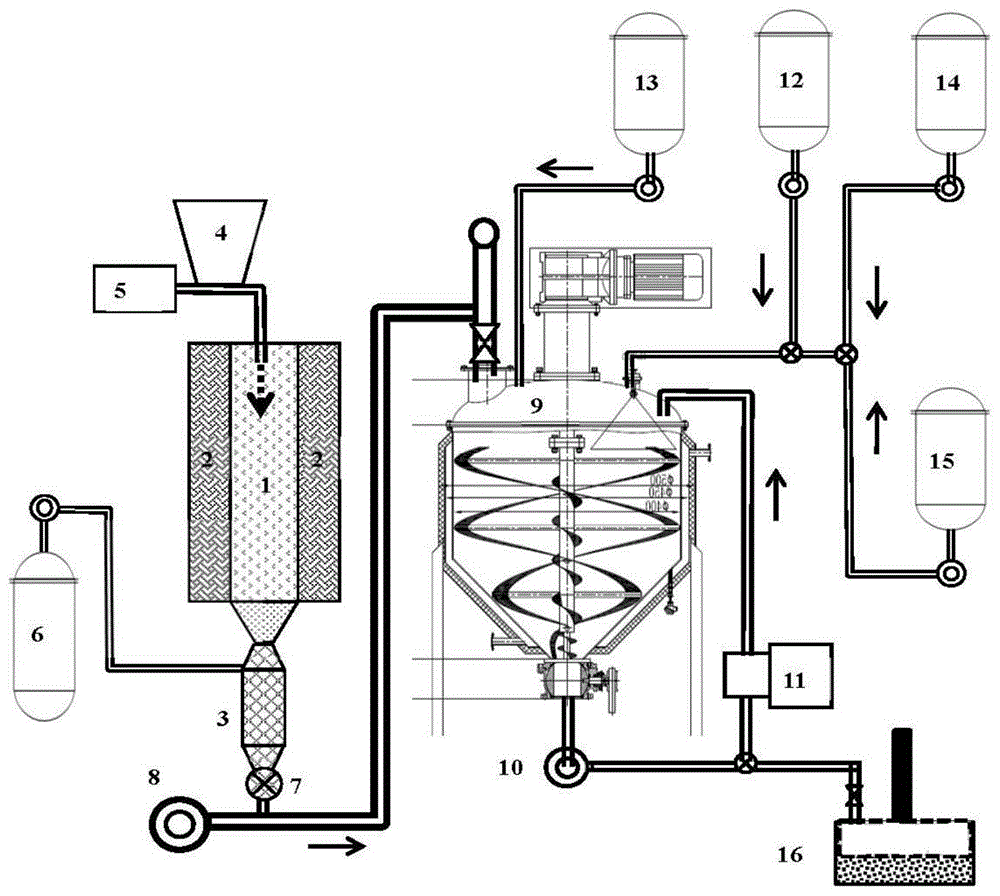
本发明涉及橡胶领域,尤其涉及一种石墨烯橡胶浓缩料及石墨烯橡胶的生产方法。
背景技术:
:天然橡胶是从热带特定植物中采集的白色胶乳经过乳液凝聚得到的,其主要成分是顺式聚异戊二烯,是分子量不同的各种聚异戊二烯分子的混合物,分子量很高。天然橡胶一般通过添加炭黑和白炭黑等增强力学性能、同时维持高回弹性、低疲劳热和优异的加工性能,使其用成为轮胎、传动带、鞋具、工程用品等领域的主要原料。节能环保是社会的主旋律,作为耗能大户的运输行业也面对节能减排的要求,随着石油和能源成本的不断升高,新型节能轮胎的需求越来越强烈。添加白炭黑的天然橡胶与添加普通炭黑的比较,节能达7%,但是白炭黑不导电和导热,会降低车体、轮胎的静电排放以及轮胎的寿命,需要添加额外的导电导热材料提高这些特性。如表1所示,与橡胶比较石墨烯具有超高的强度、模量、导热率和导电率,但大尺寸的石墨烯由于结构完整,化学稳定性极高,表面呈惰性状态,片层之间有较强的范德华力,极易聚集,使其不溶于水及常用有机溶剂。表1:石墨烯与橡胶物理和力学性能比较物性石墨烯橡胶形貌结构2维近似平面3维交联拉伸强度(gpa)1300.03杨氏模量(gpa)1000<0.1断裂拉伸(%)<<1>500泊松系数0.05~0.30.48~0.5电导率(s/m)107<10-8热导率(w/(mk))>20000.15高度氧化的石墨烯、即氧化石墨烯并不具备石墨烯的本征性能,目前所谓的石墨烯多数从氧化石墨烯还原所得、即还原氧化石墨烯,其性能远低于石墨烯的本征性能,很难最大限度地发挥石墨烯本征性能优势,且氧化石墨烯在还原时容易重新堆积成为石墨结构造成石墨烯特性的丢失。氧化石墨烯是通过石墨的过氧化分解制得,虽然原材料的鳞片石墨价格低廉,使用超过其20倍重量的酸和氧化剂制得的氧化石墨烯价格在每公斤50美元以上,由于大量使用酸,酸废液的处理也占用了很高成本,处理不当成为公害。采用物理法剥离制备的石墨烯具有高纯度和高长径比(cn201510412742.x,石墨烯纳米粉体的低成本大规模生产工艺),其物理性能更加接近石墨烯的本征性能,即高热导率和高电导率。采用本方法制备的石墨烯适合应用于各种需要高纯度、高质量、高导热、高导电、高强度等的场景(cn201710127349.5,一种低锌粉含量重防腐涂料及其应用;cn201711282927.9一种微波吸波材料及其制备方法;cn2018105777611,一种制备混凝土用石墨烯纳米水性浆料的装置及方法;cn201810909123.5,一种超宽入射角微波吸波材料及其制备方法)。物理法制备的石墨烯拥有非常低的表面官能团,对其进行表面改性和其它材料兼容性的改善难以实现,采用常规的化学氧化法同样有污染和环保问题。技术实现要素:为了解决上述技术问题,本发明提供了一种石墨烯橡胶浓缩料及石墨烯橡胶的生产方法,本发明结合臭氧氧化与物理方法对多层石墨烯进行处理,制得的石墨烯本征性好、易于与橡胶结合的石墨烯。将其与乳胶复合制得导电、导热性好的石墨烯橡胶。此外本发明方法成本低、可实现连续大规模生产。本发明的具体技术方案为:一种石墨烯橡胶浓缩料的生产方法,包括以下步骤:a)以膨胀倍数大于600倍的可膨胀石墨为原材料,在低惰性载气流量或无载气条件下加热至900~1800℃膨胀后得到比表面积大于60m2/g的石墨蠕虫;b)将石墨蠕虫转移至浓度3%以上的臭氧环境中,在150~350℃下氧化5~180秒;c)将石墨蠕虫与浓度为5~25wt%的巯丙基甲基二甲氧基硅烷乙醇水溶液或si69乙醇水溶液按重量比1∶0.01~1以喷雾方式混合,先在室温下反应,然后加热至70~100℃进行表面改性;d)将表面改性后的石墨蠕虫加入至5~100倍质量的去离子水中,分散混合10min-5h,得到均匀的石墨浆料;对石墨浆料在20~50℃下以≥10000/s的剪切速度进行高剪切循环剥离均质处理,得到粘稠的、平均粒径小于20μm的石墨烯浆料;e)将石墨烯浆料与浓度为30~60wt%的氨水稳定乳胶水溶液按重量比1~35∶100缓慢混合,在混合过程中逐渐提高分散速度,分散速度大于100rpm,分散时间为10min-2h,得到混合浆料;对混合浆料在20-50℃下以≥10000/s的剪切速度进行高剪切循环剥离均质处理,得到平均粒径小于20μm的石墨烯乳胶浆料;f)向石墨烯乳胶浆料加入甲酸溶液使ph低于5,使乳胶与石墨烯共同凝絮,与水分相,将水压滤挤出,干燥后得石墨烯橡胶浓缩料。在本发明中,具有以下几个技术效果:1、步骤a)中,本发明以高膨胀倍数的可膨胀石墨为原材料制备石墨蠕虫,所得石墨蠕虫产品比表面积可超过60平方米/克,石墨蠕虫蜂窝结构的壁厚少过50层碳原子,厚度不到20纳米。天然石墨的厚度为微米级其比表面积一般远远少于10平方米/克,剥离至纳米级的石墨烯需更多的能量,所以可膨胀石墨是更佳的原材料。为了得到高含碳量的石墨蠕虫,本发明发现在高温环境下进行膨胀更加理想,膨胀温度更好超过1200℃甚至超过1600℃。杂质在高温处理的过程中挥发排出,不仅使得石墨蠕虫的碳含量可以得到更好的提升,同时产生的纳米孔也是溶剂扩散浸入的开口,也可以使用氦气和其它惰性气体作为载气,有氧的空气等不适合作为载气因为在450℃以上氧可以与石墨蠕虫反应成为一氧和二氧化碳。本发明所得石墨蠕虫碳含量可达98%以上。2、步骤b)中,本发明选用臭氧对石墨蠕虫进行氧化,使之表面拥有活性官能团。本发明团队发现氧化温度要严格控制,若温度高于350℃则氧化速度太快,出现表面过度氧化,若温度低于150℃则氧化速度较慢,与石墨蠕虫的生成速度无法匹配。石墨蠕虫为多层片状结构,本发明用臭氧改性后,在特定氧化温度下,只在表面有缺陷的石墨烯结构进行氧化,与现有技术中在剥离制得石墨烯后再进行改性的方式相比,不会过氧化,对石墨烯结构的影响较小,更加能够保持石墨烯的本征性,原因在于剥离制得石墨烯后,片层间距进一步增加,容易使得中间层的平面也大量发生氧化,容易导致石墨烯的本征性丧失。3、步骤c)中,本发明选用巯丙基甲基二甲氧基硅烷乙醇水溶液或si69乙醇水溶液对石墨蠕虫进行进一步表面改性,优点在于:巯丙基甲基二甲氧基硅烷与石墨烯含氧官能团反应,巯丙基甲基二甲氧基硅烷极性较高与石墨烯的极性相近,在降低石墨烯表面极性的同时,活性官能团可以与乳胶兼容,不会产生乳胶破乳现象。进一步地,本发明还采用两步阶段性反应,第二步通过继续加热将残余官能团聚合,使多余官能团失活,确保与乳胶混合时不会产生太多化学键,降低弹性。最后,本发明采用喷雾的方式添加原料,好处在于:喷雾混合有利于增大改性剂与石墨蠕虫的有效接触面积,使得氧化过程更为充分、高效。4、步骤e)中,本发明将石墨蠕虫与氨水稳定乳胶溶液缓慢混合分散,再进行高速剪切剥离,在该剥离过程中,石墨片层间距加大,此时乳胶能够顺势渗透进入片层之间并后续在原位与石墨烯上的活性官能团结合,能够防止石墨烯片层不会在后期重新堆砌。作为优选,步骤b)中,臭氧浓度大于5%。作为进一步优选,步骤b)中,臭氧浓度大于10%。作为优选,所述石墨蠕虫与巯丙基甲基二甲氧基硅烷乙醇水溶液或si69乙醇水溶液的重量比1∶0.1~0.5;巯丙基甲基二甲氧基硅烷乙醇水溶液或si69乙醇水溶液中乙醇水溶液的配方为78-82%乙醇、16-20%去离子水和1-3%乙酸。本发明团队发现,在上述配方中,加入一定量的乙酸,能够有效促进硅氧烷的水解没有利于对石墨蠕虫的改性。作为优选,步骤c)中,室温反应时间为10-200min,加热至70~100℃后反应20~300min。作为优选,步骤f)中,加入甲酸溶液使ph低于4;压滤压力大于0.3mpa,干燥温度为55-65℃,干燥后石墨烯的含量大于10wt%。在干燥时可以采用连续加热隧道,也可以采用红外线和微波加热,由于石墨烯的添加,石墨烯橡胶浓缩料的红外线和微波吸收效率更高,干燥速度更快。作为进一步优选,步骤f)中,压滤压力大于1mpa。作为优选,所述石墨烯橡胶浓缩料通过石墨烯橡胶浓缩料大规模连续生产装置制得,所述装置包括依次连接的可膨胀石墨储罐、高温电加热膨胀炉、臭氧氧化炉、旋转闭风器、搅拌耐压反应釜、浆料泵和压滤机。其中,可膨胀石墨储罐通过螺杆进料机向高温电加热膨胀炉进料,高温电加热膨胀炉的周侧设有碳化硅加热棒,臭氧氧化炉上连接有臭氧发生器,旋转闭风器与搅拌耐压反应釜之间的管路上设有鼓风机,搅拌耐压反应釜的顶部连接有偶联剂储罐、乳胶储罐、甲酸储罐和去离子水储罐;搅拌耐压反应釜底部的排料阀门和搅拌耐压反应釜顶部之间设有循环回路的胶体磨均质机;搅拌耐压反应釜内设有搅拌机构和加热机构。所述胶体磨均质机中,在每段环节采用多组定子和转子的组合,定子和转子之间的距离在50至200微米。本发明人发现,距离越小剪切效率越高。所述搅拌机构包括驱动机构、搅拌轴和环绕搅拌轴的立式螺带,所述搅拌机构的转动方向可调节,顺时针转动时混料,逆时针转动时排料。本发明的搅拌机构的转动方向可调节,从上往下看,顺时针转动时混料,逆时针转动时排料。立式螺带使得搅拌过程更为充分,可调节搅拌方向,使得混料、排料随时切换,同时有利于实现混料、排料程序的连续化,提高生产效率,能够实现连续化生产。其中,需要注意的是,氧化装置的容积必须满足氧化的滞留时间,大约是膨胀倍数和生产速度积的2倍,以每小时20公斤的产能氧化装置需要50~100升的内容积。作为优选,所述旋转闭风器的叶片上设有透气孔。旋转闭风器可以控制蠕虫的流量和氧化时间,在旋转闭风器的叶片设计有透气孔,但是蠕虫不会通过,这样可以确保炉内的压力不会过高。一种利用上述方法制得的石墨烯橡胶浓缩料制备石墨烯橡胶的方法,包括以下步骤:1)将生胶和白炭黑在密炼机内密炼,加入硫化剂、硫化促进剂、硫化活性剂、防老化剂继续密炼;2)加入石墨烯橡胶浓缩料继续密炼,得到均匀的石墨烯生橡胶;3)用开炼机挤出生胶片,将生胶片置于密闭模具内用硫化机硫化,得石墨烯橡胶,石墨烯在石墨烯橡胶中的含量为0.01~5wt%。本发明所制得的石墨烯橡胶,具有出色的高导热系数和低电阻率。作为优选,步骤1)中,两次密炼时间均为4-6min,密炼温度为90-110℃;所述硫化剂、硫化促进剂、硫化活性剂、防老化剂、白炭黑与生胶的重量比为1~5∶0.5~4∶1~10∶0.5~5∶10~60∶100;所述白炭黑为纳米白炭黑,所述硫化剂为硫磺,所述促进剂为cbs,所述硫化活性剂为氧化锌,所述防老剂为2,6-二叔丁基-4-甲基苯酚;步骤2)中,密炼时间为5-30min。作为优选,步骤3)中,硫化温度为130-160℃,硫化时间为10-60min。与现有技术对比,本发明的有益效果是:1、本发明结合臭氧氧化与物理方法对多层石墨烯进行处理,制得的石墨烯本征性好,与传统的氧化还原发相比,并不会改变石墨烯整体物理性能很多,同时易于与橡胶结合,将其与乳胶复合制得导电、导热性好的石墨烯橡胶。2、本发明方法成本低、可实现连续大规模生产。附图说明图1为本发明石墨烯橡胶浓缩料的生产装置结构示意图;图2为石墨烯橡胶的拉伸强度;图3为石墨烯橡胶的热导率曲线;图4为石墨烯橡胶的电阻率曲线;图5为石墨烯0.5%含量橡胶的断裂面显微镜照片。附图标记为:高温电加热膨胀炉1、碳化硅加热棒2、臭氧氧化炉3、可膨胀石墨储罐4、螺杆进料机5、臭氧发生器6、旋转闭风器7、鼓风机8、搅拌耐压反应釜9、浆料泵10、胶体磨均质机11、偶联剂储罐12、甲酸储罐13、乳胶储罐14、去离子水储罐15、压滤机16。具体实施方式下面结合实施例对本发明作进一步的描述。总实施例一种石墨烯橡胶浓缩料的生产方法,包括以下步骤:a)以膨胀倍数大于600倍的可膨胀石墨为原材料,在低惰性载气流量或无载气条件下加热至900~1800℃膨胀后得到比表面积大于60m2/g的石墨蠕虫。b)将石墨蠕虫转移至浓度3%以上(优选大于5%,最优选大于10%)的臭氧环境中,在150~350℃下氧化5~180秒。c)将石墨蠕虫与浓度为5~25wt%的巯丙基甲基二甲氧基硅烷乙醇水溶液或si69乙醇水溶液按重量比1∶0.01~1(优选1∶0.1~0.5)以喷雾方式混合,先在室温下反应10-200min,然后加热至70~100℃进行表面改性20~300min。其中乙醇水溶液的配方为78-82%乙醇、16-20%去离子水和1-3%乙酸。d)将表面改性后的石墨蠕虫加入至5~100倍质量的去离子水中,分散混合10min-5h,得到均匀的石墨浆料;对石墨浆料在20~50℃下以≥10000/s的剪切速度进行高剪切循环剥离均质处理,得到粘稠的、平均粒径小于20μm的石墨烯浆料。e)将石墨烯浆料与浓度为30~60wt%的氨水稳定乳胶水溶液按重量比1~35∶100缓慢混合,在混合过程中逐渐提高分散速度,分散速度大于100rpm,分散时间为10min-2h,得到混合浆料;对混合浆料在20-50℃下以≥10000/s的剪切速度进行高剪切循环剥离均质处理,得到平均粒径小于20μm的石墨烯乳胶浆料。f)向石墨烯乳胶浆料加入甲酸溶液使ph低于5(优选低于4),使乳胶与石墨烯共同凝絮,与水分相,将水压滤挤出(压滤压力大于0.3mpa,优选大于1mpa),55-65℃干燥后得石墨烯橡胶浓缩料,干燥后石墨烯的含量大于10wt%。其中,如图1所示,所述石墨烯橡胶浓缩料通过石墨烯橡胶浓缩料大规模连续生产装置制得,所述装置包括依次连接的可膨胀石墨储罐4、高温电加热膨胀炉1、臭氧氧化炉3、旋转闭风器7、搅拌耐压反应釜9、浆料泵10和压滤机16。其中,可膨胀石墨储罐通过螺杆进料机5向高温电加热膨胀炉进料,高温电加热膨胀炉的周侧设有碳化硅加热棒2,臭氧氧化炉上连接有臭氧发生器6,旋转闭风器与搅拌耐压反应釜之间的管路上设有鼓风机8,搅拌耐压反应釜的顶部连接有偶联剂储罐12、乳胶储罐14、甲酸储罐13和去离子水储罐15;搅拌耐压反应釜底部的排料阀门和搅拌耐压反应釜顶部之间设有循环回路的胶体磨均质机11;搅拌耐压反应釜内设有搅拌机构和加热机构。所述胶体磨均质机中,在每段环节采用多组定子和转子的组合,定子和转子之间的距离在50至200微米。所述搅拌机构包括驱动机构、搅拌轴和环绕搅拌轴的立式螺带,所述搅拌机构的转动方向可调节,顺时针转动时混料,逆时针转动时排料。作为优选,所述旋转闭风器的叶片上设有透气孔。一种利用上述方法制得的石墨烯橡胶浓缩料制备石墨烯橡胶的方法,包括以下步骤:1)将生胶和白炭黑在密炼机内密炼4-6min,加入硫化剂、硫化促进剂、硫化活性剂、防老化剂继续密炼4-6min,密炼温度为90-110℃。所述硫化剂、硫化促进剂、硫化活性剂、防老化剂、白炭黑与生胶的重量比为1~5∶0.5~4∶1~10∶0.5~5∶10~60∶100;所述白炭黑为纳米白炭黑,所述硫化剂为硫磺,所述促进剂为cbs,所述硫化活性剂为氧化锌,所述防老剂为2,6-二叔丁基-4-甲基苯酚。2)加入石墨烯橡胶浓缩料继续密炼5-30min,得到均匀的石墨烯生橡胶。3)用开炼机挤出生胶片,将生胶片置于密闭模具内用硫化机在130-160℃下硫化10-60min,得石墨烯橡胶,石墨烯在石墨烯橡胶中的含量为0.01~5wt%。实施例1a)以膨胀倍数600倍、50目的可膨胀石墨为原材料,在无载气的条件下加热至950℃膨胀后得到比表面积70m2/g的石墨蠕虫。b)将石墨蠕虫转移至浓度10%的臭氧氧化炉(容积为0.1m3)中,在200℃下氧化15秒。c)将石墨蠕虫与浓度为10wt%的si69乙醇水溶液按重量比1∶0.2以喷雾方式混合,先在室温下反应100min,然后加热至70℃进行表面改性30min,然后在1h内加热至100℃继续表面改性60min,然后持续搅拌降温至50℃以下,完成表面改性。其中乙醇水溶液的配方为80%乙醇、18%去离子水和2%乙酸。d)将表面改性后的石墨蠕虫加入至9.8倍质量的去离子水中,分散混合60min,得到均匀的石墨浆料;对石墨浆料在40℃下以15000/s的剪切速度进行高剪切循环剥离均质处理,得到粘稠的、平均粒径小于20μm的石墨烯浆料。e)将石墨烯浆料与浓度为50wt%的氨水稳定乳胶水溶液按重量比1∶8缓慢混合,在混合过程中逐渐提高分散速度,分散速度150rpm,分散时间为60min,得到混合浆料;对混合浆料在40℃下以>15000/s的剪切速度进行高剪切循环剥离均质处理,得到平均粒径小于20μm的石墨烯乳胶浆料。f)向石墨烯乳胶浆料加入65wt%甲酸溶液使ph低于4,使乳胶与石墨烯共同凝絮,与水分相,将水压滤挤出(压滤压力为1mpa),60℃干燥后得石墨烯橡胶浓缩料,干燥后石墨烯的含量为20wt%。g)将生胶和白炭黑在密炼机内密炼5min,加入硫化剂、硫化促进剂、硫化活性剂、防老化剂继续密炼5min,密炼温度为100℃。所述硫化剂、硫化促进剂、硫化活性剂、防老化剂、白炭黑与生胶的重量比为2∶1∶3∶2∶20∶100;所述白炭黑为纳米白炭黑,所述硫化剂为硫磺,所述促进剂为cbs,所述硫化活性剂为氧化锌,所述防老剂为2,6-二叔丁基-4-甲基苯酚。h)加入石墨烯橡胶浓缩料继续密炼15min,得到均匀的石墨烯生橡胶。i)用开炼机挤出2.1mm厚的生胶片,将生胶片置于2.0mm深密闭模具内用硫化机在145℃下硫化40min,得石墨烯橡胶,石墨烯在石墨烯橡胶中的含量为0-2wt%。然后切成所需测试样件,进行力学和硫化后性能等测试,测试按gb/t528-1998进行,测得力学性能如图2所示,当石墨烯含量在0.2%时得到最高拉伸强度,如图3所示,导热系数则随石墨烯的含量增加而线性地增加,符合预期。如图4所示,电阻率数则随石墨烯的含量增加而减小,符合预期。从图5的扫描电镜照片得知,石墨烯在橡胶中均匀分布。实施例2:a)以膨胀倍数600倍、50目的可膨胀石墨为原材料,在无载气的条件下加热至1050℃膨胀后得到比表面积74m2/g的石墨蠕虫。b)将石墨蠕虫转移至浓度10%的臭氧氧化炉(容积为0.1m3)中,在250℃下氧化10秒。c)将石墨蠕虫与浓度为8wt%的巯丙基甲基二甲氧基硅烷乙醇水溶液按重量比1∶0.25以喷雾方式混合,先在室温下反应90min,然后加热至70℃进行表面改性50min,然后在1h内加热至100℃继续表面改性90min,然后持续搅拌降温至50℃以下,完成表面改性。其中乙醇水溶液的配方为80%乙醇、18%去离子水和2%乙酸。d)将表面改性后的石墨蠕虫加入至10.8倍质量的去离子水中,分散混合60min,得到均匀的石墨浆料;对石墨浆料在40℃下以>15000/s的剪切速度进行高剪切循环剥离均质处理,得到粘稠的、平均粒径小于20μm的石墨烯浆料。e)将石墨烯浆料与浓度为50wt%的氨水稳定乳胶水溶液按重量比10∶100缓慢混合,在混合过程中逐渐提高分散速度,分散速度150rpm,分散时间为60min,得到混合浆料;对混合浆料在40℃下以>15000/s的剪切速度进行高剪切循环剥离均质处理,得到平均粒径小于20μm的石墨烯乳胶浆料。f)向石墨烯乳胶浆料加入65wt%甲酸溶液使ph低于4,使乳胶与石墨烯共同凝絮,与水分相,将水压滤挤出(压滤压力为1.5mpa),60℃干燥后得石墨烯橡胶浓缩料,干燥后石墨烯的含量为16.5wt%。g)将生胶和白炭黑在密炼机内密炼4min,加入硫化剂、硫化促进剂、硫化活性剂、防老化剂继续密炼4min,密炼温度为110℃。所述硫化剂、硫化促进剂、硫化活性剂、防老化剂、白炭黑与生胶的重量比为3∶2∶5∶3∶30∶100;所述白炭黑为纳米白炭黑,所述硫化剂为硫磺,所述促进剂为cbs,所述硫化活性剂为氧化锌,所述防老剂为2,6-二叔丁基-4-甲基苯酚。h)加入石墨烯橡胶浓缩料继续密炼20min,得到均匀的石墨烯生橡胶。i)用开炼机挤出2.1mm厚的生胶片,将生胶片置于2.0mm深密闭模具内用硫化机在130℃下硫化60min,得石墨烯橡胶。实施例3:a)以膨胀倍数1000倍、50目的可膨胀石墨为原材料,在无载气的条件下加热至1050℃膨胀后得到比表面积83m2/g的石墨蠕虫。b)将石墨蠕虫转移至浓度8%的臭氧氧化炉(容积为0.1m3)中,在180℃下氧化60秒。c)将石墨蠕虫与浓度为10wt%的si69乙醇水溶液按重量比1∶0.3以喷雾方式混合,先在室温下反应90min,然后加热至70℃进行表面改性60min,然后在1h内加热至100℃继续表面改性90min,然后持续搅拌降温至50℃以下,完成表面改性。其中乙醇水溶液的配方为80%乙醇、18%去离子水和2%乙酸。d)将表面改性后的石墨蠕虫加入至11.7倍质量的去离子水中,分散混合60min,得到均匀的石墨浆料;对石墨浆料在40℃下以>15000/s的剪切速度进行高剪切循环剥离均质处理,得到粘稠的、平均粒径小于20μm的石墨烯浆料。e)将石墨烯浆料与浓度为50wt%的氨水稳定乳胶水溶液按重量比1∶12缓慢混合,在混合过程中逐渐提高分散速度,分散速度150rpm,分散时间为60min,得到混合浆料;对混合浆料在40℃下以>15000/s的剪切速度进行高剪切循环剥离均质处理,得到平均粒径小于20μm的石墨烯乳胶浆料。f)向石墨烯乳胶浆料加入65wt%甲酸溶液使ph低于4,使乳胶与石墨烯共同凝絮,与水分相,将水压滤挤出(压滤压力为1.5mpa),60℃干燥后得石墨烯橡胶浓缩料,干燥后石墨烯的含量为14.5wt%。g)将生胶和白炭黑在密炼机内密炼6min,加入硫化剂、硫化促进剂、硫化活性剂、防老化剂继续密炼6min,密炼温度为90℃。所述硫化剂、硫化促进剂、硫化活性剂、防老化剂、白炭黑与生胶的重量比为5∶4∶10∶5∶60∶100;所述白炭黑为纳米白炭黑,所述硫化剂为硫磺,所述促进剂为cbs,所述硫化活性剂为氧化锌,所述防老剂为2,6-二叔丁基-4-甲基苯酚。h)加入石墨烯橡胶浓缩料继续密炼20min,得到均匀的石墨烯生橡胶。i)用开炼机挤出2.1mm厚的生胶片,将生胶片置于2.0mm深密闭模具内用硫化机在130℃下硫化60min,得石墨烯橡胶。本发明中所用原料、设备,若无特别说明,均为本领域的常用原料、设备;本发明中所用方法,若无特别说明,均为本领域的常规方法。以上所述,仅是本发明的较佳实施例,并非对本发明作任何限制,凡是根据本发明技术实质对以上实施例所作的任何简单修改、变更以及等效变换,均仍属于本发明技术方案的保护范围。当前第1页12