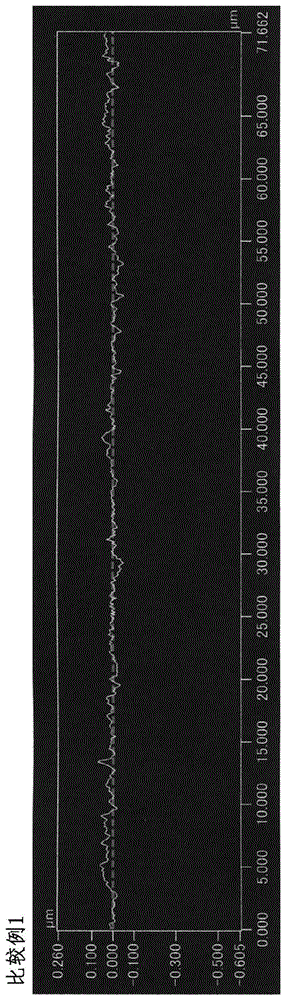
本发明涉及涂有类金刚石碳(dlc:diamond-likecarbon)膜的构件的表面处理方法,并且更具体地,涉及用于形成多个细小凹坑以便显示出诸如dlc涂层构件上的dlc膜的表面上的滑动阻力减小等有益效果的dlc涂层构件的表面处理方法。
背景技术:
:作为非晶(无定形)硬碳的dlc具有高硬度,具有优异的耐磨性,并且还具有诸如摩擦系数低和阻止其他材料粘附等特性。因此,用dlc膜涂覆切削工具的切削刃、滑动构件的滑动表面和模具空腔的内表面是用于表面改性的方法,其目的是改善耐磨性和滑动性、以及改善脱模性(demoldability)等。因此,涂有dlc膜的dlc涂层构件具有以下有益效果:摩擦系数低、优异的耐磨性、以及优异的脱模性等。然而,还提出了在dlc膜的表面上形成充当储油器等的多个细小凹坑,其目的是实现这种dlc涂层构件在降低摩擦系数和提高耐磨性方面的进一步改善,并且实现脱模性等的进一步改善。有人提出了一种用于形成这种凹坑的方法,在该方法中,例如,在形成dlc膜之前,在基材(basematerial)的表面上形成将变为这种凹坑的压痕。然后,通过在基材的表面上形成dlc膜,也会使形成在基材上的凹坑出现在dlc膜的表面上。然而,该方法会导致膜的质量不均匀,例如,dlc膜的膜厚度在隐藏于形成在基材上的压痕内部的部分处较薄而在突起处较厚。除此之外,这导致形成在dlc膜上的凹坑的轮廓不能精确地反映形成在基材上的压痕和突起的轮廓。这意味着:由于需要在基材上形成压痕和突起,因此在考虑到轮廓等的这种变化的同时,需要经验和直觉来在dlc膜上形成具有所需轮廓的凹坑。因此,提出了直接在dlc膜上形成凹坑而不在基材侧上形成压痕的方法。这种方法包括:在形成dlc膜的过程的同时形成凹坑的方法、以及在预先形成dlc膜之后通过后处理形成凹坑的方法。在日本专利申请特开(在下文中称为jp-a)第2004-339564号中公开了这些方法中的作为在形成dlc膜的过程的同时形成凹坑的方法的一种方法。该方法使用如下的非平衡磁控溅射(unbalancedmagnetronsputtering):其中,在dlc膜形成期间调节施加到基材侧的偏压,以便能够在由此获得的dlc膜的表面上形成细小凹坑(参见jp-a第2004-339564号中的权利要求4和5)。在jp-a第2006-38000号中还公开了一种如下的方法:其中,在形成dlc膜之后,通过使用等离子体蚀刻、聚焦离子束或激光处理的后处理来形成凹坑。在jp-a第2005-193390号中还公开了一种如下的方法:其中,通过使用聚焦离子束部分地去除dlc涂层来形成凹坑(参见jp-a第2006-38000号中的权利要求4和6等以及jp-a第2005-193390号中的权利要求4)。此外,在下面描述的jp-a第2010-126419号中还公开了一种用于在形成dlc膜之后通过后处理形成凹坑的单独的方法。在该方法中,通过将由陶瓷材料等制成的细小颗粒高速喷射到dlc膜的表面上以便引起dlc膜的细小尺寸的剥离(detachment)并露出构成下层的基板的表面和中间层的表面来形成凹坑(参见jp-a第2010-126419号中的第[0016]段)(在下面描述的国际公开wo2017/169303中也提到了通过细小颗粒撞击dlc涂层构件来形成凹坑)。需要注意,尽管与dlc涂层构件的表面处理无关,但是本发明的申请人已经提交了与金属制品的表面处理方法有关的申请,该表面处理方法的目的是沿着由软质材料和硬质材料构成的金属制品的表面连续地形成均匀的纳米晶体结构。在这种方法中,在0.05mpa~0.5mpa的喷射压力下,将中位直径d50为1μm~20μm且穿过空气的下落时间不小于10s/m的大致球形的喷射颗粒喷射到金属制品上,以便通过微粉化成平均晶粒直径不大于300nm的纳米晶体并对金属制品的表面施加压缩残余应力,在从金属制品的表面到指定深度的区域中沿着金属制品的表面连续地形成均匀的纳米晶体结构(参见jp-a第2017-206761号中的权利要求1等)。从上述用于在dlc膜上形成凹坑的方法中,如在jp-a第2004-339564中所述的方法一样,从能够在不破坏或不损坏所形成的dlc膜的情况下形成凹坑的角度来看,在形成dlc膜的过程期间形成凹坑是优异的。然而,用于形成dlc膜的方法限于非平衡磁控溅射方法。在非平衡磁控溅射方法中,通过改变施加到基板的偏压来控制待形成的dlc膜的机械特性,例如平滑度、硬度等。因此,在jp-a2004-339564中所述的通过将偏压控制在指定范围内(150v~600v)而在dlc表面上形成压痕的方法中,由此获得的dlc膜的机械特性也受到限制,此外,为了在dlc膜的表面上形成所需尺寸的压痕而调节操作条件等也是繁琐的。与此相比,在已经形成dlc膜之后通过去除所形成的dlc膜的一部分来形成凹坑的方法中,不限于使用非平衡磁控溅射方法,并且在不限制用于形成dlc的方法的情况下,可以在已经通过诸如普通磁控溅射(平衡磁控溅射)、真空沉积、等离子体cvd等其他方法形成的各种dlc膜上形成凹坑。特别地,在jp-a第2010-126419号和国际公开wo2017/169303中所述的通过发射细小颗粒来形成凹坑的方法中,可以通过使用具有气动喷射等的喷射装置来形成凹坑(参见jp-a第2010-126419号中的第[0027]段),即,通过使用喷砂装置来形成凹坑(参见国际公开wo2017/169303中的第[0076]段)。因此,由于能够使用比jp-a第2006-38000号的通过等离子体蚀刻、聚焦离子束或激光处理来去除dlc膜或者jp-a第2005-193390号的通过使用聚焦离子束来去除dlc膜而形成凹坑的方法更简单的装置构造来形成凹坑,因此能够以低成本执行处理。然而,由于根据这两种方法形成凹坑是通过对已经形成的dlc膜执行小尺寸的去除或剥离的构造而实现的,即,由于dlc膜被损坏而形成凹坑,因此在形成凹坑的部分处容易产生dlc膜的进一步的裂缝或剥离。鉴于此,jp-a第2010-126419号描述了一种通过发射细小颗粒形成凹坑的方法,在该方法中,指出凹坑的总覆盖率不应超过总表面的10%,并且还指出如果所形成的凹坑超过该范围,则容易发生dlc膜的剥离(参见jp-a第2005-193390号中的第[0016]~[0017]段)。因此,该方法不能以能够充分显示使用凹坑来提高滑动性的功能的覆盖率(即,50%以上)来形成凹坑。本领域技术人员众所周知,dlc膜由于膜厚度薄且应力高而易碎,使得在受到强烈撞击时,dlc膜容易被破坏和剥离。因此,在jp-a第2010-126419号中,dlc膜的这种特性被用来通过使dlc膜在被细小颗粒撞击的部分处发生剥离来形成凹坑。因此,在该方法中,通过如上所述的对dlc膜赋予称为局部剥离的损坏的处理来形成凹坑。因此,以这种方式形成的凹坑的覆盖率不可避免地受到限制。然而,从能够通过使用已知的喷砂装置等相对便宜地形成凹坑的角度来看,通过发射细小颗粒形成凹坑的方法是优异的。因此,本发明的目的是提供dlc涂层构件的表面处理方法,该方法在能够通过细小颗粒的撞击相对简单地形成凹坑的同时,还能够在不发生dlc膜的局部剥离和基材的随之露出的情况下在dlc膜的表面上形成凹坑,并且该方法能够形成凹坑,使得总投影面积(totalprojectedarea)不小于处理区域的50%,从而能够赋予诸如改善的滑动性等功能。技术实现要素:为了实现该目的,本发明的dlc涂层构件的表面处理方法包括:将dlc涂层构件当作处理对象,所述dlc涂层构件具有涂在基材表面上的dlc膜;以0.01mpa~0.7mpa的喷射压力,将中位直径d50为1μm~20μm且穿过空气的下落时间不小于10s/m的大致球形的喷射颗粒喷射到所述dlc涂层构件的所述dlc膜的表面上;以及在不露出所述基材的情况下,在所述dlc膜的所述表面上形成凹坑,使得所述凹坑的总投影面积不小于处理区域的50%,并且使得所述dlc膜的所述表面被加工成算术平均高度(sa)为0.01μm~0.1μm并且纹理纵横比(str)不小于0.4。在dlc涂层构件的表面处理方法中,所述喷射颗粒的喷射速度优选地不小于80m/s。在dlc涂层构件的表面处理方法中,所述处理对象优选地是在被平滑化至表面粗糙度ra不大于0.1μm的所述基材表面上形成有dlc膜的dlc涂层构件。如上所述的本发明的表面处理方法能够显示出以下显著的有益效果。即,迄今为止,在通过类似地喷射的细小颗粒的撞击而在dlc膜上形成凹坑的表面处理方法(jp-a第2010-126419号)中,通过dlc膜的局部破坏和剥离以露出基材而在dlc膜中形成凹坑。然而,在本发明的表面处理方法中,可以在dlc膜的表面上形成凹坑,而不会由于dlc膜的局部破坏而导致dlc膜的剥离和伴随的基材的露出。结果,即使在处理目标区域的表面上已经形成总投影面积不小于处理区域的50%的凹坑的情况下,本发明的方法也能够防止dlc膜在使用时发生剥离等。尽管本发明的表面处理方法能够形成凹坑而不会伴随有dlc膜的损坏和剥离的机制尚不完全清楚,但是本发明的方法中所使用的喷射颗粒很小,中位直径d50在1μm~20μm的范围内,并且喷射颗粒的质量很小,以便穿过空气的下落时间不小于10s/m。这意味着:当撞击dlc膜的表面时,应力局部地集中在受撞击的部分处并且集中在表面附近,以便不会穿透到与基材的界面。然而,如上所述限定的喷射颗粒易于被气流携带,并且可以以接近气流速度的速度推进。这使得喷射颗粒能够以与在喷射喷嘴内部流动的气流的流速相近的高速度喷射,例如,即使在大约0.01mpa的相对低的喷射压力下喷射时,也能够以不小于80m/s的速度喷射。以这种方式,尽管由于撞击期间的应力局部集中且没有到达更深的部分(与基材的界面)而可以防止dlc膜的剥离,但是由于以高速执行喷射,因此仍然能够获得高撞击能量。这被认为意味着可以通过细小颗粒撞击时的能量来提高dlc膜的密度,并且也可以通过由于撞击而同时发生的结构破坏的重建来提高dlc膜的密度,以便能够在不会导致dlc膜的损坏和剥离并且不会露出基材的情况下形成凹坑。附图说明根据结合附图提供的对本发明的优选实施例的详细描述,本发明的目的和优点将变得显而易见,其中:图1是通过激光显微镜测量的未处理的dlc涂层构件(比较例1)的表面粗糙度分布图。图2是通过激光显微镜测量的经过本发明的表面处理方法的dlc涂层构件(示例1)的表面粗糙度分布图。图3a和图3b是模具表面的电子显微照片:图3a是未处理的模具表面的电子显微照片(比较例1),并且图3b是经过本发明的表面处理方法的模具表面的电子显微照片(示例1)。具体实施方式以下是关于本发明的示例性实施例的说明。处理对象制品通过本发明的表面处理方法进行处理的对象具有涂有dlc膜的表面,并且还具有形成在该表面上的凹坑,以便显示出由于储油器、贮气器(airreservoir)、脱模剂容器(releaseagentreservoir)等而引起的滑动性改善和脱模性改善等有益效果。例如,使用本发明处理的对象可以是诸如切削工具的切削刃、滑动构件(例如轴承、轴等)的滑动表面和各种模具的模制表面等各种dlc涂层构件中的任何一种,该dlc涂层构件上形成有dlc膜,并且该dlc涂层构件还从在dlc膜的表面上形成凹坑中发现有益效果。dlc涂层构件不限于以dlc完全涂覆的构件,并且可以部分地涂有dlc。作为处理对象的dlc涂层构件的基材的材料没有特别限制,只要其是可以在其上形成dlc膜的材料即可。待处理的材料的示例包括诸如硬质合金、冷作模具钢、高速工具钢或不锈钢等各种金属基材,并且包括陶瓷基材。需要注意,在处理对象构件的表面上形成底层,然后在该底层的表面上形成dlc膜的情况下,该底层对应于本发明的基材。优选地,用作处理对象的dlc涂层构件是在基材表面上形成有dlc膜的处理对象,该基材表面被抛光成具有不大于0.1μm的表面粗糙度ra的镜面光洁度(mirrorfinish)。这是因为如果表面粗糙度ra超过0.1μm,则压痕和突起的尖端易于成为破裂的起点,使得当通过本发明进行处理时容易发生剥离。对用于在作为处理对象的dlc涂层构件上形成dlc膜的方法或形成的dlc膜的类型没有特别限制。经过本发明的处理的dlc膜可以是使用真空电弧沉积法形成的称为四面体非晶碳(ta-c)的高硬度无氢dlc膜,可以是通过溅射法等形成的称为非晶碳(a-c)的低硬度无氢dlc膜,可以是通过等离子体cvd(化学气相沉积)法等形成的称为氢化非晶碳(a-c:h)(其中,具有称为氢化四面体非晶碳(ta-c:h)的相对高硬度的膜)的含氢dlc膜。通过本发明处理的对象还可以是形成有金刚石结构(sp3键合)、石墨结构(sp2键合)或两者的混合结构的dlc膜。dlc膜的膜厚度为0.5μm~2.0μm。表面处理将大致球形的喷射颗粒喷射到将在上述的dlc涂层构件的表面上形成凹坑的区域上,以便撞击该区域。下面给出在执行上述表面处理时所使用的喷射颗粒、喷射装置和喷射条件的示例。(1)喷射颗粒对于在本发明的表面处理方法中使用的大致球形的喷射颗粒,“大致球形”意味着它们不需要是严格的“球形”,并且为此可以使用普通的“喷丸(shot)”。诸如椭圆形形状和桶形形状等任何无角形状的颗粒都包括在本发明中所使用的“大致球形的喷射颗粒”中。可用于喷射颗粒的材料包括金属基材料和陶瓷基材料。用于金属基喷射颗粒的材料的示例包括钢、高速工具钢(hss)(skh)、不锈钢(sus)和铬硼钢(fecrb)等。可用于陶瓷基喷射颗粒的材料的示例包括氧化铝(al2o3)、氧化锆(zro2)、锆石(zrsio4)、碳化硅(sic)和玻璃等。关于所使用的喷射颗粒的颗粒直径,使用中位直径(d50)在1μm~20μm的范围内的颗粒。“中位直径d50”是指在累积质量50%处的直径,即,当用作用于将一组颗粒分成两组的颗粒直径时会导致直径较大的一组颗粒中的颗粒的总质量与直径较小的一组颗粒中的颗粒的总质量相同的直径。这与jisr6001(1987)中的“累积50%点处的颗粒直径”的定义相同。该中位直径可以由激光衍射法测量。对于中位直径为1μm~20μm的细粉状喷射颗粒,通过选择喷射颗粒的材料密度,可以赋予喷射颗粒穿过空气(使喷射颗粒漂浮在空气中)的下落时间长的特性。具有这种特性的喷射颗粒易于乘在气流上,并且可以以与气流的流速相似的速度推进。在本发明的表面处理方法中,所使用的喷射颗粒在静止空气条件下具有不小于10s/m的下落时间。这使得喷射颗粒能够以与从喷砂装置的喷射喷嘴中喷射的气流的流速基本相同的速度喷射。关于下落速度,对于相同的颗粒直径,下落时间越长,构成喷射颗粒的材料的密度越低。对于相对密度为7.85的铁基喷射颗粒,对于20μm的颗粒直径,下落时间为10.6s/m,并且对于10μm的颗粒直径,下落时间为41.7s/m。对于相对密度为3.2的陶瓷基喷射颗粒,对于20μm的颗粒直径,下落时间为26.3s/m,并且对于10μm的颗粒直径,下落时间为100s/m。(2)喷射装置可以使用已知的用于将磨料与压缩气体一起喷射的喷砂装置作为喷射装置,以将上述的喷射颗粒朝向待处理区域的表面喷射。这种喷砂装置在市场上是可以买到的,例如,使用通过喷射压缩气体而产生的负压来喷射磨料的抽吸式喷砂装置、使从磨料箱下落的磨料由压缩气体携带并喷射的重力式喷砂装置、将压缩气体引入到填充有磨料的箱中且通过将来自磨料箱的磨料流与来自单独设置的压缩气体供应源的压缩气体流合并来喷射磨料的直压式喷砂装置、以及使用由鼓风机单元产生的气流来携带并喷射来自这种直压式喷砂装置的压缩气体流的鼓风机式喷砂装置。可以使用上述喷砂装置中的任何一种喷砂装置来喷射上述的喷射颗粒。(3)处理条件以0.01mpa~0.7mpa的喷射压力,将由上述材料等中的一种材料构成、中位直径d50为1μm~20μm、且穿过空气的下落时间不小于10s/m的大致球形的喷射颗粒喷射到如上所述的dlc涂层构件上,以便在不露出基材的情况下形成凹坑。对dlc膜的表面执行这种喷射颗粒的喷射,直到凹坑的总投影面积不小于处理区域的50%。需要注意,在本说明书中,“投影面积”是指凹坑的轮廓面积。此外,喷射喷射颗粒,使得处理后的dlc表面的表面粗糙度为由iso25178定义的算术平均高度sa,该算术平均高度sa位于0.01μm~0.1μm的范围内。此外,执行该处理,以便实现由iso25178定义的不小于0.4的纹理纵横比(textureaspectratio)str,从而将dlc膜的表面加工成非定向表面。操作等如上所述的本发明的表面处理方法能够在dlc膜上形成总投影面积不小于处理区域的50%的细小凹坑,而不会导致dlc膜剥离且因此不会露出基材。结果,利用本发明的方法进行的处理能够减小滑动期间的阻力。这是通过减小在dlc膜的表面上形成有细小凹坑的dlc涂层构件与相对构件之间的接触面积来实现的。此外,通过本发明的方法形成的dlc涂层构件的表面的压痕-突起轮廓是由平滑的压痕和突起主导的轮廓。这意味着压痕和突起的倾斜角度很浅,并且还实现了作用在突起上的摩擦力的减小。此外,由于形成了小直径的浅凹坑,因此,由于在滑动期间在dlc膜的表面上形成空气层而获得空气润滑效果,从而实现了滑动性的改善。此外,形成的凹坑还充当储油器,因此,在将润滑油涂抹到滑动部分和没有涂抹润滑油的两种情况下,也都可以实现滑动性的改善。示例接下来,将给出对已经通过本发明的方法执行了表面处理的dlc涂层构件和未处理的dlc涂层构件执行的比较测试的结果。如下所述,使用轮廓分析激光显微镜(由基恩士公司制造的vk-x250)测量粗糙度,并且在3000×的测量倍率下进行测量。基于这些分析结果,使用适用于该激光显微镜的分析软件(多文件分析应用程序vk-h1mx)计算由此获得的轮廓。测试示例1:铝罐成型拉延模(aluminum-can-formingdrawdie)(1)测试方法分别使用已经通过本发明的方法执行了表面处理的铝罐成型拉延模和未处理的铝罐成型拉延模来形成10,000个铝罐。在使用上述的铝罐成型拉延模形成罐之后,然后通过目测分别评估dlc膜从铝罐成型拉延模的表面剥离的状态和铝对铝罐成型拉延模的表面粘附的状态。(2)示例和比较例在将基材表面搭接抛光(lappolishing)至ra不大于0.02μm之后,通过在基材表面上形成膜厚度为0.5μm的dlc膜来制备硬质合金铝罐成型拉延模。然后,在表1中列出的条件下对模具表面进行本发明的表面处理方法(示例1~3)。然后,分别使用这些模具和未处理的硬质合金铝罐成型拉延模(比较例1)来形成铝罐。表1示例1~3和比较例1(3)评估结果使用上述的激光显微镜(由基恩士公司制造的vk-x250)进行测量,并且在图1(未处理:比较例1)和图2(本发明的表面处理:示例1)中图示了模具的各个表面粗糙度分布。在图3a中图示了针对未处理(比较例1)的对各个模具的表面进行成像的电子显微照片,并且在图3b中图示了针对本发明的表面处理(示例1)的对各个模具的表面进行成像的电子显微照片。此外,在形成示例1~3的铝罐成型拉延模和比较例1的铝罐成型拉延模的铝罐之后,通过目测dlc膜的剥离状态和铝粘附的状态来确认下表2中列出的结果。表2dlc膜的剥离状态和铝粘附的状态的确认结果示例1示例2示例3比较例1dlc膜的剥离无无无局部剥离铝粘附非常轻微非常轻微轻微明显从与图1所示的未处理模具(比较例1)的表面的比较可以明显看出,对于图2所示的经过本发明的表面处理的模具,可以确认在表面上形成有凹坑。这些凹坑形成到膜厚度为0.5μm的dlc上,并且这些凹坑全部形成为深度不大于0.2μm。因此,本发明的表面处理方法能够在dlc涂层构件的表面上形成凹坑而不露出模具的基材。这使得能够防止dlc膜以凹坑形成位置作为起点发生剥离,如已经引起dlc膜的局部剥离的情况一样。此外,从图2和图3b中显而易见,使用本发明的表面处理方法形成有凹坑的模具的表面轮廓主要是具有相对平滑轮廓的压痕和突起,从而实现在滑动期间作用在突起上的摩擦力减小。结果,尽管在使用没有通过本发明的方法进行表面处理的铝罐成型拉延模(比较例1)形成铝罐之后,发生了dlc膜的局部剥离和相对大的铝粘附,但是对于经过本发明的表面处理方法的铝罐成型拉延模(示例1~3),没有看到dlc膜的剥离,并且仅有非常轻微或轻微的铝粘附。因此,与未处理的dlc涂层构件相比,可以证实:通过本发明的方法进行表面处理来执行表面处理能够改善机械特性。测试示例2:轮廓冲头(profilepunch)(1)测试方法分别使用通过本发明的方法进行了表面处理的轮廓冲头和未处理的轮廓冲头将电气部件材料(黄铜材料)模切15,000次。然后,通过目测评估dlc膜与使用后的轮廓冲头的表面的剥离状态。(2)示例和比较例在将基材表面搭接抛光至ra不大于0.02μm之后,通过在基材表面上形成膜厚度为1.5μm的dlc膜来制备硬质合金轮廓冲头。然后,在表3中列出的条件下对硬质合金轮廓冲头进行本发明的表面处理方法(示例4~6)。然后,分别使用这些轮廓冲头和未处理的硬质合金轮廓冲头(比较例2)进行冲压。表3示例4~6和比较例2(3)评估结果在下表4中列出了观察到的示例4~6的轮廓冲头和比较例2的轮廓冲头的dlc膜的剥离状态的结果。表4dlc膜的剥离状态上述结果证实,在使用未经过本发明的表面处理方法的轮廓冲头切出电气部件材料之后,位于冲头前端的dlc膜发生剥离(比较例2)。与此相比,在通过本发明的方法进行了表面处理的轮廓冲头(示例4~6)的任何部分,包括在冲头的前端部分,都没有看到dlc膜的剥离。这可以证实:与未处理的dlc涂层构件相比,通过本发明的表面处理方法执行表面处理可以改善冲头的机械特性。测试示例3:部件输送轨道(1)测试方法分别使用通过本发明的方法进行了表面处理的部件输送轨道(示例7)和未处理的部件输送轨道(比较例3)输送部件。然后,通过目测确认在输送期间是否会卡住输送的部件。(2)示例和比较例在将基材表面搭接抛光至ra不大于0.02μm之后,通过在基材表面上形成膜厚度为1.5μm的dlc膜来制备由sus304制成的部件输送轨道。然后,在表5中列出的条件下对部件输送轨道进行本发明的表面处理方法(示例7)。然后,分别使用该部件输送轨道和未处理的部件输送轨道(比较例3)进行部件输送。表5示例7和比较例3(3)评估结果在下表6中列出了通过目测确认的示例7的部件输送轨道和比较例3的部件输送轨道输送的部件的卡住状态的结果。表6输送的部件的卡住示例7比较例3输送的部件的卡住无一些上述结果证实,使用未经过本发明的表面处理方法的部件输送轨道(比较例3)会发生输送的部件的卡住。在这些部分卡住被认为是由于dlc膜中产生的裂缝和剥离。与此相比,对于通过本发明的方法进行了表面处理的部件输送轨道(示例7),没有看到输送的部件的卡住,并且可以证实在dlc膜中没有产生裂缝和剥离,并且由此显示出良好的滑动性。因此,以下最广义的权利要求并不针对以特定方式构造的机器。相反,所述最广义的权利要求旨在保护该突破性发明的核心或本质。本发明明显是新的且有用的。此外,当整体考虑时,鉴于现有技术,在做出本发明时本发明对于本领域普通技术人员而言并不是显而易见的。此外,鉴于本发明的革命性,这明显是一项开创性发明。正因如此,根据法律,有权对以下权利要求进行非常广义的解释,以便保护本发明的核心。因此,可以看出,有效地获得了上述目的和根据前述描述显而易见的目的,并且由于在不脱离本发明的范围的情况下可以对上述结构进行某些改变,因此前述描述中所包含的或附图中所示的所有事项都应被解释为说明性的而不是限制性的。此外,应当理解,以下权利要求旨在涵盖本文中所述的本发明的所有一般和特定特征、以及在语言上可以说落入这些特征之中的本发明的范围的所有陈述。现在已经描述了本发明。当前第1页12