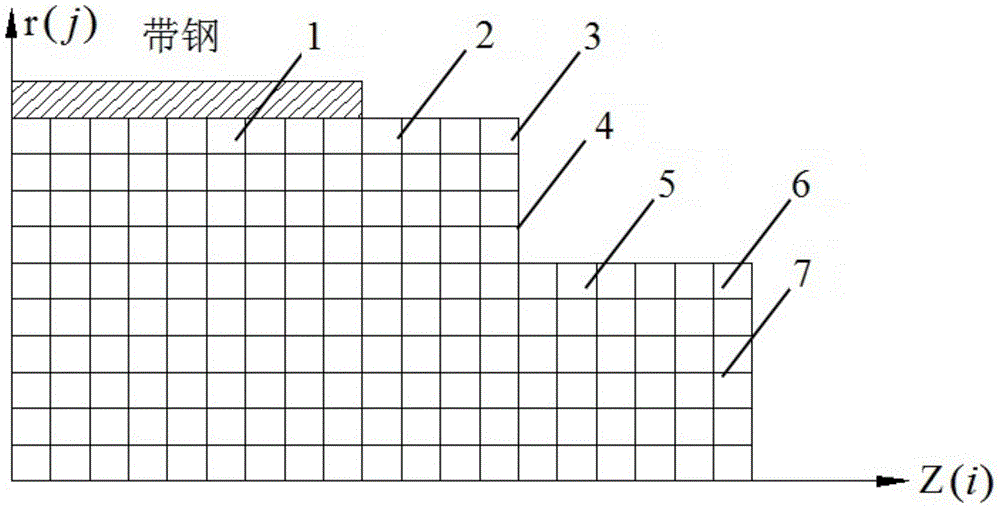
本发明涉及连续退火设备的温度预测方法,更具体地说,涉及连退机组炉子段炉辊温度场与热辊型的预测方法。
背景技术:
:在冷轧生产流程中,CAPL逐渐成为冷轧生产组织的重要部位,而炉子段的设备稳定直接影响CAPL机组运行。目前,跑偏和热瓢曲是影响连退机组高速稳定通板两大难题,而减少跑偏和热瓢曲的发生率需要根据炉子段炉辊辊型和退火温度,对张力设定进行严格控制,一般情况下,退火温度随钢种而给定。因此,炉子段内炉辊的温度场分布及其热辊型成为制约CAPL机组高速稳定运行的重要因素。在以往的实际生产过程中,设备厂家给定的设定张力值太大,极易引起带钢的热瓢曲,需要现场技术人员对各工艺段的张力设定值重新调整。但是,对特定钢种的退火温度给定的情况下,技术人员没有一种方法或仪器对炉辊的热辊型进行测量,也往往忽略炉辊热辊型对稳定通板的影响,对不同工艺段的张力设定值只能在厂家给定的基础上从大到小不断调整,但当带钢的钢种和规格发生变化时,退火温度也相应改变,对张力又要重复相同的调整。这一过程存在很多缺点:(1)耗费时间长,需要在生产中不断改进、调整;(2)盲目调试后的结果不够准确,张力值过大或过小,引发带钢的热瓢曲或跑偏,制约带钢的稳定通板性;(3)降低了生产效率。技术实现要素:针对现有技术中存在的各种问题,本发明的目的是提供连退机组炉子 段炉辊温度场与热辊型的预测方法。为实现上述目的,本发明采用如下技术方案:一种连退机组炉子段炉辊温度场与热辊型的预测方法,其特征在于,包括以下步骤:步骤a,手机机组关键设备与工艺参数;步骤b,定义相关参数;步骤c,对炉辊进行温度网格划分;步骤d,相关参数赋初值;步骤e,设定导热时间参数;步骤f,计算炉辊辊身与带钢接触部位的表面温度分布;步骤g,计算炉辊辊身与炉内气体接触部分的表面温度分布;步骤h,计算炉辊辊身与辊肩连接点的表面温度分布;步骤i,计算炉辊辊肩部分的表面温度分布;步骤j,计算炉辊辊颈部分的表面温度分布;步骤k,计算炉辊辊颈与辊端连接点部分的表面温度分布步骤l,计算辊端部分的表面温度分布;步骤m,计算炉辊内部温度场网格单元的温度分布;步骤n,对温度收敛精度进行判断;步骤o,计算炉辊辊身部分热凸度;步骤p,输出炉辊温度场分布及原始辊型与热凸度叠加后的热辊型。根据本发明的一实施例,步骤a的参数包括:炉辊辊形参数,主要包括:炉辊最大辊径D1、炉辊辊身长度L1、炉辊凸台区长度S、炉辊凸度δ、辊颈直径D2、辊颈长度L2;工艺参数,主要包括:带钢宽度B、带钢温度TA、工艺段的设定温度TB、轴承温度TC、室温TD。步骤b的相关参数包括:i,j—温度场网格单元坐标、αA—炉辊与带钢热交换系数、αB—炉辊与炉内气体热交换系数、αC—炉辊与轴承热交换系数、αD—炉辊与室内空气热交换系数、ρ—炉辊密度、Cp—炉辊比热、k—炉辊导热系数、β—炉辊热膨胀系数、υ—泊松比、ri,j—坐标为(i,j)的单元格距轴线距离、Δr—单元格径向长度、Δz—单元格轴向长度、Δt—时间搜索步长、Ti,j—坐标为(i,j)的单元格换热前温度、T′i,j—坐标为(i,j)的单元格换热后温度、λ—时间调整参数、t—导热时间参数、ε—温度收敛精度、Δδi—炉辊横坐标i处的热凸度、Di—炉辊横坐标i处的热辊型;步骤c沿炉辊轴线方向将辊身部分划分为M1段,辊颈部分分为M2段,带钢与炉辊接触部分为M0段,沿辊径方向将辊身部分分为N1段,辊颈部分分为N2段,其中:M0=B2Δz,M1=L12Δz,N1=D12Δr,M2=L22Δz,N2=D22Δr;]]>步骤d的相关参数初值为:令Ti,j=TD(i=0,1,2...M1+M2,j=0,1,2...N1)、坐标为(i,j)的单元格距轴线距离ri,j=|i-0.5|Δr、时间调整参数λ=0,给定时间搜索步长Δt,换热系数αA、αB、αC、αD,炉辊密度ρ、炉辊比热Cp、炉辊导热系数k、炉辊热膨胀系数β、泊松比υ、温度收敛精度ε;步骤e的导热时间参数t=λΔt,并令炉辊温度场网格坐标轴的边界温度T0,j=T1,j(j=1,…,N1),Ti,0=Ti,1(i=1,…,M1+M2)。根据本发明的一实施例,步骤f的计算方法为:T′i,j(i=1,2...M0,j=N1);Ti,j′=Δtρ(ri,jΔrΔz)Cp[αAΔz(ri,j+Δr2)(TA-Ti,j)+kΔz(ri,j-Δr2)(Ti,j-1-Ti,jΔr)]+Δtρ(ri,jΔrΔz)Cp[k(ri,j·Δr)(Ti-1,j-Ti,jΔz)+k(ri,j·Δr)(Ti+1,j-Ti,jΔz)]+Ti,j.]]>根据本发明的一实施例,步骤g的计算方法为:T′i,j(i=M0+1,…,M1-1,j=N1);Ti,j′=Δtρ(ri,jΔrΔz)Cp[αBΔz(ri,j+Δr2)(TB-Ti,j)+kΔz(ri,j-Δr2)(Ti,j-1-Ti,jΔr)]+Δtρ(ri,jΔrΔz)Cp[k(ri,j·Δr)(Ti-1,j-Ti,jΔz)+k(ri,j·Δr)(Ti+1,j-Ti,jΔz)]+Ti,j.]]>根据本发明的一实施例,步骤h的计算方法为:T′i,j(i=M1,j=N1);Ti,j′=Δtρ(ri,jΔrΔz)Cp[αBΔz(ri,j+Δr2)(TB-Ti,j)+kΔz(ri,j-Δr2)(Ti,j-1-Ti,jΔr)]+Δtρ(ri,jΔrΔz)Cp[k(ri,j·Δr)(Ti-1,j-Ti,jΔz)+αB(ri,j·Δr)(TB-Ti,j)]+Ti,j.]]>根据本发明的一实施例,步骤i的计算方法为:T′i,j(i=M1,j=N2+1,…,N1-1);Ti,j′=Δtρ(ri,jΔrΔz)Cp[kΔz(ri,j+Δr2)(Ti,j+1-Ti,jΔr)+kΔz(ri,j-Δr2)(Ti,j-1-Ti,jΔr)]+Δtρ(ri,jΔrΔz)Cp[k(ri,j·Δr)(Ti-1,j-Ti,jΔz)+αB(ri,j·Δr)(TB-Ti,j)]+Ti,j.]]>根据本发明的一实施例,步骤j的计算方法为:T′i,j(i=M1+1,…,M1+M2-1,j=N2);Ti,j′=Δtρ(ri,jΔrΔz)Cp[αCΔz(ri,j+Δr2)(TB-Ti,j)+kΔz(ri,j-Δr2)(Ti,j-1-Ti,jΔr)]+Δtρ(ri,jΔrΔz)Cp[k(ri,j·Δr)(Ti-1,j-Ti,jΔz)+k(ri,j·Δr)(Ti+1,j-Ti,jΔz)]+Ti,j.]]>根据本发明的一实施例,步骤k的计算方法为:T′i,j(i=M1+M2,j=N2);Ti,j′=Δtρ(ri,jΔrΔz)Cp[αCΔz(ri,j+Δr2)(TC-Ti,j)+kΔz(ri,j-Δr2)(Ti,j-1-Ti,jΔr)]+Δtρ(ri,jΔrΔz)Cp[k(ri,j·Δr)(Ti-1,j-Ti,jΔz)+αD(ri,j·Δr)(TD-Ti,j)]+Ti,j.]]>根据本发明的一实施例,步骤l的计算方法为:T′i,j(i=M1+M2,j=1,…,N2-1);Ti,j′=Δtρ(ri,jΔrΔz)Cp[kΔz(ri,j+Δr2)(Ti,j+1-Ti,jΔr)+kΔz(ri,j-Δr2)(Ti,j-1-Ti,jΔr)]+Δtρ(ri,jΔrΔz)Cp[k(ri,j·Δr)(Ti-1,j-Ti,jΔz)+αD(ri,j·Δr)(TD-Ti,j)]+Ti,j.]]>根据本发明的一实施例,步骤m的炉辊内部温度场网格单元的温度分布T′i,j,主要包括三个部分:辊身内部温度场网格(i=1,…,M1-1,j=1,…,N1-1);辊身与辊颈连接处温度场网格(i=M1,j=1,…,N2);辊颈内部温度场网格(i=M1+1,…,M1+M2-1,j=1,…,N2-1);Ti,j′=Δtρ(ri,jΔrΔz)Cp[kΔz(ri,j+Δr2)(Ti,j+1-Ti,jΔr)+kΔz(ri,j-Δr2)(Ti,j-1-Ti,jΔr)]+Δtρ(ri,jΔrΔz)Cp[k(ri,j·Δr)(Ti-1,j-Ti,jΔz)+k(ri,j·Δr)(Ti+1,j-Ti,jΔz)]+Ti,j.]]>步骤n判断T′1,1-T1,1<ε是否成立?若不等式成立,转入步骤o;若不等式不成立,令Ti,j=T′i,j,λ=λ+1,转入步骤e;步骤o计算炉辊辊身部分热凸度步骤p输出炉辊温度场分布T′i,j及原始辊型与热凸度叠加后的热辊型Di。在上述技术方案中,本发明的连退机组炉子段炉辊温度场与热辊型的预测方法适合于连退机组炉子段炉辊温度场与热辊型的预测方法,根据炉辊相关传热学参数及辊型参数,在已知工艺段设定温度及带钢温度的条件下,即可求得炉辊的温度场分布及热辊型,为机组的高速稳定运行起到指导作用。附图说明图1是炉辊辊身部分原始辊型图;图2是温度场网格图;图3是本发明的流程图;图4是炉辊热凸度曲线图;图5是炉辊辊身温度场示意图;图6是炉辊原始辊型及热辊型曲线示意图。具体实施方式下面结合附图和实施例进一步说明本发明的技术方案。如图1和图2所示,根据相关传热学原理,本发明首先通过对炉辊进行温度场网格划分,并从能量平衡角度出发建立圆柱体温度场的差分方程,并利用C++等程序语言实现,进而实现了连退过程中炉辊的温度场分布及相应的热辊型的直观体现。图2中各个数字所代表的含义如下所示:(1)辊身与带钢接触部分(2)辊身与炉内气体接触部分(3)辊身与辊肩连接点部分(4)辊肩部分(5)辊颈部分(6)辊颈与辊端连接点部分(7)辊端部分在连退过程中,机组内炉辊受带材热传导接触作用,当带钢经过上一工艺段退火处理后,到达此工艺段时:若带钢温度高于此工艺段炉辊温度,则炉辊其表层温度在短时间内迅速升高,在炉辊径向,热流从外层向中心传导,在炉辊轴向,热流从中部向两端传导;若带钢温度低于此工艺段炉辊温度,则炉辊其表层温度在短时间内迅速降低,在炉辊径向,热流从中心向外层传导,在炉辊轴向,热流从两端向中部传导。刚投入使用时(换新辊或停机较长时间),炉辊是冷的,炉辊温度可认为与室温相同;机组 开机以后,各工艺段内温度逐渐增高,并最终达到退火工艺要求的温度值。当生产一段时间后,炉辊温度达到一个稳态平均值,得到所求温度场分布;并进一步根据炉辊的热膨胀系数,沿炉辊径向对热膨胀后的网格进行叠加,最终可得到炉辊膨胀后的热辊型。在连退机组中,炉辊的转速较大,每分钟可达几百米以上,因此炉辊的圆周方向温度波动较小。并且,考虑炉辊的回转周期与热凸度对退火温度变化的响应时间相比为二阶小,因此可以忽略炉辊圆周方向接触条件的变化对温度场的影响;另外,由于炉辊的轴对称性,可取炉辊四分之一建立炉辊轴对称温度场网格图,如图2所示。如图3所示,为了实现上述发明目的,本发明采用以下技术方案,包括以下由计算机执行的步骤(a)收集机组的关键设备与工艺参数,主要包括以下步骤:(a1)收集炉辊辊形参数,主要包括:炉辊最大辊径D1、炉辊辊身长度L1、炉辊凸台区长度S、炉辊凸度δ、辊颈直径D2、辊颈长度L2;(a2)收集工艺参数,主要包括:带钢宽度B、带钢温度TA、工艺段的设定温度TB、轴承温度TC、室温TD。(b)定义相关参数,包括:i,j—温度场网格单元坐标、αA—炉辊与带钢热交换系数、αB—炉辊与炉内气体热交换系数、αC—炉辊与轴承热交换系数、αD—炉辊与室内空气热交换系数、ρ—炉辊密度、Cp—炉辊比热、k—炉辊导热系数、β—炉辊热膨胀系数、υ—泊松比、ri,j—坐标为(i,j)的单元格距轴线距离、Δr—单元格径向长度、Δz—单元格轴向长度、Δt—时间搜索步长、Ti,j—坐标为(i,j)的单元格换热前温度、T′i,j—坐标为(i,j)的单元格换热后温度、λ—时间调整参数、t—导热时间参数、ε—温度收敛精度、Δδi—炉辊横坐标i处的热凸度、Di—炉辊横坐标i处的热辊型。(c)对炉辊进行温度网格划分,沿炉辊轴线方向将辊身部分划分为M1段,辊颈部分分为M2段,带钢与炉辊接触部分为M0段,沿辊径方向将辊 身部分分为N1段,辊颈部分分为N2段,其中:M0=B2Δz,M1=L12Δz,N1=D12Δr,]]>M2=L22Δz,N2=D22Δr;]]>(d)相关参数赋初值:炉辊进行换热前,可以认为炉辊温度场分布均与室温相同,即令Ti,j=TD(i=0,1,2...M1+M2,j=0,1,2...N1)、坐标为(i,j)的单元格距轴线距离ri,j=|i-0.5|Δr、时间调整参数λ=0,给定时间搜索步长Δt,换热系数αA、αB、αC、αD,炉辊密度ρ、炉辊比热Cp、炉辊导热系数k、炉辊热膨胀系数β、泊松比υ、温度收敛精度ε;(e)令导热时间参数t=λΔt,并令炉辊温度场网格坐标轴的边界温度T0,j=T1,j(j=1,…,N1),Ti,0=Ti,1(i=1,…,M1+M2);(f)根据炉辊辊身与带钢接触部位的边界条件,炉辊与带钢进行接触换热,由牛顿冷却定律及能量守恒原理,计算这一部位的表面温度分布T′i,j(i=1,2...M0,j=N1);Ti,j′=Δtρ(ri,jΔrΔz)Cp[αAΔz(ri,j+Δr2)(TA-Ti,j)+kΔz(ri,j-Δr2)(Ti,j-1-Ti,jΔr)]+Δtρ(ri,jΔrΔz)Cp[k(ri,j·Δr)(Ti-1,j-Ti,jΔz)+k(ri,j·Δr)(Ti+1,j-Ti,jΔz)]+Ti,j.]]>(g)根据炉辊辊身与炉内气体接触部分的边界条件,炉辊与炉内气体进行对流换热,由牛顿冷却定律及能量守恒原理,计算这一部位的表面温度分布T′i,j(i=M0+1,…,M1-1,j=N1);Ti,j′=Δtρ(ri,jΔrΔz)Cp[αBΔz(ri,j+Δr2)(TB-Ti,j)+kΔz(ri,j-Δr2)(Ti,j-1-Ti,jΔr)]+Δtρ(ri,jΔrΔz)Cp[k(ri,j·Δr)(Ti-1,j-Ti,jΔz)+k(ri,j·Δr)(Ti+1,j-Ti,jΔz)]+Ti,j.]]>(h)根据炉辊辊身与辊肩连接点所处环境,可将炉辊与炉内气体进行对流换热作为边界条件,由牛顿冷却定律及能量守恒原理,计算这一部位的表面温度分布T′i,j(i=M1,j=N1);Ti,j′=Δtρ(ri,jΔrΔz)Cp[αBΔz(ri,j+Δr2)(TB-Ti,j)+kΔz(ri,j-Δr2)(Ti,j-1-Ti,jΔr)]+Δtρ(ri,jΔrΔz)Cp[k(ri,j·Δr)(Ti-1,j-Ti,jΔz)+αB(ri,j·Δr)(TB-Ti,j)]+Ti,j.]]>(i)根据炉辊辊肩部分所处环境,可将炉辊与炉内气体进行对流换热作为边界条件,由牛顿冷却定律及能量守恒原理,计算这一部位的表面温度分布T′i,j(i=M1,j=N2+1,…,N1-1);Ti,j′=Δtρ(ri,jΔrΔz)Cp[kΔz(ri,j+Δr2)(Ti,j+1-Ti,jΔr)+kΔz(ri,j-Δr2)(Ti,j-1-Ti,jΔr)]+Δtρ(ri,jΔrΔz)Cp[k(ri,j·Δr)(Ti-1,j-Ti,jΔz)+αB(ri,j·Δr)(TB-Ti,j)]+Ti,j.]]>(j)根据炉辊辊颈部分的边界条件,辊颈与轴承进行接触换热,由牛顿冷却定律及能量守恒原理,计算这一部位的表面温度分布T′i,j(i=M1+1,…,M1+M2-1,j=N2);Ti,j′=Δtρ(ri,jΔrΔz)Cp[αCΔz(ri,j+Δr2)(TB-Ti,j)+kΔz(ri,j-Δr2)(Ti,j-1-Ti,jΔr)]+Δtρ(ri,jΔrΔz)Cp[k(ri,j·Δr)(Ti-1,j-Ti,jΔz)+k(ri,j·Δr)(Ti+1,j-Ti,jΔz)]+Ti,j.]]>(k)根据炉辊辊颈与辊端连接点部分的边界条件,可按炉辊与轴承及室内空气进行对流换热处理,由牛顿冷却定律及能量守恒原理,计算这一部位的表面温度分布T′i,j(i=M1+M2,j=N2);Ti,j′=Δtρ(ri,jΔrΔz)Cp[αCΔz(ri,j+Δr2)(TC-Ti,j)+kΔz(ri,j-Δr2)(Ti,j-1-Ti,jΔr)]+Δtρ(ri,jΔrΔz)Cp[k(ri,j·Δr)(Ti-1,j-Ti,jΔz)+αD(ri,j·Δr)(TD-Ti,j)]+Ti,j.]]>(l)在实际生产中,辊端部分的温度分布受轴承温度及室温的影响,考虑到辊端位置距离辊身较远,对辊身处的温度场分布及热辊型影响不大,故可以将与室内空气对流换热作为边界条件,由此,可计算这一部位的表面温度分布T′i,j(i=M1+M2,j=1,…,N2-1);Ti,j′=Δtρ(ri,jΔrΔz)Cp[kΔz(ri,j+Δr2)(Ti,j+1-Ti,jΔr)+kΔz(ri,j-Δr2)(Ti,j-1-Ti,jΔr)]+Δtρ(ri,jΔrΔz)Cp[k(ri,j·Δr)(Ti-1,j-Ti,jΔz)+αD(ri,j·Δr)(TD-Ti,j)]+Ti,j.]]>(m)在炉辊内部,炉辊温度场网格单元之间的热流传导属于内部节点之间的传导,根据能量守恒原理,可计算炉辊内部温度场网格单元的温度分布T′i,j,主要包括三个部分:辊身内部温度场网格(i=1,…,M1-1,j=1,…,N1-1),辊身与辊颈连接处温度场网格(i=M1,j=1,…,N2),辊颈内部温度场网格(i=M1+1,…,M1+M2-1,j=1,…,N2-1);Ti,j′=Δtρ(ri,jΔrΔz)Cp[kΔz(ri,j+Δr2)(Ti,j+1-Ti,jΔr)+kΔz(ri,j-Δr2)(Ti,j-1-Ti,jΔr)]+Δtρ(ri,jΔrΔz)Cp[k(ri,j·Δr)(Ti-1,j-Ti,jΔz)+k(ri,j·Δr)(Ti+1,j-Ti,jΔz)]+Ti,j.]]>(n)判断T′i,1-T1,1<ε是否成立?若不等式成立,转入步骤(o);若不等式不成立,令Ti,j=T′i,j,λ=λ+1,转入步骤(e);(o)计算炉辊辊身部分热凸度如图4所示;(p)输出炉辊温度场分布T′i,j及原始辊型与热凸度叠加后的热辊型Di,如图5和图6所示。实施例下面通过一个具体的实施例,配合以具体的参数来进一步详细地说明上述技术方案。(1)收集机组的关键设备与工艺参数,主要包括以下步骤:(a1)收集预热段炉辊辊形参数,主要包括:炉辊最大辊径D1=900mm、炉辊辊身长度L1=1950mm、炉辊凸台区长度S=250mm、炉辊凸度δ=3mm、辊颈直径D2=150mm、辊颈长度L2=145mm;(a2)收集预热段工艺参数,主要包括:带钢宽度B=1020mm、带钢温度TA=120℃、工艺段的设定温度TB=150℃、轴承温度TC=50℃、室温TD=25℃。(2)定义相关参数,包括:i,j—温度场网格单元坐标、αA—炉辊与带钢热交换系数、αB—炉辊与炉内气体热交换系数、αC—炉辊与轴承热交换系数、αD—炉辊与室内空气热交换系数、ρ—炉辊密度、Cp—炉辊比热、k—炉辊导热系数、β—炉辊热膨胀系数、υ—泊松比、ri,j—坐标为(i,j)的单元格距轴线距离、Δr—单元格径向长度、Δz—单元格轴向长度、Δt—时间搜索步长、Ti,j—坐标为(i,j)的单元格换热前温度、T′i,j—坐标为(i,j)的单元格换热后温度、λ—时间调整参数、t—导热时间参数、ε—温度收敛精度、Δδi—炉辊横坐标i处的热凸度、Di—炉辊横坐标i处的热辊型。(3)对炉辊进行温度网格划分,沿炉辊轴线方向将辊身部分划分为M1段,辊颈部分分为M2段,带钢与炉辊接触部分为M0段,沿辊径方向将辊身部分分为N1段,辊颈部分分为N2段,其中:M0=11、M1=20、N1=20、M2=3、N2=6;(4)相关参数赋初值:炉辊进行换热前,可以认为炉辊温度场分布均与室温相同,即令Ti,j=TD(i=0,1,2...M1+M2,j=0,1,2...N1)、坐标为(i,j)的单元格距轴线距离ri,j=|i-0.5|Δr、时间调整参数λ=0,给定时间搜索步长Δt=5s,换热系数αA=2500W/m2·℃、αB=50W/m2·℃、αC=2500W/m2·℃、αD=50W/m2·℃,炉辊密度ρ=7800kg/m3、炉辊比热Cp=460J/kg·℃、炉辊导热系数k=29W/m·℃、炉辊热膨胀系数β=12×10-6/℃、泊松比υ=0.3、温度收敛精度ε=0.1℃;(5)令导热时间参数t=λΔt,并令炉辊温度场网格坐标轴的边界温度T0,j=T1,j(j=1,…,N1),Ti,0=Ti,1(i=1,…,M1+M2);(6)根据炉辊辊身与带钢接触部位的边界条件,炉辊与带钢进行接触换热,由牛顿冷却定律及能量守恒原理,计算这一部位的表面温度分布T′i,j(i=1,2...M0,j=N1);Ti,j′=Δtρ(ri,jΔrΔz)Cp[αAΔz(ri,j+Δr2)(TA-Ti,j)+kΔz(ri,j-Δr2)(Ti,j-1-Ti,jΔr)]+Δtρ(ri,jΔrΔz)Cp[k(ri,j·Δr)(Ti-1,j-Ti,jΔz)+k(ri,j·Δr)(Ti+1,j-Ti,jΔz)]+Ti,j.]]>(7)根据炉辊辊身与炉内气体接触部分的边界条件,炉辊与炉内气体进行对流换热,由牛顿冷却定律及能量守恒原理,计算这一部位的表面温度分布T′i,j(i=M0+1,…,M1-1,j=N1);Ti,j′=Δtρ(ri,jΔrΔz)Cp[αBΔz(ri,j+Δr2)(TB-Ti,j)+kΔz(ri,j-Δr2)(Ti,j-1-Ti,jΔr)]+Δtρ(ri,jΔrΔz)Cp[k(ri,j·Δr)(Ti-1,j-Ti,jΔz)+k(ri,j·Δr)(Ti+1,j-Ti,jΔz)]+Ti,j.]]>(8)根据炉辊辊身与辊肩连接点所处环境,可将炉辊与炉内气体进行对流换热作为边界条件,由牛顿冷却定律及能量守恒原理,计算这一部位的表面温度分布T′i,j(i=M1,j=N1);Ti,j′=Δtρ(ri,jΔrΔz)Cp[αBΔz(ri,j+Δr2)(TB-Ti,j)+kΔz(ri,j-Δr2)(Ti,j-1-Ti,jΔr)]+Δtρ(ri,jΔrΔz)Cp[k(ri,j·Δr)(Ti-1,j-Ti,jΔz)+αB(ri,j·Δr)(TB-Ti,j)]+Ti,j.]]>(9)根据炉辊辊肩部分所处环境,可将炉辊与炉内气体进行对流换热作为边界条件,由牛顿冷却定律及能量守恒原理,计算这一部位的表面温度分布T′i,j(i=M1,j=N2+1,…,N1-1);Ti,j′=Δtρ(ri,jΔrΔz)Cp[kΔz(ri,j+Δr2)(Ti,j+1-Ti,jΔr)+kΔz(ri,j-Δr2)(Ti,j-1-Ti,jΔr)]+Δtρ(ri,jΔrΔz)Cp[k(ri,j·Δr)(Ti-1,j-Ti,jΔz)+αB(ri,j·Δr)(TB-Ti,j)]+Ti,j.]]>(10)根据炉辊辊颈部分的边界条件,辊颈与轴承进行接触换热,由牛顿冷却定律及能量守恒原理,计算这一部位的表面温度分布T′i,j(i=M1+1,…,M1+M2-1,j=N2);Ti,j′=Δtρ(ri,jΔrΔz)Cp[αCΔz(ri,j+Δr2)(TB-Ti,j)+kΔz(ri,j-Δr2)(Ti,j-1-Ti,jΔr)]+Δtρ(ri,jΔrΔz)Cp[k(ri,j·Δr)(Ti-1,j-Ti,jΔz)+k(ri,j·Δr)(Ti+1,j-Ti,jΔz)]+Ti,j.]]>(11)根据炉辊辊颈与辊端连接点部分的边界条件,可按炉辊与轴承及室内空气进行对流换热处理,由牛顿冷却定律及能量守恒原理,计算这一部位的表面温度分布T′i,j(i=M1+M2,j=N2);Ti,j′=Δtρ(ri,jΔrΔz)Cp[αCΔz(ri,j+Δr2)(TC-Ti,j)+kΔz(ri,j-Δr2)(Ti,j-1-Ti,jΔr)]+Δtρ(ri,jΔrΔz)Cp[k(ri,j·Δr)(Ti-1,j-Ti,jΔz)+αD(ri,j·Δr)(TD-Ti,j)]+Ti,j.]]>(12)在实际生产中,辊端部分的温度分布受轴承温度及室温的影响,考虑到辊端位置距离辊身较远,对辊身处的温度场分布及热辊型影响不大,故可以将与室内空气对流换热作为边界条件,由此,可计算这一部位的表面温度分布T′i,j(i=M1+M2,j=1,…,N2-1);Ti,j′=Δtρ(ri,jΔrΔz)Cp[kΔz(ri,j+Δr2)(Ti,j+1-Ti,jΔr)+kΔz(ri,j-Δr2)(Ti,j-1-Ti,jΔr)]+Δtρ(ri,jΔrΔz)Cp[k(ri,j·Δr)(Ti-1,j-Ti,jΔz)+αD(ri,j·Δr)(TD-Ti,j)]+Ti,j.]]>(13)在炉辊内部,炉辊温度场网格单元之间的热流传导属于内部节点之间的传导,根据能量守恒原理,可计算炉辊内部温度场网格单元的温度分布T′i,j,主要包括三个部分:辊身内部温度场网格(i=1,…,M1-1,j=1,…,N1-1),辊身与辊颈连接处温度场网格(i=M1,j=1,…,N2),辊颈内部温度场网格(i=M1+1,…,M1+M2-1,j=1,…,N2-1);Ti,j′=Δtρ(ri,jΔrΔz)Cp[kΔz(ri,j+Δr2)(Ti,j+1-Ti,jΔr)+kΔz(ri,j-Δr2)(Ti,j-1-Ti,jΔr)]+Δtρ(ri,jΔrΔz)Cp[k(ri,j·Δr)(Ti-1,j-Ti,jΔz)+k(ri,j·Δr)(Ti+1,j-Ti,jΔz)]+Ti,j.]]>(14)判断T′1,1-T1,1<ε是否成立?若不等式成立,转入步骤(15);若 不等式不成立,令Ti,j=T′i,j,λ=λ+1,转入步骤(5);(15)计算炉辊辊身部分热凸度如图4所示。本发明与现有技术相比更加简单、便捷。根据本发明,能够很容易的求出各种原始辊型的炉辊在任意工况下的热辊型,其有益效果主要体现在:(1)直观的给出了炉辊的实际辊型曲线,对为了防止跑偏和热瓢曲所需进行的张力调整起到了指导作用。(2)当钢种发生变化时,退火温度也会改变,炉辊热辊型也会随之改变,技术人员可以根据热辊型的改变量,有根据的对张力进行一定量的调整,避免了盲目性。(3)能够比较准确、快速的制定不同钢种、规格带钢在不同工艺段的张力表。根据此技术,带钢由于跑偏和瓢曲发生断带的事故率降低了百分之五十以上,有效地保证了带钢的稳定通板性,提高了生产效率。本
技术领域:
中的普通技术人员应当认识到,以上的实施例仅是用来说明本发明,而并非用作为对本发明的限定,只要在本发明的实质精神范围内,对以上所述实施例的变化、变型都将落在本发明的权利要求书范围内。当前第1页1 2 3