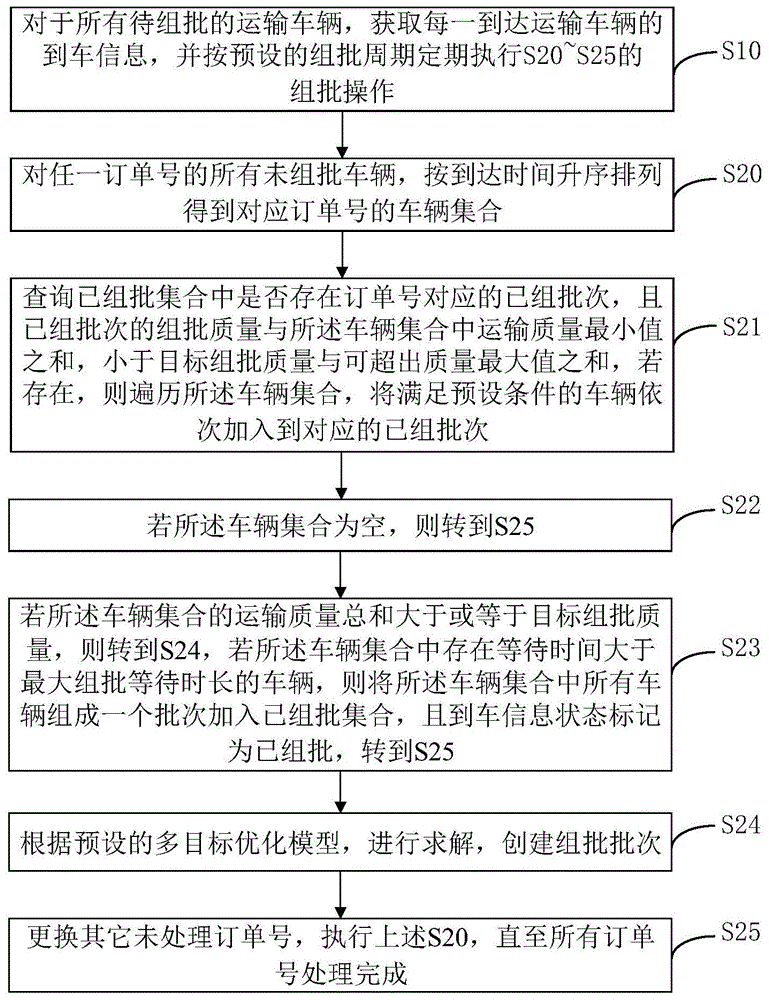
本发明属于信息
技术领域:
,具体涉及一种基于多目标优化的钢铁企业汽车取样组批方法。
背景技术:
:钢铁生产需要多种原燃料,如铁矿粉、铁合金、燃料和各种辅料等,这些原燃料的质量不仅是制定冶炼生产工艺参数的重要依据,也决定了物料的结算价格。钢铁企业在购入原燃料时,会对进厂的物流车辆进行组批取样,对取样过程有严格的规范。组批的目的是得到一个合理的能代表整体质量的样本。钢铁企业在生产中,往往是根据规范指定的批次重量,取得一定公斤数量的样本,根据化验结果对物料进行结算。采用汽车运输的物料在进厂前,需要在停车场等待组批,组批成功后,即可进厂进行称重、取样等动作。目前国内钢铁企业在对外购物资的车辆的组批调度上,普遍依靠调度人员凭借经验进行组批,存在批次组织不科学导致化验成本高和“人情批”等不规范的操作,影响企业用料成本。技术实现要素:本发明的目的在于提供一种基于多目标优化的钢铁企业汽车取样组批方法,实现物料组批质量最优化的同时,减少组批车辆的等待时长。本发明解决其技术问题所采用的技术方案为:一种基于多目标优化的钢铁企业汽车取样组批方法,包括以下步骤:s10、对于所有待组批的运输车辆,获取每一到达运输车辆的到车信息,并按预设的组批周期定期执行组批操作,所述到车信息包括车牌号、订单号、运输质量及到车时间;所述组批操作包括:s20、对任一订单号的所有未组批车辆,按到达时间升序排列,得到对应订单号的车辆集合;s21、查询已组批集合中是否存在所述订单号对应的已组批次,且已组批次的组批质量与所述车辆集合中运输质量最小值之和,小于目标组批质量与可超出质量最大值之和,若存在,则遍历所述车辆集合,将满足预设条件的车辆依次加入到对应的已组批次,并从所述车辆集合中删除,且到车信息状态标记为已组批,所述预设条件为,将未组批车辆加入到已组批次中,新的已组批次的组批质量,小于目标组批质量与可超出质量最大值之和;s22、若所述车辆集合为空,则转到s25;s23、若所述车辆集合的运输质量总和大于或等于目标组批质量,则转到s24,若所述车辆集合中存在等待时间大于最大组批等待时长的车辆,则将所述车辆集合中所有车辆组成一个批次加入已组批集合,且到车信息状态标记为已组批,转到s25;s24、根据预设的多目标优化模型,进行求解,创建组批批次;s25、更换其它未处理订单号,执行上述s20,直至所有订单号处理完成。本发明产生的有益效果是:通过将满足预设条件的车辆依次加入到对应的已组批次,进一步实现已组批的优化,并根据多目标优化和最大组批等待时长的判断,进行综合组批,从而能够实现组批质量和组批车辆平均等待时间的双重优化。在节约检化验成本的同时,也兼顾了组批车辆司机的等待成本,实现双赢。附图说明下面将结合附图及实施方式对本发明作进一步说明,附图中:图1为本发明实施例提供的一种基于多目标优化的钢铁企业汽车取样组批方法流程图;图2为本发明实施例提供的一种基于多目标优化的钢铁企业汽车取样组批方法的组批操作流程图。具体实施方式为使本发明实施例的目的、技术方案和优点更加清楚,下面将结合本发明实施例中的附图,对本发明实施例中的技术方案进行清楚、完整地描述,显然,所描述的实施例是本发明一部分实施例,而不是全部的实施例。基于本发明中的实施例,本领域普通技术人员在没有作出创造性劳动前提下所获得的所有其他实施例,都属于本发明保护的范围。如图1所示,本发明实施例提供一种基于多目标优化的钢铁企业汽车取样组批方法,该方法包括:s10、对于所有待组批的运输车辆,获取每一到达运输车辆的到车信息,并按预设的组批周期定期执行组批操作,所述到车信息包括车牌号、订单号和运输质量。在s10中,对于所有待组批的运输车辆,首先需进行到车数据的收集,可通过设立的信息录入模块负责收集到车数据。例如,当运送物料的车辆进入停车场时,由料场门上管理人员通过信息录入模块录入该车的到车信息,到车信息包括:车辆的车牌号、运输物料所属的订单号及、运输物料的质量及车辆到达的时间等,还可包括物料的类型。除了到车数据收集以外,同时按预设的组批周期定期执行组批操作,如通过设立组批优化模块定期执行。组批优化操作执行过程的相关参数包括:组批周期t、组批的目标质量w、可超出质量最大值(组批重量允许超过目标吨位的最大值)δ及最大组批等待时长bwt,这些参数可组批优化模块中预设值。组批操作包括如下的步骤s20~s25:s20、对任一订单号的所有未组批车辆,按到达时间升序排列,得到对应订单号的车辆集合。在s20中,首先对信息录入模块中获得的到车信息按照订单号进行分组,原因是车辆取样要求运送物料的车辆必须属于同一订单。假设得到m个订单未组批,对任一订单号j的所有未组批车辆,对第j个订单中的未组批车辆按照到车时间升序排列,得到第j个订单的车辆集合vj,如令j=1,即从第一个订单号开始进行组批优化。s21、查询已组批集合中是否存在所述订单号对应的已组批次,且已组批次的组批质量与所述车辆集合中运输质量最小值之和,小于目标组批质量与可超出质量最大值之和,若存在,则遍历所述车辆集合,将满足预设条件的车辆依次加入到对应的已组批次,并从所述车辆集合中删除,且到车信息状态标记为已组批,所述预设条件为,将未组批车辆加入到已组批次中,新的已组批次的组批质量,小于目标组批质量与可超出质量最大值之和。在s21中,在已组批次集合g中搜索是否存在订单号与第j个订单的订单号相同,且已组批次的组批质量<w+δ-vj中车辆运输物料质量的最小值的组批。若存在组批g∈g满足该条件,则顺序遍历车辆集合vj,将满足检验条件(wk表示车辆k运输的物料的质量)的车辆依次加入到组批g,并从vj中删除,将组批的车辆的到车信息状态标记为已组批。s22、若所述车辆集合为空,则转到s25。s23、若所述车辆集合的运输质量总和大于或等于目标组批质量,则转到s24,若所述车辆集合中存在等待时间大于最大组批等待时长的车辆,则将所述车辆集合中所有车辆组成一个批次加入已组批集合,且到车信息状态标记为已组批,转到s25。在s23中,假设vj中剩余车辆数为n。令wi(i=1,2,…,n)表示第i台车运输的物料的重量,ati(i=1,2,…,n)表示车辆i的到达时间。若vj中车辆运输的物料的总重量≥w,则转到s24。否则,进一步判vj中是否存在车辆i的到达时间满足t-ati>bwt(t为当前时刻)。若存在,则将vj中的所有车辆组成一个新的批次加入到集合g,并修改这些车辆的到车信息状态为已组批,转到s25。s24、根据预设的多目标优化模型,进行求解,创建组批批次。在s24中,需要处理的是运输的物料的总质量大于目标组批质量w的情况。考虑到车辆集合的运输的物料的总质量会超过目标组批质量与可超出质量最大值之和,组批优化模块中预先设置有多目标优化模型,根据该多目标优化模型进行求解,从车辆集合中选出小于目标组批质量与可超出质量最大值之和的车辆,创建组批批次。s25、更换其它未处理订单号,执行上述s20,直至所有订单号处理完成。在s25中,将订单号更换为其它未执行组批操作的订单号,执行s20~s24的组批操作,直至所有订单号都遍历完成。如上述令j=1,即从第一个订单号开始进行组批优化,此步骤中,令j=j+1,若j>m则流程结束,否则转到s20。在上述实施例的基础上,作为一种可选实施例,所述多目标优化模型,包括:xi=0或1(i=1,2,...,n)其中,xi表示是否选中车辆i组批,wi为车辆i的运输质量,t为当前时刻,ati为车辆i的到达时刻,w为组批的目标质量,δ为可超出质量最大值,maxf1(x)表示最大化组批质量,maxf2(x)表示最大化车辆等待时长的平均值,及最大化车辆到达时刻与组批时刻的间隔的平均值。本发明实施例提供的一种基于多目标优化的钢铁企业汽车取样组批方法,根据预设的多目标优化模型,进行求解并创建组批批次。由于预设的多目标优化模型,一方面能够最大化组批质量,从而有利于实现组批批次的总质量最大;一方面能够最大化车辆等待时长的平均值,从而避免部分车辆等待时长过长。在处理运输的物料的总质量大于目标组批质量w的情况下,该方法能够进一步优化组批质量和组批车辆的等待时长。在上述实施例的基础上,作为一种可选实施例,若车辆i的等待时长大于最大组批等待时长,则将变量xi在上述模型中置为常数1。为避免车辆的等待时间过长,本发明实施例中,若车辆i的等待时长超过了预设的最大组批等待时长bwt,则该车辆在多目标优化中设置为必选车辆,即若车辆i的到达时间满足t-ati>bwt,则xi=1。强制将该车辆加入到即将创建的组批批次中,从而减小车辆的等待时长,进一步避免因组批不及时而导致该车辆等待时间过长。在上述实施例的基础上,作为一种可选实施例,所述进行求解,创建组批批次,包括:s2401、分别求得f1(x)和f2(x)在约束条件下的最大值为:s2402、分别求得f1(x)和f2(x)在约束条件下的最小值为:s2403、根据公式计算得到松弛因子d1,d2;s2404、采用整数线性规划方法求如下模型的最优解:maxz=λxi=0或1(i=1,2,...,n)λ≥0其中,maxz表示对目标函数z求最大值,λ为约束条件中的决策变量,其它参数参参见上述实施例。本发明实施例中,采用模糊数学解法对上述多目标线性规划模型进行求解,最后将最优解中xi=1对应的车辆组成一个新的取样批次加入已组批集合g,并从车辆集合vj中删除,将组批的车辆的到车信息状态标记为已组批。该方法通过模糊数学解法,进一步得到多目标优化模型的最优解。基于上述各方法实施例的内容,下面结合实例对本发明作进一步说明,但不限定本发明。本实施例公开的是某钢铁企业原燃料场的一种基于多目标优化的汽车取样自动组批方法,其中:组批周期t=1小时,组批目标吨位w=600吨,组批重量允许超过目标吨位的最大值δ=20吨,车辆在停车场等待组批的最大时长bwt=3小时。下面以某订单的到车情况对本发明的组批过程进行说明。假设目前该订单不存在已完成的组批,该订单的车辆达到信息如下表所示:车牌号物料发运净重(吨)到达时间001动力煤852019-5-808:00002动力煤922019-5-808:03003动力煤872019-5-808:05004动力煤862019-5-808:09005动力煤872019-5-808:12006动力煤832019-5-808:15007动力煤842019-5-808:20008动力煤982019-5-808:25009动力煤852019-5-808:36010动力煤862019-5-808:45料场门上管理人员在车辆到达时,依次录入车辆001~010的到车信息。本实施例中,定时周期t=1小时,假设组批周期定时触发组批优化流程的时刻在08:45。结合图2,组批优化流程按如下步骤进行处理:(1)对信息录入模块中获得的到车信息按照订单号进行分组,原因是汽车取样要求运送物料的车辆必须属于同一订单。(2)由步骤(1)得到m=1个订单未组批,令j=1,即从第一个订单号开始进行组批优化。(3)对第j个订单中的未组批车辆按照到车时间升序排列,得到车辆集合vj。(4)将符合条件的车辆插入到已有组批。具体地:在已组批次集合g中搜索是否存在订单号与第j个订单的订单号相同,且组批吨位<w+δ-vj中车辆运输物料重量的最小值的组批。若存在组批g∈g满足条件,则顺序遍历车辆集合vj,将满足检验条件的车辆加入到组批g,并从vj中删除,将组批的车辆的到车信息状态标记为已组批。本实施例中不存在组批g∈g满足条件。(5)进行下一步。(6)vj中剩余车辆数为n=10。令wi(i=1,2,…,n)表示第i台车运输的物料的重量,ati(i=1,2,…,n)表示车辆i的到达时间。vj中车辆运输的物料的总重量≥w,则转到步骤(7);(7)通过建立并求解多目标优化模型创建新的取样批次。优化模型构建如下:xi=0或1(i=1,2,...,n)其中,xi表示是否选中车辆i组批,maxf1(x)表示最大化组批吨位,maxf2(x)最大化车辆到达时刻与组批时刻的间隔的平均值。另外,若车辆i的到达时间满足t-ati>bwt,则xi=1,将变量xi在上述模型中退化为常数。采用模糊数学解法对上述多目标线性规划模型进行求解。该方法的求解步骤如下:1)分别求得f1(x)和f2(x)在约束条件下的最大值为:2)分别求得f1(x)和f2(x)在约束条件下的最小值为:3)根据公式计算得到松弛因子d1=620,d2=25.1;4)采用整数线性规划方法求解如下模型:maxz=λxi=0或1(i=1,2,...,n)λ≥0得到最优解为(1,1,1,1,1,1,0,1,0,0,0.9801)t,即原模型的最优解为x*=(1,1,1,1,1,1,0,1,0,0)t。将最优解中xi=1对应的车辆,即001,002,003,004,005,006和008,组成一个新的取样批次加入g,并从vj中删除,然后将组批的车辆的到车信息状态标记为已组批。(8)令j=j+1,若j>m则流程结束,否则转到步骤(3)。以上所述仅为本发明技术方案的较佳实施例而已,并非用于限定本发明的保护范围。凡在本发明的精神和原则之内,所作的任何修改、等同替换、改进等,均应包含在本发明的保护范围之内。当前第1页12