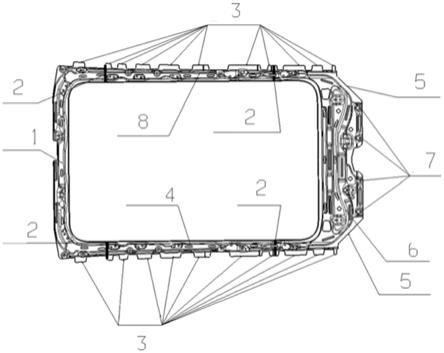
[0001]
本实用新型属于汽车车身技术领域,具体涉及一种汽车全景天窗加强环及车辆。
背景技术:[0002]
现有汽车全景天窗加强环具有分体式结构(如:cn206155114u公开的一种分件式汽车全景天窗加强环)和一体化结构(cn106080142a一种天窗加强环结构及车辆)。其中,分体式结构的汽车全景天窗加强环存在的问题是:加强环焊接精度保证度差,影响天窗加强环止口位置的密封性能;焊接点数量有限,固定强度较差;分件较多,工装模具等费用较大。一体式结构的汽车全景天窗加强环存在的问题是:材料利用率低,影响车身轻量化的提升,且成本较高。因此,有必要开发一种新的汽车全景天窗加强环及车辆。
技术实现要素:[0003]
本实用新型的目的是提供一种汽车全景天窗加强环及车辆,能提升坯料利用率,实现车身轻量化目标,提高制造成品率,降低零件成本。
[0004]
第一方面,本实用新型所述的一种汽车全景天窗加强环,由加强环前框梁、加强环后框梁、加强环左侧边框及加强环右侧边框通过拼焊而成,所述加强环左侧边框和加强环右侧边框的厚度均小于加强环前框梁和加强环后框梁的厚度。
[0005]
所述加强环后框梁上间隔设有四个用于与顶盖后横梁连接的安装孔,通过安装孔与顶盖后横梁固定连接成一体,增强了顶盖系统的强度和刚度;且所述加强环后框梁的左右两端部具有工艺切除角,在不降低性能的前提下,减少了零件的重量。
[0006]
所述加强环左侧边框和加强环右侧边框上均设有若干焊接边,通过焊接边与侧围总成连接固定,形成上车体结构框架,增设了焊接边的数量,增加了汽车全景天窗加强环的强度和刚度。
[0007]
第二方面,本实用新型所述的一种车辆,采用本实用新型所述的汽车全景天窗加强环。
[0008]
本实用新型具有以下优点:材料利用率提升了43%,重量降低了15.3%,成本降低了11.2%,白车身性能在设计目标范围之上,满足了新车型的技术、成本轻量化等要求,实现了降本增效。
附图说明
[0009]
图1为本实施例的结构示意图;
[0010]
图2为本实施例的使用状态图;
[0011]
其中:1、加强环前框梁,2、激光拼焊焊缝,3、焊接边,4、加强环左侧边框,5、工艺切除角,6、加强环后框梁,7、安装孔,8、加强环右侧边框,9、顶盖后横梁,10、汽车全景天窗加强环,11、顶盖前横梁,12、侧围。
具体实施方式
[0012]
下面结合附图对本实用新型作进一步说明。
[0013]
参见图1,本实施例中,一种汽车全景天窗加强环,由加强环前框梁1、加强环后框梁6、加强环左侧边框4及加强环右侧边框8通过拼焊而成,激光拼焊焊缝2把加强环前框梁1、加强环后框梁6、加强环右侧边框8和加强环左侧边框4固定在一起;该汽车全景天窗加强环10通过四块板子拼接而成,提升了材料的利用率。所述加强环左侧边框4和加强环右侧边框8的厚度均小于加强环前框梁1和加强环后框梁6的厚度,利用cae性能分析计算合理设置料厚分布,实现了车身轻量化设计。
[0014]
参见图1,本实施例中,所述加强环后框梁6上间隔设有四个用于与顶盖后横梁9连接的安装孔7,所述加强环后框梁6的左右两端部具有工艺切除角5,在不降低性能的前提下,减少了零件的重量。
[0015]
参见图1,所述加强环左侧边框4和加强环右侧边框8上均设有若干焊接边3,通过焊接边3与侧围12连接固定,形成上车体结构框架,通过增设焊接边3的数量,增加了汽车全景天窗加强环10的强度和刚度。
[0016]
参见图2,本实施例中,加强环前框梁1与顶盖前横梁11连接,加强环前框梁1作为顶盖前部一个横梁结构强度补充,增强了顶盖系统的结构刚度和强度,实现了天窗的前部安装、密封配合及承载功能。汽车全景天窗加强环10通过焊接边3与两侧围12连接固定,形成上车体结构框架。汽车全景天窗加强环10的加强环后框梁6通过安装孔7与顶盖后横梁9固定连接形成为一体,增强了顶盖系统的强度和刚度,达到了减重和降低车辆油耗的目的。
[0017]
本实施例所述的汽车全景天窗加强环10的材料利用率提升了43%,重量降低了15.3%,成本降低了11.2%,白车身性能在设计目标范围之上,满足了新车型的技术、成本轻量化等要求,实现了降本增效。
[0018]
本实施例中,一种车辆,采用本实施例中所述的汽车全景天窗加强环10。