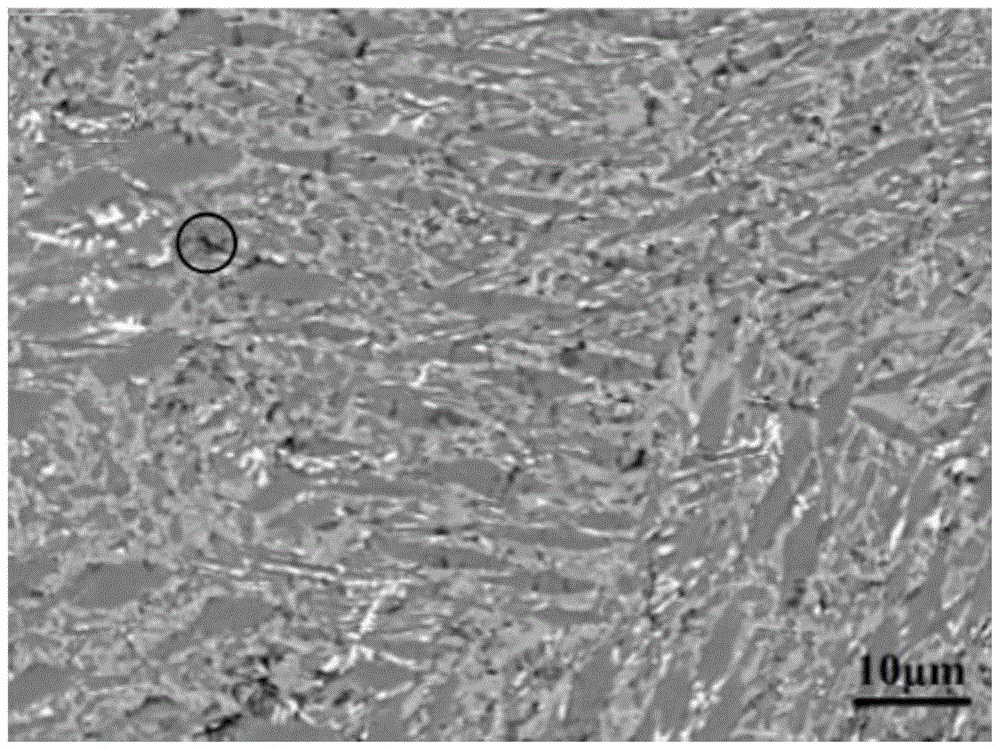
本发明涉及一种钢渣处理方法,特别是一种提高钢渣中铁回收率的钢渣处理方法。
背景技术:
:钢渣是炼钢过程产生的副产品,其排放量巨大,长期以来未得到有效利用。堆砌放置的钢渣不仅严重占用有限的土地资源,污染水与土壤,同时也是一种巨大的资源浪费。一方面钢渣中含有部分胶凝矿物,可作为水泥混凝土的部分原料使用;另一方面,钢渣中还存在含量较高的氧化亚铁及一定质量的游离氧化钙和氧化镁,氧化亚铁无法通过磁选直接分离且易引起钢渣水泥强度降低。铁在钢渣中一般以feo、fe2o3及单质fe的形式存在,并且占据了相当大的比例(质量百分比10-25%),颗粒较大的单质fe可以经磁选分离,而弱磁性的feo、fe2o3和小部分单质fe在磁选后依然存在于尾渣中。直接放弃尾渣中的这部分铁是对资源的极大浪费,同时铁氧化物的存在会导致尾渣易磨性变差,使得尾渣作为水泥、陶瓷等原料在应用过程中受到限制。因而尾渣中铁的回收,对于钢渣再利用、节约企业资源、降低环境污染、增加企业经济效益等方面都有着长远的现实意义。基于氧化法的研究基础,目前提出了转炉钢渣的固相改质工艺,通过对冷态钢渣在空气中进行煅烧,使钢渣中铁氧化物和氧化镁向强磁性镁铁尖晶石发生转变,强磁性镁铁尖晶石可通过磁选分离,钢渣经过固相改质形成镁铁尖晶石的工艺整个过程中不会排放产生温室效应的气体。然而在转炉钢渣的固相改质过程中,由于转炉钢渣难以与空气中的氧气充分接触造成钢渣铁氧化物和氧化镁向强磁性镁铁尖晶石的转变不够充分,进而造成钢渣中的铁回收率较低。技术实现要素:转炉钢渣的固相改质工艺是采取氧化气氛下煅烧钢渣的方式,以完成钢渣原矿中非磁性氧化亚铁和氧化镁向磁性富铁相聚集的转变,钢渣表面必须存在足够大的孔洞才能保证氧分子能够进入产物层深处与剩余反应物结合。在现有的转炉钢渣的固相改质工艺过程中,由于转炉钢渣难以与空气中的氧气充分接触造成钢渣铁氧化物和氧化镁向强磁性镁铁尖晶石的转变不够充分,进而造成钢渣中的铁回收率较低。本发明的目的在于提供一种提高钢渣中铁回收率的钢渣处理方法,通过在对钢渣进行固相改质前进行预处理,向熔融状态下的原钢渣通入氮气的同时进行冷却并在冷却后进行液氮低温粉碎和研磨,以提高钢渣中的孔隙率、孔隙大小和比表面积,使钢渣在进行固相改质时,空气中的氧气能够和钢渣内部充分接触,从而使强磁性镁铁尖晶石的转变更加充分,进而提高钢渣中的铁回收率。本发明的目的是通过以下技术方案来实现的:一种提高钢渣中铁回收率的钢渣处理方法,其特征在于:第一步,对原钢渣进行预熔融处理,在惰性气体保护下加热原钢渣使原钢渣完全熔融,随后向熔融的原钢渣中通入氮气,通入氮气的同时对熔融的原钢渣进行冷却至室温;第二步,对第一步中得到的预熔融处理钢渣进行液氮低温粉碎处理,粉碎并进一步研磨至钢渣粒径小于0.1mm;第三步,将第二步中液氮低温粉碎并研磨后的钢渣在高温下通入空气煅烧以进行固相改质处理。一种提高钢渣中铁回收率的钢渣处理方法,其特征在于:所述第一步处理向熔融的原钢渣中通入氮气的速度为4-6l/min。一种提高钢渣中铁回收率的钢渣处理方法,其特征在于:所述第一步处理中的惰性气体为氩气。一种提高钢渣中铁回收率的钢渣处理方法,其特征在于:所述第一步处理中将原钢渣加热至1500℃从而完全熔融。一种提高钢渣中铁回收率的钢渣处理方法,其特征在于:所述第一步处理中通入氮气的同时以10℃/min的冷却速度对熔融的原钢渣进行冷却至室温。一种提高钢渣中铁回收率的钢渣处理方法,其特征在于:所述第三步固相改质处理具体是将第二步中液氮低温粉碎并研磨后的钢渣松装于氧化铝坩埚并置于高温箱式马弗炉内,马弗炉内预先通入氮气以确保炉内没有空气存在,设定升温速率,当达到设定的温度时将氮气切换为空气,监控并调节空气通入速率,保温一定时间后将空气重新切换为氮气并快速冷却至室温。一种提高钢渣中铁回收率的钢渣处理方法,其特征在于:第三步处理中所述升温速率为10℃/min。一种提高钢渣中铁回收率的钢渣处理方法,其特征在于:第三步处理中所述设定的温度为1100℃。一种提高钢渣中铁回收率的钢渣处理方法,其特征在于:第三步处理中通过lzb玻璃转子流量计监控空气通入速率。一种提高钢渣中铁回收率的钢渣处理方法,其特征在于:第三步处理中所述空气通入速率为7.5l/min。本发明具有以下优点:钢渣经过通气预熔融处理和液氮体温粉碎研磨处理的预处理步骤再进行固相改质,能够有效提高钢渣中的孔隙率并增大孔隙内径,同时以高的比表面积状态与氧气充分接触,从而使钢渣在固相改质时空气中的氧气能够深入钢渣内部充分反应,冷态钢渣在空气中进行煅烧,促使钢渣中铁氧化物和氧化镁向强磁性镁铁尖晶石转变更加充分,进而使处理后的钢渣在磁选时铁回收率得到提高,钢渣中的铁、镁杂质转变为强磁性镁铁尖晶石后,钢渣的易磨性能够达到更为理想的水平,同时尾渣作为水泥应用时强度能够得到很大程度上的提高,附图说明图1为实施例2中处理后的钢渣显微组织形貌;图2为实施例4中处理后的钢渣显微组织形貌。图中:圆圈处的黑点为多个孔隙中的一个。具体实施方式实施例1第一步,对原钢渣进行预熔融处理,取50g原钢渣松装入容积为100ml的氧化铝坩埚中,置于高温箱式马弗炉内,通过rh/pt标准热电偶测温,炉内温度通过可编程调节器控制,精度为±3℃。在氩气保护下首先加热至1500℃使原钢渣完全熔融,随后向熔融的原钢渣中以4l/min的速度通入氮气,通入氮气的同时以10℃/min的冷却速度对熔融的原钢渣进行冷却至室温。第二步,对第一步中得到的预熔融处理钢渣进行液氮低温粉碎处理,粉碎并进一步研磨至钢渣粒径小于0.1mm。第三步,将第二步中液氮低温粉碎并研磨后的钢渣松装于氧化铝坩埚,并置于高温箱式马弗炉内,马弗炉内预先通入氮气以确保炉内没有空气存在,升温速率设定为10℃/min,当到达1100℃时,将氮气切换为空气,通过lzb玻璃转子流量计监控空气通入速率,调节空气通入速率为7.5l/min,保温30min后,将空气重新切换为氮气并快速冷却至室温。实施例2第一步,对原钢渣进行预熔融处理,取50g原钢渣松装入容积为100ml的氧化铝坩埚中,置于高温箱式马弗炉内,通过rh/pt标准热电偶测温,炉内温度通过可编程调节器控制,精度为±3℃。在氩气保护下首先加热至1500℃使原钢渣完全熔融,随后向熔融的原钢渣中以5l/min的速度通入氮气,通入氮气的同时以10℃/min的冷却速度对熔融的原钢渣进行冷却至室温。第二步,对第一步中得到的预熔融处理钢渣进行液氮低温粉碎处理,粉碎并进一步研磨至钢渣粒径小于0.1mm。第三步,将第二步中液氮低温粉碎并研磨后的钢渣松装于氧化铝坩埚,并置于高温箱式马弗炉内,马弗炉内预先通入氮气以确保炉内没有空气存在,升温速率设定为10℃/min,当到达1100℃时,将氮气切换为空气,通过lzb玻璃转子流量计监控空气通入速率,调节空气通入速率为7.5l/min,保温30min后,将空气重新切换为氮气并快速冷却至室温。实施例3第一步,对原钢渣进行预熔融处理,取50g原钢渣松装入容积为100ml的氧化铝坩埚中,置于高温箱式马弗炉内,通过rh/pt标准热电偶测温,炉内温度通过可编程调节器控制,精度为±3℃。在氩气保护下首先加热至1500℃使原钢渣完全熔融,随后向熔融的原钢渣中以6l/min的速度通入氮气,通入氮气的同时以10℃/min的冷却速度对熔融的原钢渣进行冷却至室温。第二步,对第一步中得到的预熔融处理钢渣进行液氮低温粉碎处理,粉碎并进一步研磨至钢渣粒径小于0.1mm。第三步,将第二步中液氮低温粉碎并研磨后的钢渣松装于氧化铝坩埚,并置于高温箱式马弗炉内,马弗炉内预先通入氮气以确保炉内没有空气存在,升温速率设定为10℃/min,当到达1100℃时,将氮气切换为空气,通过lzb玻璃转子流量计监控空气通入速率,调节空气通入速率为7.5l/min,保温30min后,将空气重新切换为氮气并快速冷却至室温。实施例4称取50g原钢渣松装于氧化铝坩埚,并置于高温箱式马弗炉内,马弗炉内预先通入氮气以确保炉内没有空气存在,升温速率设定为10℃/min,当到达1100℃时,将氮气切换为空气,通过lzb玻璃转子流量计监控空气通入速率,调节空气通入速率为7.5l/min,保温30min后,将空气重新切换为氮气并快速冷却至室温。对原钢渣和固相改质钢渣分别进行湿式磁选,湿式磁选效果可通过磁感应强度在0.1t时的磁选回收率进行评价。回收率b(%)表示精矿所含fe与原矿所含fe的质量比。回收率:b=((qx×β)/(q。×α))×100%其中:q。表示原矿质量(t);qx表示精矿质量(t);α表示原矿品位(%);β表示精矿品位(%)。样品回收率b实施例171.2%实施例275.3%实施例372.5%实施例462.6%从图1和图2所示的钢渣显微组织形貌可以看出,通过在对钢渣进行固相改质前进行预处理,向熔融状态下的原钢渣通入氮气的同时进行冷却并在冷却后进行液氮低温粉碎和研磨,经过上述处理后的钢渣从微观形貌上观察,其孔隙大小和数量都远远高于未经过上述预处理而直接进行固相改质的钢渣。从磁选回收率的角度来看,经过预处理的钢渣中铁回收率明显高于没有经过预处理的钢渣,从另一个角度可以说明经过预处理而孔隙率提高孔径增大的钢渣能够更充分地形成强磁性镁铁尖晶石,从而使钢渣中的铁回收率得到提高。以上所述仅是本发明的优选实施方式,应当理解本发明并非局限于本文所披露的形式,不应看作是对其他实施例的排除,而可用于各种其他组合、修改和环境,并能够在本文所述构想范围内,通过上述教导或相关领域的技术或知识进行改动。而本领域人员所进行的改动和变化不脱离本发明的精神和范围,则都应在本发明所附权利要求的保护范围内。当前第1页1 2 3