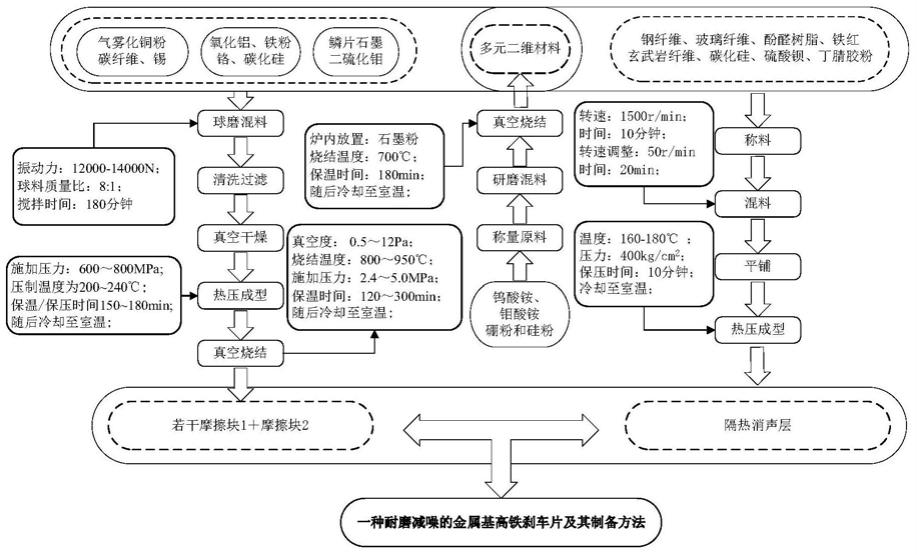
[0001]
本发明涉及一种耐磨减噪的金属基高铁刹车片及其制备方法,属于高铁零部件的摩擦材料技术领域。
背景技术:[0002]
随着现代科技的快速发展,人们对交通运输工具的速度、负荷以及安全性要求越来越高。随着京津城际高铁的开通,我国高铁最高时速已经超过350km/h。保证速度稳定提高的前提是刹车片性能的提升。由于高铁在速度为350km/h的条件下,制动时摩擦表面上的瞬时最高温度可能超过900℃,故传统的合成材料和普通的粉末冶金材料无法承受如此苛刻的工况。我国的刹车片研发起步比较晚,与世界上的其他发达国家差距较大。刹车片性能的好坏直接影响高铁等交通工具的稳定性和可靠性,关系到操作人员与乘客们的生命和财产安全。
[0003]
摩擦材料是刹车片摩擦副的关键材料,其性能好坏直接影响刹车片的制动效果。理想的刹车片摩擦材料不能产生有害健康的物质;此外,对汽车刹车片的制造工艺和技术装备也提出了越来越严格的要求,即除了有适当的摩擦系数、高温高速和高压下保持稳定外,还要求耐磨、强度高、导热性好、噪声小和不产生咬死等。
[0004]
高速列车制动系统刹车片的摩擦材料有铁基和铜基粉末冶金刹车片;其中,对铜基粉末冶金摩擦材料刹车片的运用最广泛,速度在250km/h以上的高速列车多采用铜基粉末冶金刹车片。为打破国外技术壁垒,急需开发一种新型高性能金属基高铁刹车片以满足我国高速列车在复杂工况下服役的要求。
技术实现要素:[0005]
针对现有技术的不足,本发明目的是提供一种耐磨减噪的金属基高铁刹车片及其制备方法,所制备的金属基刹车片能满足良好的机械摩擦性能,具备适当的摩擦系数、低磨损率、良好的隔热耐磨和减噪的性能,可以解决现存产品摩擦材料的磨损率高、刹车灵敏低、使用寿命短及噪声污染大等问题。
[0006]
为实现以上目的,本发明通过以下技术方案予以实现:
[0007]
一种耐磨减噪的金属基高铁刹车片,其特征在于主要包括隔热消声层、摩擦块和背板,所述隔热消声层平铺安设于背板上且与背板通过热压成型连接,所述摩擦块安装在隔热消声层。
[0008]
按上述方案,所述摩擦块的原料按质量百分比包括:铜42-60wt.%、碳纤维1.2-4wt.%和锡2.5-6wt.%;氧化铝3-6.2wt.%、铁12-20wt.%、铬4.5-10wt.%和碳化硅:2.5-4.5wt.%;石墨12-16wt.%、二硫化钼1.5-3wt.%和多元二维材料1.5-2wt.%;其中,多元二维材料主要由钨酸铵、钼酸铵、硼和硅混合烧结而成。其中,摩擦块的基体组元为铜粉、碳纤维和锡,摩擦组元为氧化铝、铁、铬和碳化硅,润滑组元为石墨、二硫化钼和多元二维材料。
[0009]
按上述方案,所述隔热消声层的原料按质量百分比包括:钢纤维35-45wt.%、玻璃纤维4-6wt.%、酚醛树脂5-15wt.%、玄武岩纤维8-12wt.%、碳化硅2-5wt.%、硫酸钡10-18wt.%、丁腈胶粉8-16wt.%、铁红7-13wt.%和多元二维材料1.5-3wt.%;其中,多元二维材料主要由钨酸铵、钼酸铵、硼和硅混合烧结合成。
[0010]
按上述方案,所述多元二维材料主要由钨酸铵16-20wt.%、钼酸铵14-18wt.%、硼粉30-34wt.%和硅粉原料粉末32-35wt.%混合烧结而成。
[0011]
进一步地,所述摩擦块的制备方法,主要包括如下步骤:
[0012]
1)配料和研磨:按原料的质量百分比分别称量铜粉、碳纤维、锡、氧化铝、铁粉、铬、碳化硅、石墨、二硫化钼和多元二维材料,球磨混合均匀,得到混合粉末;其中,所述的铜粉、铁粉、铬和锡的粒径为70-80μm,纯度在99.5%以上;鳞片石墨的粒径为130-150μm;碳化硅、二硫化钼和氧化铝的粒径在70-140μm,纯度在90%以上;
[0013]
2)热压成型:将步骤1)所得混合粉末放入成型模具中,采用热压成型工艺压制成压坯;
[0014]
3)真空加压烧结:将步骤2)的压坯放入真空烧结炉中进行烧结,得到摩擦块。其中,热压成型工艺的主要参数为:施加压力为600-800mpa,压制温度为200-240℃,保温、保压时间150-180min,随后冷却至室温;在真空烧结炉进行烧结时,真空度为0.5-12pa,烧结温度为800-950℃,施加压力为2.4-5mpa,保温时间120-300min,随炉冷却至室温。
[0015]
进一步地,所述隔热消声层的制备方法,主要包括如下步骤:
[0016]
1)按原料的质量百分比分别称量钢纤维、玻璃纤维、酚醛树脂、玄武岩纤维、碳化硅、硫酸钡、丁腈胶粉、铁红和多元二维材料;
[0017]
2)将将步骤1)称量的原料经混料机得到均匀混料,然后所述混料平铺于背板上进行热压成型,冷却至室温,得到平铺于背板上的隔热消声层。其中,热压成型时,温度为160-180℃,压力为400-600kg/cm2,保压时间为10-30min。
[0018]
进一步地,所述多元二维材料的制备方法为:按多元二维材料的原料的成分配比,将钨酸铵、钼酸铵、硼粉和硅粉原料粉末通过研磨机进行研磨混合,再用气氛炉烧结,烧结温度为600-800℃,保温时间为180-210min,烧结保护气氛为氩气,烧结过程中通入氧气增强反应,氧气通入量为60-150ml/min,制备得到多元二维材料。
[0019]
本发明的目的还在于提供一种耐磨减噪的金属基高铁刹车片的制备方法,主要包括如下步骤:
[0020]
1)根据尺寸和材质选取刹车片的背板;
[0021]
2)隔热消声层平铺于背板上,然后通过热压成型将隔热消声层和背板进行连接,热压成型时的温度为160-180℃,压力为400-600kg/cm2,保压时间为10-30min,冷却至室温,得到平铺于背板上的隔热消声层;
[0022]
3)摩擦块通过螺栓与隔热消声层和背板进行连接固定,得到耐磨减噪的金属基高铁刹车片。
[0023]
按上述方案,隔热消声层的厚度优选为3-5mm,背板的厚度优选为6-8mm,摩擦块的厚度优选为6-9mm。背板材质通常是钢板,优选q235。
[0024]
按上述方案,摩擦块为若干块,分为摩擦块1和摩擦块2,摩擦块1位于最内排和最外排,摩擦块2位于中间排(注:处在最内排和最外排之间的排数构成中间排)。优选地,摩擦
块2为中间设有通孔的六棱柱;摩擦块1靠近消音层外廓线的侧面为弧形(即摩擦块1背离摩擦块2的侧面为弧形),不靠近消音层外廓线的侧面与摩擦块2的侧面相同。更优选地,摩擦块1的截面面积为78-143mm2,摩擦块2的截面面积为93-156mm2;摩擦块呈均匀分布,间距优选为9-15mm。
[0025]
本发明所制备的耐磨减噪的金属基高铁刹车片具备适当的摩擦系数、低磨损率和减少噪声的性能,在测试中的累计磨损率<1.2
×
10-7
cm3/(n
·
m),振动噪声为68-75db,硬度hrs为60.35-72.86;滑动摩擦系数:0.32-0.45,性能参数优于国家标准和传统刹车片产品。
[0026]
本发明所述的金属基高铁刹车片在原料设置上的主要构思如下:摩擦块所使用基体组元铜的硬度很低,导热性和耐磨性能较好,但铁、二碳化硅等强化摩擦组元的硬度很高,加入到基体中可以相助提高材料的硬度指标和摩擦系数,使得摩擦块在摩擦磨损的过程中显示出更好的耐磨性;所使用的氧化铝和二碳化硅具有高温稳定性和高硬度,而铁更加耐高温,能够承受较大载荷,使得金属基高铁刹车片高温承受能力强且硬度较高,降低材料磨损;所使用的二碳化硅与金属基体通过物理化学反应能够形成了一层过渡层,有利于提高材料的强度;且铁在基体铜中的溶解度较小,铁基本上以颗粒状态镶嵌于基体中,组织较为致密,没有特别粗大的相,使得高铁刹车片强度硬度均得到改善,从而增强刹车片的承载能力;所使用的摩擦层中的鳞片石墨和二硫化钼和多元二维材料作为润滑组元,起到降低材料磨损率、降低摩擦表面磨损和材料发生摩擦自激振尖叫的倾向,有效抑制摩擦噪声的产生。此外,隔热消声层中的多元二维材料能够对噪声进行吸收,从而减弱噪声的传播。
[0027]
与现有技术相比,本发明有益效果如下:
[0028]
1.本发明的高铁刹车片具有具备适当的摩擦系数、低磨损率、良好的隔热耐磨和减噪的性能,能够提高使用寿命和刹车灵敏且减少噪声污染等特点,可以解决现存产品摩擦材料的磨损率高、刹车灵敏低、使用寿命短及噪声污染大等问题。
[0029]
2.本发明所述金属基高铁刹车片,其摩擦块的润滑组元使用了由钨酸铵、钼酸铵、硼粉和硅粉原料粉末混合制成的多元二维材料,起到降低材料磨损率、降低摩擦表面磨损和材料发生摩擦自激振尖叫的倾向,有效抑制摩擦噪声的产生。
[0030]
3.本发明所述金属基高铁刹车片,其独特的隔热消声层配方及多元二维材料的使用能够对噪声进行吸收,从而减弱噪声的传播,起到较好的减噪作用。
[0031]
4.本发明所述金属基高铁刹车片,所使用的摩擦块边缘为圆弧形,可以对边缘减少应力集中,提高使用寿命;且独特的摩擦块配方及由内到外的摩擦块布局,能够起到较好的制动效果,使制动灵敏度和耐磨性能得到提高。
附图说明
[0032]
图1是本发明所述的耐磨减噪的金属基高铁刹车片的制备方法的工艺流程图。
[0033]
图2是本发明实施例1的多元二维材料的形貌图。
[0034]
图3是本发明实施例2的多元二维材料的形貌图。
[0035]
图4是本发明实施例1、2和3的金属基高铁刹车片硬度变化曲线。
[0036]
图5是本发明实施例1、2和3的金属基高铁刹车片摩擦系数变化曲线。
[0037]
图6是本发明实施例1、2和3的金属基高铁刹车片等效声压级变化曲线。
[0038]
图7是本发明所述的耐磨减噪的金属基高铁刹车片的结构示意图。
具体实施方式
[0039]
为了更好地理解本发明,下面结合实施例对本发明内容进行清楚、完整地描述,但所描述的实施例仅仅是本发明一部分实施例,而不是全部的实施例。
[0040]
下述实施例中,所述的铜粉、铁粉、铬和锡的粒径为70-80μm,纯度在99.5%以上;鳞片石墨的粒径为130-150μm;碳化硅、二硫化钼和氧化铝的粒径在70-140μm,纯度在90%以上。
[0041]
下述实施例中,所述耐磨减噪的金属基高铁刹车片,如图7所示,包括隔热消声层、摩擦块和背板;其中,所述隔热消声层平铺安设于背板上且与背板通过热压成型连接,隔热消声层的截面大小和背板相同;所述摩擦块通过螺栓与隔热消声层和背板进行连接固定。摩擦块为若干块,分为摩擦块1和摩擦块2,摩擦块1位于最内排和最外排,摩擦块2位于中间排;且,摩擦块2为中间设有通孔的六棱柱;摩擦块1为中间设有通孔的柱体,柱体靠近消音层外廓线的侧面为圆弧形,不靠近消音层外廓线的侧面与摩擦块2的侧面相同。摩擦块个数由最内排到最外排逐排递增,间距优选为9-15mm。
[0042]
下述实施例中,背板材质为q235钢板。
[0043]
实施例1
[0044]
一种耐磨减噪的金属基高铁刹车片,包括隔热消声层、摩擦块和背板。具体地,摩擦块1的截面面积为78mm2,摩擦块2的截面面积为93mm2,且,间距为9-12mm,呈均匀分布;背板厚度为6mm,隔热消声层的截面大小和背板相同,厚度为3mm;摩擦块厚度均为6mm。
[0045]
本实施例中,所述摩擦块的原料按质量百分比包括:气雾化铜粉45wt.%、碳纤维3.5wt.%和锡4.5wt.%;氧化铝4.5wt.%、铁粉17.5wt.%、铬4.5wt.%、碳化硅:3.5wt.%;鳞片石墨13wt.%、二硫化钼2.5wt.%和多元二维材料1.5wt.%;
[0046]
所述隔热消声层的原料按质量百分比为:钢纤维37wt.%、玻璃纤维5wt.%、酚醛树脂9wt.%、玄武岩纤维8wt.%、碳化硅3wt.%、硫酸钡14wt.%、丁腈胶粉12wt.%、铁红10wt.%和多元二维材料2wt.%;
[0047]
其中,摩擦块和隔热消声层中的多元二维材料,由钨酸铵18wt.%、钼酸铵18wt.%、硼粉32wt.%和硅粉原料粉末32wt.%混合烧结而成。
[0048]
如图1所示,上述耐磨减噪的金属基高铁刹车片的制备方法,具体包括如下步骤:
[0049]
1)制备多元二维材料:称量钨酸铵(1.8g)、钼酸铵(1.8g)、硼粉(3.2g)和硅粉原料粉末(3.2g),通过研磨机进行研磨混合,再用气氛炉烧结,温度为600℃,保温时间为200min,烧结保护气氛为氩气,烧结过程中通入氧气增强反应,氧气通入量为120ml/min,得到多元二维材料,其形貌图如图2;
[0050]
2)制备摩擦块:称量气雾化铜粉(90.0g)、碳纤维(7.0g)、锡(9.0g)、氧化铝(9.0g)、铁粉(35.0g)、铬(9.0g)、碳化硅(7.0g)、鳞片石墨(26.0g)、二硫化钼(5.0g)和多元二维材料(3.0g),然后一起放入球磨机进行球磨,振动力为12000n,球料质量比为8:1,搅拌时间为180min;球磨结束后,使用去离子水对混合浆料清洗和不锈钢筛子进行过滤,利用真空干燥箱进行干燥处理,得到混合粉末;
[0051]
将上述混合粉末放入模具(模具分别采用摩擦块1和2的模具,则分别制得摩擦块1和2)中,采用热压成型工艺压制成压坯,施加压力为650mpa,压制温度为220℃,保温、保压时间180min,随后冷却至室温;再将压坯固定在支撑背板上,放入真空烧结炉中进行烧结,
真空度为2pa,烧结温度为800℃,施加压力为2.5mpa,保温时间160min,随炉冷却至室温,得到摩擦块1和2。
[0052]
3)制备隔热消音层:称量钢纤维(37.0g)、玻璃纤维(5.0g)、酚醛树脂(9.0g)、玄武岩纤维(8g)、碳化硅(3.0g)、硫酸钡(14.0g)、丁腈胶粉(12.0g)、铁红(10.0g)和多元二维材料(2.0g),然后一起加入混料机中,转速为1500r/min;时间为10min;随后转速调整为50r/min,时间为20min;得到均匀混料;
[0053]
将上述混料平铺于背板上进行热压成型,温度为160℃,压力为600kg/cm2,保压时间为30min,冷却至室温,得到热压成型于背板上的隔热消音层;
[0054]
4)连接固定成型:隔热消声层平铺于背板上,得到热压成型于背板上的隔热消音层;两种摩擦块通过螺栓与隔热消声层和背板进行连接固定,得到耐磨减噪的金属基高铁刹车片。
[0055]
将本实施例制备的耐磨减噪的金属基高铁刹车片,试样尺寸为5mm
×
10mm
×
15mm,在mft-5000摩擦实验机上进行摩擦磨损测试,其中摩擦实验的对磨球材料是氮化硅,往复直线运动的位移为8mm,往复频率为1hz,加载压力为20n;电容式麦克风摩擦噪声测试装置测定噪声,接收频率为3.5hz-20khz,动态测量范围为15-137db;此外,使用hv-1000显微硬度计对试验硬度进行三次测量。其他实施例的测试方法与实施例1相同。
[0056]
根据上述性能测试,实施例1所制备的耐磨减噪的金属基高铁刹车片的累计磨损率<1.2
×
10-7
cm3/(n
·
m),硬度hrs为62.12-68.36(图4),滑动摩擦系数为0.32-0.40(图5),平均等效声压值为70-75db(图6)。
[0057]
实施例2
[0058]
一种耐磨减噪的金属基高铁刹车片,包括隔热消声层、摩擦块和背板。具体地,摩擦块1的截面面积为86mm2,摩擦块2的截面面积为123mm2,且,间距为10-12mm,呈均匀分布;背板厚度为7mm,隔热消声层的截面大小和背板相同,厚度为4mm;摩擦块厚度均为6mm。
[0059]
本实施例中,所述摩擦块的原料按质量百分比包括:气雾化铜粉50wt.%、碳纤维2.0wt.%和锡3.0wt.%;氧化铝4.0wt.%、铁粉15.0wt.%、铬5.0wt.%和碳化硅3.0wt.%;鳞片石墨14.2wt.%、二硫化钼2.0wt.%和多元二维材料1.8wt.%;隔热消声层的原料按质量百分比为钢纤维40wt.%、玻璃纤维4wt.%、酚醛树脂6wt.%、玄武岩纤维10wt.%、碳化硅3wt.%、硫酸钡12wt.%、丁腈胶粉14wt.%、铁红8wt.%和多元二维材料3wt.%。其中,摩擦块和隔热消声层中的多元二维材料,由钨酸铵20wt.%、钼酸铵16wt.%、硼粉30wt.%和硅粉原料粉末34wt.%配制合成。
[0060]
一种耐磨减噪的金属基高铁刹车片的制备方法,多元二维材料的具体制备方法包括如下步骤:
[0061]
1)制备多元二维材料:称量钨酸铵(2.0g)、钼酸铵(1.6g)、硼粉(3.0g)和硅粉原料粉末(3.4g),通过研磨机进行研磨混合,再用气氛炉烧结,温度为700℃,保温时间为180min,烧结保护气氛为氩气,烧结过程中通入氧气增强反应,氧气通入量为100ml/min,得到多元二维材料;
[0062]
2)制备摩擦块:称量气雾化铜粉(100.0g)、碳纤维(4.0g)、锡(6.0g)、氧化铝(8.0g)、铁粉(30.0g)、铬(10.0g)、碳化硅(6.0g)、鳞片石墨(28.4g)、二硫化钼(4.0g)和多元二维材料(3.6g),然后一起放入球磨机进行球磨,振动力为14000n,球料质量比为8:1,搅
拌时间为180min;球磨结束后,使用去离子水对混合浆料清洗和不锈钢筛子进行过滤,利用真空干燥箱进行干燥处理,得到混合粉末;
[0063]
将上述混合粉末放入模具(模具分别采用摩擦块1和2的模具,则分别制得摩擦块1和2)中,采用热压成型工艺压制成压坯,施加压力为700mpa,压制温度为240℃,保温、保压时间160min,随后冷却至室温;再将压坯固定在支撑背板上,放入真空烧结炉中进行烧结,真空度为1.5pa,烧结温度为850℃,施加压力为3.0mpa,保温时间150min,随炉冷却至室温,得到摩擦块1和2;
[0064]
3)制备隔热消音层:称量钢纤维(40.0g)、玻璃纤维(4.0g)、酚醛树脂(6.0g)、玄武岩纤维(10.0g)、碳化硅(3.0g)、硫酸钡(12.0g)、丁腈胶粉(14.0g)、铁红(8.0g)和多元二维材料(3.0g),然后一起加入混料机中,转速为1500r/min;时间为10min;随后转速调整为50r/min,时间为20min;得到均匀混料;
[0065]
将上述混料平铺于背板上进行热压成型,温度为170℃,压力为500kg/cm2,保压时间为20min,冷却至室温,得到热压成型于背板上的隔热消音层;
[0066]
4)连接固定成型:隔热消声层平铺于背板上,得到热压成型于背板上的隔热消音层;两种摩擦块通过螺栓与隔热消声层和背板进行连接固定,得到耐磨减噪的金属基高铁刹车片。
[0067]
根据上述性能测试,本实施例所制备的耐磨减噪的金属基高铁刹车片的累计磨损率<1.2
×
10-7
cm3/(n
·
m),硬度hrs为60.35-68.64(图4),平均滑动摩擦系数为0.37-0.45(图5),平均等效声压值为68-72db(图6)。
[0068]
实施例3
[0069]
一种耐磨减噪的金属基高铁刹车片,包括隔热消声层、摩擦块和背板。具体地,摩擦块1的截面面积为138mm2,摩擦块2的截面面积为152mm2,且,间距为12mm,呈均匀分布;背板厚度为8mm,隔热消声层的截面大小和背板相同,厚度为5mm;摩擦块厚度均为8mm。
[0070]
本实施例中,所述摩擦块的原料按质量百分比包括:气雾化铜粉55.0wt.%、碳纤维1.5wt.%和锡2.5wt.%;摩擦组元:氧化铝3.5wt.%、铁粉14.0wt.%、铬5.0wt.%和碳化硅:2.5wt.%;润滑组元:鳞片石墨13.0wt.%、二硫化钼1.5wt.%和多元二维材料1.5wt.%;隔热消声层的原料按质量百分比为钢纤维42wt.%、玻璃纤维6wt.%、酚醛树脂12wt.%、玄武岩纤维8wt.%、碳化硅2wt.%、硫酸钡10.5wt.%、丁腈胶粉10wt.%、铁红8wt.%和多元二维材料1.5wt.%。其中,摩擦块和隔热消声层中的多元二维材料,由钨酸铵16wt.%、钼酸铵18wt.%、硼粉34wt.%和硅粉原料粉末32wt.%配制合成。
[0071]
一种耐磨减噪的金属基高铁刹车片的制备方法,多元二维材料的具体制备方法包括如下步骤:
[0072]
1)制备多元二维材料:称量钨酸铵(1.6g)、钼酸铵(1.8g)、硼粉(3.4g)和硅粉原料粉末(3.2g),通过研磨机进行研磨混合,再用气氛炉烧结,温度为800℃,保温时间为180min,烧结保护气氛为氩气,烧结过程中通入氧气增强反应,氧气通入量为80ml/min,得到多元二维材料;
[0073]
2)制备摩擦块:称量气雾化铜粉(110.0g)、碳纤维(3.0g)、锡(5.0g)、氧化铝(7.0g)、铁粉(28.0g)、铬(10.0g)、碳化硅(5.0g)、鳞片石墨(26.0g)、二硫化钼(3.0g)和多元二维材料(3.0g),然后一起放入球磨机进行球磨,振动力为12000n,球料质量比为8:1,搅
拌时间为180min;球磨结束后,使用去离子水对混合浆料清洗和不锈钢筛子进行过滤,利用真空干燥箱进行干燥处理,得到混合粉末;
[0074]
将上述混合粉末放入模具(模具分别采用摩擦块1和2的模具,则分别制得摩擦块1和2)中,采用热压成型工艺压制成压坯,施加压力为750mpa,压制温度为240℃,保温、保压时间150min,随后冷却至室温;再将压坯固定在支撑背板上,放入真空烧结炉中进行烧结,真空度为8pa,烧结温度为900℃,施加压力为4mpa,保温时间120min,随炉冷却至室温,得到摩擦块1和2;
[0075]
3)制备隔热消音层:称量钢纤维(42.0g)、玻璃纤维(6.0g)、酚醛树脂(12.0g)、玄武岩纤维(8.0g)、碳化硅(2.0g)、硫酸钡(10.5g)、丁腈胶粉(10.0g)、铁红(8.0g)和多元二维材料(1.5g),然后一起加入混料机中,转速为1500r/min;时间为10min;随后转速调整为50r/min,时间为20min;得到均匀混料;
[0076]
将上述混料平铺于背板上进行热压成型,温度为180℃,压力为400kg/cm2,保压时间为10min,冷却至室温,得到热压成型于背板上的隔热消音层;
[0077]
4)连接固定成型:隔热消声层平铺于背板上,得到热压成型于背板上的隔热消音层;两种摩擦块通过螺栓与隔热消声层和背板进行连接固定,得到耐磨减噪的金属基高铁刹车片。
[0078]
根据上述性能测试,本实施例所制备的耐磨减噪的金属基高铁刹车片的累计磨损率<1.2
×
10-7
cm3/(n
·
m),硬度hrs为65.35-70.65(图4)。滑动摩擦系数为0.40-0.44(图5),平均等效声压值为68-73db(图6)。
[0079]
以上所述仅是本发明的优选实施方式,应当指出,对于本领域的普通技术人员来说,在不脱离本发明创造构思的前提下,还可以做出若干改进和变换,这些都属于本发明的保护范围。