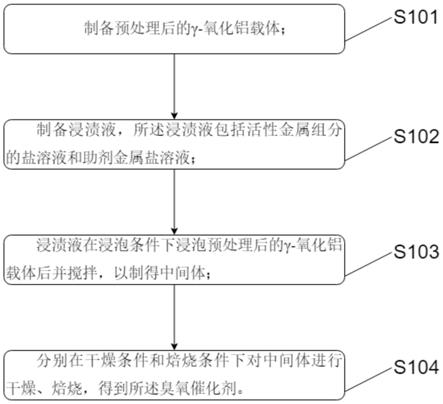
1.本发明涉及废水处理技术领域,尤其涉及一种用于农药废水中高浓度有机磷转化处理的臭氧催化剂、制备方法及应用。
背景技术:2.我国是农药生产和使用大国,年产量居世界第二位。农药是保证我国农业生产持续发展必不可少的生产资料,但含磷农药生产过程中产生有机磷废水,特别是乙烯生产类废水的有机磷浓度高,毒性大,可生化性差,现有催化臭氧氧化法进行处理,而在催化臭氧氧化水处理技术中,其关键技术在于臭氧催化剂的制备。然而,对于现有技术中的臭氧催化剂,由于制备工艺路线决定了缺乏特异性,不同废水具有不同特性,催化臭氧氧化的效果也不尽相同,相同臭氧催化剂针对不同废水会影响臭氧催化剂使用寿命,和增加了污水处理成本。
技术实现要素:3.本发明为了解决现有的常规臭氧催化剂制备方法存在特异性低、活性金属易流失、制备原料利用率低、制备过程繁琐和时间长等问题,提出了一种用于农药废水中高浓度有机磷转化处理的臭氧催化剂、制备方法及应用。
4.一种用于农药废水中高浓度有机磷转化处理的臭氧催化剂,所述臭氧催化剂包括活性金属组分、助剂金属和载体,所述活性金属组分为mn、ti、fe、co、cu、v中的至少两种,所述助剂金属为la或ce中的任一种,所述载体为预处理后的γ
‑
氧化铝,以所述臭氧催化剂的总重量计,所述活性金属组分和所述助剂金属在所述臭氧催化剂上的负载量为1.0
‑
5.0wt%。
5.本发明还提出一种采用如上述所述的一种用于农药废水中高浓度有机磷转化处理的臭氧催化剂的制备方法,包括如下步骤:
6.制备预处理后的γ
‑
氧化铝载体;
7.制备浸渍液,所述浸渍液包括活性金属组分的盐溶液和助剂金属盐溶液;
8.浸渍液在浸泡条件下浸泡预处理后的γ
‑
氧化铝载体后并搅拌,以制得中间体;
9.分别在干燥条件和焙烧条件下对中间体进行干燥、焙烧,得到所述臭氧催化剂。
10.其中,所述制备预处理后的γ
‑
氧化铝载体包括以下步骤:
11.将γ
‑
氧化铝载体在加热沸腾的离子水ph为弱酸性的条件下,煮沸30
‑
60min,冷却后用去离子水冲洗1
‑
3次;
12.然后将γ
‑
氧化铝载体在加热沸腾的的离子水ph为弱碱性的条件下,煮沸30
‑
60min,冷却后用去离子水冲洗1
‑
3次;
13.最后将γ
‑
氧化铝载体在去离子水中静置30
‑
60min,取出后在100℃
‑
105℃下恒温处理30
‑
60min,从而得到预处理后的γ
‑
氧化铝载体。
14.其中,所述制备浸渍液包括以下步骤:
15.按照预处理后γ
‑
氧化铝的空隙体积,计算需要的活性金属组分和稀土金属的质量,将活性金属组分和稀土金属溶于2倍空隙体积去离子水中,制得浸渍液。
16.其中,所述浸泡条件为:
17.浸泡温度为50℃
‑
80℃,浸泡时间为2h~8h。
18.其中,所述搅拌的搅拌速率为100rpm~300rpm,搅拌时间为1h~3h。
19.其中,所述干燥条件为:
20.干燥温度为100℃
‑
120℃,干燥时间为2h~5h。
21.其中,所述焙烧条件为:
22.焙烧温度为500℃
‑
600℃,焙烧时间为2h~5h。
23.本发明还提出一种采用如上述所述的一种用于农药废水中高浓度有机磷转化处理的臭氧催化剂在高浓度有机磷废水中的应用。
24.其中,所述高浓度有机磷废水的总含磷量在1500~3000mg/l,反应条件为常温常压,初始ph为6
‑
8,进水流量为1
‑
5l/min,所述臭氧催化剂与总含磷量的重量比为0.5
‑
1.0,所述臭氧催化剂浓度为50
‑
150mg/l。
25.本发明的有益效果为:本发明提出一种臭氧催化剂及制备方法和应用,采用预处理后的γ
‑
氧化铝作为载体,活性金属组分和助剂金属的盐溶液中进行浸泡、干燥、焙烧得到的臭氧催化剂具备较好的催化臭氧氧化特异性,特别针对高浓度有机磷废水,具有很高的有机磷到无机磷的转化率,并且稳定性高,且制备工艺简单,制备材料利用率高,可实现工程化。
附图说明
26.为了更清楚地说明本发明实施例或现有技术中的技术方案,下面将对实施例或现有技术描述中所需要使用的附图作简单地介绍,显而易见地,下面描述中的附图仅仅是本发明的一些实施例,对于本领域普通技术人员来讲,在不付出创造性劳动的前提下,还可以根据这些附图获得其他的附图。
27.图1是本发明一种用于农药废水中高浓度有机磷转化处理的臭氧催化剂、制备方法及应用的制备工艺步骤图。
28.图2是本发明一种用于农药废水中高浓度有机磷转化处理的臭氧催化剂、制备方法及应用的预处理γ
‑
氧化铝的制备工艺步骤图。
29.图3是本发明一种用于农药废水中高浓度有机磷转化处理的臭氧催化剂、制备方法及应用的制备浸渍液的制备工艺步骤图。
具体实施方式
30.下面详细描述本发明的实施例,所述实施例的示例在附图中示出,其中自始至终相同或类似的标号表示相同或类似的元件或具有相同或类似功能的元件。下面通过参考附图描述的实施例是示例性的,旨在用于解释本发明,而不能理解为对本发明的限制。
31.在本发明的描述中,需要理解的是,术语“长度”、“宽度”、“上”、“下”、“前”、“后”、“左”、“右”、“竖直”、“水平”、“顶”、“底”“内”、“外”等指示的方位或位置关系为基于附图所
示的方位或位置关系,仅是为了便于描述本发明和简化描述,而不是指示或暗示所指的装置或元件必须具有特定的方位、以特定的方位构造和操作,因此不能理解为对本发明的限制。此外,在本发明的描述中,“多个”的含义是两个或两个以上,除非另有明确具体的限定。
32.请参阅图1至图3,本发明提供一种技术方案:
33.一种用于农药废水中高浓度有机磷转化处理的臭氧催化剂,所述臭氧催化剂包括活性金属组分、助剂金属和载体,所述活性金属组分为mn、ti、fe、co、cu、v中的至少两种,所述助剂金属为la或ce中的任一种,所述载体为预处理后的γ
‑
氧化铝,以所述臭氧催化剂的总重量计,所述活性金属组分和所述助剂金属在所述臭氧催化剂上的负载量为1.0
‑
5.0wt%。
34.本发明还提出一种采用如上述所述的一种用于农药废水中高浓度有机磷转化处理的臭氧催化剂的制备方法,包括如下步骤:
35.s101:制备预处理后的γ
‑
氧化铝载体;
36.s102:制备浸渍液,所述浸渍液包括活性金属组分的盐溶液和助剂金属盐溶液;
37.s103:浸渍液在浸泡条件下浸泡预处理后的γ
‑
氧化铝载体后并搅拌,以制得中间体;
38.s104:分别在干燥条件和焙烧条件下对中间体进行干燥、焙烧,得到所述臭氧催化剂。
39.进一步的,所述制备预处理后的γ
‑
氧化铝载体包括以下步骤:
40.s201:将γ
‑
氧化铝载体在加热沸腾的离子水ph为弱酸性的条件下,煮沸30
‑
60min,冷却后用去离子水冲洗1
‑
3次;
41.s202:然后将γ
‑
氧化铝载体在加热沸腾的的离子水ph为弱碱性的条件下,煮沸30
‑
60min,冷却后用去离子水冲洗1
‑
3次;
42.s203:最后将γ
‑
氧化铝载体在去离子水中静置30
‑
60min,取出后在100℃
‑
105℃下恒温处理30
‑
60min,从而得到预处理后的γ
‑
氧化铝载体。
43.进一步的,所述制备浸渍液包括以下步骤:
44.s301:按照预处理后γ
‑
氧化铝的空隙体积,计算需要的活性金属组分和稀土金属的质量,将活性金属组分和稀土金属溶于2倍空隙体积去离子水中,制得浸渍液。
45.进一步的,所述浸泡条件为:
46.浸泡温度为50℃
‑
80℃,浸泡时间为2h~8h。
47.进一步的,所述搅拌的搅拌速率为100rpm~300rpm,搅拌时间为1h~3h。
48.进一步的,所述干燥条件为:
49.干燥温度为100℃
‑
120℃,干燥时间为2h~5h。
50.进一步的,所述焙烧条件为:
51.焙烧温度为500℃
‑
600℃,焙烧时间为2h~5h。
52.本发明还提出一种采用如上述所述的一种用于农药废水中高浓度有机磷转化处理的臭氧催化剂在高浓度有机磷废水中的应用。
53.进一步的,所述高浓度有机磷废水的总含磷量在1500~3000mg/l,反应条件为常温常压,初始ph为6
‑
8,进水流量为1
‑
5l/min,所述臭氧催化剂与总含磷量的重量比为0.5
‑
1.0,所述臭氧催化剂浓度为50
‑
150mg/l。
54.预处理后的γ
‑
氧化铝载体,在加热沸腾的离子水ph为弱酸的条件下,煮沸30
‑
60min,冷却后用去离子水冲洗1
‑
3次;然后在加热沸腾的的离子水ph为弱碱性的条件下,煮沸30
‑
60min,冷却后用去离子水冲洗1
‑
3次,预处理γ
‑
氧化铝质量与酸碱溶液体积比为0.5
‑
1.0,与清洗液的体积比为0.2
‑
0.5;最后在去离子水中静置30
‑
60min,取出后放在100℃
‑
105℃恒温箱中30
‑
60min,从而得到所述预处理臭氧催化剂载体,配制活性金属组分盐溶液和助剂金属盐溶液混合溶液:按照预处理后γ
‑
氧化铝的空隙体积,计算需要相应质量活性金属组分质量和助剂金属质量,将其溶于2倍空隙体积去离子水中,得到活性金属盐溶液/助剂金属盐溶液混合溶液;以预处理后γ
‑
氧化铝为载体,将活性金属组分盐溶液/助剂金属盐溶液混合溶液浸渍于预处理后γ
‑
氧化铝载体上,得到臭氧催化剂中间体;将臭氧催化剂中间体于100
‑
120℃干燥2
‑
5h,冷却室温后,以500
‑
600℃焙烧2
‑
5h,最后再100
‑
120℃干燥2
‑
5h,得到成型的臭氧催化剂。
55.具体实施例实施条件:
56.总磷含量和正磷酸根磷采用德国默克公司生产的prove600光度计进行测定;ph采用雷磁phs
‑
3c精密ph计测定;使用固定床连续反应评价装置评价所制备的臭氧催化剂在催化臭氧氧化技术中的应用。
57.实验采用的乙烯利生产废水水质:总磷含量:2400mg/l,ph:7.5,连续反应:常温常压,初始ph为7.5,o3(mg/l):总磷含量(mg/l)=0.5
‑
1.0,o3浓度为100mg/l,o3出气流量为25
‑
250ml/min,反应时间为2h,废水进水流量:2l/h。
58.优选的,所述活性金属组分中mn元素、ti元素、co元素和fe元素的质量比为2:1:1:2、4:1:1:2、2:2:1:2、2:1:2:2、2:1:1:4中的一种。
59.优选的,所述浸渍液中的mn元素、ti元素、co元素和fe元素的含量按照1kgγ
‑
氧化铝负载10g
‑
20g的mn元素、5g
‑
10g的ti元素、5g
‑
10g的co元素、10g
‑
20g的fe元素的比例进行配置。
60.优选的,所述助剂金属为la和ce中的一种,所述助剂金属为ce,并且在浸渍液中,ce元素的含量按照1kgγ
‑
氧化铝负载0.1g
‑
0.5g的ce元素。
61.具体实施例1:
62.取10g氧化锰、5g纳米二氧化钛、5g硝酸钴和10g九水合硝酸铁溶解于质量分数为0.1
‰
的硝酸铈溶液中,并继续定容至1000ml,得到混合溶液a;
63.以预处理后的γ
‑
氧化铝为载体,将混合溶液a以等2倍体积浸渍法浸渍于预处理后的γ
‑
氧化铝载体上,得到中间体a;
64.中间体a于105℃干燥2h,冷却至室温后,600℃焙烧2h,得到臭氧催化剂a。
65.具体实施例2:
66.取20g氧化锰、5g纳米二氧化钛、5g硝酸钴和10g九水合硝酸铁溶解于质量分数为0.1
‰
的硝酸铈溶液中,并继续定容至1000ml,得到混合溶液b;
67.以预处理后的γ
‑
氧化铝为载体,将混合溶液b以等2倍体积浸渍法浸渍于预处理后的γ
‑
氧化铝载体上,得到中间体b;
68.中间体b于105℃干燥2h,冷却至室温后,600℃焙烧2h,得到臭氧催化剂b。
69.具体实施例3
70.取10g氧化锰、10g纳米二氧化钛、5g硝酸钴和10g九水合硝酸铁溶解于质量分数为
0.1
‰
的硝酸铈溶液中,并继续定容至1000ml,得到混合溶液c;
71.以预处理后的γ
‑
氧化铝为载体,将混合溶液c以等2倍体积浸渍法浸渍于预处理后的γ
‑
氧化铝载体上,得到中间体c;
72.中间体c于105℃干燥2h,冷却至室温后,600℃焙烧2h,得到臭氧催化剂c。
73.具体实施例4
74.取10g氧化锰、5g纳米二氧化钛、10g硝酸钴和10g九水合硝酸铁溶解于质量分数为0.5
‰
的硝酸铈溶液中,并继续定容至1000ml,得到混合溶液d;
75.以预处理后的γ
‑
氧化铝为载体,将混合溶液d以等2倍体积浸渍法浸渍于预处理后的γ
‑
氧化铝载体上,得到中间体d;
76.中间体d于105℃干燥2h,冷却至室温后,600℃焙烧2h,得到臭氧催化剂d。
77.具体实施例5:
78.取10g氧化锰、5g纳米二氧化钛、5g硝酸钴和20g九水合硝酸铁溶解于质量分数为0.1
‰
的硝酸铈溶液中,并继续定容至1000ml,得到混合溶液e;
79.以预处理后的γ
‑
氧化铝为载体,将混合溶液e以等2倍体积浸渍法浸渍于预处理后的γ
‑
氧化铝载体上,得到中间体e;
80.中间体e于105℃干燥2h,冷却至室温后,600℃焙烧2h,得到臭氧催化剂e。
81.具体实施例6:
82.取10g氧化锰、5g纳米二氧化钛、5g硝酸钴和10g九水合硝酸铁溶解于质量分数为0.2
‰
的硝酸铈溶液中,并继续定容至1000ml,得到混合溶液f;
83.以预处理后的γ
‑
氧化铝为载体,将混合溶液f以等2倍体积浸渍法浸渍于预处理后的γ
‑
氧化铝载体上,得到中间体f;
84.中间体f于105℃干燥2h,冷却至室温后,600℃焙烧2h,得到臭氧催化剂f。
85.具体实施例7:
86.取10g氧化锰、5g纳米二氧化钛、5g硝酸钴和10g九水合硝酸铁溶解于质量分数为0.1
‰
的硝酸铈溶液中,并继续定容至1000ml,得到混合溶液g;
87.以预处理后的γ
‑
氧化铝为载体,将混合溶液g以等2倍体积浸渍法浸渍于预处理后的γ
‑
氧化铝载体上,得到中间体g;
88.中间体g于105℃干燥2h,冷却至室温后,600℃焙烧2h,得到臭氧催化剂g。
89.对照例:
90.取预处理后的γ
‑
氧化铝于105℃干燥2h,冷却至室温后,600℃焙烧2h,得到空白臭氧催化剂。
91.实施对照结果:
92.将本发明的臭氧催化剂用于固定床反应器中处理废水,废水为某农药企业有机磷农药生产废水,该有机磷农药废水包括清洗、直接冷凝水和生产废水,其中以生产废水为主,并且其中总磷含量为大约2400mg/l,正磷酸根磷含量低于5mg/l臭氧催化剂床层体积为2l、进水流量2l/h、臭氧浓度为100mg/l、臭氧投加量为1200mg/l。在室温下连续运行5h时,废水的总磷含量到正磷酸根磷转化率和臭氧催化剂的金属离子溶出度列,反应结果见表1。
93.表1
[0094][0095]
通过表1可以看出,使用根据本发明构思的具体实施例中的臭氧催化剂的有机磷转化率明显高于使用根据对比例的空白臭氧催化剂的有机磷转化率,且使用根据本发明具体实施例1的臭氧催化剂a的离子溶出浓度明显低于其他具体实施例的臭氧催化剂b、臭氧催化剂c、臭氧催化剂d、臭氧催化剂e、臭氧催化剂f、臭氧催化剂g的离子溶出浓度且转化率相似。
[0096]
本发明通过浸渍的方式将多活性组分负载在预处理后γ
‑
氧化铝载体上以制得催化臭氧氧化臭氧催化剂,这种制备方法优于一般的浸渍的方法所制备的臭氧催化剂。具体体现在但不限于以下方面中:金属离子溶出度大大降低,保证出水金属离子浓度不超标;由于金属离子溶出度大大降低,从而使得臭氧催化剂使用寿命大大延长,降低了投资成本;有机磷转化效果得到明显提高,降低了运行成本。
[0097]
以上所揭露的仅为本发明一种较佳实施例而已,当然不能以此来限定本发明之权利范围,本领域普通技术人员可以理解实现上述实施例的全部或部分流程,并依本发明权利要求所作的等同变化,仍属于发明所涵盖的范围。