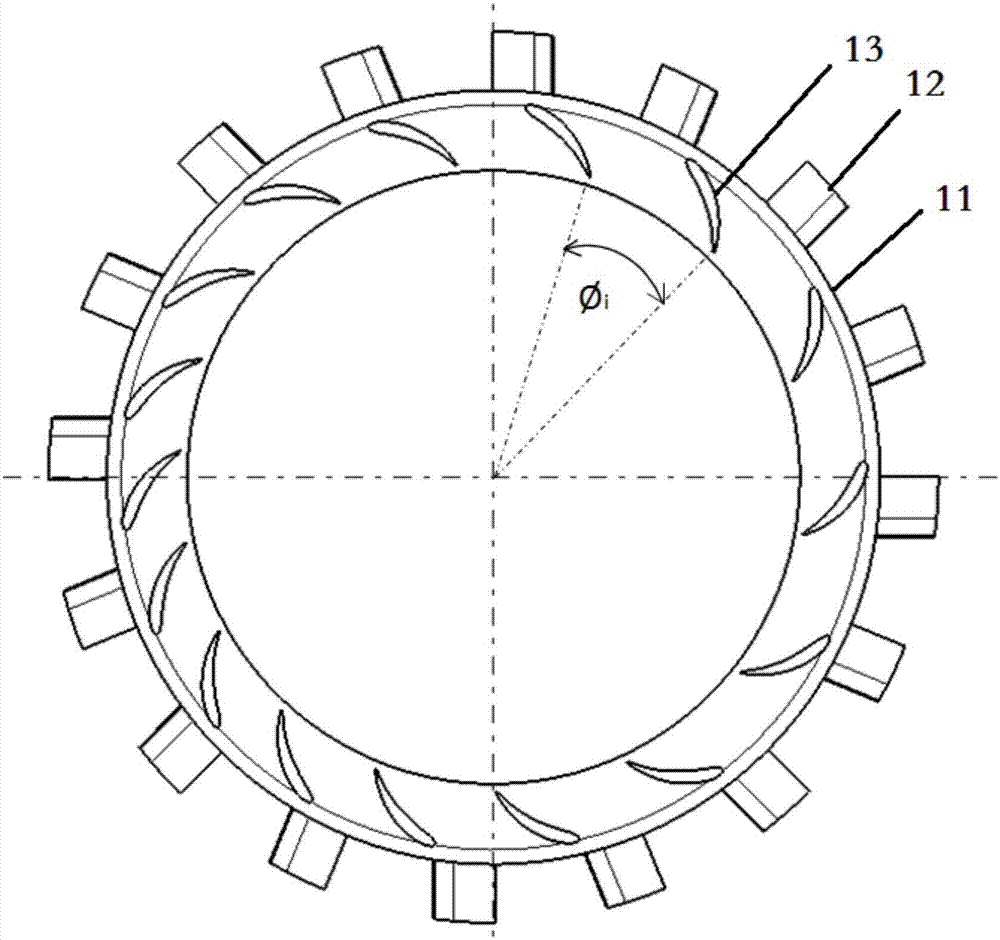
本实用新型涉及一种新型扩压器及包括该扩压器的风机。
背景技术:
:对于吸尘器噪音而言,风机部分是主要的声源。降噪的需求往往出现在产品开发后期,基于控制成本考虑,希望对现有设计改动小。吸尘器的方面的主动降噪,风机的再优化设计是很重要的一部分。风机噪音中的离散噪音,尤其叶片通过频率处的高噪音是产品设计生产中经常遇到的问题。高频处的噪声峰值若过大,人耳常感到声音尖锐,极大的降低了产品的舒适度体验。常规的办法是将叶轮叶片改为非对称分布,但是这样往往导致叶轮的初始动不平衡量很大,叶轮切除量较大,从而也较大的影响了叶轮的气动性能,降低了风机效率。技术实现要素:为了解决上述技术问题,本实用新型提出了一种新型扩压器及包括该扩压器的风机,其可以有效地降低风机的气动噪声,而且对风机性能影响很小。为了达到上述目的,本实用新型的技术方案如下:一种新型扩压器,包括呈圆环柱体的扩压器本体、设置于扩压器本体外侧壁上的多个导叶片以及设置于扩压器本体端面上的多个扩压片,多个扩压片之间采用非等角分布。常规扩压片采用等角分布,相邻扩压片之间的夹角相同。而本实用新型扩压器扩压片采用非等角分布,能有效地降低风机的气动噪声,而且对风机性能影响很小。在上述技术方案的基础上,还可做如下改进:作为优选的方案,相邻扩压片之间的夹角满足以下关系式,i<=n;其中,为扩压片i与扩压片i+1之间的夹角;为等角分布对应n个扩压片时的相邻两扩压片之间的夹角,即n为扩压片的个数;A为常数。采用上述优选的方案,能有效地降低风机的气动噪声,而且对风机性能影响很小。作为优选的方案,A在0.03至0.25之间。采用上述优选的方案,避免夹角最大最小值之间差异过大。作为优选的方案,扩压片的型线为弯曲的对称翼型。采用上述优选的方案,翼型扩压片有助于减小叶片尾部涡流,从而提高叶轮效率。作为优选的方案,扩压片的翼型中弧线为圆弧,将中弧线m等分,等分点为P1、P2、...Pm-1,各点到翼型上弧线和翼型下弧线的距离相等。采用上述优选的方案,减小扩压片压力面近壁面处的流动分离,从而降低风机宽频噪音。作为优选的方案,扩压片的前缘和尾缘的尖锐部分具有倒圆。采用上述优选的方案,结构尺寸,风机的性能更佳。作为优选的方案,多个导叶片绕扩压器本体的中心呈圆周等角均匀分布。采用上述优选的方案,扩压器的导叶片与电机机壳配合形成密封的导流流道。作为优选的方案,导叶片在扩压器本体侧壁上的投影为等厚曲面,该等厚曲面的外曲面型线L为椭圆线。采用上述优选的方案,可以有效将气流导向旋转轴流向。作为优选的方案,外曲面型线L底部的切线与扩压器本体中心线的夹角为θ,θ在0°至30°之间。采用上述优选的方案,导流效果更佳。风机,包括:叶轮、风罩以及机壳,还包括新型扩压器,扩压器设置于轴承支撑板上,与轴承支撑板配合连接。本实用新型提出的风机从非旋转部件的扩压器入手,改善叶轮与扩压器之间的动静干涉,打破这种周期性,降低扩压片通过频率的离散噪音。附图说明图1为本实用新型实施例提供的一种新型扩压器的结构示意图。图2为本实用新型实施例提供的一种新型扩压器的俯视图。图3为本实用新型实施例提供的风机的局部结构示意图。图4为本实用新型实施例提供的风机匹配不同扩压器的噪声对比图。图5为本实用新型实施例提供的扩压片的结构示意图。图6为本实用新型实施例提供的一种新型扩压器的主视图。其中:1扩压器、11扩压器本体、12导叶片、13扩压片、2叶轮、3风罩、4机壳、5轴承支撑板、61翼型中弧线、62翼型上弧线、63翼型下弧线;a-采用本实用新型扩压器的风机噪音曲线,b-采用等角扩压片的扩压器的风机噪音曲线。具体实施方式下面结合附图详细说明本实用新型的优选实施方式。为了达到本实用新型的目的,一种新型扩压器及包括该扩压器的风机的其中一些实施例中,如图1和2所示,一种新型扩压器1包括呈圆环柱体的扩压器本体11、设置于扩压器本体11外侧壁上的多个导叶片12以及设置于扩压器本体11端面上的多个扩压片13,多个扩压片13之间采用非等角分布。如图3所示,风机包括:新型扩压器1、叶轮2、风罩3、机壳4以及轴承支撑板5,扩压器1设置于轴承支撑板5上,与轴承支撑板5配合连接。扩压器1为中空结构,与轴承支撑板5为接触配合,并有键槽定位。同一叶轮2可以匹配有不同结构的扩压器1,以满足不同孔板流量的静压和效率需要,而不需要改动电机本体结构,风罩,轴承支撑板等,只需要重新修改扩压器,如扩压片安放角度等,以更换当前的扩压器,即做到一机多用。本实用新型的扩压器将叶轮2出口气流进行90°的转弯,即从水平流向改为竖直流向(或反之)。扩压片13使得气流减速并均匀扩压,减少流动中冲击损失。导叶片12将低速的气流实现90°转向。本实用新型从非旋转部件的扩压器入手,改善叶轮与扩压器之间的动静干涉,打破这种周期性,降低叶片通过频率的离散噪音,相对于非等角叶片叶轮的动平衡处理,能够减少加工成本,加工工艺也更为简单。常规扩压片采用等角分布,相邻扩压片之间的夹角相同。而本实用新型扩压器扩压片采用非等角分布,能有效地降低风机的气动噪声,而且对风机性能影响很小。实验证明,能够使得风机噪音总声功率降低3dBA左右,有效提高风机的综合性能。为了进一步地优化本实用新型的实施效果,在另外一些实施方式中,其余特征技术相同,不同之处在于,相邻扩压片13之间的夹角满足以下关系式,i<=n;其中,为扩压片i与扩压片i+1之间的夹角;为等角分布对应n个扩压片时的相邻两扩压片之间的夹角,即n为扩压片的个数;A为常数,A在0.03至0.25之间。采用上述优选的方案,能有效地降低风机的气动噪声,而且对风机性能影响很小,A在0.03至0.25之间,避免夹角最大最小值之间差异过大。表1举例说明了A=0、0.1、0.2、0.3时相邻扩压片之间的夹角数值。表1相邻扩压片之间的夹角数值表如图4所示,经实验证明,匹配现有一款混流叶轮,和等角等厚圆弧扩压片相比,其叶片通过频率点的噪音由原来的77.7dB降低到至71dB.降幅达到6.6dBA。为了进一步地优化本实用新型的实施效果,在另外一些实施方式中,其余特征技术相同,不同之处在于,扩压片13的型线为弯曲的对称翼型。采用上述优选的方案,翼型扩压片13有助于减小叶片尾部涡流,从而提高叶轮效率。如图5所示,进一步,扩压片13的翼型中弧线61为圆弧,将中弧线m等分,等分点为P1、P2、...Pm-1,其中t1、t2、...tm-1为各点到中弧线的距离,各点到翼型上弧线62和翼型下弧线63的距离相等,即厚度相等。采用上述优选的方案,减小扩压片压力面近壁面处的流动分离,从而降低风机宽频噪音。先确定中弧线长度S,若将中弧线10等分,单位弦长为1的NACA0012翼型弦长0.1处对应厚度T约为0.048,则完全对称翼型中弧线P1点对应处的翼型厚度则为0.048*S。具体数值计算,见表2。表2扩压片厚度表弦长百分比NACA0012对应弦长处的相对厚度T中弧线长度S弯曲翼型中弧10等分点处的厚度t1.00.0017.30.0090.90.0140.1010.80.0270.1960.70.0360.2630.60.0460.3360.50.0530.3830.40.0580.4240.30.0600.4380.20.0570.4160.10.0480.350在其他实施例中,也也可以选用其他对称翼型,如NACA0006、NACA0008等等。为了进一步地优化本实用新型的实施效果,在另外一些实施方式中,其余特征技术相同,不同之处在于,多个导叶片12绕扩压器本体11的中心呈圆周等角均匀分布。采用上述优选的方案,扩压器的导叶片12与电机机壳4配合形成密封的导流流道。如图6所示,进一步,导叶片12在扩压器本体11侧壁上的投影为等厚曲面,该等厚曲面的外曲面型线L为椭圆线,外曲面型线L底部的切线与扩压器本体中心线的夹角为θ,θ在0°至30°之间。采用上述优选的方案,可以有效将气流导向旋转轴流向。以上的仅是本实用新型的优选实施方式,应当指出,对于本领域的普通技术人员来说,在不脱离本实用新型创造构思的前提下,还可以做出若干变形和改进,这些都属于本实用新型的保护范围。当前第1页1 2 3