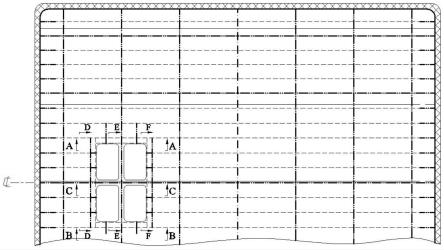
一种用于双燃料超大型集装箱船的b型lng燃料舱的气液组合穹顶结构
技术领域
1.本发明涉及船舶设计领域,特别是涉及一种用于双燃料超大型集装箱船的b型lng燃料舱的气液组合穹顶结构。
背景技术:2.常规的大型lng运输船的液货舱通常单舱舱容较大尺寸也较大,限于igc规范相关要求,通常需要设置一个气穹和一个液穹,考虑船舶艉倾状态较多,气穹通常需设置在靠舱前端的位置,而液穹设置在靠舱后端的位置,而b型lng燃料舱通常相对于大型lng运输船的液货舱来说舱容要小很多,其尺寸也相对较小,且集装箱船的lng燃料舱通常布置在上层建筑中岛的下方,受限于空间布置,不方便在舱靠前端再布置一个气穹,且因燃料舱长度不是太长,艉倾带来的倾斜角影响有限能满足igc规范的相关要求可考虑气穹后移至与液穹差不多的位置,因此就诞生了气液组合穹顶结构的概念。
3.因为b型舱是独立型的舱,所以组合穹顶的整体布置与结构型式需要结合b型舱本身的结构型式以及周边船体的结构型式进行综合考虑,气穹与液穹合二为一后其内部的穿舱管件数量较多,同时还要考虑布置人员和设备检修通道,因此怎样在有限的空间里进行合理的结构布置与设计是一项具有挑战性的关键技术。
技术实现要素:4.本发明的目的是在当前背景技术下考虑多重因素,设计出一种用于双燃料超大型集装箱船的b型lng燃料舱的气液组合穹顶结构。本发明结构要能够在有限的空间内实现检修通行要求,减少了冗余结构,提高建造效率。
5.为达到上述目的,本发明所采用的技术方案是:
6.一种用于双燃料超大型集装箱船的b型lng燃料舱的气液组合穹顶结构,所述气液组合穹顶结构位于b型lng燃料舱的顶部上方中央靠艉端的位置,其主体外围结构包括围壁和顶盖板,内部有水平布置的穿舱夹层和垂向的通道井壁结构,这些主体结构与b型lng燃料舱顶板焊接连接,整体坐落在b型lng燃料舱的顶部中纵桁和横向强框架组成的十字交叉状强结构上方。所述气液组合穹顶结构所有材料均为9ni钢,超低温性能极好。
7.作为优选地,所述围壁成方形,四个角都做成圆弧倒角型式,可有效防止焊缝应力集中降低产生裂纹的风险,所述围壁的前后两端壁在b型lng燃料舱顶板的反面设有肘板进行反面加强,围壁的两侧端壁的位置刚好对齐b型lng燃料舱顶部的纵骨。所述围壁和通道井壁上均设置有垂向加强筋,其中围壁上的垂向加强筋其末端做成肘板型式,通道井壁上的垂向加强筋其末端做成削斜型式,可加强围壁和通道井壁的承力能力。
8.作为优选地,所述顶盖板比围壁的范围整体大一圈,边缘四角也是圆弧倒角型式,所述顶盖板在通道井壁范围的位置设有人孔与吊物口复合型舱口及舱盖,方便人员检修与泵等设备的更换,所述顶盖板的边缘为下垂的环形t排结构,便于与船体构件之间安装固定
密封圈。
9.作为优选地,所述穿舱夹层位于顶盖板下方一定范围内,具体高度可根据实际状态进行调整,所述穿舱夹层和所述顶盖板上均设有若干水平加强筋,其末端均采用肘板型式,可加强穿舱夹层与顶盖板的承力能力。
10.所述顶盖板和所述穿舱夹层上均开设有多种大小不一的管孔,这里大小不一的管孔包括有燃气管孔、喷淋管孔、底部注入管孔、顶部注入管孔、bog排放管孔、bog应急排放管孔、0%取样管孔、50%取样管孔、100%取样管孔、安全阀泄放管孔及仪表管孔。
11.优选地,上述管孔中0%取样管孔、50%取样管孔和100%取样管孔在顶盖板上合并成一个大孔。
12.基于上述技术方案,本发明的气液组合穹顶结构经过实践应用取得了如下积极有益的效果:
13.采用本发明提供的这种气液组合穹顶结构使得在有限的空间内实现了lng燃料舱里所有穿舱管件的布置要求与人员设备的检修通行要求,在保障穹顶结构本身强度的同时又尽量减少了冗余的结构,且穹顶结构的顶盖板边缘的特殊设计使得其与船体构件之间便于安装固定密封圈保证弹性密封避免超低温气体从此处泄漏的风险,具有非常大的实用价值。
附图说明
14.图1是本发明一种用于双燃料超大型集装箱船的b型lng燃料舱的气液组合穹顶结构的纵向布置示意图。
15.图2是本发明一种用于双燃料超大型集装箱船的b型lng燃料舱的气液组合穹顶结构的横向布置示意图。
16.图3为本发明应用所在区域的b型lng燃料舱舱顶图。
17.图4为本发明图3的“a-a”向视图。
18.图5为本发明图4“a1-a1”向视图。
19.图6为本发明图3的“b-b”向视图。
20.图7为本发明图6的“b1-b1”向视图。
21.图8为本发明图3的“c-c”向视图。
22.图9为本发明图3的“d-d”向视图。
23.图10为本发明图9的“d1-d1”视图。
24.图11为本发明图3的“e-e”视图。
25.图12为本发明图3的“f-f”视图。
26.图13为本发明图8的“g-g”向视图。
27.图14为本发明图13的“g1-g1”向视图。
28.图15为本发明图8的“h-h”向视图。
29.图中标号的具体含义为:1为b型lng燃料舱顶板,2为围壁,3为顶盖板,4为穿舱夹层,5为通道井壁,6为下垂的环形t排结构, 7为垂向加强筋,8为水平加强筋,9为人孔与吊物口复合型舱口及舱盖,p为燃气管孔,l为喷淋管孔,e1为底部注入管孔,e2为顶部注入管孔,z1为bog排放管孔,z2为bog应急排放管孔,n1为0%取样管孔,n2为50%取样管孔,k为
100%取样管孔,j为安全阀泄放管孔,r为仪表管孔。
具体实施方式
30.为使本发明的目的、技术方案和优点更加清楚明了,下面结合附图对本发明实施例进行详细描述。
31.应当明确,所描述的实施例仅是本发明的一部分实施例而不是全部实施例。基于本发明的实施例,本领域普通技术人员在没有作出创造性劳动前提下所获得的所有其它实施例,都属于本发明保护范围。
32.对于全新设计的含有b型lng燃料舱双燃料超大型集装箱船来说,lng燃料舱n位于超大型集装箱船中岛上层建筑区域下方,且位于主甲板k的下方,所述lng燃料舱n采用b型独立罐体,所述lng 燃料舱尺寸为全宽型,长度为上层建筑区域加上半个货舱的长度,即 lng燃料舱n的长度约为上层建筑长度加上1个bay的长度,lng燃料舱高度为船舶内底板至二甲板下方的隔离空舱处,双燃料超大型集装箱船上燃料舱区域两侧船体内壳采用大斜坡型式,所述b型lng燃料舱底部两侧也采用与两侧船体内壳平行的大斜坡型式,所述lng燃料舱n与船体内壳之间设有各种类型的支座相连。
33.如图1和图2所示,在上述双燃料超大型集装箱船上燃料舱区域,还设有与lng燃料舱n配套的气液组合穹顶m、lng存储转换过渡间、燃气准备间、隔离空舱和lng加注站。其中,所述气液组合穹顶m设置在lng燃料舱n的靠艉端顶部,气液组合穹顶位于lng燃料舱n横剖面中央位置,所述气液组合穹顶m穿过隔离空舱伸入到lng存储转换过渡间内。所述lng存储转换过渡间位于气液组合穹顶的正上方。
34.如图3-图15所示,本发明中气液组合穹顶结构位于b型lng燃料舱的顶部上方中央靠艉端的位置,其主体外围结构包括围壁2和顶盖板3,内部有水平布置的穿舱夹层4和垂向的通道井壁5结构,这些主体结构与b型lng燃料舱顶板1焊接连接,整体坐落在b型lng 燃料舱的顶部中纵桁和横向强框架组成的十字交叉状强结构上方,如图3、图8和图11所示。所述气液组合穹顶结构所有材料均为9ni 钢,超低温性能极好。
35.如图9、图10和图12所示,所述围壁2整体上做成方形,四个角都做成圆弧倒角型式,可有效防止焊缝应力集中降低产生裂纹的风险,所述围壁2的前后两端壁在b型lng燃料舱顶板的反面设有肘板进行反面加强,围壁2的两侧端壁的位置刚好对齐b型lng燃料舱顶部的纵骨,如图4-图7所示。所述围壁2和通道井壁5上均设置有垂向加强筋7,其中围壁2上的垂向加强筋7其末端做成肘板型式,通道井壁5上的垂向加强筋7其末端做成削斜型式,可加强围壁2和通道井壁5的承力能力。
36.所述顶盖板3比围壁2的范围整体大一圈,边缘四角也是圆弧倒角型式,所述顶盖板3在通道井壁5范围的位置设有人孔与吊物口复合型舱口及舱盖9,方便人员检修与泵等设备的更换,所述顶盖板3 的边缘为下垂的环形t排结构6,便于与船体构件之间安装固定密封圈,如图13和图14所示。
37.所述穿舱夹层4位于顶盖板3下方一定范围内,具体高度可根据实际状态进行调整,所述穿舱夹层4和所述顶盖板3上均设有若干水平加强筋8,其末端均采用肘板型式,可加强穿舱夹层4与顶盖板3 的承力能力,如图13、图14和图15所示。
38.上述顶盖板3和所述穿舱夹层4上均开设有多种大小不一的管孔,这些大小不一的
管孔包括有燃气管孔p、喷淋管孔l、底部注入管孔e1、顶部注入管孔e2、bog排放管孔z1、bog应急排放管孔z2、 0%取样管孔n1、50%取样管孔n2、100%取样管孔k、安全阀泄放管孔 j以及仪表管孔r。其中,0%取样管孔n1、50%取样管孔n2、100%取样管孔k在顶盖板3上合并成一个大孔,如图8和图9所示。
39.本发明一种用于双燃料超大型集装箱船的b型lng燃料舱的气液组合穹顶结构的安装流程大致为:
40.气液组合穹顶结构与b型燃料舱分开独立建造,采取反态制作法,控制好与b型燃料舱体的对接建造精度。先在顶盖板3和穿舱夹层4上的相应位置上开好舱盖口及所有的穿舱管孔,然后在加工好的顶盖板3上反态焊接安装好围壁2和通道井壁5,接着安装好顶盖板 3上所有的水平加强筋8,再安装穿舱夹层4及其上的水平加强筋8,然后在围壁2和通道井壁5上安装好垂向加强筋7,之后在顶盖板3 的边缘安装好下垂的环形t排结构6,至此气液组合穹顶结构模块建造完成。
41.在b型燃料舱的顶板1下方相应位置提前安装好反面的加强肘板和扁钢,然后将气液组合穹顶结构模块翻身后整体吊装到b型燃料舱顶部上方相应位置保证相应构件上下对齐,对接的焊接完成后整个气液组合穹顶结构就已全部安装完成。
42.采用本发明提供的这种气液组合穹顶结构使得在有限的空间内实现了lng燃料舱里所有穿舱管件的布置要求与人员设备的检修通行要求,在保障穹顶结构本身强度的同时又尽量减少了冗余的结构,且穹顶结构的顶盖板边缘的特殊设计使得其与船体构件之间便于安装固定密封圈保证弹性密封避免超低温气体从此处泄漏的风险。
43.最后应当说明的是:以上实施例仅用以说明本发明的技术方案而非对其限制;尽管参照较佳实施例对本发明进行了详细的说明,所属领域的普通技术人员应当理解;依然可以对本发明的具体实施方式进行修改或者对部分技术特征进行等同替换;而不脱离本发明技术方案的精神,其均应涵盖在本发明请求保护的技术方案范围当中。