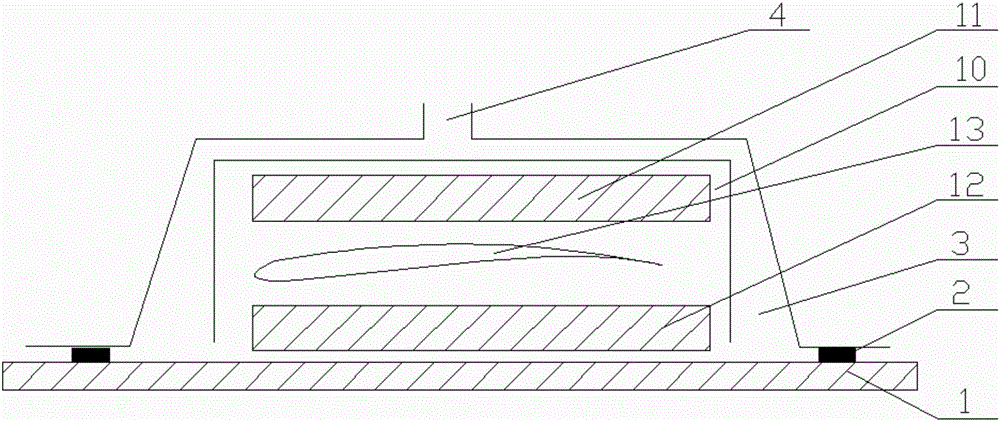
本发明属于螺旋桨叶的制备
技术领域:
,涉及一种平流层飞艇用一体化复合材料螺旋桨叶的制备方法。
背景技术:
:近年来,各国都在开展研究各类平流层飞行器。平流层飞艇是一种新型低成本、低能耗平流层飞行器,其大型高性能螺旋桨在控制方面起到了关键性作用已成为关键技术,一般螺旋桨都采用拼接方式其强度与一体化螺旋桨相差近2倍之多,在同等强度时一般螺旋桨又比一体化螺旋桨重近1倍,存在薄壁桨叶分层,粘接气泡等问题的出现,需要研究一种轻质、高效的平流层飞艇用一体化复合材料螺旋桨叶解决上述瓶颈问题。技术实现要素:本发明的目的是针对现有技术的不足,提供一种平流层飞艇用一体化复合材料螺旋桨叶的制备方法,其中,所述制备方法包括:步骤一:准备制备所述螺旋桨叶的模具装置,包括,模具装置底板,设置于所述模具装置底板上的模具本体,将所述模具本体封闭于所述模具装置内部的真空袋,所述真空袋上部具有真空嘴,所述模具本体包括外模具下模,芯模和外模具上模,所述外模具上模和所述外模具下模的相对表面设有外模具空腔,在所述外模具上模和所述外模具下模的所述空腔外侧的相应位置各设置至少一个定位装置;步骤二:准备碳纤维预浸布作为所述芯模的铺层;步骤三:对所述外模具上模和所述外模具下模进行清洗,并在表面喷涂脱模剂;清除芯模上的杂质,涂抹改性树脂胶膜;步骤四:按照螺旋桨叶铺层设计在所述芯膜外表面铺敷所述碳纤维预浸布,形成所述螺旋桨叶的预制件;步骤五:将铺敷完成的所述预制件放入所述外模具空腔内,并通过所述外模具上模和所述外模具下模上的所述定位装置固定所述模具本体;步骤六:根据螺旋桨叶要求,将所述模具本体设置于所述模具装置底板上,将所述真空袋罩在所述模具本体的外部,通过所述真空封泥将所述真空袋固定于所述模具装置底板上,将所述模具本体封闭于所述模具装置内部,将所述真空嘴与真空装置相连接,将所述模具装置内部抽成真空;步骤七:根据螺旋桨叶的固化要求通过加温加压设备对所述模具设备进行加温、加压固化;步骤八:固化完成后,根据所述碳纤维预浸布固化要求进行降温处理,从所述加温加压设备中取出固化完成的所述模具装置,冷却至室温;步骤九:根据螺旋桨叶的脱模要求拆除所述真空装置,按照所述模具装置的安装顺序的相反的顺序拆除所述模具装置,进行脱模处理;步骤十:对脱模的螺旋桨叶的进行打磨修边,完成成品的制备。进一步的,所述步骤一中的所述外模具的上模和所述外模具的下模采用钢材料。进一步的,所述步骤一中的所述芯模采用高性能聚甲基丙烯酰亚胺材料。进一步的,所述步骤一中的所述模具装置底板采用铝材料。进一步的,所述步骤三采用丙酮清洗。进一步的,所述步骤三中的脱模剂采用美国PMR脱模剂。进一步的,所述步骤三中的改性树脂胶膜采用型号为JCH47。进一步的,所述步骤七中的所述加温加压设备为高温釜。进一步的,所述步骤七中的所述加温温度范围为125℃±10℃。进一步的,所述步骤七中的所述加压的压力范围为8-14个大气压。本发明的有益效果为:1、本发明为平流层飞行器的螺旋桨制作提供了一种新的方法,本方法工艺相对简单,成品质量较好,成品强度较高、重量轻,制作效率较高。2、本发明采用芯模填充技术,有效的提高了螺旋桨的承载能力;3、本发明采用芯模填充技术,增强体纤维丝连续保证了一体化成型,提高了螺旋桨的整体质量4、本发明采用了真空技术,通过真空排出制作时存在的气泡,有效的提高了成品率;5、本发明采用了热压技术,通过对模具整体进行加压,保证了螺旋桨叶固化时所受压力一致,避免了因受力不均导致的变形或有气泡的情况。6、本发明方法制作的平流层飞艇用一体化复合材料螺旋桨叶提高了平流层飞行器的机动性能,保证整体刚度和稳定性的同时降低了自身重量,提高了螺旋桨的工作效率。附图说明图1是本发明的一体化复合材料螺旋桨叶的制备方法的流程图。图2是本发明的一体化复合材料螺旋桨叶的制备装置正视图。图3是本发明的一体化复合材料螺旋桨叶的制备装置的模具本体结构的的示意图。图4是本发明的一体化复合材料螺旋桨叶的制备装置的外模具上模的立体图。图5是本发明的一体化复合材料螺旋桨叶的制备装置的预制件的立体图。图6是本发明的一体化复合材料螺旋桨叶的制备装置的预制件的A-A剖面图。图中:1-模具装置底板,2-真空封泥,3-真空袋,4-真空嘴,10-模具本体,11-外模具上模,12-外模具下模,13-预制件,14-定位装置,15-外模具空腔,16-碳纤维预浸布,17-芯模。具体实施方式下面结合附图和具体实施方式,对本发明作进一步的说明。实施例一本发明的所述螺旋桨叶的制备方法,如图1所示,包括:步骤一:准备制备所述螺旋桨叶的模具装置,如图2所示,所述模具装置包括,模具装置底板1,设置于所述模具装置底板1上的模具本体10,将所述模具本体10封闭于所述模具装置内部的真空袋3,所述真空袋3上部具有真空嘴4,如图3和图4所示,所述模具本体10包括外模具下模12,芯模17和外模具上模11,所述外模具上模11和所述外模具下模12的相对表面设有外模具空腔15,在所述外模具上模11和所述外模具下模12的所述空腔15外侧的相应位置各设置至少一个定位装置14,所述外模具上模11和所述外模具下模12采用钢材料,所述芯模17采用高性能聚甲基丙烯酰亚胺,所述模具装置底板1采用铝材料;步骤二:根据如表1所示的铺层要求,准备碳纤维预浸布16作为所述芯模17的铺层;表1序号规格角度数量12200*32030°222200*32090°131800*280150°241500*2800°15700*3200°46500*280150°27500*30090°28500*30030°19700*1800°210100*800°211100*8090°212100*80150°213100*8030°2步骤三:对所述外模具上模11和所述外模具下模12进行清洗,所述清洗剂优选丙酮,并在表面喷涂脱模剂,所述脱模剂优选美国PMR脱模剂,清除所述芯模13上的杂质,涂抹改性树脂胶膜,所述改性树脂胶膜优选型号为JCH47;步骤四:按照螺旋桨叶铺层设计在所述芯膜17外表面铺敷所述碳纤维预浸布16,使得所述芯模17和所述碳纤维预浸布16形成一体化复合材料螺旋桨叶的预制件13,如图5和图6所示;步骤五:将铺敷完成的所述预制件13放入所述外模具空腔15内,并通过所述外模具上模11和所述外模具下模12上的所述定位装置14固定所述模具本体10,如图3所示;步骤六:根据螺旋桨叶要求,将所述模具本体10设置于所述模具装置底板1上,将所述真空袋3罩在所述模具本体10的外部,通过所述真空封泥4将所述真空袋3固定于所述模具装置底板1上,将所述模具本体10封闭于所述模具装置内部,将所述真空嘴4与真空装置相连接,将所述模具装置内部抽成真空,如图2所示;步骤七:根据所述螺旋桨叶的固化要求,通过加温加压设备对所述模具装置进行加温、加压固化;所述加温加压设备采用高温釜,设置好高压釜加热、加压固化程序,加热、加压程序根据所述碳纤维预浸布16的固化工艺参数进行设置,然后进行加热、加压固化。加温温度为125℃±10℃,加压的压力范围为8-14个大气压;步骤八:固化完成后,根据所述碳纤维预浸布16固化要求进行降温处理,从所述加温加压设备中取出固化完成的所述模具装置,冷却至室温;步骤九:根据所述螺旋桨叶的脱模要求拆除所述真空装置,按照所述模具装置的安装顺序的相反的顺序拆除所述模具装置,进行脱模处理;从高压釜取出固化完成的模具,冷却至室温,将所述真空袋3打开,取下所述上模具11,取出复合材料螺旋桨叶;步骤十:对脱模的螺旋桨叶的进行打磨修边,完成成品的制备。本发明并不限于上述实施方式,在不背离本发明实质内容的情况下,本领域技术人员可以想到的任何变形、改进、替换均落入本发明的保护范围。当前第1页1 2 3