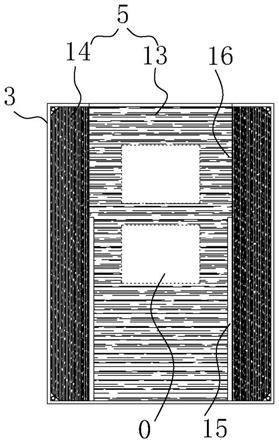
一种vc均热板下盖板毛细结构
技术领域
1.本发明涉及散热技术领域,具体涉及一种vc均热板下盖板毛细结构。
背景技术:2.近年来,随着电子信息技术相关产业的快速发展,各种高集成度、高功率的电子器件不断的应用在手机、平板等智能设备中,与此同时,为了保证设备的稳定工况,确保设备的性能,对散热模组的要求也越来越高。均热板是广泛应用在手机、平板中的一种散热装置,其具有散热效果好、产品适应性强等优势。
3.传统均热板通常包括铜质的上盖板、下盖板,上盖板和上盖板焊接封闭为一个真空腔室,下盖板上设置毛细结构;生产时,通过预留在上盖板和下盖板上的除气口(也是注水口)将腔室内部抽真空,并注入纯水,然后对除气口进行封闭。使用时,将均热板贴附在热源上,热量被纯水吸收后,纯水发生气化相变,吸收大量的热;然后在上盖板上冷凝,然后在重力作用下汇聚;依靠下盖板上的毛细结构,冷凝的纯水被重新吸附至蒸发热源所在的位置,进入下一个散热循环。目前,均热板技术虽然已经广泛的应用在各种高端电子器件的散热中,但发明人经过对均热板的长期研究发现,现有的均热板还存在以下缺陷:
4.1、传统均热板的工作介质(也就是纯水)回流,完全依靠设在下盖板上的毛细结构通过毛细效应进行回流吸附,也就是说工作介质的工作过程包括在热源附近蒸发、在上盖板上冷凝、在重力作用下沿着上盖板流动至低位汇聚、在毛细结构的作用下吸附回流至热源附近;在一定程度上,工作介质的整个工作行程时长就决定了均热板的散热效率,
5.在设备高功率、高频运行时,若上盖板上的工作介质仍然需要沿着上盖板汇聚至最低位,再通过毛细结构形成吸附回流,则会由于行程过长,影响到均热板的散热效率。在部分极端情况下,甚至出现局部干烧的现象,导致设备发热发烫严重,影响正常使用。因此,如果在有限的空间条件下,为冷凝工作介质返回热源提供多种路径,将能够有效的缩短工作介质的散热循环行程长度。
6.2、传统均热板的毛细结构一般就是一张极薄的毛细铜网,这种毛细铜网各部位的孔隙均匀,也就是说,整张毛细铜网各位置的毛细吸附力大体一致,在一般使用状况下,这种毛细铜网基本能满足使用需求。但对于部分散热密度需求大、有多个热源点位的设备而言,在部分使用状态下,由于工作介质的汇聚位置远离,就无法保障工作介质稳定的到达各热源位置。例如:当设备竖直使用、倾斜使用时,工作介质的汇聚位置位于均热板的底部,当均热板用于保障上下两个热源点位的散热时,工作介质往往不能稳定的到达上部热源点位,也会导致局部干烧,影响设备正常使用。因此,如何确保工作介质稳定、高效的在整个毛细铜网内回流,避免回流死角的出现,将能够有效的改善均热板的散热性能。
7.3、传统均热板独立使用,其通常一面(下盖板)与热源贴合,另一面(上盖板)与设备的散热背板贴合,均热板将热量传导至散热背板后,再通过散热背板扩散至设备后盖,进而实现散热。但由于均热板通常体积较小,其上盖板与散热背板的接触面积有限,在设备高功率、高频运行时,上盖板与散热背板之间较小的接触面积无法保证热量的快速传递,进而
导致散热背板局部淤热,造成设备局部发烫,也影响均热板内的工作介质在上盖板处的冷凝,从而导致散热的恶性循环。因此,如何改善均热板上盖板与设备散热背板之间的热量交换,也是提高均热板散热性能的关键环节。
技术实现要素:8.本发明的目的在于提供一种能够减少工作介质毛细吸附回流死角的vc均热板下盖板毛细结构。
9.为实现上述发明目的,本发明所采用的技术方案是:一种vc均热板下盖板毛细结构,包括第一均热板;
10.所述第一均热板包括上盖板和下盖板;所述下盖板的内表面沿远离上盖板的方向依次设置有支撑网孔板和主体毛细层;
11.所述主体毛细层包括位于中部的中心粗毛细区和位于两侧的边沿细毛细区,所述中心粗毛细区和边沿细毛细区均沿主体毛细层的长度方向延伸。
12.优选的,所述中心粗毛细区与边沿细毛细区的结合部位之间设置有隔离板,所述隔离板由主体毛细层的中部延伸至主体毛细层的一端,所述隔离板与主体毛细层的另一端之间构成横流段。
13.优选的,所述横流段的长度介于主体毛细层长度的1/5至1/2之间。
14.优选的,所述主体毛细层为毛细铜网,所述毛细铜网位于中心粗毛细区的孔隙密度小于边沿细毛细区。
15.优选的,所述下盖板的内表面设置有沿下盖板长度方向延伸的导流棱,所述主体毛细层压靠在导流棱的棱顶。
16.优选的,所述导流棱的棱顶还设置有沿导流棱长度方向延伸的引流槽。
17.优选的,所述引流槽和导流棱均通过对下盖板进行蚀刻构成。
18.优选的,所述上盖板与下盖板的板面之间均匀设置有若干排支撑柱,所述支撑柱的两端分别与上盖板的内表面和下盖板内的支撑网孔板相接触,所述支撑柱的外表面设置有柱表毛细层。
19.优选的,所述支撑柱的横截面呈x形,且x形的四个凹部形成四个截流储水区。
20.优选的,所述支撑柱由两个横截面呈半圆形的柱板背对背抵接构成;两个所述柱板分别设置在上盖板和支撑网孔板上。
21.本发明的有益效果集中体现在:能够确保工作介质稳定、均衡的分散至主体毛细层的各个部位,减少了吸附死角,尤其适合体积较大、多热源的电子器件的散热。具体来说,本发明在使用过程中,主体毛细层靠近下部一段(空间位置较低的一段)散热中需要的工作介质主要依靠中心粗毛细区直接进行吸附,而靠近主体毛细层上部一段(空间位置较高的一段)散热中需要的工作介质主要依靠边沿细毛细区进行吸附后,再由中心粗毛细区将工作介质从边沿细毛细区吸附而来,本发明能够保证工作介质在整个主体毛细层上的均衡分布,使得工作介质能够稳定的从汇聚区(均热板内空间位置最低的位置)吸附至主体毛细层的上段,确保了整体的散热性,防止干烧现象的发生。
附图说明
22.图1为本发明的结构示意图;
23.图2为图1中所示结构的a-a向视图;
24.图3为下盖板的俯视图;
25.图4为图3中b部放大图;
26.图5为图3中所示结构安装主体毛细层后的结构示意图;
27.图6为图5中所示结构安装支撑网孔板后的结构示意图;
28.图7为背板与上盖板相对一面的结构示意图;
29.图8为支撑柱的结构示意图;
30.图9为柱板的结构示意图。
具体实施方式
31.如图1-9所示的,均热板散热模组,主要应用在智能电子设备,如:手机、平板电脑、笔记本电脑等设备中,用于对显卡、cpu等高发热密度的核心电子器件进行散热降温,以提高设备工作的稳定性,提高设备综合性能。
32.与传统的均热板相较,本发明主要包括以下三大方面的性能优化:
33.1、为均热板内的工作介质的回流提供了新路径,缩短了部分工作介质的回流行程,促使工作介质能够更加高效的参与到散热循环中,提高均热板散热模组整体的散热效果;
34.2、优化了均热板内的毛细结构,具体是主体毛细层的分区设置,使得工作介质能够更加稳定高效的回流至主体毛细层的各个位置,降低了毛细回流死角出现的风险;
35.3、针对高热密度的热源进行散热时,采用双层均热板的散热形式,也就是第一均热板和第二均热板协同动作,且两层均热板共享一个盖板,能够有效的避免热量淤积,实现热量的分散、导出。
36.本发明上述三大方面的改进和优化可独立应用在均热板散热模组中,亦可两两结合或全部结合应用在均热板散热模组中,对此,本发明不进行限制,本领域技术人员在本发明的基础上,根据实际使用情况进行具体结合即可。
37.下面将从三大方面的具体改进上对本发明的核心技术方案进行阐述:
38.从第一个方面来看,如图1和2中所示,本发明包括第一均热板1,所述第一均热板1包括上盖板2和下盖板3,上盖板2和下盖板3通常为铜板,其尺寸相同,便于二者的焊接;但在采用双层均热板的情况下,上盖板2的尺寸要远大于下盖板3,这种情况详见下文,在本实施例中不进行具体介绍。所述上下盖板的上下是根据正常使用过程中靠近热源0来进行界定的,所述的下盖板3也就是靠近热源0的盖板,而上盖板2就是相对于下盖板3而言,远离热源0的盖板,使用时,热源0紧贴在下盖板3的外表面,一般为了保证热传导的稳定性,可通过导热脂进行粘结。
39.如图2中所示,所述下盖板3的内表面沿远离上盖板2的方向依次设置有支撑网孔板4和主体毛细层5,所述主体毛细层5也就是均热板内起到毛细吸附作用的核心部件,其具备较好的毛细效应,一般可采用铜粉烧结的方式形成、直接采用多孔隙的毛细铜网,或者采用其他方式形成均可。上盖板2与下盖板3的板面之间均匀设置有若干排支撑柱6,所述支撑
柱6的两端分别与上盖板2的内表面和下盖板3内的支撑网孔板4相接触,支撑柱6的作用主要在于对上盖板2和下盖板3形成支撑,避免塌陷,以保证上下盖板之间的空间支撑的可靠性。相邻的两排支撑柱6之间可以相对,使得支撑柱6整体呈矩阵排布,当然,如图6和7中所示,相邻两排支撑柱6之间也可以相互交错。
40.本发明所述支撑柱6的外表面设置有柱表毛细层7,柱表毛细层7也就是设置在支撑柱6表面的毛细层,其能够将上盖板2上冷凝的工作介质吸收并回流转移至主体毛细层5中,以进行再次的蒸发冷凝循环。柱表毛细层7的构成方式亦较多,例如:由烧结在支撑柱6外表面的铜粉形成,或者通过在支撑柱6的表面包覆多孔隙的层结构形成均可。但对于大部分使用情况而言,由于散热模组整体体积不大,支撑柱6的体积更小,不便于进行包覆,因此,大多数情况下采用铜粉烧结的形式形成柱表毛细层7。
41.本发明在使用过程中,将热源0与下盖板3接触,热源产生的热量通过下盖板3传导至第一均热板1内;工作介质吸收大量的热量,并产生气化相变,气态的工作介质在上盖板2处冷凝,并放出热量,经上盖板2朝后续的低温区传递;冷凝后的液态工作介质在重力作用下沿着上盖板2朝低位滑落,在滑落的过程中,部分液态工作介质会被支撑柱6阻挡,并受到支撑柱6上的柱表毛细层7的吸引,沿着支撑柱6直接回流至主体毛细层5对应的区域,或者被柱表毛细层7直接吸收,并暂存在柱表毛细层7内。在此基础上,为了提高工作介质运动的顺畅性,可以在所述柱板9的外表面设置有沿柱板9长度方向延伸的导流槽10,导流槽10一般通过蚀刻形成。相较于传统的单纯通过主体毛细层5进行吸附回流的方式相比,本发明拓宽了工作介质的回流路径,缩短了工作介质的回流行程,能够有效的提高均热板的散热效果。同时,柱表毛细层7可以作为液态工作介质的暂存空间,也能够减少干烧现象的发生,尤其适合高热密度的电子器件的散热。
42.本发明支撑柱6的具体形态较多,例如:可采用圆柱形、方柱形等等形状,但这些形状由于外周面没有凹部,其对工作介质的暂存量有限,理论上只能达到柱表毛细层7的饱和吸附量;为了进一步提高整体的散热效率,本发明更好的做法还可以是,所述支撑柱6的周面上设置有多个内凹的截流储水区8。所述的截流储水区8也就是在支撑柱6周面上形成的凹陷区域,冷凝的工作介质在沿着上盖板2回流时,受到支撑柱6的阻挡,沿着支撑柱6运动,并可以在一定程度上汇聚至截流储水区8内。例如:当支撑柱6呈圆柱形时,截流储水区8就可以是设置在支撑柱6侧面的弧形凹槽。
43.由于本发明依附在智能电子设备上进行使用,如手机等设备使用时,其握持方向并不是完全固定的,为了在各种角度下实现对工作介质的有效截流暂存,如图8中所示,本发明所述支撑柱6的横截面呈x形,且x形的四个凹部形成四个截流储水区8,这样在多种使用角度下,截流储水区8均具有较好的效果。一般情况下,支撑柱6可直接通过烧结、焊接等方式设置在上盖板2上,但为了进一步提高支撑效果,保证上下盖板安装的稳定性,以及第一均热板1整体的稳定性,本发明采用拼合抵接的方式形成支撑柱6。如图8和9中所示,也就是说,本发明所述支撑柱6由两个横截面呈半圆形的柱板9背对背抵接构成,且两个所述柱板9分别设置在上盖板2和支撑网孔板4上。这样不仅能够形成完整的支撑柱6,同时,通过上盖板3上的主板9与支撑网孔板4上的柱板9的抵靠,还能够实现对上盖板2、支撑网孔板4和下盖板3的定位,使得第一均热板1保持良好的结构稳定性和结构强度。
44.当然,为了保证支撑网孔板4在下盖板3内安装的稳定性,如图3和4所示,所述下盖
板3的四个角部设置有三角形的支撑台阶11,所述支撑网孔板4的边沿搭靠在支撑台阶11上,支撑网孔板4的板面压靠在主体毛细层5上。进一步的,还可以在所述支撑台阶11上还设置有定位凹部12,所述支撑网孔板4上设置有与定位凹部12相配合的定位凸起,所述定位凸起位于定位凹部12内。
45.从第二个方面来看,本发明还通过对主体毛细层5毛细结构的改良,使得工作介质能够更好的在主体毛细层5上进行吸附,减少由于主体毛细层5吸附力不足导致的,工作介质无法回流的回流死区的出现风险。如图5中所示,本发明所述主体毛细层5包括位于中部的中心粗毛细区13和位于两侧的边沿细毛细区14,所述中心粗毛细区13和边沿细毛细区14均沿主体毛细层5的长度方向延伸。所述中心粗毛细区13和边沿细毛细区14的粗和细,也就是说二者的理论毛细吸附力存在一定的大小差异,换言之,也就是边沿区域的毛管力大于中心区域的毛管力,在其他条件完全相同的情况下,边沿区域对工作介质的回流吸附效果较中心区域更优。例如:当所述主体毛细层5为毛细铜网时,其具体的形态表现为所述毛细铜网位于中心粗毛细区13的孔隙密度小于边沿细毛细区14,边沿细毛细区14具备更好的毛细效应,在如图5中所示的竖直的工作状态下,其能够将工作介质吸附至更高的区域。
46.在此基础上,为了进一步保证上述效果,所述中心粗毛细区13与边沿细毛细区14的结合部位之间设置有隔离板15,所述隔离板15由主体毛细层5的中部延伸至主体毛细层5的一端,所述隔离板15与主体毛细层5的另一端之间构成横流段16,通常所述横流段16的长度介于主体毛细层5长度的1/5至1/2之间,该长度的具体范围,设计人员可根据热源0位置、热源的数量等进行适应性设计,如图5中虚线框处的空白区域即表示热源0相对的位置。在这种情况下,主体毛细层5一般由位于中心的稀疏孔隙的中心粗毛细区13和两侧的密集孔隙的边沿细毛细区14拼接形成,二者的下段之间设置隔离板15,上段之间直接紧密拼合。当然,为了提高主体毛细层5整体的稳定性,还可以在外部加设边框。
47.在使用过程中,主体毛细层5靠近下部一段(空间位置较低的一段)散热中需要的工作介质主要依靠中心粗毛细区13直接进行吸附,而靠近主体毛细层5上部一段(空间位置较高的一段)散热中需要的工作介质主要依靠边沿细毛细区14进行吸附后,再由中心粗毛细区13将工作介质通过横流段16吸附而来,本发明能够保证工作介质在整个主体毛细层5上的均衡分布,使得工作介质能够稳定的从汇聚区(均热板内空间位置最低的位置)吸附至主体毛细层的上段,确保了整体的散热性,防止干烧现象的发生。
48.另外,为了进一步提高工作介质跟随主体毛细层5流动的顺畅性,如图2和3中所示,本发明所述下盖板3的内表面设置有沿下盖板3长度方向延伸的导流棱17,所述主体毛细层5压靠在导流棱17的棱顶。在此基础上,还可以在所述导流棱17的棱顶还设置有沿导流棱17长度方向延伸的引流槽18。所述引流槽18和导流棱17均通过对下盖板3进行蚀刻构成。通过导流棱17和引流槽18的设计,使得下盖板3与主体毛细层5接触的表面上形成多道纵向的、起到导流、引流作用的通道,使得工作介质的流动更加的顺畅。
49.从第三方面来看,为了适应超高热密度的电子器件的散热,解决传统单层均热板(可以看做第一均热板1)与设备的散热背板之间热传导不畅导致的淤热问题,本发明还采用双层均热板的形式进行散热。具体来说,如图7中所示,所述上盖板2的尺寸(外层方框)大于下盖板3的尺寸(内层方框对应的尺寸),结合图1和2中所示,所述上盖板2远离下盖板3的一面还设置有背板19,所述背板19与上盖板2焊接形成第二均热板20。所述第一均热板1的
下盖板3与热源0相接触。
50.在使用过程中,下盖板3和上盖板2共同构成第一均热板1主要用于对热源产生的高密度热量进行初步分散,上盖板3和背板19共同构成的第二均热板20主要用于将分散后的热量快速的朝外发散;第一均热板1的上盖板2和第二均热板20的“下盖板”共用,热量的传导效果好,热量的分散铺展面积更大,有效的保证了散热的性能。至于所述第二均热板20内部的毛细结构、支撑柱结构等,其可以与第一均热板1相同,其也可以采用传统的均热板结构。
51.考虑到第一均热板1和第二均热板20在散热时,针对的热密度具有较大的区别,所述第一均热板1内部的工作介质为纯水,第二均热板20内部的工作介质为r245fa。采用纯水作为第一均热板的工作介质,纯水具备高达的比热,能够保证对热源0散发的热量的吸收率;采用r245fa作为第二均热板20的工作介质,其具有极好的热敏感性,能够保证对分散后的低密度热量进行高效的吸收;二者协同作用,使得本发明相较于传统均热板,具备更佳优异的性能。
52.关于上盖板2与下盖板3的焊接形式,如图2中所示,可以是所述上盖板2与下盖板3相对的边沿设置有横截面呈半圆形的焊接缝21,所述焊接缝21的一半位于上盖板2上、另一半位于下盖板3上。进一步的,所述焊接缝21外设置有一圈环形的包片22,所述焊接缝21通过包片22遮蔽。可以想见的是,所述背板19与上盖板2之间,也可以采用上盖板2和下盖板3之间的焊接形式,也就是说,所述上盖板2与背板19相对的边沿也设置有焊接缝21和包片22。