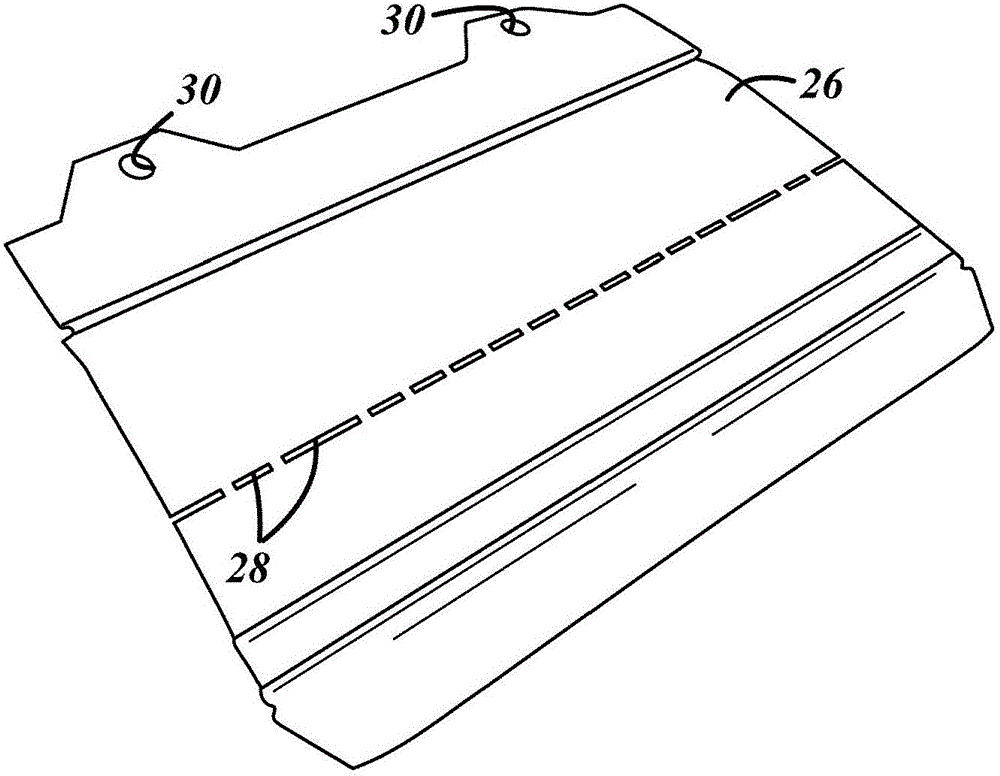
本公开主要涉及含有安全气囊门的车辆内饰面板并涉及用于制造该面板的模制技术和作业工具。
背景技术:车辆安全气囊是在发生撞车时朝着车辆内部展开以帮助避免其购买者受伤的安全装置。在发生撞车之前,安全气囊在正常车辆行驶期间可隐藏在内饰面板后方或下方。当安全气囊展开时,其通常通过形成于内饰面板中或内饰面板周围的展开开口进行展开。展开开口可预先形成在面板中,该面板可被移走以露出开口,或者该开口可在安全气囊展开期间形成于面板中的预定位置处。当在展开期间形成时,可在面板的一个或多个部件中提供撕裂缝以至少部分地限定对应于安全气囊门的开口的位置。在安全气囊展开期间,安全气囊门可在通过铰链或其它装置保持附接至面板的同时朝着车辆内部打开,使得其不被投入车舱。Klisch等人的第2006/0079144号美国专利申请公布描述了位于安全气囊之上的用于车辆内饰的塑料基板。该基板沿着该基板的铰链区模制有一系列长型凹槽。在该铰链区处包含有织物部分,使得在安全气囊展开期间围绕铰链区旋转的活板保持与塑料基板的可靠附接。织物部分具有宽网格配置并在模制期间位于基板中模制工具中,使得熔化的塑料穿过宽网格渗透织物部分并在成品近半的后侧或底侧将织物部分固定到位。在模制过程之后通过激光从成品基板的后侧切割撕裂线。割下织物部分并且沿着撕裂线部分切割基板塑料,并且铰链区不被激光切割。
技术实现要素:根据本发明的一个实施方式,提供了一种制造车辆内饰面板的方法,该车辆内饰面板具有基板,该基板沿着安全气囊门的边界具有减小厚度的部分。该方法包括以下步骤:(a)使用基板模具的第一模具部分和第二模具部分形成模具腔,其中第一模具部分和第二模具部分包括各自的第一模具表面和第二模具表面,第一模具表面和第二模具表面一同至少部分限定腔,第一模具部分包括可动模具构件,可动模具构件至少部分限定第一模具表面;(b)将熔化的可发泡塑料材料引入模具腔;(c)使模具部分中的至少一个模具部分移动并远离另一个模具部分,从而增加第一模具表面与第二模具表面之间的距离,以允许塑料材料膨胀;以及(d)在塑料材料固化以在模具构件处形成基板的减小厚度的部分之前将可动模具构件定位为比第一模具表面的周围部分更靠近第二模具表面。在另一个实施方式中,减小厚度的部分至少部分限定安全气囊门的铰链。在另一个实施方式中,该方法还包括如下步骤:在步骤(b)之前将铰链加固件固定在模具腔中,使得加固件的一部分在可动模具构件处位于模具表面之间。在另一个实施方式中,固定步骤包括经由穿过铰链加固件形成的开口支撑所述铰链加固件。在另一个实施方式中,减小厚度的部分至少部分地限定撕裂缝位置。在另一个实施方式中,步骤(c)和(d)同时执行。在另一个实施方式中,根据步骤(a)-(d)提供了一种结构化其它注射过程。在另一个实施方式中,在步骤(c)之前和在步骤(d)之后,模具构件相对于第二模具表面位于相同的位置。在另一个实施方式中,可动模具构件包括滑动件,其中步骤(d)包括仅在与步骤(c)中模具部分的相对运动平行的方向上移动滑动件。在另一个实施方式中,提供了一种用于在安全气囊之上使用的车辆内饰面板。车辆内饰面板包括设置在发泡的塑料基板之上的装饰性覆盖物。基板具有安全气囊门,安全气囊门在基板的减小厚度的部分处具有一体式铰链。该面板还包括在一体式铰链处至少部分地嵌入基板的铰链加固件。在另一个实施方式中,铰链加固件是亚麻布材料。在另一个实施方式中,安全气囊门具有由铰链和沿着预定展开开口位置穿过基板形成的多个开口限定的边界。在另一个实施方式中,车辆内饰面板是车辆仪表面板。根据另一个实施方式,提供了一种用于模制具有一体式安全气囊门的车辆内饰面板基板的注射模塑工具。该注射模塑工具包括:基板模具,具有第一模具部分和第二模具部分,第一模具部分和第二模具部分具有各自的相对的第一表面和第二表面,当模具位于关闭位置时,第一表面和第二表面一起形成模具腔。第一模具部分包括滑动件,滑动件具有端部,该端部部分地限定第一表面,并且滑动件被布置为在模制过程中从第一模具部分延伸以形成安全气囊门的非底切特征。在另一个实施方式中,非底切特征是铰链。在本申请的范围内,可以设想,在前面的段落中、在权利要求中和/或在下面的描述和附图中陈述的各种方面、实施方式、实施例、特征和替代选择可以独立地或以任何组合的方式实施。例如,结合一个实施方式公共的特征可应用于所有实施方式,除非存在不兼容特征。附图说明将在下面结合附图描述一个或多个实施方式,其中相同的参考标号指代相同的元件,其中:图1是根据一个实施方式的具有一对安全气囊门的仪表面板的剖开立体图;图2是来自图1的仪表面板的铰链加固件的立体图;图3是包括由可动模具构件部分限定的模具表面的处于关闭位置上的基板模具的一部分的截面图;图4是包括可动模具构件并示出位于可动模具构件与相对的模具表面之间的铰链加固件;图5是图4的视图,其中与图4相比基板模具稍微打开;以及图6是图5的视图,其中与图5相比可动模具构件更加靠近相对的模具表面。具体实施方式通过下面的公开,显而易见的是,沿着安全气囊门的边界具有减小厚度的部分的车辆内饰面板基板可通过使用包括可动模具构件的基板模具对基板进行模制来形成。该模具构件可在模制过程中并在熔化的塑料材料被引入模具腔内以在成品零件中形成减小厚度的部分之后移动。以减小的厚度为特征的安全气囊门铰链、撕裂缝、或其它基板特征可通过这种方法形成。图1示出用于安全气囊之上的车辆内饰面板的一个实施方式。所示的面板10是仪表面板,并且该面板的乘客侧以剖开视图的方式示出。面板10包括上覆盖基板14的装饰性覆盖物12。面板10被配置为帮助安全气囊穿过面板10从下面的安全气囊模块展开。预定的撕裂缝位置16至少部分地由穿过基板14形成的多个开口18限定。在这种情况下,撕裂缝位置16被布置为H形,使得当安全气囊展开时,基板14沿着位置16破裂,并且两个安全气囊门20、20’朝着车辆内部打开。每个安全气囊门20、20’在安全气囊展开期间围绕各自的铰链22、22’旋转。在该实施方式中,安全气囊门和铰链是基板的组成部分,这意味着它们与周围的基板一同被制造为单个部件。为了简化起见,铰链22、22’在图1中被描绘为代表示意性铰链位置的直线。铰链的实际形状和配置可以变化,如后续附图的实施例中所示,并且可包括凹陷部分、凸起部分、切口或凹槽部分、穿孔、或被设计为有助于安全气囊门枢转的其它特征。每个安全气囊门20、20’包括各自的边界24、24’,边界24、24’由铰链22、22’和撕裂缝位置16的一部分限定。例如,上安全气囊门20的边界24由上铰链22和H形撕裂缝位置16的上腿和横杆限定,而下安全气囊门20’的边界24’由下铰链22’和H形撕裂缝位置16的下腿和横杆限定。穿过面板10形成的安全气囊展开开口共用这些边界中的一部分。其它面板配置也是可能的,包括与方向盘安全气囊系统、侧面撞击安全气囊系统、或其它系统一起使用的面板。在一个实施方式中,基板不包括撕裂缝位置而是包括沿着整个安全气囊门边界(除了该边界的铰链部分)的贯通槽。在另一个实施方式中,在在撕裂缝位置处与覆盖物相对的基板下侧包括凹槽或其它类型的应力集中部,并且该基板可以包含或不包含开口18。对本领域技术人员来说,其它变形将变得显而易见,这些变形包括具有不同安全气囊门形状的基板、覆盖物16中的应力集中部的用于撕裂缝构造的内含物、非整体安全气囊门铰链、无铰链安全气囊门等。在包括安全气囊门的实施方式中,面板10还可包括铰链加固件26,如图2所示。图中所示的具体加固件26是一片亚麻布材料,该材料与图1的基板14模制在一起,使得其至少部分地嵌入基板的塑料材料中。如文中所使用,术语“嵌入”涉及被其他材料在多侧进行封装的材料或凹进并因此附接至其它材料的材料。亚麻布材料可被描述为纺织或织物材料(编织或非编织),并且可包括天然和/或人造纤维。加固件可从其它材料(诸如金属纤维或玻璃纤维、丝网或织物)形成。亚麻布材料26的轮廓在图1中用虚线大致地画出以示出其在面板10中的位置。在该具体实施例中,亚麻布26是从上安全气囊门铰链22延伸至下安全气囊门铰链22’并稍微超出各铰链的单片。材料26还包括与撕裂缝位置16的一部分对齐的穿孔28,使得材料26在安全气囊展开期间沿着穿孔28撕裂。所示亚麻布材料26的宽度小于撕裂缝位置16的H形的直立部分。但是,亚麻布材料26可以更宽并且根据需要包括额外的穿孔28或其它应力集中部。还可沿着铰链加固件26的边缘或者在其他位置包括开口30,如图所示。这些开口可用于在注塑模具腔中支撑加固件或用于其它材料处理目的。铰链加固件26是任选的,并且其它配置也是可能的。例如,在使用时,铰链加固件不需要几乎跨越如图所示的从一个铰链到另一个铰链的整个安全气囊门区域。作为加固件,其仅仅需要存在于铰链在安全气囊展开期间最有可能断裂的安全气囊门铰链处,使得其有助于在该断裂的两侧处将安全气囊门固定至基板。将参照图3-6描述可用于形成诸如如图1所示的用于用于在安全气囊之上使用的车辆内饰面板的基板的示例性过程和设备。更具体地,下面所述的技术可用于形成基板,该基板沿着安全气囊门的边界具有减小厚度的部分。虽然文中所述的在减小厚度的部分处形成安全气囊门铰链并在铰链处具有铰链加固件,但应理解,下面的方法可用于在沿着模制基板的任何位置(诸如沿着上述撕裂缝位置)形成减小厚度的部分。如文中所述,“减小厚度的部分”涉及基板的一部分,该部分的厚度小于周围基板的标称壁厚并且所小的量大于普通制造偏差,并且“减小厚度的部分”不涉及孔或通孔(即,0厚度)。该方法的一个实施方式包括以下步骤:(a)在基板模具的第一和第二模具部分的第一和第二模具表面之间形成模具腔,其中模具部分中的至少一个包括部分限定各自的模具表面的可动模具构件;(b)将熔化的塑料材料引入模具腔;(c)使基板模具的模具部分中的至少一个模具部分移动并远离另一个模具部分,从而增加第一和第二模具表面之间的距离;以及(d)在塑料材料固化以在模具构件处形成基板的减小厚度的部分之前将可动模具构件定位为比第一模具表面的周围部分更加靠近第二模具表面。图3是包括第一和第二模具部分102、104的示意性基板模具100的一部分的截面图。第一和第二模具部分102、104可以是半个模具,或者它们可以是组成基板模具100的更大数量的模具部分中的两个。该截面是沿模具的形成安全气囊门的部分截取的。该模具在图3中被示出为位于关闭位置,并且模具部分102、104被配置为沿双箭头所指示的方向朝着和远离彼此运动。在所示实施方式中,模具部分102是模具的后半部分并且是可动的那一半,半个模具104是模具的前半部分并且是与注塑喷嘴配合的静止的那一半。模具部分中的至少一个,在本情况下为第一模具部分102,包括可动模具构件106,可动模具构件106用于在模制过程中形成基板的减小厚度的部分。除了能够在第一模具部分运动时随着第一模具部分运动之外,可动模具构件106还能够相对于第一模具部分的周围部分运动。在该具体实施例中,可动模具构件106是滑动件,并且附加的可动模具构件106’被包括以在沿着成品基板的另一个位置处(诸如在不同的安全气囊门铰链处)形成减小厚度的部分。当模具100如图所示位于关闭位置时,模具腔108形成于这两个模具部分之间。图4-6是示出在模制过程的各步骤期间的示意性基板模具的图3的一部分的放大视图。图4示出处于图3的关闭位置的模具100。模具部分102、104中的每一个均包括限定模具腔108的各自的模具表面110、112。在该实施例中,模具表面110的一部分由模具构件106的端部114限定。模具构件106被构造和布置为在从其对应的模具部分朝着另一个模具部分的方向上延伸并且在相反方向上缩回。在所示实施方式中,可动模具构件106被配置为当模具部分打开和关闭时仅在与模具部分的运动方向平行的方向上运动。在该实施例中,任选的铰链加固件26被示出位于模具腔108中。加固件26可通过各种手段支撑在模具腔108内,这些手段包括穿过加固件形成的开口(例如,图2的开口30)、模具表面110处的真空、静电荷、或其它手段。例如,销或钉可设置在相应的模具部分上以在加固件中的上述开口处或穿孔处支撑加固件26。图5示出在通过典型的注塑模制步骤或其它技术将熔化的塑料材料引入模具腔内之后的基板模具。附加地,图5示出彼此稍微分离,即不再处于关闭位置的模制部分102、104。具体地,在该实施例中,被引入模具腔的塑料材料是可发泡塑料材料,并且该模具从关闭位置被打开预定量以允许塑料材料在模制表面之间膨胀至更大体积。在该实施例中,当塑料材料被允许膨胀时—即塑料材料与对应于成品基板的下侧的模具表面110邻接,加固件26在模具腔内通常位于其初始位置,如图所示。在一个实施方式中,可发泡塑料材料是包括发泡剂(诸如当阈值温度、压力或时间满足时在塑料材料内形成气泡的热、压力或时间激化的发泡剂)的塑料材料。在另一个实施方式中,可发泡塑料材料是当材料处于熔化状态时包括被注入和/或溶入材料中的气体的塑料材料,其中气体在其遇到模具腔的较低压力时膨胀。在另一个是实例中,可发泡塑料材料是经历在所产生的塑料材料中形成气泡的化学反应的材料的混合物。共同地,使用可发泡塑料材料的过程可被称为结构化气体注射(SGI)过程。这些过程可产生成品部件,该成品部件具有由更稠密和/或未发泡外壳或表皮包围的发泡塑料核心。例如,当可发泡塑料材料首先被注入模具腔108中时,与模具表面110、112接触的材料可在可发泡塑料开始膨胀之前固化,从而形成由熔化的可发泡塑料填充的未发泡外壳。封装的熔化材料随后被允许膨胀,从而形成具有发泡核心和未发泡外壳的成品部件。使用可发泡塑料材料的模制过程的一个具体实施例是处理(可从美国马萨诸塞州威明顿市的卓细公司(Trexel,Inc.,Wilmington,MA)获得),其中气体诸如氮气或二氧化碳在被注入模具腔之前被溶解在熔化的材料中。通过SGI过程生产的部件的密度通常低于大多数塑料在未发泡情况下的密度。图6示出处于开离位置的模具构件106。模具106从第一模具部分延伸,从而在塑料材料固化之前,将模具106定位为比第一模具表面的周围部分更加靠近第二模具表面。模具构件106因此形成成品基板14的减小厚度的部分,在这种情况下为安全气囊门铰链22。模具部件运动的顺序可以改变。在一个实施方式中,模具构件在模具从其关闭位置被打开预定量之后可重新定位以允许可发泡塑料材料膨胀。在另一个实施方式中,模具构件与模具的受控开口同时运动。在图中所示的实施例中,这可能导致从模具处于关闭位置时开始直至塑料材料固化并且从模具移除成品基板时模具构件的总体位置相对于其它模具部分保持不变。在另一个实施方式中,在模具开始打开之后但在模具完成打开预定量以供塑料材料膨胀之前,模具构件开始运动。不同模具部件的运动量也是可变的。在一个实施方式中,当基板模具处于关闭位置时模具表面110、112之间的标称距离为约2.0mm;模具表面110、112进一步分离约2.0mm以允许可发泡塑料材料膨胀;并且模具构件106在塑料材料固化之前延伸约2.0mm。因此,在这种情况下,模具构件106在模具构件被延伸之后相对于另一半模具的位置与模具构件106在模具构件被延伸之前并且模具处于关闭位置之前相对于另一半模具的位置相同。所产生的基板具有约4.0mm的标称厚度,并具有约2.0mm的减小厚度的部分。本领域技术人员应理解,该实施例的非限制特性以及模制部件运动的许多组合也是可能的。在某些实施方式中,可动模具构件106可以仅仅延伸一小段距离,使得模具打开以供材料膨胀。在另一个实施方式中,滑动件延伸的量可以大于模具打开以供材料膨胀的量。因此,可以根据具体应用改变减小厚度的部分以影响安全气囊门铰链刚度,基板撕裂缝功能等。如图所示,通过移动模具构件106来使铰链加固件26(当存在时)在模具腔内位移。铰链加固件26的位于模具构件106与第二模具表面112之间的部分,例如可在与模具构件106相邻的位置处移动远离模具表面110。根据加固件的刚性和整体性、其总体尺寸、或其它因素,整个加固件26可被位移,使得其更加靠近成品基板的外表面或顶侧(与加固件26在不存在模具构件106运动的情况相比—在这种情况下,其将终止于成品基板的下侧)。换言之,模具构件运动可使铰链加固件位于被基板的塑料材料更好地封装的位置(与铰链加固件在左侧邻接模具表面的情况相比)。显然,为了形成成品基板,可以包括其它方法步骤,诸如模具开口步骤、从模具中退出移除或固化的塑料部件的步骤、后期模具最后工序步骤等。在模具完全打开以用于零件移除之前或之后或在模具正在打开期间,模具构件106可相对于其对应模具的缩回至其初始位置。可动模具构件的构造和操作可根据已知结构和方法,如滑动件,例如,通常被用于塑料模制操作中的部件。然而,采用可动模具构件在成品零件中形成非底切特征是非传统的。通过上述教导还可用于在成品零件中经由沿与模具打开/关闭方向不同的方向的模具构件运动形成底切特征,所示实施方式中的模具构件被用于在成品零件中形成非底切特征。应理解,前述内容是本发明的一个或多个优选示例性实施方式的描述。本发明不限于文中公开的具体实施方式,而是通过所附权利要求单独限定。此外,前面描述中的所包含的陈述涉及具体搜索法并且不被认为是对本发明的范围或权利要求中所使用的术语的定义的限制,除非术语或短语在上面明确定义。各种其它实施方式和对所公开的实施方式的各种改变和修改对本领域技术人员来说是显而易见的。所有这些其它实施方式、改变、和修改旨在落伍所附权利要求的范围内。如说明书和权利要求中所使用,术语“例如”、“比如”、“诸如”和“等”以及动词“包括”、“具有”、“包含”及它们的其他动词形式,在与一个或多个部件或其它项目的列举结合使用时,分别被认为是开放式的,这意味着该列举不被认为是排出其它的、附加的部件或项目。其它术语使用它们最广义的合理含义构造,除非它们被用于需要不同解释的环境中。