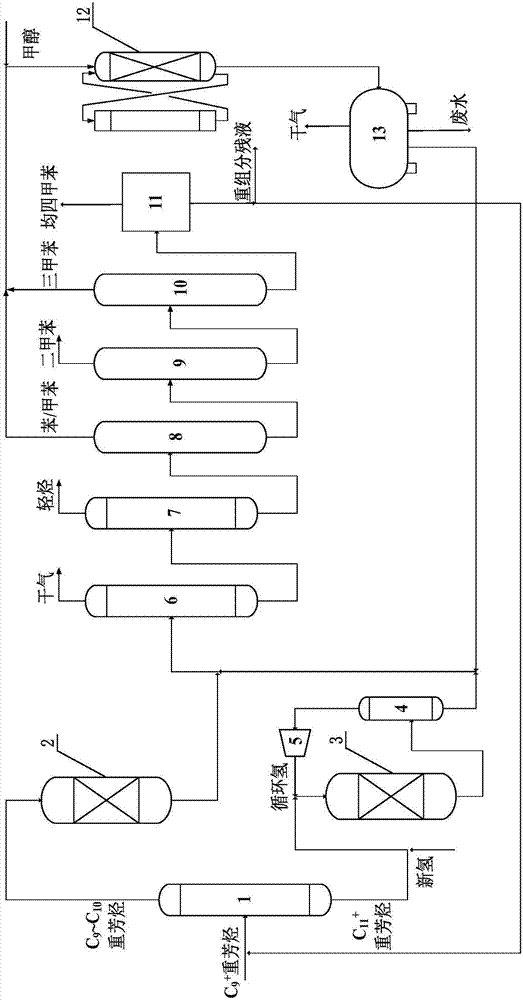
本发明属于芳烃化工生产
技术领域:
,具体涉及一种由c9+重芳烃制备二甲苯联产均四甲苯的方法。
背景技术:
:二甲苯是重要的有机化工原料,二甲苯中用量最大的是对二甲苯(px),主要用于生产聚酯,在合成树脂、塑料、医药、农药等领域也有着广泛的应用。近年来,国内聚酯产业高速发展,带动了对上游原料px的需求,我国px对外依存度逐年提高,需要寻求新的增产途径。均四甲苯是一种重要的有机化工原料,主要用于生产聚酰亚胺绝缘薄膜。聚酰亚胺在耐热性工程塑料中占有极为重要的位置,是目前热塑性工程塑料中耐热性最好的品种之一,广泛应用于航空、航天、机电及电子等领域。催化重整在生产btx的同时,会副产一部分c9+重芳烃,c9+重芳烃约占重整加工产能的20%。据统计,目前国内重整产能为12000万吨/年,c9+重芳烃产量约为2500万吨/年。未来随着芳烃联合装置产能的提高,副产的c9+重芳烃会越来越多,迫切需要寻求高值化利用途径。c9+重芳烃芳潜较高,是制备btx的优质原料,若通过催化裂解方式将乙基苯、丙基苯等c2以上烷基芳烃进行选择性裂解,可得到高纯度btx。btx分离后,可将得到的苯、甲苯通过与甲醇烷基化转化为二甲苯。另外,裂解后的c9芳烃中几乎全为三甲苯,且以偏三甲苯为主,经过偏三甲苯-甲醇烷基化后可转化为高附加值均四甲苯。cn102746091a公布了一种重芳烃生产btx芳烃和三甲苯的方法,采用全馏分c9+重芳烃临氢裂解工艺,将c9+重芳烃中乙基苯、丙基苯等芳烃脱除,然后进行分离得到btx、均三甲苯和偏三甲苯。该方法可以降低三甲苯分离难度,但由于采用全馏分临氢裂解方式,存在氢耗较高、干气产率高的问题。cn103772121a公开了一种c9及以上重质芳烃组分裂解多产三甲苯的方法,通过采用将c9+重芳烃原料在催化剂存在、临氢条件下,重质芳烃加氢脱烷基并与轻质芳烃发生烷基转移反应,并富集c9芳烃中的三甲苯,液相产物根据不同的沸点分别分离出轻烃、btx、均三甲苯和偏三甲苯、碳九和连三甲苯馏分,其中碳九和连三甲苯可返回作为进料继续处理。该方法采用临氢裂解方式,同样存在氢耗高、干气产率高的问题。另外,由于采用具有烷基转移功能的催化剂,相当大部分c9芳烃中的高附加值三甲苯单体与苯、甲苯发生烷基转移,降低了三甲苯单体的收率。cn1045557428a公布了一种芳烃烷基转移与烷基化增产二甲苯的方法,该方法通过采用一种烷基转移和烷基化增产二甲苯的方法,以甲苯、c9+重芳烃及烷基化试剂为原料,在临氢条件下通过至少一个反应区发生烷基转移与烷基化反应,生成富含二甲苯的流出物,其中甲苯与c9+重芳烃的重量之比为100:0~20:80,甲苯与烷基化试剂摩尔比为20:1~1:10。该方法采用烷基转移和甲苯-甲醇烷基化组合工艺可达到增产对二甲苯的目的,但仍采用临氢操作模式,且需要外加大量的甲苯作为烷基转移受体,干气产量高、原料转化率低、甲苯循环量大。另外,在烷基化反应单元,由于烷基转移后产物未进行分离直接进入烷基化单元,导致一部分生成的二甲苯也会发生烷基化生成三甲苯、四甲苯等更重组分。综上所述,现有c9+重芳烃加工技术普遍存在氢耗高、干气产量大、产物附加值不高等问题。技术实现要素:本发明主要解决目前c9+重芳烃加工技术氢耗高、干气产量大、产物附加值低的问题,采用催化裂解、苯/甲苯/三甲苯烷基化组合工艺制二甲苯及均四甲苯,具有氢耗低、干气收率低、目的产物收率高、产物附加值高的优点。本发明解决上述技术问题,采用以下技术方案:一种由c9+重芳烃制备二甲苯联产均四甲苯的方法,该方法包括如下步骤:(1)原料c9+重芳烃经过原料脱重塔分离后得到c9~c10重芳烃和c11+重芳烃;(2)所述c9~c10重芳烃进入催化裂解反应器内,在反应温度为400~600℃,压力为0.1~1.5mpa,质量空速为0.5~2.5h-1的条件下转化为以btx和三甲苯为主的一段混合烃类产物;(3)所述c11+重芳烃与氢气混合后进入加氢裂化反应器,在反应温度为350~480℃,压力为1.0~5.0mpa,质量空速为0.5~3.0h-1,氢烃体积比为200:1~1000:1的条件下转化为二段混合烃类产物;(4)所述二段混合烃类产物经气液分离罐分离后得到富氢气体和液态烃,富氢气体通过循环压缩机返回加氢裂化反应器,液态烃与所述一段混合烃类产物经脱乙烷塔、脱轻烃塔、脱甲苯塔、脱二甲苯塔、脱三甲苯塔分离后得到干气、轻烃、苯/甲苯、二甲苯、三甲苯、c10+重芳烃;(5)所述干气、轻烃、二甲苯作为产品输出系统,所述苯/甲苯、三甲苯与一定量的甲醇共同进入烷基化反应器内,在反应温度为350~500℃,压力为0.1~2.0mpa,原料质量空速为1.0~4.0h-1,(苯/甲苯、三甲苯)与甲醇摩尔比为1:1~5:1的条件下进行烷基化反应,得到富含二甲苯和均四甲苯的三段混合烃类产物;(6)所述三段混合烃类产物经三相分离器分离出干气和废水后进入步骤(4)所述的脱乙烷塔进一步分离;(7)步骤(4)分离得到的c10+重芳烃经过均四甲苯结晶分离系统分离后得到均四甲苯和重组分残液,均四甲苯和部分重组分残液作为产品输出系统,其余的重组分残液返回步骤(3)所述的加氢裂化反应器。在上述技术方案中,步骤(2)中催化裂解反应器为固定床反应器,催化裂解催化剂为zno改性的小晶粒zsm-5分子筛催化剂;步骤(3)中加氢裂化反应器为固定床反应器,催化剂为nio改性的纳米y型分子筛催化剂;步骤(5)所述的烷基化反应器为移动床反应器,催化剂为水热处理改性的纳米zsm-5分子筛催化剂。本发明方法还可进一步优选,包括如下步骤:(1)原料c9+重芳烃经过原料脱重塔分离后得到c9~c10重芳烃和c11+重芳烃;(2)所述c9~c10重芳烃进入装有zno改性的小晶粒zsm-5分子筛催化剂的固定床催化裂解反应器内,在反应温度为450~550℃,压力为0.1~0.5mpa,质量空速为0.5~1.5h-1的条件下转化为以btx和三甲苯为主的一段混合烃类产物;(3)所述c11+重芳烃与氢气混合后进入装有nio改性的纳米y型分子筛催化剂的加氢裂化反应器,在反应温度为360~420℃,压力为2.0~4.0mpa,质量空速为1.0~2.0h-1,氢烃体积比为400:1~800:1的条件下转化为二段混合烃类产物;(4)所述二段混合烃类产物经气液分离罐分离后得到富氢气体和液态烃,富氢气体通过循环压缩机返回加氢裂化反应器,液态烃与所述一段混合烃类产物经脱乙烷塔、脱轻烃塔、脱甲苯塔、脱二甲苯塔、脱三甲苯塔分离后得到干气、轻烃、苯/甲苯、二甲苯、三甲苯、c10+重芳烃;(5)所述干气、轻烃、二甲苯作为产品输出系统,所述苯/甲苯、三甲苯与一定量的甲醇共同进入装有水热处理改性的纳米zsm-5分子筛催化剂的移动床烷基化反应器内,在反应温度为360~460℃,压力为0.1~1.0mpa,原料质量空速为1.0~2.0h-1,(苯/甲苯、三甲苯)与甲醇摩尔比为1:1~3:1的条件下进行烷基化反应,得到富含二甲苯和均四甲苯的三段混合烃类产物;(6)所述三段混合烃类产物经三相分离器分离出干气和废水后进入步骤(4)所述的脱乙烷塔进一步分离;(7)步骤(4)分离得到的c10+重芳烃经过均四甲苯结晶分离系统分离后得到均四甲苯和重组分残液,均四甲苯和部分重组分残液作为产品输出系统,其余的重组分残液返回步骤(3)所述的加氢裂化反应器。与现有技术相比,本发明方法具有以下优势:1)将c9+重芳烃原料进行分离后分别处理,c9~c10相对较轻的芳烃采用非临氢裂解工艺,乙基苯、丙基苯等c2以上烷基芳烃裂解产生的乙烯、丙烯可以进一步发生芳构化反应生成btx,干气收率较低。c11+重芳烃采用加氢裂化方式进行处理,可增加原料转化率。另外,由于仅将c11+重芳烃采用加氢方式,总体氢耗较低;2)裂解产生的苯/甲苯、三甲苯共同进入烷基化反应器,在同一反应器里完成苯/甲苯-甲醇烷基化制二甲苯,偏三甲苯-甲醇烷基化制均四甲苯两个反应,从而得到高附加值的二甲苯和均四甲苯;3)烷基化反应采用移动床反应器,催化剂可保持较高的反应活性,原料转化率、甲醇甲基利用率较高。附图说明图1为本发明由c9+重芳烃制备二甲苯联产均四甲苯的方法工艺流程示意图。图中:1-原料脱重塔;2-催化裂解反应器;3-加氢裂化反应器;4-气液分离罐;5-循环压缩机;6-脱乙烷塔;7-脱轻烃塔;8-脱甲苯塔;9-脱二甲苯塔;10-脱三甲苯塔;11-均四甲苯结晶分离系统;12-烷基化反应器;13-三相分离器。具体实施方式为了更清楚地说明本发明由c9+重芳烃制备二甲苯联产均四甲苯的方法,下面结合附图及具体实施例对本发明方法作进一步描述。如图1所示,c9+重芳烃原料先进入原料脱重塔1分为c9~c10重芳烃和c11+重芳烃,其中c9~c10重芳烃进入固定床催化裂解反应器2内转化为一段混合烃类产物,c11+重芳烃与氢气进入加氢裂化反应器3内转化为二段混合烃类产物。二段混合烃类产物经气液分离罐4分离后得到富氢气体和液态烃产物,富氢气体经过循环压缩机5返回加氢裂化反应器3,液态烃产物与一段混合烃类产物混合后依次经过脱乙烷塔6、脱轻烃塔7、脱甲苯塔8、脱二甲苯塔9、脱三甲苯塔10分离后得到干气、轻烃、苯/甲苯,二甲苯,三甲苯、c10+重芳烃。干气、轻烃、二甲苯作为产品排出系统,苯/甲苯、三甲苯与一定量甲醇进入烷基化反应器12反应得到富含二甲苯和均四甲苯的三段混合烃类产物,产物经三相分离器13分离出干气、废水后返回脱乙烷塔6。c10+重组分经均四甲苯结晶分离系统11后得到均四甲苯和重组分残液,均四甲苯和部分重组分残液作为产品输出系统,其余的重组分残液返回加氢裂化反应器3。实施例1以某炼厂的c9+重芳烃为原料,将原料进行切割,切除c11+重组分后进行非临氢催化裂解反应,催化剂采用负载3.0wt%zno的小晶粒zsm-5分子筛,反应温度为480℃,压力为0.3mpa,质量空速为1.0h-1。切割前后c9+重芳烃原料及催化裂解反应的液相产物组成如表1所示。实施例2催化裂解反应装填1wt%zno改性的小晶粒zsm-5分子筛催化剂,反应条件为:反应温度为450℃,压力为0.1mpa,质量空速为0.5h-1。加氢裂化反应器内装填4.0wt%nio改性的纳米y型分子筛催化剂反应条件为:反应温度360℃,压力2.5mpa,原料质量空速1.5h-1,氢烃体积比为500:1。烷基化反应器内装填450℃水热处理改性的纳米zsm-5分子筛催化剂,反应条件为:应温度为380℃,压力为0.3mpa,原料质量空速为1.0h-1,(苯/甲苯、三甲苯)与甲醇摩尔比为1:1的条件下进行烷基化反应。通过上述工艺,各产物收率见表2。实施例3催化裂解反应装填3wt%zno改性的小晶粒zsm-5分子筛催化剂,反应条件为:反应温度为500℃,压力为0.3mpa,质量空速为1.0h-1。加氢裂化反应器内装填8.0wt%nio改性的纳米y型分子筛催化剂反应条件为:反应温度380℃,压力3.5mpa,原料质量空速2.0h-1,氢烃体积比为600:1。烷基化反应器内装填500℃水热处理改性的纳米zsm-5分子筛催化剂,反应条件为:应温度为420℃,压力为0.6mpa,原料质量空速为1.5h-1,(苯/甲苯、三甲苯)与甲醇摩尔比为2:1的条件下进行烷基化反应。通过上述工艺,各产物收率见表2。实施例4催化裂解反应装填5.0wt%zno改性的小晶粒zsm-5分子筛催化剂,反应条件为:反应温度为550℃,压力为0.5mpa,质量空速为1.5h-1。加氢裂化反应器内装填12.0wt%nio改性的纳米y型分子筛催化剂反应条件为:反应温度420℃,压力4.0mpa,原料质量空速2.0h-1,氢烃体积比为800:1。烷基化反应器内装填550℃水热处理改性的纳米zsm-5分子筛催化剂,反应条件为:应温度为460℃,压力为1.0mpa,原料质量空速为2.0h-1,(苯/甲苯、三甲苯)与甲醇摩尔比为3:1的条件下进行烷基化反应。通过上述工艺,各产物收率见表2。实施例5催化裂解反应装填3.0wt%zno改性的小晶粒zsm-5分子筛催化剂,反应条件为:反应温度为500℃,压力为0.1mpa,质量空速为1.0h-1。加氢裂化反应器内装填8.0wt%nio改性的纳米y型分子筛催化剂反应条件为:反应温度400℃,压力3.5mpa,原料质量空速1.5h-1,氢烃体积比为600:1。烷基化反应器内装填500℃水热处理改性的纳米zsm-5分子筛催化剂,反应条件为:应温度为420℃,压力为0.5mpa,原料质量空速为1.0h-1,(苯/甲苯、三甲苯)与甲醇摩尔比为1:1的条件下进行烷基化反应。通过上述工艺,各产物收率见表2。实施例6催化裂解反应装填5.0wt%zno改性的小晶粒zsm-5分子筛催化剂,反应条件为:反应温度为450℃,压力为0.3mpa,质量空速为1.5h-1。加氢裂化反应器内装填4.0wt%nio改性的纳米y型分子筛催化剂反应条件为:反应温度380℃,压力3.0mpa,原料质量空速1.0h-1,氢烃体积比为400:1。烷基化反应器内装填450℃水热处理改性的纳米zsm-5分子筛催化剂,反应条件为:应温度为400℃,压力为0.5mpa,原料质量空速为1.0h-1,(苯/甲苯、三甲苯)与甲醇摩尔比为2:1的条件下进行烷基化反应。通过上述工艺,各产物收率见表2。表1实施例1原料及液相产物组成由表1可知,切割后的c9+重芳烃经过催化裂解后,液相产物c9芳烃中几乎不含丙基苯和乙基苯,且主要以偏三甲苯为主,通过三甲苯-甲醇烷基化很容易得到高纯度均四甲苯。c8芳烃中几乎不含乙苯,利于c8单体芳烃的分离。表2实施例2~6反应结果产物收率/wt%实施例2实施例3实施例4实施例5实施例6二甲苯54.952.955.651.252.7均四甲苯22.124.225.126.324.2干气7.28.39.37.85.8轻烃7.56.75.18.99.1重组分残夜8.37.94.95.88.2注:当前第1页12