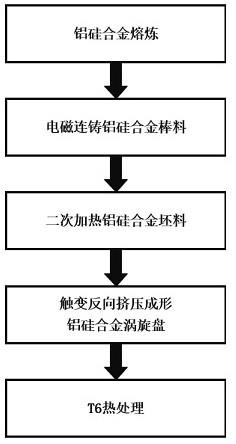
1.本发明属于铸造技术领域,具体涉及一种采用触变挤压铸造工艺制备高性能铝硅合金的方法。
背景技术:2.随着汽车向轻量化方向的发展,迫使铝硅合金在汽车上用量日益增加,对汽车用铸造铝硅合金产品(如涡旋盘、转向节等)的制造提出了更高要求,不仅要求其具有更高的强度、良好的塑性、抗振性能和耐磨性,还需要其简化制备工艺,缩短流程,节能降耗。
3.铝硅合金作为结构材料,具有重量轻、耐腐蚀性好、热膨胀系数低、高温强度高、力学性能好、流动性好等特点,是铸造行业中最重要、应用最广泛的铝硅合金。传统汽车涡旋盘或者转向节产品一般采用正向液态模锻、低压铸造、砂型铸造或背压成形技术制备。采用液态模锻工艺制备产品时,产品充型质量良好,但其模具寿命短且产品毛刺多,易产生偏析缺陷且力学性能较低;采用低压铸造制备的产品力学性能不好,内部缺陷多,但由于铝硅合金中si含量较高,铸态显微组织分别为粗块状初生si相和针状/片状共晶si相,这些粗si相容易引起应力集中,产生微裂纹,这将严重恶化合金的加工和力学性能,尤其是延展性,热处理性能差;背压成形工艺制备产品的力学性能优异,成形精度高,但高硅铝硅合金锻造温度范围小,易发生脆裂,且模具结构复杂,需要进行多次小压下量高温锻造成形,生产效率低,成本高,且容易产生穿流、裂纹及叠层等缺陷。采用砂型铸造方法由于其自身工艺的限制,无法直接铸造出接近于涡旋压缩机动、静涡盘成品件的涡旋形状,强度不能满足要求,甚至出现缩孔、缩松和填充不满等铸造缺陷,导致涡旋件表面形成缺陷。另外,砂型铸造生产效率低,浪费造型材料,还有粉尘污染,铸件精度和表面质量均不高,无法实现大批量生产。
4.综上所述,针对现有汽车铝硅合金铸件的生产工艺容易出现填充不满、涡旋体曲面复杂,凹模局部强度较低、硅相粗大、高表面质量和高力学性能难以兼具的问题。亟需发展一种可促进硅相细小、弥散分布且表面质量高,工艺流程短及产品综合性能优异的铝硅合金涡旋盘制备加工方法。
技术实现要素:5.为解决上述问题,本发明公开了一种采用触变挤压铸造工艺制备高性能铝硅合金的方法,该方法可获得组织致密、无气孔缺陷、共晶硅细小、力学性能好、表面质量优异的高性能铝硅合金涡旋盘,且该方法制造的生产效率高,成本低。
6.一种高性能铝硅合金触变挤压铸造成形方法,包括以下步骤:步骤1:铝硅合金熔炼;步骤2:电磁连铸铝硅合金棒料步骤3:二次加热铝硅合金坯料;步骤4:触变反向挤压成形铝硅合金涡旋盘;
步骤5:t6热处理。
7.本发明进一步改进在于:所述步骤2采取电磁搅拌、连铸技术制备表面质量优异、组织致密、成分均匀的铝硅合金棒料。
8.本发明进一步改进在于:所述步骤3:将铝硅合金棒料进行分切成块,然后将分切块料重新进行电磁感应加热到固液两相区间,获得具有球状晶悬浮在共晶液相的半固态铝硅合金坯料。
9.本发明进一步改进在于:所述步骤4中半固态铝硅合金挤入模具型腔中直至充满整个型腔后加压推动料筒的活塞致使铝硅合金快速凝固。
10.本发明进一步改进在于:所述步骤3中二次加热采用电磁式加热、电阻式加热中的其中一种。
11.本发明进一步改进在于:二次加热的温度为532~571 ℃,保温时间为1~60 min。
12.本发明进一步改进在于:二次加热以后坯料的液相率体积分数控制在0~60%左右。
13.本发明进一步改进在于:所述步骤4中通过由下向上推动活塞,使熔体以层流反重力方式顺利充满模具型腔,充型平稳;其中挤压模具温度为150~250 ℃,压射力为100~160 mpa,冲型速度为0.05~0.3m/s,冲型温度为545~700℃;所述模具的润滑剂为水基石墨,将配比好的石墨水涂料均匀喷涂在模具型腔,喷涂完成,吹干。
14.其中从下往上的层流有利于空气从模具内排出,有效地避免传统液态模锻出现的喷射和紊流现象,大幅降低了气孔和缩孔等缺陷;解决了固态模锻易产生的充型不满、穿流、折痕等缺陷,获得表面质量优异的铝硅合金。
15.本发明进一步改进在于:所述步骤3中二次感应加热温度为545℃~700℃,并在该温度下保温3~4小时。
16.本发明进一步改进在于:所述步骤5中t6热处理的固溶温度为520~540 ℃,固溶时间3~5h;所述t6热处理的时效温度为150~200 ℃,时效时间为5~10h。
17.本发明采取电磁搅拌+连铸技术制备表面质量优异、组织致密、成分均匀的铝硅合金棒料,将铝硅合金棒料进行分切成块,然后将分切块料重新进行电磁感应加热到固液两相区间,获得具有球状晶悬浮在共晶液相的半固态铝硅合金坯料,最后将半固态铝硅合金挤入模具型腔中直至充满整个型腔后加压推动料筒的活塞致使铝硅合金快速凝固,对获得的铝硅合金涡旋盘进行t6热处理。该方法可获得组织致密、无气孔缺陷、共晶硅细小、力学性能好、表面质量优异的高性能铝硅合金涡旋盘,且该方法制造的生产效率高,成本低。采用电磁搅拌连铸技术可获得成分和组织致密均匀的铝硅合金,而且经过不同于正向挤压的反向触变挤压成形使得铝硅合金经历强烈塑性变形,引起位错增殖,产生加工硬化,可获得更大的时效析出形核驱动力,进一步析出大量析出相,避免了传统铸造工艺中铸态组织进行时效处理时存在的析出形核驱动力较弱等问题。使得铝硅合金涡旋盘在制备加工过程中能充分析出数量多、尺寸细小的析出相,合金元素在基体中的固溶度低,最终获得力学性能和表面质量优异的高质量高性能铝硅合金涡旋盘。
18.本发明的有益效果:1、与传统制备工艺相比,采用电磁半连铸技术制备铝硅合金坯料组织均匀,气孔缺陷少,组织致密,晶粒细小,进行二次加热获得的触变坯料变形抗力低,可进行反向挤压一次成形,成形性能优异,能极大地提高了铝硅合金材料的利用率和成材率,降低了能耗,
缩短了工艺流程。
19.2、通过反向挤压铸造成形,熔体以层流方式顺利充满模具型腔,充型平稳,从下往上的层流有利于空气从模具内排出,有效地避免传统液态模锻出现的喷射和紊流现象,大幅降低了气孔和缩孔等缺陷;解决了固态模锻易产生的充型不满、穿流、折痕等缺陷,获得表面质量优异的铝硅合金。
20.3、反向挤压铸造成形使得铝硅合金经历强烈塑性变形,引起位错增殖,产生加工硬化,可获得更大的时效析出形核驱动力,进一步析出大量析出相,避免了传统铸造工艺中铸态组织进行时效处理时存在的析出形核驱动力较弱等问题。使得铝硅合金涡旋盘在制备加工过程中能充分析出数量多、尺寸细小的析出相,合金元素在基体中的固溶度低,综合性能堪比固态锻造成形,同时没有锻件中通常存在的各向异性,具有极大的应用潜力。
21.4、本发明提出的技术不仅适用于铸造性能好的合金,而且也适用于铸造性能不好的变形合金。既可用于铝、铜、镁、锌等有色合金,还可用于铁、钢等黑色金属,还用于镍、钴等高温合金,甚至可用于复合材料等方面。
附图说明
22.图1、根据本发明的涡旋盘触变反向挤压铸造工艺流程图。
具体实施方式
23.下面结合附图和具体实施方式,进一步阐明本发明,应理解下述具体实施方式仅用于说明本发明而不用于限制本发明的范围。需要说明的是,下面描述中使用的词语“前”、“后”、“左”、“右”、“上”和“下”指的是附图中的方向,词语“内”和“外”分别指的是朝向或远离特定部件几何中心的方向。
24.实施例1:一种高强韧、高耐磨4032铝硅合金涡旋盘制备。
25.本实施例的一种采用半固态触变挤压方式制备铝硅合金涡旋盘方法。选用4032铝硅合金为原料,采用电磁连铸技术制备4032铝硅合金棒材,取用4032铝硅合金棒材作母材,将坯料置入炉中。通过采用应变诱发融化技术,在温度为545℃~560℃下进行保温3~4h获得半固态浆料,将半固态浆料冷凝成坯。对成形的坯料根据需要进行切割,将切取得坯料进行二次熔炼,通过电磁感应半固态重熔加热方法,在温度为554℃保温半小时来获得半固态浆料,将浆料置入经快速涂抹石墨润滑剂的模腔内,在设置压力机的压射力为160mpa,冲型速度为0.12m/s,冲型温度为700℃,模具材料为h13,模具温度为250℃的情况下进行挤压铝硅合金半固态坯料。将挤压成形的涡旋盘在温度为520~540℃进行固溶3~4h,然后再165℃下进行时效处理8h来获得质量更好的涡旋盘。
26.实施例2:一种高强度、高韧性a356铝硅合金汽车转向节制备。
27.本实施例的一种采用触变挤压铸造方式制备高性能铝硅合金方法。本实例所选用的原料为a356铝硅合金,取用a356铝硅合金铸锭作为母材,将坯料置入炉中。通过采用应变诱发融化技术,在温度为545℃~560℃下进行保温3~4h获得半固态浆料,将半固态浆料冷凝成坯。对成形的坯料根据需要进行切割,将切取得坯料进行二次熔炼,通过电磁感应半固态重熔加热方法,在温度为554℃保温半小时来获得半固态浆料,将浆料置入经快速涂抹石墨润滑剂的模腔内,在设置压力机的压射力为160mpa,冲型速度为0.12m/s,冲型温度为700
℃,模具材料为h13,模具温度为250℃的情况下进行挤压铝硅合金半固态坯料。将挤压成形的涡旋盘在温度为520~540℃进行固溶3~4h,然后再165℃下进行时效处理8h来获得质量更好的涡旋盘。
28.实施例3:一种高强度、高韧性a390铝硅合金压缩机活塞制备。
29.本实施例的一种采用半固态触变挤压方式制备铝硅合金涡旋盘方法。本实例涡旋盘所选用的原料为a390铝硅合金,取用a390铝硅合金棒材作母材,将坯料置入炉中。通过采用应变诱发融化技术,在温度为545℃~560℃下进行保温3~4h获得半固态浆料,将半固态浆料冷凝成坯。对成形的坯料根据需要进行切割,将切取得坯料进行二次熔炼,通过电磁感应半固态重熔加热方法,在温度为554℃保温半小时来获得半固态浆料,将浆料置入经快速涂抹石墨润滑剂的模腔内,在设置压力机的压射力为160mpa,冲型速度为0.12m/s,冲型温度为700℃,模具材料为h13,模具温度为250℃的情况下进行挤压铝硅合金半固态坯料。将挤压成形的涡旋盘在温度为520~540℃进行固溶3~4h,然后再165℃下进行时效处理8h来获得质量更好的涡旋盘。
30.对比例1:采用背压成形技术制备4032铝硅合金涡旋盘。
31.本对比例采用背压成形技术制备4032铝硅合金涡旋盘。以4032铝硅合金铸锭作为原料,采用火焰将模具加热使上下模温度达到200
ꢀ°
c。将4032铝硅合金坯料放入电阻炉内进行加热,当温度达到480
ꢀ°
c时将坯料放入凹模内,启动液压机进行预锻和终锻,随后进行t6热处理,具体工艺为:固溶温度520
ꢀ°
c、固溶时效4 h、时效温度160
ꢀ°
c、时效时间8 h。所获得的4032铝硅合金涡旋盘含有大量尺寸10~160 nm的不均匀分布m2si、 al2cu析出相,存在裂纹、穿流等缺陷,室温抗拉强度360 mpa,延伸率4%。
32.对比例2:采用高压压铸技术制备a390铝硅合金压缩机活塞。
33.本对比例采用高压压铸技术制备a390铝硅合金汽车转向节。以a390铝硅合金铸锭作为原料,采用火焰将模具加热使上下模温度达到200
ꢀ°
c。将a390铝硅合金坯料放入电阻炉内进行熔化,加热到700 ℃时进行精炼除气,静置20 min后,将液态金属降温到660 ℃,然后将液态金属注入压铸机浇口进行压铸,从而获得a356铝硅合金汽车转向节。随后进行t6热处理,具体工艺为:固溶温度500
ꢀ°
c、固溶时效8 h、时效温度175
ꢀ°
c、时效时间4 h。所获得的a390铝硅合金汽车转向节初生α-al晶粒平均尺寸为60 μm,初生硅平均尺寸30 μm,室温抗拉强度360 mpa,延伸率4.2%。
34.对比例3:采用砂型铸造技术制备a356铝硅合金轮毂。
35.本对比例采用砂型铸造技术制备a356铝硅合金轮毂。以a356铝硅合金铸锭作为原料,采用火焰将模具加热使上下模温度达到200
ꢀ°
c。将a356铝硅合金坯料放入电阻炉内进行熔化,加热到700 ℃时进行精炼除气,静置20 min后,将液态金属降温到660 ℃,然后将液态金属注入砂型模具内,从而获得a356铝硅合金轮毂。随后进行t6热处理,具体工艺为:固溶温度520
ꢀ°
c、固溶时效4 h、时效温度160
ꢀ°
c、时效时间3 h。所获得的a356铝硅合金轮毂初生α-al晶粒平均尺寸为102 μm,室温抗拉强度290 mpa,延伸率8.5 %。
36.表1 合金牌号制造工艺抗拉强度(mpa)延伸率(%)实施例14032铝硅合金背压成形技术3985.5实施例2a390铝硅合金高压压铸技术3268.9
实施例3a356铝硅合金砂型铸造技术3007.3对比例14032铝硅合金触变挤压铸造技术72045.2对比例2a390铝硅合金触变挤压铸造技术58087.2对比例3a356铝硅合金触变挤压铸造技术65074.2本发明方案所公开的技术手段不仅限于上述实施方式所公开的技术手段,还包括由以上技术特征任意组合所组成的技术方案。