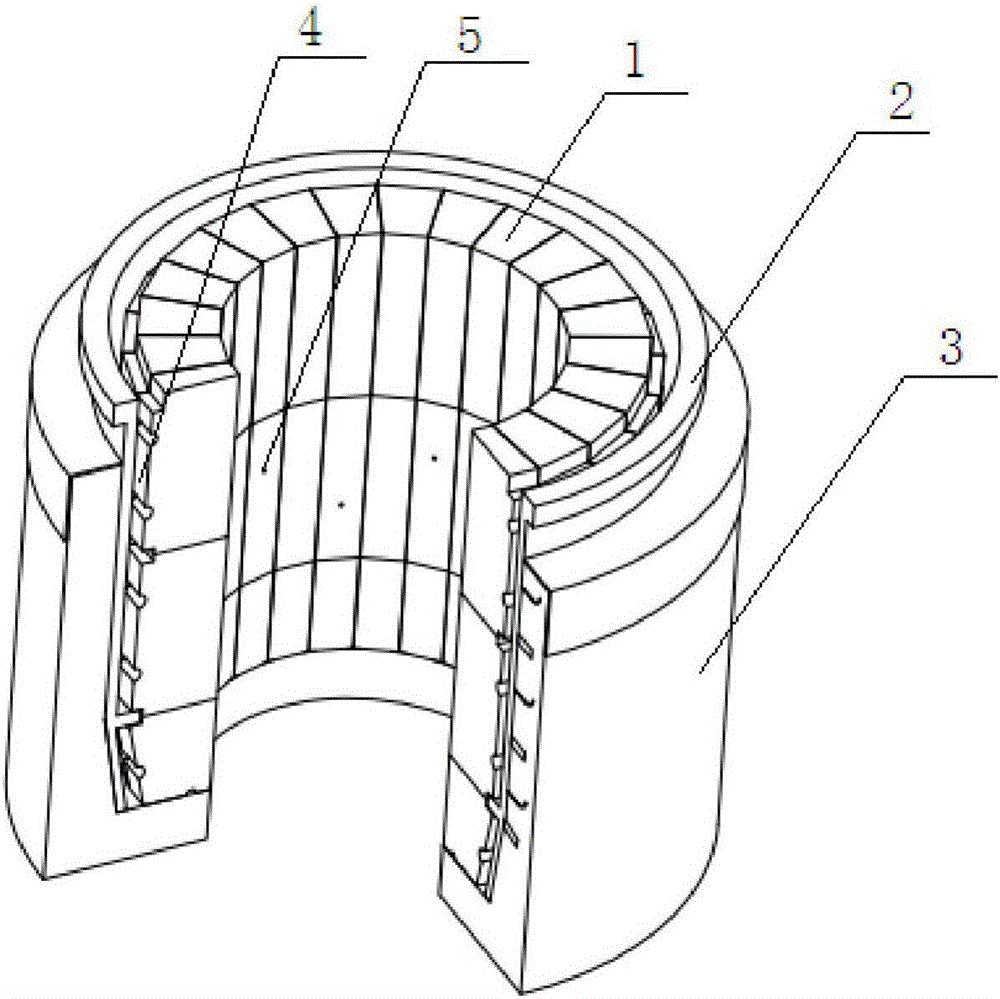
本发明涉及炼钢厂RH真空精炼设备,特别涉及一种高温使用时整体结构稳定性优良的RH炉浸渍管。
背景技术:
:近几十年,RH炉外精炼技术取得了巨大进展,由原来单一的脱气功能发展到现在的真空脱气、脱碳、吹氧脱碳、喷粉脱硫、温度补偿、去夹杂、均匀温度和成分等多种功能,成为目前冶炼精品钢最常用的二次精炼冶金方法。其中,RH炉浸渍管是RH真空精炼工序最重要的耐材,RH炉浸渍管从内向外,依次是镁铬(无铬)环砖、自流料、钢结构件及外层浇注料,RH炉浸渍管在高温使用中,如何保证整体结构的完整性,少裂纹,不脱落,不漏气,是高性能RH炉浸渍管的必备条件。RH真空插入管工作时直接浸入钢水中,温度在1600℃以上,浸泡处理时间30-40分钟。由于RH炉浸渍管中的镁铬(无铬)环砖、自流料、钢结构件及外层浇注料等几种材料,热膨胀系数各不相同,尤其是钢结构与几种耐材的热膨胀系数相差近10倍,而如此大的差距,即便如何调整耐火材料的配方,也很难让彼此的热膨胀系数达到一致或是接近。因此,在RH炉浸渍管生产过程中低温烘烤时(300-500℃),在RH炉浸渍管上线前烘烤时(1100℃左右),尤其是高温使用时(1600℃以上),各种材料的热膨胀系数不一致,常常导致RH炉浸渍管的外层浇注料表面上、浇注料与镁铬(无铬)环砖之间,以及钢结构件与浇注料之间,因热膨胀不均而常常产生大量裂纹。这些裂纹如没有在喷补维护中有效控制,而继续加剧,在高温使用中,必将导致RH炉浸渍管整体结构稳定性欠佳且结构强度损失,有时会导致外层浇注料脱落,如果是上升管,一旦氩气管受损,直接造成RH炉浸渍管无法使用,提前下线;有时会导致与镁铬(无铬)环砖相连接的浇注料脱落,镁铬(无铬)环砖失去依托而下沉,也会成RH炉浸渍管因解体损坏而无法使用,提前下线。技术实现要素:本发明的目的是克服现有技术中的不足,提供了一种整体结构稳定的RH炉浸渍管,提高了RH炉浸渍管整体结构的稳定性,防止外层浇注料脱落、开裂,延长RH炉浸渍管的使用寿命。为实现上述目的,本发明采用以下技术方案实现:一种整体结构稳定的RH炉浸渍管,包括RH环砖、钢结构件、浇注料层、自流料层,RH环砖、自流料层、钢结构件与浇注料层从内至外依次设置;所述RH环砖的底部一高一低相隔交错砌筑,在高RH环砖的侧面设置有浇注料连接凹槽,同时在两个相邻的高RH环砖之间固定有锚固件,高RH环砖的底平面连接钢结构件,浇注料层的底部透过钢结构件底部的豁口渗入到高RH环砖与低RH环砖之间的空间,并通过浇注料连接凹槽和锚固件与RH环砖固定连接;所述自流料层透过钢结构件侧壁上的长形开口与浇注料层固定连接。在所述钢结构件的侧壁上设置有长形开口,在钢结构件的底部设置有豁口。所述浇注料层是由下述原料按重量份配比制成:10mm≥粒径>5mm的板状刚玉20-25份;5mm≥粒径>3mm的板状刚玉10-20份;3mm≥粒径>1mm的板状刚玉10-20份;1≥粒径≥0.088mm的板状刚玉颗粒8-15份;粒径为1mm-0.088mm的电熔镁铝尖晶石8-15份;粒径≤0.044mm的板状刚玉细粉10-20份;粒径≤0.074mm的电熔镁铝尖晶石细粉8-18份;粒径<10μm的电熔镁铝尖晶石微粉2-10份;粒径<5μm的活性氧化铝微粉1-5份;粒径<10μm的煅烧氧化铝微粉0-4份;铝酸钙水泥3-6份;粒径<1μm的硅灰0-2.5份;高效减水剂0.05-0.20份;水泥高效增强剂1-3份;热震稳定剂0.01-0.03份;多晶氧化锆纤维0.1-2份。所述浇注料层的制备方法,包括以下步骤:1)制作复合添加剂:将上述重量份数的粒径为1mm-0.088mm的电熔镁铝尖晶石;高效减水剂;水泥高效增强剂;热震稳定剂放入搅拌磨中共磨、搅拌10-15分钟,封闭待用;2)按照上述重量份数称重,先将10mm≥粒径>5mm的板状刚玉、5mm≥粒径>3mm的板状刚玉、3mm≥粒径>1mm的板状刚玉、1≥粒径≥0.088mm的板状刚玉颗粒、多晶氧化锆纤维,投入到行星式搅拌机中,一次混合2-6分钟;再加入粒径≤0.044mm的板状刚玉细粉、粒径≤0.074mm的电熔镁铝尖晶石细粉、粒径<10μm的电熔镁铝尖晶石微粉、粒径<5μm的活性氧化铝微粉、粒径<10μm的煅烧氧化铝微粉、纯铝酸钙水泥、粒径<1μm的硅灰,最后再加入步骤1)中制备完成待用的复合添加剂,二次混合2-6分钟;然后加入3.8-4.8份的水,三次混合3-5分钟;最后浇注振动成型、养生、脱模、二次养生、干燥、拣选、检验、包装入库。与现有的技术相比,本发明的有益效果是:1)本发明的RH炉浸渍管底部环砖由于优化设计,在RH环砖表面设置了凹槽,在RH环砖的下端打孔穿进金属钢锚固件,最大程度地增强了RH炉浸渍管底部的整体性,最大程度地实现底部浇注料与环砖的一体性,有效地避免了底部浇注料脱落,提高RH炉浸渍管的使用寿命;2)通过加大浇注料临界颗粒尺寸,并同时引进多晶氧化锆纤维、热震稳定剂及水泥高效增强剂,有效改善了浇注料的热震稳定性和高温机械强度,大大减少了浇注料在高温使用时出现的脱落。改进前后部分指标典型值对比见表1。表1:改进前改进后热震稳定性(水冷)7次10次高温抗折强度(1500℃×3小时)10.5MPa12.5MPa高温耐压强度(1500℃×3小时)105MPa130MPa3)本发明的RH炉浸渍管,在金属钢结构件(钢胆)上引入膨胀缝的设计,即在其高度方向上,等距离割开若干细长的孔隙,有效缓解其在高温时,水平方向上的剧烈膨胀,避免相邻的外层浇注料因钢结构件(钢胆)膨胀而被挤压开裂,有效解决了外层浇注料常常发生的脱落现象,提高了RH炉浸渍管的整体性。附图说明图1是本发明一种整体结构稳定的RH炉浸渍管的结构示意图;图2是本发明中钢结构件的结构示意图;图3是本发明中RH环砖的结构示意图;图4是钢结构件设置有长形开口处其两侧自流料、浇注料相互连接的示意图。图中:1-RH环砖、2-钢结构件、3-浇注料层、4-自流料层、5-氩气管、6-长形开口、7-豁口、8-高RH环砖、9-低RH环砖、10-浇注料连接凹槽、11-锚固件。具体实施方式下面结合附图对本发明的实施方式进一步说明:见图1-图4,一种整体结构稳定的RH炉浸渍管,包括RH环砖1、钢结构件2、浇注料层3、自流料层4,RH环砖1、自流料层4、钢结构件2与浇注料层3从内至外依次设置;所述RH环砖1的底部一高一低相隔砌筑,在高RH环砖8的侧面设置有浇注料连接凹槽10,同时在两个相邻的高RH环砖8之间固定有锚固件11,高RH环砖8的底平面连接钢结构件2,浇注料层3的底部透过钢结构件2底部的豁口7渗入到高RH环砖8与低RH环砖9之间的空间,并通过浇注料连接凹槽10和锚固件11与RH环砖1固定连接;所述自流料层4透过钢结构件2侧壁上的长形开口6与浇注料层4固定连接。在所述钢结构件2的侧壁上设置有长形开口6,在钢结构件2的底部设置有豁口7。现有RH炉浸渍管浇注料层的底部与RH环砖连接处,由于彼此热膨胀系数不同,加上喷补维护较难,常常产生底部浇注料与RH环砖衔接不好现象,最终底部浇注料大面积脱落,RH环砖失去依托而下沉,RH炉浸渍管因为解体损坏而无法使用,提前下线。见图3,针对这个问题,本发明的技术方案是优化RH环砖1底部与浇注料层4底部连接处的砖型设计,在RH环砖1底部与浇注料的接触面上设置有浇注料连接凹槽10,同时在RH环砖1上固定金属锚固件11。这样,一方面加大了浇注料与砖的接触面积,使浇注料与砖在两个维度上形成交错镶嵌结构,有效避免浇注料脱落;另一方面通过增设的金属钢锚固件11,大大提高了底部浇注料的整体性。见图2,本发明根据膨胀缝的原理,在保证钢结构件2必要的高温强度和拉力的前提下,在钢结构件2的高度方向上,等距离割开若干细长的孔隙,有效缓解钢结构件2在高温时,水平方向上的剧烈膨胀,避免相邻的浇注料层4因钢结构件2膨胀而被挤压开裂,造成损坏,提前下线。同时,由于在钢结构件2上开口,使钢结构件2内侧的自流料,与钢结构件2外侧的浇注料不再被分开,而是紧密结合,大大地调高了浇注料层4在钢结构件2上的附着性,有效解决了浇注料层4常常发生的脱落现象,提高了RH浸渍管的整体性。所述浇注料层4是由下述原料按重量份配比制成:10mm≥粒径>5mm的板状刚玉20-25份;5mm≥粒径>3mm的板状刚玉10-20份;3mm≥粒径>1mm的板状刚玉10-20份;1≥粒径≥0.088mm的板状刚玉颗粒8-15份;粒径为1mm-0.088mm的电熔镁铝尖晶石8-15份;粒径≤0.044mm的板状刚玉细粉10-20份;粒径≤0.074mm的电熔镁铝尖晶石细粉8-18份;粒径<10μm的电熔镁铝尖晶石微粉2-10份;粒径<5μm的活性氧化铝微粉1-5份;粒径<10μm的煅烧氧化铝微粉0-4份;铝酸钙水泥3-6份;粒径<1μm的硅灰0-2.5份;高效减水剂0.05-0.20份;水泥高效增强剂1-3份;热震稳定剂0.01-0.03份;多晶氧化锆纤维0.1-2份。浇注料层制备原料中主要成分的化学指标及说明见表2;表2:所述浇注料层的制备方法,包括以下步骤:1)制作复合添加剂:将上述重量份数的粒径为1mm-0.088mm的电熔镁铝尖晶石;高效减水剂;水泥高效增强剂;热震稳定剂放入搅拌磨中共磨、搅拌10-15分钟,封闭待用;2)按照上述重量份数称重,先将10mm≥粒径>5mm的板状刚玉、5mm≥粒径>3mm的板状刚玉、3mm≥粒径>1mm的板状刚玉、1≥粒径≥0.088mm的板状刚玉颗粒、多晶氧化锆纤维,投入到行星式搅拌机中,一次混合2-6分钟;再加入粒径≤0.044mm的板状刚玉细粉、粒径≤0.074mm的电熔镁铝尖晶石细粉、粒径<10μm的电熔镁铝尖晶石微粉、粒径<5μm的活性氧化铝微粉、粒径<10μm的煅烧氧化铝微粉、纯铝酸钙水泥、粒径<1μm的硅灰,最后再加入步骤1)中制备完成待用的复合添加剂,二次混合2-6分钟;然后加入3.8-4.8份的水,三次混合3-5分钟;最后浇注振动成型、养生、脱模、二次养生、干燥、拣选、检验、包装入库。实施例1:浇注料层是由下述原料按重量份配比制成:10mm≥粒径>5mm的板状刚玉20份;5mm≥粒径>3mm的板状刚玉10份;3mm≥粒径>1mm的板状刚玉10份;1≥粒径≥0.088mm的板状刚玉颗粒8份;粒径为1mm-0.088mm的电熔镁铝尖晶石8份;粒径≤0.044mm的板状刚玉细粉10份;粒径≤0.074mm的电熔镁铝尖晶石细粉8份;粒径<10μm的电熔镁铝尖晶石微粉2份;粒径<5μm的活性氧化铝微粉1份;铝酸钙水泥3份;高效减水剂0.05份;水泥高效增强剂1份;热震稳定剂0.01份;多晶氧化锆纤维0.1份。浇注料层的制备方法,包括以下步骤:1)制作复合添加剂:将上述重量份数的粒径为1mm-0.088mm的电熔镁铝尖晶石;高效减水剂;水泥高效增强剂;热震稳定剂放入搅拌磨中共磨、搅拌10-15分钟,封闭待用;2)按照上述重量份数称重,先将10mm≥粒径>5mm的板状刚玉、5mm≥粒径>3mm的板状刚玉、3mm≥粒径>1mm的板状刚玉、1≥粒径≥0.088mm的板状刚玉颗粒、多晶氧化锆纤维,投入到行星式搅拌机中,一次混合2-6分钟;加入粒径≤0.044mm的板状刚玉细粉、粒径≤0.074mm的电熔镁铝尖晶石细粉、粒径<10μm的电熔镁铝尖晶石微粉、粒径<5μm的活性氧化铝微粉、粒径<10μm的煅烧氧化铝微粉、纯铝酸钙水泥,最后再加入步骤1)中制备完成待用的复合添加剂,二次混合2-6分钟;然后加入3.8-4.8份的水,三次混合3-5分钟;最后浇注振动成型、养生、脱模、二次养生、干燥、拣选、检验、包装入库。实施例2:浇注料层是由下述原料按重量份配比制成:10mm≥粒径>5mm的板状刚玉25份;5mm≥粒径>3mm的板状刚玉20份;3mm≥粒径>1mm的板状刚玉20份;1≥粒径≥0.088mm的板状刚玉颗粒15份;粒径为1mm-0.088mm的电熔镁铝尖晶石15份;粒径≤0.044mm的板状刚玉细粉20份;粒径≤0.074mm的电熔镁铝尖晶石细粉18份;粒径<10μm的电熔镁铝尖晶石微粉10份;粒径<5μm的活性氧化铝微粉5份;粒径<10μm的煅烧氧化铝微粉4份;铝酸钙水泥6份;粒径<1μm的硅灰2.5份;高效减水剂0.20份;水泥高效增强剂3份;热震稳定剂0.03份;多晶氧化锆纤维2份。浇注料层的制备方法同实施例1。实施例3:浇注料层是由下述原料按重量份配比制成:10mm≥粒径>5mm的板状刚玉21份;5mm≥粒径>3mm的板状刚玉11份;3mm≥粒径>1mm的板状刚玉11份;1≥粒径≥0.088mm的板状刚玉颗粒9份;粒径为1mm-0.088mm的电熔镁铝尖晶石9份;粒径≤0.044mm的板状刚玉细粉11份;粒径≤0.074mm的电熔镁铝尖晶石细粉9份;粒径<10μm的电熔镁铝尖晶石微粉3份;粒径<5μm的活性氧化铝微粉2份;粒径<10μm的煅烧氧化铝微粉1份;铝酸钙水泥4份;粒径<1μm的硅灰1份;高效减水剂0.06份;水泥高效增强剂2份;热震稳定剂0.02份;多晶氧化锆纤维0.2份。浇注料层的制备方法同实施例1。实施例4:浇注料层是由下述原料按重量份配比制成:10mm≥粒径>5mm的板状刚玉22份;5mm≥粒径>3mm的板状刚玉12份;3mm≥粒径>1mm的板状刚玉12份;1≥粒径≥0.088mm的板状刚玉颗粒10份;粒径为1mm-0.088mm的电熔镁铝尖晶石10份;粒径≤0.044mm的板状刚玉细粉12.5份;粒径≤0.074mm的电熔镁铝尖晶石细粉10份;粒径<10μm的电熔镁铝尖晶石微粉4份;粒径<5μm的活性氧化铝微粉3份;粒径<10μm的煅烧氧化铝微粉2份;铝酸钙水泥5份;粒径<1μm的硅灰1.5份;高效减水剂0.07份;水泥高效增强剂2份;热震稳定剂0.02份;多晶氧化锆纤维0.3份。浇注料层的制备方法同实施例1。实施例5:浇注料层是由下述原料按重量份配比制成:10mm≥粒径>5mm的板状刚玉23份;5mm≥粒径>3mm的板状刚玉15份;3mm≥粒径>1mm的板状刚玉15份;1≥粒径≥0.088mm的板状刚玉颗粒12份;粒径为1mm-0.088mm的电熔镁铝尖晶石13份;粒径≤0.044mm的板状刚玉细粉16份;粒径≤0.074mm的电熔镁铝尖晶石细粉15份;粒径<10μm的电熔镁铝尖晶石微粉6份;粒径<5μm的活性氧化铝微粉4份;粒径<10μm的煅烧氧化铝微粉3份;铝酸钙水泥5份;粒径<1μm的硅灰2份;高效减水剂0.10份;水泥高效增强剂2份;热震稳定剂0.02份;多晶氧化锆纤维1份。浇注料层的制备方法同实施例1。实施例6:浇注料层是由下述原料按重量份配比制成:10mm≥粒径>5mm的板状刚玉23份;5mm≥粒径>3mm的板状刚玉17份;3mm≥粒径>1mm的板状刚玉18份;1≥粒径≥0.088mm的板状刚玉颗粒14份;粒径为1mm-0.088mm的电熔镁铝尖晶石14份;粒径≤0.044mm的板状刚玉细粉19.5份;粒径≤0.074mm的电熔镁铝尖晶石细粉16份;粒径<10μm的电熔镁铝尖晶石微粉8份;粒径<5μm的活性氧化铝微粉5份;粒径<10μm的煅烧氧化铝微粉4份;铝酸钙水泥6份;粒径<1μm的硅灰0.5份;高效减水剂0.15份;水泥高效增强剂3份;热震稳定剂0.03份;多晶氧化锆纤维1.5份。浇注料层的制备方法同实施例1。本发明通过在浇注料层4的制备原料中加入多晶氧化锆纤维,增加其基质强度。通过在原料中引入10mm≥粒径>5mm的板状刚玉大颗粒,增强浇注料的热震性能,改善材料的耐剥落性。通过在原料中加入热震稳定剂,使材料内部气孔均匀分散,也是为了进一步增强浇注料的热震性能。通过在原料中加入水泥高效增强剂,有利于促进浇注料层基质高温烧结,调整产品整体性能均一性,改善材料强度分布,从而达到改善浇注料的高温整体强度,减少或避免浇注料局部脱落。实施效果:按以上方案实施之后,RH炉浸渍管的整体完整性改善极为明显。RH炉浸渍管改进前后使用寿命初步统计见表3:表3从表3可以看出,通过本发明所采用的结构及浇注料层的制备方法,改善RH炉浸渍管的整体性,使浸渍管的使用寿命提高明显,提高幅度为19.89%,这样一方面很好地满足了钢厂冶炼的要求,同时也为耐火材料生产厂家创造了可观的效益。当前第1页1 2 3