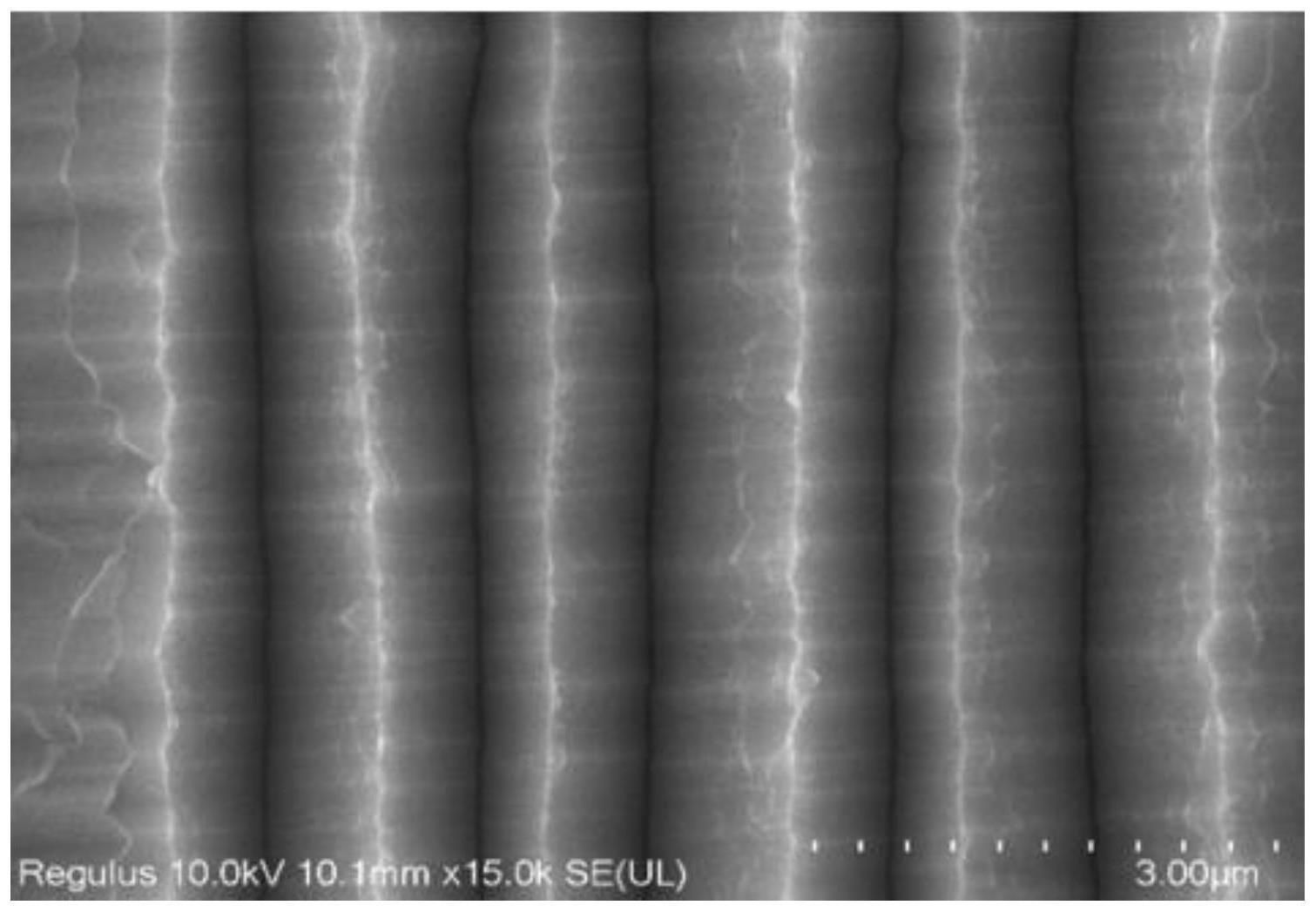
碱制绒液、晶体硅v型槽绒面结构及其制备方法
技术领域
1.本技术涉及太阳能电池生产技术领域,具体而言,涉及一种碱制绒液、晶体硅v型槽绒面结构及其制备方法。
背景技术:2.目前,工业上生产常用的制绒液通常会在硅片表面形成“金字塔”状绒面结构,尺寸一般在1-10μm之间,虽然这种绒面结构在太阳光垂直入射时具有较优异的减反性能,可以将硅片表面反射率降至10%左右,但是当光照条件发生变化时,尤其是光入射角度发生改变后,“金字塔”状的绒面结构就不再能继续行使良好的减反能力,通常反射率随角度改变迅速升高至30%,使得这种绒面结构的太阳能电池在实际应用中光利用率低,不能达到理论的光转换效率。
3.由于v型槽结构具有良好的全向性,即当入射的太阳光角度在较大的范围内变化时,v型槽结构的反射率始终可以保持在较低的范围内,可以在不同光照条件下实现良好的光吸收,因此,v型槽结构绒面是一种较为理想的太阳电池的绒面结构。然而,v型槽结构的常规制备方法为掩膜法,其制备过程较为复杂且成本较高,限制了上述结构在太阳能电池领域的应用和发展。
技术实现要素:4.本技术提供了一种碱制绒液、晶体硅绒面结构及其制备方法,其提供一种新的设计思路,采用碱制绒的方式制得具有准全向性的v型槽绒面结构,操作可控,便于工业化生产。
5.本技术的实施例是这样实现的:
6.在第一方面,本技术示例提供了一种碱制绒液,按质量百分比计,其包括:表面活性剂0.0001%-0.1%,含氯氧化剂0.001%-0.1%,强碱1%-20%,以及余量的水。
7.本技术提供的碱制绒液在实际应用于晶体硅绒面结构的制备过程中时,能够与特定的硅片配合,利用碱制绒的方式形成晶体硅v型槽绒面结构,并且上述各原料配比合理,有利于获得表面无毛刺且较为均匀分布的v型槽绒面结构。
8.本技术一些可选地实施例中,含氯氧化剂包括次氯酸盐、高氯酸盐、二氧化氯、次氯酸以及氯气中的至少一种。
9.本技术一些可选地实施例中,表面活性剂包括亚甲基双萘磺酸钠。
10.本技术一些可选地实施例中,强碱为氢氧化钾和氢氧化钠中的至少一种。
11.在第二方面,本技术示例提供了一种晶体硅v型槽绒面结构的制备方法,其包括:
12.获得表面具有非晶硅掩膜层的晶体硅。
13.其中,所述非晶硅掩膜层的厚度沿预设方向呈周期性变化,或者,所述非晶硅掩膜层由多个互相平行且沿所述预设方向间隔布置的条状非晶硅层构成。
14.采用上述碱制绒液对所述晶体硅进行制绒处理。
15.本技术提供的制备方法中,利用非晶硅掩膜层与上述碱制绒液的配合,有效制得v型绒面结构。
16.实际刻蚀过程中,当非晶硅掩膜层的厚度沿预设方向呈周期性变化时,碱制绒液会先刻蚀掉厚度较薄的非晶硅以暴露晶体硅,此时厚度较厚的非晶硅残留于晶体硅的表面且间隔布置,以此时残留的非晶硅为掩膜,利用非晶硅的碱刻蚀速率小于晶体硅的碱刻蚀速率,以及利用含氯氧化剂可进一步增加非晶硅与晶体硅在碱溶液中的刻蚀速率差异,使得被暴露的晶体硅先被强碱刻蚀,并且呈现出由悬挂键密度最小的(111)面,控制晶体硅的(111)面延伸、合并最终得到大小均匀、由(111)面组成的v型槽绒面结构,并且碱制绒液也将继续刻蚀厚度较厚的非晶硅以去除非晶硅。
17.当所述非晶硅掩膜层由多个互相平行且沿所述预设方向间隔布置的条状非晶硅层构成时,利用非晶硅的碱刻蚀速率小于晶体硅的碱刻蚀速率,以及利用含氯氧化剂可进一步增加非晶硅与晶体硅在碱溶液中的刻蚀速率差异,使得未被遮蔽的晶体硅先被强碱刻蚀,并且呈现出由悬挂键密度最小的(111)面,控制晶体硅的(111)面延伸、合并最终得到大小均匀、由(111)面组成的v型槽绒面结构,并且碱制绒液也将继续刻蚀并去除非晶硅。
18.也即是,上述制备方法可适用于对不同规格的晶体硅进行v型绒面结构制绒,满足工业化生产的目的。
19.本技术一些可选地实施例中,制绒处理的温度为60℃-80℃,制绒处理的时间为800s-1200s。
20.本技术一些可选地实施例中,所述非晶硅掩膜层由以下方法制得:
21.以加载应力≥12gpa的条件下切割晶体硅的表面以形成多个互相平行的线槽,所述线槽的内壁为非晶硅,所述加载应力的卸载速率≥3gpa/s。
22.本技术一些可选地实施例中,线槽采用金刚线切割所得。
23.在第三方面,本技术示例提供了一种晶体硅v型槽绒面结构,其由上述实施例提供的制备方法制得,v型槽绒面结构的槽壁由(111)面围成。
附图说明
24.为了更清楚地说明本技术实施例的技术方案,下面将对实施例中所需要使用的附图作简单地介绍,应当理解,以下附图仅示出了本技术的某些实施例,因此不应被看作是对范围的限定,对于本领域普通技术人员来讲,在不付出创造性劳动的前提下,还可以根据这些附图获得其他相关的附图。
25.图1为实施例以及对比例采用的p型金刚线切割单晶硅片的sem图;
26.图2为实施例1制得的绒面结构的sem图;
27.图3为实施例2制得的绒面结构的sem图;
28.图4为实施例3制得的绒面结构的sem图;
29.图5为实施例4制得的绒面结构的sem图;
30.图6为对比例1制得的绒面结构的sem图;
31.图7为对比例2制得的绒面结构的sem图;
32.图8为对比例3制得的绒面结构的sem图;
33.图9为实施例1以及对比例1制得的绒面结构的变角度反射率对比曲线图;
34.图10实施例1以及对比例1对应的电池的变角度外量子效率以及电池片的效率结果对比图。
具体实施方式
35.下面将结合实施例对本技术的实施方案进行详细描述,但是本领域技术人员将会理解,下列实施例仅用于说明本技术,而不应视为限制本技术的范围。实施例中未注明具体条件者,按照常规条件或制造商建议的条件进行。所用试剂或仪器未注明生产厂商者,均为可以通过市售购买获得的常规产品。
36.以下针对本技术实施例的碱制绒液、晶体硅v型槽绒面结构及其制备方法进行具体说明:
37.在第一方面,本技术示例提供了一种碱制绒液,按质量百分比计,其包括:表面活性剂0.0001%-0.1%,含氯氧化剂0.001%-0.1%,强碱1%-20%,以及余量的水。
38.本技术提供的碱制绒液在实际应用于晶体硅绒面结构的制备过程中时,能够与表面具有非晶硅掩膜层的晶体硅配合,利用含氯氧化剂增加非晶硅层与晶体硅在碱溶液中的刻蚀速率差异,从而实现以碱制绒的制备方式形成晶体硅v型槽绒面结构,并且上述各原料配比合理,有利于获得表面无毛刺且较为均匀分布的v型槽绒面结构。
39.可选地,含氯氧化剂包括次氯酸盐、高氯酸盐、二氧化氯、次氯酸以及氯气中的至少一种。
40.示例性地,含氯氧化剂可以为次氯酸盐、高氯酸盐、二氧化氯、次氯酸或氯气,也可以为次氯酸盐和高氯酸盐的混合物,或者为高氯酸盐、二氧化氯的混合物。需注意的是,当含氯氧化剂为上述原料中的至少两种的组合物时,其具体配合可根据实际的需求进行选择。
41.次氯酸盐、高氯酸盐均为水溶性盐,例如钠盐或钾盐等,在此不做限定。
42.表面活性剂可去除晶体硅表面脏污,不仅用于增加碱制绒液与晶体硅之间的浸润性,而且可降低水的表面张力,减缓腐蚀速率,制得的均匀分布的v型槽绒面结构。
43.可选地,表面活性剂包括亚甲基双萘磺酸钠。
44.亚甲基双萘磺酸钠不仅可改善碱制绒液与硅片表面的润湿性,而且可对强碱中的oh-离子向反应界面的输运过程具有缓冲作用,使得大批量刻蚀加工v型槽绒面结构时,强碱含量具有较宽的工艺窗口,有利于提高产品工艺加工质量的稳定性。
45.强碱具有强腐蚀性,用于刻蚀去除非晶硅,并且刻蚀晶体硅以形成绒面结构。
46.可选地,强碱为氢氧化钾和氢氧化钠中的至少一种。
47.需要说明的是,上述碱制绒液只需在开始配液的时候用搅拌棒搅拌使料液混合均匀即可,在制绒过程中,处于制绒槽内的碱制绒液不需要鼓泡或循环泵,可有效节约能耗。
48.在第二方面,本技术示例提供了一种晶体硅v型槽绒面结构的制备方法,其包括:
49.s1、获得表面具有非晶硅掩膜层的晶体硅。
50.其中,所述非晶硅掩膜层的厚度沿预设方向呈周期性变化,或者,所述非晶硅掩膜层由多个互相平行且沿所述预设方向间隔布置的条状非晶硅层构成。
51.非晶硅掩膜层的厚度沿预设方向呈周期性变化是指其厚度沿预设方向呈周期性的厚-薄变化,也即是当其被强碱刻蚀一定的时间后,较薄的非晶硅掩膜层会被刻蚀掉,暴
露晶体硅,此时厚度较厚的部分依然存在于晶体硅的表面作为掩膜,此时其相当于具有多个基本平行且沿所述预设方向间隔布置的条状非晶硅层。
52.上述表面具有非晶硅掩膜层的晶体硅可以采用在晶体硅的表面气相沉积非晶硅所得,也可以采用高加载力及快速卸载加载力的方式获得,在此不做限定,可根据实际的需求选择,并且上述表面具有非晶硅掩膜层的晶体硅可自行制备,也可以直接提出需求购买于厂家。
53.本技术一些可选地实施例中,所述非晶硅掩膜层由以下方法制得:
54.以加载应力≥12gpa的条件下切割晶体硅的表面以形成多个互相平行的线槽,所述线槽的内壁为非晶硅,所述加载应力的卸载速率≥3gpa/s。
55.采用上述加载应力以及快速的应力卸载,可在切割硅片时导致晶体硅的表面存在厚度呈周期性起伏的非晶硅层,也即是线槽。
56.本技术一些可选地实施例中,线槽采用金刚线切割所得。操作简单,制作效率高。
57.本技术一些可选地实施例中,各线槽的最大宽度为50nm-1μm,线槽的最大深度为50nm-1μm,任意相邻的两个线槽之间的最短间距为50nm-1μm。
58.s2、采用上述碱制绒液中对晶体硅进行制绒处理。
59.由于晶体硅的各个晶面的原子密度不同,导致不同晶面的表面悬挂键密度不同,即表面活性不同,故不同的晶面与强碱发生反应的速度不同,且该速度与表面悬挂键的密度成正相关。因此,当晶体硅在强碱溶液中被刻蚀后会呈现出由悬挂键密度最小的(111)面围成的绒面结构。
60.实际刻蚀过程中,当非晶硅掩膜层的厚度沿预设方向呈周期性变化时,碱制绒液会先刻蚀掉厚度较薄的非晶硅以暴露晶体硅,此时厚度较厚的非晶硅残留于晶体硅的表面且间隔布置,以此时残留的非晶硅为掩膜,利用非晶硅的碱刻蚀速率小于晶体硅的碱刻蚀速率,以及利用含氯氧化剂可进一步增加非晶硅与晶体硅在碱溶液中的刻蚀速率差异,使得被暴露的晶体硅先被强碱刻蚀,并且呈现出由悬挂键密度最小的(111)面,控制晶体硅的(111)面延伸、合并最终得到大小均匀、由(111)面组成的v型槽绒面结构,并且碱制绒液也将继续刻蚀厚度较厚的非晶硅以去除非晶硅,最终绒面结构无残留的非晶硅。
61.当所述非晶硅掩膜层由多个互相平行且沿所述预设方向间隔布置的条状非晶硅层构成时,利用非晶硅的碱刻蚀速率小于晶体硅的碱刻蚀速率,以及利用含氯氧化剂可进一步增加非晶硅与晶体硅在碱溶液中的刻蚀速率差异,使得未被遮蔽的晶体硅先被强碱刻蚀,并且呈现出由悬挂键密度最小的(111)面,控制晶体硅的(111)面延伸、合并最终得到大小均匀、由(111)面组成的v型槽绒面结构,并且碱制绒液也将继续刻蚀并去除非晶硅,最终绒面结构无残留的非晶硅。
62.可选地,制绒处理的温度为60℃-80℃,制绒处理的时间为800s-1200s。
63.上述温度和时间配合下,有利于获得外观均匀的v型槽绒面结构,温度过低,无法进行碱制绒,温度过高,制绒速率过快,不利于控制制绒形状,时间过短,制绒结构过小,时间过长,制绒外观差。
64.示例性地,制绒的温度为60℃、65℃、70℃、75℃、80℃等中的任一值或介于任意两个值之间。
65.示例性地,制绒的时间为800s、830s、850s、900s、930s、950s、1000s、1050s、1070s、
1100s、1150s、1200s等中的任一值或介于任意两个值之间。
66.在第三方面,本技术示例提供了一种晶体硅v型槽绒面结构,其由上述实施例提供的制备方法制得,v型槽绒面结构由(111)面围成。
67.上述晶体硅v型槽绒面结构性能相对传统“金字塔”绒面结构提高,具体表现为:(1)入射光沿所得绒面v型槽方向入射时,入射角度在0-75
°
变化时,反射率保持在17%以下,而“金字塔”绒面反射率最高超过30%;(1)入射光沿所得绒面v型槽方向入射时,入射角度在0-75
°
变化时,v型槽绒面结构硅电池外量子效率可保持在90%以上,而“金字塔”绒面硅电池外量子效率最高达到~80%;(2)v型槽绒面结构的少子寿命是传统“金字塔”绒面的1.4倍,最终v型槽绒面结构的硅电池全年发电量比同样规格的金字塔绒面结构的硅电池电池多2.68%。
68.以下结合实施例对本技术的碱制绒液、晶体硅v型槽绒面结构及其制备方法作进一步的详细描述。
69.以下实施例以及对比例中,p型金刚线切割单晶硅片均购买于于同一批次,其尺寸为158.75mm
×
158.75mm,电阻率为1~3ωcm,其扫描电镜图如图1所示,非晶硅掩膜层覆盖晶体硅的表面且厚度沿预设方向呈周期性变化,图1中所示的非晶硅掩膜层的较厚部分的厚度为260nm,较薄部分的厚度为46nm。
70.实施例1
71.(1)配置碱性制绒液,其中氢氧化钾质量百分含量为1.1%,亚甲基双萘磺酸钠质量百分含量为0.002%,次氯酸钠质量百分含量为0.06%,去离子水质量百分含量为98.838%。
72.(2)将p型金刚线切割单晶硅片浸入到制绒剂中进行制绒,制绒温度控制在70℃,制绒时间1080s,所得的绒面结构如图2所示为v型槽绒面结构。
73.所得的绒面结构中,v型槽宽度1-2μm,大小均匀,反射率为10.9%,制绒后的p型金刚线切割单晶硅片的厚度减薄5.3μm。
74.实施例2
75.(1)配置碱性制绒液,其中氢氧化钾质量百分含量为1.1%,亚甲基双萘磺酸钠质量百分含量为0.002%,次氯酸钠质量百分含量为0.06%,去离子水质量百分含量为98.838%。
76.(2)将p型金刚线切割单晶硅片浸入到制绒剂中进行制绒,制绒温度控制在68℃,制绒时间1200s,所得的绒面结构如图3所示为v型槽绒面结构。
77.所得的绒面结构中,v型槽宽度1-3μm,大小均匀,反射率为12.4%,制绒后的p型金刚线切割单晶硅片的厚度减薄4.2μm。
78.实施例3
79.(1)配置碱性制绒液,其中氢氧化钾质量百分含量为1.1%,亚甲基双萘磺酸钠质量百分含量为0.0016%,次氯酸钠质量百分含量为0.047%,去离子水质量百分含量为98.8514%。
80.(2)将p型金刚线切割单晶硅片浸入到制绒剂中进行制绒,制绒温度控制在72℃,制绒时间840s,所得的绒面结构如图4所示为v型槽绒面结构。
81.所得的绒面结构中,v型槽宽度2-3μm,大小均匀,反射率为12.1%,制绒后的p型金
刚线切割单晶硅片的厚度减薄5.1μm。
82.实施例4
83.(1)配置碱性制绒液,其中氢氧化钾质量百分含量为1.1%,亚甲基双萘磺酸钠质量百分含量为0.004%,次氯酸钠质量百分含量为0.1%,去离子水质量百分含量为98.796%。
84.(2)将p型金刚线切割单晶硅片浸入到制绒剂中进行制绒,制绒温度控制在70℃,制绒时间800s,所得的绒面结构如图5所示为v型槽绒面结构。
85.所得的绒面结构中,v型槽宽度1-2μm,大小均匀,反射率为10.9%,制绒后的p型金刚线切割单晶硅片的厚度减薄5.3μm。
86.对比例1
87.(1)配置碱性制绒液,其中氢氧化钾质量百分含量为1.1%,亚甲基双萘磺酸钠质量百分含量为0.004%,去离子水质量百分含量为98.896%。
88.(2)将p型金刚线切割单晶硅片浸入到制绒剂中进行制绒,制绒温度控制在70℃,制绒时间800s,所得的绒面结构如图6所示为金字塔绒面结构。金字塔绒面结构中金字塔宽度1-4μm,反射率为12.56%,制绒后的p型金刚线切割单晶硅片的厚度减薄4.2μm。
89.对比例2
90.(1)配置碱性制绒液,其中氢氧化钾质量百分含量为1.1%,亚甲基双萘磺酸钠质量百分含量为0.004%,去离子水质量百分含量为98.896%,双氧水质量百分比含量为0.1%。
91.(2)将p型金刚线切割单晶硅片浸入到制绒剂中进行制绒,制绒温度控制在70℃,制绒时间800s,所得的绒面结构如图7所示。
92.对比实施例1-4以及对比例1、2可知,含氯氧化剂对于制备获得v型槽绒面结构至关重要,不含或采用其他非含氯氧化剂均无法利用碱制绒的方式获得v型槽绒面结构。
93.对比例3
94.其与实施例1的区别仅在于:
95.配置碱性制绒液,其中氢氧化钾质量百分含量为1.1%,亚甲基双萘磺酸钠质量百分含量为0.002%,次氯酸钠质量百分含量为2%,去离子水质量百分含量为98.798%。
96.所得的绒面结构如图8所示,无法获得v型槽绒面结构。
97.试验例1
98.取实施例1制得的v型槽绒面结构的单晶硅片,以及对比例1金字塔绒面结构单晶硅片,测试沿v型槽方向、垂直v型槽方向以及“金字塔”入射角度变化时的反射率,结果如图9所示(v-grove表示v型槽绒面结构,pyramid表示金字塔绒面结构)。
99.根据图9,可以看出,入射光沿所得绒面v型槽方向入射时,入射角度在0-75
°
变化时,反射率保持在17%以下,而金字塔绒面结构反射率最高超过30%。也即是,v型槽绒面结构具有良好的陷光效果,相比于金字塔绒面结构可以更有效地增加硅片表面的光吸收。
100.试验例2
101.将实施例1以及对比例1制绒后的硅片制作为同样规格的perc电池,并测试电池的各项电学性能参数。电池的电学性能参数见表1。
102.结果如表1以及图10所示。表1中,voc为开路电压,jsc为短路电流密度,ff为填充
因子,eff为转换效率,图10中v-grove表示v型槽绒面结构,pyramid表示金字塔绒面结构。
103.表1电池性能
[0104] voc(mv)jsc(ma/cm2)ff(%)eff(%)对比例1668.139.9381.1221.64实施例1669.939.881.2721.67
[0105]
从表1中可以看出,与具有正金字塔绒面结构的太阳能电池相比,采用具有v型槽绒面结构的制绒片制备成的太阳能电池具有更高的开路电压和填充因子,太阳能电池的转换效率明显提升。
[0106]
根据图10,入射光沿所得绒面v型槽方向入射时,入射角度在0-75
°
变化时,v型槽绒面硅电池外量子效率保持在90%以上,而金字塔绒面硅电池外量子效率最高达到80%。
[0107]
实际使用过程中,v型槽绒面结构的少子寿命是传统金字塔绒面结构的1.4倍,最终v型槽绒面硅电池全年发电量比金字塔绒面硅电池多2.68%。
[0108]
综上,本技术提供的碱制绒液、晶体硅绒面结构及其制备方法,其提供一种新的设计思路,采用碱制绒的方式制得具有准全向性的v型槽绒面结构,操作可控,便于工业化生产。
[0109]
以上所述仅为本技术的具体实施例而已,并不用于限制本技术,对于本领域的技术人员来说,本技术可以有各种更改和变化。凡在本技术的精神和原则之内,所作的任何修改、等同替换、改进等,均应包含在本技术的保护范围之内。