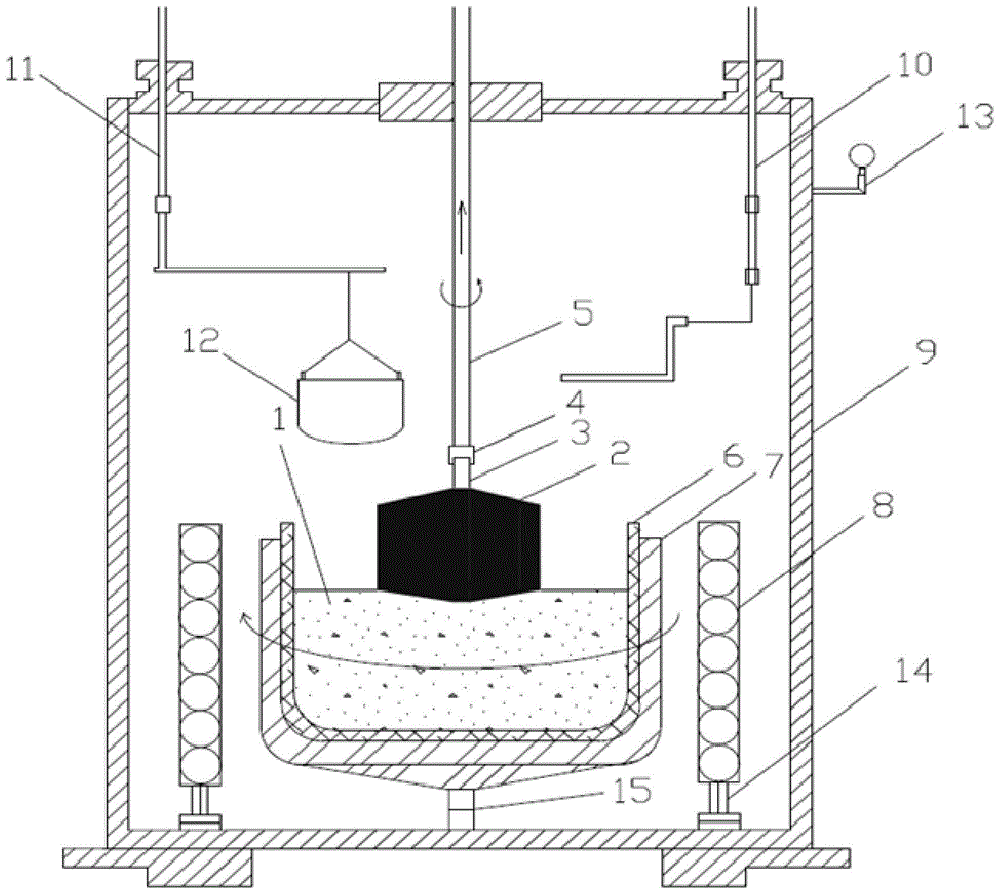
本发明属于高纯金属材料领域,涉及一种超高纯镉晶体的制备方法。
背景技术:
:超高纯镉晶体纯度达到99.99999%(7n),由超高纯镉制备的碲锌镉(czt)核辐射探测器及碲镉汞(mct)红外探测器衬底材料在国防、安防、定位、制导的红外探测等领域有着广泛应用。镉中的杂质直接影响czt和mct晶体材料的使用性能,进而影响这两种探测器的探测范围及探测精度,因此研究制备一种纯度超高、质量性能稳定的超高纯镉产品具有重大意义。目前超高纯镉的主要制备方法包括:真空蒸馏法、定向凝固法、区域熔炼法等,这些方法提纯效果不佳,存在各种各样的缺陷,严重制约了超高纯镉制备技术及后端产业链的发展,如区域熔炼或定向凝固生产的产品需要经过后续处理方式,例如切割、腐蚀等,这些工序可能造成产品交叉污染、工序延长、成本增加等。技术实现要素:为解决上述现有技术中存在的缺点和不足,本发明的目的在于提供一种操作简单、后续处理工序少、提纯效果好、安全经济环保的超高纯镉晶体的制备方法。本发明提供了一种超高纯镉晶体(纯度7n以上)的制备方法,包括以下步骤:(1)将原料镉置于漏斗中,再在真空条件下或保护气气氛中使所述原料镉完全熔化以形成镉熔体,所述镉熔体沿所述漏斗的漏孔滴入或流入坩埚中;(2)采用垂直提拉法对所述坩埚中的镉熔体进行提纯,得到晶体产品;所述晶体产品即为超高纯镉晶体,或者将所述晶体产品重复步骤(1)-(2)的处理1次以上,即得超高纯镉晶体。原料镉,如5n镉,在制备过程中,表面会形成富含杂质的氧化镉薄膜,如果将其直接置于坩埚中熔料,那么后续采用垂直提拉法提纯时,这些氧化渣料会附着在镉晶体表面,因此需要增加扒渣工序以去掉大部分渣料,但受限于设备结构,渣料无法完全去除。上述制备方法将原料镉在漏斗中熔料,熔化后熔体会沿漏孔滴入或流入坩埚中,在此过程中,氧化渣料会漂浮在熔体表面形成薄膜最终残留在漏斗中,这样坩埚内的熔体无需扒渣处理,即可光亮无氧化。另外,上述制备方法采用垂直提拉法对坩埚中的镉熔体进行提纯,所得晶体结构稳定,表面光亮无氧化,显金属本色,无需后续处理,可根据客户需要拉制不同大小的产品。另外,垂直提拉法还存在以下优点:在生产过程中可以方便的观察晶体的生长状态;晶体在熔体表面处生长,而不与坩埚相接触,这样能显著地减小晶体的应力,并防止锅壁的寄生成核;可以方便地使用定向籽晶和“缩颈”工艺,缩颈后面的籽晶位错可大大减少,这样可使放大后生长出来的晶体位错密度降低。总之,垂直提拉法生长的晶体完整性很高,生长率和晶体尺寸也能令人满意,且具有较低的位错密度,较高的光学均匀性,也不存在锒嵌结构。上述保护气一般为氮气或者惰性气体,惰性气体包括氦气、氖气、氩气。优选地,所述步骤(1)中,所述原料镉先在真空度不高于5×10-3pa的条件下预热至150~200℃,保温30-60min后在0.1-0.15mpa的保护气气氛中完全熔化,然后在320~350℃条件下滴入或流入所述坩埚中。优选地,所述垂直提拉法包括以下步骤:先将镉籽晶预热以防引晶时液面凝固,再在所述镉籽晶相对所述坩埚旋转的条件下,使所述镉籽晶与所述坩埚中的镉熔体接触,待所述镉籽晶与所述坩埚中的镉熔体接触部分熔为一体后,依次经引晶、放肩、转肩、等径生长处理,然后停止晶体生长,冷却,得到所述晶体产品。上述制备方法在引晶时即让镉籽晶相对坩埚中的镉熔体进行旋转,这不仅使镉籽晶能更好的形成晶体,也使后续得到的晶体结构更好。优选地,所述镉籽晶预热的处理方法为:将镉籽晶置于所述坩埚中的镉熔体上方5-10mm处,并在320~350℃条件下预热10-15min。优选地,所述旋转的转速为18~27r/min;所述引晶的速度为10~30mm/min,所述引晶的长度为2-5cm;所述放肩的速度为5~10mm/h;所述转肩的速度为15~30mm/h;所述等径生长的速度为15~30mm/h。优选地,所述镉籽晶相对所述坩埚进行所述旋转时,所述镉籽晶和所述坩埚分别进行方向相反的旋转运动,其中,所述镉籽晶以10~15r/min的转速旋转运动,所述坩埚以8~12r/min的转速旋转运动。优选地,所述停止晶体生长时,所述坩埚内物料剩余10~15%。优选地,所述原料镉的纯度为5n,所述重复步骤(1)-(2)的处理的次数为1~2次。优选地,所述漏斗和所述坩埚均为石英材质,所述漏斗和所述坩埚的表面均镀有热解碳膜。高温下,石英容器会污染熔体,例如si造成晶体的纯度降低;另外液态镉冷凝成固态,表面张力影响导致石英破裂。在石英器件表面镀热解碳膜,能避免将石英器件中的杂质带入物料中,减少物料的污染,同时,石英器件镀碳后,物料冷却后不会粘连在石英器件上,既能减少物料损失,又能避免石英器件破裂。优选地,所述漏斗的漏孔为1~2mm。当漏斗的漏孔为1~2mm时,镉熔体滴入坩埚中,能很好的去除其内的氧化渣料。与现有技术相比,本发明具有如下优点:本发明将原料镉在漏斗中熔料,以将其内的氧化渣料残留在漏斗中,使沿漏斗漏孔滴入或流入坩埚中的镉熔体无需扒渣处理,即可光亮无氧化;另外,采用垂直提拉法对坩埚中的镉熔体进行提纯,所得晶体位错密度低、光学均匀性高、结构稳定,表面光亮无氧化,显金属本色,无需后续处理,可根据客户需要拉制不同大小的产品。附图说明图1为各实施例所用单晶炉示意图;其中,1-镉原料熔体,2-镉单晶产品,3-籽晶,4-籽晶夹具,5-籽晶杆,6-石英坩埚,7-石墨坩埚,8-加热温场,9-炉体外壳,10-扒渣杆,11-挂料杆,12-石英漏斗,13-压力表,14-加热电极,15-石墨坩埚基座。具体实施方式为更好的说明本发明的目的、技术方案和优点,本发明通过下列实施例进一步说明。显然,下列实施例仅是本发明的一部分实施例,而不是全部的实施例。应理解,本发明实施例仅用于说明本发明的技术效果,而非用于限制本发明的保护范围。实施例1本实施例为本发明超高纯镉晶体的制备方法的一种实施方式。本实施例超高纯镉晶体的制备方法所采用的装置如图1所示,并包括以下步骤:(1)将5n原料镉投入石英漏斗中,石英漏斗与石英坩埚上下对齐,关闭单晶炉炉门,开启真空泵抽真空至5×10-3pa以下;(2)开启预热,预热至150℃,然后继续抽真空,并预热保温30min;(3)关闭真空泵,往炉体内充入经净化的高纯氮气(6n以上),至压力充为0.1mpa,关闭充气阀;(4)调大加热功率,将5n原料镉熔化,使其从石英漏斗中滴入石英坩埚中,待原料镉全部熔化完后,将温度稳定在320℃,保温30min;(5)调节籽晶杆,将籽晶下降至距熔体10mm,预热籽晶10min;(6)使籽晶杆以10r/min的转速逆时针旋转,石墨坩埚以8r/min的转速顺时针旋转;(7)缓慢将籽晶降至与石英坩埚中的镉熔体接触,待籽晶与熔体熔为一体后,开始手动点动引晶,设置引晶速度为10mm/min,引晶长度为2cm;(8)引晶结束后,进入系统自动控制,开始进行放肩操作,设置放肩速度为5mm/h;(9)放肩至需要的肩面大小,开始进行转肩操作,设置转肩速度为15mm/h;(10)转肩完成后,进行等径生长操作,等径生长速度为15mm/h;(11)待石英坩埚内物料剩余15%时,停止晶体生长,将晶体提升至脱离熔体,关闭加热,冷却后出炉,得到的产品为6n镉;(12)重复步骤1~11操作以将6n镉重新提拉一次,参数不变,得到7n超高纯镉晶体。将所得超高纯镉晶体产品取样送gdms检测。实施例2本实施例为本发明超高纯镉晶体的制备方法的一种实施方式。本实施例超高纯镉晶体的制备方法所采用的装置如图1所示,并包括以下步骤:(1)将5n原料镉投入石英漏斗中,石英漏斗与石英坩埚上下对齐,关闭单晶炉炉门,开启真空泵抽真空至5×10-3pa以下;(2)开启预热,预热至180℃,然后继续抽真空,并预热保温30min;(3)关闭真空泵,往炉体内充入经净化的高纯氮气(6n以上),至压力充为0.1mpa,关闭充气阀;(4)调大加热功率,将5n原料镉熔化,使其从石英漏斗中滴入石英坩埚中,待原料镉全部熔化完后,将温度稳定在340℃,保温30min;(5)调节籽晶杆,将籽晶下降至距熔体10mm,预热籽晶10min;(6)使籽晶杆以12r/min的转速逆时针旋转,石墨坩埚以10r/min的转速顺时针旋转;(7)缓慢将籽晶降至与熔体接触,待籽晶与熔体熔为一体后,开始手动点动引晶,设置引晶速度为20mm/min,引晶长度为2cm;(8)引晶结束后,进入系统自动控制,开始进行放肩操作,设置放肩速度为10mm/h;(9)放肩至需要的肩面大小,开始进行转肩操作,设置转肩速度为30mm/h;(10)转肩完成后,进行等径生长操作,等径生长速度为30mm/h;(11)待石英坩埚内物料剩余15%时,停止晶体生长,将晶体提升至脱离熔体,关闭加热,冷却后出炉,得到的产品为6n镉;(12)重复步骤1~11操作以将6n镉重新提拉一次,参数不变,得到7n超高纯镉晶体。将所得超高纯镉晶体产品取样送gdms检测。实施例3本实施例为本发明超高纯镉晶体的制备方法的一种实施方式。本实施例超高纯镉晶体的制备方法所采用的装置如图1所示,并包括以下步骤:(1)将5n原料镉投入石英漏斗中,石英漏斗与石英坩埚上下对齐,关闭单晶炉炉门,开启真空泵抽真空至5×10-3pa以下;(2)开启预热,预热至200℃,然后继续抽真空,并预热保温30min;(3)关闭真空泵,往炉体内充入经净化的高纯氮气(6n以上),至压力充为0.1mpa,关闭充气阀;(4)调大加热功率,将5n原料镉熔化,使其从石英漏斗中滴入石英坩埚中,待原料镉全部熔化完后,将温度稳定在350℃,保温30min;(5)调节籽晶杆,将籽晶下降至距熔体10mm,预热籽晶10min;(6)使籽晶杆以15r/min的转速逆时针旋转,石墨坩埚以12r/min的转速顺时针旋转;(7)缓慢将籽晶降至与熔体接触,待籽晶与熔体熔为一体后,开始手动点动引晶,设置引晶速度为30mm/min,引晶长度为2cm;(8)引晶结束后,进入系统自动控制,开始进行放肩操作,设置放肩速度为10mm/h;(9)放肩至需要的肩面大小,开始进行转肩操作,设置转肩速度为15mm/h;(10)转肩完成后,进行等径生长操作,等径生长速度为30mm/h;(11)待石英坩埚内物料剩余10%时,停止晶体生长,将晶体提升至脱离熔体,关闭加热,冷却后出炉,得到的产品为6n镉;(12)重复步骤1~11操作以将6n镉重新提拉一次,参数不变,得到7n超高纯镉晶体。将所得超高纯镉晶体产品取样送gdms检测。实施例4本实施例为本发明超高纯镉晶体的制备方法的一种实施方式。本实施例超高纯镉晶体的制备方法所采用的装置如图1所示,并包括以下步骤:(1)将5n原料镉投入石英漏斗中,石英漏斗与石英坩埚上下对齐,关闭单晶炉炉门,开启真空泵抽真空至5×10-3pa以下;(2)开启预热,预热至150℃,然后继续抽真空,并预热保温30min;(3)关闭真空泵,往炉体内充入经净化的高纯氮气(6n以上),至压力充为0.1mpa,关闭充气阀;(4)调大加热功率,将5n原料镉熔化,使其从石英漏斗中滴入石英坩埚中,待原料镉全部熔化完后,将温度稳定在320℃,保温30min;(5)调节籽晶杆,将籽晶下降至距熔体10mm,预热籽晶10min;(6)使籽晶杆以12r/min的转速逆时针旋转,石墨坩埚以12r/min的转速顺时针旋转;(7)缓慢将籽晶降至与熔体接触,待籽晶与熔体熔为一体后,开始手动点动引晶,设置引晶速度为30mm/min,引晶长度为2cm;(8)引晶结束后,进入系统自动控制,开始进行放肩操作,设置放肩速度为10mm/h;(9)放肩至需要的肩面大小,开始进行转肩操作,设置转肩速度为30mm/h;(10)转肩完成后,进行等径生长操作,等径生长速度为30mm/h;(11)待石英坩埚内物料剩余10%时,停止晶体生长,将晶体提升至脱离熔体,关闭加热,冷却后出炉,得到的产品为6n镉;(12)重复步骤1~11操作以将6n镉重新提拉一次,参数不变,得到7n超高纯镉晶体。将所得超高纯镉晶体产品取样送gdms检测。实施例5本实施例为本发明超高纯镉晶体的制备方法的一种实施方式。本实施例超高纯镉晶体的制备方法所采用的装置如图1所示,并包括以下步骤:(1)将5n原料镉投入石英漏斗中,石英漏斗与石英坩埚上下对齐,关闭单晶炉炉门,开启真空泵抽真空至5×10-3pa以下;(2)开启预热,预热至200℃,然后继续抽真空,并预热保温30min;(3)关闭真空泵,往炉体内充入经净化的高纯氮气(6n以上),至压力充为0.1mpa,关闭充气阀;(4)调大加热功率,将5n原料镉熔化,使其从石英漏斗中滴入石英坩埚中,待原料镉全部熔化完后,将温度稳定在330℃,保温30min;(5)调节籽晶杆,将籽晶下降至距熔体10mm,预热籽晶10min;(6)使籽晶杆以15r/min的转速逆时针旋转,石墨坩埚以10r/min的转速顺时针旋转;(7)缓慢将籽晶降至与熔体接触,待籽晶与熔体熔为一体后,开始手动点动引晶,设置引晶速度为10mm/min,引晶长度为2cm;(8)引晶结束后,进入系统自动控制,开始进行放肩操作,设置放肩速度为5mm/h;(9)放肩至需要的肩面大小,开始进行转肩操作,设置转肩速度为15mm/h;(10)转肩完成后,进行等径生长操作,等径生长速度为15mm/h;(11)待石英坩埚内物料剩余15%时,停止晶体生长,将晶体提升至脱离熔体,关闭加热,冷却后出炉,得到的产品为6n镉;(12)重复步骤1~11操作以将6n镉重新提拉一次,参数不变,得到7n超高纯镉晶体。将所得超高纯镉晶体产品取样送gdms检测。实施例1-5制得的超高纯镉晶体产品为单晶,它们的gdms分析结果如表1所示。表1超高纯镉杂质情况统计表(单位:ppb)杂质agalcacrcufeznmgnipbsn国标<5<5<5<5<5<10<20<5<5<5<5实施例1<5<5<5<5<5<5<5<5<5<5<5实施例2<5<5<55<565<5<56<5实施例3<5<5<5<5<5710<5<5<5<5实施例4<5<5<5<5<558<5<5<5<5实施例5<5<5<5<5<567<5<5<5<5由表1可以看出,经过2次垂直提拉法提纯后,镉的杂质含量都可以控制在100ppba以下,且单个杂质都在标准范围内,符合超高纯镉杂质含量要求。同时,得到工艺合理的参数设计为:真空度在5×10-3pa以下,预热温度150~200℃,物料熔化后温度维持在320~350℃,籽晶杆、石墨坩埚转速分别为10~15r/min和8~12r/min,引晶速度为10~30mm/min,放肩速度为5~15mm/h,转肩速度为15~30mm/h,等径生长速度为15~30mm/h,石英坩埚内物料剩余10~15%;最佳参数控制为:真空度在5×10-3pa以下,预热温度150℃,物料熔化后温度维持在320℃,籽晶杆、石墨坩埚转速分别为10r/min和8r/min,引晶速度为10mm/min,放肩速度为5mm/h,转肩速度为15mm/h,等径生长速度为15mm/h,石英坩埚内物料剩余10~15%。最后应当说明的是,以上实施例仅用以说明本发明的技术方案而非对本发明保护范围的限制,尽管参照较佳实施例对本发明作了详细说明,本领域的普通技术人员应当理解,可以对本发明的技术方案进行修改或者等同替换,而不脱离本发明技术方案的实质和范围。当前第1页12