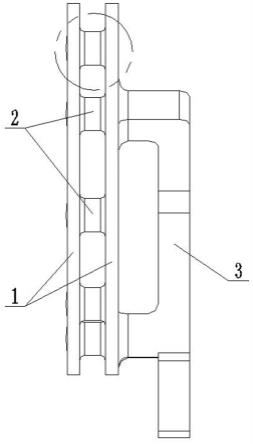
1.本发明涉及支承环熔模铸造用蜡模领域,尤其涉及一种支承环熔模铸造用蜡模的制作方法。
背景技术:2.支承环是航空装备上重要零部件之一,其主要作用是支承和连接,是航空工业熔模精密铸造领域常遇到的铸件产品,支撑环为双圆环结构,通常圆环外径在φ75~φ150mm之间,内径在φ50~φ125mm之间,厚度为2mm,其特点是双环间沿圆周方向等间距分布直径φ8mm、长度8~10mm的圆柱体,该零件双环及圆柱往往是与其它承重零件协同配合的重要部位,因此对其外形尺寸精度及表面质量要求较为严格。
3.支承环通常采用铸造的方式,而铸造砂型需要使用蜡模,熔模铸造支承环采用熔融态模料制作蜡模,先制作一个具有与蜡模相同形状内腔的金属模具,然后向金属模具内进行压注,蜡模会由表及里逐层凝固,将金属模具拆除后即得到蜡模。支承环薄壁部分凝固过程中能够持续得到射蜡通道和圆柱厚区蜡液的补缩,体收缩小,凹陷较轻;而射蜡通道先于圆柱厚区凝固,使得靠近圆柱体的支承环端面得不到熔融蜡的持续补缩,导致收缩量偏大,凹缩严重;此外,蜡模取模后冷却过程中由于圆柱两端表面“硬壳效应”会造成硬壳层产生集中凹陷,最终在支承环外表面上多个圆柱体的投影位置会形成的凹坑,影响蜡模外观质量。现有的修复方法是采用烙铁预先熔化蜡液,分别滴在蜡模外表面凹坑中,待冷却定型后,再采用刮刀逐一修复平整。这种方式修模量大,效率低,尺寸稳定性差,过程中还可能会出现过热而损坏蜡模,急需合理优化。
技术实现要素:4.为解决现有制作支承环熔模铸造用蜡模容易使蜡模表面产生凹坑的问题,本发明提供了一种支承环熔模铸造用蜡模的制作方法。
5.本发明为解决上述技术问题所采用的技术方案是:一种支承环熔模铸造用蜡模的制作方法,所述的蜡模包括支承环蜡模体和y形浇道蜡模体,支承环蜡模体包括两个相对设置的环形体,两个环形体之间设有多个连接柱,y形浇道蜡模体位于支承环蜡模体的一侧,y形浇道蜡模体与其中一个环形体的侧壁连接;该方法包括以下步骤:首先制作金属模具,金属模具的内腔与蜡模相匹配,并在与两个环形体相互背离一侧的表面相对应的金属模具内腔表面设置多个补偿凹坑,多个补偿凹坑分别与多个连接柱在两个环形体相互背离一侧表面的投影相对应,补偿凹坑的深度为0.25~0.5mm,补偿凹坑的边沿与金属模具内腔表面平滑过渡;然后使用金属模具采用压注法制作蜡模,蜡模凝固成型后将金属模具拆除,通过多个补偿凹坑使蜡模的两个环形体相互背离一侧的表面分别形成多个与连接柱的投影相对应的补偿凸起,然后对两个环形体相互背离一侧的表面进行修整,即制得支承环熔模铸造用蜡模。
6.优选的,蜡模凝固成型并从金属模具内取出后,对环形体表面的补偿凸起进行刮磨或擦拭处理,使两个环形体相互背离一侧的表面均达到平整。
7.根据上述技术方案,本发明的有益效果是:本发明在设计制作金属模具时,预先在金属模具内腔表面设置多个补偿凹坑,而这些补偿凹坑的位置均为蜡模在压注过程中容易形成凹坑的位置,因此使用本发明的金属模具压注成形的蜡模表面必然不会出现凹坑,而会在原本容易出现凹坑的位置形成多个与金属模具的补偿凹坑相对应的补偿凸起,即通过预先给予金属模具一定的逆向补偿量,获得在原有的凹坑位置具有反向补偿凸起的蜡模,因此在压蜡完成后只需对蜡模的表面进行修整,将补偿凸起与蜡模的表面修平整即可,无需在凹坑位置进行人工“熔滴”补蜡工作,即可得到表面质量好,尺寸精度高的蜡模,不仅避免了支承环熔模铸造用蜡模的表面凹坑问题,也可以减少支承环熔模铸造用蜡模的表面补蜡修复工作量,特别适合批量生产,可大幅降低支承环熔模铸造用蜡模的生产成本和周期。
附图说明
8.图1为蜡模的侧视图;图2为图1的左视图;图3为图1的右视图;图4为图1的局部放大图。
9.图中标记:1、环形体,2、连接柱,3、y形浇道蜡模体,4、补偿凸起。
具体实施方式
10.参见附图,具体实施方式如下:一种支承环熔模铸造用蜡模的制作方法,如图1-3所示,该蜡模包括支承环蜡模体和y形浇道蜡模体3,支承环蜡模体包括两个相对设置的环形体1,两个环形体1之间设有多个连接柱2,y形浇道蜡模体3位于支承环蜡模体的一侧,y形浇道蜡模体3与其中一个环形体1的侧壁连接。支承环蜡模体的形状与支承环的形状一致,在砂型内受热消失后能够形成与支承环对应的浇铸内腔,y形浇道蜡模体3在砂型内受热消失后能够形成与浇铸内腔相连通的浇道。
11.该方法包括以下步骤:首先制作金属模具,金属模具的内腔与蜡模相匹配,并在与两个环形体1相互背离一侧的表面相对应的金属模具内腔表面设置多个补偿凹坑,多个补偿凹坑分别与多个连接柱2在两个环形体1相互背离一侧表面的投影相对应,补偿凹坑的深度为0.25~0.5mm,补偿凹坑的边沿与金属模具内腔表面平滑过渡。
12.然后使用金属模具采用压注法制作蜡模,蜡模凝固成型后将金属模具拆除,通过多个补偿凹坑使蜡模的两个环形体1相互背离一侧的表面分别形成多个与连接柱2的投影相对应的补偿凸起4。如图2-4所示,其中一个环形体1的表面具有9个补偿凸起4,另一个环形体1的表面有三处位置与y形浇道蜡模体3连接,因此具有6个补偿凸起4。这些补偿凸起4的位置均为蜡模在压注过程中容易形成凹坑的位置,因此能有效避免蜡模的表面形成凹坑。
13.蜡模凝固成型并从金属模具内取出后,对环形体1表面的补偿凸起4进行刮磨或擦拭处理,使两个环形体1相互背离一侧的表面均达到平整,即制得支承环熔模铸造用蜡模,通过预先给予金属模具一定的逆向补偿量,获得在原有的凹坑位置具有反向补偿凸起的蜡模,因此无需在凹坑位置进行人工“熔滴”补蜡工作,即可得到表面质量好,尺寸精度高的蜡模,不仅避免了支承环熔模铸造用蜡模的表面凹坑问题,也可以减少支承环熔模铸造用蜡模的表面补蜡修复工作量。
技术特征:1.一种支承环熔模铸造用蜡模的制作方法,所述的蜡模包括支承环蜡模体和y形浇道蜡模体(3),支承环蜡模体包括两个相对设置的环形体(1),两个环形体(1)之间设有多个连接柱(2),y形浇道蜡模体(3)位于支承环蜡模体的一侧,y形浇道蜡模体(3)与其中一个环形体(1)的侧壁连接,其特征在于,该方法包括以下步骤:首先制作金属模具,金属模具的内腔与蜡模相匹配,并在与两个环形体(1)相互背离一侧的表面相对应的金属模具内腔表面设置多个补偿凹坑,多个补偿凹坑分别与多个连接柱(2)在两个环形体(1)相互背离一侧表面的投影相对应,补偿凹坑的深度为0.25~0.5mm,补偿凹坑的边沿与金属模具内腔表面平滑过渡;然后使用金属模具采用压注法制作蜡模,蜡模凝固成型后将金属模具拆除,通过多个补偿凹坑使蜡模的两个环形体(1)相互背离一侧的表面分别形成多个与连接柱(2)的投影相对应的补偿凸起(4),然后对两个环形体(1)相互背离一侧的表面进行修整,即制得支承环熔模铸造用蜡模。2.根据权利要求1所述的一种支承环熔模铸造用蜡模的制作方法,其特征在于:蜡模凝固成型并从金属模具内取出后,对环形体(1)表面的补偿凸起(4)进行刮磨或擦拭处理,使两个环形体(1)相互背离一侧的表面均达到平整。
技术总结一种支承环熔模铸造用蜡模的制作方法,在与蜡模的两个环形体相互背离一侧的表面相对应的金属模具内腔表面设置多个补偿凹坑,多个补偿凹坑分别与蜡模的多个连接柱在环形体表面的投影相对应;然后使用金属模具采用压注法制作蜡模,蜡模凝固成型后将金属模具拆除,通过多个补偿凹坑使蜡模的两个环形体相互背离一侧的表面分别形成多个与连接柱的投影相对应的补偿凸起,通过预先给予金属模具一定的逆向补偿量,获得在原有的凹坑位置具有反向补偿凸起的蜡模,因此只需对蜡模的表面进行修整即可,无需在凹坑位置进行人工熔滴补蜡,即可得到表面质量好,尺寸精度高的蜡模,不仅避免了蜡模的表面凹坑问题,也可以减少蜡模的表面补蜡修复工作量。蜡修复工作量。蜡修复工作量。
技术研发人员:孙冰 麻毅 孙宏喆 乔海滨 王哲 杨学东
受保护的技术使用者:洛阳双瑞精铸钛业有限公司
技术研发日:2022.03.28
技术公布日:2022/8/5