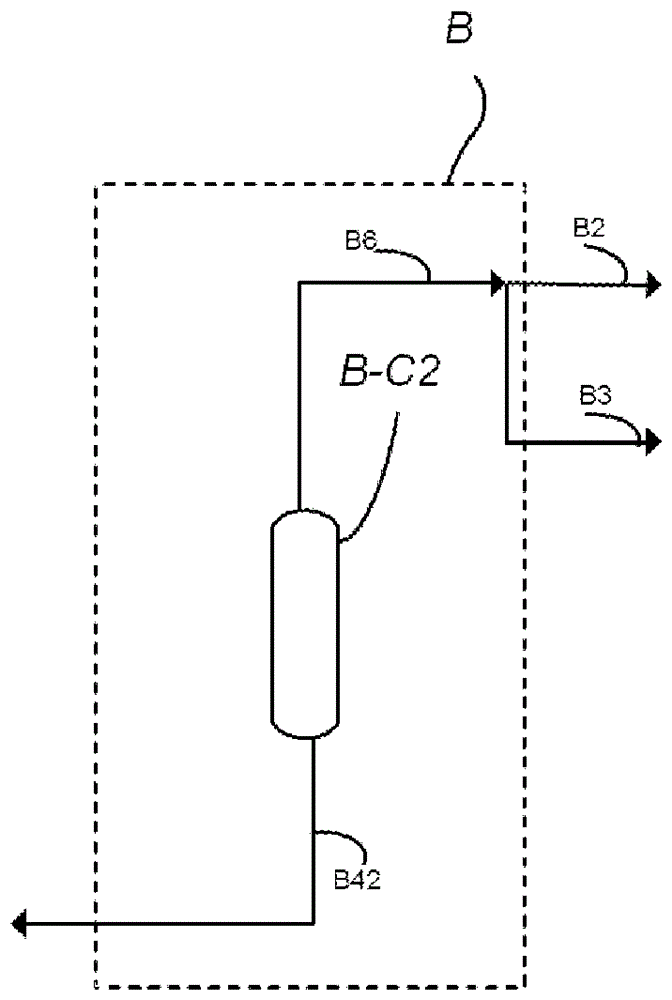
对二甲苯主要用于生产对苯二甲酸和聚对苯二甲酸乙二醇酯树脂,其用于生产合成纺织品、瓶子、更通常是塑料。本发明涉及使用特定顺序的步骤生产高纯度对二甲苯的方法,以实现对二甲苯的高产量。
背景技术:
:使用通过吸附分离的步骤生产高纯度对二甲苯在现有技术中是公知的。工业上,所述步骤在一系列“c8-芳族环路”或“二甲苯环路”方法内进行。该“c8-芳族环路”包括在称为“二甲苯塔”的蒸馏塔中除去重质化合物(即含有多于9个碳原子的化合物,表示为c9+)的步骤。然后将来自该塔的含有c8-芳族异构体的塔顶物流送入对二甲苯分离过程,其通常是在模拟移动床中通过吸附分离的步骤。然后使用提取塔、然后使用甲苯塔将在模拟移动床中通过吸附分离的步骤结束时获得的提取物(其含有对二甲苯)蒸馏,以获得高纯度的对二甲苯。在通过蒸馏除去解吸剂的步骤之后,将在模拟移动床中通过吸附分离的步骤结束时获得的提余液(其富含间二甲苯、邻二甲苯和乙苯)用于异构化步骤中,可以获得其中二甲苯(或邻二甲苯、间二甲苯和对二甲苯)的比例实际上处于热力学平衡并且贫含乙苯的混合物。将该混合物与用于生产对二甲苯的新鲜原料一起再次送入“二甲苯塔”。现有技术提出了该方案的许多变型,其使用一个或多个分离步骤(通过吸附、结晶、蒸馏或通过膜)和/或一个或多个气相异构化步骤(通过异构化将乙苯转化为二甲苯或通过脱烷基化将乙苯转化为苯)或液相异构化步骤(不转化乙苯)。现有技术中提出的变型之一包括在两个单独的步骤中实施异构化。第一步骤可以将富含间二甲苯、邻二甲苯和乙苯的提余液中所含的乙苯异构化。在分馏之后,将来自该第一异构化区段的流出物(其贫含乙苯)送入第二区段,该第二区段包括通过吸附分离对二甲苯、然后是将二甲苯异构化为对二甲苯的第二步骤。异构化催化剂和操作条件的优化可以限制不期望的副反应。因此,确定的是,为了促使乙苯转化为二甲苯,优选在高温下在气相中进行异构化。另外,已知在低温下在液相中的异构化使假裂化烷基转移和歧化反应最小化,并且还限制了乙苯的转化。使用两个异构化步骤生产高纯度对二甲苯的方法更复杂并且导致对二甲苯产量的增益是有限的。其原因在于,为了实现足够高的乙苯转化率,第一气相异构化步骤的操作条件是苛刻的并且伴随有导致损失c8芳族化合物的副反应,这对对二甲苯的总收率具有实质性影响。专利fr2862638描述了使用两个模拟移动床分离步骤和两个异构化步骤由烃原料生产对二甲苯的方法。该方法的缺点是它需要两个模拟移动床分离步骤,这导致生产成本的显著增加。专利fr3023840和专利fr3023841描述了包括两个模拟移动床分离步骤和两个异构化单元步骤的替代方法,其中在来自第一模拟移动床分离单元的提余液回路上串联或并联地实施所述两个异构化步骤。专利fr3023842描述了包括模拟移动床吸附步骤和两个异构化步骤(一个在气相中,另一个在液相中)的替代方法,其中将产生自来自吸附单元的流出物的分馏的相同原料进料至所述两个异构化单元。在本发明的领域中,本领域技术人员不断寻求限制用于操作所用的二甲苯环路的投资成本和操作成本,同时增加所获得的高纯度对二甲苯的量。令人意外的是,本申请人已发现在生产高纯度对二甲苯的方法中,组合在smb中通过吸附分离的步骤与随后在第一三馏分蒸馏塔中通过蒸馏分离而产生至少两个提余液的步骤和两个异构化步骤可以改善芳族环路的对二甲苯总收率并使经济影响最小化。与现有技术方法相比,根据本发明的方法的一个优点是它在产能(capacity)增加方面具有小的折衷的情况下实现了对二甲苯的高产量。本发明的另一个优点是它具有很大的灵活性,这可以在操作中得以运用,因此可以适应所实施的每个异构化步骤的催化性能的变化。定义和缩写在整个说明书中,以下术语或缩写具有以下含义。需要指出的是,在整个说明书中,表述“在......和......之间”应理解为包括所提到的限值。缩写eb表示乙苯。缩写px表示对二甲苯。缩写ox表示邻二甲苯。缩写mx表示间二甲苯。术语“二甲苯”(也表示为xyl)是指至少两种选自邻二甲苯、间二甲苯和对二甲苯的二甲苯异构体的混合物。缩写smb表示模拟移动床。术语“c9+烃”是指含有至少9个碳原子的烃。术语“c8+烃”是指含有至少8个碳原子的烃。术语“c8芳族化合物”,也表示为c8a,表示含有8个碳原子的芳烃,即eb、px、ox、mx,优选eb、ox、mx。术语“提余液”是指贫含px的c8a混合物,其可含有解吸剂,即其具有小于2.0%、优选小于1.5%、优选1.0%的px的质量含量。出于本发明的目的,术语“不含”是指相对于所考虑的馏分(例如eb)的总质量,给定化合物的质量含量小于0.5重量%,优选小于0.1%,优选小于0.01%。给定化合物的术语“残余量”是指其相对于所考虑的馏分的总质量的质量含量小于5.0重量%、优选5.0-1.0重量%、优选4.0-1.0重量%、优选3.0-1.0重量%的量。在本发明中,等同地使用术语“流出物”、“提余液”、“物流”和“馏分”。术语“两馏分蒸馏塔和三馏分蒸馏塔”是指分别用于获得两个馏分和三个馏分的蒸馏塔。技术实现要素:因此,本发明涉及由含有二甲苯、乙苯和c9+烃的原料生产对二甲苯的方法,其包括:-采用作为吸附剂的沸石和解吸剂、在20-250℃的温度、1.0-2.2mpa的压力下、以模拟移动床分离单元中0.4-2.5的解吸剂与原料的体积比在模拟移动床中实施的将所述原料分离的单个步骤a;所述步骤a可以产生:含有对二甲苯和解吸剂的混合物的第一馏分a1,和至少一个含有乙苯(eb)、邻二甲苯(ox)和间二甲苯(mx)和解吸剂的第二馏分a2或a21,-在至少一个第一蒸馏塔b-c3中通过蒸馏分馏产生自步骤a的所述第二馏分的步骤b,所述步骤b可以产生三个馏分:含有eb、ox和mx的第一馏分b2,含有ox和mx的第二馏分b3和含有解吸剂的第三馏分b42。优选地,产生自步骤b的第一馏分b2具有大于产生自步骤b中使用的第一塔b-c3的第二馏分b3的eb含量的eb含量。优选地,第一馏分的eb含量比第二馏分的eb含量高至少1.0%。优选地,步骤b中使用的蒸馏塔包括30-80个理论塔板。在另一个具体的实施方案中,分离步骤a还可以产生贫含eb,含有mx、ox和解吸剂的混合物的第三馏分a22,所述馏分a21和所述馏分a22被送入所述分馏步骤b中。有利地,在该实施方案中,将产生自步骤a的第三馏分a22送入第二蒸馏塔b-c4中,从而产生不含解吸剂,含有mx和ox的馏分b31和由解吸剂组成的馏分b43。在另一个具体的实施方案中,将第二馏分b3送入第二蒸馏塔b-c4中的分馏步骤b中,从而产生不含解吸剂,含有mx和ox的馏分b31和由解吸剂组成的馏分b43。有利地,在该实施方案中,在产生自第一蒸馏塔b-c3的第二馏分b3的侧向注入点的下方将产生自步骤a的第三馏分a22引入第二蒸馏塔b-c4中。有利地,蒸馏步骤b使用包括内壁的塔。有利地,所述方法还包括将产生自分馏步骤的含有eb、ox和mx的第一馏分b2气相异构化的步骤c。有利地,所述方法还包括将产生自分馏步骤b中使用的第一蒸馏塔b-c3的含有ox和mx的第二馏分b3液相异构化的步骤d。有利地,所述方法还包括将产生自分馏步骤中使用的第二蒸馏塔b-c4的含有ox和mx的馏分b31液相异构化的步骤d。有利地,在高于300℃的温度、低于4.0mpa的压力、小于10.0h-1的空速、小于10.0的氢气与烃的摩尔比以及催化剂的存在下实施气相异构化步骤c,所述催化剂包含至少一种具有通道的沸石和至少一种含量为0.1重量%-0.3重量%的来自第viii族的金属,所述通道的孔径由具有10或12个氧原子的环(10mr或12mr)限定。有利地,步骤c中使用的催化剂包含1重量%-70重量%的euo结构类型的沸石,所述沸石包含硅和至少一种优选选自铝和硼的元素t,所述沸石的si/t比为5-100。有利地,在低于300℃的温度、低于4.0mpa的压力、小于5.0h-1、优选2.0至4.0h-1的空速以及催化剂的存在下实施液相异构化步骤d,所述催化剂包含至少一种具有通道的沸石,所述通道的孔径由具有10或12个氧原子的环(10mr或12mr)限定;优选地,所述沸石是zsm-5型。附图说明图1是二甲苯环路的总体方案,其包括通过吸附分离的步骤、分馏步骤、气相异构化步骤c和液相异构化步骤d。图2a表示根据现有技术的获自步骤a的提余液的蒸馏步骤b。图2b是根据本发明的获自步骤a的提余液的蒸馏步骤b的第一变型。图2c是根据本发明的获自步骤a的提余液的蒸馏步骤b的第二变型。图3a表示根据现有技术的获自步骤a的两个提余液的蒸馏步骤b。图3b是根据本发明的获自步骤a的两个提余液的蒸馏步骤b的变型。发明详述参考根据本发明的附图中图示说明的实施方案的附图标记,通过阅读以下非限制性实施例的描述,根据本发明的方法的特征和优点将变得明显。出于本发明的目的,所示的各种实施方案可以单独使用或彼此组合使用,对组合没有任何限制。因此,本发明涉及由含有二甲苯、乙苯和c9+烃的原料生产对二甲苯的方法,其包括:-采用作为吸附剂的沸石和解吸剂、在20-250℃的温度、1.0-2.2mpa的压力下、以模拟移动床分离单元中0.4-2.5的解吸剂与原料的体积比在模拟移动床中实施的将所述原料分离的单个步骤a;所述步骤a可以产生:含有对二甲苯和解吸剂的混合物的第一馏分a1,和至少一个含有乙苯(eb)、邻二甲苯(ox)和间二甲苯(mx)和解吸剂的第二馏分a2或a21,-在至少一个第一蒸馏塔b-c3中通过蒸馏分馏产生自步骤a的所述第二馏分的步骤b,所述步骤b可以产生三个馏分:含有eb、ox和mx的第一馏分b2,含有ox和mx的第二馏分b3和含有解吸剂的第三馏分b42。因此,根据本发明的方法可以在分馏步骤结束时获得两个具有不同比例的c8a的馏分,从而增加在液相中操作、采用催化剂实施的二甲苯异构化的px比例并可以限制c8a的损失。模拟移动床分离步骤a根据本发明,所述方法包括在模拟移动床(smb)中将含有二甲苯、乙苯和c9+烃的原料分离的单个步骤a。所述smb分离步骤采用作为吸附剂的沸石和解吸剂来实施,并可以产生至少两个馏分:含有对二甲苯(px)和解吸剂的混合物的馏分a1(也称为“提取物”),含有乙苯(eb)、邻二甲苯(ox)、间二甲苯(mx)和解吸剂的馏分a2(也称为“提余液”)。在作为模拟移动床操作的单元中、在至少一个分离塔中实施分离步骤,所述分离塔包括多个相互连接的床和在封闭环路中循环的解吸剂,由此得到两个馏分:•第一馏分是提取物a1,其含有对二甲苯和解吸剂,优选由对二甲苯和解吸剂组成,从而使得在分馏除去解吸剂后,px达到最小99.0重量%,优选99.9重量%的商业纯度。有利地,提取物a1占提取总质量的至少30重量%。•第二馏分是提余液a2,其含有乙苯(eb)、间二甲苯、邻二甲苯和解吸剂。优选地,提余液贫含对二甲苯,即所述提余液中的px质量含量小于1.0%,优选小于0.5%。在另一个实施方案中,在单个smb分离步骤中获得至少三个馏分,•第一馏分是提取物a1,其含有对二甲苯和解吸剂,优选由对二甲苯和解吸剂组成;在分馏该提取物后,获得商业规格的px。有利地,提取物a1占提取总质量的至少30重量%。•贫含对二甲苯的两个馏分a21和a22,其含有可变比例的eb、mx、ox和解吸剂的混合物。在该实施方案中,馏分a21和馏分a22具有不同比例的eb、mx和ox,从而使得馏分a21的c8a馏分的eb含量大于馏分a22的c8a馏分的eb含量。优选地,贫含px的馏分a21含有eb、mx、ox和解吸剂的混合物;优选地,eb是残余量。优选地,贫含eb和px的馏分a22含有mx、ox和解吸剂的混合物。优选地,在模拟移动床分离单元中使用的吸附剂是钡交换沸石x或钾交换沸石y或钡和钾交换沸石y。在一个实施方案中,经由根据本发明的方法处理的原料中所含的解吸剂据说是重质的,即其具有高于二甲苯的沸点的沸点。在另一个实施方案中,经由根据本发明的方法处理的原料中所含的解吸剂据说是轻质的,即其具有低于二甲苯的沸点的沸点。优选地,在模拟移动床分离单元中使用的解吸剂选自对二乙苯、甲苯、对二氟苯或二乙苯,单独地或作为混合物。优选地,模拟移动床分离单元中的解吸剂与原料的体积比为0.4-2.5,优选0.5-1.5。优选地,在20℃-250℃、优选90℃-210℃、甚至更优选160℃-200℃的温度以及1.0-2.2mpa、优选1.2-2.0mpa的压力下实施模拟移动床分离步骤a。优选地,吸附器包括多个相互连接的床,所述床分布在由原料和解吸剂的注入、以及提取物和一种或多种提余液的取出界定的若干个区域。取决于提余液的数量,吸附器将优选包括15-18个床。根据一个具体的实施方案,分离单元(smb)中的床的总数为10-30个床,优选15-18个床,所述床分布在一个或多个吸附器中,调节床的数量,以使每个床具有0.70m-1.40m的高度。根据一个具体的实施方案(alt0,alt1),分离单元(smb)的每个区域中的吸附剂固体量的分布如下:•区域1中的吸附剂固体量为17%±5%,•区域2中的吸附剂固体量为42%±5%,•区域3中的吸附剂固体量为25%±5%,•区域4中的吸附剂固体量为17%±5%。根据一个具体的实施方案(alt2),分离单元(smb)的每个区域中的吸附剂固体量的分布如下:•区域1中的吸附剂固体量为18%±8%,•区域2中的吸附剂固体量为41%±8%,•区域3a中的吸附剂固体量为18%±8%,•区域3b中的吸附剂固体量为14%±8%,•区域4中的吸附剂固体量为9%±8%。分馏步骤b根据本发明的方法包括在至少一个第一三馏分塔中通过蒸馏分馏获自分离步骤a的馏分a2的步骤b,所述馏分a2包含乙苯、邻二甲苯、间二甲苯和解吸剂。所述步骤b可以产生:第一馏分b2,其含有eb、ox和mx,优选由eb、ox和mx组成,和第二馏分b3,其含有ox、mx和eb,优选由ox和mx以及残余量的eb组成,和馏分b42,其含有解吸剂,优选由解吸剂组成。有利地,第一馏分b2和第二馏分b3包含可变比例的eb、mx和ox的混合物,从而使得第一馏分的c8a中的eb含量大于第二馏分的eb含量。优选地,第一馏分和第二馏分之间的eb含量差异大于1.0%,优选大于2.0%,优选大于2.5%,优选大于3.0%,优选大于3.5%。有利地,步骤b中使用的三馏分塔具有30-80、优选35-75、优选40-80、非常优选45-65个理论塔板数。在一个实施方案中,当第二馏分b3含有解吸剂时,将所述馏分送入第二蒸馏塔b-c4中的分馏步骤b中,从而产生不含解吸剂,含有mx和ox的馏分b31和由解吸剂组成的馏分b43。有利地,当在包括60个理论塔板的单个三馏分塔中实施提余液的分馏时(实施方案alt0):-进料的位置位于从冷凝器起编号的塔板30-40上,并且优选在塔板37上。-取出的位置位于进料上方的至少第10-25个塔板处,优选位于进料上方的第18个塔板处。有利地,当在第一三馏分塔中、然后在第二两馏分塔中实施提余液的分馏时,每个塔优选包括47个理论塔板(实施方案alt1,实施方案alt2):-进料的位置位于从冷凝器起编号的塔板16-24上,并且优选在塔板18-22之间。-从三馏分塔中取出的位置位于进料位置下方的第5-10个塔板之间,优选位于进料下方的第7-8个塔板之间。-提余液塔的取出的位置和进料的位置可以作为安装在每个提余液塔中的塔板的总数的函数类似地调节。优选地,将获自步骤a的含有px和解吸剂的混合物、优选由px和解吸剂的混合物组成的馏分a1送入在蒸馏塔(b-c1)中通过蒸馏分馏的步骤中,从而产生由px组成的馏分b1和由解吸剂组成的馏分b41。根据本领域技术人员的知识实施所述蒸馏。在本发明的一个具体的实施方案中(图2b,alt0),将获自步骤a的馏分a2送入在第一三馏分蒸馏塔b-c3中通过蒸馏分馏的步骤中,从而在塔顶产生含有eb、mx和ox的馏分b2,作为侧线取出产生不含解吸剂且含有ox和mx、优选由mx和ox以及残余量的eb组成的馏分b3,并且在塔底产生含有解吸剂、优选由解吸剂组成的馏分b42。在一个优选的实施方案(图2c,alt1)中,使用所述三馏分塔b-c3以:-在塔顶获得第一馏分b2,其含有eb、ox和mx,优选由eb、ox和mx组成,-作为侧线取出获得第二馏分b3,其含有ox、mx、解吸剂和残余量的eb,优选由ox、mx和解吸剂组成,和-在塔底获得含有解吸剂、优选由解吸剂组成的馏分b42。将所述馏分b3送入第二两馏分蒸馏塔b-c4中,从而产生不含解吸剂,含有mx和ox的馏分b31以及由解吸剂组成的馏分b43。有利地,实施方案alt1(图2c)可以降低富含eb的馏分b2中的二甲苯含量。在另一个优选的实施方案alt2中,步骤a允许产生两个馏分a21和a22(图3b,alt2)。将所述馏分a21送入在第一三馏分蒸馏塔b-c3中通过蒸馏分馏的步骤b中,从而:-在塔顶产生含有eb、ox和mx、优选由eb、ox和mx组成的第一馏分b2,-作为侧线取出产生含有ox、mx、解吸剂和任选残余量的eb、优选由ox、mx和解吸剂组成的第二馏分b3,和-在塔底产生含有解吸剂、优选由解吸剂组成的第三馏分b42。在实施方案alt2中,将获自步骤b中使用的第一塔的所述第二馏分b3和获自步骤a的馏分a22送入第二蒸馏塔b-c4中,从而产生含有mx、ox和任选残余量的eb、优选由ox和mx组成的馏分b31以及含有解吸剂、优选由解吸剂组成的馏分b43。优选地,在馏分b3的注入点的下方将馏分a22引入提余液的第二塔、优选两馏分塔b-c4中。有利地,在所述实施方案alt2(图3b)中,三馏分塔b-c3仅接收获自通过smb分离的步骤a的提余液a2的富含eb的馏分a21,相对于实施方案alt1,这可以进一步降低富含eb的馏分b2中的二甲苯含量。有利地,在每个蒸馏塔的塔底回收不含c8a的解吸剂馏分b41、馏分b42和馏分b43,将它们合并为馏分b4并送入模拟移动床吸附步骤a。当所述步骤a的解吸剂是比二甲苯更重的化合物,即沸点高于二甲苯的沸点的化合物时,在三馏分塔的塔顶产生富含eb的提余液,在侧线取出中或在第二蒸馏塔的塔顶获得富含二甲苯的提余液。当所述分离步骤的解吸剂是比二甲苯更轻的化合物,即沸点低于二甲苯的沸点的化合物时,在三馏分塔的塔底产生富含二甲苯的物流,在侧线取出中或在第二蒸馏塔的塔底获得富含eb的提余液,在两个塔的塔顶取出不含c8a的解吸剂并再循环到吸附步骤中。有利地,在分馏步骤b中使用的蒸馏塔b-c1、蒸馏塔b-c3和蒸馏塔b-c4在大气压力下操作,再沸温度为210-250℃,优选220-240℃,优选230℃,并且表示为回流/原料质量比的回流比为1.0-3.0,优选1.4-2.0。有利地,在塔b-c3的塔顶回收的提余液b3以在冷凝器的下方第四个塔板取出的液态馏出物的形式获得,所述冷凝器处于全回流并且包括倾析槽以取出液态水。更准确地,当步骤b使用蒸馏塔(b-c3)时,通过蒸馏获得的提余液的分馏步骤(alt0和alt1)的性能通过以下来表征:-富含eb的提余液b2中的eb的回收率(dr):dr(eb)=eb(提余液b2)/(eb(提余液b2)+eb(提余液b3))-富含eb的提余液b2中的二甲苯的回收率(dr):dr(xyl)=xyl(提余液b2)/(xyl(提余液b2)+xyl(提余液b3))当步骤b使用第二蒸馏塔(b-c4)时,通过蒸馏获得的提余液的分馏步骤(alt2)的性能通过以下来表征:-富含eb的提余液b2中的eb的回收率(dr):dr(eb)=eb(提余液b2)/(eb(提余液b2)+eb(提余液b31))-富含eb的提余液b2中的二甲苯的回收率(dr):dr(xyl)=xyl(提余液b2)/(xyl(提余液b2)+xyl(提余液b31))有利地,在根据本发明的方法中,乙苯的回收率(表示为dr(eb))为50%-90%,优选80%-90%。有利地,在根据本发明的方法(alt0或alt1)中,当将馏分a1和馏分a2送入分馏步骤时,二甲苯的回收率dr(xyl)相对于乙苯的回收率(dr(eb))的差异为前者比后者小至少2%,优选小至少5%,优选小至少10%,优选小至少15%。有利地,当将馏分a1、馏分a21和馏分a22送入分馏步骤时,二甲苯的回收率dr(xyl)显示出严格地小至少20%、优选小至少23%的差异。根据另一个实施方案,蒸馏步骤可以采用包括第一三馏分蒸馏塔b-c3的任何其他蒸馏布置实施。优选地,根据本发明的变型alt0、alt1或alt2的所述三馏分蒸馏塔b-c3包括内壁,以改善在分离两个不含解吸剂的提余液b2、b3方面的性能。气相异构化步骤c有利地,所述方法包括将获自分馏步骤b的含有乙苯、邻二甲苯和间二甲苯的提余液b2气相异构化的步骤c。有利地,气相异构化步骤允许在气相中、在高温下操作并将乙苯转化为二甲苯的单元中将ox和mx以及eb异构化,以处理获自步骤b的富含eb的提余液b2。优选地,送入异构化步骤c中的提余液b2与在步骤b结束时获得的总提余液(b2+b3或b2+b31)的质量比为20%-90%,优选25%-60%,更优选30%-45%。所述比率有利地可以使对二甲苯的产量最大化。当所述比率高时,可以增加px的产量而不需要对二甲苯环路的产能的任何折衷;当所述比率适中时,px的产量增加得更为显著,但伴随有二甲苯环路产能的略微增加。根据本发明的方法的一个优点是能够提高二甲苯环路中的eb的固定浓度,这可以通过进入第一气相异构化单元来提高eb转化率。因此,在smb中通过吸附分离的步骤与在三馏分塔中通过蒸馏分馏的步骤b和两个异构化步骤的组合可以改善芳族环路的对二甲苯总收率并使经济影响最小化。根据本发明,气相异构化步骤可以将eb转化为二甲苯,其中每乙苯遍次(run)的转化率通常为10%-50%,优选20%-40%,c8芳族化合物(c8a)的损失小于5.0重量%,优选小于3.0重量%,优选小于1.8重量%。在高于300℃、优选350℃-480℃的温度、小于4.0mpa、优选0.5-2.0mpa的压力、小于10.0h-1、优选0.5h-1至6.0h-1的空速、小于10.0、优选3.0-6.0的氢气与烃的摩尔比以及催化剂的存在下实施气相异构化步骤,所述催化剂包含至少一种具有通道的沸石和至少一种含量为0.1重量%-0.3重量%的来自第viii族的金属,所述通道的孔径由具有10或12个氧原子的环(10mr或12mr)限定。任何能够将含有8个碳原子的烃异构化的催化剂(其可以或可以不基于沸石)都适用于气相异构化单元。优选地,所用催化剂包含酸性沸石,例如mfi、mor、maz、fau和/或euo结构类型的沸石。甚至更优选地,所用催化剂包含euo结构类型的沸石和至少一种来自元素周期表第viii族的金属。根据所述方法的一个优选变型,步骤c中使用的催化剂包含1重量%-70重量%的euo结构类型的沸石(优选eu-1),所述沸石包含硅和至少一种优选选自铝和硼的元素t,所述沸石的si/t比为5-100。优选地,所述沸石至少部分为氢形式,并且钠含量使得na/t原子比小于0.1。优选地,所述催化剂包含0.01重量%-2重量%的锡或铟以及每个来自第viii族的金属原子0.5-2个原子的比例的硫。将在步骤c中获得的具有接近于热力学平衡浓度的px、ox和mx异构体浓度的流出物c1再循环到模拟移动床吸附步骤a中。在一个具体的实施方案中,当流出物c1含有经由不期望的反应形成的重质化合物和轻质化合物时,则将所述流出物送入任选的分馏步骤以除去所述化合物。液相异构化步骤d有利地,所述方法包括将获自分馏步骤b的含有邻二甲苯和间二甲苯的馏分b3或馏分b31液相异构化的步骤d。因此,根据本发明的方法可以增加在液相中操作、通过催化剂实施的二甲苯异构化的比例并产生c8a的最低损失。二甲苯异构化步骤d在液相中进行,每遍次的eb转化率小于或等于5.0%,优选小于或等于3.0%,并且优选小于或等于0.2%并且实现二甲苯混合物的异构化,从而使得px接近大于或等于90.0%、优选大于或等于94.0%的热力学平衡。在低于300℃、优选200-260℃的温度、低于4.0mpa、优选1.0-3.0mpa的压力、小于5.0h-1、优选2.0-4.0h-1的空速以及在催化剂的存在下实施液相异构化步骤d,所述催化剂包含至少一种具有通道的沸石,所述通道的孔径由具有10或12个氧原子的环(10mr或12mr)限定,优选所述催化剂包含至少一种具有通道的沸石,所述通道的孔径由具有10个氧原子的环(10mr)限定,甚至更优选所述催化剂包含zsm-5型沸石。专利us8697929更详细地描述了可用于根据本发明的方法中的操作条件以及气相异构化催化剂和液相异构化催化剂。有利地,将在步骤d中获得的具有接近于热力学平衡浓度的px、ox和mx异构体浓度的流出物d1再循环到模拟移动床吸附步骤a中。在一个具体的实施方案中,当流出物d1含有经由不期望的反应形成的重质化合物和轻质化合物时,则将所述流出物送入任选的分馏步骤以除去所述化合物。具体实施方式以下实施例举例说明了本发明而不限制其范围。实施例1:该实施例通过分别比较根据现有技术的蒸馏步骤b(图2a))与根据本发明的方法(图2b)和图2c))(在其实施方案中表示为alt0和alt1)的性能,显示了本发明的优点。该实施例考虑545t/h的c8馏分(2),其获自二甲苯塔并且包含源自重整产物、源自烷基转移单元和源自一个或多个异构化单元的c8芳族化合物(c8a),其组成按重量%表示为如下:c8-0.4%eb4.1%px23.0%mx50.1%ox22.3%c9+0.1%c8-馏分对应于包含少于8个碳原子的化合物。模拟移动床(smb)分离步骤a将c8a馏分送至模拟移动床吸附单元a,该单元a包括通过原料和解吸剂(b4)的注入以及提余液(a2)和提取物(a1)的取出界定的四个区域。在由15个床组成的模拟床吸附单元中实施分离步骤,所述床含有钡交换沸石x,分布如下:¡区域1中3个床,在解吸剂b4的注入和提取物a1的取出之间¡区域2中6个床,在提取物a1的取出和原料的注入之间¡区域3中4个床,在原料的注入和提余液a2的取出之间¡区域4中2个床,在提余液a2的取出和解吸剂b4的注入之间温度为175°c。使用的解吸剂是对二乙苯,解吸剂相对于原料的含量是1.2(体积/体积)。因此,实施通过吸附分离的步骤a可以产生进料至蒸馏步骤b的两个馏分a1和a2:-馏分a1,其含有原料的至少97.0%的px和一部分的解吸剂;将所述馏分送入提取塔b-c1中的蒸馏步骤,以在塔顶回收纯px(物流b1)并在塔底回收解吸剂(物流b41)。-829t/h的贫含px的提余液a2,其含有407t/h的解吸剂。根据现有技术实施通过蒸馏分馏的步骤b(图2a)在该实施方案中,在第24个理论塔板处将提余液(a2)进料到蒸馏塔(b-c2)中,所述塔包括47个理论塔板、冷凝器和再沸器、在0.2mpa下以1.3的回流比操作。所述塔可以产生两个物流:-422t/h的不含解吸剂的塔顶提余液(b6),和-407t/h的不含c8a的塔底解吸剂(b42),并且在吸附所需的温度下进行热交换步骤之后,将其送入步骤a。提余液(b6)被分馏成两个物流。将表示为(b2)的不含解吸剂的提余液(b6)的90.0%送入第一异构化步骤(c),将表示为(b3)的10%的残余提余液(b6)进料至第二异构化步骤(d)。通过蒸馏塔对提余液(a2)进行所述分馏需要86.6gcal/h的再沸能量。根据本发明实施通过蒸馏分馏的步骤b在根据本发明的第一实施方案(图2b,alt0)中,对提余液(a2)实施分离步骤b。在第37个理论塔板处将所述提余液进料到三馏分蒸馏塔(b-c3)中,所述塔包括60个理论塔板、冷凝器和再沸器、在0.2mpa下以1.9的回流比操作。所述塔可以产生三个物流:-367t/h的塔顶提余液(b2),其含有提余液a2中所含的90.0%的乙苯和87.0%的由ox和mx组成的混合物,-作为第19个理论塔板上的侧线取出获得的54t/h的不含解吸剂的提余液(b3),和-407t/h的不含c8a的塔底解吸剂(b42),在吸附所需的温度下进行热交换步骤之后,将其送入步骤a。通过三馏分蒸馏塔对提余液a2进行所述分馏需要86gcal/h的再沸能量。在根据本发明的第二优选实施方案(图2c,alt1)中,对提余液(a2)实施分离步骤b。在第22个理论塔板处将所述提余液进料到三馏分蒸馏塔(b-c3)中,所述塔包括47个理论塔板、冷凝器和再沸器、在0.2mpa下以1.47的回流比操作。所述塔可以产生三个物流:-348t/h的塔顶提余液(b2),其含有总提余液(b2+b31)中所含的90.0%的乙苯和总提余液(b2+b31)中所含的82.0%的二甲苯,-作为第30个理论塔板上的侧线取出获得的202t/h的提余液(b3),和-278t/h的不含c8a的塔底解吸剂(b42),在吸附所需的温度下进行热交换步骤之后,将其送入步骤a。将含有解吸剂的提余液(b3)送至包括47个理论塔板、冷凝器和再沸器、在0.2mpa下以2.1的回流比操作的第二蒸馏塔(b-c4)的第22个塔板,这可以在塔顶回收73t/h的包含mx、ox、贫含px且eb含量为3.0重量%的提余液b31,以及最终的129t/h的不含c8a、含解吸剂的塔底产物(b43),在吸附所需的温度下进行热交换步骤之后将所述塔底产物(b43)送入步骤a。将提余液b31送入在液相中操作的异构化步骤d。经由该实施方案alt1分馏提余液需要86.1gcal/h的再沸能量。在根据本发明的这些各种实施方案中,提余液a2的分馏步骤结束时,将富含eb的提余液b2送入异构化步骤c,并将提余液b31送入异构化步骤d。根据现有技术(图2a))或根据本发明(图2b)和图2c))的提余液分离步骤的性能总结如下:现有技术根据本发明alt0根据本发明alt1图2a)图2b)图2c)dr(eb)90.0%90.0%90.0%dr(xyl)90.0%87.0%82.2%总q再沸(gcal/h)86.686.086.1塔b-c2的塔板数47--(三馏分)塔b-c3的塔板数-6047塔b-c4的塔板数--47该实施例说明了当吸附步骤产生提余液时本发明的优点。根据本发明的实施方案,对于提余液b2中90%的相同的eb回收率而言,可以将相关的二甲苯回收率降低3个百分点或8个百分点。相对于其中回收率相同的现有技术,这种富集可以增加进料至具有适度c8a损失的液相异构化单元的提余液的比例并减少进料至具有较高的c8a损失的气相异构化单元的比例。此后,如实施例3中所示,芳族环路(aromaticcomplex)的px收率增加。这种富集需要使用至少一个第一三馏分蒸馏塔,而不会对分馏步骤b的再沸所需的能量产生任何影响,或不会对吸附步骤a的布置或操作产生任何影响。如实施例3中所示,相对于现有技术,可以增加芳族环路的px收率。实施例2:该实施例通过比较根据现有技术的蒸馏步骤b(图3a))与根据本发明的方法(图3b))(在实施方案中表示为alt2)的性能,显示了本发明的优点。模拟移动床(smb)分离步骤a该实施例考虑545t/h的c8馏分(2),其获自二甲苯塔并且包含源自重整产物、源自烷基转移单元和源自一个或多个异构化单元的c8芳族化合物。所述馏分的组成按重量%给出:c8-0.4%eb4.1%px23.0%mx50.1%ox22.3%c9+0.1%c8-馏分对应于包含少于8个碳原子的化合物。将该c8a馏分送至模拟移动床吸附单元a,该单元a包括通过原料和解吸剂(b4)的注入以及提余液(a21,a22)和提取物(a1)的取出界定的五个区域。所述模拟床吸附单元由18个床组成,所述床含有钡交换沸石x,分布如下:¡区域1中3个床,在解吸剂(b4)的注入和提取物(a1)的取出之间¡区域2中6个床,在提取物(a1)的取出和原料的注入之间¡区域3a中4个床,在原料的注入和提余液(a21)的取出之间¡区域3b中3个床,在提余液(a21)的取出和提余液(a22)的取出之间¡区域4中2个床,在提余液(a22)的取出和解吸剂(b4)的注入之间温度为175°c。使用的解吸剂是对二乙苯,解吸剂相对于原料的含量是1.2(体积/体积)。因此,实施smb分离步骤a可以获得三个进料至蒸馏步骤b、表示为(a1)、(a21)和(a22)的物流。这三个物流具有如下特征:-提取物(a1),其含有原料的至少97.0%的对二甲苯px和一部分的解吸剂;将所述馏分送入提取塔中,以在塔顶回收纯px并在塔底回收解吸剂-508t/h的贫含px、富含乙苯的第一提余液(a21),其含有总提余液b2+b31中所含的98.0%的乙苯eb和总提余液b2+b31中所含的78.0%的二甲苯-320t/h的贫含px的第二提余液(a22),其主要含有mx和ox的混合物(其c8a馏分中的eb含量为0.5%)以及另一部分的解吸剂。根据现有技术实施通过蒸馏分馏的步骤b(图3a)在该实施方案中,在第27个理论塔板处将含有解吸剂的第一提余液(a21)进料到蒸馏塔(b-c2)中,所述塔包括47个理论塔板、冷凝器和再沸器、在0.2mpa下以1.1的回流比操作。在塔顶回收不含解吸剂的第一提余液(b2)并将其送入在气相中操作的第一异构化步骤。将含有解吸剂的第二提余液(a22)送入分离步骤b中。在第21个理论塔板处将所述提余液进料到塔(b-c4)中,所述塔包括47个理论塔板、冷凝器和再沸器、在0.2mpa下以2.7的回流比操作。在馏出物中回收不含解吸剂的第二提余液(b3)并将其送入在液相中操作的异构化步骤d。在吸附所需的温度下进行热交换步骤之后,将从两个提余液塔(b-c2和b-c4)的塔底获得的两个不含c8a的解吸剂物流b42和解吸剂物流b43混合并送入模拟移动床分离步骤。通过模拟移动床产生的两个提余液(a21)和(a22)的分馏步骤b需要81.2gcal/h的再沸能量。根据本发明实施通过蒸馏分馏的步骤b(图3b,alt2)在根据本发明的一个实施方案(alt2)中,在第20个理论塔板处将含有解吸剂的第一提余液(a21)进料到三馏分蒸馏塔(b-c3)中,所述塔包括47个理论塔板、冷凝器和再沸器、在0.2mpa下以1.38的回流比操作。所述塔可以产生三个物流:-284t/h的第一塔顶提余液(b2),其含有总提余液b2+b31的90.1%的乙苯含量,-从第27个理论塔板以液相取出的73.6t/h的第二馏分(b3),其含有残余的乙苯和总提余液b2+b31的12%的二甲苯以及解吸剂,和-150.6t/h的含有解吸剂、不含c8a化合物的塔底产物b42。在第18个塔板处将含有解吸剂的提余液(b3)引入第二蒸馏塔(b-c4)中,所述塔包括47个理论塔板、冷凝器和再沸器、在0.2mpa下以2.1的回流比操作。将获自模拟移动床分离步骤a的第二提余液(a22)送入蒸馏步骤b中。在该蒸馏塔(b-c4)的第24个塔板处引入所述提余液(a22)。在塔顶回收137t/h的提余液(b31)。所述提余液(b31)不含解吸剂、包含mx、ox、贫含px且具有1.6重量%的eb含量。将提余液(b31)送入在液相中操作的异构化步骤d。在吸附所需的温度下进行热交换之后,将从两个提余液塔(b-c3和b-c4)获得的两个解吸剂物流b42和解吸剂物流b43混合并送入模拟移动床。两个提余液(a21)和(a22)的分馏需要84.5gcal/h的再沸能量。根据现有技术(图3a)或根据本发明(图3b)的提余液分离步骤b的性能总结如下:现有技术本发明alt2图3a)图3b)dr(eb)98.0%90.2%dr(xyl)78.0%66.1%总q再沸(gcal/h)81.284.5提余液塔b-c2的塔板数47-(三馏分)提余液塔b-c3的塔板数-47第二提余液塔b-c4的塔板数4747该实施例说明了当吸附步骤a产生两个提余液时本发明的优点。通过将蒸馏步骤和吸附步骤相连接,可以实现比现有技术中描述的分离更好的eb/xyl分离,但是不会对设备的数量或再沸所需的能量产生影响。根据本发明的分离步骤b需要使用与第二蒸馏塔相连的第一三馏分蒸馏塔。如实施例4中所示,相对于现有技术,可以增加芳族环路的px收率。实施例3:该实施例通过详细说明图1中所示的二甲苯环路的性能来显示本发明的优点,所述二甲苯环路包括:-仅产生一个提余液a2的吸附步骤a,-将提余液分馏的步骤b,和-两个异构化步骤c和d。为了充分理解本发明的优点,根据现有技术,或者根据本发明以实施例1中所述的变型alt0和alt1实施分离步骤b。eb回收率(表示为dr(eb))设定为90.0%,二甲苯回收率(表示为dr(xyl))为90.0%、87.0%和82.0%。所述二甲苯环路进料有具有100t/h的流量的c8+馏分(物流1,图1),该馏分源自含有68t/h的c8a馏分的重整产物,其质量组成如下:eb16.7%px18.0%mx41.0%ox24.3%在第15个理论塔板处将所述馏分c8a(物流1,图1)与来自两个异构化步骤c和d的再循环流出物(c1,d1)一起引入包括72个塔板、采用1.8的回流比操作的二甲苯塔中,可以在塔顶处回收馏出物中99.8%的c8a并从模拟移动床分离单元px的原料(物流2,图1)中除去c9+。将所述馏分c8a送入模拟移动床分离步骤a中,从而产生富含px和解吸剂的提取物a1和贫含px且含有解吸剂的提余液a2。如实施例1所述,将提取物a1和提余液a2送入包括若干个蒸馏塔的分馏步骤b。这可以将解吸剂再循环到吸附步骤a中,并且产生纯度为99.8%的px和两个提余液,一个富含eb(b2),另一个贫含eb(b3或b31),如实施例1所述并在图2a、图2b、图2c中图示说明。在第一异构化步骤c中将与再循环氢气混合的提余液(b2)进料到乙苯转化单元中,该单元在以下条件下操作:压力:0.9mpa,温度:376℃,h2/hc比=4:1,催化剂:含铂和eu-1沸石,空速:5h-1。在这些条件下,eb转化率为28.9%(现有技术);29.3%(根据本发明,alt0变型);29.9%(根据本发明,alt1变型),c8a损失为1.8重量%,px接近92.0%的平衡,ox接近87.0%的平衡。在反应器的出口处,一系列分离可以产生送至反应器入口的主要含有氢气、甲苯以及链烷烃和环烷烃馏分的气体(c2)。将流出物的最重质的部分(c1)再循环到二甲苯塔的入口(图1)。在第二异构化步骤d中将提余液(b3)进料到二甲苯异构化单元中,该单元在以下条件下操作:温度240℃,压力1.8mpa,空速2.5h-1,具有含zsm-5型沸石的催化剂。在这些条件下,eb转化率为3.4%,px接近94.5%的平衡。将来自反应区的流出物(d1)再循环到二甲苯塔中(图1)。如此描述的二甲苯环路的物料平衡总结在下表中:该实施例说明了本发明的优点,其可以增加二甲苯环路的产量,所述二甲苯环路包括两个异构化,具有产生两个流出物的模拟移动床,在分馏步骤b中使用第一三馏分蒸馏塔。分馏步骤b的能量消耗不受影响。基于px平均价格1500$/t($/吨)估算的px产量增益为1.3mm$/y(百万美元/年)(对于alt0变型而言)和3.3mm$/y(对于alt1变型而言)并证明与分馏步骤b的改变相关的边际投资的合理性。实施例4:该实施例通过详细说明图1中所示的二甲苯环路的性能显示了本发明的优点,所述二甲苯环路包括产生两个提余液a21和a22的吸附步骤a、提余液分馏步骤b和两个异构化步骤c和d。为了说明本发明的优点,根据现有技术或根据实施例2中描述的变型alt2实施分离步骤b。因此,经由根据现有技术的方法获得的eb回收率dr(eb)和二甲苯回收率dr(xyl)分别为98.0%和78.0%,而根据本发明方法的变型alt2,回收率分别为90.0%和66%。所述二甲苯环路进料有100t/h的c8+馏分(物流1,图1),该馏分源自含有68t/h的c8a馏分的重整产物,其质量组成如下:eb16.7%px18.0%mx41.0%ox24.3%在第15个理论塔板处将所述c8a馏分(物流1,图1)与来自两个异构化步骤的再循环流出物一起引入包括72个塔板、采用1.8的回流比操作的二甲苯塔中,可以在塔顶处回收馏出物中99.8%的c8芳族化合物并从模拟移动床分离单元px的原料(物流2,图1)中除去c9+。将所述c8a馏分进料到模拟移动床中,从而产生富含px和解吸剂的提取物a1和贫含px且含有解吸剂的两个提余液a21和a22。如实施例1所述,将提取物和提余液送入包括若干个精馏塔的分离步骤b。将由此分离出的解吸剂(b4)再循环到吸附步骤a中。所述步骤b可以产生纯度为99.8%的对二甲苯和两个提余液,其富含eb(b2)或贫含eb(b3或b31),如实施例2所述并在图3a和图3b中图示说明。在第一异构化步骤c中将与再循环氢气混合的提余液b2进料到乙苯转化单元中,该单元在以下条件下操作:压力:0.9mpa,温度:376℃,h2/hc比=4:1,催化剂:含铂和eu-1沸石,空速:5h-1。在这些条件下,eb转化率为30.6%(现有技术);32.1%(本发明,alt2变型),c8a损失为1.8重量%,px接近92%的平衡,ox接近87%的平衡。在反应器的出口处,一系列分离可以产生送至反应器入口的主要含有氢气、甲苯以及链烷烃和环烷烃馏分的气体c2。将异构产物的最重质的部分(c1)再循环到二甲苯塔的入口。在第二异构化步骤d中将提余液b3进料到二甲苯异构化单元中,该单元在以下条件下操作:温度240℃,压力1.8mpa,空速2.5h-1,具有含zsm-5型沸石的催化剂。在这些条件下,eb转化率为3.4%,px接近94.5%的平衡。将来自反应区的流出物(d1)再循环到二甲苯塔中。二甲苯环路的物料平衡总结在下表中:这些结果清楚地说明,根据本发明的方法可以通过采用产生三个流出物的模拟移动床、在分离步骤b中使用第一三馏分蒸馏塔(如实施例1所述)来增加二甲苯环路的对二甲苯收率。有利地,根据本发明的方法的这种特定实施方案对设备的数量或能量消耗没有影响。基于平均px成本1500$/t的估计增益为3.4mm$/y。实施例5:在称为alt3的具体变型中,所述方法使用与实施例4的变型alt2(图3b)相同的设备和相同的二甲苯环路的构造来进行。该实施例说明了当希望由相同的原料获得非常高收率的px时本发明的优点,伴随有异构化催化剂和分子筛的边际增加。吸附步骤a的操作参数与实施例4相同,但修改了提余液分馏步骤b的操作参数,从而使得来自第一蒸馏塔b-c3的富含eb的提余液b2的流量降低,以使进料至第二蒸馏塔b-c4的侧线取出b3的流量增加及其导致馏出物(b31)的流量增加。在该实施方案中,分馏步骤b的新性能品质使得dr(eb)=60%且dr(xyl)=38%。然后将所述提余液b2送入异构化步骤c中。该实施方案可以通过具有最小c8a损失的催化剂来增加二甲苯异构化的比例,并最终增加px的收率。由于异构化步骤d中的每遍次的eb转化率低,因此eb再循环的程度增加,这具有增加其固定浓度的效果。此后,由热力学平衡控制的第一气相异构化中的每遍次的eb转化率也增加并达到36.5%。有利地,根据本发明的两个异构化步骤的组合可以在产能增加方面具有小的折衷的情况下实现高px产量。如此描述的二甲苯环路的物料平衡总结在下表中:当前第1页1 2 3