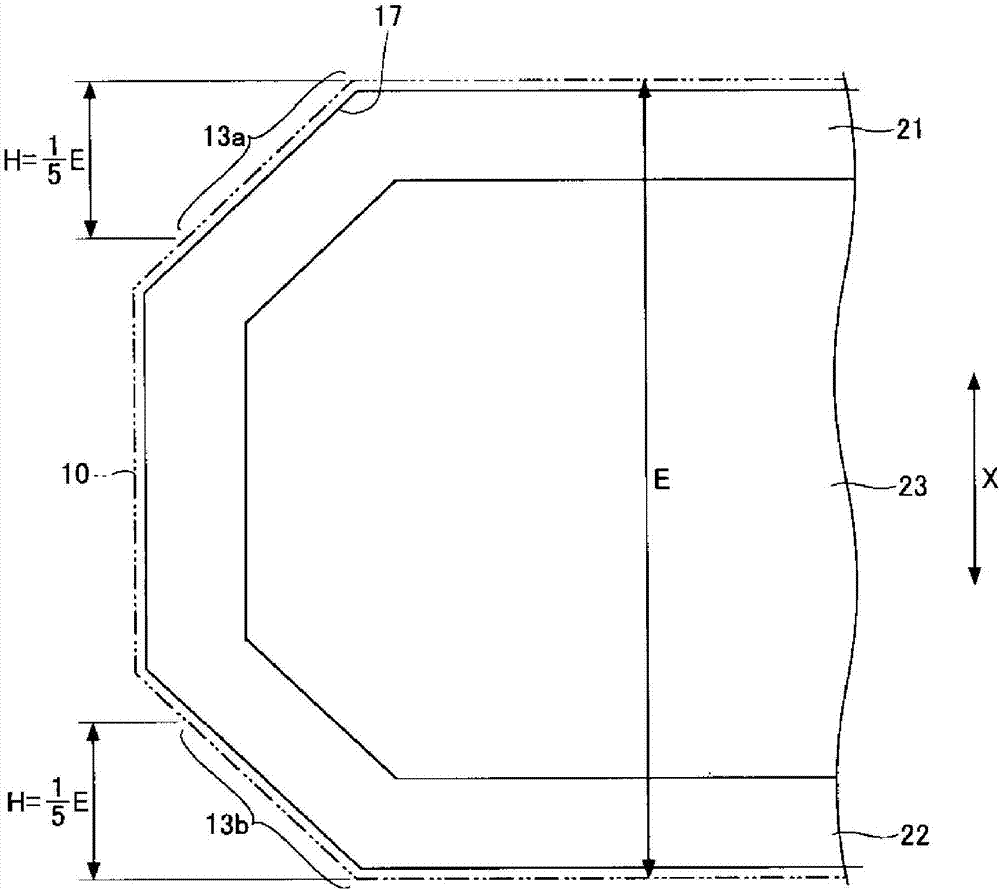
本申请是申请日为2013年5月21日、国际申请号为pct/jp2013/064130、中国申请号为201380027498.4的中国专利申请的分案申请。本发明涉及适合于手机、便携信息终端(pda)、平板pc等移动设备、触控面板、大型液晶电视机等大型薄型电视机、车载仪表显示装置等显示装置的保护玻璃等的化学强化玻璃板。
背景技术:
:近年来,对于手机、pda、平板pc等移动设备、触控面板、液晶电视机等显示装置而言,使用用于保护显示器并且改善美观的保护玻璃的情况增多。另外,有时会对液晶电视机等薄型电视机的保护玻璃等进行例如具有防反射、防止冲击破损、屏蔽电磁波、屏蔽近红外线、修正色调等功能的膜的形成等表面加工。对于这样的显示装置,为了减小薄型设计所产生的差异并且减小负担以便于移动,要求轻量化、薄型化。因此,在显示器保护用途中使用的保护玻璃也要求减薄。但是,如果减薄保护玻璃的厚度,则强度降低,在固定型设备的情况下,有时会由于物体的飞来、落下所产生的冲击而使保护玻璃自身破裂,或者,在便携设备的情况下,有时会由于使用中的落下等而使保护玻璃自身破裂,存在无法发挥保护显示装置这样的原来的作用的问题。为了解决上述问题,考虑提高保护玻璃的强度,作为其方法,一般已知在玻璃表面上形成压应力层的方法。作为在玻璃表面上形成压应力层的方法,代表的方法是利用风冷等将加热至软化点附近的玻璃板表面快速冷却的风冷强化法(物理强化法)和在玻璃化转变温度以下的温度下利用离子交换将玻璃板表面的离子半径小的碱金属离子(典型地为li离子、na离子)交换为离子半径更大的碱离子(典型地为k离子)的化学强化法。如前所述,要求保护玻璃的厚度要薄。但是,在对作为保护玻璃所要求的、厚度小于2mm的薄玻璃板应用风冷强化法时,难以产生表面与内部的温度差,因此,难以形成压应力层,无法得到作为目标的高强度这样的特性。因此,通常使用通过化学强化法进行了强化的保护玻璃。作为这样的保护玻璃,广泛使用对钠钙玻璃进行化学强化而得到的保护玻璃(例如,参考专利文献1)。钠钙玻璃价格低廉,并且具有能够使通过化学强化形成在玻璃表面上的压应力层的表面压应力s为550mpa以上的特征,但存在难以使压应力层的厚度dol(以下,有时也称为压应力层深度)为20μm以上的问题。另外,后述的例28的玻璃为钠钙玻璃。因此,提出了对与钠钙玻璃不同的sio2-al2o3-na2o系玻璃进行化学强化而得到的玻璃作为这样的保护玻璃(例如,参考专利文献2、3)。上述sio2-al2o3-na2o系玻璃具有不仅能够使上述s为550mpa以上、而且也能够使上述dol为20μm以上的特征。另外,迄今为止已知具有触控面板功能的显示装置(例如,手机、便携信息终端(pda)、平板pc等)。这样的显示装置通过将搭载有触控传感器的玻璃基板配置到液晶显示器(lcd)上并进一步在其上搭载化学强化玻璃作为保护玻璃来构成(图33(a))。近年来,如专利文献4所述,为了进一步轻量化、薄型化,开发了通过将触控传感器直接搭载到化学强化玻璃上而省略玻璃基板并将搭载有触控传感器的化学强化玻璃配置到液晶显示器(lcd)上的、所谓二合一(2-in-1)方式的显示装置(图33(b))。作为这样的二合一方式的显示装置中使用的带触控传感器的化学强化玻璃,有三种化学强化玻璃正在流通。第一种是压应力层的表面压应力s为500mpa、压应力层深度dol为9μm的化学强化玻璃,第二种是压应力层的表面压应力s为722mpa、压应力层深度dol为32μm的化学强化玻璃,第三种是压应力层的表面压应力s为623mpa、压应力层深度dol为19μm的化学强化玻璃。现有技术文献专利文献专利文献1:日本特开2007-11210号公报专利文献2:美国专利申请公开第2009/0298669号说明书专利文献3:美国专利申请公开第2008/0286548号说明书专利文献4:日本特开2011-197708号公报技术实现要素:发明所要解决的问题移动设备从手、口袋、包中掉落而使其保护玻璃产生伤痕(压痕)的机会多,另外,也有时会踩到掉落的移动设备或者在将移动设备装入口袋中的状态下坐在移动设备上面,因此,对保护玻璃施加大的负荷的机会也多。以往使用的保护玻璃的表面压应力s为650~750mpa,但鉴于如上所述施加大的负荷的可能性,近年来,要求表面压应力s比650~750mpa大的保护玻璃。这样施加于保护玻璃的负荷在各种各样的情况下发生。结果,保护玻璃有时会产生破损,但破损的方式在各个情况下有所不同。本发明人对这些破损的方式进行了分析,结果发现,破损的方式可以分为下述四种方式。(a)保护玻璃的正面侧周缘该现象容易由于在移动设备落下到地面等时移动设备的周缘碰撞到小的物体而产生。(b)保护玻璃的背面侧周缘该现象容易由于在移动设备落下到地面等时移动设备的周缘碰撞到大的物体而产生。(c)保护玻璃的背面侧主面该现象容易由于在移动设备落下到地面等时移动设备的主面碰撞到曲率半径大的近似球面状的物体而产生。(d)保护玻璃的正面侧主面该现象容易由于在移动设备落下到地面等时移动设备的主面碰撞到存在于地面等上的锐利的砂、石头等而产生。其中,关于(d)的破损,本发明人有下述发现。即,自保护玻璃的正面侧主面产生的破损容易在该主面碰撞到锐利的物体时产生,因此,会产生裂纹穿透表面压应力层而到达内部拉应力层的结果。因此,即使增大如上提出的表面压应力s的值,也难以减少(d)的破损。另外,即使增大表面压应力层的厚度dol,dol的值最多也就是100μm左右,无法完全防止由于与锐利的物体碰撞而产生的裂纹穿透表面压应力层。在更广泛地使用这样的大大小小的显示装置时,与使用少时相比,保护玻璃产生破损的情况多样化。本发明的目的在于提供应对这样的多样化情况而不易产生破损的化学强化玻璃板、保护玻璃、带触控传感器的化学强化玻璃。另外,为了对多种破损情况进行说明,列举了保护玻璃的例子作为一例,但本发明不限于此。用于解决问题的手段本发明人在对显示装置中使用的保护玻璃和带触控传感器的化学强化玻璃的破损方式进行考察、研究的基础上发现,保护玻璃等的破损方式分为上述四种方式,从而完成了本发明。以下,参考图15对四种破损方式更详细地进行说明。另外,在本说明书中,带触控传感器的化学强化玻璃是指搭载有触控传感器的化学强化玻璃,在仅称为化学强化玻璃时,是指未搭载触控传感器的化学强化玻璃自身。(a)保护玻璃的正面侧周缘保护玻璃的正面侧周缘的破损也称为赫兹断裂(赫兹裂纹破裂),是在对保护玻璃等的端面施加冲击时以产生在冲击面(端面)上的被称为赫兹圆锥的圆锥形断面为起点发生断裂的破损。对于该保护玻璃的正面侧周缘的破损,可以通过后述的赫兹破裂试验和四点弯曲试验来测定其耐性。(b)保护玻璃的背面侧周缘保护玻璃的背面侧周缘的破损是在对保护玻璃的端面施加冲击时以因产生在与冲击面相反的一侧的非冲击面(端面)上的内部拉应力而产生的伤痕为起点发生断裂的破损。对于该保护玻璃的背面侧周缘的破损,可以通过后述的背面破裂试验和四点弯曲试验来测定其耐性。(c)保护玻璃的背面侧主面保护玻璃的背面侧主面的破损是在对保护玻璃的主面施加冲击时以因产生在与冲击面相反的一侧的非冲击面(主面)上的内部拉应力而产生的伤痕为起点发生断裂的破损。对于该保护玻璃的背面侧主面的破损,可以通过后述的落球试验来测定其耐性。(d)保护玻璃等的正面侧主面保护玻璃的正面侧主面的破损是在对保护玻璃的主面施加冲击时以穿透压应力层的伤痕为起点而产生使玻璃以较慢的速度破裂的慢速裂纹所引起的破裂(以下,将这样的玻璃的破裂方式也称为慢速裂纹破裂)。该慢速裂纹破裂是破裂碎片一般较少、最典型地为自断裂起点延伸出一条裂纹而使带触控传感器的化学强化玻璃破裂为两片的现象,是在手机、便携信息终端(pda)、平板pc等具有触控面板功能的显示装置的保护玻璃等中典型地观察到的破裂。手机、便携信息终端等是使用者随身携带的设备,因此,由于落下等而受到冲击的可能性高,与产生穿透压应力层的伤痕的物质接触的可能性高。另外,对于平板pc而言,尺寸典型地为150~350mm×100~250mm,并且重量为150~1000g,尽管尺寸大且重量重,但也是使用者随身携带的设备。作为使用方法的例子,例如有:在厨房将平板pc立起来边看菜谱边做料理,或者在会议室将平板pc立起来边看资料边讨论等的使用方式。因此,在使手机、便携信息终端等落下的情况下,或者在误使平板pc落下或使其倒下的情况下,容易产生穿透表面压应力层的伤痕,从而更容易发生慢速裂纹破裂。在此,以平板pc的保护玻璃中发生的慢速裂纹破裂为例,参考图16~图22对慢速裂纹破裂进行说明。平板pc以包围图像显示部的方式设置有近似矩形的框架,保护玻璃被支撑于框架上。如图16所示,在平板pc1落下到地面(沥青混凝土等)上并以保护玻璃2朝下的状态与沥青混凝土3中的碎石4上的砂5等接触时,压应力作用于断裂起点o,拉应力作用于保护玻璃的图像显示部侧(图17(a))。接着,拉应力作用于断裂起点o,裂纹c延伸,保护玻璃2破裂(图17(b))。另外,断裂起点有时也产生在保护玻璃的中央部,但框架会限制保护玻璃的弯曲,产生在断裂起点的应力增大,因此断裂起点多产生在由框架支撑的区域的一部分。这种保护玻璃2的破裂不限于在落下到地面上的情况下发生,在落下到会议室、起居室、厨房等的地板面上时也会发生。图18(a)是表示发生了慢速裂纹破裂的平板pc的照片的图,图18(b)是表示从上方观察断裂起点时的放大照片的图,图18(c)是表示从侧面观察断裂起点时的照片的图。此时的保护玻璃的破裂,由图18(c)的断裂面可知,比压应力层深度深的伤痕成为断裂起点。在图18(a)和图18(b)中,自断裂起点延伸出一条裂纹而使保护玻璃破裂为两片。进一步观察该图18(c)所示的断裂面时,在比压应力层深度深的断裂起点的周围,观察到如镜子般光滑的镜面半径(mirrorradius)长的镜面(mirror)。图19是示意性地表示图18(c)的断裂面的图。断裂面反映出断裂的过程即断裂起点、断裂的进行方向、断裂是缓慢进行还是快速进行等因素。根据该慢速裂纹破裂的断裂面分析,镜面半径长的镜面意味着以小的应力使断裂进行,这样的光滑的断裂面意味着裂纹以比音速慢得多的速度缓慢地增长。因此,根据图18(c)的断裂面可知,在保护玻璃中形成比压应力层深度深的起点后,裂纹缓慢增长,以小的应力使断裂进行。由于这样的慢速裂纹破裂而破裂的保护玻璃的破裂碎片达到数片至(根据情况)数十片。典型地为2片至20片,自图18(a)和(b)所示的断裂起点延伸出一条裂纹而使保护玻璃破裂为两片的例子是慢速裂纹破裂的象征性的例子。是否为慢速裂纹破裂以下述方式更细微地进行辨别。首先,如果看不出断裂起点,则不能称为慢速裂纹破裂。另外,在通过对该断裂起点附近进行观察而确认到穿透压应力层的伤痕、即比压应力层深度深的伤痕为断裂起点的情况下,为慢速裂纹破裂。另外,在镜面半径长、断裂截面为镜面且未观察到雾状面、锯齿面的情况下,为慢速裂纹破裂。接着,为了与慢速裂纹破裂进行对比,对于不是慢速裂纹破裂的保护玻璃的破裂方式(以下,也称为非慢速裂纹破裂)进行说明。作为非慢速裂纹破裂,对于将努普压头压入玻璃表面而产生的保护玻璃的破裂进行说明。图20是表示从侧面观察非慢速裂纹破裂所致的保护玻璃的断裂起点时的照片的图,图21是示意性地表示图20的断裂面的图。观察该非慢速裂纹破裂的断裂面时,在压应力层内形成断裂起点,在周围观察到如镜子般光滑的镜面半径短的镜面,进而在镜面的周围存在雾状面(mist)。根据该非慢速裂纹破裂的断裂面分析,镜面半径短的镜面意味着以大的应力使断裂进行,雾状面意味着裂纹快速增长。因此,根据图20的断裂面可知,在保护玻璃中形成比压应力层深度浅的断裂起点后,以大的应力使断裂进行,裂纹快速增长。发生非慢速裂纹破裂时,如图22所示,保护玻璃由于以蜘蛛网状延伸的多条裂纹而成为多片(20片以上)的玻璃片(以下,将这样的破裂方式也称为蛛网状破裂)。由此可知,慢速裂纹破裂和非慢速裂纹破裂以完全不同的模式产生断裂。对于慢速裂纹破裂而言,断裂起点产生在超过压应力层的区域、即内部拉应力层(伤痕的深度典型地为数十微米至数百微米,由化学强化产生的压应力层为数微米至数十微米)中,因此,在容易发生慢速裂纹破裂的显示装置中,需要选择具有耐慢速裂纹破裂性强的机械特性的化学强化玻璃。对于该慢速裂纹破裂(保护玻璃的正面侧主面的破损),可以通过后述的锥形金刚石压头试验和砂纸落球试验来测定其耐性。另外,非慢速裂纹破裂是为了与慢速裂纹破裂进行对比而强制发生的断裂模式,不是归类于上述四种方式中的破损方式。本发明的化学强化玻璃板、保护玻璃、带触控传感器的化学强化玻璃及显示装置能够抑制因上述四种破损方式中的任意一种方式引起的破裂。本发明提供下述方式。(1)一种化学强化玻璃板,其为具有正主面和背主面以及该正主面与背主面间的端面的化学强化玻璃板,其中,表面压应力为800mpa以上,内部拉应力为42mpa以下,并且,在所述端面中设置有倒角部,在所述倒角部的板厚方向的距离为板厚的1/5以内的部分,不存在深度超过20μm的潜伤,所述化学强化玻璃板以基于下述氧化物的摩尔百分率计,含有56~75%的sio2、5~20%的al2o3、8~22%的na2o、0~10%的k2o、0~14%的mgo、0~5%的zro2、0~5%的cao。(2)如(1)所述的化学强化玻璃板,其中,表面压应力为850mpa以上。(3)如(1)所述的化学强化玻璃板,其中,所述内部拉应力为35mpa以下。(4)如(3)所述的化学强化玻璃板,其中,所述内部拉应力为30mpa以下。(5)如(1)所述的化学强化玻璃板,其中,表面压应力层的厚度为15~40μm。(6)如(5)所述的化学强化玻璃板,其中,所述表面压应力层的厚度为20~35μm。(7)如(1)所述的化学强化玻璃板,其中,板厚为0.8mm以下。(8)如(1)所述的化学强化玻璃板,其中,sio2、al2o3、na2o、mgo和b2o3的含量的合计为98%以上。(9)如(1)所述的化学强化玻璃板,其中,sio2、al2o3、na2o和mgo的含量的合计为98%以上。(10)如(1)所述的化学强化玻璃板,其中,从na2o含量中减去al2o3含量而得到的差小于5%。(11)如(1)所述的化学强化玻璃板,其中,在所述倒角部的板厚方向的距离为板厚的1/5以内的部分,不存在深度为10μm以上的潜伤。(12)如(1)所述的化学强化玻璃板,其中,在所述主面上设置有触控传感器。(13)一种化学强化玻璃板,其为具有正主面和背主面以及该正主面与背主面间的端面的化学强化玻璃板,其中,表面压应力为800mpa以上,内部拉应力为42mpa以下,并且,在所述端面中设置有倒角部,在所述倒角部的板厚方向的距离为板厚的1/5以内的部分,不存在深度超过20μm的潜伤,所述化学强化玻璃板以基于下述氧化物的摩尔百分率计,含有60~75%的sio2、11~15%的al2o3、11~16%的na2o、0~5%的k2o、0~10%的mgo、0~1%的zro2、0~5%的cao。(14)如(13)所述的化学强化玻璃板,其中,表面压应力为850mpa以上。(15)如(13)所述的化学强化玻璃板,其中,所述内部拉应力为35mpa以下。(16)如(15)所述的化学强化玻璃板,其中,所述内部拉应力为30mpa以下。(17)如(13)所述的化学强化玻璃板,其中,表面压应力层的厚度为15~40μm。(18)如(17)所述的化学强化玻璃板,其中,所述表面压应力层的厚度为20~35μm。(19)如(13)所述的化学强化玻璃板,其中,板厚为0.8mm以下。(20)如(13)所述的化学强化玻璃板,其中,sio2、al2o3、na2o、mgo和b2o3的含量的合计为98%以上。发明效果根据本发明,能够得到能耐受多种破损情况的化学强化玻璃板、保护玻璃、带触控传感器的化学强化玻璃及显示装置。附图说明图1是本发明的第一实施方式的化学强化玻璃板的局部侧截面图。图2是本发明的第一实施方式的化学强化玻璃板的局部侧截面图。图3是本发明的第一实施方式的化学强化玻璃板的局部侧截面图。图4是表示本发明的第二实施方式的化学强化玻璃板的制造方法的侧截面图。图5是表示本发明的第二实施方式的化学强化玻璃板的制造方法的侧截面图。图6是表示本发明的第二实施方式的化学强化玻璃板的制造方法的侧截面图。图7是表示本发明的第三实施方式的化学强化玻璃板的制造方法的侧截面图。图8是表示本发明的第三实施方式的化学强化玻璃板的制造方法的侧截面图。图9是表示本发明的第三实施方式的化学强化玻璃板的制造方法的侧截面图。图10是表示本发明的第四实施方式的化学强化玻璃板的制造方法的侧截面图。图11是表示本发明的第四实施方式的化学强化玻璃板的制造方法的侧截面图。图12是构成本发明的第五实施方式的带触控传感器的化学强化玻璃的主要部分的俯视图。图13是图12的a-a线截面图。图14是对本发明的第六实施方式的带触控传感器的化学强化玻璃的制造方法进行说明的图。图15是对保护玻璃等中发生的四种破损的方式进行说明的图。图16是表示在平板pc落下时保护玻璃发生慢速裂纹破裂的状况的示意图。图17是示意性地表示慢速裂纹破裂的发生机制的图,(a)是表示断裂起点的图,(b)是表示裂纹的图。图18(a)是表示发生了慢速裂纹破裂的带触控传感器功能的平板pc的照片的图,图18(b)是表示从上方观察断裂起点时的放大照片的图,图18(c)是表示从侧面观察断裂起点时的照片的图。图19是示意性地表示图18(c)的断裂面的图。图20是表示从侧面观察发生了非慢速裂纹破裂的保护玻璃的断裂起点时的照片的图。图21是示意性地表示图20的断裂面的图。图22是表示发生了蛛网状破裂的保护玻璃的照片的图。图23是砂纸落球试验的示意图。图24是示意性地表示在图23的砂纸落球试验中的化学强化玻璃发生破裂的机制的图,(a)是表示断裂起点的图,(b)是表示裂纹的图。图25(a)是表示在将化学强化玻璃配置在由花岗岩构成的基台上并使化学强化玻璃的上表面与p30的砂纸的摩擦面接触的状态下使φ0.75英寸、4g的不锈钢性的球体从17cm的高度落下而发生了慢速裂纹破裂的保护玻璃的照片的图,图25(b)是表示从侧面观察断裂起点时的照片的图。图26(a)是表示p30的砂纸的放大照片的图,图26(b)是表示沥青混凝土的放大照片的图,图26(c)是表示p30的砂纸尖端的角度分布和砂的尖端的角度分布的图。图27是表示由四棱锥压头压入试验得到的内部拉应力t与载荷f50的关系性的图。图28是表示由四点弯曲试验得到的表面压应力s与弯曲强度的关系性的图。图29是表示由落球试验得到的表面压应力s与断裂能的关系性的图。图30是表示由四点弯曲试验得到的表面压应力层的厚度dol与弯曲强度的关系性的图。图31是表示本发明的一个方式的化学强化玻璃板的四点弯曲强度的韦伯图。图32(a)是表示赫兹破裂试验的结果的图,图32(b)是表示背面破裂试验的结果的图,图32(c)是表示落球试验的结果的图,图32(d)是表示砂纸落球试验的结果的图。图33(a)是表示现有的具有触控面板功能的显示装置的示意图,图33(b)是二合一方式的显示装置的示意图。具体实施方式如上所述,本发明人发现了保护玻璃的破损方式可以分为下述四种,并且发现了对(a)保护玻璃的正面侧周缘、(b)保护玻璃的背面侧周缘、(c)保护玻璃的背面侧主面、(d)保护玻璃的正面侧主面这四种破损方式中的任意一种方式均具有高强度的化学强化玻璃。从(d)的破损的观点考虑,通过使内部拉应力t为42mpa以下,能够减小破损的程度。内部拉应力t优选为40mpa以下,更优选为37mpa以下,更优选为35mpa,进一步优选为34mpa以下,特别优选为30mpa。内部拉应力t过小时,无法增大表面压应力s、压应力层深度,因此,无法综合性地提高强度。因此,内部拉应力t的下限为3mpa以上,优选为8mpa以上,更优选为9mpa以上,进一步优选为10mpa以上。从(d)的破损的观点考虑,关于玻璃的耐性,从是否会在玻璃表面上残留伤痕的观点考虑,何种物质与玻璃接触是很重要的。特别是与(主要由sio2等形成的)砂等硬的物质接触时,这些物质会压入玻璃表面而残留压痕以及由此产生的裂纹或者擦伤。此时,从是否会由该伤痕产生裂纹的观点考虑,所接触的物质的角度是很重要的。到目前为止,关于保护玻璃等的对裂纹产生的耐性,一直使用维氏压头来进行试验,但本发明人认为应当在使用角度更锐利的压头的情况下时分出裂纹产生的优劣,因此,使用进行了化学强化处理以使得内部拉应力t不同的多个样品,测定了在使用维氏硬度计中顶角为110°的锥形金刚石压头施加载荷时发生断裂的概率达到50%时的载荷f50(单位:kgf)。另外,该测定使用future-tech制造的维氏硬度计flc-50v来实施。将表示由上述的四棱锥压头压入试验得到的内部拉应力t与f50的关系性的图示于图27中。内部拉应力t越大,则在越小的载荷下发生断裂。由该测定结果确认,为了抑制(d)的破损,优选内部拉应力t更低。另外,作为用于重现(d)保护玻璃的正面侧主面的破损的方法,本发明人发现了与锥形金刚石压头试验不同的以下说明的砂纸落球试验。如图23所示,砂纸落球试验为如下试验:将表面形成有压应力层的化学强化玻璃320配置于基台331上,使化学强化玻璃320与包含大小为压应力层深度以上的研磨材料的砂纸332的摩擦面332a接触,使铁球等球体333从上方落下。此时,砂纸332优选配置于化学强化玻璃320的上方,化学强化玻璃320的上表面330a与砂纸332的摩擦面332a接触,球体333落下到砂纸332的与摩擦面332a相反的一侧的表面332b上。作为基台331,优选由花岗岩这样的硬石形成。由此,能够排除容易产生成为断裂起点的伤痕的由框架支撑的保护玻璃的区域这样的应力集中部位(応力の逃げ場)。但是,基台331的材质的弹性模量、挠度可以根据目的来改变,可以适当选择直材(ストレート材)、玻璃、中央被挖空的框架等。砂纸不限于研磨纸(砂纸、jisr6252:2006),包括在基材上利用胶粘剂涂装有研磨材料的研磨纸或与其相当的研磨纸,例如包括研磨布(jisr6251:2006)、耐水研磨纸(jisr6253:2006)等。在砂纸332中,根据所含的研磨材料的粒度,存在p12~p2500号(jisr6252、2006)。研磨材料典型地为氧化铝、碳化硅。如果将沥青混凝土中含有的砂的粒径假定为0.06mm~1mm,则作为砂纸332中含有的研磨材料的粒度,p30~p600大致与此对应。例如,如果将压应力层的深度假定为30μm,则作为含有比压应力层深度大的研磨材料的砂纸,可选择p30(d3:710μm)、p100(d3:180μm)、p320(d3:66.8μm)、p600(d3:43.0μm)等砂纸。球体333的材质、重量可以根据目的来改变,典型地,使用不锈钢制的4~150g的不锈钢球。这样,通过使球体333落下到配置于基台331上的化学强化玻璃320上,利用砂纸332中含有的研磨材料在化学强化玻璃320的上表面330a侧的比压应力层深的部位产生断裂起点o。此时,压应力作用于断裂起点o,拉应力作用于其周围(图24(a))。接着,拉应力作用于断裂起点o,裂纹c延伸,保护玻璃破裂(图24(b))。即,虽然断裂起点的表面存在上表面与下表面的差异,但以与图17(a)和(b)中说明的慢速裂纹破裂相同的机制发生破裂。图25(a)是表示在将化学强化玻璃320配置在由花岗岩构成的基台上并使化学强化玻璃320的上表面与p30的砂纸332的摩擦面接触的状态下使φ0.75英寸、4g的由不锈钢构成的球体333从17cm的高度落下而发生了慢速裂纹破裂的保护玻璃的照片的图,图25(b)是表示从侧面观察断裂起点时的照片的图。化学强化玻璃中,一条裂纹延伸而使保护玻璃破裂为两片,另外,图25(b)显示出与图18(c)同样的断裂面,可知以与慢速裂纹破裂相同的机制发生了破裂。图26(a)是p30的砂纸的放大照片,图26(b)是沥青混凝土(从横滨采集)的放大照片,图26(c)是表示p30砂纸尖端的角度分布和砂的尖端的角度分布的图。图26(c)是分别观测了砂纸的144个部位、砂的149个部位并以横轴表示砂纸或砂的尖端角度、以纵轴表示频率而得到的图。本发明中,基于p30砂纸中含有的作为研磨材料的氧化铝与沥青混凝土中含有的碎石等的形状近似性,选择了p30砂纸。本发明中,进行了如下的砂纸落球试验:将化学强化玻璃配置在由花岗岩构成的基台上,在使保护玻璃的上表面与p30(jisr6252、2006)砂纸的摩擦面接触的状态下,使φ0.75英寸、29g的由不锈钢构成的球体从上方落下。测定在以下的条件下进行。准备20张将下述的a~e这五种玻璃材料的玻璃a4~e4切割为50mm×50mm的尺寸并进行研磨而得到的化学强化玻璃,将20张玻璃依次配置在由花岗岩构成的基台上,在使玻璃的上表面与p30(jisr6252、2006)砂纸的摩擦面接触的状态下,使φ0.75英寸、29g的由不锈钢构成的球体从上方落下,算出断裂时的落球高度的简单平均值,将其作为平均断裂高度。另外,玻璃a4~e4具有表1所示的性能。表1和图32(d)中示出了各玻璃的砂纸落球试验的试验结果。另外,表1中,t表示内部拉应力,s表示表面压应力。另外,玻璃a1~a4由玻璃材料a形成,玻璃b1~b4由玻璃材料b形成,玻璃c1~c4由玻璃材料c形成,玻璃d1~d4由玻璃材料d形成,玻璃e1~e4由玻璃材料e形成,切割为50mm×50mm,进行研磨,利用#600的砂轮进行c倒角。然后,对各玻璃进行了化学强化。玻璃材料a具有以下的组成。玻璃材料b具有以下的组成。玻璃材料c具有以下的组成。玻璃材料d具有以下的组成。玻璃材料e具有以下的组成。表1由图32(d)确认,(d)保护玻璃的正面侧主面的破损存在如下倾向:破损时的落球高度与内部拉应力t成反比例,内部拉应力t越小,则破损时的落球高度越高,即,越不易发生破裂。另外认为,通过尽可能地增大表面压应力s的值,能够减少(a)、(b)、(c)的破损,因此,本发明的玻璃板的表面压应力s设定为800mpa以上。从(a)、(b)、(c)的破损的观点考虑,表面压应力s优选更高。表面压应力s优选为850mpa以上,更优选为900mpa以上,进一步优选为950mpa以上,特别优选为1000mpa以上。为了考察从(a)、(b)的破损的观点来看的玻璃的耐性与表面压应力s的关联性,使用进行了化学强化处理以使得表面压应力s不同的多个样品,将两个支撑点的间隔设定为40mm,将两个载荷点的间隔设定为10mm,进行四点弯曲试验(jisr1601),测定弯曲强度。另外,该测定使用岛津制作所制造的オートグラフags-x来实施。将表示由上述的四点弯曲试验得到的表面压应力s与弯曲强度的关系性的图示于图28中。表面压应力s越高,则弯曲强度也越增加。由该测定结果确认,为了抑制(a)、(b)的破损,优选表面压应力s更高。另外,对于(a)保护玻璃的正面侧周缘的破损,可以通过赫兹破裂试验求出破裂强度。赫兹破裂试验是通过使超硬材料的细径的圆柱棒碰撞到玻璃端面上而在玻璃端面的表面中产生赫兹应力、由此发生赫兹裂纹破裂的试验,通过圆柱棒的冲击能(碰撞能j=高度m×重量kg×9.8m/秒2),可以测定对(a)的破损的耐性。测定在以下的条件下进行。将上述的a~e这五种玻璃材料的玻璃a1~e1切割为50mm×50mm的尺寸并进行研磨,利用#600的砂轮进行c倒角。然后,对各玻璃进行化学强化。将上述的玻璃配置到基台上,使φ3mm的超硬锤头以摆式碰撞到其端面上,使玻璃的端面正面侧发生赫兹破裂,将上述操作重复20次,计算出断裂时的圆柱棒的冲击能的简单平均值,将其作为平均断裂能。另外,玻璃a1~e1具有表2所示的性能。表2和图32(a)中示出了各玻璃的赫兹破裂试验的试验结果。表2另外,对于(b)保护玻璃的背面侧周缘的破裂,可以通过背面破裂试验求出破裂强度。背面破裂试验是通过使粗径的超硬材料的圆柱棒碰撞到玻璃端面上而在玻璃端面的背面侧产生冲击拉应力、从而发生端面/背面破裂的试验,通过圆柱棒的冲击能(碰撞能j=高度m×重量kg×9.8m/秒2),可以测定对(b)的破损的耐性。测定在以下的条件下进行。将上述的a、c~e这四种玻璃材料的玻璃a2、c2~e2切割为50mm×50mm的尺寸并进行研磨,利用#600的砂轮进行c倒角。然后,对各玻璃进行化学强化。将上述的玻璃配置到基台上,使φ40mm的超硬锤头以摆式碰撞到其端面上,使玻璃的端面背面侧发生冲击性断裂,将上述操作重复20次,计算出断裂时的圆柱棒的冲击能的简单平均值,将其作为平均断裂能。另外,玻璃a2、c2~e2具有表3所示的性能。表3和图32(b)中示出了各试验结果。表3接着,为了考察从(c)的破损的观点来看的玻璃的耐性与表面压应力s的关联性,使用进行了化学强化处理以使得表面压应力s不同的多个样品,通过落球试验进行了断裂能测定。落球试验通过将尺寸为50mm×50mm×0.7mm的样品固定并使130g的由不锈钢构成的球体落下到样品上来实施。通过不锈钢球的冲击能(碰撞能j=高度m×重量kg×9.8m/秒2),可以测定对(c)的破损的耐性。将表示由上述的落球试验得到的表面压应力s与断裂能的关系性的图示于图29中。表面压应力s越高,则断裂能也越增加。由该测定结果确认,为了抑制(c)的破损,优选表面压应力s更高。另外,落球试验也在以下的条件下进行。将上述的a、c~e这四种玻璃材料的玻璃a3、c3~e3切割为50mm×50mm的尺寸并进行研磨。然后,对各玻璃进行化学强化。将上述的玻璃配置到中央部40mm×40mm被挖空的基台上,使φ30mm、130g的铁球落下到其表面上,使玻璃的背面侧发生冲击性断裂,将上述操作重复20次,计算出断裂时的铁球的冲击能的简单平均值,将其作为平均断裂能。另外,玻璃a3、c3~e3具有表4所示的性能。表4和图32(c)中示出了各玻璃的落球试验的试验结果。表4由图32(a)~图32(c)可知,这三种破损的方式存在如下倾向:破裂发生时的平均断裂能与表面压应力成比例,表面压应力越大,则破裂发生所需的平均断裂能越大,即,越不易发生破裂。进而,本发明人特别关注了(a)、(b)的破损,发现(a)、(b)的破损、即在玻璃板的周缘处的破损由于残留在该周缘、特别是端面上的伤痕而变得显著。因此发现,在本发明的一个方式的玻璃板中,通过在玻璃板的端面中设置倒角部、并且使自与该倒角部相邻的主面起在板厚方向上的距离为板厚的1/5以内的部分在蚀刻后在蚀刻面上不存在深度10μm以上的凹坑,强度进一步提高。另外发现,通过使成为玻璃板的破损的起点的倒角部的潜伤的深度相对于表面压应力层的厚度dol的比为0.9以下,强度也进一步提高。从原理上而言,已知化学强化玻璃板的内部拉应力t与表面压应力s、表面压应力层的厚度dol、板厚t的关系为t=s*dol/(t-2dol)。因此,在想要尽可能增大表面压应力s的值而减少(a)、(b)、(c)的破损时,内部拉应力t的值增大,难以减少(d)的破损。因此,本发明的一个方式的玻璃基板的表面压应力s为850~1200mpa,表面压应力层的厚度dol为20~35μm,内部拉应力t为3~42mpa,板厚为0.6mm以上。作为其他方式,内部拉应力t根据强化条件也可以设定为10~42mpa,另外,也可以设定为20~42mpa,还可以设定为25~42mpa。在保护玻璃等的用途的情况下,从重量的观点出发,更优选将板厚设定为1.5mm以下。另外,更优选表面压应力为900~1100mpa、表面压应力层的厚度为25~30μm、内部拉应力为30~40mpa、板厚为0.7~1.1mm。另外,以往,为了减少玻璃板的破损,普遍认为可以增大dol的值。但是,在特别想要减少(a)、(b)的破损而增大dol的值时,如图30所示,在dol为特定值以上时,即使增大dol的值,也不会显著改善该破损的程度。另外,图30是表示在室温下测定的由四点弯曲试验(jisr1601)得到的表面压应力层的厚度dol与弯曲强度的关系性的图。样品使用尺寸为50mm×50mm×1.0mm并对端面进行了cnc研磨的样品。将两个支撑点的间隔设定为40mm,将两个载荷点的间隔设定为10mm。作为弯曲强度,采用10个试验片的平均值。四点弯曲试验使用岛津制作所制造的オートグラフags-x来实施。因此,为了减少(a)、(b)的破损并且减小t的值以减少(d)的破损,本发明的一个方式的玻璃板的dol设定为35μm以下。另外,设定为小于20μm时,t的值进一步减小,但根据图30,弯曲强度降低,因此,为了也减少(a)、(b)的破损,将玻璃板的dol设定为20μm以上。另外,图20~22中示出的非慢速裂纹破裂是为了与慢速裂纹破裂进行对比而强制发生的破损,不是归类于上述四种方式的破损方式,但对于非慢速裂纹破裂而言,由于断裂起点产生在表面压应力层内,因此,为了防止非慢速裂纹破裂,与上述的(a)、(b)、(c)的破损同样,增大表面压应力s是有效的。使用附图对这样的玻璃板更详细地进行说明。[第一实施方式]图1~图3是本发明的第一实施方式的玻璃板的说明图。玻璃板10具有正主面11和背主面12以及与两个主面11、12相邻的端面13。两个主面11、12是相互平行的平坦面。端面13由与两个主面11、12垂直的平坦部14和形成在各主面11、12与平坦部14之间的倒角部15、16构成。平坦部14可以是对面积比玻璃板10大的平板玻璃进行切割而得到的原始的切割面,也可以是对切割面进行加工而得到的加工面。倒角部15、16例如可以与矩形的主面11、12的四条边对应地设置四个,也可以仅设置一个,其设置数没有特别限定。为了适当减少(a)、(b)的破损,优选设置在所有的边上。倒角部15、16通过将切割面或加工面与主面的角部除去而形成。倒角部15、16例如是相对于主面11、12倾斜的平坦面。图1中,倒角部15、16具有相同的尺寸形状,但也可以具有不同的尺寸形状。另外,本实施方式的倒角部15、16是相对于主面11、12倾斜的平坦面,但只要是从板厚方向观察(从x方向观察)时自主面11、12起朝向平坦部14逐渐向外突出的面即可,也可以是弯曲面。这种情况下,可以没有平坦部14而使倒角部15、16彼此连接,倒角部15、16可以具有大致相同的曲率半径。玻璃板10在两主面11、12中具有自各主面11、12起以预定深度形成的化学强化层(压应力层)21、22。另外,化学强化层(压应力层)21、22也连续地形成在包括平坦部14和倒角部15、16在内的端面13中。压应力层通过将玻璃浸渍于离子交换用的处理液中而形成。玻璃表面所含有的离子半径小的离子(例如,li离子、na离子)被置换为离子半径大的离子(例如,k离子),在玻璃表面中自表面起以预定的深度形成压应力层。为了平衡应力,在玻璃的内部形成内部拉应力层23。另外,本实施方式的两个压应力层21、22具有相同的表面压应力和相同的厚度,但也可以具有不同的表面压应力、不同的厚度。图2是表示本发明的一个实施方式的玻璃板的蚀刻后的状态的概略图。图2中,用实线表示玻璃板10的蚀刻后的状态,用双点划线表示玻璃板10的蚀刻前的状态。图3是图2的局部放大图,示出了蚀刻面17、形成在蚀刻面17上的凹坑18与蚀刻面17的理想面19的关系。本实施方式中,对端面13的预定部分13a、13b进行蚀刻后,在蚀刻面17上不存在深度10μm以上(优选深度8μm以上,更优选深度6μm以上)的凹坑18。预定部分13a、13b是端面13中自与倒角部15、16相邻的主平面11、12起在板厚方向上的距离h为板厚e的1/5以内(h≤1/5×e)的部分。关于“蚀刻”,将整个玻璃板10浸渍于蚀刻液中,在室温(25℃)下进行。作为蚀刻液,使用含有5质量%的氢氟酸(hf)和95质量%的纯水的水溶液。蚀刻液深入到形成在玻璃板10的表面、内部的潜伤中,使潜伤扩大而变得明显。“蚀刻量”通过浸渍时间来控制。具体而言,预先使用相同组成的玻璃进行预定时间的蚀刻并算出蚀刻速率后,调节浸渍时间进行蚀刻,以达到期望的蚀刻量。另外,根据玻璃的种类,有时为了调节上述蚀刻速率而改变氢氟酸浓度。“凹坑的深度”基于jisb0671-2:2002中规定的突出谷部深度rvk的测定法求出。在此,将考察有无深度10μm以上的凹坑18的对象设定为端面13的上述部分13a、13b的原因在于,在上述部分13a、13b存在微小伤痕时,玻璃板10有时会以该微小伤痕为起点产生破损。本实施方式中,测定了对上述部分13a、13b进行例如深度为10μm的蚀刻时的蚀刻面17的表面的凹坑18。蚀刻是为了使潜伤变得明显而实施的,深度不限于10μm。另外,无论有无蚀刻,测定上述部分13a、13b中的潜伤,并进行该潜伤深度的测定。在此,“潜伤深度”通过如下所述的工序来进行测定。首先,对玻璃板10进行蚀刻后,对玻璃基板的主平面进行预定量的研磨,进行清洗和干燥,利用光学显微镜对通过蚀刻处理而形成了圆形凹坑或椭圆形凹坑的加工变质层进行观察。在此,“加工变质层”是指在形状赋予、倒角和磨削等加工工序中存在产生在玻璃基板中的伤痕、裂纹等的层。例如,光学显微镜使用20倍的物镜,在635μm×480μm的观察视野中进行观察。将该工序重复多次,将观察不到圆形凹坑或椭圆形凹坑的时刻的玻璃板10的蚀刻量作为“潜伤深度”。本实施方式的玻璃板10中,通过以使潜伤深度相对于dol为0.9以下的方式进行化学强化,即使在倒角部存在潜伤,也能够得到压应力层的效果,因此优选。作为更优选的实施方式,潜伤深度相对于dol为0.7以下,进一步优选为0.5以下。在此所述的dol优选测定倒角部的dol,但也可以测定自倒角部与主面的边界区域起内侧10mm处的dol。如果该区域的dol相对于倒角部的潜伤深度为0.9以下,则能够得到同样的效果。作为更详细的评价,也可以在玻璃板的四条边的各边中央使自倒角部与主面的边界区域起内侧10mm处的dol与倒角部的潜伤深度的比分别为0.9以下。这些优选的方式中,对于板厚0.6~1.5mm的玻璃板而言,内部拉应力t为47mpa以下、优选为45mpa以下、进一步优选为40mpa以下、特别优选为35mpa以下是适当的。此时的内部拉应力t的下限为20mpa、优选为25mpa是适当的。[第二实施方式]本实施方式涉及具有倒角部的玻璃板的制造方法。图4~图6是本发明的第二实施方式的玻璃板的制造方法的说明图。图4示出了包含作为原板的玻璃板110的层叠体130和对层叠体130的外缘部进行研磨的刷140。图5放大示出了利用刷140对层叠体130的外缘部进行研磨的状态。图6中,用实线表示刷式研磨后的玻璃板110a,用双点划线表示刷式研磨前的玻璃板110。玻璃板的制造方法包括在玻璃板110彼此之间夹设隔垫120而制作层叠体130的层叠工序以及利用刷140对层叠体130的外缘部进行研磨的研磨工序。另外,玻璃板的制造方法还包括将利用刷140对玻璃板110进行研磨而得到的玻璃板110a与隔垫120分离的分离工序。如图4所示,层叠体130包含多个玻璃板110和夹设在玻璃板110彼此之间的板状的隔垫120。将玻璃板110与隔垫120交替重叠后,用夹子等夹具夹持而固定。在玻璃板110与隔垫120之间,可以配设用于防止玻璃板110的损伤的保护片。保护片由树脂等构成。另外,本实施方式的玻璃板110和隔垫120用夹具固定,但固定方法没有特别限定。例如,固定方法可以是将玻璃板110与隔垫120胶粘的方法。作为胶粘剂,使用在研磨工序后的分离工序中可除去的胶粘剂,例如使用热软化性的树脂。也可以使用隔垫120自身作为胶粘剂层来代替在玻璃板110与隔垫120之间形成胶粘剂层。关于各玻璃板110,有时通过例如在对面积比玻璃板110大的平板玻璃进行化学强化后进行切割而得到多张玻璃板。关于平板玻璃的种类、化学强化方法、切割方法,与第一实施方式相同,因此省略说明。如图5所示,各玻璃板110具有两个主平面111、112以及与两个主平面111、112相邻的侧面113。两个主平面111、112是互相平行的平坦面。侧面113是切割面,是与主平面111、112垂直的平坦面。各玻璃板110与图1所示的玻璃板10同样地在两主平面111、112和侧面113中具有自各主平面111、112和侧面113起以预定深度形成的压应力层。为了平衡应力,在压应力层之间形成内部拉应力层。如图4所示,各玻璃板110具有大致相同的尺寸形状,并以在从层叠方向观察(图中为箭头x方向)时外缘彼此重叠的方式进行层叠。因此,各玻璃板110的外缘部被均等地研磨。各隔垫120使用比玻璃板软质的材料,例如由聚丙烯树脂、发泡聚氨酯树脂等构成。各隔垫120具有大致相同的尺寸形状。各隔垫120配置在从层叠方向观察(图中为从箭头x方向观察)时比玻璃板110的外缘更靠内侧的位置,在玻璃板110彼此之间形成槽状的间隙160。如图4所示,刷140为辊刷,由与层叠体130的层叠方向平行的旋转轴141和相对于旋转轴141大致垂直保持的刷毛142等构成。刷140在以旋转轴141为中心旋转的同时沿层叠体130的外缘相对移动,朝向层叠体130的外缘排出含有研磨材料的浆料,对层叠体130的外缘部进行刷式研磨。作为研磨材料,使用二氧化铈、二氧化锆等。研磨材料的粒径(d50)例如为5μm以下,优选为2μm以下。刷140为压片刷(チャンネルブラシ),其通过将植有多个刷毛142的长条构件(刷片)以螺旋状缠绕在旋转轴141上而形成。刷毛142主要由聚酰胺等树脂构成,可以含有氧化铝(al2o3)、碳化硅(sic)、金刚石等研磨材料。刷毛142形成为线状,可以具有逐渐变细的尖端部。在本实施方式中,间隙160的宽度w1为刷毛142的最大直径a的1.25倍以上(w1≥1.25×a)。因此,如图5所示,刷毛142顺畅地插入到间隙160内,利用刷毛142将玻璃板110的主平面111、112与侧面113的角部倒角成曲面。间隙160的宽度w1优选为1.33×a以上,更优选为1.5×a以上。为了提高刷式研磨的效率,间隙160的宽度w1可以小于玻璃板110的板厚e。如图6中实线所示,利用刷140研磨后的玻璃板110a具有两个主平面111a、112a以及与两个主平面111a、112a相邻的侧面113a。两个主平面111a、112a是相互平行的平坦面。侧面113a由与主平面111a、112a垂直的平坦部114a以及形成在各主平面111a、112a与平坦部114a之间的倒角部115a、116a构成。倒角部115a、116a是在从板厚方向观察(从x方向观察)时自主平面111a、112a起朝向平坦部114a逐渐向外突出的曲面。平坦部114a通过利用柔软的刷毛142对图6中用双点划线表示的玻璃板110的侧面进行研磨而形成。倒角部115a、116a通过利用刷毛142的外周面对图6中用双点划线表示的玻璃板110的主平面与侧面的角部进行研磨而形成。对于玻璃板110a的侧面113a,将刷毛142插入到利用隔垫120调节后的间隙内,使用含有粒径为5μm以下的研磨材料的浆料进行了研磨,因此,对侧面113a的预定部分进行深度为10μm的蚀刻时,在蚀刻面上不存在深度为1μm以上的凹坑。预定部分是侧面113a中自与倒角部115a、116a相邻的主平面111a、112a起在板厚方向上的距离为板厚的1/5以内的部分。由此,能够得到与第一实施方式同样的弯曲强度优良的玻璃板110a。[第三实施方式]本实施方式涉及具有倒角部的玻璃板的制造方法。本实施方式中,在制作层叠体之前,还包括对玻璃板的外缘部进行磨削的工序。图7~图9是本发明的第三实施方式的玻璃板的制造方法的说明图。图7示出了作为原板的玻璃板110和对玻璃板110的外缘部进行磨削的旋转磨石240。图8放大示出了利用刷140(参考图4)对包含用旋转磨石240磨削后的玻璃板110b的层叠体130b的外缘部进行研磨的状态。图9中,用实线表示刷式研磨后的玻璃板110c,用双点划线表示刷式研磨前的玻璃板110b。玻璃板的制造方法包括利用圆盘状的旋转磨石240对玻璃板110的外缘部进行磨削的磨削工序、在通过对玻璃板110进行磨削而得到的玻璃板110b彼此之间夹设隔垫120而制作层叠体130b的层叠工序、以及利用刷140对层叠体130b的外缘部进行研磨的研磨工序。另外,玻璃板的制造方法还包括将通过利用刷140对玻璃板110b进行研磨而得到的玻璃板110c与隔垫120分离的分离工序。在旋转磨石240的外周面241上形成有沿圆周方向延伸的环状的磨削槽242。磨削槽242的壁面含有氧化铝、碳化硅、金刚石等磨粒。磨粒的粒度(jisr6001)例如为#300~#2000。粒度根据jisr6002进行测定。粒度越小,则粒径越大,因此磨削效率好。旋转磨石240在以旋转磨石240的中心线为中心旋转的同时沿玻璃板110的外缘相对移动,利用磨削槽242的壁面对玻璃板110的外缘部进行磨削。磨削时可以使用水等冷却液。如图8所示,利用旋转磨石240磨削后的玻璃板110b具有两个主平面111b、112b以及与两个主平面111b、112b相邻的侧面113b。侧面113b是利用旋转磨石240磨削而得到的磨削面,由与主平面111b、112b垂直的平坦部114b以及形成在各主平面111b、112b与平坦部114b之间的倒角部115b、116b构成。倒角部115b、116b例如为相对于主平面111b、112b倾斜的平坦面。另外,本实施方式的倒角部115b、116b是相对于主平面111b、112b倾斜的平坦面,但只要是在从板厚方向观察(从x方向观察)时自主平面111b、112b起朝向平坦部114b逐渐向外突出的面即可,也可以是弯曲面。这种情况下,可以没有平坦部114b而使倒角部115b、116b彼此连接,倒角部115b、116b可以具有大致相同的曲率半径。层叠体130b包含利用旋转磨石240磨削后的多个玻璃板110b和夹设在玻璃板110b彼此之间的板状的隔垫120。将玻璃板110b与隔垫120交替重叠后,用夹子等夹具夹持而固定。在玻璃板110b与隔垫120之间,可以配设用于防止玻璃板110b的损伤的保护片。保护片由树脂等构成。另外,作为将玻璃板110b与隔垫120固定的方法,可以与第二实施方式同样地使用其他固定方法。利用旋转磨石240磨削后的各玻璃板110b具有大致相同的尺寸形状,并以从层叠方向观察(图中为箭头x方向)时外缘相互重叠的方式进行层叠。因此,各玻璃板110b的外缘部被均等地研磨。研磨时可以使用水等冷却液。各隔垫120具有大致相同的尺寸形状,并配置在从层叠方向观察(图中为从箭头x方向观察)时比各玻璃板110b的磨削面(平坦部114b和倒角部115b、116b)更靠内侧的位置,在玻璃板110b彼此之间形成间隙160b。在本实施方式中,与第二实施方式同样地,间隙160b的宽度w2为刷毛142的最大直径a的1.25倍以上(w2≥1.25×a)。因此,如图8所示,刷毛142顺畅地插入到间隙160b内,利用刷毛142将玻璃板110b的主平面111b、112b与倒角部115b、116b的边界部倒角成曲面。此时,倒角部115b、116b与平坦部114b的边界部也利用刷毛142倒角成曲面。间隙160b的宽度w2优选为1.33×a以上,更优选为1.5×a以上。为了提高刷式研磨的效率,间隙160b的宽度w2可以小于玻璃板110b的板厚e。如图9中实线所示,利用刷140(参考图4)研磨后的玻璃板110c具有两个主平面111c、112c以及与两个主平面111c、112c相邻的侧面113c。两个主平面111c、112c是相互平行的平坦面。侧面113c由与主平面111c、112c垂直的平坦部114c以及形成在各主平面111c、112c与平坦部114c之间的倒角部115c、116c构成。倒角部115c、116c是从板厚方向观察(从x方向观察)时自主平面111c、112c起朝向平坦部114c逐渐向外突出的面。对于玻璃板110c的侧面113c,将刷毛插入到利用隔垫120调节后的间隙内,使用含有粒径为5μm以下的研磨材料的浆料进行了研磨,因此,对侧面113c的预定部分进行蚀刻时,在蚀刻面上不存在深度为10μm以上的凹坑。预定部分是侧面113c中自与倒角部115c、116c相邻的主平面111c、112c起在板厚方向上的距离为板厚的1/5以内的部分。由此,能够得到与第一实施方式同样的弯曲强度优良的玻璃板110c。[第四实施方式]本实施方式涉及具有倒角部的玻璃板的制造方法。本实施方式包括利用带有磨粒的片对玻璃板进行研磨的工序来代替利用刷对玻璃板进行研磨的工序。图10~图11是本发明的第四实施方式的玻璃板的制造方法的说明图。图10示出了作为原板的玻璃板110和对玻璃板110进行研磨的片340。图11中,用实线表示片研磨后的玻璃板110d,用双点划线表示片研磨前的玻璃板110。玻璃板的制造方法包括利用含有磨粒的片340对玻璃板110的外缘部进行研磨的研磨工序。片340使用在由树脂、纸等构成的片基材上均匀地胶粘有磨粒的片、在树脂制的片基材中埋设磨粒并以使该磨粒的一部分露出的方式构成的片。片340固定在基台350的固定面351上,形成跟随固定面351的形状。固定面351例如可以如图10所示是平坦面,也可以是弯曲面。片340在与固定面351相反的一侧的表面上含有磨粒。通过将玻璃板110按压到该含有磨粒的表面上并使其滑动来对玻璃板110进行研磨。在研磨时可以使用水等润滑液。另外,本实施方式的片340固定在基台350上,将玻璃板110按压到片340的含有磨粒的表面上并使其滑动,但也可以将施加有张力的状态的片340的含有磨粒的表面按压到玻璃板110上并使其滑动。作为片340的磨粒,例如使用氧化铝、碳化硅、金刚石的粉末,使用粒度(jisr6001)为#6000以上的磨粒。粒度越大,则粒径越小。磨粒的粒度根据jisr6002进行测定。磨粒的粒度优选为#8000以上,更优选为#10000以上。如图11中实线所示,研磨后的玻璃板110d具有两个主平面111d、112d以及与两个主平面111d、112d相邻的侧面113d。两个主平面111d、112d是相互平行的平坦面。侧面113d由与主平面111d、112d垂直的平坦部114d以及形成在各主平面111d、112d与平坦部114d之间的倒角部115d、116d构成。倒角部115d、116d是从板厚方向观察(从x方向观察)时自主平面111d、112d起朝向平坦部114d逐渐向外突出的面,是相对于主平面111d、112d倾斜的平坦面。平坦部114d是原始的切割面,因此未形成潜伤。另外,平坦部114d也可以通过利用片340进行研磨而形成。倒角部115d、116d通过利用含有粒度比以往大的(粒径比以往小的)磨粒的片340进行研磨而形成。玻璃板110d的侧面113d使用含有粒度比以往大的(粒径比以往小的)磨粒的片340进行了研磨,因此,对侧面113d的预定部分进行蚀刻时,在蚀刻面上不存在深度为10μm以上的凹坑。预定部分是侧面113d中自与倒角部115d、116d相邻的主平面111d、112d起在板厚方向上的距离为板厚的1/5以内的部分。由此,能够得到与第一实施方式同样的弯曲强度优良的玻璃板110d。[第五实施方式]本实施方式涉及带触控传感器的化学强化玻璃。图12是构成本发明的一个实施方式的带触控传感器的化学强化玻璃的主要部分的俯视图,图13是图12的a-a线截面图。带触控传感器的化学强化玻璃210具备触控传感器211和搭载该触控传感器211的化学强化玻璃220,是在二合一方式的显示装置中使用的带触控传感器的化学强化玻璃。即,带触控传感器的化学强化玻璃210的化学强化玻璃220兼具作为保护玻璃的功能和作为传感器基板的功能。触控传感器211通过如下方式构成:在化学强化玻璃220的单侧的表面上,沿交叉的x轴、y轴这两个轴各自的轴向延伸的列电极通过在其交叉部分之间夹设电绝缘层而以电气非接触的状态形成。在此,将沿x轴方向延伸的列电极称为第一电极212a、将沿y轴方向延伸的列电极称为第二电极212b时,为了检测触控位置,沿各轴向延伸的第一电极212a与第二电极212b必须相互独立。因此,本实施方式中,在化学强化玻璃220的单侧的表面上,使构成矩阵状的各第一电极212a和第二电极212b的列电极图案(沿各轴向延伸的多列电极图案)以一层透明电极图案212的形式排列,而且,在两列交叉的区域,将以使其中任意一列不与另一列接触的方式隔断的透明电极图案212的隔断部位用桥接线214连接。另外,在桥接线214与透明电极图案212重叠的区域(交叉区域),在透明电极图案212与桥接线214之间设置有由绝缘性物质形成的绝缘层213。标号215是以包围透明电极图案212的方式形成在化学强化玻璃220的周缘部的具有遮光性的黑色层,标号216表示引向形成各列的电极集合的引绕线。引绕线216连接到各列的电极图案中的任意一个上即可。在触控传感器211的最下层形成有保护玻璃217。作为构成绝缘层213的透明性的电绝缘性物质,可以使用有机树脂材料,在使用有机树脂材料来形成绝缘层的情况下,利用光刻技术可以容易地得到图案化的树脂制绝缘层。作为构成桥接线214的导电物质,优选使用能够容易地对化学强化玻璃220得到高粘附力的金属材料。特别是在透明基板为玻璃基板的情况下,可以优选使用对玻璃基板的粘附力高、导电性比ito高、耐久性、耐磨损性也优良的mo、mo合金、al、al合金、au、au合金等金属材料。搭载触控传感器211的化学强化玻璃220的板厚为1.5mm以下,更优选为1.0mm以下,进一步优选为0.8mm以下。用于得到化学强化玻璃220的化学强化例如通过将玻璃在380℃~450℃的硝酸钾(kno3)熔盐中浸渍0.1~20小时来进行,但通过改变硝酸钾(kno3)熔盐的温度、浸渍时间、熔盐等,能够调节化学强化的进行程度。通过进行化学强化,在玻璃表面上形成压应力层,在内部形成内部拉应力层。本发明的化学强化玻璃220需要对上述的四种破损方式均具有耐性,为此,进行化学强化以使得压应力层的表面压应力s为800mpa以上、内部拉应力t为8mpa以上且40mpa以下。其理由如下所示。这样进行了化学强化的化学强化玻璃220中,压应力层深度优选为15μm以上,更优选为20μm以上,进一步优选为25μm以上。这是因为,通过使压应力层比切割、倒角等端面处理中产生的潜伤深,能够产生期望的端面强度。[第六实施方式]本实施方式涉及带触控传感器的化学强化玻璃的制造方法。图14是对带触控传感器的化学强化玻璃的制造方法进行说明的图。首先,准备可分割为多个显示装置用化学强化玻璃的大型化学强化玻璃200(图14(a)),在化学强化玻璃200的单侧的表面上,在与各个化学强化玻璃的周缘部相对应的位置形成黑色层215(图14(b))。另外,如上所述,该化学强化玻璃200为进行了化学强化以使得表面压应力s为800mpa以上、内部拉应力为8mpa以上且40mpa以下的化学强化玻璃。接着,在化学强化玻璃200的单侧的表面上,形成透明电极图案212(图14(c))。例如,在化学强化玻璃200的单侧的表面上,使用溅射法等形成ito膜,将形成的ito膜加工为如图12所示的图案形状,由此,形成具有预定图案的透明电极图案212。在形成该透明电极图案212时,可以采用涂布ito膜并使用预定图案的掩模进行曝光、接着进行蚀刻的光刻工艺法(以下,称为光刻技术)。此时,在形成有透明电极图案212的化学强化玻璃200的同一面(形成有透明电极图案212的表面)上,利用例如光刻技术形成覆盖透明电极图案212的特定部位(x轴方向的第一电极212a的列电极图案与y轴方向的第二电极212b的列电极图案交叉的区域、即作为列电极图案的交叉区域)的绝缘层213(图14(d))。接着,以从设置在各交叉区域的绝缘层213的上方跨过的方式形成使透明电极图案212的特定部位(第一电极212a的隔断部位)间连接的各桥接线214(图14(e))。例如,使用溅射法等在形成有绝缘层213的化学强化玻璃200的同一面(形成有绝缘层213的表面)上将金属制的导电物质成膜而形成金属膜,利用光刻技术对该金属膜进行图案化,从而形成具有预定形状的图案的桥接线214。此时,以将引绕线部分也覆盖的方式形成金属膜,在用于形成桥接线的利用光刻法进行的图案化工序的同时对该金属膜进行图案化,形成引绕线216。由此,完成图12所示的状态。接着,溅射sio2而形成保护玻璃217(图14(f)),将其分割为各带触控传感器的化学强化玻璃210(图14(g)),对各带触控传感器的化学强化玻璃210的角部进行倒角(图14(h))。最后,在各带触控传感器的化学强化玻璃210上压接柔性布线基板218并进行连接,由此,制造带触控传感器的化学强化玻璃210。这样,带触控传感器的化学强化玻璃210在形成触控传感器211时,可以使用光刻技术来制造。因此,化学强化玻璃220优选具有耐酸性,将化学强化玻璃在温度90℃、0.1摩尔%的盐酸中浸渍20小时后的减重优选为1mg/cm2以下。这样,通过使用耐酸性高的化学强化玻璃,能够使用光刻技术在化学强化玻璃上搭载触控传感器。在此,准备将上述的a~e这五种玻璃材料的玻璃a5~e5切割为50mm×50mm的尺寸并进行了研磨的化学强化玻璃,对于将各化学强化玻璃在温度90℃、0.1摩尔%的盐酸中的盐酸中浸渍20小时后的每单位面积玻璃的减重(mg/cm2)进行评价。另外,玻璃a5~e5具有表5所示的性能。表5中示出了各玻璃的减重(mg/cm2)。表5根据该结果,对于玻璃a、c和d而言,每单位面积玻璃的减重低于1mg/cm2,可以说耐酸性优良。以上,对本发明的第一至第六实施方式进行了说明,但本发明不限于上述的实施方式,在不脱离本发明的范围的情况下,可以对上述的实施方式进行各种变形和置换。例如,在第三实施方式的旋转磨石的外周面上形成有磨削槽,但也可以不形成磨削槽。在不具有磨削槽的情况下,由旋转磨石的外周面磨削后的玻璃板的侧面成为与主平面垂直的面。因此,在不具有磨削槽的情况下,通过磨削,可得到形状与图6中用双点划线表示的作为原板的玻璃板110大致相同的玻璃板,通过之后的刷式研磨,可得到形状与图6中用实线表示的玻璃板110a大致相同的玻璃板。另外,在第三实施方式中,可以利用片对玻璃板的角部进行研磨来代替利用具有磨削槽的旋转磨石进行磨削。通过片研磨,可得到形状与图9中用双点划线表示的玻璃板110b大致相同的玻璃板,通过之后的刷式研磨,可得到形状与图9中用实线表示的玻璃板110c大致相同的玻璃板。这种情况下,片中含有的磨粒的粒度与第四实施方式不同,为#1000以上即可。另外,在第三实施方式中,可以在利用不具有磨削槽的旋转磨石进行磨削后利用片对磨削后的玻璃板的角部进行研磨来代替利用具有磨削槽的旋转磨石进行磨削。通过片研磨,可得到形状与图9中用双点划线表示的玻璃板110b大致相同的玻璃板,通过之后的刷式研磨,可得到形状与图9中用实线表示的玻璃板110c大致相同的玻璃板。这种情况下,片中含有的磨粒的粒度与第四实施方式不同,为#1000以上即可。作为用于得到本发明的强化玻璃板的化学强化处理的方法,只要是能够将玻璃表层的na与熔盐中的k进行离子交换的方法则没有特别限定,可以列举例如将玻璃浸渍在加热后的硝酸钾熔盐中的方法。另外,本发明中,硝酸钾熔盐或硝酸钾盐除了kno3以外,还包含含有kno3和10质量%以下的nano3的熔盐等。用于在玻璃上形成具有期望的表面压应力的化学强化层(压应力层)的化学强化处理条件根据玻璃板的厚度等而不同,典型的是将玻璃基板在350~550℃的硝酸钾熔盐中浸渍2~20小时。从经济性的观点出发,优选在350~500℃、2~16小时的条件下浸渍,更优选的浸渍时间为2~10小时。本发明的玻璃板大致呈矩形,但从正面观察时,角部可以为曲线状,在边部可以向面方向外侧或内侧具有突出或凹陷。本发明中的玻璃板的制造方法没有特别限制,例如通过如下方法制造:将各种原料适量进行调配,加热至约1400℃~约1800℃使其熔融后,通过脱泡、搅拌等进行均质化,通过公知的浮法、下拉法、压制法等成形为板状,退火后切割为期望的尺寸。本发明的玻璃板的玻璃的玻璃化转变温度tg优选为400℃以上。低于400℃时,在离子交换时表面压应力松弛,可能无法得到充分的应力。更优选为550℃以上。本发明的玻璃板的玻璃的粘度达到102dpa·s时的温度t2优选为1800℃以下,更优选为1750℃以下。本发明的玻璃的粘度达到104dpa·s时的温度t4优选为1350℃以下。本发明的玻璃板的玻璃的比重ρ优选为2.37~2.55。本发明的玻璃板的玻璃的杨氏模量e优选为65gpa以上。低于65gpa时,玻璃的作为保护玻璃的刚性、断裂强度可能会变得不充分。本发明的玻璃板的玻璃的泊松比σ优选为0.25以下。大于0.25时,玻璃的耐裂纹性可能会变得不充分。接着,在没有特别说明的情况下,使用以摩尔百分率计的含量对本发明的玻璃板的玻璃组成进行说明。sio2是构成玻璃的骨架的成分,是必需的,并且是减少在玻璃表面上赋予伤痕(压痕)时的裂纹的产生或者减小在化学强化后赋予压痕时的断裂率的成分。sio2低于56%时,作为玻璃的稳定性、耐候性或耐崩裂性降低。sio2优选为58%以上,更优选为60%以上。sio2超过75%时,玻璃的粘性增大,熔融性降低。al2o3是对于提高离子交换性能和耐崩裂性有效的成分,是增大表面压应力的成分,并且是减小在利用110°的压头赋予压痕时的裂纹产生率的成分,是必需的。al2o3低于5%时,无法通过离子交换得到期望的表面压应力值或压应力层厚度。优选为9%以上。al2o3超过20%时,玻璃的粘性变高,难以进行均匀的熔融。al2o3优选为15%以下,典型地为14%以下。sio2和al2o3的含量合计sio2+al2o3优选为80%以下。超过80%时,高温下的玻璃的粘性增大,有可能难以熔融,优选为79%以下,更优选为78%以下。另外,sio2+al2o3优选为70%以上。低于70%时,赋予压痕时的耐裂纹性降低,更优选为72%以上。na2o是通过离子交换形成表面压应力并且提高玻璃的熔融性的成分,是必需的。na2o低于8%时,难以通过离子交换形成期望的表面压应力层,优选为10%以上,更优选11%以上。na2o超过22%时,耐候性降低,或者容易从压痕产生裂纹。优选为21%以下。k2o不是必需的,但为了增大离子交换速度,可以在10%以下的范围内含有。超过10%时,可能容易从压痕产生裂纹,或者可能会使由硝酸钾熔盐中的nano3浓度引起的表面压应力的变化增大。k2o为5%以下,更优选为0.8%以下,进一步优选为0.5%以下,典型地为0.3%以下。在想要减小由硝酸钾熔盐中的nano3浓度引起的表面压应力的变化的情况下,优选不含有k2o。mgo是增大表面压应力的成分,并且是提高熔融性的成分,是必需的。在想要抑制应力松弛等情况下,优选含有mgo。在不含有mgo的情况下,在进行化学强化处理时容易因熔盐温度的偏差而使应力松弛的程度随化学强化处理槽的部位发生变化,结果,可能难以得到稳定的压应力值。另外,mgo超过14%时,玻璃可能会容易失透,或者可能会使由硝酸钾熔盐中的nano3浓度引起的表面压应力的变化增大,优选为13%以下。上述sio2-mgo优选为64%以下,更优选为62%以下,典型地为61%以下。上述al2o3-mgo优选为9%以下,更优选为8%以下。sio2、al2o3、na2o和mgo的含量合计优选为98%以上。该合计低于98%时,可能难以在维持耐裂纹性的同时得到期望的压应力层。典型地为98.3%以上。zro2不是必需的,但为了降低高温下的粘性,或者为了增大表面压应力,可以在5%以下的范围内含有。zro2超过5%时,可能会使从压痕产生裂纹的可能性增高。因此,优选为2%以下,进一步优选为1%以下,典型地不含有zro2。b2o3不是必需的,但为了提高高温下的熔融性或玻璃强度等,可以在6%以下的范围内含有。b2o3超过6%时,难以得到均质的玻璃,可能难以进行玻璃的成形,或者耐裂纹性可能会降低。典型地不含有b2o3。sio2、al2o3、na2o和mgo的含量合计优选为98%以上。本发明的玻璃板的优选玻璃成分在本质上由以上说明的成分构成,但在不损害本发明目的的范围内,可以含有其他成分。在含有这样的成分的情况下,这些成分的含量合计优选低于2%,更优选为1%以下。以下,对上述其他成分例示性地进行说明。为了提高玻璃的高温下的熔融性,有时可以含有例如2%以下的zno,优选为1%以下,在通过浮法进行制造等情况下,优选为0.5%以下。zno超过0.5%时,在浮法成形时可能会发生还原而成为制品缺陷。典型地不含有zno。tio2通过与玻璃中存在的fe离子共存而使可见光透射率降低,可能使玻璃着色为褐色,因此,即使含有也优选为1%以下,典型地不含有tio2。li2o是降低应变点从而容易引起应力松弛、结果无法得到稳定的表面压应力层的成分,因此优选不含有,即使在含有时,其含量也优选低于1%,更优选为0.05%以下,特别优选低于0.01%。另外,li2o在化学强化处理时有时会溶出到kno3等熔盐中,在使用含有li的熔盐进行化学强化处理时,表面压应力显著降低。从该观点出发,优选不含有li2o。为了提高高温下的熔融性或者不易发生失透,可以在5%以下的范围内含有cao。cao超过5%时,离子交换速度或对裂纹产生的耐性降低。典型地不含有cao。sro可以根据需要含有,但与mgo、cao相比,降低离子交换速度的效果更大,因此,即使在含有时,也优选其含量低于1%。典型地不含有sro。在碱土金属氧化物中,bao降低离子交换速度的效果最大,因此,优选不含有bao,或者即使在含有时,也优选其含量低于1%。在含有sro或bao时,它们的含量合计优选为1%以下,更优选低于0.3%。在含有cao、sro、bao和zro2中的任意一种以上时,这四种成分的含量合计优选低于1.5%。该合计为1.5%以上时,离子交换速度可能会降低,典型地为1%以下。作为玻璃熔融时的澄清剂,可以适当含有so3、氯化物、氟化物等。但是,为了提高触控面板等显示装置的视认性,优选尽可能地减少在可见光区域具有吸收的fe2o3、nio、cr2o3等作为原料中的杂质混入的成分,各自以质量百分率计优选为0.15%以下,更优选为0.05%以下。实施例表6~12的例1~45中,以达到从sio2至k2o的栏中以摩尔百分率表示(质量百分率表示)的组成的方式适当选择氧化物、氢氧化物、碳酸盐或硝酸盐等通常使用的玻璃原料,以玻璃计称量400g。向该称量物中添加相当于其质量的0.2%的质量的硫酸钠,对所得物进行混合。接着,将混合后的原料装入铂制坩埚中,投入到1650℃的电阻加热式电炉中,熔融6小时,并进行脱泡、均质化。将所得到的熔融玻璃浇铸到模具中,在tg+50℃的温度下保持1小时后,以0.5℃/分钟的速度冷却至室温,得到玻璃块。表6~12中,例1~40、42~44为实施例,例41、45为比较例。将这些玻璃的杨氏模量e(单位:gpa)、玻璃化转变温度tg(单位:℃)、粘度达到102dpa·s时的温度t2(单位:℃)、粘度达到104dpa·s时的温度t4(单位:℃)、50~350℃下的平均线膨胀系数α(单位:-7/℃)示于表中。对玻璃块进行切割、磨削,最后,将两面加工为镜面,得到尺寸为30mm×30mm、厚度为1.0mm的板状玻璃。到镜面研磨为止的工序中,使用#1000的磨石将板状的玻璃磨削300~1000μm,得到板状玻璃,然后,使用二氧化铈进行研磨,使其表面成为镜面。接着,对例1~45的板状玻璃进行下述的化学强化处理。各化学强化条件如下所述。例1、2、11~14、16、18、20、42是分别在含有95质量%的kno3和5质量%的nano3的425℃的熔盐中浸渍6小时而进行了化学强化处理的玻璃。例3、4、6、15、31、44是分别在含有95质量%的kno3和5质量%的nano3的425℃的熔盐中浸渍10小时而进行了化学强化处理的玻璃。例5、7、8、10、33、43是分别在含有95质量%的kno3和5质量%的nano3的450℃的熔盐中浸渍6小时而进行了化学强化处理的玻璃。例9、45是分别在含有95质量%的kno3和5质量%的nano3的450℃的熔盐中浸渍10小时而进行了化学强化处理的玻璃。例17、19、21、24、27、30、32、34~38、40是分别在425℃的100%的kno3熔盐中浸渍6小时而进行了化学强化处理的玻璃。例22、25、28、41是分别在450℃的100%的kno3熔盐中浸渍6小时而进行了化学强化处理的玻璃。例23、26、29、39是分别在425℃的100%的kno3熔盐中浸渍10小时而进行了化学强化处理的玻璃。对于化学强化处理后的各玻璃,利用折原制作所公司制造的表面应力计fsm-6000测定表面压应力s(单位:mpa)和压应力层深度dol(单位:μm),计算出内部拉应力t(单位:mpa)。将结果示于表的对应栏中。表6例1234567sio264(60.2)62(57.6)64(59.5)62(58.7)60(56.1)60(56.1)62(58.0)al2o312(19.2)14(22.1)14(22.1)12(19.3)14(22.2)14(22.2)14(22.2)b2o30000000mgo8(5.1)8(5.0)8(5.0)10(6.4)10(6.3)10(6.3)10(6.3)cao0000000zro20000000na2o16(15.5)16(12.3)14(13.4)16(15.6)16(15.4)16(15.4)14(13.5)k2o0000000e77798079818182α2.472.482.462.482.492.492.47tg659689724661691691726t21677171118031631166516651757t41272132214001251130113011379s881874850859917866877dol30.027.933.331.233.730.532.5t28.125.830.328.633.128.130.5表7例891011121314sio260(57.2)58(54.6)60(56.5)60(56.4)58(53.8)60(55.7)66(62.6)al2o312(19.4)14(22.3)14(22.4)12(19.1)14(22.0)14(22.1)11(17.7)b2o30000000mgo12(7.7)12(7.6)12(7.6)8(5.0)8(5.0)8(5.0)8(5.1)cao0000000zro20000000na2o16(15.7)16(15.5)14(13.6)20(19.4)20(19.1)18(17.2)15(14.7)k2o0000000e81838476787976α2.502.512.492.502.512.492.45tg663693728589619654662t21585161817111493152716191707t41230128013581116116612441285s888851894847893904900dol31.033.828.834.133.430.429.0t29.330.827.331.032.029.327.7表8例15161718192021sio266(62.6)66(62.2)68(65.3)68(65.3)68(64.9)68(64.9)68(65.8)al2o311(17.7)12(19.2)9(14.7)9(14.7)10(16.2)10(16.2)9(14.8)b2o30000000mgo8(5.1)8(5.1)8(5.2)8(5.2)8(5.1)8(5.1)10(6.5)cao0000000zro20000000na2o15(14.7)14(13.6)15(14.9)15(14.9)14(13.8)14(13.8)13(13.0)k2o0000000e76777373757576α2.452.452.442.442.442.442.44tg662694632632665665669t21707177016741674173617361719t41285134912341234129912991291s896888112085012008591152dol35.029.034.030.031.029.026.0t33.727.340.927.139.726.431.6表9例22232425262728sio268(65.8)68(65.8)68(65.3)68(65.3)68(65.3)68(64.9)68(64.9)al2o39(14.8)9(14.8)10(16.3)10(16.3)10(16.3)11(17.8)11(17.8)b2o30000000mgo10(6.5)10(6.5)10(6.4)10(6.4)10(6.4)10(6.4)10(6.4)cao0000000zro20000000na2o13(13.0)13(13.0)12(11.9)12(11.9)12(11.9)11(10.8)11(10.8)k2o0000000e76767777777979α2.442.442.432.432.432.432.43tg669669702702702734734t21719171917821782178218451845t41291129113561356135614201420s1107114311371116113110741060dol35.034.026.035.033.025.033.0t41.741.731.242.040.028.337.5表10例29303132333435sio268(64.9)68(64.6)68(64.6)68(64.3)68(64.3)68(64.0)68(64.6)al2o311(17.8)10(16.1)10(16.1)10(16.0)10(16.0)10(16.0)10(16.1)b2o30000000mgo10(6.4)8(5.1)8(5.1)8(5.1)8(5.1)8(5.0)8(5.1)cao0000000zro200.5(1.0)0.5(1.0)1(1.9)1(1.9)1.5(2.9)0na2o11(10.8)13.5(13.2)13.5(13.2)13(12.7)13(12.7)12.5(12.1)13(12.7)k2o0000001(1.5)e79757576767676α2.432.452.452.462.462.472.43tg734673673682682690677t21845175917591782178218051782t41420131813181338133813571338s10691165887116485611601154dol33.030.034.028.034.026.031.0t37.837.232.434.531.231.838.1表11例36373839404142sio268(64.2)68(64.3)68(64.0)68(64.0)66(61.8)66(61.8)68(64.5)al2o310(16.0)10(16.0)10(16.0)10(16.0)13(20.6)13(20.6)11(17.7)b2o30000000mgo8(5.1)8(5.1)8(5.0)8(5.0)8(5.0)8(5.0)8(5.1)cao0000000zro200.5(1.0)1(1.9)1(1.9)000na2o12(11.7)12.5(12.2)12(11.6)12(11.6)13(12.6)13(12.6)13(12.7)k2o2(3.0)1(1.5)1(1.5)1(1.5)000e77767777797976α2.432.442.462.462.442.442.43tg689685694694727727697t21828180518281828183218321799t41377135713771377141414141363s107011231110110313001243843dol31.030.028.035.029.040.028.0t35.435.832.941.540.054.025.0表12例434445sio268(64.5)68(64.5)68(64.5)al2o311(17.7)11(17.7)11(17.7)b2o3000mgo8(5.1)8(5.1)8(5.1)cao000zro2000na2o13(12.7)13(12.7)13(12.7)k2o000e767676α2.432.432.43tg697697697t2179917991799t4136313631363s843836845dol38.036.050.0t34.732.446.9图31是表示本发明的一个方式的化学强化玻璃板的四点弯曲强度的韦伯图。化学强化玻璃板的样品使用对组成与实施例19和20相同的玻璃进行强化而使表面压应力s为905mpa、dol为22.7μm、板厚为1.1mm的样品。化学强化后,使用粒度不同的磨石分别进行倒角处理。在此,#400的磨石是磨粒的平均粒径为44~37μm(最大粒径75μm)的磨石,#600的磨石是磨粒的平均粒径为26~31μm(最大粒径53μm)的磨石。如前所述,如果想要抑制全部的四种破损方式,则表面压应力s的值越高越优选,另一方面,内部拉应力t的值越低越优选。本方式的化学强化玻璃通过在将表面压应力s和内部拉应力t的值调节为适当的值的同时对玻璃板端面进行研磨,进一步提高了弯曲强度。由图31可知,利用#400的磨石研磨后的化学强化玻璃板观察到多个弯曲强度为500mpa以下的样品,但利用#600的磨石研磨后的化学强化玻璃板未观察到弯曲强度为500mpa以下的样品。化学强化玻璃板一般要求具有500mpa以上的弯曲强度作为实用的弯曲强度,因此,通过利用#600的磨石进行研磨,能够在使内部拉应力t低于预定值的同时确保500mpa以上的弯曲强度。另外,从外观上的观点考虑,也优选利用粒度为#600以上的磨石进行研磨。对各玻璃板的倒角部的潜伤(凹坑)深度进行了测定,结果,利用#400的磨石研磨后的化学强化玻璃板的最大潜伤深度为25μm,利用#600的磨石研磨后的化学强化玻璃板的最大潜伤深度为20μm。因此,通过在倒角部、特别是在自与倒角部相邻的主面起在板厚方向上的距离为板厚的1/5以内的部分使潜伤(凹坑)深度为20μm以下,能够提供能更加耐受多种破损情况的化学强化玻璃板。由图31可知,在利用#400的磨石研磨后的化学强化玻璃板、即具有最大为25μm的潜伤(凹坑)深度的情况下,在500mpa以下的弯曲强度下产生破损的概率为约20%。另一方面,通过使潜伤(凹坑)深度最大为20μm,能够将在500mpa以下的弯曲强度下产生破损的概率抑制得极低。另外,如前所述,潜伤深度通过反复进行蚀刻处理来测定。另外,利用#400的磨石研磨后的化学强化玻璃板的表面粗糙度ra为0.43μm,利用#600的磨石研磨后的化学强化玻璃板的表面粗糙度ra为0.26μm。如上所述,通过在将表面压应力s和内部拉应力t的值调节为预定值的同时对端面进行研磨,能够提供针对多种破损情况不易产生破损的化学强化玻璃板。产业实用性本发明能够利用于显示装置的保护玻璃、带触控传感器的化学强化玻璃等。另外,还能够利用于太阳能电池基板、飞机用窗玻璃等。本申请基于2012年5月25日提出的日本专利申请2012-119719、2012年5月30日提出的日本专利申请2012-123353和2012年10月23日提出的日本专利申请2012-233702,其内容作为参考并入本说明书中标号说明10玻璃板11、12主面13端面13a、13b端面的预定部分15、16倒角部17蚀刻面18凹坑21、22化学强化层(压应力层)23内部拉应力层110玻璃板120隔垫130层叠体140刷142刷毛210带触控传感器的化学强化玻璃211触控传感器220化学强化玻璃240旋转磨石340片当前第1页12