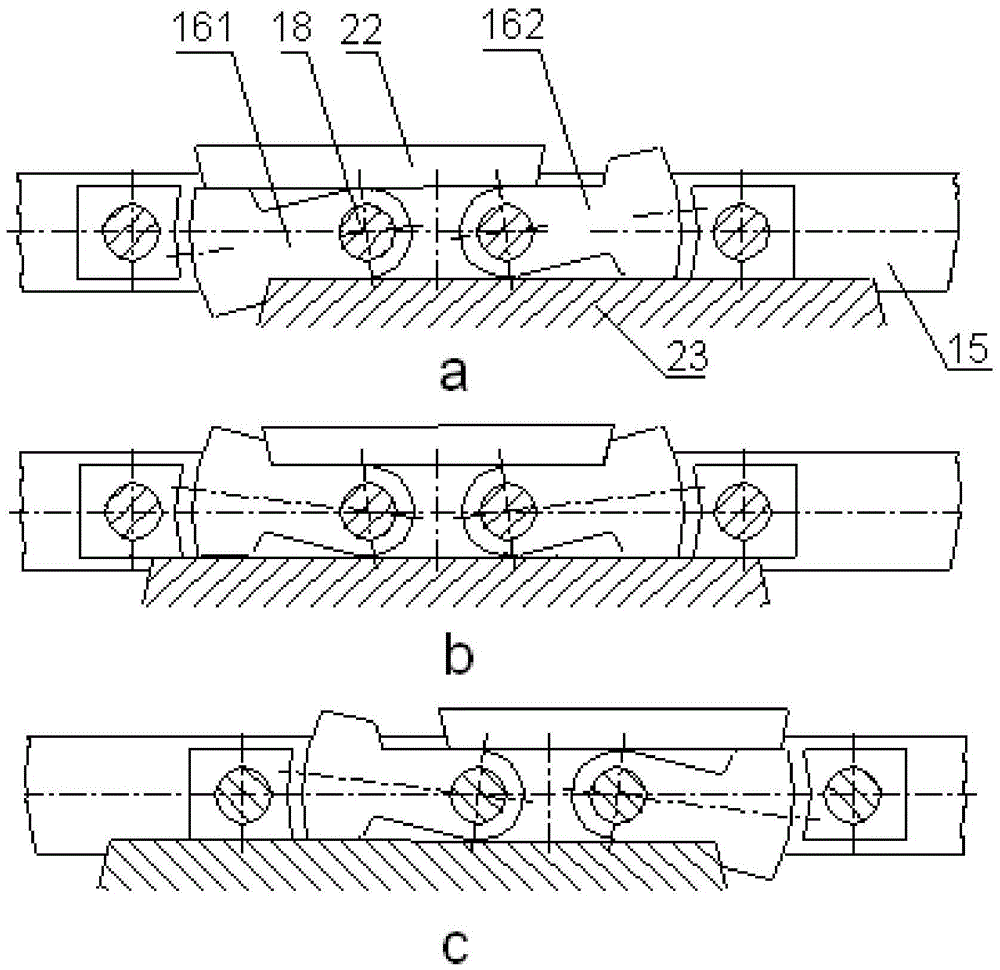
本发明涉及铁路技术领域,特别是涉及一种电动液压转辙机。
背景技术:随着铁路运输向重载、高速方向发展,对转辙机的可靠性要求越来越高。国内现有道岔转换设备主要有电动和电液两种制式的转辙机,其中,电动转辙机主要存在转换力输出不稳定、不易调整,机械磨损大,使用控制器材多、投资和耗能大等问题;而既有电液转辙机采用主付机方式牵引时存在转换同步性差等问题。因此,创设一种转换同步性好,既适合国内高密度、重载,同时又适合高速特点要求的新的电动液压转辙机,成为当前业界极需改进的目标。
技术实现要素:本发明的目的是提供一种电动液压转辙机,能够使多个转换单元实现同步转换,转换快速、同步性好,适用于各种铁路道岔尤其是高速铁路道岔的转换、锁闭、表示,适合国内铁路高密度、重载、高速的特点,从而克服现有电液转辙机存在转换同步性差的不足。为实现上述目的,本发明采用如下技术方案:一种电动液压转辙机,包括液压动力单元和多个转换单元,所述每个转换单元包括转换锁闭机构,所述转换锁闭机构包括油缸,所述多个转换单元的油缸串联连接且油缸容积相等,所述液压动力单元驱动所述多个油缸同步动作。进一步地,所述电动液压转辙机的液压系统为开式液压系统,所述液压动力单元包括油箱、油泵、连接并驱动油泵的电机,所述多个转换单元的油缸串联后与所述油泵连接。进一步地,所述油泵为双向油泵,所述互相串联的多个油缸中,位于端部的两个油缸分别通过第一、第二油路与所述油泵的第一、第二油口连接;所述第一、第二油路上分别对应连接有第一、第二液控单向阀,所述第一液控单向阀的液压控制口与第二油路连通,所述第二液控单向阀的液压控制口与第一油路连通,当所述液控单向阀的液压控制口通油时,该液控单向阀导通油液回流至油箱。进一步地,所述第一、第二油路上还设置有单向阀。进一步地,所述第一、第二油路的近油泵侧还连接有溢流阀。进一步地,所述第一油路的溢流阀支路与所述第二液控单向阀的液压控制口连通;所述第二油路的溢流阀支路与所述第一液控单向阀的液压控制口连通。进一步地,所述第一、第二油路上分别设置有压力传感器。进一步地,还包括与所述油箱连接的手动泵、与手动泵连接的手动换向阀、与手动换向阀连接的液压锁,所述液压锁的两个液控单向阀分别连接在所述第一、第二油路的近油缸侧。进一步地,所述油箱连接有回油滤油器。进一步地,所述油箱内设有液位传感器。进一步地,所述油泵为两个,且互相并联互为冗余。进一步地,所述每个油缸两端分别并联有两个溢流阀。进一步地,所述每个油缸两端并联有梭式平衡阀启动油缸。进一步地,所述每个油缸两侧分别设有滤芯。进一步地,所述转换锁闭机构还包括动作杆、锁块,所述动作杆上设有第一销孔,所述锁块通过与第一销孔配合的销轴安装在动作杆上;所述动作杆设有位于销轴一侧并垂直于销轴和动作杆的第二销孔,销轴一侧设有与第二销孔对应的凹槽,所述第二销孔与销轴的凹槽内设有防松销。进一步地,所述动作杆上还安装有加强板,所述加强板上开有与所述锁块形状配合的凹台,所述锁块在所述凹台与动作杆形成的框架内运动。进一步地,所述动作杆的中间部分具有配合所述锁块运动的平面。进一步地,所述动作杆两端安装有导向用圆孔套,所述圆孔套内嵌有与之同轴且内径相等的防尘圈。进一步地,所述圆孔套内还嵌有与之同轴且内径相等的耐磨环,所述耐磨环与防尘圈之间、沿圆孔套内壁开有环形储油槽,所述储油槽通过安装在圆孔套上的黄油嘴注油。进一步地,所述油缸的缸筒与缸座之间螺纹连接,所述缸筒及缸座的侧壁上开有对应的环形凹槽,所述环形凹槽内安装有钢丝挡圈。由于采用上述技术方案,本发明至少具有以下优点:1.由于采用了串联油缸,油缸等容积设计,多个油缸可共用一套动力单元,实现了多点同步转换,且转换快速、同步性好。2.液压系统采用开式系统,具有自净化功能,液压动力单元方便检修。3.采用体积小效率高的双向泵,双油泵时还可实现冗余功能。4.采用单向阀提高了液压系统的可靠性。5.采用液控单向阀克服动作机构到位反弹。6.液压动力单元设有溢流阀,每个油缸两端并联有溢流阀,可分别调整各自的输出力。7.设有手动液压机构,手动泵可替代电机油泵组输出动力带动各转换单元的油缸动作。通过手动液压机构使得单人即可完成多点牵引道岔的手动操作。8.油缸两端并联有梭式平衡阀启动缸,可平衡两腔压力、改善交流电机启动特性,启动缸体积加大,可满足多泵启动。9.油缸两侧分别安装吸油和回油滤芯,提高系统的清洁度,液压元件的可靠性提高,使用寿命延长。10.设有对主要参数进行监测的传感器,可对油箱液位、油路压力等进行监测,用于接收传感器信号的下位机具备微机监测接口条件,便于进行实时状态监测及数据采集与处理。11、所述动作杆与锁块之间设有防松销防止松动;所述动作杆中间部分设计成带有平面的形式,方便锁块安装并配合锁块运动。12、动作杆两端的圆孔套设置了防尘圈和耐磨环,并在两者之间进一步设有储油槽,分别起到了防尘、减少磨损、增加润滑的作用。13、油缸的缸筒与缸座之间连接处开有环形孔槽用于安装环形挡圈,防止油缸与缸座之间松动。附图说明上述仅是本发明技术方案的概述,为了能够更清楚了解本发明的技术手段,以下结合附图与具体实施方式对本发明作进一步的详细说明。图1为本发明电动液压转辙机的液压系统示意图。图2为转换锁闭机构解锁、转换、锁闭过程示意图。图3为本发明电动液压转辙机的动作杆、锁块、加强板连接示意图。图4为本发明电动液压转辙机的动作杆结构示意图。图5为本发明电动液压转辙机的圆孔套结构示意图。图6为本发明电动液压转辙机的缸座与缸筒机械防松结构示意图。图7为本发明电动液压转辙机的动作板与接点组滚轮间隙调整结构示意图。图8a是螺母接头的轴向剖视图;图8b、8c分别是图8a中AA向和BB向的剖视图。图9a、9b分别是调整螺母的俯视图和侧视图。图10是挡圈结构示意图。具体实施方式转辙机是铁路道岔转换的关键设备,用于各种铁路道岔的转换、锁闭、表示。电动液压转辙机采用液压传动,包括液压动力单元和转换单元,转换单元的作用是转换、锁闭并表示道岔状态,转换单元分可挤和不可挤型,不可挤转换单元一般用于多点牵引道岔的尖轨(心轨)的第一牵引点,可挤转换单元一般用于单点牵引道岔或多点牵引道岔除尖轨(心轨)第一牵引点外的其它牵引点。不可挤转换单元主要包括转换锁闭机构、锁闭表示机构、机械手动机构;转换锁闭机构主要由油缸组、动作杆组及锁闭铁等组成,其作用是转换并锁闭尖轨或心轨在终端位置;锁闭表示机构主要由接点组、锁闭杆等组成,其作用是正确反映尖轨或心轨状态并锁闭尖轨或心轨在密贴位置;机械手动机构主要由手动齿轮、齿条等组成,其作用是道岔安装调整或电路、油路系统故障时,人工扳动道岔。可挤转换单元主要包括转换锁闭机构、挤脱表示机构、机械手动机构;转换锁闭机构、机械手动机构作用及组成同不可挤转换单元,挤脱表示机构主要由挤脱接点组、表示杆(单点牵引时为锁闭表示杆)等组成,其作用是正确反映尖轨或心轨状态,并有挤岔断表示功能,单点牵引道岔锁闭表示杆还具有锁闭功能。本发明的电动液压转辙机,包括液压动力单元和多个转换单元,转换单元可以根据牵引点位置设置为上述不可挤转换单元或可挤转换单元。每个转换单元的转换锁闭机构通过油缸带动动作杆运动完成转换及锁闭动作。多个转换单元的的油缸串联连接且油缸容积相等,所述液压动力单元驱动所述多个油缸同步动作。通过各转换单元的油缸串联、等容积设计,实现转换单元的同步转换动作。请参阅图1所示,以转辙机具有三个转换单元为例,对应的三个油缸1依次串联连接,通过油路连接并传输液压动力,并共用一套液压动力单元。所述液压系统为开式液压系统,液压动力单元包括油箱、油泵3、电机2,电机2与油泵3之间通过联轴器连接。其中,所述电机2的机体优选采用高强度铝合金,以提高绝缘等级。油泵3及其连接件浸于油箱油内,减少了连接件,缩小了体积。进一步地,所述油泵3的吸油管路上可设置单向阀4和滤芯12,所述油箱前方可设置回油滤油器13,油箱内可设置液位传感器14。优选地,如图1中所示,所述油泵3为双向油泵,所述互相串联的多个油缸1中,位于端部的两个油缸1分别通过第一、第二油路与所述双向油泵3的两个油口连接;所述第一油路上连接有第一液控单向阀71,第二油路上连接有第二液控单向阀72,所述第一液控单向阀71的液压控制口与第二油路连通,所述第二液控单向阀72的液压控制口与第一油路连通。当某液控单向阀的液压控制口通油时,该液控单向阀导通油液回流至油箱。进一步地,所述第一、第二油路上还均设置有带有复位弹簧的单向阀5,用于增加油路系统的稳定性。所述第一、第二油路的近油泵侧均连接有溢流阀61,用于调整油路压力。在第一、第二油路上还均设置了压力传感器8,用于检测油路压力。所述第一油路的溢流阀的连接支路与所述第二液控单向阀72的液压控制口连通,所述第二油路的溢流阀的连接支路与所述第一液控单向阀71的液压控制口连通,用于对应双向泵双向输出时,所述第一和第二油路互为进油和出油油路。具体而言,以电机2向右旋转带动双向油泵3从左侧吸油时进行说明:油箱中的油液经滤芯12、单向阀4后被油泵3泵出,泵出的高压油通过第一油路进入第一个转换单元的进油口,该转换单元的出油口与下一个转换单元的进油口连接,同时由于液控单向阀72的液压控制口与溢流阀61连接第一油路的管路相连通,进油使得液控单向阀72被打开,末端转换单元的出油通过低压回油侧的液控单向阀72、回油滤油器13回到油箱;当高压油达到动力单元溢流阀61的设定值时溢流回到油箱。各转换单元的油缸1的两端分别并联两个溢流阀62,两个溢流阀62用于分别调定拉入或伸出最大转换力;每个油缸1的两侧均设有滤芯12,用于保证油路清洁。此外,每个油缸1两端还并联有梭式平衡阀启动缸11(可参见公开号为CN103615425A的专利文献),用于平衡两腔压力、改善交流电机启动特性。上述液压系统中,电机、联轴器、油泵构成油泵电机组,其作用是将电能转变为液压能;油管,单向阀,液控单向阀,滤芯、溢流阀及油箱等油路部件将液压能传输给转换单元。其中,油泵3还可进一步设置成互相并联互为冗余的双油泵。具体而言,可设置两台泵组分别由独立的电机、油泵和液压元件组成,通过管路、液控阀并联输出,两泵组同时工作驱动转换单元转换,当其中一泵组因故不能工作时,另一泵组的输出继续驱动转换单元工作,使道岔转换到位,仅转换时间延长(通过转换时间监测可获得故障信息)。除了前述机械手动机构可实现人工扳动道岔外,本发明的转辙机还进一步设置了液压手动机构,所述液压手动机构包括与所述油箱连接的手动泵9、与手动泵9连接的手动换向阀10、与手动换向阀10连接的液压锁,所述液压锁的两个液控单向阀分别连接在所述第一、第二油路的近油缸侧。液压手动机构还包括安全开关,用于实现可靠切断电机动作电源同时断开动力系统油路、接通手动油路,且非经人工恢复,不能接通电机动作电源和动力系统油路。安全开关设有定位装置,防止其正常工作时误动。一般状态下,液压手动机构的换向阀处于图1中所示的中间位,为常态位,当需要人工通过油路系统扳动道岔时,首先根据需要将安全开关置于所需位置,当手动油路接通,同时断开电机动作电源和动力系统油路后,人工手摇手动泵,使手动泵替代原油泵电机组输出动力,带动各转换单元动作。该手动机构输出高压油到转换单元,转换单元的回油通过液压锁中的液控单向阀回到油箱,完成手动转换。利用上述液压手动机构可实现单人即可完成多点牵引道岔的手动操作。本例中通过该机构单人可实现道岔三个牵引点之内的定反位操作。本发明的液压转辙机还设有监测系统,所述监测系统包括下位机以及相应的信息采集传感器,信息采集传感器包括但不限于所述油箱内设置的液位传感器14,所述第一、第二油路上分别设置的压力传感器8。如也可进一步设置采集设备对电流、动作时间、动作次数等参数进行监测,这些采集设备将检测数据传送到下位机,下位机具有微机接口条件,可连接上位机进行实时监测,实现查询历史数据,分析、诊断、提示功能,如提供道岔动作压力曲线等,从而为现场维护提供参考。请配合参阅图2所示,上述液压动力单元通过驱动每个转换单元的油缸带动动作杆运动完成转换及锁闭动作,以下对转换锁闭机构的动作原理做简要介绍:所述转换锁闭机构的动作杆15上通过销轴18安装有两个锁块,分别为定位锁块161和反位锁块162,动作杆15两侧分别为推杆22和锁闭铁23,推杆22固定在油缸1(图2中未示出)的侧方,油缸1的活塞杆固定不动。液压动力单元工作时,由于活塞杆固定不动,使油缸1向右动作,固定在油缸1侧方的推板22接触反位锁块162后(图2中a所示),油缸1继续向前移动时,通过推板22和反位锁块162带动动作杆15向右移动,同时定位锁块161开始解锁,当油缸1走完解锁动程后,反位锁块162和定位锁块161处于锁闭铁23和推板22的间隙内,油缸1继续通过推1板22和反位锁块162带动动作杆15向右移动(图2中b所示),当动作杆15继续移动到反位锁块162与锁闭铁23的锁闭面将要作用时,开始进入锁闭过程,继续向右移动15.2mm,将反位锁块162推入锁闭铁23的反位锁闭面,反位尖轨密贴于基本轨,此时,动作杆15的行程为7.6mm,(因此,在尖轨密贴时,动作杆15上的转换力可增加一倍,当尖轨密贴于基本轨后,油缸1继续向右移动,动作杆15不动作,推板22进入反位锁块162的锁闭面,进入锁闭状态(图2中c所示)。请配合参阅图3所示,反位锁块161通过销轴18安装在动作杆15上的第一销孔内,所述动作杆15还设有位于销轴18一侧并垂直于销轴18和动作杆15的第二销孔,销轴18一侧设有与第二销孔对应的凹槽,所述第二销孔与销轴18的凹槽内设有防松销19。所述动作杆15上还安装有加强板17,加强板17由螺钉20加上垫圈21固定于动作杆15上。所述加强板17上开有与所述反位锁块161形状配合的凹台,所述反位锁块161在所述凹台与动作杆15形成的框架内运动。定位锁块162(图3中未示出)的固定方式与反位锁块161相同。请参阅图4所示,本发明的液压动力转辙机所采用的动作杆15设计成如下形式:中间部分截面呈矩形,具有配合定位锁块162和反位锁块161运动的平面,便于锁块的导向和固定;两端部分截面为圆形,用于与下述圆孔套配合,便于防尘防水和润滑。圆孔套为动作杆或锁闭杆(表示杆)在转辙机内运动的导向定位装置,由于这些杆件为圆形设计,所以圆孔套的内孔为圆形。请参阅图5所示,本发明的液压动力转辙机所采用的圆孔套24内设有与之同轴且内径相等的防尘圈26。进一步地,所述圆孔套24内还设有与之同轴且内径相等的耐磨环27,具体地,防尘圈26及耐磨环27嵌合在圆孔套24内壁开设的环形凹槽中。在防尘圈26与耐磨环27之间、沿圆孔套内壁还开有环形储油槽,所述储油槽通过安装在圆孔套24上的黄油嘴25注油。圆孔套24优选采用耐磨自润滑粉末冶金材料制造。一般而言,转辙机中油缸1的缸筒与缸座之间采用螺纹连接,由于震动等原因会出现松脱的现象,造成漏油故障,因此,本发明的液压动力转辙机还设置了缸座与缸筒的机械防松结构,具体地,请参阅图6所示,在缸筒28及缸座30的侧壁上开有对应的环形凹槽,在所述环形凹槽内安装钢丝挡圈29。在缸座30上设有与环形凹槽相通的外部开口,缸筒28与缸座30两零件装配好后,钢丝挡圈29由开口处穿入环形凹槽内部,起到防松作用。请参阅图7所示,油缸1在转辙机转换单元中的横向位置是靠两侧(图中仅示出一侧)竖直设置的支撑板33来固定的,支撑板33上设有安装孔,油缸接头体32套装在油缸活塞杆31上,油缸活塞杆31端部为螺纹接头。本发明的转辙机在油缸1两端与支撑板33连接部位做了改进,使得动作板与接点组滚轮间隙可实现无级调整,调整精确,操作简便、快捷,克服了现有通过增减调整垫改变油缸的位置对所述间隙进行调整时,存在间隙无法全部吃掉和调整步骤繁琐的弊端。上述间隙调整通过改进螺母接头、增设调整螺母及挡圈来实现,具体而言,请参阅图7所示,改进后的调整结构包括螺母接头34、调整螺母35及挡圈36。请参阅图8a-8c所示,所述螺母接头34由具有内螺纹的端头41和具有外螺纹的螺杆组成,所述螺母接头4的螺杆为台阶式,包括第一台阶43、第一台阶43与所述端头41之间的第二台阶42,所述第二台阶42的直径大于第一台阶41,所述第二台阶42上开有轴向凹槽44。请参阅图9a、9b所示,所述调整螺母45包括具有内螺纹的环形侧壁,所述环形侧壁的一端设有径向外凸52,另一端沿其圆周均匀开设多个轴向缺口51。请参阅图10所示,所述挡圈36为环状结构,在挡圈36的内壁上设有齿状凸起63。请配合参阅图7,实际安装时,所述螺母接头34的一端用于连接所述活塞杆31的螺纹接头,所述螺母接头34的另一端依次套装调整螺母35、支撑板33和挡圈36。所述调整螺母35旋套在所述螺母接头34的第二台阶42上,且调整螺母35上的缺口51可分别与所述第二台阶42上的凹槽44位置相对形成叠加槽;调整螺母35的环形侧壁外径与所述支撑板33的安装孔内径相当,所述支撑板33通过安装孔套装在所述调整螺母35的环形侧壁上;所述挡圈36环套在所述调整螺母35的侧壁上,且其上的齿状凸起63嵌入所述叠加槽内;所述螺母接头34的第一台阶43穿过所述挡圈36并通过螺母37固定在支撑板33外侧。通过以上设置形式,所述调整螺母35通过在所述第二台阶42上旋进旋出调整位置,并通过将所述挡圈36的齿状凸起63嵌入所述叠加槽内锁定位置。作为优选的实施例,如图9a、9b中所示,所述调整螺母35的环形侧壁一端均匀开设六个轴向缺口51。所述调整螺母35采用公制螺纹规格为M24*2,所述轴向缺口51设置为宽8mm、深6mm,使得当所述调整螺母35上从一个轴向缺口旋至与之相邻的另一个轴向缺口位置,所述调整螺母35的轴向运动距离为1/3mm。即转辙机动作板与接点组滚轮间隙每次的最小调整距离为1/3mm,增加了调整精度。如果在同样规格的调整螺母35上进一步增加轴向缺口51的数量,则相邻轴向缺口51之间的旋转距离所能实现的轴向运动距离将更小,即进一步缩减了最小调整距离,增加了调整精度。以上设置使得在油缸1装入转换单元内部后,可通过调整螺母35顺或逆时针旋转来改变油缸1的位置,调整好后通过挡圈36上的齿状凸起63有效固定防松,从而使转辙机中的锁闭表示机构的接点组滚轮与动作板之间的间隙实现无级调整,且操作简便,调整精确,调整过程稳定且易于控制。综上所述,由于采用了以上技术方案,本发明电动液压转辙机的油路系统、转换系统、监测系统相比现有技术有如下特点:一、油路系统:1.油路系统设计了串联油缸,实现了同步转换。2.采用双向开式系统,具有自净化功能。3.安装吸油和回油滤芯,提高系统的清洁度,液压元件的可靠性提高,使用寿命延长。4.采用有复位弹簧的单向阀,提高了液压系统的可靠性。5.油路系统采用液控单向阀克服动作机构到位反弹。6.动力单元设有总溢流阀,每个转换单元设有带滤芯的溢流阀,可分别调整各自的输出力。7.动力单元设有独立的液压手动机构,提高了手摇效率,单人可完成多点牵引道岔手动操作。8.电机机体采用高强度铝合金,提高了绝缘等级。9.动力单元采用开放式设计,方便检修。10.油泵及其连接件浸于油内,减少了连接件,缩小了体积。11.油缸并联有梭式平衡阀启动缸平衡两腔压力、改善交流电机启动特性。启动缸体积加大,可满足多泵启动。12.采用体积小效率高的双向泵,双油泵时还可实现冗余功能。二、转换系统:1.用等容积串联油缸,实现各牵引点同步转换。2.不可挤转换单元具有双杆锁闭功能,用于单点牵引的可挤转换单元具有双杆锁闭和挤岔断表示功能。3.动作杆、锁闭杆(表示杆)采用圆柱形结构,锁闭杆(表示杆)还设置了防张口装置,即用一圆环将两分别动作的半圆型锁闭杆(表示杆)固定在一起构成一个圆形,但仍可保证其可顺着杆长度方向相对运动。4.圆孔套采用耐磨自润滑粉末冶金材料制造,设有储油槽,并装有导向环、防尘圈,减少了杆件与圆孔套之间的磨损,提高防尘防水性能。5.转换单元设有机械手动机构,方便现场安装调试,需要时,将溢流阀松开,可迅速进行转换和调整。6.油缸两端与支撑板连接部位结构改进,方便调整启动片、接点滚轮与油缸动作板间隙,实现无级调整,调整精确,调整过程稳定且易于控制,操作简便、快捷,并且调整结构上利用配合的挡圈实现有效防松。7.油缸缸座与缸筒间设有机械防松装置。8.转换单元动作杆与销轴间设有防松销,防止销轴退槽,加强板采用带有防松结构的螺钉固定。9.主要结构件采用高强度铝合金,减轻了自重,保证了强度,提高了防腐性能,方便了安装。10.接点设计了两种型号:一种是圆弧结构,另一种是密封SPX接点,该接点密封、免维护、耐震动高达230g。现场无需调整维护。三、监测系统可对油箱液位、压力、电流、动作时间、动作次数等参数进行监测,具备微机监测接口条件。通过微机监测可查询历史数据,提供道岔动作压力曲线;具有分析、诊断、提示功能,为现场维护提供参考。以上所述,仅是本发明的较佳实施例而已,并非对本发明作任何形式上的限制,本领域技术人员利用上述揭示的技术内容做出些许简单修改、等同变化或修饰,均落在本发明的保护范围内。