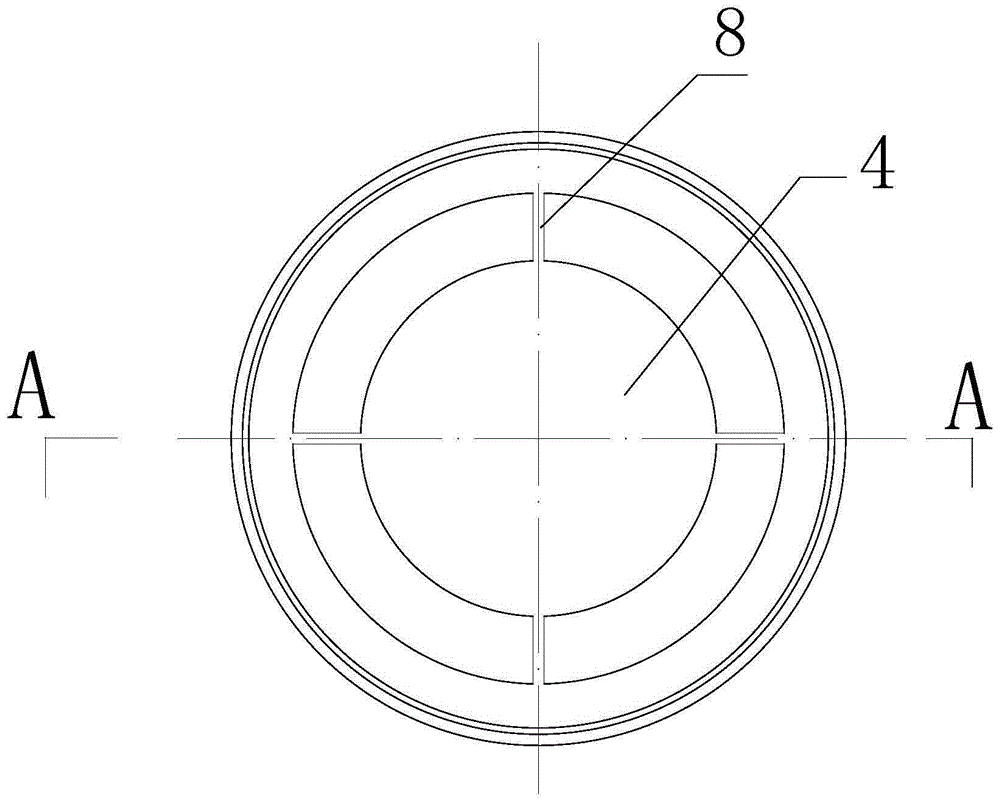
本发明创造属于非均相的反应
技术领域:
,尤其是涉及一种用于非均相的反应系统及应用该系统的反应工艺。
背景技术:
:非均相反应的反应物是两相或两相以上的组分(固体和气体、固体和液体、两种互不混溶的液体),或者一种或多种反应物在界面上(如固体催化剂表面上)进行的化学反应。烯烃的水合反应,是己内酰胺绿色化生产的核心步骤之一,是制约整个流程产能的关键步骤。由于该反应是液液固三相反应,因此反应时间受传质速率的影响很大,究其原因,环己烯水合反应时分子筛固体催化的环己烯和水的液液固反应,传质大大影响了反应的速率;目前环己烯水合制环己醇工艺流程为两反应釜串联,环己烯和高纯水从第一反应釜进料,溢流堰分离出的油相进入第二反应釜,进一步反应后进塔精制分离,总反应停留时间为25-40分钟,较长的停留时间使反应器体积过大;转化率一般为8%~9%,过低的转化率使后续的环己烯和环己醇分离的能耗过高。cn102180772b对水合工艺进行了优化,利用分离的环己烯作为萃取剂萃取分离出的水相中的环己醇,很大程度上避免了溶解有环己醇的水相直接返回反应体系,使单程转化率提高了1.5-2%。然而,作为萃取剂的环己烯分离后需要重新进行分离精制,加大了后续分离塔的分离能力,提高了分离成本,同时对转化率的提高有限。cn101805244b公开了一种环己烯水合工艺,使用wo3/zro2固体超强酸作为催化剂,在固定床反应器中进行水合反应;反应物料在催化剂床层停留30s-60s,环己烯转化率即可达到9.5-10.3%;但是其反应温度在200-300℃,反应压力为15-35mpa,超高的反应压力对反应器要求极高,加大了设备投资、检修成本,不利于工业化生产实践。技术实现要素:有鉴于此,本发明创造旨在提出一种用于非均相的反应系统及应用该系统的反应工艺,以克服现有技术的不足,较大程度的缩短反应时间,且保证反应的高转化率和选择性。为达到上述目的,本发明创造的技术方案是这样实现的:一种用于非均相的反应系统,包括依次通过管道连接的混合装置、反应器和分离器,其中混合装置的进口通过管道连接原料罐;分离器与混合装置之间设有循环管道,分离器与后序工序设备通过管道连接,且混合装置为一过式;且在管道上设有驱动反应物质在各装置之间流动的动力装置;优选的,混合装置在1~20s内实现油水混合乳化。优选的,动力装置为循环泵,循环泵设置在分离器与混合装置之间的循环管道上;或动力装置为气体源,气体源和混合器与反应器之间的管道连通。优选的,所述混合装置为一套或两套,当混合装置为两套时,分离器分别与两套混合装置通过循环管道连接,且循环管道上均设有循环泵;一套混合装置包括一个或两个以上的混合器;分离器与混合装置之间设置中间处理装置。优选的,当动力装置为循环泵时,分离器与两套混合装置分别连通的管道上均设有循环泵。本发明创造给出一种新的反应系统以及工艺思路,通过增加混合装置,在混合装置能够实现在短时间内较高水油比的充分混合,且与催化剂充分接触,实现在反应器内快速混合反应,且由于催化剂也在混合器与原料进行混合,接触更为充分。在该前提下,反应器可以不设置搅拌装置,仅仅是提供相应的反应环境即可。且整体反应的停留时间较短,较大程度增加了生产效率。当动力装置为气体源时,由持续通入的气相作为环流的驱动源;粉末状原料/催化剂打浆后进入反应系统;气相通过混合器进入反应器;反应体系加热,升温到达反应温度后,在气相持续喷入的前提下,液相原料通过混合器与浆料混合,进入反应器发生反应,反应后混合物进入油水分离器进行分离,连续相再次进入反应器。通过调节原料进量和气相通量,可以实现气液比和水油比的调节,可以显著提高原料转化率,产物的选择性;催化剂可在线再生,不需要停工,反应时间大大缩短,可大大提高装置的产能。气相可以是其中的一个反应物,也可以是对反应物惰性的气体。当动力装置为循环泵时,靠循环泵实现物料的循环。分离器部分油相产品可直接进入原料混合器进入反应器或进入在反应器合适位置另外设置的混合器进入反应器进行二次反应,进一步提高原料的转化率。本发明提供的反应系统,不仅仅局限于以下所述的混合器,只要混合装置能够实现快速混合,就可以适用上述反应系统,优选的,混合器,包括若干混合单元,所述混合单元包括分散单元和集中单元;所述分散单元包括挡水板,且挡水板通过支架与分散单元的内壁连接,分散单元的内壁为曲面,挡水板为内凹的球面结构;所述集中单元包括漏斗形通道,所述漏斗形通道的侧壁为曲面,且内径从上到下逐渐变小;所述漏斗形通道的下方设有内凹的挡水面;且挡水板的开口与漏斗形通道的底端位置相互对应。优选的,当分散单元与集中单元连接时,分散单元曲面内壁与其上方设置的集中单元上的挡水面平滑过渡相接,且分散单元曲面内壁与其下方设置集中单元的漏斗形通道的侧壁平滑过渡相接。平滑过渡保证液体的流畅性,且同时避免混合器中出现死角。优选的,所述漏斗形通道的底端与挡水板的中心对齐。保证水流对挡水板冲击的平衡性,避免挡水板因不平衡造成损坏。所述挡水板的纵截面为劣弧,且最低点留泪空;挡水板的高度与分散单元曲面内壁的高度相同,为h1;分散单元曲面内壁的内径逐渐缩小,且最低端内径为r1,且h1为r1的10%~30%。分散单元曲面内壁位于挡水板的顶面以下,且挡水板顶端与分散单元曲面内壁的顶端持平,两者之间设置的开口的面积为该平面上分散单元曲面内壁所在圆周面积的30%~90%。优选的,集中单元上漏斗形通道的底端内径r2为顶部内径r3的5%-30%。优选的,挡水面的纵截面呈圆弧状,且靠近r2部分有少量突出,突出部分h3的高度不超过分散单元的挡水板高度h1的1/2;分散单元曲面内壁的高度h1与集中单元的漏斗形通道的高度h2的比值是1:5-1:1。合理的设置各部件的尺寸,保证混合的效果,且同时保证混合器返修率降低。优选的,相邻的分散单元与集中单元之间的侧壁通过螺纹连接;每个混合器由3-50组混合单元组成。分散单元与集中单元也可以采用其他方式连接,只要保证连接后,具有稳定性,且同时内部的结构符合本发明创造中的相关要求就可,再次不再一一列举。其中螺纹连接的方式,是分别在集中单元与分散单元设置内螺纹或外螺纹,使相邻的两个单元之间可以相互配合即可,不需要特别限定内螺纹或外螺纹与集中单元或分散单元的设置的位置关系。根据反应需要可以调节相应的混合单元的组数。上述的混合器,集中单元通过漏斗形通道的侧壁的曲面设置,提高通过液体的返混程度,同时通过漏斗形通道的内径不断缩小,使液体不断加速,并与分散单元的挡水板撞击,形成强湍流场,经过与挡水板的撞击,会有部分液体再次反弹到挡水面上,进行再次撞击混合;通过增加重复单元,该过程不停重复,可高效的将油水或液相与固体浆料混合;该混合器结构简单,混合器内无混合死区,安装、检修方便,可通过增加或减少混合单元来控制混合效果;同时该混合器在允许的条件下也可直接作为反应器。优选的,设置在顶端的分散单元上方连接进口单元,且进口单元上设有进口管,进口管的数量为2~5个。本发明同时提供如上所述的非均相的反应系统在用于液液或液液固、或含气相的非均相反应中的应用,优选的,在烯烃水合反应工艺中的应用;或在苯加氢或环己烯水合反应工艺中的应用。本发明也提供一种利用如上所述的用于非均相的反应系统进行烯烃水合反应工艺,烯烃为含5-12个碳原子的有或没有取代基的链状或环状烯烃,优选的,烯烃为5~7元烯烃,优选的,烯烃为环己烯、环庚烯、己烯中的一种或两种以上;固体催化剂为分子筛类催化剂或负载类催化剂固体超强酸;优选的,分子筛类催化剂为zsm-5;负载类催化剂固体超强酸为氧化锆做载体超强酸催化剂;反应器中的水油比为1~2000,优选的,水油比为50~500;催化剂固含量为1%-40%;反应温度为80℃-200℃,反应压力0mpag-2.5mpag。优选的,烯烃为环己烯,催化剂为hzsm-5;催化剂固含量为23%,循环泵流量为160l/h;环己烯进料泵流量为36~60ml/min,水油比为45~74:1,反应压力为0.55~0.65mpa,反应温度为120~130℃,停留时间为45s。本发明也提供一种利用如上所述的用于非均相的反应系统进行加氢反应工艺,加氢反应为苯加氢反应,催化剂为负载类催化剂或金属加氢催化剂;反应的水油比在1~200范围内;催化剂固含为1%-40%,反应温度为80℃-200℃,反应压力0mpag-10mpag。相对于现有技术,本发明创造所述的一种用于非均相的反应系统及应用该系统的反应工艺,具有以下优势:反应原料经混合器混合后进入反应器,反应后的产物经过分离器分离取出(根据实际反应产物的密度来决定产物相在油水分离器的位置;如产物为环己烯/环己醇,则产物在分离器的上层,水相催化剂在下层,反之则相反),催化剂相可直接或经过再生等中间处理后通过循环泵返回至混合器,与原料重新混合;为进一步提高转化率,产品相可分出一部分重新进入另一混合器进行二次反应;本系统可用于加氢反应、烯烃水合反应、氯丙烯与双氧水制备环氧氯丙烷等非均相反应,可实现在催化剂催化下与水在高水油比,高转化率和选择性的发生反应,同时大大缩短了反应时间,有着很好的工业化前景。附图说明构成本发明创造的一部分的附图用来提供对本发明创造的进一步理解,本发明创造的示意性实施例及其说明用于解释本发明创造,并不构成对本发明创造的不当限定。在附图中:图1为本发明创造实施例所述的分散单元的俯视图;图2为图1中的a-a向的剖视图;图3为本发明创造实施例所述的集中单元的俯视图;图4为图3中的a-a向的剖视图;图5为进口单元的剖视图;图6为混合单元的剖视图;图7为多个混合单元连接成混合器后的剖视图;图8为非均相反应系统(动力装置为循环泵)的简单示意图;图9为非均相反应系统(动力装置为气体源)的简单示意图。附图标记说明:1、分散单元;2、集中单元;3、进口单元;4、挡水板;5、分散单元曲面内壁;6、进口管;7、漏斗形通道;8、支架;9、挡水面;10、原料罐;11、混合装置;12、反应器;13、分离器;14、后序工序设备;15、中间处理装置;16、循环泵;17、气体源。具体实施方式需要说明的是,在不冲突的情况下,本发明创造中的实施例及实施例中的特征可以相互组合。在本发明创造的描述中,需要理解的是,术语“中心”、“纵向”、“横向”、“上”、“下”、“前”、“后”、“左”、“右”、“竖直”、“水平”、“顶”、“底”、“内”、“外”等指示的方位或位置关系为基于附图所示的方位或位置关系,仅是为了便于描述本发明创造和简化描述,而不是指示或暗示所指的装置或元件必须具有特定的方位、以特定的方位构造和操作,因此不能理解为对本发明创造的限制。此外,术语“第一”、“第二”等仅用于描述目的,而不能理解为指示或暗示相对重要性或者隐含指明所指示的技术特征的数量。由此,限定有“第一”、“第二”等的特征可以明示或者隐含地包括一个或者更多个该特征。在本发明创造的描述中,除非另有说明,“多个”的含义是两个或两个以上。在本发明创造的描述中,需要说明的是,除非另有明确的规定和限定,术语“安装”、“相连”、“连接”应做广义理解,例如,可以是固定连接,也可以是可拆卸连接,或一体地连接;可以是机械连接,也可以是电连接;可以是直接相连,也可以通过中间媒介间接相连,可以是两个元件内部的连通。对于本领域的普通技术人员而言,可以通过具体情况理解上述术语在本发明创造中的具体含义。下面将参考附图并结合实施例来详细说明本发明创造。如图1~图9所示,一种用于液液或液液固非均相的反应系统,包括依次通过管道连接的混合装置11、反应器12和分离器13,其中混合装置11的进口通过管道连接原料罐10;分离器13与混合装置11之间设有循环管道,该管道上设有循环泵16,分离器13与后序工序14的反应装置通过管道连接。且在管道上设有驱动反应物质在各装置之间流动的动力装置。所述混合装置为一套或两套,当混合装置为两套时,分离器分别与两套混合装置通过循环管道连接;一套混合装置包括一个或两个以上的混合器;分离器与混合装置之间设置中间处理装置。动力装置为循环泵16,循环泵16设置在分离器13与混合装置11之间的循环管道上;或动力装置为气体源,气体源和混合器与反应器之间的管道连通。所述混合器,包括若干混合单元,所述混合单元包括分散单元1和集中单元2;所述分散单元1包括挡水板4,且挡水板4通过支架8与分散单元1的内壁连接,分散单元1的内壁为曲面,挡水板4为内凹的球面结构;所述集中单元2包括漏斗形通道7,所述漏斗形通道7的侧壁为曲面,且内径从上到下逐渐变小;所述漏斗形通道7的下方设有内凹的挡水面9;且挡水板4的开口与漏斗形通道7的底端位置相互对应。当分散单元1与集中单元2连接时,分散单元曲面内壁5与其上方设置的集中单元2上的挡水面9平滑过渡相接,且分散单元曲面内壁5与其下方设置集中单元2的漏斗形通道7的侧壁平滑过渡相接。所述漏斗形通道7的底端与挡水板4的中心对齐;所述挡水板4的纵截面为劣弧,且最低点留泪空;挡水板4的高度与分散单元曲面内壁5的高度相同,为h1;分散单元曲面内壁5的内径逐渐缩小,且最低端内径为r1,且h1为r1的10%~30%;分散单元曲面内壁5位于挡水板4的顶面以下,且挡水板4顶端与分散单元曲面内壁5的顶端持平,两者之间设置的开口的面积为该平面上分散单元曲面内壁所在圆周面积的30%~90%。集中单元2上漏斗形通道7的底端内径r2为顶部内径r3的1%-30%;挡水面9的纵截面呈圆弧状,且靠近r2部分有突出,突出部分h3的高度不超过分散单元的挡水板4高度h1的1/2;分散单元曲面内壁5的高度h1与集中单元2的漏斗形通道7的高度h2的比值是1:5-1:1;相邻的分散单元1与集中单元2之间的侧壁通过螺纹连接;每个混合器由3-50组混合单元组成;设置在顶端的分散单元1上方连接进口单元3,且进口单元3上设有进口管6,进口管6的数量跟原料罐的数量对应。尺寸编号r3h1r1h2s%r2h3r4尺寸/mm3015252060%4313以下实施例中,每个混合装置为一套混合器,且一套混合器由8组混合单元组成。且实施例1~4,以及对比例1、2中,动力装置均为循环泵。实施例5~6以及对比例3中,动力装置为气体源。实施例1本实施例使用催化剂为tcc-042-01,主要成分为hzsm-5;烯烃选择为环己烯,反应条件为:催化剂固含量23%,循环泵流量160l/h;催化剂直接返回,未做再生等中间处理;环己烯进料泵流量36ml/min,轻相不返回;水油比74:1;反应压力0.58,反应温度123.5℃;平均停留时间:45s;反应结果为:转化率12.33%,选择性99.87%。实施例2本实施例使用催化剂为tcc-042-01,主要成分为hzsm-5;烯烃选择为环己烯,反应条件为:催化剂固含量23%,循环泵流量160l/h;催化剂直接返回,未做再生等中间处理;环己烯进料泵流量60ml/min,轻相不返回;水油比45:1;反应压力0.61mpa,反应温度125.2℃;停留时间45s;反应结果为:转化率11.28%,选择性99.85%。实施例3本实施例使用催化剂为tcc-042-01,主要成分为hzsm-5;烯烃选择为环己烯,未新增混合器,油相返混直接返回至原料混合器;反应条件为:催化剂固含量23%,循环泵流量160l/h;催化剂直接返回,未做再生等中间处理;环己烯进料泵流量36ml/min;油水分离器上层油相的20%通过循环泵2重新返回至混合器,返混比例为4:1;水油比74:1;反应压力0.58mpa,反应温度123.5℃;停留时间:45s;反应结果为:转化率13.65%,选择性99.65%。对比例1本对比例使用催化剂为tcc-042-01,主要成分为hzsm-5;烯烃选择为环己烯,使用反应釜进行对比实验,反应条件为:催化剂固含量23%,搅拌桨为推进式搅拌桨,线速度3m/s,反应温度125℃,反应釜升温110℃开始计时,反应时间30min;水油比2:1,反应压力0.60mpa;反应结果:转化率9.64%,选择性99.79%。实施例4本实施例使用催化剂为tcc-042-02,主要成分为hzsm-5;烯烃选择为异戊烯,反应条件为:催化剂固含量10%,循环泵流量80l/h;催化剂直接返回,未做再生等中间处理;异戊烯进料泵流量36ml/min,油水分离器上层油相的20%通过循环泵2重新返回至混合器,返混比例为4:1;轻相返混比例为20:1,停留时间90s;水油比74:1;反应压力0.58-0.72mpa,反应温度80℃;反应结果为:转化率29.87%。对比例2本对比例使用催化剂为tcc-042-02,主要成分为hzsm-5;烯烃选择为异戊烯,使用反应釜进行对比实验,反应条件为:催化剂固含量10%,搅拌桨为推进式搅拌桨,线速度3m/s,反应温度80℃,反应釜升温75℃开始计时,反应时间1h;水油比2:1,反应压力0.60-0.70mpa;反应结果:转化率28.30%。实施例5本实施例使用催化剂为tcc-121-03,催化剂总固含控制在5%-8%;反应压力4~4.5mpa,反应温度150℃;氢气作为环流动力和反应原料,苯进料量为40ml/min,氢气流量为0.4nm3/h;反应器体积3l,无返混;催化剂直接返回,未做再生等中间处理;反应结果为:转化率42.3%,选择性81.5%。实施例6本实施例使用催化剂为tcc-121-03,催化剂总固含控制在5%-8%;反应压力4~4.5mpa,反应温度150℃;氢气作为环流动力和反应原料,苯进料量为40ml/min,氢气流量为0.4nm3/h;反应器体积3l,反应液返混比例20:1;催化剂直接返回,未做再生等中间处理;反应结果为:转化率53.1%,选择性79.6%。对比例3本对比例使用催化剂为tcc-121-03,反应压力4~4.5mpa,釜式反应器,搅拌桨为两个推进式搅拌桨,线速度~4m/s;反应时间30min,取样结果为:转化率42.1%,选择性80.2%。实验条件转化率/%选择性/%实施例5无返混42.3%81.5%实施例6返混20:146.1%79.6%对比例3釜式反应器42.1%80.2%以上所述仅为本发明创造的较佳实施例而已,并不用以限制本发明创造,凡在本发明创造的精神和原则之内,所作的任何修改、等同替换、改进等,均应包含在本发明创造的保护范围之内。当前第1页12