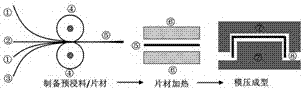
本发明属于材料领域,具体涉及一种热塑性纤维增强复合材料,该材料的制备方法,以及应用;还涉及以该材料为原材料制备箱包壳体的方法。
背景技术:
:复合材料是由两种或两种以上不同性质的材料,通过物理或化学的方法,在宏观(微观)上组成具有新性能的材料。各种材料在性能上互相取长补短,产生协同效应,使复合材料的综合性能优于原组成材料而满足各种不同的要求。与传统的金属材料相比,复合材料具有如下的优点:(1)高比强度、高比模量,可达到明显的减重效果;(2)可设计性强;(3)热膨胀系数低,尺寸稳定性好;(4)耐腐蚀;(5)耐疲劳。目前对于复合材料的应用,较为先进的是航空航天领域,但是所占比例较小;应用较为广泛的是民用领域:汽车领域,体育用品,户外用品等,截至目前复合材料在拉杆箱上的应用呈现不断增长的趋势和需求。现在市场上较为常见的复合材料拉杆箱均采用碳纤维增强树脂基复合材料,该拉杆箱是采用液体成型工艺中的真空辅助传递模塑(vari)制备,或者采用预浸料热压罐成型制备箱包壳体。相比传统的硬质箱并没有明显重量上的优势,而且由于其所采用的树脂为热固性环氧树脂,产品性脆,不耐冲击、撞击,且相对传统的吸塑成型工艺效率很低,材料和成型工艺成本高;其产品并不满足环境友好的要求,所制备的产品容易损坏且不具修复性,损坏后不可回收,造成了材料的浪费和环境污染。因此并不能很好的符合拉杆箱的发展理念,所以没有得到很好的推广和批量化生产。目前在航空以及民用领域广泛应用的为树脂基复合材料,其分为热固性树脂基复合材料和热塑性树脂基复合材料,所采用的基体为热固性和热塑性树脂两大类,较为常用的增强体为纤维织物。其最大的特点就是可以根据产品的需求对所采用的材料种类和铺层方案进行选择,从而在满足产品要求以及多样化的前提下降低成本。但是应用最为广泛的热固性树脂基复合材料存在性脆,不耐冲击,不具备再修复性,成本高且不可回收、环境污染等问题。这些都是热固性基体自带的不可避免的缺陷。对于热塑性树脂在复合材料中的应用,最主要的问题一方面是高性能热塑性树脂的成型温度高;另一方面是热塑性树脂与纤维织物结合的界面问题,比如市场上现存的碳纤维织物大多是适合于热固性树脂基体的上浆剂,该种上浆剂对于热塑性树脂并不适用且会起到增加缺陷降低性能的效果。关于复合材料在箱包中的应用,有以下文献做过披露:cn93108057.6公开了一种软硬箱结合的箱包复合材料。是由外层为纺织品面料内层为abs材料二者紧密地结合在一起的板材构成。这种新的箱包材料,可以采用缝纫的方法加工制成,生产成本低,投资少,同时又具有由abs材料制成的硬箱的优点高抗冲击强度、表面强度不易被利器割破、方便耐用的优点。尤其是花色品种可以随纺织品面料的多种多样变幻无穷,而且价格仅为abs箱包的一半,具有广阔的市场前景和良好的经济效益。以上文献中披露的复合材料所制得的产品,其缺点是:以纺织品面料为外层以abs材料为内层,两者接触部位很容易因为粘接不良造成开裂。主要承力仍然是abs材料,其力学性能以及耐冲击方面没有得到有效的提高,且表面纺织品面料不耐脏,难以打理,且不防水。cn1860015一种制备纤维复合构件用的纤维复合材料的制法,纤维复合材料由增强纤维,树脂和填料构成,其特征在于,填料由研磨的和/或切碎的增强纤维构成。以上文献中披露的材料和方法,其缺陷是:增强纤维不连续,制品表面不美观,且由于纤维的不连续,增强纤维的性能得不到充分的发挥,材料的力学性能以及冲击性能得不到充分的发挥,与连续纤维增强复合材料的力学性能以及冲击性能差距很大。因此,为了满足复合材料更好的在民用领域应用和进一步扩展,需要针对以上复合材料的缺陷,对其进行改进,设计一种性能更好的例如质量轻、韧性高、力学性能优良的复合材料,应用其制作的产品不仅质轻、韧性高且具有良好的防刮性能。技术实现要素:为了解决上述的技术问题,本发明提供了一种质量轻、韧性高、力学性能优良的复合材料,应用其制作的产品不仅质轻、韧性高且具有良好的防刮性能。并且可以根据产品需求将合适的衬里与复合材料预浸料/片材共同成型制备得到带有衬里的复合材料预浸料/片材。本发明还提供了一种上述复合材料的制备方法,通过该方法可在产品废弃后处理中实现对壳体材料的全部回收,实现零排放的环境友好化发展。本发明的热塑性纤维增强复合材料,主要包括热塑性纤维织物与热塑性树脂。热塑性纤维织物与热塑性树脂的重量比为:(0.4-2):1。热塑性纤维织物的材料为聚乙烯纤维、超高分子量聚乙烯纤维、聚丙烯纤维、芳纶纤维、abs纤维、聚苯乙烯纤维、聚酰胺纤维、聚酰亚胺纤维、聚苯硫醚纤维、聚醚醚酮、聚碳酸酯纤维、聚醚砜纤维及其混编纤维织物中的至少一种;热塑性树脂的材料包括聚乙烯、超高分子量聚乙烯、聚丙烯、abs、聚苯乙烯、聚酰胺、聚酰亚胺、聚苯硫醚、聚醚醚酮、聚碳酸酯、聚醚砜及其改性塑料中的至少一种。热塑性纤维织物包括平纹、斜纹、缎纹、针织、经编织物中的任一种;热塑性纤维织物为单种纤维的编织,或多种纤维的混合编织。热塑性纤维增强复合材料的制备方法,包括下述的步骤:(1)取原材料热塑性纤维织物和热塑性树脂,按照铺层设计进行叠放;(2)在高温高压下将热塑性树脂熔融浸润热塑性纤维织物;(3)冷却,得热塑性纤维增强预浸料/片材。热塑性纤维增强复合材料的制备方法,包括以下的步骤:步骤(1)中热塑性纤维织物与热塑性树脂交替叠放,热塑性纤维织物与热塑性树脂的重量比为0.4-2:1;步骤(2)中,高温高压条件为:熔融浸润的温度高于热塑性树脂的熔点,高压下的压力为单位面积5-10mpa;步骤(3)中,待模具冷却至50℃-70℃。将里布/内衬直接铺覆在步骤(1)中所铺放好的原料的表面,经高温高压成型粘接一体,得热塑性纤维增强预浸料/片材。上述的热塑性纤维增强复合材料在制备箱包、乐器盒、汽车内饰件、体育用品、无人机、船舶、轨道交通中的应用,也是本发明所要保护的范围。热塑性纤维增强复合材料用以制备箱包壳体,包括下述的步骤:(1)取原料热塑性纤维织物和热塑性树脂,交替叠放;(2)在高温高压下将热塑性树脂熔融浸润热塑性纤维织物;(3)冷却,得热塑性纤维增强预浸料/片材;(4)将(3)中的热塑性纤维增强预浸料/片材加热至100℃以上,且使片材软化至橡胶态,再采用常规模压成型工艺,得箱包壳体。现有的塑料箱包大多采用abs,pc或二者共混使用,材料比较单一,且相对容易老化;箱包笨重,在冲击时容易破裂。本发明采用了热塑性纤维增强塑料作为箱包壳体材质,与现有的纯塑料箱包相比其先进性表现为以下几个方面:采用了热塑性纤维进行增强塑料并制备成箱包壳体,可大幅提高箱包的冲击韧性,冲击强度可提高到传统塑料的5倍以上,大幅提高箱包材质的强度,材料强度可提高到现有箱包塑料材质的3倍以上,有效的减少箱包在使用过程中的损坏,提高箱包使用寿命采用了热塑性纤维进行增强塑料并制备成箱包壳体,由于材质的强度得到大幅提高,从而可以减小箱包壳体的厚度,可大幅降低箱包重量,使箱包更为轻便采用了热塑性纤维进行增强塑料并制备成箱包壳体,纤维的颜色,材质,编织方式种类很多,塑料的种类,颜色同样繁多,将纤维和塑料复合制备复合材料的样式将极为丰富,设计空间非常大,使箱包的样式极为丰富,现有的箱包衬里都是通过缝合的方式连接到壳体内部,本发明所采用的衬里为四面弹力布,并在制作复合材料预浸料/片材时直接附着在片材的表面,从而与箱包壳体紧密粘接为一体,不再需要缝合,减少后续的装配,重要的是使得箱包内部整洁美观。采用模压成型的示意图如图1所示。将塑料膜①、热塑性增强纤维织物②以及里布/内衬③按照设计铺层好,整体经过上下加热压辊④,制备得到热塑性纤维增强复合材料预浸料/片材⑤,热塑性纤维增强复合材料预浸料/片材⑤经过加热板⑥的加热后,在上下模压模具⑦的压力作用下成型,待冷却后即可制备得到热塑性纤维增强复合材料箱包壳体⑧。采用本发明所提供的热塑性纤维增强预浸料/片材用于制备箱包壳体,相对于传统的硬质箱体,可以大幅度提高箱包的强度和抗冲击性能,由于材质强度的大幅提高可减小壳体的厚度从而减轻箱包自身的重量,相对传统的硬质箱可减重40%左右,并大幅提高了箱包的抗冲击性,减少箱包在使用、托运过程中的损坏。与传统软箱相比,解决了软质箱包的不耐压和不防水性,皮革箱易刮花及破损且不易修补或者修补费用较高的缺点。此外,在制备热塑性纤维增强预浸料/片材过程中,可将里布/内衬通过塑料的熔融粘接与预浸料/片材形成整体,其减少了后续安装里布/内衬的程序,节省成本、简单美观。由于采用了热塑性纤维增强塑料,使得箱包具有质轻、防水、韧性好、强度高、耐冲击、防刮等优点,极大的减轻箱包自身重量,并有效防止箱包在使用或托运过程中的损坏。由于增强纤维和树脂基体均为热塑性材质,使得箱包壳体可以全部回收,绿色环保。附图说明图1为实施例2中的复合材料应用于箱包制作的工艺流程图;①塑料膜,②热塑性增强纤维织物,③里布/内衬,④加热压辊,⑤热塑性纤维增强复合材料预浸料/片材,⑥加热板,⑦模压模具,⑧热塑性纤维增强复合材料箱包壳体。具体实施方式下面结合附图和具体实施方式来对本发明作更进一步的说明,以便本领域的技术人员更了解本发明,但并不以此限制本发明。实施例1热塑性纤维增强复合材料的制备方法,包括以下的步骤:(1)取原料热塑性pp纤维织物和热塑性pp树脂膜,按照设计好的纤维体积含量,将热塑性pp纤维织物和热塑性pp树脂膜交叉叠放;(2)在高温高压下将热塑性树脂熔融浸润热塑性纤维织物:所采用的成型温度约为280℃,且高于热塑性树脂的熔点;成型采用的压力为单位面积5-10mpa;(3)冷却到55℃左右,得热塑性纤维增强预浸料/片材。对所得到的热塑性纤维增强预浸料的性能进行检测,得到以下的数据:采用复合材料的实验测试标准,制备好标准尺寸的样条,粘贴应变片,在力学试验机上进行拉伸测试,采集实验过程的载荷和应变,按照标准的计算公式计算得到强度、模量以及延伸率。采用摆锤冲击实验来测试复合材料的冲击强度。表1不同材质材料的性能材料模量(mpa)强度(mpa)延伸率(%)冲击强度(j/m)实施例1545140281238abs材料13203925231实施例2以热塑性纤维增强复合材料为原料制备拉杆箱的壳体,其具体的方法如下:以热塑性pp纤维织物和pp塑料膜为原材料,制备带有衬里的全热塑性复合材料拉杆箱壳体。具体步骤为:如附图1所示,将pp塑料薄膜①、pp纤维织物②以及里布/内衬③按照设计铺层好,整体经过上下加热压辊④,塑料薄膜熔融浸润纤维织物制备得到热塑性纤维增强复合材料预浸料/片材⑤,将热塑性纤维增强复合材料预浸料/片材⑤裁剪成需要的尺寸,并经过加热板⑥的加热软化后,在上下模压模具⑦的压力作用下成型,待冷却后即可制备得到pp纤维增强复合材料箱包壳体⑧。采用热塑性纤维增强复合材料制得拉杆箱。制得的pp复合材料性能与现有箱包abs材料性能如表2所示。对比可以发现pp复合材料的强度是abs材料的3.5倍,冲击强度是abs材料的5.5倍左右。表2现有箱包abs材料与pp复合材料性能当前第1页12