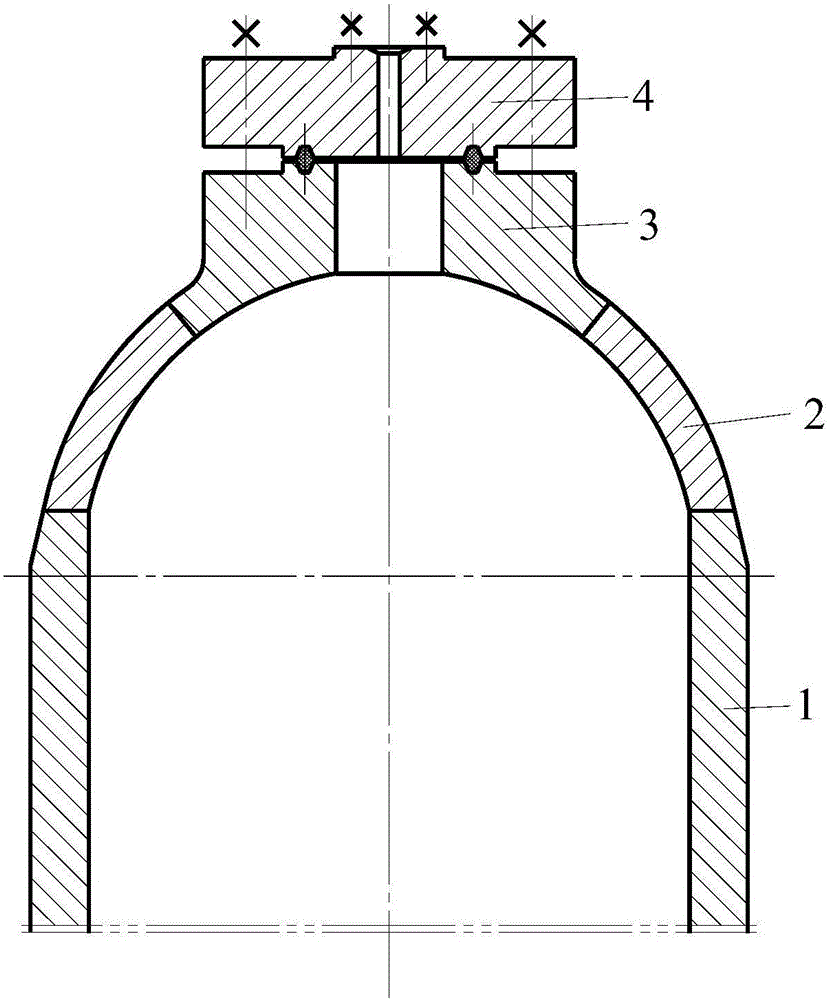
本发明涉及石油化工、煤化工生产
技术领域:
,具体而言,涉及一种缓冲罐。
背景技术:
:目前,某项目低密度高压聚乙烯(简称LDPE)装置采用BASELL工艺技术,。其中,LDPE装置的关键设备是高压氮气缓冲罐,工作温度为39℃,工作压力为29.5MPa,设计温度为90℃/-30℃(最高设计温度为90℃,最低设计温度为-30℃),设计压力高达32.5MPa,设备直径为680mm,罐体长度为5200mm。为了提高设备设计的安全性,经过分析,确定高压氮气缓冲罐按照JB4732《钢制压力容器—分析设计标准》进行设计和制造。对于小直径高压氮气缓冲罐,其罐体1通常采用锻焊结构,罐体1的两端采用球形封头2结构,大开孔通常采用嵌入式接管3结构,详见图1。根据设计条件,该氮气缓冲罐的罐体1、接管3(作为手孔)和法兰盖4选择的材料为高强度低温钢20MnMOD锻件。该材料在设计温度90℃以下,其抗拉强度为530MPa,屈服强度为370MPa,许用应力220Mpa,弹性模量为19550MPa。根据以前高压氮气缓冲罐的设计经验,图1中接管3的结构设计是该高压容器制造成败与否的关键环节之一。除受较高的设计压力外,该接管3的通孔通过法兰盖的通气孔传递将会承受外部管道的载荷。根据配管专业所提条件,接管3的通孔所受载荷如下表1:表1载荷名称管口所承受荷载设计压力P(MPa)32.5经向力FL(N)618750环向力FG(N)618750轴向力FA(N)2505000经向弯矩ML(N*m)51562.50环向弯矩MG(N*m)51562.50扭矩MT(N*m)77343.75采用ANSYS软件将球形封头和接管所建的加载前的应力模型如图2所示,加载表1所列荷载后的应力模型如图3所示。从图3可以看出,应力的最大点在接管3的外壁上,沿该点垂直于内壁做线性化,沿最大点MX到外壁的P2路径应力模型如图4所示,线性化计算结果如下所示:按照JB4732《钢制压力容器》应力评定规则,根据上述的结果可以得出局部薄膜应力为391.4Mpa,远远大于20MnMoD材料的许用应力强度评定值330MPa(1.5×220MPa),而且接管3外壁的峰值应力高达566.6Mpa,大于该材料的抗拉强度530MPa。对于小直径的高压氮气缓冲罐,其罐体1通常采用锻焊结构,两端采用球形封头2结构,大开孔通常采用嵌入式接管3的结构。因顶部接管3的整体结构小,所受载荷较大,根据上述结果可知,局部薄膜应力和峰值应力超过许用应力,无法满足法规的要求。为了改善该接管3的受力情况,当增加球形封头2的厚度至150mm时,此处局部应力校核无法通过。对直径小于800mm的高压氮气缓冲罐的球形封头,当球形封头厚度大于80mm时,球形封头热成型也很难实施。技术实现要素:本发明的主要目的在于提供一种缓冲罐,以解决现有技术中接管的局部应力过大的问题。为了实现上述目的,本发明提供了一种缓冲罐,包括:罐体,罐体具有第一内腔和与内腔连通的开口;一体成形的封头,封头设置在开口处以封堵开口,封头的朝向开口的一侧具有第二内腔,第二内腔与第一内腔连通,第二内腔呈弧面状。进一步地,第二内腔的纵向剖面的形状为半椭圆形。进一步地,封头为平底椭圆封头。进一步地,封头的外表面为一个圆柱面,封头的内表面为旋转体面,封头的内径和外径分别与罐体的内径和外径相同。进一步地,封头还具有与第二内腔连通的开孔。进一步地,缓冲罐还包括法兰盖,法兰盖设置在封头的远离第二内腔的一侧,法兰盖具有与开孔连通的通孔。进一步地,封头与罐体通过焊接连接。进一步地,法兰盖与封头通过螺栓连接。进一步地,第一内腔内径不大于800mm。应用本发明的技术方案,缓冲罐包括罐体和一体成形的封头,罐体具有第一内腔和与内腔连通的开口,封头设置在开口处以封堵开口,封头的朝向开口的一侧具有第二内腔,第二内腔与第一内腔连通,第二内腔呈弧面状,开孔直接开在封头的顶部中心。上述封头开孔结构为一体成形的,这样大大地改善了封头顶部管口处的受力状况,减少了采用球形封头结构中的球形封头和嵌入式接管的焊缝,有效地避免了高压缓冲罐中最容易出现焊缝缺陷导致容器的失效。附图说明构成本申请的一部分的说明书附图用来提供对本发明的进一步理解,本发明的示意性实施例及其说明用于解释本发明,并不构成对本发明的不当限定。在附图中:图1示出了现有技术的缓冲罐的实施例的结构示意图;图2示出了图1的缓冲罐的加载前的应力模型及网格划分图;图3示出了图1的缓冲罐的加载后的应力模型图;图4示出了图3的缓冲罐的加载后沿最大应力线性化路径的应力模型图;图5示出了根据本发明的缓冲罐的实施例的结构示意图;图6示出了图5的缓冲罐的加载前的应力模型及网格划分图;图7示出了图5的缓冲罐的加载后的应力模型图;以及图8示出了图5的缓冲罐的加载后沿最大应力线性化路径的应力模型图。其中,上述附图包括以下附图标记:1、罐体;2、球形封头;3、接管;4、法兰盖;10、罐体;11、第一内腔;20、封头;21、第二内腔;22、开孔;30、法兰盖;31、通孔。具体实施方式需要说明的是,在不冲突的情况下,本申请中的实施例及实施例中的特征可以相互组合。下面将参考附图并结合实施例来详细说明本发明。为解决此问题,我们发明高压氮气缓冲罐锻件制平底椭圆封头管口结构,大大降低接管与罐体处的局部应力,满足了材料许用应力的要求。如图5所示,本实施例的缓冲罐包括罐体10和一体成形的封头20,罐体10具有第一内腔11和与内腔连通的开口,封头20设置在开口处以封堵开口,封头20的朝向开口的一侧具有第二内腔21,第二内腔21与第一内腔11连通,第二内腔21呈弧面状。其中,一体成形的封头20的含义是指将将现有技术中的封头和接管是一体结构的,并不是分体结构的。应用本实施例的缓冲罐,缓冲罐包括罐体10和一体成形的封头20,罐体10具有第一内腔11和与内腔连通的开口,封头20设置在开口处以封堵开口,封头20的朝向开口的一侧具有第二内腔21,第二内腔21与第一内腔11连通,第二内腔21呈弧面状。上述封头20的结构为一体成形的,这样大大地改善了封头20顶部管口处的受力状况,减少了球形封头和嵌入式接管的焊缝,有效地避免了高压缓冲罐中最容易出现焊缝缺陷导致容器的失效问题。相对于设备材料成本、锻件的制造难度等,确保高压氮气缓冲罐的本质安全是至关重要的,尤其是设计结构中的容器强度必须满足材料许用应力和法规的要求。现有技术中,球形封头与嵌入式接管的焊接接管不可避免存在一定的质量缺陷,从而诱发容器局部失效的风险。而本实施例的封头管口结构减少了现有技术中的接管和球形封头的焊接,有效地减少了容器局部失效的风险。在本实施例中,第二内腔21的纵向剖面的形状为半椭圆形(长短轴之比为2:1),优选封头20为平底椭圆封头,采用锻件制平底椭圆封头管口结构代替了现有的球形封头和嵌入式接管结构。对于直径不大于800mm缓冲罐采用本实施例的封头,封头的材料成本比现有技术中的球形封头结构虽略有上升,但是降低了封头的制造难度。由于应用本实施例的封头减少了球形封头压制前后、接管焊接的多次热处理,也减少接管和球形封头的焊接和无损检测工作量等,综合成本略有降低。在本实施例中,封头20的外表面为一个圆柱面,封头20的内表面为旋转体面,封头20的内径和外径分别与罐体10的内径和外径相同。本实施例的缓冲罐将平底椭圆封头制成一个整体锻件,利用ANSYS软件将平底椭圆封头所建的加载前的应力模型如图6所示,加载表1所列荷载后的应力模型如图7所示。从图7可以看出,封头20的管口处受力状况大大地改善了,尤其是封头20的管口的根部处所受最大应力不大于72.5MPa,远远小于材料的许用应力220MPa。从图7也可以看出,本实施例的封头20的结构的受力最大点落在封头20过渡区的内壁,沿该点垂直于内壁做线性化,沿最大点MX到外壁的P1路径应力模型如图8所示,线性化计算结果如下所示:按JB4732《钢制压力容器—分析设计标准》应力评定规则,根据上述的结果可以得出局部薄膜力为118.1MPa,远远小于材料的许用应力强度评定值330MPa(1.5×220MPa),而且封头20的内壁的峰值应力也只有325.3MPa,远比该材料的抗拉强度530MPa小。因此,本实施例的缓冲罐采用平底椭圆封头的结构,大大地改善了封头20顶部管口处的受力状况,减少了采用球形封头结构中的球形封头和嵌入式接管的焊缝,有效地避免高压缓冲罐中最容易出现此处焊缝缺陷导致容器的失效。在本实施例中,封头20还具有与第二内腔21连通的开孔22。开孔22一方面可以用于通气的;另一方便可以用于操作者通过开孔22伸入至缓冲罐中清理缓冲罐,方便清理异物等。在本实施例中,缓冲罐还包括法兰盖30,法兰盖30设置在封头20的远离第二内腔21的一侧,法兰盖30具有与开孔22连通的通孔31。通孔31主要用于通气的。在本实施例中,封头20与罐体10通过焊接连接。焊接连接具有连接强度高、操作简便等特点。在本实施例中,法兰盖30与封头20通过螺栓连接。螺栓连接具有结构简单、便于维修、操作省力、成本低等特点。本实施例的缓冲罐采用锻件制平底椭圆封头管口结构代替了现有技术中的球形封头和嵌入式接管的结构,其优点如下:1、优化了高压氮气缓冲罐的封头的结构形式,大大改善封头的管口受力状况。2、大大降低封头的管口的根部的峰值应力,减少结构的不连续性,增加设备的耐疲劳性能。3、改变了封头的制造方法,降低了封头的制造难度,有效地避免了球形封头易发生质量缺陷的情况。高压氮气缓冲罐若采用球形封头,需采用圆形锻饼经冲压成型,由于球形封头的直径小,壁厚大(至少45mm以上),材料强度高(20MnMoD)加工难度大,易产生裂纹等缺陷。而本实施例的锻件制平底椭圆封头采用整体锻件机加工成型,降低了因封头制造缺陷导致的设备质量事故的风险;4、锻件制平底椭圆封头的管口结构采用整体锻件,减少了球形封和嵌入式接管的焊缝,减少了焊缝无损检测成本,避免了由于焊缝质量缺陷而导致容器失效风险。5、减少平底椭圆封头的顶部结构热处理的次数,提高了材料的机械性能,减少了封头冲压、焊接等残余应力,降低了热处理成本。由于热处理后将会降低材料的机械性能,若采用球形封头和嵌入式接管的结构不可避免地需要多次热处理,并且还存在一定的残余应力。而采用本实施例的锻件制平底椭圆封头管口结构只需整体热处理,减少了封头热处理次数,提高封头顶部结构整体性能。以上所述仅为本发明的优选实施例而已,并不用于限制本发明,对于本领域的技术人员来说,本发明可以有各种更改和变化。凡在本发明的精神和原则之内,所作的任何修改、等同替换、改进等,均应包含在本发明的保护范围之内。当前第1页1 2 3