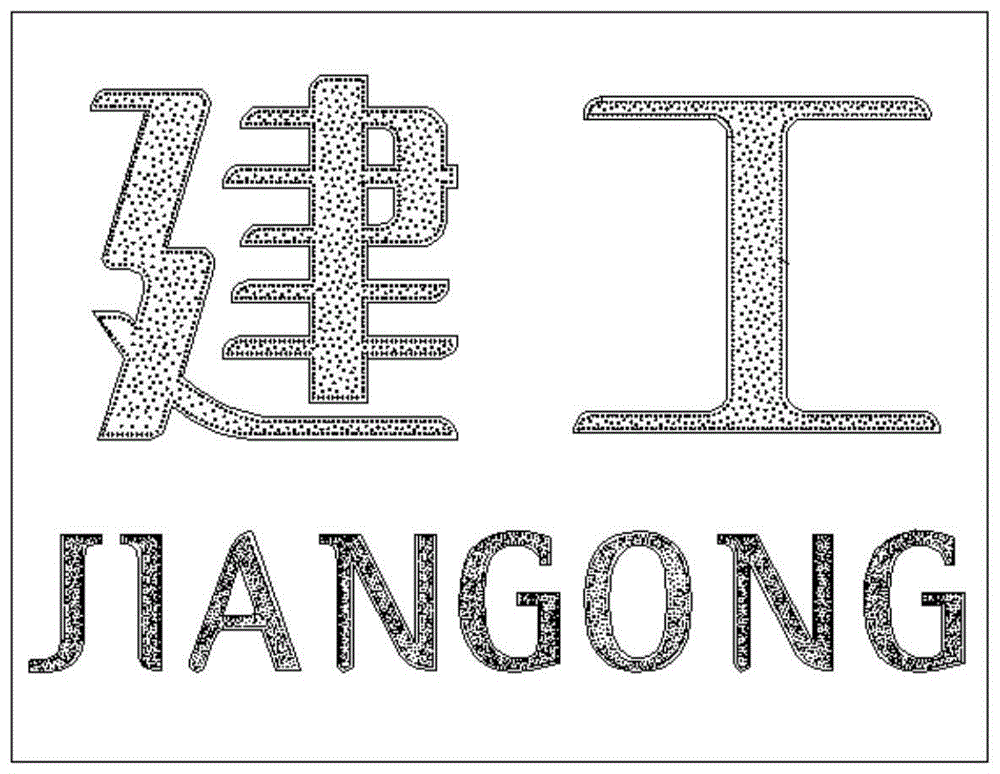
本发明预制混凝土构件
技术领域:
,具体涉及一种造型透光混凝土的制作方法。
背景技术:
:透光混凝土是一种全新透光材料,在材料组成、透光原理、材料性能等各个方面与传统的透光材料完全不同。其材料组成特征是:水泥基和导光材料,导光材料以一定空间排列组合方式埋入水泥基材料基体中,形成复杂多样的导光图案。造型混凝土是利用弹性造型模板或者硬质泡沫造型模板来制作表面带有造型的混凝土,是一种新型装饰混凝土,使得混凝土既保留了本身朴素美,又具有丰富多样的造型表现形式。在预制混凝土构件制作领域,制作具有透光性能的造型混凝土具有积极意义。具有透光性能的造型混凝土在制作的过程中需要克服多重问题,其中最主要的包括以下几个方面:(1)脱模困难;(2)混凝土与导光棒界面间的粘结性差;(3)混凝土的抗裂性能差。技术实现要素:针对现有技术中存在的问题,本发明提供一种造型透光混凝土的制作方法,本发明所用原料来源广泛,流动度大,粘结力强,成本低,且具备良好的抗裂性能;本发明脱模简单,可整体成型透光混凝土大板,制得的造型透光混凝土制品达到相关技术指标,具有较好的耐久性能,同时具有良好的艺术造型表观效果。为实现上述目的,本发明采用以下技术方案:本发明提供一种造型透光混凝土的制作方法,包括以下步骤:步骤1、根据混凝土表面定制造型图案制作造型模板;步骤2、安装混凝土浇筑所需的钢模具;步骤3、按照透光图案在造型模板上对应的位置打出点阵式密布的光导纤维定位孔,并将光导纤维呈现透光图案的一端穿入造型模板的定位孔中固定,并在造型模板的表面涂刷脱模剂;步骤4、将造型模板固定在钢模具上,并将光导纤维的另一端固定在光纤定位钢板上,光纤定位钢板固定在上方的工装架上;步骤5、配置水泥基,并将水泥基浇入步骤4形成的浇筑模具中;步骤6、将混凝土在养护室中进行一次养护后脱模,脱模后进行二次养护即得产品。作为本发明的一个实施例,所述步骤s1中,采用弹性造型模板,具体如下:按照混凝土的表面造型在模种上利用3d雕刻机雕刻出对应的定制造型图案;在模种上涂刷脱模剂,并将液态胶模基材浇筑在模种上,养护后脱模即得弹性造型模板。作为本发明的一个实施例,所述步骤s1中,采用硬质泡沫造型模板,具体如下:采用3d雕刻机在硬质泡沫模板上雕刻出对应的定制造型图案。作为本发明的一个实施例,所述步骤s3中,光导纤维与造型模板通过胶黏剂固定,所述步骤s4中,造型模板与钢模具通过胶黏剂固定。作为本发明的一个实施例,所述步骤s5中,水泥基包括以下重量份的各组分:水130份、硅酸盐水泥130份、粉煤灰50份、聚羧酸减水剂4份、中砂402份、石屑402份、聚丙烯长坚纤维200份、脱硫石膏10份。通过加入脱硫石膏使得碱激发和硫酸盐激发并存,促进水化硅酸钙和水化铝酸钙的形成,生成钙钒石,这些水化产物填充于孔隙中,增加混凝土结构的密实性,优化了孔隙结构,利于强度发展,并提高混凝土的耐久性;本发明通过加入水溶性好的聚丙烯长坚纤维有效降低混凝土自身收缩,降低透光混凝土板产生裂缝的风险,可一次成型较大面积的透光混凝土板;本发明通过用石屑等质量替代50%的细骨料,有效改善了混凝土的开裂问题。作为本发明的一个实施例,所述步骤s5中,水泥基包括以下重量份的各组分:水170份、硅酸盐水泥361-369份、硫铝酸盐水泥13-18份、粉煤灰63-65份、无水硫酸钠6-7份、聚羧酸减水剂2.9份、中砂1350份、可再分散乳胶粉6.3份,硫铝酸盐水泥与无水硫酸钠的重量比为(1.3-2.6):1,硅酸盐水泥、粉煤灰、硫铝酸盐水泥、无水硫酸钠的混合物与可再分散乳胶粉的重量比为1000:14。通过加入硫铝酸盐水泥和无水硫酸钠能有效降低混凝土自身收缩,降低透光混凝土板产生裂缝的风险,可一次成型较大面积的透光混凝土板。通过加入可再分散乳胶粉,进一步提高混凝土抗裂性及混凝土与光导纤维界面的粘结力,增强透光混凝土板抗折强度。作为优选的技术方案,水泥基包括以下重量份的各组分:水170份,硅酸盐水泥364.5份,硫铝酸盐水泥13.5份,粉煤灰65.25份,无水硫酸钠6.75份,聚羧酸减水剂2.9份,可再分散乳胶粉6.3份,中砂1350份。作为本发明的一个实施例,所述步骤s6中,一次养护的时间为48小时,二次养护的时间为28天,一次养护与二次养护的温度为20±2℃。与现有技术相比,本发明具有以下有益效果:(1)本发明的造型透光混凝土制作所用的造型模板不仅可实现混凝土表面各种不同定制造型,同时可按设计透光图案精确定位光导纤维,一材两用,并且造型模板可拆卸重复利用,节约造价。(2)本发明的混凝土原料来源广泛,工作性能好,粘结力强,成本低,且具备良好的抗裂性能,可整体成型透光混凝土大板,制得的透光混凝土达到相关技术指标,具有较好的耐久性能。附图说明为了更清楚地说明本发明实施例或现有技术中的技术方案,下面将对实施例或现有技术描述中所需要使用的附图作简单地介绍,显而易见地,下面描述中的附图仅仅是本发明的一些实施例,对于本领域普通技术人员来讲,在不付出创造性劳动的前提下,还可以根据这些附图获得其他的附图。图1为本发明造型混凝土浇筑时的光导纤维布置图。图2为本发明造型混凝土的浇筑模具的结构示意图。其中,附图标记具体说明如下:造型模板(弹性造型模板、硬质泡沫造型模板)1、钢模具2、光纤定位钢板3、光导纤维4。具体实施方式下面将结合本发明实施例中的附图,对本发明实施例中的技术方案进行清楚、完整地描述,显然,所描述的实施例仅仅是本发明一部分实施例,而不是全部的实施例。基于本发明中的实施例,本领域普通技术人员在没有付出创造性劳动前提下所获得的所有其他实施例,都属于本发明保护的范围。实施例1本实施例提供一种造型透光混凝土的制作方法,包括以下步骤:步骤1、根据混凝土表面定制造型图案制作弹性造型模板1;具体如下:按照混凝土的表面造型在模种上利用3d雕刻机雕刻出对应的定制造型图案;在模种上涂刷脱模剂,并将液态胶模基材浇筑在模种上,养护后脱模即得弹性造型模板1;步骤2、安装混凝土浇筑所需的钢模具2;步骤3、按照透光图案在弹性造型模板1上对应的位置打出点阵式密布的光导纤维4定位孔,并将光导纤维4呈现透光图案的一端穿入弹性造型模板1的定位孔中,光导纤维4与弹性造型模板1通过胶黏剂固定,并在弹性造型模板1的表面涂刷脱模剂;步骤4、将弹性造型模板1通过胶黏剂固定在钢模具2上,并将光导纤维4的另一端固定光纤定位钢板3上,光纤定位钢板3固定在上方的工装架上;步骤6、将混凝土在养护室中进行一次养护后脱模,一次养护的时间为48小时,脱模后进行二次养护即得产品,二次养护的时间为28天,一次养护与二次养护的温度为20±2℃。实施例2本实施例提供一种造型透光混凝土的制作方法,包括以下步骤:步骤1、根据混凝土表面定制造型图案制作硬质泡沫造型模板1,具体如下:采用3d雕刻机在硬质泡沫上雕刻出对应的定制造型图案;步骤2、安装混凝土浇筑所需的钢模具2;步骤3、按照透光图案在硬质泡沫造型模板1上对应的位置打出点阵式密布的光导纤维4定位孔,并将光导纤维4呈现透光图案的一端穿入硬质泡沫造型模板1的定位孔中,光导纤维4与硬质泡沫造型模板1通过胶黏剂固定,并在硬质泡沫造型模板1的表面涂刷脱模剂;步骤4、将硬质泡沫造型模板1通过胶黏剂固定在钢模具2上,并将光导纤维4的另一端固定光纤定位钢板3上,光纤定位钢板3固定在上方的工装架上;步骤5、配置水泥基,并将水泥基浇入步骤4形成的浇筑模具中;步骤6、将混凝土在养护室中进行一次养护后脱模,一次养护的时间为48小时,脱模后进行二次养护即得产品,二次养护的时间为28天,一次养护与二次养护的温度为20±2℃。通过实施发现:弹性造型模板1在光导纤维定位和造型定制精度方面都比硬质泡沫造型模板1更高,但弹性造型模板1制作工艺复杂,原材料价格较高,硬质泡沫造型模板1经济性更好,具体实施方法可视工程情况而定。下面通过实施例3-实施例11介绍水泥基的制作过程,水泥基用于实施例1与实施例2的步骤5中。实施例3本实施例提供一种水泥基的制作方法,步骤如下:称取水130g、硅酸盐水泥130g、粉煤灰50g、聚羧酸减水剂4g、中砂402g、石屑402g、聚丙烯长坚纤维200g、脱硫石膏10g,于搅拌机中混合均匀后即得。通过加入脱硫石膏使得碱激发和硫酸盐激发并存,促进水化硅酸钙和水化铝酸钙的形成,生成钙钒石,这些水化产物填充于孔隙中,增加混凝土结构的密实性,优化了孔隙结构,利于强度发展,并提高混凝土的耐久性;本发明通过加入水溶性好的聚丙烯长坚纤维有效降低混凝土自身收缩,降低透光混凝土板产生裂缝的风险,可一次成型较大面积的透光混凝土板;本发明通过用石屑等质量替代50%的细骨料,有效改善了混凝土的开裂问题。实施例4本实施例提供了一种水泥基的制作方法,包括:步骤1、称取硅酸盐水泥803g、二级粉煤灰142g、硫铝酸盐水泥40g、无水硫酸钠15g;步骤2、将步骤1称取的一定量的硅酸盐水泥、二级粉煤灰、硫铝酸盐水泥、无水硫酸钠依次投入搅拌机搅拌均匀,搅拌30s,制得复合胶凝材料;步骤3、称取上述比例所得的胶凝材料450g,水170g,标准砂1350g,聚羧酸减水剂2.9g(减水剂减水率为15%)。根据gb/t17671-1999(iso679:1989)《水泥胶砂强度检验方法》中规定的程序进行搅拌并振实成型,进行1d抗压、抗折试验。实施例5本实施例提供了一种水泥基的制作方法,包括:步骤1、称取硅酸盐水泥803g、二级粉煤灰142g、硫铝酸盐水泥30g、无水硫酸钠15g;步骤2、将步骤1称取的一定量的硅酸盐水泥、二级粉煤灰、硫铝酸盐水泥、无水硫酸钠依次投入搅拌机搅拌均匀,搅拌30s,制得复合胶凝材料;步骤3、称取上述比例所得的胶凝材料450g,水170g,标准砂1350g,聚羧酸减水剂2.9g(减水剂减水率为15%)。根据gb/t17671-1999(iso679:1989)《水泥胶砂强度检验方法》中规定的程序进行搅拌并振实成型,进行1d抗压抗折试验。实施例6本实施例提供了一种水泥基的制作方法,包括:步骤1、称取硅酸盐水泥803g、二级粉煤灰142g、硫铝酸盐水泥20g、无水硫酸钠15g;步骤2、将步骤1称取的一定量的硅酸盐水泥、二级粉煤灰、硫铝酸盐水泥、无水硫酸钠依次投入搅拌机搅拌均匀,搅拌30s,制得复合胶凝材料;步骤3、称取上述比例所得的胶凝材料450g,水170g,标准砂1350g,聚羧酸减水剂2.9g(减水剂减水率为15%)。根据gb/t17671-1999(iso679:1989)《水泥胶砂强度检验方法》中规定的程序进行搅拌并振实成型,进行1d抗压抗折试验。实施例7本实施例提供了一种水泥基的制作方法,包括:步骤1、称取硅酸盐水泥810g、二级粉煤灰145g、硫铝酸盐水泥30g、无水硫酸钠15g;步骤2、将步骤1称取的一定量的硅酸盐水泥、二级粉煤灰、硫铝酸盐水泥、无水硫酸钠依次投入搅拌机搅拌均匀,搅拌30s,制得复合胶凝材料;步骤3、称取上述比例所得的胶凝材料450g,水170g,标准砂1350g,聚羧酸减水剂2.9g(减水剂减水率为15%)。根据gb/t17671-1999(iso679:1989)《水泥胶砂强度检验方法》中规定的程序进行搅拌并振实成型,进行1d抗压抗折试验。实施例8本实施例提供了一种水泥基的制作方法,包括:步骤1、称取硅酸盐水泥820g、二级粉煤灰145g、硫铝酸盐水泥40g、无水硫酸钠15g;步骤2、将步骤1称取的一定量的硅酸盐水泥、二级粉煤灰、硫铝酸盐水泥、无水硫酸钠依次投入搅拌机搅拌均匀,搅拌30s,制得复合胶凝材料;步骤3、称取上述比例所得的胶凝材料450g,水170g,标准砂1350g,聚羧酸减水剂2.9g(减水剂减水率为15%)。根据gb/t17671-1999(iso679:1989)《水泥胶砂强度检验方法》中规定的程序进行搅拌并振实成型,进行1d抗压抗折试验。实施例9本实施例提供了一种水泥基的制作方法,包括:步骤1、称取硅酸盐水泥820g、二级粉煤灰145g、硫铝酸盐水泥30g、无水硫酸钠15g;步骤2、将步骤1称取的一定量的硅酸盐水泥、二级粉煤灰、硫铝酸盐水泥、无水硫酸钠依次投入搅拌机搅拌均匀,搅拌30s,制得复合胶凝材料;步骤3、称取上述比例所得的胶凝材料450g,水170g,标准砂1350g,聚羧酸减水剂2.9g(减水剂减水率为15%)。根据gb/t17671-1999(iso679:1989)《水泥胶砂强度检验方法》中规定的程序进行搅拌并振实成型,进行1d抗压抗折试验。实施例10本实施例提供了一种水泥基的制作方法,包括:步骤1、称取硅酸盐水泥820g、二级粉煤灰145g、硫铝酸盐水泥20g、无水硫酸钠15g;步骤2、将步骤1称取的一定量的硅酸盐水泥、二级粉煤灰、硫铝酸盐水泥、无水硫酸钠依次投入搅拌机搅拌均匀,搅拌30s,制得复合胶凝材料;步骤3、称取上述比例所得的胶凝材料450g,水170g,标准砂1350g,聚羧酸减水剂2.9g(减水剂减水率为15%)。根据gb/t17671-1999(iso679:1989)《水泥胶砂强度检验方法》中规定的程序进行搅拌并振实成型,进行1d抗压抗折试验。实施例11本实施例提供了一种水泥基的制作方法,包括:步骤1、称取硅酸盐水泥810g、二级粉煤灰144g、硫铝酸盐水泥30g、无水硫酸钠15g、可再分散乳胶粉14g;步骤2、将步骤1称取的一定量的硅酸盐水泥、二级粉煤灰、硫铝酸盐水泥、无水硫酸钠、可再分散乳胶粉依次投入搅拌机搅拌均匀,搅拌30s,制得复合胶凝材料;步骤3、称取上述比例所得的胶凝材料450g,水170g,标准砂1350g,聚羧酸减水剂2.9g(减水剂减水率为15%)。根据gb/t17671-1999(iso679:1989)《水泥胶砂强度检验方法》中规定的程序进行搅拌并振实成型,进行1d抗压抗折试验。其中上述8个实施例中胶凝材料各组分满足如下指标:硅酸盐水泥的强度等级为45mpa、粉煤灰为f类ⅱ级粉煤灰、硫铝酸盐水泥的强度等级为45mpa,无水硫酸钠的ph值为6.5。试验结果见表1。表1:各实施例所得的复合胶凝材料制得的砂浆强度对比实施例为了验证实施例4-11中膨胀剂(硫铝酸盐水泥和无水硫酸钠)的加入在透光混凝土中的抗裂作用,另外做了4组对比例进行对比,具体实施如下:对比例1步骤1、称取硅酸盐水泥850g、二级粉煤灰150g、硫铝酸盐水泥0g、无水硫酸钠0g;步骤2、将步骤1称取的一定量的硅酸盐水泥、二级粉煤灰、硫铝酸盐水泥、无水硫酸钠依次投入搅拌机搅拌均匀,搅拌30s,制得复合胶凝材料;步骤3、称取上述比例所得的胶凝材料450g,水170g,标准砂1350g,聚羧酸减水剂2.9g(减水剂减水率为15%)。根据gb/t17671-1999(iso679:1989)《水泥胶砂强度检验方法》中规定的程序进行搅拌并振实成型,进行1d抗压抗折试验。对比例2步骤1、称取硅酸盐水泥837g、二级粉煤灰148g、硫铝酸盐水泥0g、无水硫酸钠15g;步骤2、将步骤1称取的一定量的硅酸盐水泥、二级粉煤灰、硫铝酸盐水泥、无水硫酸钠依次投入搅拌机搅拌均匀,搅拌30s,制得复合胶凝材料;步骤3、称取上述比例所得的胶凝材料450g,水170g,标准砂1350g,聚羧酸减水剂2.9g(减水剂减水率为15%)。根据gb/t17671-1999(iso679:1989)《水泥胶砂强度检验方法》中规定的程序进行搅拌并振实成型,进行1d抗压抗折试验。对比例3步骤1、称取硅酸盐水泥799g、二级粉煤灰141g、硫铝酸盐水泥60g、无水硫酸钠0g;步骤2、将步骤1称取的一定量的硅酸盐水泥、二级粉煤灰、硫铝酸盐水泥、无水硫酸钠依次投入搅拌机搅拌均匀,搅拌30s,制得复合胶凝材料;步骤3、称取上述对比例所得的胶凝材料450g,水170g,标准砂1350g,聚羧酸减水剂2.9g(减水剂减水率为15%)。根据gb/t17671-1999(iso679:1989)《水泥胶砂强度检验方法》中规定的程序进行搅拌并振实成型,进行1d抗压抗折试验。对比例4步骤1、称取硅酸盐水泥786g、二级粉煤灰139g、硫铝酸盐水泥60g、无水硫酸钠15g;步骤2、将步骤1称取的一定量的硅酸盐水泥、二级粉煤灰、硫铝酸盐水泥、无水硫酸钠依次投入搅拌机搅拌均匀,搅拌30s,制得复合胶凝材料;步骤3、称取上述对比例所得的胶凝材料450g,水170g,标准砂1350g,聚羧酸减水剂2.9g(减水剂减水率为15%)。根据gb/t17671-1999(iso679:1989)《水泥胶砂强度检验方法》中规定的程序进行搅拌并振实成型,进行1d抗压抗折试验。对比例中胶凝材料各组分满足如下指标:硅酸盐水泥的强度等级为45mpa、粉煤灰为f类ⅱ级粉煤灰、硫铝酸盐水泥的强度等级为45mpa,无水硫酸钠的ph值为6.5。对比试验制得的复合胶凝材料制得的砂浆1d抗压、抗折强度如表2所示。表2:各对比试验复合胶凝材料制得的砂浆强度对比例1d抗折强度/mpa1d抗压强度/mpa对比例14.014.9对比例25.217.9对比例34.515.0对比例45.116.4从上述实施例4-11和对比例1-4的试验数据可知:硫铝酸盐水泥和无水硫酸钠的加入起到了微膨胀的效应,有利于提高混凝土的早期强度,加入可再分散乳胶粉可提高混凝土界面粘结力,较大提高混凝土的早期抗折强度和抗压强度,明显改善混凝土的抗裂性能并改善混凝土的裂缝问题,达到良好的表观效果。经试验验证,制备该水泥基的最优材料组分为:水170份,硅酸盐水泥364.5份,硫铝酸盐水泥13.5份,粉煤灰65.25份,无水硫酸钠6.75份,聚羧酸减水剂2.9份,可再分散乳胶粉6.3份,中砂1350份。尽管上述实施例已对本发明作出具体描述,但是对于本领域的普通技术人员来说,应该理解为可以在不脱离本发明的精神以及范围之内基于本发明公开的内容进行修改或改进,这些修改和改进都在本发明的精神以及范围之内。当前第1页12