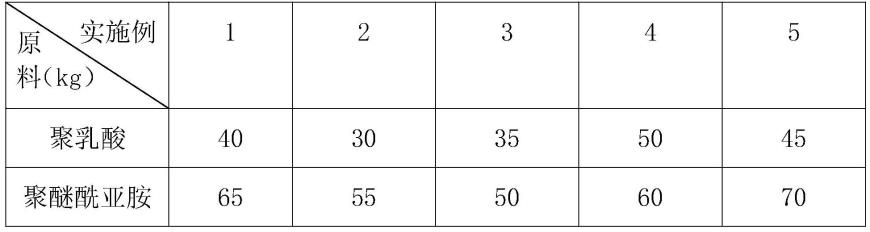
1.本技术涉及汽车内饰件技术领域,更具体地说,它涉及一种轻型高强度新能源汽车左后座椅靠背支架塑胶件及其制备方法。
背景技术:2.随着人们对日常便捷出行需求的增长,汽车的需求量也随之增长,已经达到了较为普及的现状。同时随着人们环保理念的提高,新能源汽车也逐渐被广大民众所接受。
3.汽车内饰是除汽车性能外较受人关注的部分,而为了迎合消费者的消费倾向,大部分汽车厂家对汽车内饰的打造投入也逐渐变大。其中汽车座椅靠背支架通常是用塑胶材料制成,在具有较好肤感的同时还可以起到扶手、储物的作用。作为汽车内饰件之一,该支架对耐高温性能的需求也是必要的。
4.相关技术中通过将无机填料与尼龙树脂共混后挤出的方式制备具有耐高温性能的支架。虽然在一定程度上可以利用无机填料来提高支架的耐高温性能,但是由于无机填料与尼龙树脂的结合效果较差;且无机填料在尼龙树脂体系中的分散效果也较差,容易导致支架各部分的耐高温性能差异较大。
技术实现要素:5.为了改善这一缺陷,即提高无机填料在体系中的分散及结合效果,进而提高支架塑胶件耐高温性能的均匀度,本技术提供一种轻型高强度新能源汽车左后座椅靠背支架塑胶件及其制备方法。
6.第一方面,本技术提供一种轻型高强度新能源汽车左后座椅靠背支架塑胶件,采用如下的技术方案:一种轻型高强度新能源汽车左后座椅靠背支架塑胶件,包括以下质量份的原料:聚乳酸30~50份、聚醚酰亚胺50~70份、季铵化聚乙烯亚胺10~20份、改性无机填料3~10份、其他助剂1~5份;所述改性无机填料是无机填料经过阴离子表面活性剂湿磨后得到。
7.通过采用上述技术方案,聚乳酸和聚醚酰亚胺作为塑胶体系的主要基材,其中聚乳酸是一种绿色高分子材料,且具有较好的耐热性能、手感、耐菌性能、阻燃性能和抗紫外性能,与其他组分的相容性较好。而聚醚酰亚胺同样具备较好的耐高温性能,同时耐磨性、结构稳定性和阻燃性较好。两者复合效果较好,同时季铵化聚乙烯亚胺与两者均具有较好的结合效果,且季铵化聚乙烯亚胺由于季铵基团的存在,使得其整体表现为较为稳定的正电荷,且季铵基团的存在对其其他性能的消极影响较小。同时无机填料在与阴离子表面活性剂湿磨后,所得到的改性无机填料表面会吸附较多的阴离子,即使得改性无机填料表现为带负电荷。因此改性无机填料与聚乳酸-聚醚酰亚胺-季铵化聚乙烯亚胺共混过程中,在正负电荷的相互吸引作用下,改性无机填料可以较为稳定且均匀地分散并结合在体系中。从而制备得到的支架塑胶件具有较为优异且均匀的耐高温性能,同时该支架塑料件的其他
性能也较为优异。
8.作为优选,所述季铵化聚乙烯亚胺的制备方法包括以下步骤:1)在聚乙烯亚胺水溶液中采用滴加的方式加入环氧丙烷,搅拌反应,反应结束后升温蒸出未反应的环氧丙烷,得到混合液;2)混合氯化苄和混合液,静置分层后取上层液进行萃取,得到季铵化聚乙烯亚胺溶液,干燥后得到季铵化聚乙烯亚胺成品。
9.通过采用上述技术方案,制备工艺较为简便,实用及工业化生产前景好。
10.作为优选,所述改性无机填料包括改性氧化钙、改性二氧化硅、改性氧化锌中的至少一种。
11.通过采用上述技术方案,由于氧化钙、二氧化硅和氧化锌在于阴离子表面活性剂湿磨过程中均能够较好的吸附阴离子,且三者添加至塑胶体系中可以有效改善体系的耐高温性能,且在体系中的分散均匀度较高,有助于提高制得支架塑胶件耐高温性能的均匀度。
12.作为优选,所述改性无机填料的粒径为50~100μm。
13.通过采用上述技术方案,粒径为50~100μm的改性无机填料在体系中的分散效果较好,且不易出现团聚的现象,对提高支架塑胶件耐高温性能的均匀度具有积极意义。
14.作为优选,所述改性无机填料的制备方法包括以下步骤:混合搅拌无机填料与阴离子表面活性剂,得到混合物;然后湿磨混合物,干燥后制得改性无机填料。
15.通过采用上述技术方案,在无机填料与阴离子表面活性剂共混湿磨后,可以使得无机填料表面负载有较为稳定的阴离子,即得到的改性无机填料带有负电荷。因此在正负电荷的相互吸引作用下,改性无机填料可以较为均匀地分散在聚乳酸-聚醚酰亚胺-季铵化聚乙烯亚胺体系中,且结合力较强,从而有助于提高制得的支架塑胶件耐高温性能的均匀度。
16.作为优选,所述阴离子表面活性剂包括聚丙烯酰胺、十二烷基苯磺酸钠、脂肪醇硫酸酯盐中的至少一种。
17.作为优选,所述其他助剂为抗老化剂和增塑剂按照质量比1:(3~5)组成的混合物。
18.通过采用上述技术方案,添加抗老化剂有助于延长支架塑胶件的使用寿命;而增塑剂可以有效提高支架塑胶件的塑性,即有助于提高支架塑胶件的柔性和强度。
19.作为优选,所述抗老化剂为紫外吸收剂和抗氧剂按照质量比1:1组成的混合物。
20.通过采用上述技术方案,以紫外吸收剂和抗氧剂作为抗老化剂的有效成分,可以有效减少支架塑胶件的光老化和氧老化的情况,有助于延长支架塑胶件的使用寿命。
21.作为优选,所述增塑剂为聚乙二醇,且所述聚乙二醇的相对分子质量mn=(10.1~16.5)kg/mol。
22.通过采用上述技术方案,小分子量的聚乙二醇与聚乳酸-聚醚酰亚胺-季铵化聚乙烯亚胺具有较好的相容性,且可以有效提高制得的支架塑胶件的柔性和强度。同时相对分子质量mn=(10.1~16.5)kg/mol的聚乙二醇在与体系具有较好相容性的前提下,其在体系中的迁移速率会降低,从而可以有效减少因聚乙二醇迁移到表面而导致材料老化的情况。
23.第二方面,本技术提供一种轻型高强度新能源汽车左后座椅靠背支架塑胶件的制备方法,采用如下的技术方案。
24.一种轻型高强度新能源汽车左后座椅靠背支架塑胶件的制备方法,包括以下步骤:混料:混合聚乳酸、聚醚酰亚胺、季铵化聚乙烯亚胺、改性无机填料和其他助剂,得到混合料;熔融挤出:熔融挤出混合料,并通过模具定型得到成品。
25.综上所述,本技术具有以下有益效果:1、本技术以聚乳酸和聚醚酰亚胺作为塑胶件主要基材,并通过季铵化聚乙烯亚胺使得体系中聚乳酸-聚醚酰亚胺-季铵化聚乙烯亚胺的结合力较强,同时季铵化聚乙烯亚胺因季铵基团的存在而带有正电荷,无机填料与阴离子表面活性剂湿磨后得到的改性无机填料表面带有负电荷;因此在共混过程中,在正负电荷的相互吸引作用下,改性无机填料可以较为均匀且稳定地分散并结合在聚乳酸-聚醚酰亚胺-季铵化聚乙烯亚胺中,从而使得制得的支架塑胶件具有较为优异且均匀的耐高温性能。
26.2、本技术通过添加控制改性无机填料的粒径为50~100μm,可以有效提高改性无机填料在体系中的分散效果,且团聚现象较少。
27.3、本技术通过小分子量聚乙二醇提高聚乳酸-聚醚酰亚胺-季铵化聚乙烯亚胺的柔性和强度,且进一步控制聚乙二醇相对分子质量mn=(10.1~16.5)kg/mol,可以有效减少因聚乙二醇迁移至表面而导致材料抗老化性能下降的情况。
具体实施方式
28.以下结合实施例和对比例对本技术作进一步详细说明,本技术涉及的原料均可通过市售获得,其中聚乳酸产自后亿国际贸易(上海)有限公司,货号为6252d;聚醚酰亚胺产自上海辉晟达塑胶有限公司,货号为2100-7301-1000;聚乙烯亚胺产自上海尤恩化工有限公司,货号为un0001254。实施例
29.实施例1~5以下以实施例1为例进行说明。
30.实施例1一种轻型高强度新能源汽车左后座椅靠背支架塑胶件,包括以下质量的原料:聚乳酸40kg、聚醚酰亚胺65kg、季铵化聚乙烯亚胺15kg、改性无机填料5kg、其他助剂3kg;其中改性无机填料是粒径为50~100μm的二氧化硅经过阴离子表面活性剂(十二烷基苯磺酸钠)湿磨后得到,具体的制备方法如下:混合5kg二氧化硅和3kg阴离子表面活性剂,得到混合物;然后湿磨混合物20min,70℃下干燥30min后得到改性无机填料;季铵化聚乙烯亚胺的具体制备方法如下:1)在10kg聚乙烯亚胺水溶液中采用滴加的方式加入1kg环氧丙烷,在10℃的温度下搅拌反应30min,反应结束后升温至40℃蒸出未反应的环氧丙烷,得到混合液;2)混合氯化苄和混合液,静置分层后取上层液用乙醚进行萃取,得到季铵化聚乙烯亚胺溶液,50℃下真空干燥后得到季铵化聚乙烯亚胺成品。
31.其他助剂为抗老化剂和增塑剂按照质量比1:5组成的混合物,且抗老化剂为紫外吸收剂和抗氧剂按照质量比1:1组成的混合物,紫外吸收剂为uv-531,抗氧剂为受阻胺类衍生物;增塑剂为聚乙二醇,且聚乙二醇的相对分子质量mn=16.5kg/mol。
32.该轻型高强度新能源汽车左后座椅靠背支架塑胶件的制备方法包括以下步骤:混合搅拌聚乳酸、聚醚酰亚胺、季铵化聚乙烯亚胺、改性无机填料和其他助剂,得到混合料;然后在挤出机中混合熔融混合料,并利用模具定型制得成品塑胶件。
33.如表1所示,实施例1~5的区别之处主要在于原料配比不同。
34.表1原料配比表表1原料配比表实施例6本实施例与实施例1的区别之处在于,改性无机填料为改性氧化钙。
35.实施例7本实施例与实施例1的区别之处在于,改性无机填料的粒径为200~300μm。
36.实施例8本实施例与实施例1的区别之处在于,增塑剂为聚乙二醇,且聚乙二醇的相对分子质量mn=10.1kg/mol。
37.实施例9本实施例与实施例1的区别之处在于,增塑剂为聚乙二醇,且聚乙二醇的相对分子质量mn=5.3kg/mol。
38.实施例10本实施例与实施例1的区别之处在于,增塑剂为聚乙二醇,且聚乙二醇的相对分子质量mn=35.2kg/mol。
39.实施例11本实施例与实施例1的区别之处在于,增塑剂为邻苯二甲酸二(2-乙基己)酯。
40.对比例对比例1本对比例与实施例1的区别之处在于,不添加聚乳酸,用等量的聚醚酰亚胺补足。
41.对比例2
本对比例与实施例1的区别之处在于,不添加聚醚酰亚胺。用等量的聚乳酸补足。
42.对比例3本对比例与实施例1的区别之处在于,不添加季铵化聚乙烯亚胺,用等量的聚醚酰亚胺补足。
43.对比例4本对比例与实施例1的区别之处在于,用等量的聚乙烯亚胺替换季铵化聚乙烯亚胺。
44.对比例5本对比例与实施例1的区别之处在于,用等量的二氧化硅替换改性二氧化硅。
45.对比例6本对比例与实施例1的区别之处在于,不添加改性无机填料,并用聚乳酸补足。
46.对比例7一种耐高温尼龙汽车内饰件,包括以下质量的原料:尼龙树脂100kg、无机填料10kg、偶联剂1.5kg、抗氧剂1kg和竹纤维2kg;其中无机填料为贝壳粉,且粒径为1~3μm;偶联剂为硅烷偶联剂kh-560。
47.该耐高温尼龙汽车内饰件的制备方法为:首先混合尼龙树脂、无机填料、偶联剂、抗氧剂和竹纤维,得到混合料;然后在挤出机中混合熔融混合料,然后通过双螺杆挤出机在260℃的条件下利用模具直接成型,制得成品内饰件。
48.性能检测试验方法耐极限高温性能试验:将各实施例和对比例中的样品均一分为三,尽量保证每份样品大小形状一致,每个实施例和对比例中的三份样品分别标号1、2、3。并参照q_jlyj7110192b-2016《汽车内外饰塑料件耐温性能试验规范》中耐极限高温性能测试方法对实施例1~11和对比例1~7中的支架塑胶件(内饰件)的三份样品进行试验,记录各标号样品的极限温度。
49.拉伸强度:参照gb1040-92《塑料拉伸性能试验方法》中的测试方法对实施例1~11和对比例1~7中的支架塑胶件(内饰件)进行试验。
50.表2检测数据表
通过表2的检测数据,结合实施例1~5和对比例7的检测数据来看,本技术中的支架塑胶件不仅耐高温性能和拉伸强度较为优异,而且同一个支架塑胶件中的三个样品所能承受的极限温度差距较小,即耐高温性能的均匀度较好。
51.结合实施例1和实施例6的检测数据来看,无机填料选用改性二氧化硅比改性氧化钙的耐高温性能优异,且分散均匀度更高。
52.结合实施例1和实施例8~10的检测数据来看,聚乙二醇的分子量对样品的耐高温性能存在一定影响,且原则上相对分子质量越高越不容易出现聚乙二醇迁移至表面而影响抗老化性能,但是相对分子质量过高对样品的拉伸强度具有较为明显的消极影响,可能是因为相对分子质量过高的聚乙二醇与体系的相容性会变差,从而对样品的拉伸强度造成消极影响。
53.结合实施例1和对比例1~2的检测数据来看,聚乳酸与聚醚酰亚胺复合使用不仅耐高温性能得到较为明显的提升,且拉伸强度也有较为明显的改善。
54.结合实施例1和对比例3~5的检测数据来看,聚乙烯亚胺自身因其较好的结合效果和吸附效果,可以在一定程度上提高无机填料的分散均匀度,且对各组分的结合效果具有一定的积极意义,在拉伸强度上可以得到验证。同时季铵化聚乙烯亚胺与改性无机填料存在配合关系,即正负电荷的吸引作用有助于提高改性无机填料的分散均匀度。
55.本具体实施例仅仅是对本技术的解释,其并不是对本技术的限制,本领域技术人员在阅读完本说明书后可以根据需要对本实施例做出没有创造性贡献的修改,但只要在本技术的权利要求范围内都受到专利法的保护。