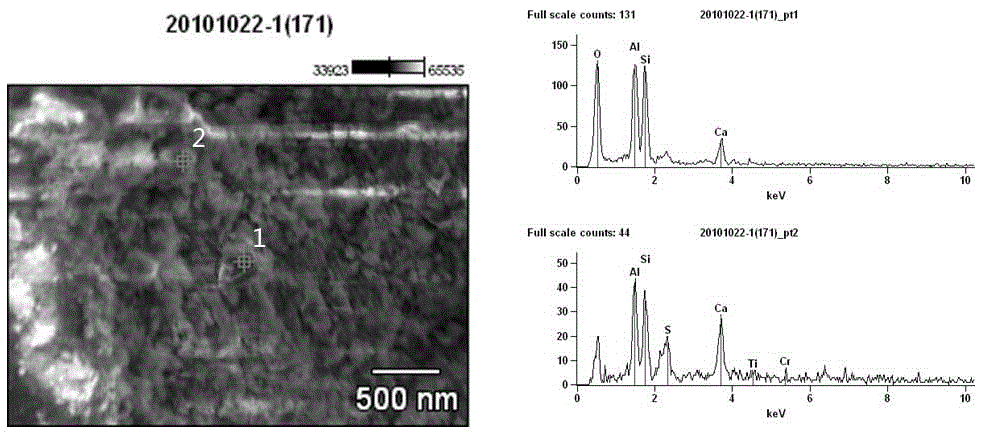
本发明涉及一种新型建筑材料,特别是一种综合利用冶金矿渣与石膏类材料耦合制造建筑材料的方法。
背景技术:
:粒化高炉矿渣矿渣是指在高炉冶炼生铁时,所得以硅酸盐与硅铝酸盐为主要成分的熔融物,经淬冷成粒后,即为粒化高炉矿渣,冶炼生铁时从高炉中排出的废物,当炉温达到1400~1600℃时,炉料熔融,矿石中的脉石、焦炭中的灰分和助溶剂和其他不能进入生铁中的杂质形成以硅酸盐和铝酸盐为主浮在铁水上面的熔渣。高炉渣中主要成分为CaO、SiO2、Al2O3。根据冷却方式分为气冷渣、水淬渣和膨胀矿渣等。根据化学成分分为碱性矿渣、中性矿渣和酸性矿渣。由于矿渣矿物组成与水泥相似,但磨成细粉后不能单独水化,在碱性环境中或有硫酸盐激发条件下,具有较高的水化活性,常用来生产矿渣水泥、混凝土矿物掺和料、涂料填料等,利用率90%以上。但是产品附加值较低,影响企业经济效益。水淬锰渣是高炉矿渣的一种,它是锰矿石冶炼生铁过程中排出的熔渣,在高温熔融状态下经水淬急冷形成的一种MnO含量比普通矿渣高的高炉矿渣。由于我国锰矿品位较低、富锰矿较少、贫矿多、杂质含量高、矿床规模小、可选性质差,因此在生产过程中产生了大量的水淬锰渣,据统计,每年排放约1300万吨锰渣。由于现有的利用水淬锰渣的技术还不是很完善,水淬锰渣大部分采用堆填处理。随着经济的发展,水淬锰渣排放造成的一系列社会、经济和环境问题开始凸现出来,一方面堆填占用大量土地,增加企业成本,此外还会导致成片的“渣山”出现;另一方面,水淬锰渣中的Mn、Cr元素在雨水作用下很容易流失,污染水质。水淬锰渣化学组成与水淬矿渣相似,其中MnO的含量高达10%左右。水淬锰渣中主要含有α´-C2S、镁蔷薇辉石、锰钙辉石和少量钙铝黄长石等矿物组成。水淬锰渣由大量不规则颗粒组成,玻璃体占据大部分,还有少部分结晶体。原状水淬锰渣的水化活性较低,如果不经活性激发用于建筑材料,将会明显降低建筑材料制品的力学性能。镍铁渣是在金属镍冶炼过程中排放的一种工业废弃物,即在金属镍冶炼过程中所形成的以SiO2、A12O3、CaO、MgO、Fe2O3等为主要化学成分的高温熔融物再经水淬后形成的粒化炉渣(部分少数企业不经水淬而直接外排)。生产1吨金属镍大约排,6~16t废渣。随着我国镍产量的逐年增加水淬镍铁渣的排放量也急剧增加,再加之目前我国的水淬镍铁渣利用率较低,大部分堆积在渣场。目前,我国水淬镍铁渣的年产量已突破500万吨,累计存积水淬镍铁渣己达4000余万吨,但水淬镍铁渣的有效综合利用率仅为15%~25%,如果不加任何治理而随意堆放,不仅占用了大量的土地,而且会对环境造成污染,因此水淬镍铁渣的综合利用问题己成为镍矿冶炼企业急需解决的问题。目前对水淬镍铁渣在建材领域资源化利用的研究主要集中以下几个方面:(1)水淬镍铁渣作为水泥硅质原料或铁质矫正原料进行配料来煅烧水泥;(2)水淬镍铁渣作为水泥混合材配制水泥;(3)水淬镍铁渣作为混合料或集料(代替部分砂)用于水泥混凝土中;(4)水淬镍铁渣作为细集料或磨细后作胶凝材料用于矿山井下充填料:(5)水淬镍铁渣作为集料或胶凝材料用来生产建筑砌块。但由于活性差,利用率低,生产的建筑砌块强度低于20MPa。钢渣是一种工业固体废物。炼钢排出的渣,依炉型分为转炉渣、平炉渣、电炉渣。排出量约为粗钢产量的15~20%。钢渣主要由钙、铁、硅、镁和少量铝、锰、磷等的氧化物组成。主要的矿物相为硅酸三钙、硅酸二钙、钙镁橄榄石、钙镁蔷薇辉石、铁铝酸钙以及硅、镁、铁、锰、磷的氧化物形成的固熔体,还含有少量游离氧化钙以及金属铁、氟磷灰石等。有的地区因矿石含钛和钒,钢渣中也稍含有这些成分。钢渣中各种成分的含量因炼钢炉型、钢种以及每炉钢冶炼阶段的不同,有较大的差异。钢渣在温度1500~1700℃下形成,高温下呈液态,缓慢冷却后呈块状,一般为深灰、深褐色。有时因所含游离钙、镁氧化物与水或湿气反应转化为氢氧化物,致使渣块体积膨胀而碎裂;有时因所含大量硅酸二钙在冷却过程中(约为675℃时)由β型转变为γ型而碎裂。钢渣的用途因成分而异。钢渣可用作铁路道碴和道路材料,做法是先将加工后的钢渣存放3~6个月,待体积稳定以后使用。这类钢渣广泛用于道路路基的垫层、结构层,尤宜用作沥青拌合料的骨料铺筑路面层。钢渣筑路,具有强度高,耐磨性和防滑性好,耐久性好,维护费用低等优点。各类钢渣均可作为填坑、填海造地材料。中国目前生产少量钢渣水泥,多用转炉钢渣掺50%左右高炉粒化渣,10%左右石膏,磨制无熟料钢渣水泥,或以15%左右水泥熟料代替钢渣磨制少熟料水泥。此外,钢渣还可制造砖、瓦、碳化建筑材料等。钢渣在建筑建材行业中利用受制约的主要因素是钢渣的体积不稳定性。以上所述的冶金矿渣都是金属冶炼过程中产生的废渣,每年的排放量极大,存在资源浪费和环境污染的问题,应用于建筑材料又存在不同的需要克服的难点。技术实现要素:本发明要解决的技术问题是提供一种利用冶金矿渣制备建筑材料的方法,该方法合利用冶金矿渣与石膏类材料耦合,以至少解决现有石膏类产品强度低、耐久性差的缺点。一种利用冶金矿渣制备建筑材料的方法,其特征在于,包括如下步骤:1)以质量百分比计的如下原料制成干混料,冶金矿渣15~50%、石膏或工业副产石膏10~60%、钙质胶凝材料3~12%、集料22~35%;2)向步骤1)制得的干混料中加入水或溶入了激发剂的水,混合3~10min,湿混制得湿混料,其中,水占全部固体物料干基质量的12~20%,激发剂为干矿渣质量的0.2~1.5%;3)将湿混料进行静置,静置时间为15min~2h;4)将经步骤3)处理的物料进行静压成型,得到坯体,成型压力为20~50MPa,保压时间为15~60s;5)将步骤4)制得的坯体进行自然养护28天或经静停0.5~3h后蒸汽养护3~24h,最后制得建筑材料,其中,蒸汽养护温度为70~95℃。作为优选的技术方案,所述的冶金矿渣是指金属冶炼过程中产生的以硅铝酸盐矿物为主要成分的冶金废渣。作为优选的技术方案,所述的冶金废渣为水淬粒化高炉矿渣、水淬锰渣、水淬镍铁渣、钢渣中的一种或几种的组合。所述的工业副产石膏优选自氟石膏、钛石膏、盐石膏、柠檬酸石膏、废模型石膏中的一种或几种的组合。作为优选的技术方案,所述的钙质胶凝材料是以氧化钙、硅酸钙或铝酸钙为主要矿物的材料。作为优选的技术方案,所述的钙质胶凝材料为石灰、电石渣、水泥熟料、水泥中的一种或多种的组合。作为优选的技术方案,所述的集料为粒径为0.1~10mm的河砂、机制砂、矿渣颗粒、炉渣颗粒、建筑垃圾再生细集料、各种尾矿中的一种或多种的组合。作为优选的技术方案,冶金矿渣、石膏或工业副产石膏、钙质胶凝材料采用单独粉磨后混合或者混合后粉磨的方式处理,制得混合粉体,控制混合粉体的比表面积在400~800m2/kg。作为优选的技术方案,混合粉体与集料混合3~5min,制得干混料。作为优选的技术方案,干混料加入水或溶入了激发剂的水混合3~10min制得湿混料。本发明利用冶金矿渣与石膏类材料耦合制备超高强建筑材料的机理:(1)根据材料最紧密堆积原理和水化活性增强原理设计粉体材料(冶金矿渣、石膏类材料、钙质胶凝材料)与集料最佳配比范围,与水混合后在较高压力下(以集料抗压强度为限)静压模压成型,获得致密坯体。(2)经过细磨的石膏在致密坯体孔隙液中发生溶解和再结晶反应,受到致密坯体孔隙大小和相貌的影响,生成数量巨大的纳米石膏晶须(见图1),穿插在孔隙中和铝硅酸盐矿物的水化产物中,起到了进一步增加致密度和纤维增强作用,极大程度提高了材料强度。(4)冶金矿渣水化产物在碱激发剂作用下还与硫酸根离子(或石膏)反应生成水合硫酸方柱石,如:(CaO,xNa2O)[ySiO2·zAl2O3]SO3·nH2O)(见图2),使得矿渣水化产物与石膏晶体或晶须表面薄弱结合区减少,提高了材料的强度和耐水性。本发明与现有方法相比,具有如下有益效果:(1)强度高,各种冶金矿渣的强度如表1所示,是现有常规方法制备的石膏基材料强度(10~30MPa)或铝硅酸盐类工业废渣基材料(10~40MPa)的数倍,甚至十多倍,实现了此类材料强度突破;表1冶金矿渣种类水淬粒化高炉矿渣水淬锰渣水淬镍铁渣钢渣强度(单位:MPa)100~20060~15070~18060~150(2)耐水性好,克服了石膏制品耐水性差的致命缺陷;(3)生产工艺简单,可以通过对现有粉煤灰免烧砖生产线进行简单改造即可实现规模化生产;(4)产品品种调节容易,以实现功能化。利用本发明的技术,可通过变化成型模具方法制备高强建筑砖、高强道路砖、高强透水砖、路沿石、各种装饰板材等各种高强、高耐久性产品;(5)本发明的实施属于工业固废资源化利用采用本发明的技术方案,对工业副产石膏等固体废弃物的利用率可达90%以上,因此,它可以提高固体废弃物的附加值,真正地实现变废为宝。附图说明图1为本发明建筑材料水化产物特征(晶须增强)。图2为本发明建筑材料水化产物能谱图。图3为本发明实施例1-4的材料强度。图4为本发明实施例5-8的材料强度。图5为本发明实施例9-12的材料强度。图6为本发明实施例13-16的材料强度。具体实施方式为了使本领域技术人员更好的理解本发明,以下结合实施例对本发明作进一步清楚、完整的说明。需要说明的是,在不冲突的情况下,本申请中的实施例及实施例中的特征可以相互组合。实施例1将比表面积450m2/kg钛石膏400g(40%)、比表面积600m2/kg水淬粒化高炉矿渣300g(30%)、比表面积580m2/kgP·O42.5水泥50g(5%)和细度模数为2.8的河砂250g(25%)在混合机中干混3min;然后加入180g水(全部固体物料干基质量的18%),水中额外加入1.5g碱性激发剂(占水淬粒化高炉矿渣的0.5%),湿混10min;静置15min后在40MPa下保压30s,制得超强材料坯体;在混凝土养护室内自然养护28天得超高强建筑材料K1,经静停1h后在75℃下饱和蒸汽养护6h,制得超高强建筑材料K2,抗压强度见图3。实施例2将水淬粒化高炉矿渣2500g、废模型石膏2500g放入500×500mm标准球磨机粉磨50min,制得比表面积618m2/kg的混合料,取620g混合料(其中水淬粒化高炉矿渣占总干基物料的31%,废模型石膏占总干基物料的31%),与比表面积680m2/kgP·O42.5水泥80g(占总干基物料的8%)和细度模数为2.8的河砂300g(占总干基物料的30%)在混合机中干混4min;然后加入130g的水(占总干基物料的13%),水中额外加入1.8g碱性激发剂(占水淬粒化高炉矿渣的0.6%),湿混8min;静置30min后在45MPa下保压15s,制得超强材料坯体;在实验室(温度20℃~31℃)自然养护28天得超高强建筑材料K3,经静停1h后在75℃下饱和蒸汽养护12h,制得超高强建筑材料K4,抗压强度见图3。实施例3将水淬粒化高炉矿渣2800g、氟石膏2200g放入500×500mm标准球磨机粉磨65min,制得比表面积662m2/kg的混合料,取670g混合料(其中水淬粒化高炉矿渣占总干基物料的37.5%,氟石膏占总干基物料的29.5%),与比表面积500m2/kgP·O42.5水泥90g(占总干基物料的9%)和细度模数为3.2的机制砂240g(占总干基物料的24%)在混合机中干混3min;然后加入200g的水(占总干基物料的20%),水中额外加入1.4g碱性激发剂(占水淬粒化高炉矿渣的0.47%),湿混9min;静置30min后在45MPa下保压50s,制得超强材料坯体;经静停3h后在90℃下饱和蒸汽养护6h,制得超高强建筑材料K5,抗压强度见图3。实施例4将水淬粒化高炉矿渣2400g、钛石膏2300g和石灰300g放入500×500mm标准球磨机粉磨60min,制得比表面积532m2/kg的混合料,取700g混合料(其中钛石膏占总干基物料的32.2%、水淬粒化高炉矿渣占总干基物料的33.6%、石灰占总干基物料的4.2%),和细度模数为2.8的砂浆再生集料300g(占总干基物料的30%)在混合机中干混3min;然后加入140g的水(占总干基物料的14%),湿混7min;静置30min后在403MPa下保压45s,制得超强材料坯体;经静停2h后在90℃下饱和蒸汽养护6h,制得超高强材料K6,抗压强度见图3。实施例5将比表面积500m2/kg钛石膏400g(40%)、比表面积580m2/kg水淬锰渣粉300g(30%)、比表面积380m2/kgP·O42.5水泥50g(5%)和细度模数为2.8的河砂250g(25%)在混合机中干混3min;然后加入130g水(占全部固体物料干基质量的13%),水中额外加入1.5g碱性激发剂(占水淬锰渣粉的0.5%),湿混10min;静置15min后在40MPa下保压30s,制得超强材料坯体;在混凝土养护室内自然养护28天得超高强材料M1,经静停1h后在75℃下饱和蒸汽养护6h,制得超高强材料M2,抗压强度见图4。实施例6将水淬锰渣2500g、废模型石膏2500g放入500×500mm标准球磨机粉磨50min,制得比表面积550m2/kg的混合料,取620g混合料(其中水淬锰渣占总干基物料的31%,废模型石膏占总干基物料的31%),与比表面积380m2/kgP·O42.5水泥80g(占总干基物料的8%)和细度模数为2.8的河砂300g(占总干基物料的30%)在混合机中干混4min;然后加入140g的水(占总干基物料的14%),水中额外加入1.8g碱性激发剂(占水淬锰渣粉的0.6%),湿混8min;静置30min后在30MPa下保压15s,制得超强材料坯体;在实验室(温度20℃~31℃)自然养护28天得超高强材料M3,经静停1h后在75℃下饱和蒸汽养护12h,制得超高强材料M4,抗压强度见图4。实施例7将水淬锰渣2800g、氟石膏2200g放入500×500mm标准球磨机粉磨65min,制得比表面积621m2/kg的混合料,取670g混合料(其中水淬锰渣占总干基物料的37.5%,氟石膏占总干基物料的29.5%),与比表面积380m2/kgP·O42.5水泥90g(占总干基物料的9%)和细度模数为3.2的机制砂240g(占总干基物料的24%)在混合机中干混3min;然后加入200g的水(占总干基物料的20%),水中额外加入1.4g碱性激发剂(占水淬锰渣粉的0.37%),湿混9min;静置30min后在45MPa下保压50s,制得超强材料坯体;经静停3h后在90℃下饱和蒸汽养护6h,制得超高强材料M5,抗压强度见图4。实施例8将水淬锰渣2400g、钛石膏2300g和石灰300g放入500×500mm标准球磨机粉磨60min,制得比表面积561m2/kg的混合料,取700g混合料(其中钛石膏占总干基物料的32.2%、水淬锰渣占总干基物料的33.6%、石灰占总干基物料的4.2%),和细度模数为2.8的砂浆再生集料300g(占总干基物料的30%)在混合机中干混3min;然后加入130g的水(占总干基物料的13%),湿混7min;静置30min后在20MPa下保压45s,制得超强材料坯体;经静停2h后在90℃下饱和蒸汽养护6h,制得超高强材料M6,抗压强度见图4。实施例9将比表面积500m2/kg钛石膏400g(40%)、比表面积560m2/kg水淬镍铁渣粉300g(30%)、比表面积380m2/kgP·O42.5水泥50g(5%)和细度模数为2.8的河砂250g(25%)在混合机中干混3min;然后加入130g水(全部固体物料干基质量的13%),水中额外加入1.5g碱性激发剂(占水淬镍铁渣粉的0.5%),湿混10min;静置15min后在40MPa下保压30s,制得超强材料坯体;在混凝土养护室内自然养护28天得超高强材料N1,经静停1h后在75℃下饱和蒸汽养护6h,制得超高强材料N2,抗压强度见图5。实施例10将水淬镍铁渣2500g、废模型石膏2500g放入500×500mm标准球磨机粉磨50min,制得比表面积585m2/kg的混合料,取620g混合料(其中水淬镍铁渣占总干基物料的3131%,废模型石膏占总干基物料的31%),与比表面积380m2/kgP·O42.5水泥80g(占总干基物料的8%)和细度模数为2.8的河砂300g(占总干基物料的30%)在混合机中干混4min;然后加入140g的水(占总干基物料的14%),水中额外加入1.8g碱性激发剂(占水淬镍铁渣粉的0.6%),湿混8min;静置30min后在30MPa下保压15s,制得超强材料坯体;在实验室(温度20℃~31℃)自然养护28天得超高强材料N3,经静停1h后在75℃下饱和蒸汽养护12h,制得超高强材料N4,抗压强度见图5。实施例11将水淬镍铁渣2800g、氟石膏2200g放入500×500mm标准球磨机粉磨65min,制得比表面积598m2/kg的混合料,取670g混合料(其中水淬镍铁渣占总干基物料的37.5%,氟石膏占总干基物料的29.5%),与比表面积380m2/kgP·O42.5水泥90g(占总干基物料的9%)和细度模数为3.2的机制砂240g(占总干基物料的24%)在混合机中干混3min;然后加入200g的水(占总干基物料的20%),水中额外加入1.8g碱性激发剂(占水淬镍铁渣粉的0.47%),湿混9min;静置30min后在45MPa下保压50s,制得超强材料坯体;经静停3h后在90℃下饱和蒸汽养护6h,制得超高强材料N5,抗压强度见图5。实施例12将水淬镍铁渣2400g、钛石膏2300g和石灰300g放入500×500mm标准球磨机粉磨60min,制得比表面积583m2/kg的混合料,取700g混合料(其中钛石膏占总干基物料的32.2%、水淬镍铁渣占总干基物料的33.6%、石灰占总干基物料的4.2%),和细度模数为2.8的砂浆再生集料300g(占总干基物料的30%)在混合机中干混3min;然后加入130g的水(占总干基物料的13%),湿混7min;静置30min后在50MPa下保压45s,制得超强材料坯体;经静停2h后在90℃下饱和蒸汽养护6h,制得超高强材料N6,抗压强度见图5。实施例13将比表面积450m2/kg钛石膏400g(40%)、比表面积600m2/kg钢渣粉300g(30%)、比表面积560m2/kg矿渣粉50g(5%)和细度模数为2.4的河砂250g(25%)在混合机中干混3min;然后加入150g水(全部固体物料干基质量的15%),水中额外加入1.5g碱性激发剂(占钢渣粉的0.5%),湿混10min;静置15min后在40MPa下保压30s,制得坯体;在混凝土养护室内自然养护28天得超高强材料S1,经静停1h后在80℃下饱和蒸汽养护9h,制得超高强材料S2,抗压强度见图6。实施例14将含水率8%废模型石膏2500g、钢渣2500g放入500×500mm标准球磨机粉磨65min,制得比表面积652m2/kg的混合料,取620g混合料(其中废模型石膏占总干基物料的29%,钢渣占总干基物料的32%),与比表面积612m2/kg粉煤灰60g(占总干基物料的6.2%)和细度模数为2.4的河砂320g(占总干基物料的32.8%)在混合机中干混4min;然后加入150g的水(加上石膏带入的水占总干基物料的17.9%),水中额外加入1.8g碱性激发剂(占钢渣的0.6%),湿混8min;静置30min后在45MPa下保压15s,制得坯体;在实验室(温度20℃~31℃,相对湿度67%~83%)自然养护28天得超高强材料S3,经静停1h后在75℃下饱和蒸汽养护12h,制得超高强材料S4,抗压强度见图6。实施例15将含水率6%氟石膏2800g、钢渣2200g放入500×500mm标准球磨机粉磨66min,制得比表面积632m2/kg的混合料,取670g混合料(其中干氟石膏占总干基物料的36.1%,钢渣占总干基物料的30.1%),与比表面积647m2/kg磷渣粉90g(占总干基物料的9.2%)和细度模数为3.2的机制砂240g(占总干基物料的24.6%)在混合机中干混3min;然后加入140g的水(加上石膏带入的水占总干基物料的16.6%),水中额外加入1.4g碱性激发剂(占钢渣粉的0.47%),湿混9min;静置30min后在45MPa下保压50s,制得坯体;经静停3h后在90℃下饱和蒸汽养护6h,制得超高强材料S5,抗压强度见图6。实施例16将钢渣2200g、盐石膏2300g和水淬镍铁渣500g放入500×500mm标准球磨机粉磨55min,制得比表面积501m2/kg的混合料,取700g混合料(其中钢渣粉占总干基物料的30.8%、干盐石膏占总干基物料的32.2%、水淬镍铁渣占总干基物料的7%),和细度模数为2.8的砂浆再生集料300g(占总干基物料的30%)在混合机中干混3min;然后加入160g的水(占总干基物料的16%),湿混7min;静置30min后在43MPa下保压45s,制得超强材料坯体;经静停2h后在90℃下饱和蒸汽养护6h,制得超高强材料S6,抗压强度见图6。实施例17将水淬锰渣900g、钛石膏3600g放入500×500mm标准球磨机粉磨67min,制得比表面积400m2/kg的混合料,取750g混合料(其中水淬锰渣占总干基物料的15%,钛石膏占总干基物料的60%),与比表面积800m2/kgP·O42.5电石渣30g(占总干基物料的3%)和细度模数为3.2的炉渣颗粒220g(占总干基物料的22%)在混合机中干混5min;然后加入120g的水(占总干基物料的12%),水中额外加入0.3g碱性激发剂(占水淬锰渣的0.2%),湿混3min;静置2h后在20MPa下保压1min,制得坯体;经静停0.5h后在70℃下饱和蒸汽养护3h,制得超高强材料M7。实施例18将钢渣3000g、柠檬酸石膏600g放入500×500mm标准球磨机粉磨58min,制得比表面积624m2/kg的混合料,取600g混合料(其中钢渣占总干基物料的50%,柠檬酸石膏占总干基物料的10%),与比表面积380m2/kgP·O42.5水泥120g(占总干基物料的12%)和细度模数为2.4的河砂100g和机制砂180g(总共占总干基物料的28%)在混合机中干混5min;然后加入150g的水(占总干基物料的15%),水中额外加入7.5g碱性激发剂(占钢渣的1.5%),湿混10min;静置30min后在50MPa下保压15s,制得坯体;在实验室(温度20℃~31℃,相对湿度67%~83%)自然养护28天得超高强材料M8,经静停2h后在95℃下饱和蒸汽养护24h,制得超高强材料M9。实施例19将水淬镍铁渣2040g、钛石膏1000g和氟石膏500g放入500×500mm标准球磨机粉磨58min,制得比表面积624m2/kg的混合料,取590g混合料(其中水淬镍铁渣占总干基物料的34%,钛石膏和氟石膏占总干基物料的25%),与比表面积380m2/kgP·O42.5水泥200g和石灰150g(总共占总干基物料的12%)和细度模数为2.4的河砂350g(占总干基物料的35%)在混合机中干混4min;然后加入180g的水(占总干基物料的18%),水中额外加入3.4g碱性激发剂(占水淬镍铁渣的1.0%),湿混5min;静置60min后在30MPa下保压30s,制得坯体;经静停1h后在75℃下饱和蒸汽养护10h,制得超高强材料M10。本发明要求保护的范围不限于以上具体实施方式,对于本领域技术人员而言,本发明可以有多种变形和更改,凡在本发明的构思与原则之内所作的任何修改、改进和等同替换都应包含在本发明的保护范围之内。当前第1页1 2 3