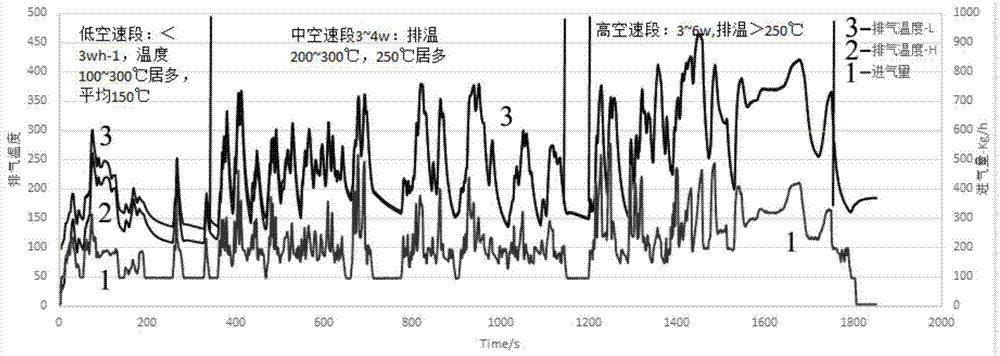
本发明涉及一种汽车尾气催化剂,特别是一种与scr匹配使用的lnt(leannoxtrap,稀燃nox捕集)催化剂,本发明同时还公开了该lnt催化剂的制备方法,属于汽车尾气催化剂
技术领域:
。
背景技术:
在柴油汽车尾气中,氮氧化合物(nox)是尾气的主要成分之一。传统技术路线是采用选择性还原催化剂(scr)在还原剂nh3作用下将nox还原为n2,此处nh3来源于尿素的分解。图1是某柴油发动机whtc循环的排温曲线,在whtc测试循环中,低空速段平均温度仅150℃,若采用传统尿素scr技术路线,在低空速段由于温度过低,尿素无法分解并且易结晶,无法喷射尿素,进而无法有效处理nox,因此需引入新的后处理技术路线以解决低温时nox的排放问题。本世纪初,欧洲国家开发出lnt并部分用于市场,该产品可以在稀燃状态(lean)下对nox进行捕集,在富燃状态(rich)下释放nox并将其还原,工作温度范围200-500℃。英国庄信万丰在sae2010-01-0302中已经提出了lnt+scr集成系统,该系统lnt在富燃状态下还原产生的nh3可以存储于下游的scr中,并作为scr催化剂与nox反应时的还原剂,这样在下游的scr中可以处理掉从上游逃逸的nox,并且scr催化剂前不用再额外增加尿素罐作为nh3源。随着汽车尾气排放要求越来越严格,现有的传统尿素scr后处理技术路线对低温nox处理能力有限,尤其针对3.0l以下的柴油车发动机,其排温较低,在使用现有的scr技术路线中会出现尿素结晶无法工作的情况,并且后处理装置安装空间有限,因此针对该类型发动机不能再使用传统尿素scr技术路线。针对该类型柴油车发动机后处理可以采用能产生nh3的lnt作为scr的nh3源,该类lnt的最低工作温度可以低至150℃以下,在该类lnt与scr匹配使用可以解决低温nox排放问题。专利us6607704介绍了镁铝尖晶石在lnt中的重要作用,含镁铝尖晶石的lnt具有更高的耐久性。庄信在sae2010-01-0302中研究了储氧材料和贵金属比例对nh3生成量的影响,储氧量低,高pt低pd催化剂具有更好的nh3生成能力。虽然,有诸多文献研究lnt的应用,但是关于lnt如何具体的改善低空速段排气温度过低情况下,nox的净化清除效率提升,依然属于本领域需要深入研究的难题。技术实现要素:本发明的目的在于克服现有技术中柴油发动机在低空速段排气温度过低,导致尿素喷射失效,无法有效净化尾气中nox的不足,提供一种与scr匹配使用的lnt催化剂。为了实现上述发明目的,本发明提供了以下技术方案:一种与scr匹配使用的lnt催化剂,所述lnt催化剂包括贵金属rh,以及贵金属pt、pd中至少一种。所述lnt催化剂具有分层结构,其表层rh浓度大于内层的rh浓度。通过优化设计lnt催化剂的内外层之间的不同贵金属浓度,使得lnt生成h2能力增加,,以提高nh3生成能力,可以更好与下游scr匹配使用,改善排气温度过低的情况下尾气中nox净化能力。特别是该lnt下游的scr在lnt产生的nh3的还原作用下可以实现对逃逸的nox再次处理,可大大提高系统对nox的净化效率。优选地,lnt催化剂中,内层rh浓度可以为0。即内层不含rh,仅仅在催化剂的表层含有rh,表层rh发挥出lnt催化剂的核心作用,增强对于nox的催化转化及nh3生成作用。进一步,所述贵金属包含pt;所述lnt表层pt浓度小于内层pt浓度。lnt后处理技术路线适用于稀燃(lean)发动机并辅以富燃(rich)以还原再生后处理的lnt催化剂,lnt催化剂在正常工作的lean状态下氧化并吸附nox,在rich状态下释放并还原nox为n2和nh3,同时氧化因富燃而排出的hc、co。pt浓度对于内层的催化作用至关重要,具有强烈选择性促进催化作用。进一步,所述贵金属催化剂还包括金属氧化物、贵金属、碱性金属、ni、mn元素。优选地,所述贵金属包含但不限于pt、pd、rh等贵金属元素中的一种或几种,优选地,至少包含rh。其中pd为可以包括的贵金属元素。优选地,所述金属氧化物包含但不限于氧化铝、铈锆复合氧化物、铈锆铝复合氧化物、硅铝复合氧化物、镁铝尖晶石等金属氧化物中的一种或几种。优选地,所述碱性金属是指碱金属和/或碱土金属和/或稀土碱性元素的一种或几种。优选地,稀土碱性元素可以是铈。本发明提供的与scr匹配使用的lnt,该催化剂涂层主要以金属氧化物和贵金属为基础,加以碱性金属提高其对nox的吸附能力和耐久能力,添加ni、mn等元素增加lnt对hc的重整产h2能力。同时,配合合理的涂层布局、贵金属分布和涂层材料的选用,使得lnt催化剂的核心功效得到大幅度强化提升。最终更好的实现多种原料成分相互配合,促进实现hc重整或水煤气反应的发生,使之产生大量h2,并促进h2与no反应生成nh3,而提高nh3的生成率。具体而言,本发明方法制备的lnt,除了传统的lnt所具备的lean条件下对no的氧化和存储,rich条件下对nox的释放和还原外,还包括rich条件下将nox还原为n2和nh3,并将nh3存储于下游的scr中,用于与从上游逃逸的nox反应,将nox的排放降为最低。lnt在rich状态下产生nh3,存储于下游的scr中,当有nox从上游lnt中逃逸时,nox便在下游的scr中与存储的nh3发生选择性还原反应生成n2。所以,本发明制备的lnt同时兼具较高的nh3生成能力和较高的nox去除能力。进一步,所述lnt催化剂具有涂层结构,lnt催化剂涂层包括金属氧化物、镁铝尖晶石、贵金属、碱性元素以及助剂。优选地,所述lnt涂层的主要组成为氧化铝、铈锆复合氧化物、镁铝尖晶石、铈锆铝氧化物、氧化铈和ba类似碱性金属元素。例如,ba类碱性金属元素可以是mg作为替换,或者ba、mg混合物。进一步,所述碱性金属是指碱金属、碱土金属和稀土碱性元素中的一种或几种。所述稀土碱性元素是铈。优选地,所述碱性金属是ba、mg、ce、sr、k、na等元素中的一种或几种。更优选地,所述碱性金属是ba、mg、ce中的一种或几种。进一步,所述lnt中所述贵金属至少包含pt和rh。进一步,lnt催化剂负载在载体上,涂层的涂覆量为120-400g/l。优选地,lnt催化剂中,贵金属的涂覆量为20-120g/ft3。本发明的另一目的是提供一种制备上述lnt催化剂材料的方法,通过制备工艺的调整优化,控制lnt催化剂中各种原料成分相互之间配合作用,以及优化调整催化剂分层结构中贵金属元素的分布,实现更高效率,实现高催化转化效率和还原净化nox的作用。一种上述催化剂制备方法,包括以下步骤:(1)将第一可溶性金属盐溶液浸渍到第一金属氧化物上,以金属氧化物计,占比为0-20%,然后60-120℃干燥2-12h,在350-650℃温度下,空气气氛中焙烧2-8h,得到碱性材料w0。将第二可溶性金属盐溶液浸渍到第二金属氧化物中,以金属氧化物计,占比为0-20%,然后60-120℃干燥2-12h,在350-650℃温度下,空气气氛中焙烧2-8h,得到碱性材料wn。(2)将第一贵金属前驱体溶液浸渍到wn中,以贵金属单质计,占比为0.1-5%,然后60-120℃干燥2-12h,在350-650℃温度下,空气气氛中焙烧2-8h,得到贵金属催化剂w1。将第二贵金属前驱体溶液浸渍到w0中,以贵金属单质计,占比为0.1-5%,然后60-120℃干燥2-12h,在350-650℃温度下空气气氛中焙烧2-8h,得到贵金属催化剂w2。将第三贵金属前驱体溶液浸渍到第三金属氧化物中,然后60-120℃干燥2-12h,在350-650℃温度下空气气氛中焙烧2-8h,得到贵金属催化剂w3。(3)将w1、w2、w3和第一粘接剂混合,球磨制浆,w1占比5~50%,w2占比5~50%,w3占比0~30%,第一粘接剂占比1-10%,浆料固含量控制在25-50%,浆料粒度d50控制在2μm-10μm,得到贵金属浆料n1。(4)将w2、w3和第二粘接剂混合,球磨制浆,w2占比0~50%,w3占比40-99%,第二粘接剂占比1-10%,浆料固含量控制在25-50%,浆料粒度d50控制在2μm-10μm,得到贵金属浆料n2。(5)将浆料n1涂覆于载体底层,涂层上载量100-300g/l,贵金属含量5-120g/ft3,在60-120℃温度下干燥2-12h,然后在350-650℃温度下空气气氛中焙烧2-8h,得到催化剂c0。(6)将浆料n2涂覆于载体c0上层,涂层上载量0-300g/l,贵金属含量5-120g/ft3,在60-120℃温度下干燥2-12h,然后在350-650℃温度下空气气氛中焙烧2-8h,得到催化剂c。本发明催化剂制备方法根据传统的汽车尾气催化剂制备工艺,结合本发明催化剂材料的设计特性调整配合原料应用配合的顺序,先将活性组分和碱性金属负载至金属氧化物上,最后制浆涂覆至载体上,充分调节各种原料成分相互之间的配合关系,使得催化剂活性最大化,达到设计预期的nox捕集、催化、转化的效果。发明方法工艺简单,操作简便,成本低,容易实现上述lnt催化剂产品的高品质生产加工。本发明催化剂制备方法中,将ni、mn元素分布于铈锆复合氧化物、氧化铝、铈锆铝氧化物、氧化铈中并负载pt/pd记为w1。w1具备在rich状态下促进hc重整和水煤气反应生成h2,同时w1还具备在lean状态下将no氧化为no2的能力。将碱性金属分布于氧化铝/硅铝/镁铝尖晶石/氧化铈等氧化物中并负载pt/pd记为w2。w2不但具备氧化no为no2的能力,并且还具备存储nox的能力。rh分布于铈锆复合氧化物、氧化铝、铈锆铝氧化物、氧化铈中,记为w3。w3具备将nox还原为n2或选择性还原为nh3的能力。最后将w1、w2、w3复合在一起构成具有突出催化剂效果/作用的复合lnt催化剂产品。进一步,所述载体包含但不限于堇青石、金属材质的通透式载体中的一种或几种。还可以是其他常见的载体材料。与现有技术相比,本发明的有益效果:(1)本发明通过设计贵金属比例、催化材料组成的比例和添加重整催化元素以提高hc重整反应和水煤气反应并产生h2。(2)本发明将催化重整催化剂分布于涂层的底层,重整产生的h2溢流至上层充分与还原层接触,提高h2的利用率,产生适量的nh3。(3)本发明中将碱土金属与镁铝尖晶石、氧化铈等碱性金属氧化物共同使用,大大提高nox的存储能力。(4)本发明中nox氧化与存储分布于底层或上层,使nox充分与涂层接触,提高nox的存储能力。(5)本发明采用传统的等体积浸渍工艺和制浆工艺,工艺简便可行,成本低。附图说明:图1是某柴油发动机whtc循环的排温曲线。图2是催化重整层与还原层分层原理示意图。图3是催化重整层与还原层充分接触混合原理示意图。图4是实例1-6制备的c1-c6催化剂nox转化率对比。图5是实例1-6制备的c1-c6催化剂nh3转化率对比。具体实施方式本发明主要利用pt在低铈氧化物中的催化特性,在rich条件下催化hc重整和水煤气反应产生h2,并使h2溢流至还原活性位与no反应生成nh3。本发明中将催化重整涂层分布于底层,还原层分布于上层,产生的h2溢流至上层充分与还原层接触如图2,提高h2的利用率,或催化重整涂层与还原层充分混合如图3,使产生的h2很容易溢流至还原位与nox反应生成nh3。关于本发明提供的lnt催化剂制备方法,可以有以下优选项:优选地,制备方法中所述第一可溶性金属盐溶液、第二可溶性金属盐溶液可以是相同的可溶性金属盐溶液,也可以是不同的金属盐溶液。进一步,步骤1中,优选地,所述第一可溶性金属盐是醋酸钡、硝酸钡、硝酸钾、硝酸锶或其他碱性金属盐中的一种或几种。进一步,制备方法中所述第一金属氧化物、第二金属氧化物、第三金属氧化物可以是相同的金属氧化物,也可以是不同的金属氧化物。进一步,所述第一金属氧化物是氧化铝、铈锆复合氧化物、镁铝尖晶石中、氧化铈的一种或几种。优选地,第一可溶性金属盐溶液以等体积浸渍法或过量浸渍法浸渍到金属氧化物上。进一步,所述第二可溶性金属盐是硝酸镍、硝酸锰或其他可溶性盐中的一种或几种。进一步,所述第二金属氧化物是铈锆复合氧化物、氧化铝、铈锆铝氧化物中的一种或几种。优选地,第二可溶性金属盐溶液等体积浸渍法或过量浸渍法浸渍到第二金属氧化物中。进一步,贵金属前驱体是含有铂、钯、铑中一种或几种的可溶性金属盐。贵金属前驱体包括第一贵金属前驱体、第二贵金属前驱体。所述第一贵金属前驱体、第二贵金属前驱体可以相同,也可以不同。优选地,贵金属前驱体选自硝酸铂、氯铂酸、氯化钯、硝酸钯、硝酸四胺铂、硝酸四胺钯、硝酸铑中的一种或几种。进一步,将第一贵金属前驱体溶液负载到wn。进一步,将第二贵金属前驱体溶液负载到w0。进一步,将第三贵金属前驱体溶液负载到第三金属氧化物。优选地,第一贵金属前驱体溶液以等体积浸渍法或过量浸渍法浸渍到wn中。优选地,所述第一贵金属前驱体溶液是含有pt的贵金属前驱体溶液。优选地,第二贵金属前驱体溶液以等体积浸渍法或过量浸渍法浸渍到w0中。优选地,所述第二贵金属前驱体溶液是含有pt、pd中至少一种的贵金属前驱体溶液。优选地,第三贵金属前驱体溶液以等体积浸渍法或过量浸渍法浸渍到第三金属氧化物中。优选地,所述第三贵金属前驱体溶液是含有rh的贵金属前驱体溶液。优选地,所述第三金属氧化物是铈锆复合氧化物、氧化铝、铈锆铝氧化物中的一种或几种。优选地,贵金属前驱体溶液还添加有助剂,也可以不添加助剂。贵金属和贵金属前驱体溶液可以是单一的贵金属前驱体溶液,也可以是多种贵金属前驱体溶液的混合,或者前驱体溶液和助剂盐溶液的混合。优选地,所述金属盐类优选为硝酸盐、醋酸盐或其他可溶性盐类。进一步,步骤2,w1贵金属pt∶pd∶rh比例优选为2∶1∶0~1∶0∶0,w2贵金属pt∶pd∶rh比例优选为1∶1∶0~1∶0∶0,w3贵金属pt∶pd∶rh比例优选为1∶1∶1~0∶0∶1。w1中贵金属以pt为主,pd作为辅助。以高pt低pd的贵金属在氧化物中分布,可大大提高催化剂的hc重整和水煤气反应,提高h2的产生量从而促进nh3的生成。进一步,步骤2,所述w1中铈锆复合氧化物、氧化铝、铈锆铝氧化物、氧化铈中,ce占比优选为0~30%,zr占比0~95%,氧化物中铈含量不超过30%。进一步,步骤2,所述w2中镁铝尖晶石中mg含量占比2~50%。铈、钡等碱金属元素以等体积浸渍分于镁铝尖晶石、氧化铈中,碱金属在氧化物中占比0-20%。进一步,步骤2,所述w1中镁铝尖晶石、氧化铈中,以金属氧化物计,nio2含量占比2~5%,mno2含量0-20%。镍锰元素以等体积浸渍法浸渍于铈锆复合氧化物、氧化铝、铈锆铝氧化物、氧化铈中。进一步,步骤3中,所述第一粘接剂包含但不限于铝溶胶、硅溶胶、锆溶胶中的一种或几种。进一步,步骤4中,所述第二粘接剂包含但不限于铝溶胶、硅溶胶、锆溶胶中的一种或几种。本发明制备方法是基于传统汽车尾气催化剂制备方法的应用和拓展,优选地,催化剂的载体包含但不限于堇青石、金属材质的通透式或壁流式载体。该方法工艺简单,操作简便,成本低。ba在表面分布时对nox具有最高的存储能力,ba基lnt的nox的存储与还原受老化的影响,ce-zr存在条件下,lnt耐老化能力更强。碱金属和/或碱土金属在lnt中对nox存储具有影响。lnt组成性能影响以及工作机理,具体工作机理如下:lean状态:氧化:no+o2→no2捕集:4no2+2mco3+o2→2m(no)3+2co2rich状态:释放:m(no3)2+2co→mco3+no2+no+co2还原:no2+co→no+co22no+2co→n2+co22no+h2→n2+h2o2no+5h2→2nh3+h2o为满足lnt的各项工作,lnt催化剂的组成不能缺少no氧化功能,nox捕集功能,nox释放功能,nox还原功能。并且在nox还原中需选择性还原为n2和nh3。根据以上机理,h2是nh3产生的反应物,若需提高nh3的产生量,那么就需提高反应物h2的量。虽然在柴油机尾气中含有一部分h2,但量较低。若需刻意提高nh3生成量,那么需lnt还具备催化产生h2的能力。下面结合试验例及具体实施方式对本发明作进一步的详细描述。但不应将此理解为本发明上述主题的范围仅限于以下的实施例,凡基于本
发明内容所实现的技术均属于本发明的范围。<实例1>将硝酸镍和硝酸锰溶液混合,以等体积浸渍法负载到铈锆铝复合氧化物(比表面积bet=120m2/g,ceo2:10%,zro2:10%)中,60℃干燥12h,400℃焙烧2h,得到2%ni-5%mn/cza,记为wn-1。将硝酸铂贵金属溶液以等体积浸渍法负载到wn-1中,60℃干燥12h,400℃焙烧2h,得到1.7%pt/cza,记为w1-1。将硝酸铈和硝酸钡溶液以等体积浸渍法负载到镁铝尖晶石中(bet=150m2/g,mgo:10%)中,60℃干燥12h,400℃焙烧2h,得到2.0%ce-10%ba/mao,记为w0-1。将硝酸铂贵金属溶液以等体积浸渍法负载到w0-1中,60℃干燥12h,400℃焙烧2h,得到1.7%pt/mao-ce-mg,记为w2-1。将硝酸铑溶液以等体积浸渍法负载到氧化铝(bet=170m2/g)中,60℃干燥12h,400℃焙烧2h,得到2.25%rh/al2o3,记为w3-1。将w1-1、w2-1、w3-1与粘接剂铝溶胶混合,w1-1占比40%,w2-1占比40%,w3-1占比15%,粘接剂占比5%,球磨10min,得到固含量40%,d50=5μm的浆料n1-1。将n1-1涂覆至堇青石载体上,堇青石载体规格φ143.2*76.2/400cpsi-4mil。经60℃干燥6h后再经550℃焙烧2h,得到催化剂c1,干基涂覆量250g/l,贵金属含量120g/ft3,贵金属pt∶pd∶rh比例4∶0∶1。<实例2>将硝酸镍和硝酸锰溶液混合,以等体积浸渍法负载到铈锆铝复合氧化物(bet=120m2/g,ceo2:10%,zro2:10%)中,60℃干燥12h,400℃焙烧2h,得到2%ni-5%mn/cza,记为wn-2。将硝酸铂、硝酸钯的混合贵金属溶液以等体积浸渍法负载到wn-2中,60℃干燥12h,400℃焙烧2h,得到1.7%pt1pd1/cza,记为w1-2。将硝酸铈和硝酸钡溶液以等体积浸渍法负载到镁铝尖晶石中(bet=150m2/g,mgo:10%)中,60℃干燥12h,400℃焙烧2h,得到2.0%ce-10%ba/mao,记为w0-2。将硝酸铂、硝酸钯的混合贵金属溶液以等体积浸渍法负载到w0-2中,60℃干燥12h,400℃焙烧2h,得到1.7%pt1pd1/mao-ce-mg(pt∶pd=1∶1),记为w2-2。将硝酸铑溶液以等体积浸渍法负载到氧化铝(bet=170m2/g)中,60℃干燥12h,400℃焙烧2h,得到2.25%rh/al2o3,记为w3-2。将w1-2、w2-2、w3-2与粘接剂铝溶胶混合,w1-2占比40%,w2-2占比40%,w3-2占比15%,粘接剂占比5%,球磨10min,得到固含量40%,d50=5μm的浆料n1-2。将n1-2涂覆至堇青石载体上,堇青石载体规格同实例1。经60℃干燥6h后再经550℃焙烧2h,得到催化剂c2,干基涂覆量250g/l,贵金属含量120g/ft3,贵金属pt∶pd∶rh比例2∶2∶1。<实例3>将硝酸铂、硝酸钯的混合贵金属溶液以等体积浸渍法负载到铈锆铝复合氧化物(bet=120m2/g,ceo2:10%,zro2:10%)中,60℃干燥12h,400℃焙烧2h,得到1.7%pt1pd1/cza,记为w1-3。将硝酸铈和硝酸钡溶液以等体积浸渍法负载到镁铝尖晶石中(bet=150m2/g,mgo:10%)中,60℃干燥12h,400℃焙烧2h,得到2.0%ce-10%ba/mao,记为w0-3。将硝酸铂、硝酸钯的混合贵金属溶液以等体积浸渍法负载到w0-3中,60℃干燥12h,400℃焙烧2h,得到1.7%pt1pd1/mao-ce-mg,记为w2-3。将硝酸铑溶液以等体积浸渍法负载到氧化铝(bet=170m2/g)中,60℃干燥12h,400℃焙烧2h,得到2.25%rh/al2o3,记为w3-3。将w1-3、w2-3、w3-3与粘接剂铝溶胶混合,w1-3占比40%,w2-3占比40%,w3-3占比15%,粘接剂占比5%,球磨10min,得到固含量40%,d50=5μm的浆料n1-3。将n1-3涂覆至堇青石载体上,堇青石载体规格同实例1。经60℃干燥6h后再经550℃焙烧2h,得到催化剂c3,干基涂覆量250g/l,贵金属含量120g/ft3,贵金属pt∶pd∶rh比例2∶2∶1。<实例4>将硝酸镍和硝酸锰溶液混合,以等体积浸渍法负载到铈锆铝复合氧化物(bet=120m2/g,ceo2:10%,zro2:10%)中,60℃干燥12h,400℃焙烧2h,得到2%ni-5%mn/cza,记为wn-4。将硝酸铂贵金属溶液以等体积浸渍法负载到wn-4中,60℃干燥12h,400℃焙烧2h,得到1.82%pt/cza,记为w1-4。将硝酸铈和硝酸钡溶液以等体积浸渍法负载到镁铝尖晶石中(bet=150m2/g,mgo:10%)中,60℃干燥12h,400℃焙烧2h,得到2.0%ce-10%ba/mao,记为w0-4。将硝酸铂贵金属溶液以等体积浸渍法负载到w0-4中,60℃干燥12h,400℃焙烧2h,得到1.82%pt/mao-ce-mg,记为w2-4。将硝酸铑溶液以等体积浸渍法负载到氧化铝(bet=170m2/g)中,60℃干燥12h,400℃焙烧2h,得到1.62%rh/al2o3,记为w3-4。将w1-4、w2-4与粘接剂铝溶胶混合,w1-4占比47.5%,w2-4占比47.5%,粘接剂占比5%,球磨10min,得到固含量40%,d50=5μm的浆料n1-4。将w3-4与粘接剂铝溶胶混合,w3-4占比95%,粘接剂占比5%,球磨10min,得到固含量40%,d50=5μm的浆料n2-4。将浆料n1-4涂覆至堇青石载体上,堇青石载体规格同实例1。经60℃干燥6h后再经550℃焙烧2h,得到催化剂c4-0,干基涂覆量195g/l。将浆料n2-4涂覆至c4-0上,经60℃干燥6h后再经550℃焙烧2h,得到催化剂c4,干基涂覆量250g/l,贵金属含量120g/ft3,贵金属pt∶pd∶rh比例4∶0∶1。<实例5>将硝酸镍和硝酸锰溶液混合,以等体积浸渍法负载到铈锆铝复合氧化物(bet=120m2/g,ceo2:10%,zro2:10%)中,60℃干燥12h,400℃焙烧2h,得到2%ni-5%mn/cza,记为wn-5。将硝酸铂、硝酸钯的混合贵金属溶液以等体积浸渍法负载到wn-5中,60℃干燥12h,400℃焙烧2h,得到1.82%pt1pd1/cza,记为w1-5。将硝酸铈和硝酸钡溶液以等体积浸渍法负载到镁铝尖晶石中(bet=150m2/g,mgo:10%)中,60℃干燥12h,400℃焙烧2h,得到2.0%ce-10%ba/mao,记为w0-5。将硝酸铂、硝酸钯的混合贵金属溶液以等体积浸渍法负载到w0-5中,60℃干燥12h,400℃焙烧2h,得到1.82%pt1pd1/mao-ce-mg,记为w2-5。将硝酸铑溶液以等体积浸渍法负载到氧化铝(bet=170m2/g)中,60℃干燥12h,400℃焙烧2h,得到1.62%rh/al2o3,记为w3-5。将w1-5、w2-5与粘接剂铝溶胶混合,w1-5占比47.5%,w2-5占比47.5%,粘接剂占比5%,球磨10min,得到固含量40%,d50=5μm的浆料n1-5。将w3-5与粘接剂铝溶胶混合,w3-5占比95%,粘接剂占比5%,球磨10min,得到固含量40%,d50=5μm的浆料n2-5。将浆料n1-5涂覆至堇青石载体上,堇青石载体规格同实例1。经60℃干燥6h后再经550℃焙烧2h,得到催化剂c5-0,干基涂覆量195g/l。将浆料n2-5涂覆至c5-0上,经60℃干燥6h后再经550℃焙烧2h,得到催化剂c5,干基涂覆量250g/l,贵金属含量120g/ft3,贵金属pt∶pd∶rh比例2∶2∶1。<实例6>将硝酸铂贵、硝酸钯的混合金属溶液以等体积浸渍法负载到铈锆铝复合氧化物(bet=120m2/g,ceo2:10%,zro2:10%)中,60℃干燥12h,400℃焙烧2h,得到1.82%pt1pd1/cz,记为w1-6。将硝酸铈和硝酸钡溶液以等体积浸渍法负载到镁铝尖晶石中(bet=150m2/g,mgo:50%)中,60℃干燥12h,400℃焙烧2h,得到2.0%ce-10%ba/mao,记为w0-6。将硝酸铂、硝酸钯的混合贵金属溶液以等体积浸渍法负载到w0-6中,60℃干燥12h,400℃焙烧2h,得到1.82%pt1pd1/mao-ce-mg,记为w2-6。将硝酸铑溶液以等体积浸渍法负载到氧化铝(bet=170m2/g)中,60℃干燥12h,400℃焙烧2h,得到1.62%rh/al2o3,记为w3-6。将w1-6、w2-6与粘接剂铝溶胶混合,w1-6占比47.5%,w2-6占比47.5%,粘接剂占比5%,球磨10min,得到固含量40%,d50=5μm的浆料n1-6。将w3-6与粘接剂铝溶胶混合,w3-6占比95%,粘接剂占比5%,球磨10min,得到固含量40%,d50=5μm的浆料n2-6。将浆料n1-6涂覆至堇青石载体上,堇青石载体规格同实例1。经60℃干燥6h后再经550℃焙烧2h,得到催化剂c6-0,干基涂覆量195g/l。将浆料n2-6涂覆至c6-0上,经60℃干燥6h后再经550℃焙烧2h,得到催化剂c6,干基涂覆量250g/l,贵金属含量120g/ft3,贵金属pt∶pd∶rh比例2∶2∶1。<实例7>将上述示例制备的催化剂产品分别进行反应器测试,在模拟柴油车尾气的条件下,测定不同的催化剂产品对于尾气中的nox化合物的催化转化效率。测试过程中,所使用的模拟柴油车尾气的气体混合成分及比例关系如下:表1测试气氛gasnoc3h6(c1)h2coo2h2oco2n2lean200ppm100ppm00.1%10%5%5%balancerich200ppm5000ppm0.4%1%1%5%5%balance制样:从大样中取小样,1/2半径处取样,分别记为c1~c6并注明进出气方向,得到φ25.4*76.2/400cpsi小样。预处理:550℃lean气氛吹扫1h。测试:降温稳态测试500/450/400/350/300/250/200/150℃下循环10个lean/rich循环,记录nox、hc、co、nh3、h2o和co2的浓度,计算10个循环中nox平均转化率,nh3平均生成率。c1-c6催化剂nox转化率对比如图4所示,c1-c6催化剂nh3转化率对比如图5所示。当前第1页12