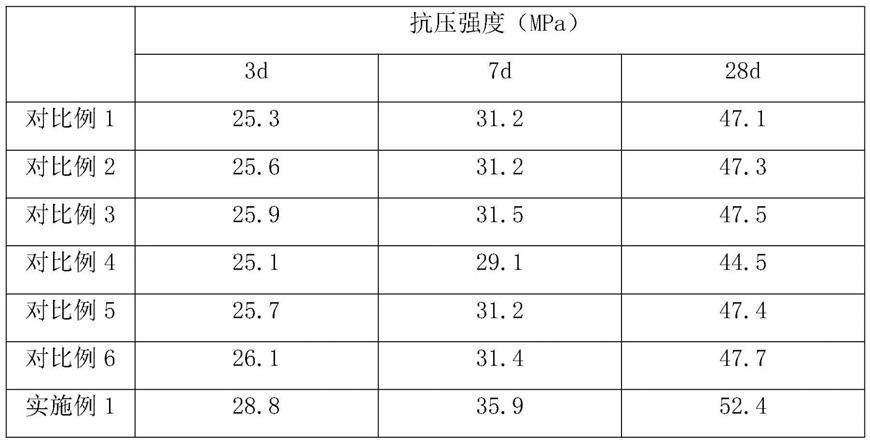
1.本发明涉及混凝土掺合料技术领域,更具体地说,本发明涉及一种早强复合型矿渣掺合料及其制备方法。
背景技术:2.掺合料是混凝土不可替代的重要组成部分,可改善新拌混凝土性能,并提高混凝土密实性耐久性。混凝土掺合料技术研究,就是减少水泥用量、改善施工性能、提高密实性与耐久性。常用的混凝掺合料有粉煤灰、粒化高炉矿渣、火山灰类物质;尤其是粉煤灰、超细粒化电炉矿渣、硅灰等应用效果良好。钢渣中含有一定量的硅酸三钙、硅酸二钙等水泥熟料类矿物,具有潜在的胶凝活性,因而可用作水泥混合材和混凝土掺合料。掺加钢渣粉或复合钢渣粉,可有效提高其后期强度、抗折强度、耐磨性,降低脆度系数低的特点。
3.矿物掺合料中往往带有矿渣这一类具有火山灰反应活性的物质,这类物质往往需要外界环境刺激才会与水泥协同水化,且钢渣中普遍含有大量的重金属元素,活性二氧化硅含量较少,水化时不易反应,因而强度增长较慢。
技术实现要素:4.为了克服现有技术的上述缺陷,本发明的实施例提供一种早强复合型矿渣掺合料及其制备方法。
5.一种早强复合型矿渣掺合料,按照重量百分比计算包括:44.6~45.6%的矿渣粉、29.4~30.4%的钢渣粉、2.1~2.9%的早强剂,其余为补充剂。
6.进一步的,所述补充剂按照重量百分比计算包括:34.4~35.4%的膨润土、15.7~16.5%的氢氧化钠、3.6~4.6%的十二烷基磺酸钠,其余为沸石。
7.进一步的,早强复合型矿渣掺合料按照重量百分比计算包括:44.6%的矿渣粉、29.4%的钢渣粉、2.1%的早强剂,其余为补充剂;所述补充剂按照重量百分比计算包括:34.4%的膨润土、15.7%的氢氧化钠、3.6%的十二烷基磺酸钠,其余为沸石。
8.进一步的,早强复合型矿渣掺合料按照重量百分比计算包括:45.6%的矿渣粉、30.4%的钢渣粉、2.9%的早强剂,其余为补充剂;所述补充剂按照重量百分比计算包括:35.4%的膨润土、16.5%的氢氧化钠、4.6%的十二烷基磺酸钠,其余为沸石。
9.进一步的,早强复合型矿渣掺合料按照重量百分比计算包括:45.1%的矿渣粉、29.9%的钢渣粉、2.5%的早强剂,其余为补充剂;所述补充剂按照重量百分比计算包括:34.9%的膨润土、16.1%的氢氧化钠、4.1%的十二烷基磺酸钠,其余为沸石。
10.进一步的,所述早强剂为:甲酸钙、乙酸钙、甲酸钠、硫酸钠、碳酸锂、硝酸钙中的一种或多种复配制成。
11.一种早强复合型矿渣掺合料的制备方法,具体制备步骤如下:
12.步骤一:称取上述重量份的矿渣粉、钢渣粉、早强剂、补充剂中的膨润土、氢氧化钠、十二烷基磺酸钠、沸石;
13.步骤二:将步骤一中的膨润土、十二烷基磺酸钠和四分之一重量份的氢氧化钠加入到去离子水中,进行水浴超声处理60~80分钟,过滤洗涤,得到改性膨润土;
14.步骤三:将步骤一中三分之一重量份的沸石和剩余的氢氧化钠加入到去离子水中,进行水浴处理11~13小时,过滤洗涤,得到改性沸石a;
15.步骤四:将步骤一中三分之一重量份的沸石在280~320℃下灼烧处理2~4小时,得到改性沸石b;将步骤一中剩余的沸石在770~830℃下煅烧处理2~4小时,得到改性沸石c;
16.步骤五:将步骤二中的改性膨润土、步骤三中的改性沸石a、步骤四中的改性沸石b和改性沸石c进行共混,得到补充剂;
17.步骤六:将步骤一中的矿渣粉和钢渣粉进行粉磨处理,得到混合料d;
18.步骤七:将步骤六中的混合料d和步骤五中的补充剂加入去离子水中,进行浸泡搅拌处理13~15天,然后进行加热保温通入二氧化碳110~130min;过滤干燥处理,得到混合料e;
19.步骤八:将步骤七中的混合料e与步骤一中的早强剂进行共混均匀,得到早强复合型矿渣掺合料。
20.进一步的,在步骤二中,膨润土、十二烷基磺酸钠和四分之一重量份的氢氧化钠的总重量与去离子水的重量比为1∶10~12,水浴温度为50~70℃,超声频率为1.3~1.5mhz,超声功率为300~400w,采用去离子水进行洗涤;在步骤三中,沸石和剩余的氢氧化钠的总重量与去离子水的重量比为1∶15~19,水浴温度为90~100℃,采用去离子水进行洗涤;在步骤七中,注塑成型时,混合料d和补充剂的总重量与去离子水的重量比为1∶8~10,加热到80~90℃后进行保温。
21.进一步的,在步骤二中,膨润土、十二烷基磺酸钠和四分之一重量份的氢氧化钠的总重量与去离子水的重量比为1∶10,水浴温度为50℃,超声频率为1.3mhz,超声功率为300w,采用去离子水进行洗涤;在步骤三中,沸石和剩余的氢氧化钠的总重量与去离子水的重量比为1∶15,水浴温度为90℃,采用去离子水进行洗涤;在步骤七中,注塑成型时,混合料d和补充剂的总重量与去离子水的重量比为1∶8,加热到80℃后进行保温。
22.进一步的,在步骤二中,膨润土、十二烷基磺酸钠和四分之一重量份的氢氧化钠的总重量与去离子水的重量比为1∶11,水浴温度为60℃,超声频率为1.4mhz,超声功率为350w,采用去离子水进行洗涤;在步骤三中,沸石和剩余的氢氧化钠的总重量与去离子水的重量比为1∶17,水浴温度为95℃,采用去离子水进行洗涤;在步骤七中,注塑成型时,混合料d和补充剂的总重量与去离子水的重量比为1∶9,加热到85℃后进行保温。
23.本发明的技术效果和优点:
24.1、采用本发明的原料配方所制备出的一种早强复合型矿渣掺合料,可有效对钢渣内部的重金属离子进行吸附隔离处理,避免重金属离子扩散;可有效加强矿物掺合料的火山灰反应活性,可有效加强矿物掺合料的碳酸化处理效果,进而有效提高混凝土抗压强度和结构强度;膨润土添加到矿渣掺合料中,可有效加强对钢渣粉和矿渣粉中的重金属离子进行吸附隔离处理,可有效避免重金属离子在混凝土中持续扩散,进而保证混凝土的稳定性和结构强度;膨润土在碱性环境下通过十二烷基磺酸钠进行表面改性处理,可进一步加强膨润土对重金属离子的吸附处理效果;沸石经过300℃左右高温灼烧处理后,得到热活化
改性处理的沸石添加到矿渣掺合料中,可有效加强对混凝土中重金属离子的吸附处理效果,进一步降低重金属离子在混凝土中的扩散性能,进一步提高混凝土的稳定性和结构强度;沸石在氢氧化钠水溶液中进行水热处理,可实现对沸石的水热钠改性处理的沸石,添加到矿渣掺合料中,可进一步加强对混凝土中重金属离子的吸附处理效果,进一步降低重金属离子在混凝土中的扩散性能,进一步提高混凝土的稳定性和结构强度;在800℃对沸石进行煅烧预处理,然后将煅烧预处理后的沸石和矿渣粉、钢渣粉在水中进行水化处理,然后通入二氧化碳对矿渣粉和钢渣粉进行碳酸化处理,高温预处理可以破坏沸石的四面体结构,增加沸石内部活性二氧化硅含量,从而改善沸石的前期火山灰活性,降低沸石自身孔隙率,在高温预处理的沸石作用下,可有效加强对矿渣粉和钢渣粉的碳酸化处理效果,可有效降低矿渣粉和钢渣粉的孔隙率,进而提高矿渣粉和钢渣粉的使用效果,混凝土结构强度更佳;
25.2、本发明在步骤二中,将膨润土、十二烷基磺酸钠和氢氧化钠加入到水中,进行水浴超声处理后,过滤洗涤,可有效加强对膨润土的改性处理效果;在步骤三中,将沸石、氢氧化钠加入到水中,进行水浴处理,过滤洗涤,可有效加强钠离子与沸石的接触改性处理效果;在步骤四中,对沸石在不同温度下进行灼烧或煅烧处理,可得到不同温度改性处理的沸石;在步骤五中,将改性膨润土、改性沸石a、改性沸石b和改性沸石c进行共混,得到补充剂;在步骤六中,将矿渣粉和钢渣粉进行粉磨处理,可有效缩小矿渣粉和钢渣粉的粒径,同时加强矿渣粉和钢渣粉的共混效果;在步骤七中,将补充剂和混合料d在水中进行浸泡搅拌预水化处理,然后加热保温通入二氧化碳,可有效加强对矿渣粉和钢渣粉碳酸化处理效果;在步骤八中,将混合料e和早强剂进行共混,得到早强复合型矿渣掺合料。
具体实施方式
26.下面将结合本发明实施例中的技术方案进行清楚、完整地描述,显然,所描述的实施例仅仅是本发明一部分实施例,而不是全部的实施例。基于本发明中的实施例,本领域普通技术人员在没有做出创造性劳动前提下所获得的所有其他实施例,都属于本发明保护的范围。
27.实施例1:
28.本发明提供了一种早强复合型矿渣掺合料,按照重量百分比计算包括:44.6%的矿渣粉、29.4%的钢渣粉、2.1%的早强剂,其余为补充剂;所述补充剂按照重量百分比计算包括:34.4%的膨润土、15.7%的氢氧化钠、3.6%的十二烷基磺酸钠,其余为沸石;矿渣粉采购自灵寿县盛运矿产品加工厂、s95级高炉矿渣微粉;钢渣粉采购自灵寿县辰洋矿产品有限公司、型号:cy-82;膨润土采购自(克拉玛尔)上海紫铭试剂厂、cas号:1302-78-9;氢氧化钠采购自济南利扬化工有限公司、cas号:1310-73-2;十二烷基磺酸钠采购自(克拉玛尔)上海紫铭试剂厂、cas号:2386-53-0、品牌:图赫;沸石采购自信阳市泰昌矿产有限公司、沸石种类:天然沸石;
29.所述早强剂为:甲酸钙采购自上海易恩化学技术有限公司、cas号:544-17-2、货号:r020230;
30.本发明还提供一种早强复合型矿渣掺合料的制备方法,具体制备步骤如下:
31.步骤一:称取上述重量份的矿渣粉、钢渣粉、早强剂、补充剂中的膨润土、氢氧化钠、十二烷基磺酸钠、沸石;
32.步骤二:将步骤一中的膨润土、十二烷基磺酸钠和四分之一重量份的氢氧化钠加入到去离子水中,进行水浴超声处理60分钟,过滤洗涤,得到改性膨润土;
33.步骤三:将步骤一中三分之一重量份的沸石和剩余的氢氧化钠加入到去离子水中,进行水浴处理11小时,过滤洗涤,得到改性沸石a;
34.步骤四:将步骤一中三分之一重量份的沸石在280℃下灼烧处理2小时,得到改性沸石b;将步骤一中剩余的沸石在770℃下煅烧处理2小时,得到改性沸石c;
35.步骤五:将步骤二中的改性膨润土、步骤三中的改性沸石a、步骤四中的改性沸石b和改性沸石c进行共混,得到补充剂;
36.步骤六:将步骤一中的矿渣粉和钢渣粉进行粉磨处理,得到混合料d;
37.步骤七:将步骤六中的混合料d和步骤五中的补充剂加入去离子水中,进行浸泡搅拌处理13天,然后进行加热保温通入二氧化碳110min;过滤干燥处理,得到混合料e;
38.步骤八:将步骤七中的混合料e与步骤一中的早强剂进行共混均匀,得到早强复合型矿渣掺合料。
39.在步骤二中,膨润土、十二烷基磺酸钠和四分之一重量份的氢氧化钠的总重量与去离子水的重量比为1∶10,水浴温度为50℃,超声频率为1.3mhz,超声功率为300w,采用去离子水进行洗涤;在步骤三中,沸石和剩余的氢氧化钠的总重量与去离子水的重量比为1∶15,水浴温度为90℃,采用去离子水进行洗涤;在步骤七中,注塑成型时,混合料d和补充剂的总重量与去离子水的重量比为1∶8,加热到80℃后进行保温。
40.实施例2:
41.与实施例1不同的是,早强复合型矿渣掺合料按照重量百分比计算包括:45.6%的矿渣粉、30.4%的钢渣粉、2.9%的早强剂,其余为补充剂;所述补充剂按照重量百分比计算包括:35.4%的膨润土、16.5%的氢氧化钠、4.6%的十二烷基磺酸钠,其余为沸石。
42.实施例3:
43.与实施例1-2均不同的是,早强复合型矿渣掺合料按照重量百分比计算包括:45.1%的矿渣粉、29.9%的钢渣粉、2.5%的早强剂,其余为补充剂;所述补充剂按照重量百分比计算包括:34.9%的膨润土、16.1%的氢氧化钠、4.1%的十二烷基磺酸钠,其余为沸石。
44.实施例4:
45.与实施例3不同的是,在步骤二中,膨润土、十二烷基磺酸钠和四分之一重量份的氢氧化钠的总重量与去离子水的重量比为1∶12,水浴温度为70℃,超声频率为1.5mhz,超声功率为400w,采用去离子水进行洗涤;在步骤三中,沸石和剩余的氢氧化钠的总重量与去离子水的重量比为1∶19,水浴温度为100℃,采用去离子水进行洗涤;在步骤七中,注塑成型时,混合料d和补充剂的总重量与去离子水的重量比为1∶10,加热到90℃后进行保温。
46.实施例5:
47.与实施例3不同的是,在步骤二中,膨润土、十二烷基磺酸钠和四分之一重量份的氢氧化钠的总重量与去离子水的重量比为1∶11,水浴温度为60℃,超声频率为1.4mhz,超声功率为350w,采用去离子水进行洗涤;在步骤三中,沸石和剩余的氢氧化钠的总重量与去离子水的重量比为1∶17,水浴温度为95℃,采用去离子水进行洗涤;在步骤七中,注塑成型时,混合料d和补充剂的总重量与去离子水的重量比为1∶9,加热到85℃后进行保温。
48.实施例6:
49.与实施例5不同的是,
50.早强复合型矿渣掺合料的制备方法,具体制备步骤如下:
51.步骤一:称取上述重量份的矿渣粉、钢渣粉、早强剂、补充剂中的膨润土、氢氧化钠、十二烷基磺酸钠、沸石;
52.步骤二:将步骤一中的膨润土、十二烷基磺酸钠和四分之一重量份的氢氧化钠加入到去离子水中,进行水浴超声处理80分钟,过滤洗涤,得到改性膨润土;
53.步骤三:将步骤一中三分之一重量份的沸石和剩余的氢氧化钠加入到去离子水中,进行水浴处理13小时,过滤洗涤,得到改性沸石a;
54.步骤四:将步骤一中三分之一重量份的沸石在320℃下灼烧处理4小时,得到改性沸石b;将步骤一中剩余的沸石在830℃下煅烧处理4小时,得到改性沸石c;
55.步骤五:将步骤二中的改性膨润土、步骤三中的改性沸石a、步骤四中的改性沸石b和改性沸石c进行共混,得到补充剂;
56.步骤六:将步骤一中的矿渣粉和钢渣粉进行粉磨处理,得到混合料d;
57.步骤七:将步骤六中的混合料d和步骤五中的补充剂加入去离子水中,进行浸泡搅拌处理15天,然后进行加热保温通入二氧化碳130min;过滤干燥处理,得到混合料e;
58.步骤八:将步骤七中的混合料e与步骤一中的早强剂进行共混均匀,得到早强复合型矿渣掺合料。
59.实施例7:
60.与实施例5不同的是,
61.早强复合型矿渣掺合料的制备方法,具体制备步骤如下:
62.步骤一:称取上述重量份的矿渣粉、钢渣粉、早强剂、补充剂中的膨润土、氢氧化钠、十二烷基磺酸钠、沸石;
63.步骤二:将步骤一中的膨润土、十二烷基磺酸钠和四分之一重量份的氢氧化钠加入到去离子水中,进行水浴超声处理70分钟,过滤洗涤,得到改性膨润土;
64.步骤三:将步骤一中三分之一重量份的沸石和剩余的氢氧化钠加入到去离子水中,进行水浴处理12小时,过滤洗涤,得到改性沸石a;
65.步骤四:将步骤一中三分之一重量份的沸石在300℃下灼烧处理3小时,得到改性沸石b;将步骤一中剩余的沸石在800℃下煅烧处理3小时,得到改性沸石c;
66.步骤五:将步骤二中的改性膨润土、步骤三中的改性沸石a、步骤四中的改性沸石b和改性沸石c进行共混,得到补充剂;
67.步骤六:将步骤一中的矿渣粉和钢渣粉进行粉磨处理,得到混合料d;
68.步骤七:将步骤六中的混合料d和步骤五中的补充剂加入去离子水中,进行浸泡搅拌处理14天,然后进行加热保温通入二氧化碳120min;过滤干燥处理,得到混合料e;
69.步骤八:将步骤七中的混合料e与步骤一中的早强剂进行共混均匀,得到早强复合型矿渣掺合料。
70.对比例1:
71.与实施例3不同的是:早强复合型矿渣掺合料按照重量百分比计算包括:45.1%的矿渣粉、29.9%的钢渣粉、2.5%的早强剂,其余为补充剂;所述补充剂按照重量百分比计算
包括:16.1%的氢氧化钠、4.1%的十二烷基磺酸钠,其余为膨润土。
72.对比例2:
73.与实施例3不同的是:早强复合型矿渣掺合料按照重量百分比计算包括:45.1%的矿渣粉、29.9%的钢渣粉、2.5%的早强剂,其余为补充剂;所述补充剂按照重量百分比计算包括:16.1%的氢氧化钠、4.1%的十二烷基磺酸钠,其余为沸石。
74.对比例3:
75.与实施例3不同的是:早强复合型矿渣掺合料按照重量百分比计算包括:45.1%的矿渣粉、29.9%的钢渣粉、2.5%的早强剂,其余为补充剂;所述补充剂按照重量百分比计算包括:34.9%的膨润土、4.1%的十二烷基磺酸钠,其余为沸石。
76.对比例4:
77.与实施例7不同的是:直接将补充剂原料进行共混处理,得到补充剂。
78.对比例5:
79.与实施例7不同的是:在步骤四中,没有进行高温灼烧和煅烧处理。
80.对比例6:
81.与实施例7不同的是:在步骤七中,将混合料d和补充剂加入去离子水中,然后进行加热保温通入二氧化碳110~130min;过滤干燥处理,得到混合料e。
82.对本发明的实施例和对比例中的早强复合型矿渣掺合料进行实验,按照比例制成混凝土,配合比(kg/m3):(水胶比:0.42、水:189、p.o42.5水泥:360、实施例或对比例中的早强复合型矿渣掺合料:90、中砂:669、碎石(5-20mm):1092、减水剂:4.5),参照《普通混凝土力学性能试验方法标准》(gb/t50081-2002)对上述混凝土进行抗压强度测试,如表一所示:
83.表一:
84.[0085][0086]
由上表可知:本发明的早强复合型矿渣掺合料,可有效对钢渣内部的重金属离子进行吸附隔离处理,避免重金属离子扩散;可有效加强矿物掺合料的火山灰反应活性,可有效加强矿物掺合料的碳酸化处理效果,进而有效提高混凝土抗压强度和结构强度。
[0087]
本发明中在早强复合型矿渣掺合料中的膨润土添加到矿渣掺合料中,可有效加强对钢渣粉和矿渣粉中的重金属离子进行吸附隔离处理,可有效避免重金属离子在混凝土中持续扩散,进而保证混凝土的稳定性和结构强度;膨润土在碱性环境下通过十二烷基磺酸钠进行表面改性处理,可进一步加强膨润土对重金属离子的吸附处理效果;沸石经过300℃左右高温灼烧处理后,得到热活化改性处理的沸石添加到矿渣掺合料中,可有效加强对混凝土中重金属离子的吸附处理效果,进一步降低重金属离子在混凝土中的扩散性能,进一步提高混凝土的稳定性和结构强度;沸石在氢氧化钠水溶液中进行水热处理,可实现对沸石的水热钠改性处理的沸石,添加到矿渣掺合料中,可进一步加强对混凝土中重金属离子的吸附处理效果,进一步降低重金属离子在混凝土中的扩散性能,进一步提高混凝土的稳定性和结构强度;在800℃对沸石进行煅烧预处理,然后将煅烧预处理后的沸石和矿渣粉、钢渣粉在水中进行水化处理,然后通入二氧化碳对矿渣粉和钢渣粉进行碳酸化处理,高温预处理可以破坏沸石的四面体结构,增加沸石内部活性二氧化硅含量,从而改善沸石的前期火山灰活性,降低沸石自身孔隙率,在高温预处理的沸石作用下,可有效加强对矿渣粉和钢渣粉的碳酸化处理效果,可有效降低矿渣粉和钢渣粉的孔隙率,进而提高矿渣粉和钢渣粉的使用效果,混凝土结构强度更佳;在步骤二中,将膨润土、十二烷基磺酸钠和氢氧化钠加入到水中,进行水浴超声处理后,过滤洗涤,可有效加强对膨润土的改性处理效果;在步骤三中,将沸石、氢氧化钠加入到水中,进行水浴处理,过滤洗涤,可有效加强钠离子与沸石的接触改性处理效果;在步骤四中,对沸石在不同温度下进行灼烧或煅烧处理,可得到不同温度改性处理的沸石;在步骤五中,将改性膨润土、改性沸石a、改性沸石b和改性沸石c进行共混,得到补充剂;在步骤六中,将矿渣粉和钢渣粉进行粉磨处理,可有效缩小矿渣粉和钢渣粉的粒径,同时加强矿渣粉和钢渣粉的共混效果;在步骤七中,将补充剂和混合料d在水中进行浸泡搅拌预水化处理,然后加热保温通入二氧化碳,可有效加强对矿渣粉和钢渣粉碳酸化处理效果;在步骤八中,将混合料e和早强剂进行共混,得到早强复合型矿渣掺合料。
[0088]
最后应说明的是:以上所述仅为本发明的优选实施例而已,并不用于限制本发明,尽管参照前述实施例对本发明进行了详细的说明,对于本领域的技术人员来说,其依然可以对前述各实施例所记载的技术方案进行修改,或者对其中部分技术特征进行等同替换。凡在本发明的精神和原则之内,所作的任何修改、等同替换、改进等,均应包含在本发明的保护范围之内。