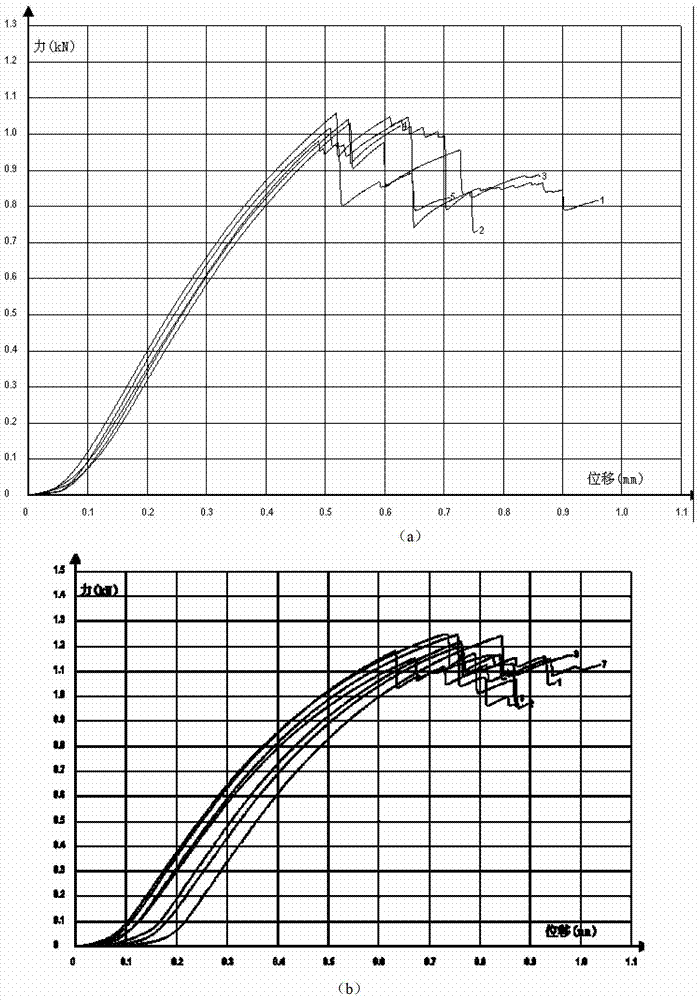
本发明属于高性能复合材料技术领域,具体涉及以高性能聚酰亚胺纤维为增强体的新型环氧树脂复合材料及其制备方法。
背景技术:高性能纤维增强环氧树脂复合材料具有高的比强度和比刚度高、抗疲劳断裂性能好、耐腐蚀、可设计性强、结构尺寸稳定性好以及便于大面积整体成型的优点,广泛应用在航天航空、电子电力、压力容器、建筑补强、运动器材等领域。其中作为基体材料环氧树脂是优良的热固性树脂,收缩率低,尺寸稳定性好,而且体系选择范围宽,具有良好的力学性能,电绝缘性能,粘合性能和耐化学腐蚀性能。常用的增强纤维包括碳纤维和高性能有机纤维,其中高性能有机纤维主要有超高强度聚乙烯纤维(UHMPE)、芳纶纤维(PPTA)和聚对苯撑苯并双噁唑纤维(PBO)。这三种高性能有机纤维均具有低密度,高强高模的优点。但也存在不足,UHMWPE纤维主要不足是熔点低(约130℃)、易蠕变、表面惰性与热固性树脂粘结性差。芳纶纤维耐水性较差,在湿环境中,会吸收一些水分(吸湿率可达7%),水分的存在使纤维结构变得松散,环境中的水通常是从复合材料外表面经界面通道侵入材料,从而加速复合材料的失效,且芳纶纤维耐紫外辐照性能差,从而限制了芳纶纤维增强复合材料的耐候性和在强辐照环境中的使用。PBO纤维表面活性低且光滑,与树脂粘结性能差,同时也存在耐紫外性能差的问题,在存放和使用过程中,复合材料性能下降较快。随着航空航天和国防军工科技的高速发展,对增强体有机纤维的要求更高,高性能聚酰亚胺纤维的研发成为高性能有机纤维的另一个重要研究方向。聚酰亚胺纤维具有优异的耐高、低温性能、高强度、高模量、耐辐射、高抗蠕变性、高尺寸稳定性、低热膨胀系数、高电绝缘性、低介电常数与介电损耗、耐腐蚀等优点,同时还具有真空挥发份低、挥发可凝物少等空间材料的特点。与碳纤维相比,聚酰亚胺纤维具有较低的密度和良好的电绝缘性能;与UHMPE相比,聚酰亚胺纤维具有显著优于它的耐热性、尺寸稳定性和表面活性;与芳纶纤维相比,聚酰亚胺纤维具有更好的耐高温性能、较低的吸水率和优异的耐辐照性能。与PBO纤维相比,聚酰亚胺纤维具有较好的表面活性,从而能够更好地与基体树脂粘结,以及优异的耐紫外及辐照等性能。因此,使用聚酰亚胺纤维作为增强体,既能够满足复合材料的基本力学和热学性能,还能够满足某些特殊环境下的使用要求,对高性能复合材料的全面发展具有重要的推动作用。
技术实现要素:本发明的目的是提供一种聚酰亚胺纤维增强环氧树脂的新型高性能复合材料,这种材料力学性能优越,界面粘结性能优良。本发明的另一目的是为聚酰亚胺纤维选配合适的环氧树脂体系。本发明的另一目的是提供上述性能优越的聚酰亚胺纤维增强环氧树脂复合材料的制备方法。为达到本发明的目的,本发明人根据复合材料获得良好的界面性能的条件,即树脂基体充分浸润纤维,树脂和纤维之间的极性相互匹配,为此选用共聚型聚酰亚胺纤维为增强体,共聚型聚酰亚胺纤维为含有含芳杂环结构的二胺的共聚型聚酰亚胺纤维,这样的聚酰亚胺纤维同时要求自身力学性能优越,拉伸强度大于2.0GPa,初始模量大于80GPa,而且由于含芳杂环的加入,表面能增大,表面极性增大,与环氧树脂的粘合能力增强。根据共聚型聚酰亚胺纤维的特点,通过环氧树脂、固化剂、稀释剂的选择和比例调配,所选配的环氧树脂体系具有与聚酰亚胺纤维匹配的表面张力及其极性分量,以及较低的粘度,适合模压成型、拉挤以及湿法缠绕成型。本发明的以高性能聚酰亚胺纤维为增强体的环氧树脂复合材料的制备步骤包括如下:(1)选取共聚型高性能聚酰亚胺纤维为增强体,该共聚型高性能聚酰亚胺纤维合成时所用的二胺中有含芳杂环结构的二胺,共聚型高性能聚酰亚胺纤维的形态可以是连续长纤维,纤维织物等。(2)选取环氧树脂作为基体材料,合理选择固化剂和活性稀释剂,其中环氧树脂选自双酚A型环氧树脂(DGEBA)、多官能基缩水甘油胺树脂(TGDDM)、脂肪族缩水甘油酯类环氧树脂(DGEAC);固化剂为芳香胺类和咪唑类共用,其中芳香胺类优选自二氨基二苯基砜(DDS),二氨基二苯基甲烷(DDM)、混合液态固化剂二乙基甲苯二胺(DETDA)中的一种或几种,咪唑类优选自咪唑、2-乙基-4-甲基咪唑(2,4-EMI)中的一种或两种;活性稀释剂选用苯基缩水甘油醚(PGE)、聚乙二醇二缩水甘油醚(PEGGE)、正丁基缩水甘油醚(BGE)、丁二醇二缩水甘油醚(BDGE),;环氧树脂可以是任意一种或者两种或者三种混合,稀释剂选用其中的任意一种或者两种。环氧树脂质量份数为100份,稀释剂的质量份数为10~30份芳香胺类固化剂的用量为固化剂中胺基中活泼氢的比例占环氧树脂和活性稀释剂中环氧官能团摩尔含量的75%~100%,咪唑类固化剂的质量份数为0.5-1.5份,配置树脂胶液时,基体材料、固化剂和稀释剂各组分在40℃~120℃下用机械搅拌混合均匀;(3)将步骤(2)配置好的树脂胶液温度在40℃~80℃时,将共聚型高性能聚酰亚胺浸胶,纤维连续长纤维浸胶后缠绕在块状模具上,或者将聚酰亚胺纤维织物直接浸胶,将浸胶且缠绕好的的纤维或者直接浸胶的纤维织物在室温~50℃下抽真空10~60min,放入模具中,在烘箱中固化加热,固化程序为80℃~110℃下保温1h~2h,120℃~160℃下保温1h~4h,170℃~200℃保温1h~4h。纤维在复合材料中所占的体积分数为30%-85%。本发明中共聚型高性能聚酰亚胺纤维为含有芳杂环结构的二胺,且拉伸强度大于2.0GPa,初始模量大于80GPa的共聚型聚酰亚胺纤维均能实现本发明的效果,其制备方法可按现有的技术方法,该材料合成时所用的二胺中有含芳杂环结构的二胺(如:2-(4-氨基)-6-氨基-4(3H)喹唑啉(Q),2-(4-氨基)-5-氨基苯并咪唑(BIA)等)即可;如按照CN102345177A制备等或其他方法均可。本发明只要含有芳杂环结构的二胺增强体的复合材料都比常规不含有芳杂环结构的二胺增强体的复合材料性能要好。所选用聚酰亚胺纤维中芳杂环二胺所占共聚时所用二胺总胺量的摩尔百分数为5%至90%,其中较优比为20%至65%。与现有技术相比,本发明具有以下的目的及效果:(1)本发明利用聚酰亚胺纤维的高强高模、耐高低温、耐紫外、耐辐照、低的吸水率和高的尺寸稳定性的特点,提供了一种高性能聚酰亚胺纤维增强环氧树脂的新材料,这种新型复合材料具有优异的综合力学性能和界面粘合强度。(2)本发明选用的高性能聚酰亚胺纤维和现有的各品种的芳纶纤维相比,具有较高的表面能和表面能极性成分,容易被环氧树脂体系浸润,且与环氧树脂相互作用力大,制备的复合材料具有强的界面结合强度。(3)本发明提供的环氧树脂配方表面张力和极性与共聚型纤维匹配,且具有良好的粘合能力和优异的力学性能。(4)本发明提供的制备复合材料的工艺简单、易行,可操作性强。在环氧树脂初始固化温度以下抽真空除去树脂间以及树脂与纤维间的气泡,确保了树脂和纤维的充分浸润。制得的聚酰亚胺纤维增强环氧树脂复合材料耐热性好,且具有良好的弯曲强度和层间剪切强度。本发明新材料的基本性能如下:因此,发明的新材料在航天航空结构材料,风电叶片,压力容器,汽车轻量化,建筑补强等领域有着广泛的应用前景。附图说明图1为本发明实施例中所用聚酰亚胺纤维的红外图。其中图1(a)为聚合时所用二胺单体中含2-(4-氨基)-6-氨基-4(3H)喹唑啉(Q)的共聚型聚酰亚胺纤维(PI-Q),图1(b)为聚合时所用二胺单体中含2-(4-氨基)-5-氨基苯并咪唑(BIA)的共聚型聚酰亚胺纤维(PI-BIA),图1(c)为PMDA-ODA均聚型聚酰亚胺纤维(PI)。图1中1776-1774cm-1,1716-1720cm-1处为聚酰亚胺环上C=O伸缩振动峰,1353-1375cm-1为酰亚胺环中C-N的伸缩振动峰,724-737cm-1处为酰亚胺环的变形振动峰。图1(a)在3474cm-1处为PI-Q中喹唑啉N-H的伸缩振动峰,图1(b)在3432cm-1处为PI-BIA中咪唑N-H的伸缩振动峰。图2为本发明提供的共聚型聚酰亚胺纤维增强环氧树脂复合材料的层间剪切测试的位移-力典型图。其中图2(a)为实施例3中制备的复合材料的位移-力图,其中5条曲线对应为实施案例3中制备的复合材料裁剪出的5个样条的曲线。图2(b)为实施例5制备的复合材料的位移-力图,其中7条曲线对应为实施案例5中制备的复合材料裁剪出的7个样条的曲线。聚酰亚胺纤维增强复合材料在抗层间剪切方面,在层间破坏后承受的载荷不会像碳纤维增强环氧树脂复合材料一样立刻大幅度下降,还能维持在较大的载荷。图3为本发明提供的共聚型聚酰亚胺纤维增强环氧树脂复合材料的扫描电子显微镜测试典型图。其中图3(a)为实施例4中复合材料剖面图,图3(b)为实施例4中层间剪切测试后继续剪切破坏的层间界面破坏图。从图3(a)中可以看出树脂包裹着纤维,纤维和树脂之间充分浸润。从图3(b)中可以看出界面破坏没有发生在界面而是纤维表层,纤维和树脂之间具有强的界面粘结强度,具体实施方式为了更清楚地说明本发明实施案例或现有技术中的技术方案和特点,下面结合具体实施例对本发明作进一步阐述,显然,所描述的实施例仅仅是本发明的一部分实施例,而不是全部的实施例。基于本发明的实施例,本领域普通人员没有付出创造性劳动前提下所获得的所有实施案例都属于本发明保护的范围。以下实施例的环氧树脂选自双酚A型环氧树脂(DGEBA,如牌号E-44,E-51等)、多官能基缩水甘油胺树脂(TGDDM,牌号AG80等)、脂肪族缩水甘油酯类环氧树脂(DGEAC,牌号TDE-85等),以下实施例所得产品中纤维体积分数50%±5%,可通过挤压浸胶后的纤维来控制最终产品中纤维体积分数,以下实施例中的聚酰亚胺纤维可参阅CN102345177A或进行简单的替换。其中以下实施案例1,PI-Q,其中Q占所用二胺摩尔总量的50%,纤维拉伸强度2.5GPa,模量100GPa。实施案例2,PI-BIA,其中BIA占所用二胺摩尔总量的20%,纤维拉伸强度2.6GPA,模量110GPa.实施案例3,PI-BIA,其中BIA占所用二胺摩尔总量的50%,纤维拉伸强度3.0GPA,模量120GPa.实施案例4,PI-Q,其中Q占所用二胺摩尔总量的25%,纤维拉伸强度2.8GPa,模量115GPa。实施案例5,PI-BIA,其中BIA占所用二胺摩尔总量的60%,纤维拉伸强度3.2GPA,模量120GPa.实施例1:在100℃下将35g二氨基二苯基砜(DDS)溶解在80g双酚A型环氧树脂(E-51)中,再加入20g聚乙二醇二缩水甘油醚和1g咪唑混合均匀。然后进行聚酰亚胺纤维(PI-Q)连续浸胶和缠绕,浸胶时树脂胶液的温度控制在40℃,缠绕好的已经浸胶的纤维在50℃下抽真空20min。然后装入凹凸模具中,110℃预固化2h,150℃固化2h,200℃后固化3h。复合材料玻璃化转变温度180℃,层间剪切强度60MPa,弯曲强度650MPa。实施例2:在50℃将40g二氨基二苯基甲烷(DDM),60g多官能基缩水甘油胺树脂(AG80),30g脂肪族缩水甘油酯类环氧树脂(TDE-85),10g正丁基缩水甘油醚(BGE),然后进行聚酰亚胺纤维(PI-BIA)连续浸胶和缠绕,浸胶时树脂胶液的温度控制在50℃,缠绕好的已经浸胶的纤维在50℃下抽真空20min。然后装入凹凸模具中,80℃预固化2h,150℃固化4h,180℃后固化2h。复合材料玻璃化转变温度170℃,层间剪切强度63MPa,弯曲强度690MPa。实施例3:在50℃将35g二乙基甲苯二胺(DETDA),80g脂肪族缩水甘油酯类环氧树脂(TDE-85),20g丁二醇二缩水甘油醚(BDGE),1g2-乙基-4-甲基咪唑(2,4-EMI)机械搅拌30min。然后进行聚酰亚胺纤维(PI-BIA)连续浸胶和缠绕,浸胶时树脂胶液的温度控制在60℃,缠绕好的浸胶纤维在室温下抽真空40min。浸胶纤维装入凹凸模具中,110℃预固化2h,150℃固化3h,200℃后固化2h。复合材料玻璃化转变温度165℃,层间剪切强度65MPa,弯曲强度680MPa。实施例4:在50℃将12g二氨基二苯基甲烷(DDM),25g二乙基甲苯二胺(DETDA),80g脂肪族缩水甘油酯类环氧树脂(TDE-85),20g聚乙二醇二缩水甘油醚,1g2-乙基-4-甲基咪唑(2,4-EMI)机械搅拌30min。然后将剪裁好的聚酰亚胺纤维(PI-Q)织物浸胶,叠层10层(固化后厚度约2mm),室温下抽真空30min。在热压机上施加1MPa的压力,110℃预固化2h,150℃固化3h,180℃后固化2h。复合材料玻璃化转变温度168℃,层间剪切强度68MPa,弯曲强度700MPa。实施例5:在50℃将32g二乙基甲苯二胺(DETDA),40g多官能基缩水甘油胺树脂(AG80),50g脂肪族缩水甘油酯类环氧树脂(TDE-85),10g丁二醇二缩水甘油醚(BDGE),1g2-乙基-4-甲基咪唑(2,4-EMI)机械搅拌30min。然后将剪裁好的聚酰亚胺纤维(PI-BIA)织物浸胶,叠层10层(固化后厚度约2mm),室温下抽真空30min。在热压机上施加2MPa的压力,110℃预固化2h,150℃固化3h,190℃后固化3h。复合材料玻璃化转变温度172℃,层间剪切强度70MPa,弯曲强度710MPa。对比例:在50℃将35g二乙基甲苯二胺(DETDA),80g脂肪族缩水甘油酯类环氧树脂(TDE-85),20g丁二醇二缩水甘油醚(BDGE),1g2-乙基-4-甲基咪唑(2,4-EMI)机械搅拌30min。然后进行PMDA-ODA均聚型聚酰亚胺纤维(PI)连续浸胶和缠绕,浸胶时树脂胶液的温度控制在50℃,缠绕好的浸胶纤维在室温下抽真空40min。浸胶纤维装入凹凸模具中,110℃预固化2h,150℃固化3h,200℃后固化2h。复合材料玻璃化转变温度165℃,层间剪切强度40MPa,弯曲强度380MPa。