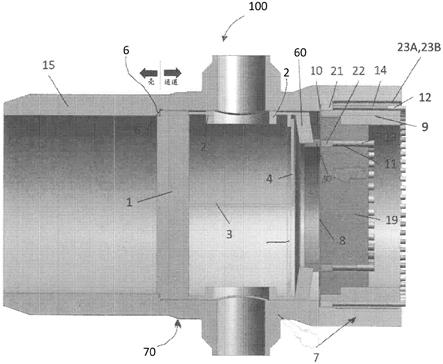
热交换器封闭组件及其使用和安装的方法
[0001]
对相关申请的交叉引用本申请要求提交于2018年3月20日的序列号为62/645662的美国专利申请的优先权,该专利申请通过引用以其整体并入本文中。
技术领域
[0002]
公开的实施例涉及热交换器封闭组件以及用于使用和安装该热交换器封闭组件的方法,并且更特别地涉及用于密封具有可移除管束的高压壳管型热交换器的封闭系统和方法,并且还更特别地涉及构造成适应变化的热负荷的热交换器封闭组件,其具有使用锁定组件固定到热交换器的通道的封闭塞组件。
背景技术:[0003]
壳管型热交换器构成化工厂、炼油厂、蒸汽厂以及类似设施中的未燃烧热传递设备的大部分。具有可移除管束(诸如具有u形管和浮动头部的管束)或者具有带有固定管板材的不可移除束的热交换器为当前使用中的壳管式热交换器的主要类型中最受欢迎的交换器之一。在实践中,通常合乎期望的是,具有可移除管束,使得热交换器可从服务中周期性地移除,管束为了清洁和检查而被移除,并且然后重新组装。还可合乎期望的是,利用可移除管束流体静力地或气动地测试管状热交换器的壳侧,使得可进行管接头和管板材垫圈的检查或验证,并且可容易地定位和维修泄漏。为了移除束,必须提供封闭件,其可在变化的热负荷和压力负荷下的长期操作之后快速地且可靠地开启。当管状热交换器相对大(在直径方面超过36英寸)并且旨在用于超过1000 psi的高压操作时,与拆卸、移除、流体静力和气动测试以及重新组装相关联的问题特别严重,因为所需构件的重量变大。为此目的开发的特定类型的封闭件为“螺旋塞”,也被称为“闩锁”型封闭件,其使用多个互锁螺纹以将锁环盖组件固定就位。该类型的系统的主要优点是,其消除了其它常规高压交换器设计的大通道盖凸缘和螺栓连接。存在现有技术中描述的螺旋塞型热交换器的两种常见分类。在其中压力在管板材的两侧上超过1000 psi使得管板材本身仅经受较低的压差的应用中,可能的是,提供完全可移除的“a型”封闭件,由此可移除束,而不移除壳盖。如果压差太高,则移除壳盖以接近束可更方便,在这种情况下,可使用“b型”封闭件。
[0004]
此外,在该类型的热交换器中使用的封闭组件必须足够刚性以控制内部压力,而没有封闭组件相对于通道的显著移动,因为这种显著移动将导致用于固定封闭组件的螺纹的部分或完全脱离。然而,组件还必须足够柔性,以适应在操作期间出现的预期热负荷。预期热负荷在温度方面随着时间改变,这可在初始启动或随后维修期间发生,或者在混乱(upset)或工厂跳闸的情况下发生,该单个情况中的任何情况均可造成内部构件相对于通道的差异热膨胀。热负荷(如果在一个或多个实施例中未被恰当地适应)可继而引起内部件的不均匀塑性变形,使得垫圈负荷不再均匀地分布并且最终组件开始泄漏。特别地,因为热交换器的内部构件通常经受比通道更高的热膨胀(这是由于热膨胀系数不同,或者较薄的内部件可比厚的通道材料以更快的速率变热的事实),所以刚性封闭组件并非合乎期望的
(如果其造成:内部件的塑性变形,这导致垫圈卸载和泄漏;以及在封闭组件和通道的螺纹部分上的较高负荷,这可导致螺纹变形)。所有上述情况和操作条件均已导致许多不同的技术解决方案的采用,这些技术解决方案仅部分成功,因为它们仅解决了一些问题,并且同时引入其它问题(尤其对于其中温度、压力以及大小在高侧上的应用而言)。
[0005]
在所有这些现有技术解决方案中,螺纹锁环和盖组件(或“封闭塞”)必须旋转若干次,通常20次或更多次,以便使锁环中的螺纹与热交换器的通道中的螺纹完全地接合。这引入特殊的搬运考虑,因为锁环组件必须准确地被定心和支承,同时在通道外部并且旋转到位。特别地,由于封闭塞的重量不可被允许靠在螺纹上,故搬运这样的重的设备件(重达21000 lb)的精度需要为热交换器供应专用夹具。已开发多种夹具设计。在一些情况下,配重的悬臂系统用于使锁环的重量平衡。在其它情况下,夹具直接地附接到通道。
[0006]
然而,特殊夹具不具有其它功能,并且可很少被使用,使得在交换器上工作的操作人员缺乏经验,并且完全地依赖由制造商提供的说明书。在最坏的情况下,如果重的组件未正确地固定到夹具,则存在在交换器上工作的工厂人员受伤的风险。在插入或移除期间,始终存在封闭塞可变得被卡住或者螺纹可被损坏的风险。这特别是在封闭塞首先插入到热交换器通道中时是这样。时间在工厂周转或维修期间为至关重要的,因此与阻塞的封闭塞相关联的任何计划外停机均可代表对工厂或精炼厂的显著财务损失。
[0007]
搬运锁环的困难意味着,在维护事件期间不止一次插入和移除锁环并非合乎期望的。如果对管或其它保压构件执行维修为必要的,则壳侧流体静力或气动测试必须在盖未就位的情况下执行,以便检查并确保没有泄漏。早期的设计在流体测试热交换器的壳侧时使用临时的内部凸缘来加载垫圈。后来的设计(诸如美国专利no. 4750554中示出的设计)提供用以将来自内部凸缘的负荷与来自内排螺栓的负荷并行地施加的机构。对于这些后来的设计而言,定位在外部锁环中的内排螺栓仅在泄漏的情况下用于加载管板材垫圈。实现该功能所需的内部构件可变得非常复杂,并且虽然设计已被良好优化,但零件的数量和复杂性增加它们可被错误地安装以及引入更多制造成本的风险。由于内部凸缘与过程流体接触,故螺栓可变得被腐蚀或者在焦炭形成时被覆盖,并且可能必须被切割或钻出。此外,内部构件的差异热膨胀可引起内部凸缘组件损坏或者可使该内部凸缘组件变形,从而导致移除和重新使用组件的困难。
[0008]
因此,现有技术没有解决在插入/移除期间搬运封闭塞并且在维持内部件的更简单设计的同时允许压力测试的问题。
[0009]
虽然螺旋封闭塞热交换器可满足关于压力控制零件的可适用设计规范,但是存在在设备设计的压力边界之内的其它构件,它们将影响该类型设备的可靠性和生命周期成本。存在对如下的装置的需要:该装置将足够刚性以限制在压力负荷下的移动,同时避免内部件在预期热负荷条件下的损坏,并且在极端的热负荷条件下向保压结构(螺纹)等提供失效安全保护。
[0010]
因此,在本领域中存在对如下的热交换器封闭组件的未得到满足的需要:该热交换器封闭组件构造成适应变化的热负荷并且包括锁环和盖,该锁环和盖可如需要那样更容易地安装和移除,而不使用专用搬运设备。
技术实现要素:[0011]
下文描述的图示的实施例的目的和优点将在以下描述中阐述并且根据该描述显而易见。图示的实施例的额外的优点将通过在书面描述及其权利要求书中以及从附图中特别指出的装置、系统和方法而实现并获得。
[0012]
为了实现这些及其它优点,并且根据图示的实施例的目的,在一个方面,描述了用于壳管型热交换器的封闭系统和方法,其中热交换器封闭组件构造成适应变化的热负荷,并且包括使用多个互锁的毂或螺纹固定到热交换器的通道的锁环。
[0013]
如前面注意到的,壳管型热交换器的最终用户特别关注以下内容:导致过程流体(诸如氢/碳氢化合物)逸出到环境中的横跨垫圈的泄漏;壳侧和管侧流体之间的过程泄漏;由于封闭塞在插入/移除期间的卡住而产生的比预期更长的维护时间;以及在插入或移除期间支承封闭塞所需的大量内部构件和专用设备的复杂性。
[0014]
根据本文中图示的某些实施例,用于开启、封闭和密封高压热交换器的当前公开的方法/系统采用盖和锁环组件(例如,封闭塞),由此封闭塞以一线性运动插入到热交换器通道中,并且优选地旋转小于一个单次转动(例如,小于360度的转动)而进入锁定位置。负荷承载表面(例如,毂)优选地不接触,直到施加最终的旋转,从而将封闭塞有效地锁定至高压热交换器。高压热交换器的通道优选地机加工有第一组毂,并且锁环机加工有互补的第二组毂,使得当封闭塞旋转时,第一组毂与第二组毂可释放地接合。在某些实施例中,轨道可附接成邻近于锁环和/或通道上的一组或多组毂,以沿着一侧提供凸起区段,这:(i)防止过度旋转;(ii)提供用于锁环组件的插入的承载表面;并且(iii)防止对负荷承载表面的损坏。
[0015]
在某些说明性实施例中,锁环机加工有规定数量(例如,8个)的锁环毂组,并且热交换器通道机加工有对应数量的通道毂组。本领域技术人员将容易认识到的是,在不脱离本公开的发明方面的情况下,毂的对应组的数量可变化。在某些说明性实施例中,毂轮廓为支柱(buttress)形状。
[0016]
将认识到的是,图示的实施例的某些优点包括封闭塞组件,其可利用单个线性运动安装,而不需要专用夹具或工具。仅一旦封闭塞组件就位并且由热交换器通道完全地支承,封闭塞组件才能通过单次部分转动(例如,塞部件的22.5
°
转动)锁定到位。封闭塞相对于热交换器通道卡住的风险被消除。另外,由于不需要旋转直到封闭塞相对于热交换器被完全地支承,故塞部件的搬运为更安全的。可容易得到的工厂设备(诸如起重机、束拉卡车(bundle pulling truck)以及叉车)可用于将封闭塞部件移动就位,由此消除与专用夹具相关联的成本。安装为更安全的,因为锁环组件/塞不需要在使用配重或悬臂来悬挂和定心时同时旋转,而是改为优选地沿着专门设计的轨道滑入,该轨道还用于提供旋转止动件。轨道的大小设定成以便确保封闭塞的锁环组件将其整个重量靠在毂的负荷承载表面上。
[0017]
根据图示的实施例,封闭塞组件的插入和移除可比现有技术的螺纹设计更快速地实现。更快的插入和移除实现简化的内部件的使用,特别是通过消除对内部凸缘的需要。在某些实施例中,为了将封闭塞组件的环锁定就位,需要封闭塞组件相对于热交换器管的仅部分转动(例如,22.5
°
)(与现有技术设计的典型的20次或更多次完整转动对比)。因此,在将封闭塞的负荷承载表面形状选择成比现有技术中使用的传统1'' acme螺纹更优的方面,提供灵活性。
[0018]
关于现有技术的设计和方法,螺旋螺纹的上紧相当于将楔形物驱动到空隙中,直到该楔形物通过摩擦和轻微的塑性变形而快速卡住。因此,螺纹必须在旋转时前进通过某一线性距离以便完全地接合。现有技术的设计典型地使用acme型的螺纹(通常关于1''螺距),使得一次完整转动使塞前进1英寸而进入通道。相比之下,本发明的某些图示的实施例的毂设计为例如阳-阴互锁的或互相交叉的几何形状,其通过在单平面中的旋转而接合,优选地使用毂形状(例如,支柱构造),该毂形状在毂上的力主要沿一个方向时为更刚硬且更适当的。轨道设在毂上并且构造在该毂上,以确保塞组件的锁环在插入期间正确地定心,并且不可过度旋转。轨道还在封闭塞部件与热交换器管的组装期间起作用,以保护毂。
[0019]
因此,由图示的实施例提供的明显优点是消除了对在锁定环旋转时支承锁定环和使锁定环定心所需的专用“夹具”的需求。根据本发明的图示的实施例,一旦塞的锁环完全地插入通道中,封闭塞的旋转就发生,因此锁环设计显著地减少为了维护操作而开启和封闭热交换器所花费的时间,消除对特殊设备/搬运的需求,并且因此降低错误安装将造成泄漏的风险。通过减少开启和封闭时间,还可能的是,消除用于压力测试目的的内部凸缘,这大大地减少了必须安装/移除以获得对管束的接近的构件的数量。
[0020]
将认识到,本发明的图示的实施例涉及热交换器结构,其通过弹性扭转部件的使用而容许在操作期间在变化的热负荷下的热膨胀。通过利用弹性扭转部件来适应预期的热膨胀,密封可通过多个操作循环来维持,而没有对设在封闭塞上的压缩螺栓的调节。预期的热负荷包括由于启动、停机、流体流速的波动以及不常见但可预见到的事件(诸如工厂跳闸或突然停机)而导致的构件的变热和冷却。在极端的热负荷使内部件的热膨胀超出设计中考虑的范围的情况下,保护封闭组件的毂免受损坏为至关重要的,因此,扭转部件设计和构造成在弹性偏转的某个范围上塑性地变形。将认识到的是,关于现有的设计和方法,需要使用专门的组装程序来维持内部管板材垫圈的密封,这通常涉及在操作期间压缩螺栓的重新上紧。即使利用这些程序,内部部件的塑性变形也可由于差异热膨胀而在操作期间发生。如上文注意到的,这已通过本发明避免。
[0021]
根据本发明的某些图示的实施例,封闭组件设计成密封高压壳管式热交换器,并且构造为“螺旋塞”类型,其在压力和变化的热负荷下维持热交换器管板材处的密封。封闭组件的外部密封优选地由隔膜和垫圈组件提供。隔膜垫圈密封优选地由外排推压螺栓维持,并且内部密封优选地由定位在管板材处的第二垫圈提供,该第二垫圈由内排推压螺栓加载。根据某些图示的实施例,热交换器管板材的内部密封负荷通过压缩环、弹性扭转部件以及套筒部件传送。将理解的是,弹性扭转部件在其接触套筒部件和压缩环的区域处枢转。
[0022]
在本发明的某些图示的实施例的组装程序期间,具有管板材垫圈的管束插入热交换器管中,后接套筒部件、弹性扭转部件,并且然后是封闭塞部件,其优选地具有盖和锁环组件。另外,隔膜和隔膜垫圈设成邻近于热交换器管中的封闭塞,以用于提供不泄漏的密封。通过使封闭塞部件围绕热交换器的纵向轴线以一线性运动同轴地转动,并且优选地旋转小于一个单次转动以便设置在锁定位置中,封闭塞部件可移除地固定到热交换器管的开放式端部通道。将认识到的是,负荷承载表面不与彼此负荷承载接触,直到施加封闭塞的最终旋转。
[0023]
根据本发明的某些图示的实施例,封闭塞和热交换器管的开放式端部通道的前述负荷承载表面优选地包括:第一组毂,其设置(例如,机加工)在封闭塞上;以及互补的第二
组毂,其设置(例如,机加工)在热交换器管的开放式端部通道部分上,使得当封闭塞旋转时,第一组毂与第二组毂接合(互相交叉)。将认识到的是,一组或多组毂区段可设在封闭塞和/或热交换器的开放式端部通道上,以便并入凸起区段(例如,轨道),其构造成:(i)防止过度旋转,(ii)提供用于封闭塞的插入的承载表面,同时(iii)防止对封闭塞和热交换器管的开放式端部通道两者的负荷承载表面的损坏。
[0024]
在又一方面,提供的是一种热交换器组件,其包括限定内部室的细长管状热交换器包封件。管板材定位在热交换器包封件的内部室内,从而使内部室分离成壳侧和通道侧。内部部分构造成可移除地接收管束,管束定位在内部室的壳侧内。环形套筒部件定位在热交换器包封件的内部室的通道侧内。环形弹性扭转部件定位在热交换器的内部室的通道侧内,使得套筒部件定位在管板材与弹性扭转部件之间。弹性扭转部件具有内圆周,该内圆周能够相对于其外圆周偏转,以用于扭转弹性扭转部件。另外,热交换器还可包括下者中的一个或多个:i)分隔组件,其中套筒部件定位在热交换器包封件的内部室的通道侧内,以将流体从延伸通过包封件的端口导引至管束中的至少两个或更多个管;ii)管板材垫圈和轴承环,管板材垫圈定位在管板材与形成在热交换器包封件的内部室内的肩部之间,轴承环定位在热交换器包封件的内部室内,其中弹性扭转部件定位在套筒部件与轴承环之间;iii)至少两个端口,其延伸通过包封件,以用于允许流体进入和离开热交换器包封件的内部室的通道侧;iv)弹性扭转部件构造成弹性地偏转直至弹性偏转极限,并且在弹性偏转极限之上塑性地偏转,使得弹性扭转部件弹性地偏转,以适应差异热膨胀并且避免在热交换器在预负荷以及预期压力负荷和热负荷下时对热交换器的构件的损坏;v)弹性扭转部件构造成在弹性扭转部件接触套筒部件的第一接触区域处以及在弹性扭转部件接触轴承环的第二接触区域处枢转;vi)弹性扭转部件具有带有倒圆拐角的四边形横截面;vii)多个弹性扭转部件相对于彼此串联堆叠;viii)弹性扭转部件构造成具有外半径“a”和内半径“b”,其中外半径小于构造成接收管束的内部室的通道的内半径,其中“a”与“b”的比率小于3;ix)弹性扭转部件构造成具有为其弹性偏转极限的近似50%的高度“h”,并且具有厚度“t”,使得弹性扭转部件在其弹性偏转极限之上塑性地变形;x)封闭组件,其用于密封热交换器包封件的内部室的通道侧,其中封闭组件包括锁环部件和盖部件,锁环部件和盖部件利用锁定组件可移除地固定到热交换器包封件;xi)锁定组件包括多个间隔开的锁环毂区段,其构造成与形成在热交换器包封件的圆柱形内表面部分上的对应的通道毂区段互相交叉;xii)隔膜和隔膜垫圈,隔膜邻近于锁环和盖部件定位在内部室的通道侧内,隔膜垫圈在锁环部件可移除地固定到热交换器包封件时抵靠隔膜而被压缩;xiii)封闭组件还包括多个第一细长压缩部件和多个第二细长压缩部件,第一细长压缩部件沿着封闭组件的外半径部分设置,以便将力传送至第一压缩环,第一压缩环将力传送至隔膜垫圈和隔膜的边缘部分,第二细长压缩部件沿着封闭组件的内半径部分设置,以便将力传送至第二压缩环,第二压缩环相对于隔膜的部分传送力,从而使隔膜的部分在封闭组件可移除地固定到热交换器包封件时远离盖部件并且朝向弹性扭转部件偏转;xiv)管板材、套筒部件、轴承环、第一和第二压缩环、锁环以及第一和第二压缩部件构造成在封闭组件固定到热交换器包封件时保持弹性直至或高于来自预负荷、热负荷以及压力负荷的总轴向负荷;xv)其中细长压缩部件被预加载,压缩部件将预负荷通过第一轴向负荷路径施加到弹性扭转部件的第一接触区域,第一接触区域将预负荷通过穿过弹性扭转部件的扭转负荷路径传送至弹性扭转部件的第二接触区
域,第二接触区域将预负荷通过第二轴向负荷路径传送至管板材垫圈;xvi)其中来自热交换器中的过程流体的压力负荷在正常的规定阈值范围内,弹性扭转部件构造成弹性地变形,从而使得其外圆周能够朝向封闭组件沿轴向移动,来自热交换器包封件中的过程流体的压力负荷通过使封闭组件远离管板材变形而减小弹性扭转部件上的负荷,并且弹性扭转部件构造成弹性地偏转直至弹性偏转极限并且在弹性偏转极限之上塑性地偏转,使得弹性扭转部件适应差异热膨胀,以避免在热交换器在预负荷以及预期压力负荷和热负荷下时对热交换器的构件的损坏。
[0025]
在又一方面,提供的是一种用于组装管式热交换器组件的过程,该过程包括提供细长热交换器包封件,其具有内部室并且限定纵向轴线并且具有开放式圆柱形通道端部。提供具有锁定组件的封闭组件,锁定组件构造成固定到细长热交换器包封件的开放式圆柱形通道端部。封闭组件的锁定组件沿着热交换器的内部室的纵向轴线沿轴向插入到开放式圆柱形通道端部中,使得细长热交换器包封件的内壁和封闭组件中的每个的负荷承载表面彼此不接触。封闭组件围绕细长热交换器包封件的纵向轴线转动,以使锁定组件可移除地固定到协作的锁定组件,该协作的锁定组件设在细长热交换器包封件的内壁上,以使负荷承载表面彼此接触,使得负荷在封闭组件与细长热交换器之间传递。另外,用于组装管式热交换器的过程还可包括下者中的一个或多个:i)封闭组件转动小于360度,以使封闭组件的锁定组件可移除地固定到设在细长热交换器包封件的内壁上的协作的锁定组件;ii)封闭组件的锁定组件和设在细长热交换器包封件的内壁上的锁定组件协作地形成卡口锁定组件;iii)卡口锁定组件包括:多个间隔开的锁环毂区段,其设在封闭组件的外表面部分上;以及多个间隔开的锁环毂区段,其设在细长热交换器包封件的内壁上,构造成与形成在封闭组件上的对应的通道毂区段互相交叉;iv)在插入锁定组件之前,将管板材垫圈沿着细长热交换器包封件的纵向轴线沿轴向插入到开放式圆柱形通道端部中,以定位成邻近细长热交换器包封件中形成的通道肩部构造;将管板材沿着细长热交换器包封件的纵向轴线沿轴向插入到开放式圆柱形通道端部中,以定位成邻近管板材垫圈,以便在细长热交换器包封件的内部室内限定壳侧和通道侧,其中内部室构造成可移除地接收定位在内部室的壳侧内的管束;将环形套筒部件沿着细长热交换器包封件的纵向轴线沿轴向插入到开放式圆柱形通道端部中,以定位成邻近管板材;将弹性扭转部件沿着细长热交换器包封件的纵向轴线插入到开放式圆柱形通道端部中,以便定位成邻近套筒部件;将轴承环沿着细长热交换器包封件的纵向轴线插入到圆柱形通道的开放式端部中,以便定位成邻近弹性扭转部件;以及将隔膜沿着细长热交换器包封件的纵向轴线插入到圆柱形通道的开放式端部中,以便定位成邻近轴承环;v)调节沿着封闭组件的外半径部分设置的多个第一外部细长压缩部件,多个第一外部细长压缩部件在封闭组件中沿着封闭组件的纵向轴线同轴地延伸,以便将力传送至第一压缩环,第一压缩环将力传送至隔膜垫圈和隔膜的边缘部分,以便将隔膜垫圈抵靠隔膜压缩;以及调节沿着封闭组件的内半径部分设置的多个第二内部细长压缩部件,多个第二内部细长压缩部件在封闭组件中沿着封闭组件的纵向轴线同轴地延伸,以便将力传送至第二压缩环,第二压缩环相对于隔膜的部分传送力,从而使隔膜的部分在封闭组件固定到热交换器包封件时远离封闭组件并且朝向热交换器组件的弹性扭转部件偏转;vi)其中管板材、套筒部件、第一和第二压缩环、封闭组件以及第一和第二细长压缩部件中的每个构造成在封闭组件固定到热交换器包封件时保持弹性直至或高于来自预负荷、热负荷以
及压力负荷的总轴向负荷;vii)其中当细长压缩部件被预加载时,压缩部件将预负荷通过第一轴向负荷路径施加到弹性扭转部件的第一接触区域,第一接触区域将预负荷通过穿过弹性扭转部件的扭转负荷路径传送至弹性扭转部件的第二接触区域,第二接触区域将预负荷通过第二轴向负荷路径传送至管板材垫圈;viii)其中扭转负荷通过应力的增加和扭转旋转来抵抗,从而使得弹性扭转部件的第一接触区域能够朝向管板材移动;ix)其中封闭组件包括将具有外径的圆柱形形状的盖部件定位成与圆柱形形状的锁环部件的内部部分同心地固定,该圆柱形形状的锁环部件限定圆柱形外表面部分和圆柱形形状的内部部分,其中外表面部分设有封闭组件的锁定组件。
[0026]
在再一方面,提供的是一种构造成可移除地固定到热交换器组件的内部室的开放式通道端部的封闭组件,该封闭组件包括圆柱形形状的锁环部件,其限定圆柱形外表面部分和圆柱形形状的内部部分。外表面部分设有多个间隔开的锁环毂区段,其构造成与形成在热交换器组件的圆柱形内表面部分上的对应的通道毂区段互相交叉。圆柱形形状的盖部件与锁环部件的内部部分同心地固定。另外,封闭组件还可包括下者中的一个或多个:i)其中盖部件可移除地固定到锁环部件,其中锁环部件具有带有肩部构造的内径表面,肩部构造构造成接收设在盖部件的外径表面上的协作的肩部构造;ii)每个锁环毂区段以从锁环部件的外表面部分延伸的规定角度延伸,构造成与设在每个通道毂区段中的对应的成角度毂区段互相交叉,每个通道毂区段形成在热交换器组件的圆柱形内表面部分上;iii)向上延伸的凸缘部件,其设在锁环部件上,构造成使封闭组件到热交换器组件的内部室中的旋转停止;vi)隔膜,其构造成定位成邻近于锁环和盖部件;v)多个可调节的外部细长锁环压缩部件,其能够可移除地固定在锁环部件中,每个外部细长锁环压缩部件穿过在锁环部件中与纵向轴线同轴地形成的相应孔,以便将力传送至第一压缩环,第一压缩环将力传送至隔膜的边缘部分;以及隔膜垫圈,其抵靠隔膜而被压缩,使得当锁环部件可移除地固定到管状热交换器组件的内部室时,隔膜通过外部细长锁环压缩部件的调节来定位在隔膜垫圈和第一压缩环部件中间;vi)多个内部可调节的细长盖压缩部件,其能够可移除地固定在盖部件中,每个内部细长盖压缩部件穿过在盖部件中与纵向轴线同轴地形成的相应孔,以便将力传送至第二压缩环,第二压缩环相对于隔膜的部分传送力,从而使隔膜的部分在封闭组件可移除地固定到热交换器组件的内部室的开放式端部时远离盖部件并且朝向热交换器组件的内部室偏转;vii)其中第一和第二压缩环、压缩杆以及压缩螺栓构造成在封闭组件可移除地固定到热交换器组件的内部室的开放式端部时保持弹性直至或高于来自预负荷、热负荷以及压力负荷的总轴向负荷;viii)其中锁部件的外表面部分设有基本上垂直于锁环部件的纵向轴线形成的直立凹槽,其构造成可滑动地接收在垂直于热交换器轴线的纵向轴线形成在热交换器组件的内表面部分中的对应凹口中,以用于便于锁环部件插入热交换器组件的内表面部分中。
[0027]
在再一方面,提供的是一种用于热交换器组件的操作方法,该热交换器组件具有管状热交换器包封件,该管状热交换器包封件构造成用于在加热和冷却序列期间适应在热交换器包封件的内部室中的内部构件的差异热膨胀,该方法包括在热交换器包封件的内部室内利用弹性扭转部件接收预负荷,使得弹性扭转部件接收扭转负荷并且弹性地偏转,以适应预负荷。利用热交换器组件接收热负荷,以使热交换器包封件的内部室中的内部构件差异地热膨胀,使得由弹性扭转部件接收的扭转负荷增加并且进一步弹性地偏转以适应热
负荷。另外,用于热交换器的操作方法还可包括下者中的一个或多个:i)在热交换器包封件的内部室内接收压力负荷,压力负荷通过使可移除地附接到热交换器包封件的封闭组件弹性地偏转并且使弹性扭转部件放松以适应压力负荷来减小由弹性扭转部件接收的扭转负荷;ii)其中使内部构件差异地热膨胀包括适应至少轴承环、弹性扭转部件、套筒部件以及管板材的差异热膨胀,而不引起至少轴承环、弹性扭转部件以及套筒部件的塑性变形;ii)其中细长压缩部件用于预加载弹性扭转部件,使得压缩部件将预负荷通过第一轴向负荷路径施加到弹性扭转部件的第一接触区域,第一接触区域将预负荷通过穿过弹性扭转部件的扭转负荷路径传送至弹性扭转部件的第二接触区域,第二接触区域将预负荷通过第二轴向负荷路径传送至管板材垫圈;iii)其中弹性扭转部件构造成在弹性扭转部件接触套筒部件的第一接触区域处以及在弹性扭转部件接触轴承环的第二接触区域处枢转;iv)将管板材垫圈沿着细长热交换器包封件的纵向轴线沿轴向插入到开放式圆柱形通道端部中,以定位成邻近细长热交换器包封件中形成的通道肩部构造;将管板材沿着细长热交换器包封件的纵向轴线沿轴向插入到开放式圆柱形通道端部中,以定位成邻近管板材垫圈,以便在细长热交换器包封件的内部室内限定壳侧和通道侧,其中内部室构造成可移除地接收定位在内部室的壳侧内的管束;将环形套筒部件沿着细长热交换器包封件的纵向轴线沿轴向插入到开放式圆柱形通道端部中,以定位成邻近管板材;将弹性扭转部件沿着细长热交换器包封件的纵向轴线插入到开放式圆柱形通道端部中,以便定位成邻近套筒部件;将轴承环沿着细长热交换器包封件的纵向轴线插入到圆柱形通道的开放式端部中,以便定位成邻近弹性扭转部件;以及将隔膜沿着细长热交换器包封件的纵向轴线插入到圆柱形通道的开放式端部中,以便定位成邻近轴承环;以及v)将封闭组件附连到内部室的开放式端部部分,封闭组件包括可偏转的隔膜和轴承环,并且还包括用于将预负荷施加到弹性扭转部件的机构。
[0028]
本文中公开的封闭组件的这些及其它独特的特征将根据以下描述和附图而变得更容易显而易见。
附图说明
[0029]
为了使公开的系统和方法所属领域中的普通技术人员将更容易地理解如何制作和使用说明根据某些图示的实施例的多种非限制性、示例性、发明性方面的公开的系统和方法,可参考附图,其中:图1a图示如在美国专利no. 4750554中描述的现有技术的管状热交换器和封闭组件的局部横截面视图;图1b图示已根据图示的实施例构建的管状热交换器和封闭组件的局部横截面视图;图2图示图1b的分解局部横截面视图,其描绘根据图示的实施例的弹性扭转部件;图3图示根据图示的实施例的压缩隔膜密封件的分解局部横截面视图;图4图示根据图示的实施例的图1b的锁环部件的局部透视图;图5图示图1b的热交换器的开放式通道端部部分的内径的局部透视图;图6图示根据图示的实施例的线性地插入到图5的热交换器的开放式通道端部部分中的图4的锁部件的局部透视图;图7图示根据另一图示的实施例的具有多个弹性扭转部件的管状热交换器和封闭组件的局部横截面视图;以及
图8图示根据另一图示的实施例的b型热交换器封闭塞组件的局部横截面视图。
具体实施方式
[0030]
现在参考附图更全面地描述本发明,在附图中示出了本发明的某些图示的实施例。本发明不以任何方式限于图示的实施例,因为下文描述的图示的实施例仅仅为本发明的实例,其可以以多种形式体现,如由本领域技术人员认识到的。因此,将理解的是,本文中公开的任何结构和功能细节将不被解释为限制性的,而仅仅作为权利要求书的基础,以及作为用于教导本领域技术人员以多种方式采用本发明的代表。此外,本文中使用的用语和短语不旨在为限制性的,而是提供本发明的可理解的描述。
[0031]
除非另外限定,否则本文中使用的所有技术和科学用语都具有与本发明所属领域中的普通技术人员通常所理解的相同的含义。尽管类似于或等同于本文中描述的方法和材料的任何方法和材料也可用于本发明的实践或测试中,但是现在描述示例性方法和材料。本文中提到的所有专利出版物都通过引用并入本文中,以公开和描述关于其而引用出版物的方法和/或材料。
[0032]
必须注意的是,如本文中和所附权利要求书中使用的,单数形式“一”、“一种”和“该”包括复数个引用对象,除非上下文另外清楚地指出。因此,例如,对“一刺激”的引用包括多个这样的刺激,而对“该信号”的引用包括对本领域技术人员已知的一个或多个信号及其等同体的引用,等等。
[0033]
众所周知的构件、材料或方法不一定极详细地描述,以便避免使本公开不清楚。本文中公开的任何具体的结构和功能细节将不被解释为限制性的,而是仅仅作为权利要求书的基础,以及作为用于教导本领域技术人员以多种方式采用本发明的代表性基础。
[0034]
现在将更全面地描述本公开,但是并非本公开的所有实施例都有必要示出。另外,在不脱离本公开的实质范围的情况下,可作出许多修改以使特定情形或材料适于本公开的教导。
[0035]
将认识到的是,本发明克服与现有技术的热交换器封闭组件相关联的许多问题。例如,参考图1a,描绘的是如美国专利no. 4750554中描述的用于壳管式热交换器的现有技术的封闭组件。图示的是壳管式热交换器的区段,该壳管式热交换器具有壳和包含管状束的通道。通道具有端口,其提供用于使流体进入和离开束的管的通路。端部封闭组件或“塞”由锁环9和盖19组成,盖19并入隔膜8和隔膜垫圈10。封闭塞组件为可移除的,以便实现可移除的管状束的插入和抽出,同时还能够维持紧密密封并在高压之下吸收所得的负荷。热交换器的开放式通道在其端部处由封闭塞组件(即,盖19和锁环9)封闭。锁环部件9包含机构,其用以通过使用螺栓11和压缩环20压缩垫圈10来抵靠隔膜8密封交换器通道。
[0036]
壳侧流体通过管板材1和管板材垫圈6与进入管(未示出)的通道流体分离。典型地,热交换器需要分隔组件来容纳双程管侧流布置。分隔组件可包括套筒部件2、分隔板3、分隔盖4和/或环17,以将流体从通道入口喷嘴通过两个或更多个管程导引至出口端口。本领域技术人员将认识到,分隔件可应用于入口或出口。
[0037]
继续参考图1a的现有技术的热交换器,锁环部件9使用螺纹来抵靠热交换器的壳的通道固定-锁环9设有阳螺纹并且通道设有对应的阴螺纹。将理解和认识到的是,螺纹为负荷承载表面,使得当组装热交换器时,螺纹吸收螺栓的预负荷。此外,在热交换器的操作
期间,流体静力负荷施加到塞盖组件19,该流体静力负荷继而直接地传递至前面提到的螺纹。
[0038]
现在参考图1b,图示的是已根据本发明的图示的实施例构建的管状热交换器和封闭组件的局部横截面视图,该管状热交换器和封闭组件总体上由数字100标记。类似于图1a的现有技术的热交换器,热交换器100为壳管式热交换器,其包括包封件70,其中包封件70具有与通道部件7一体地形成或连结到通道部件7的壳部件15,其中包封件70构造成接收管束(未示出)。热交换器通道部件7优选地具有至少两个端口,其提供用于使流体流进入和离开插入的束的管的通路。端部封闭组件或“封闭塞”优选地由环形锁环部件9、压缩环21和22以及环形盖部件19组成。还包括隔膜8和隔膜垫圈10。封闭塞为可移除的,以便实现可移除的管状束的插入和抽出,同时还能够在热交换器100的操作期间维持紧密密封并在高压之下吸收所得的负荷。通道部件7的开放式端部部分由封闭塞(例如,盖19和锁环9)封闭(密封)。锁环部件9优选地包含器件,其用以通过使用螺栓12、推杆14以及压缩环21压缩垫圈10来抵靠隔膜8密封热交换器通道7。如图1b中示出的,盖部件19可移除地固定到锁环部件9,使得锁环部件9具有内径表面,该内径表面优选地形成有埋头孔构造,其构造成接收设在盖部件9的外径表面上的协作埋头孔构造。根据图示的实施例,盖部件19的最小内径优选地小于锁环部件9的最大外径,以在其之间形成埋头孔构造。
[0039]
继续参考图1b,壳侧流体流通过管板材1和管板材垫圈6与进入管(未示出)的通道流体流分离。热交换器100典型地需要分隔组件以容纳双程管侧流布置。然而,本领域技术人员将认识到,本公开的发明方面可与单程热交换器或具有多于2程的热交换器一起使用。在该实施例中,分隔组件包括套筒部件2、分隔板3以及分隔盖4,以将流体从通道入口喷嘴通过两个或更多个管程导引至出口端口。将理解的是,分隔件可应用于入口或出口。
[0040]
封闭塞组件的锁环部件9优选地使用卡口型锁定组件来抵靠热交换器100的壳的通道7的开放式端部部分固定,该卡口型锁定组件优选地由形成的毂区段23a和23b组成。现在参考图4-6(并且继续参考图1b),锁环部件9优选地形成有毂区段23a,毂区段23a形成在环部件9的周向外表面部分上,其中每个毂区段23a通过半圆柱形的非毂区段24a分离。类似地,热交换器100的通道7的开放式端部部分优选地形成有毂区段23b,毂区段23b形成在热交换器通道7的内周向端部部分上,通过半圆柱形的非毂区段24b分离。锁环9的多个间隔开的锁环毂区段23a构造成与对应的通道毂区段23b互相交叉,对应的通道毂区段23b形成在热交换器100的通道7的圆柱形内表面部分上。
[0041]
根据图示的实施例,在封闭塞部件(例如,环部件9和盖部件19)在热交换器100的通道7的端部部分内的组装期间,锁环部件9沿着热交换器100的内部室的纵向轴线同轴地插入到开放式圆柱形通道端部7中,使得环部件9中的每个的负荷承载表面和热交换器100的开放式圆柱形通道端部7的内径使得没有负荷在封闭塞组件的环部件9与热交换器100之间传递(与前面提到的现有技术的结构和方法对比)。仅在转动锁环部件9以用于使其与细长热交换器100锁定接合之后,才存在负荷从热交换器100至封闭塞部件的传递。这通过以下方式实现:使封闭塞组件的环部件9围绕细长热交换器100的内部室的纵向轴线转动,以使环部件9的毂区段23a与设在热交换器100的开放式圆柱形通道端部7的内径上的协作毂区段23b可移除地固定,从而便于负荷从热交换器100的通道7至封闭塞组件的环部件9的传递。将认识到的是,环部件9转动小于360度,以使环部件的毂区段23a与形成在热交换器100
的开放式圆柱形通道端部7的内径部分上的对应的毂区段23b可移除地固定(互相交叉)。在一个实施例中,环部件9转动近似22.5度,其中每个毂区段23a和23b沿着它们分别形成在其上的热交换器100的开放式圆柱形通道端部7和环部件9的圆周部分延伸近似22.5度。
[0042]
在其它实施例中,将进一步认识到的是,锁环部件9和盖部件19可集成为单个整体构件。另外,在再一些其它实施例中,锁环部件9可分成两个或更多个构件。在另外的实施例中,毂区段23a和23b可在锁环部件9的一部分处相对于另一部分具有不同的形状或设计。
[0043]
根据图示的实施例,前述的毂构造可以以八个区段构造,使得存在八个带毂区段(23a和23b)和八个无毂区域(24a和24b),它们分别设在环部件9和热交换器100的开放式圆柱形通道端部7的内径上。然而,本领域技术人员将容易认识到,在不脱离本公开的发明方面的情况下,毂区域的数量可变化。例如,可存在与1、2、3、4、5、6、7、8、9、10、11或12个无毂区域组合的1、2、3、4、5、6、7、8、9、10、11或12个带毂区域。
[0044]
在封闭塞与热交换器的开放式通道7的组装期间,并且与上文描述的现有技术对比,毂23a和23b的负荷承载表面在封闭塞组件插入到热交换器通道7中期间没有损坏。该布置还确保隔膜8相对于热交换通道7的恰当对准。另外,将认识到的是,前述毂区段23a和23b可形成(例如,机加工)有螺纹螺距,使得封闭塞组件在其旋转时在热交换器100的通道7中沿轴向向内前进。
[0045]
继续参考图4-6,并且根据某些实施例,直立的轨道部件25形成为邻近于通道毂23b或锁环毂23a或者两者,以在插入期间防止毂23a、23b接触金属表面中的任何表面。将认识到的是,使轨道25设在锁环部件9上可为优选的,这是由于制造可更容易,因为锁环9可独立地旋转,而热交换器100的通道7在制造期间不可独立地旋转。
[0046]
根据另外的图示的实施例,环形直立的止动部件26(凸缘)可设在锁环部件9上,其对应于本文中引用的隔膜8的位置。止动部件26优选地围绕锁环部件9的外圆周延伸,以确保在锁环9旋转到位时形成的无毂槽形状的腔被覆盖,并且没有外来材料可进入。注意,这便于盖部件19和隔膜8被正确地定位,而不需要基于外部测量来“估计”。这与现有技术的螺旋塞设计形成对比,在现有技术的螺旋塞设计中,锁环部件的位置由可引入变化的转动次数和螺纹螺距来确定。将认识到的是,图6中示出的止动部件26的构造将被理解为说明性构造,因为可提供其它构造,以确保在锁环9旋转到位时形成的无毂槽形状的腔被覆盖,并且没有外来材料可进入。
[0047]
如图4-6中示出的,毂区段23a、23b优选地垂直于热交换器100的通道7和锁环部件9的纵向轴线对准。将认识到的是,在其它实施例中,毂区段可相对于热交换器100的通道7和锁环部件9的纵向轴线以一定角度形成(例如,机加工),使得在锁环部件旋转时,锁环部件9前进较小的距离而进入通道7。将进一步认识到的是,针对毂区段23a和23b的毂大小和形状不需要对于所有毂区段而言均为相同的,这视锁环部件9和通道7组件的长度容许锁环部件9自由地插入通道7中并且锁环部件9和通道7的毂区段23a和23b与彼此对应而定。
[0048]
现在具体地参考图6,封闭塞组件的锁环部件9示出为插入到热交换器的通道7的开放式端部中。将认识到的是,锁环部件9插入到通道7中,使得锁环9和通道7的无毂区域24a、24b分别允许带毂区域23a、23b滑动经过。例如,封闭塞组件可以以与最终锁定取向成大约22.5
°
的角度加载(锁环部件9)到热交换通道7中,使得锁环9和通道7的无毂区域24a、24b分别允许带毂区域23a、23b滑动经过,使得防止负荷承载表面由轨道接触。一旦封闭塞
部件完全地插入到热交换器的通道7中,封闭塞部件就旋转到锁定位置中。例如,封闭塞组件可顺时针转动22.5
°
到锁定位置中。该旋转可以以许多方式来实现,例如,使用螺栓连接到锁环部件9的杆以提供足够的杠杆作用来人工地转动锁环部件9,或者通过使用附接到锁环部件9和起重机的线缆以提供向上的切向力,或者通过使用安装到热交换器通道7的圆形齿条齿轮和安装到锁环部件9的对应小齿轮,其中杠杆用于转动小齿轮,该小齿轮继而施加切向力以旋转锁环部件9。可提供另外的安全特征,由此凹口27设在锁环部件9的一组毂中,并且对应的引导凹口28形成在热交换器的通道7的开放式端部部分中,以确保锁环部件7仅可相对于通道7沿一个取向插入。
[0049]
参考图4,锁环9和通道7上的外部标记进一步强调锁环部件9的正确取向,并且直立的止动部件29可邻近无毂区域24b形成在通道7的开放式端部部分中,具有比设在毂区段23a中的轨道27的宽度更宽的宽度,以确保相应的毂23a和23b在插入期间不可意外地旋转并过早地接合,同时还有助于引导锁环9的插入,使得毂23a和23b保持被保护。
[0050]
现在参考图1b和图3,隔膜8优选地抵靠通道盖部件19接合,使得来自热交换器的通道7中的流体流的压力负荷横跨隔膜8传送至通道盖部件19。通道盖部件19上的压力负荷然后传送至锁环部件9。通道7优选地由隔膜垫圈10密封。隔膜垫圈10优选地由沿着锁环部件9的外排沿轴向设置的多个压缩螺栓12和推杆14(统称为“压缩部件”)压缩,多个压缩螺栓12和推杆14穿过优选地形成在锁环部件9中的螺纹孔。这些压缩螺栓12和推杆14经由松弛的外部压缩环21(设在锁环部件9与隔膜8中间)将力传送至隔膜8及其隔膜垫圈10的边缘部分。将理解的是,内排压缩螺栓11、13可如由弹性扭转部件60和轴承环50的直径要求的那样沿着环形盖部件19或锁环9部件的半径定位,如下文描述的。
[0051]
将认识到的是,隔膜8构造成优选地在螺栓预负荷和内部压力之下偏转一定量,由此如果封闭塞部件组件没有沿轴向向内足够远地插入热交换器100的通道7中,则锁环部件9的外排推压螺栓14将需要进一步前进以使隔膜垫圈10密封,并且盖部件19的内排推压螺栓13将需要进一步前进以使管板材垫圈6密封,由此在压力施加到通道7时使隔膜8在更大程度上变形。在制造时间期间,可执行尺寸检查,以确保机加工公差对使封闭件恰当地定位而言为可接受的。在制造之后,垫片可在隔膜8与封闭塞组件之间添加。备选地,封闭塞组件上的毂可以以一定螺距机加工,使得封闭塞组件在其旋转时在热交换器100的通道7中沿轴向向内前进。通过使封闭塞组件旋转直到其接触隔膜8,然后使外排推压螺栓14前进以压缩垫圈21,然后缩回外排推压螺栓14,封闭塞可进一步旋转以最小化封闭塞组件与隔膜8之间的空隙。一旦尺寸检查被执行,封闭塞组件就以线性运动插入到热交换器100的通道7中,这可使用叉车、起重机或搬运管束已经需要的其它设备组合来实现,因此与前面提到的现有技术对比,没有特殊的工具或设备为必要的。
[0052]
在组装期间,并且现在参考图1b和图3,将认识到的是,当盖部件19的内排压缩螺栓13被上紧时,轴向负荷通过推杆11传递至松弛的(内部)压缩环22,通过隔膜8传递至由轴承环50、弹性扭转部件60以及套筒部件2组成的管板材加载组件,使得管板材垫圈6抵靠壳15和管板材1的后面而被压缩。该轴向负荷被称为预负荷。将认识到的是,该预负荷防止由于热交换器100的壳侧和管侧之间的压差而产生的泄漏。
[0053]
将进一步认识到的是,前面提到的管板材加载组件优选地适应热负荷,该热负荷引起通道7、管板材1和前述管板材加载组件(例如,轴承环50、弹性扭转部件60以及套筒部
件2)之间的差异热膨胀。差异热膨胀由两种机制引起。第一种是当通道7由于热过程流体流而比管板材1和管板材加载组件(例如,轴承环50、弹性扭转部件60以及套筒部件2)更冷时,该热过程流体流与内部构件密切接触,但是通过套筒部件2以及通过通道7中的热损失到周围环境或者通过流体温度的快速改变而在很大程度上屏蔽通道7,该快速改变使相对薄的内部构件的温度以比相对厚的通道更快的速率改变。这样的条件将不可避免地在启动(加热)期间以及在混乱或工厂跳闸和操作温度随后重建期间发生。第二种机制是当用于形成通道7的材料具有比用于管板材1和管板材加载组件(例如,轴承环50、弹性扭转部件60以及套筒部件2)的材料更低的热膨胀系数时。例如,这在碳钢用于通道7并且不锈钢用于热交换器内部的构件时为常见的。
[0054]
当管板材1和管板材加载组件(例如,轴承环50、弹性扭转部件60以及套筒部件2)的总热膨胀大于通道7的总热膨胀时,所得的差异热膨胀必须通过热交换器100中的变形来适应。由于压力的安全控制所需的通道7的相对高的刚度,故变形主要发生在管板材加载组件(例如,轴承环50、弹性扭转部件60以及套筒部件2)中的相对较低刚度的部件中。如果由该变形引起的应力超过部件的屈服应力,则造成不可恢复或塑性的变形。套筒部件2(由于形成在其中以用于容许流体进入热交换器100的内部室的穿孔的存在)周围不具有均一的刚度。因此,热负荷可造成套筒部件2的不均匀塑性变形,使得垫圈22上的负荷不可通过重新上紧内排压缩螺栓13而简单地恢复。当热负荷返回到正常时,管板材加载组件(轴承环50、弹性扭转部件60以及套筒部件2)中的剩余的轴向压缩负荷减小成低于在上紧盖部件的压缩螺栓13期间施加的负荷。如果塑性变形足够严重,则该负荷可减小成低于密封管板材垫圈6所需的最小负荷。这造成在热交换器100的壳侧和管侧之间的不合期望的泄漏。
[0055]
根据图示的实施例,为了在热交换器中没有塑性变形的情况下适应差异热膨胀,提供的是顺应性部件,如现在描述的。顺应性部件通过弹性扭转部件60的实施来实现,如图1b和图2中示出的。如示出的,环形弹性扭转部件60优选地在外圆周部分处、在第一接触区域61处、在面对管板材1靠近其外半径的侧部上接触套筒部件2,并且在内圆周部分处、在第二接触区域63处、在面对隔膜8靠近其内半径的侧部上接触轴承环50。当内部压缩螺栓13被预加载时,轴向力在弹性扭转部件60的前面提到的接触区域61和63处通过弹性扭转部件60传送。在不同半径处施加在弹性扭转部件60上的这些力在弹性扭转部件60上产生扭转负荷,使得弹性扭转部件60的内圆周能够沿轴向方向相对于其外圆周偏转,以用于扭转弹性扭转部件60,使得该扭转负荷通过应力的增加和扭转旋转来抵抗,这允许弹性扭转部件60的外半径朝向封闭塞组件的隔膜8移动,并且允许其内半径朝向管板材1移动。
[0056]
将认识到的是,轴承环50在旋转期间保护隔膜8免受由于与弹性扭转部件60接触而导致的损坏。当热交换器100在操作中时,压力负荷将通过使封闭塞组件远离管板材1变形而减小弹性扭转部件60上的负荷,但是差异热膨胀将增加负荷。将理解的是,弹性扭转部件60设计并构造成弹性地向上变形,直到达到最大所需的差异热膨胀。当负荷在热交换器操作期间保持低于该最大阈值时,弹性扭转部件60中的负荷将在热负荷和压力负荷被移除时返回至初始预负荷。根据图示的实施例,弹性扭转部件60可形成为具有在25 mm到75 mm之间的偏转范围—然而,弹性扭转部件60将不被理解为限于前述偏转范围,因为其可根据热交换器100的尺寸大小的尺度而构造。然而,如果遇到过度的差异热膨胀(诸如在过程流体的非预期热漂移期间),则弹性扭转部件60塑性地变形,以限制施加到封闭塞组件的负
荷,以用于防止封闭塞组件和/或由隔膜8提供的密封的失效。将认识到的是,当热负荷和压力负荷被移除时,弹性扭转部件60上的负荷将下降至低于初始预负荷,并且可下降成低至零。弹性扭转部件60可由在高温下不经受腐蚀、蠕变和强度损失的材料(优选为包括(但不限于)inconel 625和inconel 718的高镍合金)形成。
[0057]
现在参考图2,现在描述针对弹性扭转部件60的设计的说明性相关尺寸。将理解的是,尺寸“a”为外半径,尺寸“b”为内半径,尺寸“h”为高度,并且尺寸“t”为弹性扭转部件60的厚度。尺寸“a”小于由热交换器100的通道7限定的内半径,以便为径向热膨胀和在负荷下的旋转提供间隙。对于轴向负荷而言,比率a/b大于1并且优选地小于3,以在弹性扭转部件60中产生扭转负荷。尺寸“h”为在施加预负荷和操作负荷(压力负荷和热负荷)时其弹性偏转极限的近似50%。尺寸“t”选择成使得当弹性扭转部件60由预负荷位移和设计差异热膨胀的总和压缩使得弹性扭转部件60弹性地变形时,轴向负荷低于管板材垫圈6上的最大可允许负荷。弹性扭转部件60的材料选择成使得部件将在该最大可允许负荷之上塑性地变形。将认识到的是,管板材1、套筒部件2、轴承环50、压缩环22、压缩杆11以及压缩螺栓13设计成保持弹性直至或高于来自预负荷、热负荷以及压力负荷的总轴向负荷。
[0058]
将认识到的是,在图示的实施例(例如,图2和图3)中,弹性扭转部件60将被理解为具有带有倒圆拐角部分的四边形横截面。在备选的图示的实施例中,可使用针对弹性扭转部件60的横截面的其它构造,包括矩形形状或具有大体上倒圆侧部的形状。另外,在本文中图示的实施例中,管板材加载组件包括单个弹性扭转部件60。将理解的是,在一些实施例中,为了满足对施加到管板材垫圈6的最小压力和施加到隔膜8的最大位移的设计需求,弹性扭转部件60可设计成具有高刚度,使得最大的热膨胀在没有塑性变形的情况下不可被适应。在这样的情况下,可串联堆叠多于一个的弹性扭转部件60,以增加热膨胀能力。例如,图7图示使用三个弹性扭转部件60的设计。将认识到的是,当利用奇数数量的弹性扭转部件60时,内部压缩螺栓(11、13和22)可以以常见螺栓圆半径设在盖板部件19中。并且,当利用偶数数量的弹性扭转部件60时,内部压缩螺栓优选地以较大的螺栓圆半径定位在锁环部件9中。另外,在具有多个弹性扭转部件60的设计中,优选地包括对准环,以用于维持彼此对准。
[0059]
现在参考图3,图示的是在压缩螺栓13和14的预加载以及从热交换器100的通道7施加压力之后的隔膜8的行为。如示出的,在隔膜垫圈10处,压缩环21远离封闭塞组件的锁环部件9移位,以压缩隔膜8和隔膜垫圈10。当从热交换器100的通道7施加压力时,隔膜8变形,直到其在区域31中靠在锁环部件9和盖板部件19上。这在隔膜8中以比压缩环21的半径更小的半径产生具有高弯曲应变的区域。为了防止隔膜8的破裂,压缩环21优选地为更宽的,并且形成有弯的表面,以减小弯曲应变。
[0060]
类似于外部压缩环21,内部压缩环22远离封闭塞组件的盖部件19移位,以压缩隔膜8和管板材加载组件。如示出的,隔膜8在施加来自热交换器的通道7的压力时围绕内部压缩环22的两侧弯曲,从而在隔膜8中产生具有高弯曲应变的两个区域。为了防止隔膜8的破裂,内部压缩环22也可制得更宽,并且被赋予弯的表面,以减小弯曲应变。
[0061]
关于上文描述的某些图示的实施例,将认识到的是,本文中描述的多种非限制性实施例可被单独地使用、组合或选择性地组合以用于具体应用。此外,可使用上文的非限制性实施例的多种特征中的一些,而没有其它描述的特征的对应使用。因此,前面的描述应当被认为仅仅是本发明的原理、教导以及示例性实施例的说明,而不是对其的限制。
[0062]
例如,存在a型和b型闩锁封闭件。上文图示的实施例涉及a型,其典型地用于供给流出物类型的应用,其中壳侧和管侧流体并非独立的,使得管板材可仅被设计用于压差。然而,图示的实施例将不被理解为限于这样的a型闩锁封闭件,因为其还包括b型封闭件,在该b型封闭件中,管板材焊接到通道,并且不存在对加载管板材垫圈的需求,并且因此没有内排螺栓,如例如图8中示出的。将进一步理解的是,图示的实施例可与用于实现内部密封的多种现有技术方法一起利用。
[0063]
将理解的是,上文描述的布置仅为图示的实施例的原理的应用的说明。许多修改和备选的布置可在不脱离图示的实施例的范围的情况下由本领域技术人员设计出,并且所附权利要求书旨在涵盖这样的修改和布置。