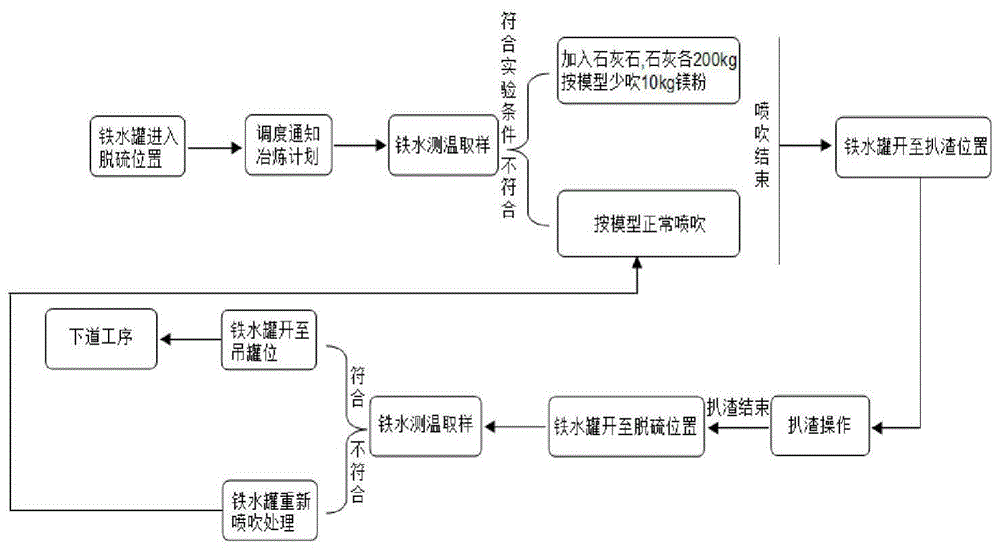
本发明涉及冶金
技术领域:
,具体是一种铁水脱硫方法。
背景技术:
:目前国内关于铁水脱硫主要有两种方式,一种是喷吹法,主要采用镁粉或镁粉+石灰粉混合喷吹工艺;另一种是近些年随着鱼雷罐运输及铁水罐保温后,随着到钢厂铁水温度的提升逐步推广使用的搅拌法,主要为kr法。喷吹法的优点是处理周期短,易与炉机匹配,由于脱硫产生的渣量偏少,渣中硫含量较高,扒渣不净易在转炉冶炼过程产生回硫现象,为了避免回硫,导致扒渣量大,扒损相对较高;kr法的优点是脱硫成本相对较低,但脱硫时间长,一座预处理站对一座转炉生产匹配有难度。有的钢厂单独为了考虑降成本,准备将现有喷吹法改为搅拌法,增加较大的设备投资,造成资产浪费。现有技术中,采用镁粉复合喷吹法深脱硫后铁水终点硫最低只能达到0.002%~0.005%,且脱硫效果稳定性差,波动大,扒渣困难,转炉吹炼终点易产生回硫现象。以上问题主要是因为脱硫渣中的s主要存在mgs中,其熔点在2000℃以上,因其存在于渣铁界面处,渣稀致渣铁界面不清晰,且脱硫渣中含硫量与铁水中的含硫量相差约三个数量级导致脱硫反应正向进行的阻力急剧加大;同时mgs相对密度在2.8左右且mgs在铁水的嵌入深度相对较深,脱硫渣铁分离不好,扒渣困难,扒渣时间长。若要将脱硫渣扒干净,则铁损增加,同时转炉回硫控制也不稳定。技术实现要素:针对上述问题本发明公开了一种在原铁水脱硫喷吹法工艺由喷枪吹入镁粉和石灰粉(喷吹比例1:2.5~3.5)的基础上在铁水罐内铁水表面添加石灰石工艺促进复合喷吹提高脱硫和扒渣效果的一种法。具体技术方案如下:一种喷吹法铁水脱硫加入石灰石提高脱硫效果的方法,1)选取铁水温度≥1200℃,喷吹时间>5min的铁水165~175吨;2)加料方式:喷吹前,在铁水罐内铁水表面加入活性石灰100~500kg+石灰石100~500kg,目的是降低渣中硫化合物的百分含量,利于脱硫反应正向进行,且利用碱性渣松散蓬松的特点能够吸收上浮的镁蒸汽,降低镁蒸汽的逸散,提高镁粉利用率,同时利用添加物改变渣相组成,渣中带铁量降低,渣铁易分离,进而降低铁损。所述的喷吹法铁水脱硫加入石灰石提高脱硫效果的方法,步骤如下:1)选取铁水温度≥1200℃,喷吹时间>5min的铁水165~175吨,铁水入站后,在铁水表面均匀铺撒活性石灰100~500kg、石灰石100~500kg,石灰和石灰石的粒度5~70mm;2)依据模型计算量减少10kg镁粉量进行喷吹镁粉、石灰粉,镁粉喷吹速率8~12kg/s,石灰粉喷吹速率18~22kg/s,喷吹时间8~11min,喷吹速率比cao/mg=1.8~2.2,镁粉粒度0.2~0.6mm,石灰粉粒度<0.2mm;3)喷吹结束后进行扒渣操作,扒渣时间3~5min左右;4)测温、取样。这里的“模型计算量”是按现有技术的工艺流程及计算方法得出的镁粉总量。本发明在冶炼超低硫钢种时,铁水脱硫工艺通过添加石灰石后可将脱硫后的铁水硫含量降低至0.001%,回硫量在0.003%以下,有效的提高了镁粉的脱硫极限,在硫含量要求0.01~0.02%的钢种上,在原脱硫工艺基础上通过添加石灰石工艺可将脱硫后的扒渣量降低0.3t/炉,减少喷吹镁粉消耗10kg/炉,降低了预处理的脱硫成本,同时缩短了脱硫处理时间1min,降低了生产成本;脱硫时间进一步缩短,利于实施铁水预处理与转炉的匹配,生产顺行,同时,减少了扒渣量,降低了铁损,对采用喷吹法脱硫工艺的钢厂有较大的推广价值,减少为了降成本取消喷吹工艺改成搅拌工艺造成的资产浪费。本发明的优点:1、提高镁粉利用率,在相同工艺条件下,能将铁水硫脱除到0.001%,回硫量在0.003%以下。2、在相同铁水条件、相同钢种降低镁粉量10kg/炉,改变渣相组成,渣中带铁量降低,渣铁易分离,进而降低铁损,扒渣量降低0.3t/炉,综合降低生产成本2.02元/t。3、缩短喷吹时间1min,喷吹法适应于炉机匹配的优势更加明显。4、对采用喷吹法脱硫的钢厂有较大的推广价值,减少为了降成本取消喷吹工艺改成搅拌工艺造成的资产浪费。附图说明图1为本发明的工艺流程图。具体实施方式本发明一是通过加入石灰石、石灰,降低渣中硫化合物的含量利于脱硫反应正向进行,提高镁粉的利用率及脱硫极限,降低镁粉使用量;二是通过加入石灰石、石灰改变渣相组成,渣中带铁量降低,渣铁易分离,进而降低铁损,同时有效控制转炉回硫量,降低生产成本。在超低硫钢种上进行脱硫极限实验,具体数据如附表1;附表1序号铁量/t到站温度/℃石灰/kg镁粉/kgs入站/%s终点/%回硫量/%1177.081284518.2188.10.0240.00100.0032181.11334462177.50.0340.00130.001在硫含量要求0.002-0.005%的钢种上进行脱硫试验,在原有喷吹模型基础上,减少喷吹镁粉10kg,喷吹前,在铁水表面加入活性石灰200kg、石灰石200kg,统计脱硫及扒渣量情况,具体如附表2;附表2序号铁量/t到站温度/℃石灰/kg镁粉/kgs入站/%s终点/%扒渣量/t1172.46135728899.90.02930.00251.82173.51407174.990.80.0280.00511.03173.41345349.991.50.030.00371.4通过上述方案的实施,预处理脱硫极限可以达到0.001%,为冶炼超低硫钢种创造条件,在其它需铁水预处理工序进行脱硫钢种能够降低镁粉消耗10kg/炉,按照现有品种比例,降低成本0.132元/t,降低扒渣量0.3t/炉,降低成本2.02元/t,去除添加石灰、石灰石成本0.133元/t,综合降低成本2.02元/吨,创效明显。同一钢种实验首先选取铁水条件,冶炼钢种符合实验要求的炉次,按照本发明的工艺流程图进行实验,实验后收集相关过程数据具体如附表3;附表3石灰/kg镁粉/kgs入站/%s终点/%铁量/t到站温度/℃扒渣量/t原工艺239.4102.60.0290.0028169.7913112.6原工艺234.6101.50.0260.0030172.213572.6试验228.7591.50.0270.0030172.613272.2试验225900.0250.0032173.313762.3通过附表3可以得出:在同一钢种铁水脱硫通过添加石灰石和石灰炉次降低镁粉喷吹量10kg,能够满足终点硫的要求,扒渣量降低0.3t/炉,脱硫渣呈颗粒状,渣铁易分离,有效的降低铁损。比较例对不同种类的钢种分别进行添加石灰石和石灰实验,并与铁水条件相近的炉次进行比对,具体如附表4:附表4在实验过程中,同时进行了单喷脱硫粉剂和添加石灰石石灰后单喷脱硫粉剂实验,实验结果具体如附表5:附表5通过附表4可以得出:在不同的钢种添加石灰石和石灰炉次降低镁粉喷吹量10kg,能够满足终点硫的要求,进一步证明了添加物对镁粉脱硫有促进作用,同时实验钢种上扒渣量有所降低,渣层中由于石灰石分解吸热使渣层温度降低,渣呈碱性渣粘度增加,脱硫渣呈颗粒状,渣铁易分离,有效的降低铁损。通过附表5可以得出:单喷石灰粉剂不能起到脱硫的作用,主要是因为石灰粉表面覆盖一层硅油,在喷吹过程中石灰表面会形成一层致密的硅酸二钙层,阻碍了cao起到脱硫的作用,而添加石灰石、石灰炉次能够产生如下反应:[s]+(cao)=[o]+(cas),当有镁存在时渣中会发生如下反应(mgs)+(cao)=(mgo]+(cas),添加物一方面起到分散脱硫产物mgs的作用,另一方面与mgs反应生成mgo,降低了脱硫产物mgs在渣中的含量,利于脱硫反应[mg]+[s]=(mgs)向正方向进行,进而提高镁的利用率和镁的脱硫极限。综上所述,本专利在原喷吹法脱硫工艺基础上通过添加活性石灰100~500kg和石灰石100~500kg,能够减少镁粉喷吹量10kg/炉,同时缩短喷吹时间1min,减少扒渣量0.3t/炉,降低生产直接成本2.02元/吨铁,易于实现铁水预处理与转炉的生产匹配,对于喷吹法钢厂有较大的推广价值,避免因降低生产成本由喷吹工艺改成搅拌工艺造成的资产浪费。当前第1页12