磨盘的最终化学成分基本一致,只是si的用量略微少一些,大致少0.13%,在浇注的过程中还需向铁水中加入占原料总重0.2%的硫氧孕育剂,以致铸铁磨盘的si含量会略高于铁水中的si含量。磨盘采样位置见图3,每个标号的位置从内而外采样三个点。表3磨盘上面的硬度值(单位:hb)检测位置12345678内136137138135136137135138中135137139135137139135138外138135139136138139137138表4磨盘下面的硬度值(单位:hb)检测位置12345678内138137139139137136135137中135137139135138139135137外136135137135138139136138实施例3待加工的磨盘铸件的尺寸为:外圆直径φ1727mm,内孔直径φ468mm,厚度186mm;冷铁厚度为149mm,冷铁间的间隙为10mm;浇注系统的直浇道、横浇道、内浇道的横截面积比为:f直:f横:f内=1:1.75:1.90;按上述尺寸完成铸模,浇注时铸型倾斜20度;铸态球墨铸铁磨盘的最终化学成分的重量百分比(%)组分为:c:3.88;si:1.80;mn:0.08;p:0.018;s:0.010;la:0.0055;mg:0.040。得到的铸件铸态实体达到以下技术要求:基体组织100%铁素体;抗拉强度rm:395mpa,断后伸长率a:24%,硬度(表5、6所示):146-150hb,硬度差小于5hb;超声波探伤达到en12680-3:2012的1级。加工过程为:将铁水通过浇道单元浇注到铸模中,浇注温度:1365℃,浇注速度:68kg/秒。铁水的组分和上述的铸态球墨铸铁磨盘的最终化学成分基本一致,只是si的用量略微少一些,大致少0.13%,,在浇注的过程中还需向铁水中加入占原料总重0.2%的硫氧孕育剂,以致铸铁磨盘的si含量会略高于铁水中的si含量。磨盘采样位置见图3,每个标号的位置从内而外采样三个点。表5磨盘上面的硬度值(单位:hb)检测位置12345678内149148149146149146147149中150146148147149146148148外149146146146147146148150表6磨盘下面的硬度值(单位:hb)实施例4待加工的磨盘铸件的尺寸为:外圆直径φ2084mm,内孔直径φ582mm,厚度202mm;冷铁厚度为160mm,冷铁间的间隙为15mm;浇注系统的直浇道、横浇道、内浇道的横截面积比为:f直:f横:f内=1:1.65:1.85;按上述尺寸完成铸模,浇注时铸型倾斜25度;铸态球墨铸铁磨盘的最终化学成分的重量百分比(%)组分为:c:3.85;si:1.75;mn:0.11;p:0.019;s:0.009;la:0.0050;mg:0.035。得到的铸件铸态实体达到以下技术要求:基体组织100%铁素体;抗拉强度rm:392mpa,断后伸长率a:25.1%,硬度(表7、8所示):139-144hb,硬度差小于5hb;超声波探伤达到en12680-3:2012的1级。加工过程为:将铁水通过浇道单元浇注到铸模中,浇注温度:1368℃,浇注速度:66kg/秒。铁水的组分和上述的铸态球墨铸铁磨盘的最终化学成分基本一致,只是si的用量略微少一些,大致少0.13%,,在浇注的过程中还需向铁水中加入占原料总重0.2%的硫氧孕育剂,以致铸铁磨盘的si含量会略高于铁水中的si含量。磨盘采样位置见图3,每个标号的位置从内而外采样三个点。表7磨盘上面的硬度值(单位:hb)表8磨盘下面的硬度值(单位:hb)检测位置12345678内144139141140141139142141中144139141144143144143139外142143142142143139142144对比例1待加工的磨盘铸件浇注系统的直浇道、横浇道、内浇道的横截面积比为:f直:f横:f内=1:1.45:1.75,余同实施例1。得到的铸件铸态实体技术要求中:抗拉强度、断后伸长率、硬度、硬度差与实施例1基本一致;但超声波探伤结果为en12680-3:2012的3级。产生上述结果的主要原因:铁液充型过程不平稳,产生二次夹渣物(氧化镁、氧化稀土和两者的氧化混合),且这些夹渣物尺寸较小,因磨盘铸件上下面冷却速度非常快,这些夹渣物在磨盘铸件的心部,超声波探伤检测可发现,其结果无法达到en12680-3:2012的1级。对比例2待加工的磨盘铸件上下、面冷铁间的间隙20mm,余同实施例2。得到的铸件铸态实体技术要求中:抗拉强度、断后伸长率、超声波探伤结果与实施例1基本一致;但硬度(表9、10所示):135-146hb,硬度差为12hb。表9磨盘上面的硬度值(单位:hb)表10磨盘下面的硬度值(单位:hb)检测位置12345678内146139142143146138144142中144138141135139145143140外137139138135144139143146对比例3待加工的磨盘铸件浇注时铸型水平放置,余同实施例3。得到的铸件铸态实体技术要求中:抗拉强度、断后伸长率与实施例3基本一致;但硬度(表11、12所示):146-153hb,硬度差为8hb;超声波探伤结果为en12680-3:2012的2级。表11磨盘上面的硬度值(单位:hb)检测位置12345678内152148151146149146150149中150146148147150149148151外149146153146152148153150表12磨盘下面的硬度值(单位:hb)检测位置12345678内151152148152148149148152中150150149149146148149150外148153146151148152153153通过上述的实施例1-4以及对比例1-3可以发现:1、浇道单元的参数不会对产品的硬度误差造成明显影响,但是会对产品的内部损伤(如氧加夹渣物存在)有一定的影响,具体参考对比例1。2、冷铁的布置、厚度选择会对产品的硬度误差造成明显的影响,在生产过程中应当严格把冷铁的参数控制在该误差范围,具体参考对比例2。3、铸型的放置角度可以改善硬度差的误差范围,但是如果角度进一步如实施例1-4,则效果更好。尽管已经示出和描述了本发明的实施例,对于本领域的普通技术人员而言,可以理解在不脱离本发明的原理和精神的情况下可以对这些实施例进行多种变化、修改、替换和变型,本发明的范围由所附权利要求及其等同物限定。当前第1页12