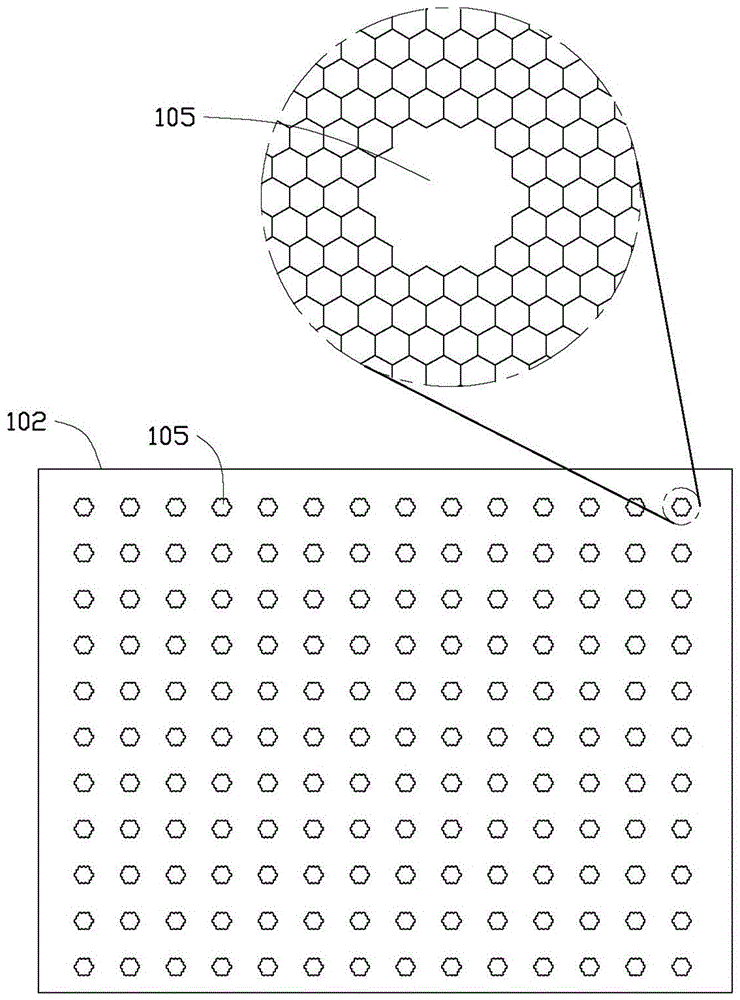
本发明涉及一种具有微构造的外延结构体。
背景技术:以GaN以及InGaN,AlGaN为主的氮化物形成的具有微构造的外延结构体是近年来备受关注的半导体结构,其连续可变的直接带隙,优异的物理化学稳定性,高饱和电子迁移率等特性,使之成为激光器,发光二极管等光电子器件和微电子器件的优选半导体结构。由于GaN等本身生长技术的限制,现今大面积的GaN半导体层大多生长在蓝宝石等其他基底上。由于氮化镓和蓝宝石基底的晶格常数不同,从而导致氮化镓外延层存在较多位错缺陷。现有技术提供一种改善上述不足的方法,其采用非平整的蓝宝石基底外延生长氮化镓。然而,现有技术通常采用光刻等微电子工艺在蓝宝石基底表面形成沟槽从而构成非平整外延生长面。该方法不但工艺复杂,成本较高,而且会对蓝宝石基底外延生长面造成污染,从而影响外延结构的质量。
技术实现要素:综上所述,确有必要提供一种位错缺陷较少,且外延层与衬底之间的应力较小的高质量的具有微构造的外延结构体。一种具有微构造的外延结构体,其包括一外延层及一石墨烯层,所述外延层一表面具有多个凹槽及多个凸起以形成一图案化表面,所述石墨烯层具有多个开口,所述石墨烯层设置于该外延层的图案化的表面,并嵌入该外延层的多个凹槽中,所述外延层的多个凸起由所述石墨烯层的多个开口露出,所述石墨烯层为具有多个开口的连续的整体结构体,所述石墨烯层的厚度为一个碳原子厚度。一种具有微构造的外延结构体,其包括层叠设置的一外延层及一具有多个开口的图案化的单层石墨烯薄膜,外延层的部分渗透所述石墨烯薄膜的多个开口露出,所述开口的尺寸为10纳米~120微米,所述图案化的单层石墨烯薄膜的占空比为1:4~4:1,所述石墨烯层为具有多个开口的连续的整体结构体,所述石墨烯层的厚度为一个碳原子厚度。与现有技术相比,本发明提供的具有微构造的外延结构体采用具有多个开口石墨烯层作为掩膜的方式生长外延层,大大降低了具有微构造的外延结构体的制备成本,并且所述石墨烯层具有良好的导电性,使得所述具有微构造的外延结构体具有广泛用途。附图说明图1为本发明第一实施例提供的具有微构造的外延结构体的制备方法的工艺流程图。图2为图1中采用的第一种图案化石墨烯层的示意图。图3为图1中采用的第二种图案化石墨烯层的示意图。图4为图1中采用的第三种图案化石墨烯层的示意图。图5为图1中采用的第四种图案化石墨烯层的示意图。图6为本发明第一实施例中采用的碳纳米管膜的扫描电镜照片。图7为图6中的碳纳米管膜中的碳纳米管片段的结构示意图。图8为本发明采用的多层交叉设置的碳纳米管膜的扫描电镜照片。图9为图1中外延层的生长过程的示意图。图10为本发明第一实施例提供的具有微构造的外延结构体的示意图。图11为图10所示的具有微构造的外延结构体沿线XI-XI的剖面示意图。图12为本发明第二实施例提供的具有微构造的外延结构体的分解示意图。图13为图12所示的具有微构造的外延结构体整合示意图。图14为本发明第四实施例提供的具有微构造的外延结构体的制备方法的工艺流程图。主要元件符号说明具有微构造的外延结构体10,20基底100外延生长面101石墨烯层102第一石墨烯层202第二石墨烯层302凹槽1043凸起1045外延层104第一外延层204第二外延层304开口105缓冲层1041外延晶粒1042外延薄膜1044碳纳米管片段143碳纳米管145如下具体实施方式将结合上述附图进一步说明本发明。具体实施方式以下将结合附图详细说明本发明实施例提供的具有微构造的外延结构体及其制备方法。为了便于理解本发明的技术方案,本发明首先介绍一种具有微构造的外延结构体的制备方法。请参照图1,本发明第一实施例提供一种具有微构造的外延结构体10的制备方法,具体包括一下步骤:S11:提供一基底100,且该基底100具有一外延生长面101;S12:在基底100的外延生长面101生长一缓冲层1041;S13:在所述缓冲层1041的远离基底100的表面设置一图案化的石墨烯层102;S14:在设置有石墨烯层102的缓冲层1041表面生长一外延层104;S15,去除所述基底100,得到所述具有微构造的外延结构体10。在步骤S11中,所述基底100提供了生长所述外延层104的外延生长面101。所述基底100的外延生长面101是分子平滑的表面,且去除了氧或碳等杂质。所述基底100可以为单层或多层结构。当所述基底100为单层结构时,该基底100可以为一单晶结构体,且具有一晶面作为外延层104的外延生长面101。所述单层结构的基底100的材料可以为SOI(silicononinsulator,绝缘基底上的硅)、LiGaO2、LiAlO2、Al2O3、Si、GaAs、GaN、GaSb、InN、InP、InAs、InSb、AlP、AlAs、AlSb、AlN、GaP、SiC、SiGe、GaMnAs、GaAlAs、GaInAs、GaAlN、GaInN、AlInN、GaAsP、InGaN、AlGaInN、AlGaInP、GaP:Zn或GaP:N等。当所述基底100为多层结构时,其需要包括至少一层上述单晶结构体,且该单晶结构体具有一晶面作为外延层104的外延生长面101。所述基底100的材料可以根据所要生长的外延层104来选择,优选地,使所述基底100与外延层104具有相近的晶格常数以及热膨胀系数。所述基底100的厚度、大小和形状不限,可以根据实际需要选择。所述基底100不限于上述列举的材料,只要具有支持外延层104生长的外延生长面101的基底100均属于本发明的保护范围。本实施例中,所述基底100的材料为Al2O3。步骤S12中,所述缓冲层1041的生长方法可以分别通过分子束外延法(MBE)、化学束外延法(CBE)、减压外延法、低温外延法、选择外延法、液相沉积外延法(LPE)、金属有机气相外延法(MOVPE)、超真空化学气相沉积法(UHVCVD)、氢化物气相外延法(HVPE)、以及金属有机化学气相沉积法(MOCVD)等中的一种或多种实现。所述缓冲层1041的材料可以为Si、GaAs、GaN、GaSb、InN、InP、InAs、InSb、AlP、AlAs、AlSb、AlN、GaP、SiC、SiGe、GaMnAs、GaAlAs、GaInAs、GaAlN、GaInN、AlInN、GaAsP、InGaN、AlGaInN、AlGaInP、GaP:Zn或GaP:N。当缓冲层1041根据所要生长的外延层的材料选取,所述缓冲层1041的材料能够减少所述外延层生长过程中的晶格失配,降低生长的的位错密度即可。所述缓冲层1041的材料可与基底100的材料相同或不同。本实施例中,采用MOCVD工艺进行外延生长缓冲层1041。其中,采用高纯氨气(NH3)作为氮的源气,采用氢气(H2)作载气,采用三甲基镓(TMGa)或三乙基镓(TEGa)、三甲基铟(TMIn)、三甲基铝(TMAl)作为Ga源、In源和Al源。所述缓冲层1041的生长具体包括以下步骤:首先,将蓝宝石基底100置入反应室,加热到1100℃~1200℃,并通入H2、N2或其混合气体作为载气,高温烘烤200秒~1000秒。其次,继续同入载气,并降温到500℃~650℃,通入三甲基镓或三乙基镓以及氨气,低温生长GaN层,所述低温GaN层作为继续生长外延层104的缓冲层1041,其厚度10纳米~50纳米。在步骤S13中,所述石墨烯层102可以由石墨烯粉末或石墨烯薄膜构成。所述石墨烯粉末为分散的石墨烯颗粒,所述石墨烯薄膜为一连续的单层碳原子层,即单层石墨烯。当所述石墨烯层102包括石墨烯粉末时,所述石墨烯粉末需要经过溶液分散、涂覆以及刻蚀等图案化工艺形成图案化的整体结构。当所述石墨烯层102包括多个石墨烯薄膜时,该多个石墨烯薄膜可以层叠设置或共面设置。所述石墨烯薄膜可以经过切割或刻蚀等工艺处理形成图案化结构。所述单层石墨烯有着非常独特的性能。首先,单层石墨烯几乎完全透明,大约只吸收2.3%的可见光,并可透过大部分红外线;其次,单层石墨烯厚度仅约为0.34nm,比表面积的理论值为2630m2·g-1,而实测石墨烯的抗拉强度为125GPa,杨氏模量达到了1.0TPa;再次,石墨烯薄膜的热导率实测值为5300W·m-1·K-1,其载流子迁移率的理论值为2×105cm2·V-1·s-1,而其电阻率只有1×10-6Ω·cm,约为铜的2/3;最后,在室温下即能观测到石墨烯薄膜具有量子霍尔效应和无散射传输现象。本实施例中,所述石墨烯层102为一纯石墨烯结构,即仅包括石墨烯材料。所述石墨烯层102的厚度为1纳米~100微米,比如1纳米、10纳米、200纳米,1微米或10微米。可以理解,当所述石墨烯层102为单层石墨烯时,所述石墨烯层102为一个碳原子厚度。优选地,所述石墨烯层102为一图案化结构。当所述石墨烯层102设置在所述缓冲层1041的远离基板100的表面时,使所述缓冲层1041的远离基板100的表面通过所述石墨烯层102部分暴露出来,以便于在该所述缓冲层1041暴露出来的部分表面上生长半导体外延层104,即所述石墨烯层102起掩模作用。如图2~图4所示,所述“图案化结构”指所述石墨烯层102为一具有多个开口105的连续整体结构。当所述石墨烯层102设置在所述缓冲层1041的远离基板100的表面时,使所述所述缓冲层1041的远离基板100的表面对应开口105的部分暴露出来。所述多个开口105的形状不限,可以为圆形、方形、三角形、菱形或矩形等。同一个石墨烯层102的多个开口105的形状可以相同或不同。所述多个开口105从所述石墨烯层102的厚度方向贯穿所述石墨烯层102。所述开口105可以为如图2所示的微孔或者如图3所示的条形的间隙。所述开口105为微孔时其孔径(平均孔径)范围为10纳米~500微米,所述开口105为间隙时其宽度(平均宽度)范围为10纳米~500微米。以下称为“所述开口105的尺寸”是指孔径或间隙宽度的尺寸范围。所述石墨烯层102中的微孔和间隙可以同时存在并且两者尺寸可以在上述尺寸范围内不同。所述开口105的尺寸可以为10纳米~300微米,比如10纳米、1微米、10微米、80微米或120微米等。所述开口105的尺寸越小,有利于在生长外延层的过程中减少位错等缺陷的产生,以获得高质量的半导体外延层104。优选地,所述开口105的尺寸为10纳米~10微米。进一步地,所述石墨烯层102的占空比为1:100~100:1,如1:10、1:2、1:4、4:1、2:1或10:1。优选地,所述占空比为1:4~4:1。所谓“占空比”指该石墨烯层102设置于所述缓冲层1041的远离基板100的表面后,该缓冲层1041的远离基板100的表面被石墨烯层102占据的部分与通过开口105暴露的部分的面积比。本实施例中,所述开口105在所述石墨烯层102中均匀分布。所述“图案化结构”也可以为设置于基底100表面的多个间隔设置的图案,且相邻两个图案之间形成多个开口105。当所述石墨烯层102设置在所述缓冲层1041的远离基板100的表面时,使所述缓冲层1041的远离基板100的表面对应开口105的部分暴露出来。如图5所示,所述石墨烯层102为多个平行且间隔设置的石墨烯条带,相邻的石墨烯条带之间为所述开口105。所述石墨烯层102可以直接生长在所述缓冲层1041的远离基板100的表面或先制备石墨烯后再转移至所述缓冲层1041的远离基板100的表面。所述石墨烯粉末可以通过液相剥离法、插层剥离法、剖开碳纳米管法、溶剂热法、有机合成法等方法中的一种或多种制备。所述石墨烯薄膜可以通过化学气相沉积(CVD)法、机械剥离法、静电沉积法、碳化硅(SiC)热解法、外延生长法等方法中的一种或多种制备。本实施例中,参见图5,所述石墨烯层102为多个间隔设置的条形石墨烯层102,且每个条形石墨烯为多个石墨烯粉末组成的整体结构,其制备方法具体包括以下步骤。首先,制备一石墨烯粉末溶液。所述石墨烯粉末可以通过液相剥离法、插层剥离法、剖开碳纳米管法、溶剂热法、有机合成法等方法制备。所述石墨烯粉末溶液的溶剂可以为水、乙醇、N-甲基吡咯烷酮、四氢呋喃以及2-氮甲基乙酰胺中的一种或多种。所述石墨烯粉末溶液的浓度为1毫克/毫升~3毫克/毫升。其次,在缓冲层1041的远离基板100的表面形成连续的石墨烯涂层。本实施例,将石墨烯粉末溶液滴到缓冲层1041的远离基板100的表面,并进行甩膜旋涂处理,从而得到连续的石墨烯涂层。所述甩膜旋涂的转速为3000转/分钟~5000转/分钟,所述甩膜旋涂的时间为1分钟~2分钟。最后,将该连续的石墨烯涂层图案化。所述将该连续的石墨烯涂层图案化方法包括光催化二氧化钛切割法、离子束刻蚀法、原子力显微镜刻蚀法、以及等离子体刻蚀法中的一种或多种。本实施例中,通过光催化二氧化钛切割连续的石墨烯涂层,具体包括以下步骤:(a)制备一图案化的金属钛层;(b)将该图案化的金属钛层加热氧化得到一图案化的二氧化钛层;(c)将该图案化的二氧化钛层与连续的石墨烯涂层接触,并采用紫外光照射该图案化的二氧化钛层;以及(d)去除图案化的二氧化钛层。可以理解,该方法中,得到的石墨烯层102的图案与所述二氧化钛层的图案相互啮合,即所述连续的石墨烯涂层与二氧化钛层对应的地方被去除。所述步骤(a)中,所述图案化的金属钛层可以通过掩模蒸镀法或光刻曝光法制备形成在一石英基底表面。所述石英基底的厚度为300微米~1000微米,所述金属钛层的厚度为3纳米~10纳米。本实施例中,所述石英基底的厚度为500微米,所述金属钛层的厚度为4纳米。所述图案化的金属钛层为一具有多个间隔设置的条形开口的连续金属钛层。所述步骤(b)中,将图案化的金属钛层在500℃~600℃条件下加热1小时~2小时。所述步骤(c)中,所述紫外光的波长为200纳米~500纳米,所述紫外光照射的气氛为空气或氧气,所述紫外光照射的环境湿度为40%~75%,所述紫外光照射的时间为30分钟~90分钟。由于二氧化钛为光催化半导体材料,在紫外光照射下会产生电子与空穴的分离。该电子与空穴分别被二氧化钛表面的Ti(IV)和晶格氧所捕获,从而具有很强的氧化还原能力。被捕获的电子与空穴很容易氧化还原空气中的氧气和水而形成O2和H2O2等活性物质,该活性物质可以将石墨烯分解。所述步骤(d)中,通过将石英基底移开去除图案化的二氧化钛层。可以理解,所述步骤(a)中,还可以通过将金属钛直接沉积在一图案化的碳纳米管结构表面。该碳纳米管结构可以为碳纳米管膜,碳纳米管线或其组合。当该碳纳米管结构为多个碳纳米管线时,该多个碳纳米管线可以平行间隔或交叉设置,由于碳纳米管线之间具有微孔或间隙,所以该多个碳纳米管线形成一图案化结构。当该碳纳米管结构为碳纳米管膜时,由于碳纳米管膜中的碳纳米管之间具有微孔或间隙,所以该碳纳米管膜形成一图案化结构。由于金属钛层直接沉积在碳纳米管膜中的碳纳米管表面,所以也形成一图案化结构。所述步骤(b)中,还可以通过给碳纳米管通入电流的方式加热氧化碳纳米管表面的金属钛。所述步骤(c)中,与碳纳米管对应位置的石墨烯被分解去除形成开口105。即,得到的石墨烯层102的图案与所述碳纳米管结构的图案相互啮合。由于碳纳米管的直径仅为0.5纳米~50纳米,所以可以制备出几十纳米尺寸的开口105。通过选择碳纳米管的直径可以控制石墨烯层102的开口105的尺寸。该碳纳米管结构为一自支撑结构。所谓“自支撑”指该碳纳米管结构不需要大面积的载体支撑,而只要相对两边提供支撑力即能整体上悬空而保持自身状态,即将该碳纳米管结构置于(或固定于)间隔特定距离设置的两个支撑体上时,位于两个支撑体之间的碳纳米管结构能够悬空保持自身状态。所述步骤(d)中,由于该碳纳米管结构为一自支撑结构,所以通过将碳纳米管结构移开,可以方便的去除图案化的二氧化钛层。例如,首先,将多个平行间隔设置的碳纳米管线表面沉积金属钛;然后,通过加热将金属钛氧化形成二氧化钛;其次,将该多个平行间隔设置的碳纳米管线设置于连续的石墨烯涂层表面,并采用紫外光照射该多个平行间隔设置的碳纳米管线;最后,将多个平行间隔设置的碳纳米管线去除得到具有多个条形开口的石墨烯层102。所述碳纳米管膜可以为一从碳纳米管阵列中拉取获得自支撑结构。参见图6和图7,具体地,所述碳纳米管膜包括多个连续且定向延伸的碳纳米管片段143。该多个碳纳米管片段143通过范德华力首尾相连。每一碳纳米管片段143包括多个相互平行的碳纳米管145,该多个相互平行的碳纳米管145通过范德华力紧密结合。该碳纳米管片段143具有任意的长度、厚度、均匀性及形状。所述碳纳米管膜可通过从一碳纳米管阵列中选定部分碳纳米管后直接拉取获得。所述碳纳米管膜的厚度为1纳米~100微米,宽度与拉取出该碳纳米管膜的碳纳米管阵列的尺寸有关,长度不限。所述碳纳米管膜中相邻的碳纳米管之间存在微孔或间隙,且该微孔的孔径或间隙的尺寸小于10微米。优选地,所述碳纳米管膜的厚度为100纳米~10微米。该碳纳米管膜中的碳纳米管145沿同一方向择优取向延伸。所述碳纳米管膜及其制备方法具体请参见申请人于2007年2月9日申请的,于2010年5月26日公告的第CN101239712B号中国公开专利“碳纳米管膜结构及其制备方法”。为节省篇幅,仅引用于此,但上述申请所有技术揭露也应视为本发明申请技术揭露的一部分。请参阅图8,当多层碳纳米管膜层叠设置时,相邻两层碳纳米管膜中的碳纳米管的延伸方向形成一交叉角度α,且α大于等于0度小于等于90度(0°≤α≤90°)。所述石墨烯层102还可以为一包括石墨烯以及添加材料的复合结构。所述添加材料包括碳纳米管、碳化硅、氮化硼、氮化硅、二氧化硅、无定形碳等中的一种或多种。所述添加材料还可以包括金属碳化物、金属氧化物及金属氮化物等中的一种或多种。所述添加材料可以通过化学气相沉积(CVD)、物理气相沉积(PVD)、磁控溅射等方法形成于石墨烯的表面。可以理解,本实施例中,也可以先对缓冲层1041的远离基板100的表面进行表面处理形成石墨烯浸润区域与石墨烯不浸润区域,然后涂敷石墨烯层直接形成图案化的石墨烯层102。所述表面处理的方法为自组装分子法、臭氧处理法、氧等离子处理法、氩等离子处理法、紫外光照法、以及蒸镀法中的一种或多种。所述石墨烯层102还可以为一包括石墨烯以及添加材料的复合结构。所述添加材料包括碳纳米管、碳化硅、氮化硼、氮化硅、二氧化硅、无定形碳等中的一种或多种。所述添加材料还可以包括金属碳化物、金属氧化物及金属氮化物等中的一种或多种。所述添加材料可以通过化学气相沉积(CVD)、物理气相沉积(PVD)、磁控溅射等方法形成于石墨烯的表面。以上内容可知,所述石墨烯层102起着生长半导体外延层104的掩模作用。所谓“掩模”是指该石墨烯层102用于遮挡所述缓冲层1041的部分表面,且暴露部分缓冲层1041的表面,从而使得半导体外延层104仅从所述缓冲层1041的表面的暴露的部分生长。由于石墨烯层102具有多个开口105,所以该石墨烯层102形成一图案化的掩模。由于所述石墨烯层102在所述缓冲层1041的远离基板100的表面形成多个开口105,从而使得所述缓冲层1041的远离基板100的表面上具有一图案化的掩模。可以理解,相对于光刻等微电子工艺,通过设置石墨烯层102作为掩模进行外延生长的方法工艺简单、成本低廉,不易在基底100的外延生长面101引入污染,而且绿色环保。可以理解,所述基底100、缓冲层1041和石墨烯层102共同构成了用于生长异质外延结构的衬底。该衬底可用于生长外延层104,如半导体外延层、金属外延层或合金外延层。该衬底也可用于生长同质外延层,从而得到一同质外延结构。步骤S14中,所述外延层104的生长方法可以分别通过分子束外延法(MBE)、化学束外延法(CBE)、减压外延法、低温外延法、选择外延法、液相沉积外延法(LPE)、金属有机气相外延法(MOVPE)、超真空化学气相沉积法(UHVCVD)、氢化物气相外延法(HVPE)、以及金属有机化学气相沉积法(MOCVD)等中的一种或多种实现,所述外延层104的材料可以与缓冲层1041的材料相同或者不同。所述外延层104的生长的厚度可以根据需要制备。具体地,所述外延层104的生长的厚度可以为0.5纳米~1毫米。例如,所述外延层104的生长的厚度可以为100纳米~500微米,或200纳米~200微米,或500纳米~100微米。所述外延层104的材料为半导体材料,如Si、GaAs、GaN、GaSb、InN、InP、InAs、InSb、AlP、AlAs、AlSb、AlN、GaP、SiC、SiGe、GaMnAs、GaAlAs、GaInAs、GaAlN、GaInN、AlInN、GaAsP、InGaN、AlGaInN、AlGaInP、GaP:Zn或GaP:N。可以理解,所述外延层104的材料也可以为金属或合金等其他材料,只要保证所述材料可用上述生长方法如MBE、CBE、MOVPE等方法生长即可。本实施例中,生长所述外延层104时采用的所述石墨烯层102为一图案化的单层石墨烯薄膜。所述外延层104的制备方法为,在生长完缓冲层1041的工艺条件下,将设置有石墨烯层102及缓冲层1041的基底100的温度保持在1000℃~1100℃,持续通入氨气和载气,同时通入三甲基镓或三乙基镓,在高温下生长出高质量的外延层104。具体的,参见图9所述外延层104的制备方法包括以下步骤:S141:沿着基本垂直于所述缓冲层1041表面的方向成核并外延生长形成多个外延晶粒1042;S142:所述多个外延晶粒1042沿着基本平行于所述缓冲层1041表面的方向外延生长形成一连续的外延薄膜1044;S143:所述外延薄膜1044沿着基本垂直于所述缓冲层1041表面的方向外延生长形成一外延层104。在步骤S141,由于石墨烯层102设置于所述缓冲层1041表面,因此外延晶粒仅从所述缓冲层1041暴露的部分生长,即外延晶粒从石墨烯层102的开口105处生长出来。在步骤S142中,通过控制生长条件使所述多个外延晶粒1042沿着基本平行于所述基底100的外延生长面101的方向同质外延生长并连成一体将所述石墨烯层102覆盖。即,该步骤中所述多个外延晶粒1042进行侧向外延生长直接合拢,并最终形成多个凹槽1043将石墨烯层102包围。所述凹槽1043的形状与石墨烯层102的图案有关。步骤S143中,由于所述石墨烯层102的存在,使得外延晶粒1042与基底100之间的晶格位错在形成连续的外延薄膜1044的过程中停止生长。因此,该步骤的外延层104相当于在没有缺陷的外延薄膜1044表面进行同质外延生长。步骤S15中,所述基底100的去除方法可为激光照射法、腐蚀法或温差自剥离法。所述去除方法可根据基底100以及外延层104材料的不同进行选择。本实施例中,所述基底100的去除方法为激光照射法。具体的,所述去除方法包括以下步骤:S151,将所述基底100中未生长外延层104的表面进行抛光并清洗;S152,将经过表面清洗的基底100放置于一平台(图未示)上,并利用激光对所述基底100与外延层104进行扫描照射;S153,将经激光照射后的基底100浸入溶液中去除所述基底100,形成所述具有微构造的外延结构体10。在步骤S151中,所述抛光方法可为机械抛光法或化学抛光法,使所述基底100的表面平整光滑,以减少后续激光照射中激光的散射。所述清洗可用盐酸、硫酸等冲洗所述基底100的表面,从而去除表面的金属杂质以及油污等。在步骤S152中,所述激光从基底100抛光后的表面入射,且入射方向基本垂直于所述基底100抛光后的表面,即基本垂直于所述基底100与外延层104的界面。所述激光的波长不限,可根据缓冲层1041以及基底100的材料选择。具体的,所述激光的能量小于基底100的带隙能量,而大于缓冲层1041的带隙能量,从而激光能够穿过基底100到达缓冲层1041,在缓冲层1041与基底100的界面处进行激光剥离。所述界面处的缓冲层1041对激光产生强烈的吸收,从而使得界面处的缓冲层1041温度快速升高而分解。本实施例中所述外延层104为GaN,其带隙能量为3.3ev;基底100为蓝宝石,其带隙能量为9.9ev;所述激光器为KrF激光器,发出的激光波长为248nm,其能量为5ev,脉冲宽度为20~40ns,能量密度为400~600mJ/cm2,光斑形状为方形,其聚焦尺寸为0.5mm×0.5mm;扫描位置从所述基底100的边缘位置开始,扫描步长为0.5mm/s。在扫描的过程中,所述GaN缓冲层1041开始分解为Ga和N2。可以理解,所述脉冲宽度、能量密度、光斑形状、聚焦尺寸以及扫描步长可根据实际需求进行调整;可根据缓冲层1041对特定波长的激光具有较强的吸收作用选择相应波长的激光。由于所述GaN缓冲层1041对上述波长的激光具有很强的吸收作用,因此,所述缓冲层1041的温度快速升高而分解;而所述外延层104对上述波长的激光吸收较弱或不吸收,因此所述外延层104并不会被所述激光所破坏。可以理解,对于不同的缓冲层1041可以选择不同波长的激光,使缓冲层1041对激光具有很强的吸收作用。所述激光照射的过程在一真空环境或保护性气体环境进行以防止在激光照射的过程中石墨烯层102被氧化而破坏。所述保护性气体可以为氮气、氦气或氩气等惰性气体。在步骤S153中,可将激光照射后的基底100及外延层104浸入一酸性溶液中,以去除GaN分解后的Ga,从而实现基底100与外延层104的剥离,形成所述具有微构造的外延结构体10。所述溶液可为盐酸、硫酸、硝酸等可溶解Ga的溶剂。由于缓冲层1041的存在,一方面,所述缓冲层1041设置在石墨烯层102与基底100之间,将所述石墨烯层102与基底100隔离开,因此在剥离基底100的过程中,所述石墨烯层102不会直接吸附于基底100上而从外延层104中剥离;另一方面,在激光照射缓冲层1041的过程中,所述缓冲层1041受热分解并经溶液溶解后,石墨烯层102会与所述缓冲层1041脱离,从而使得所述石墨烯层102保留于凹槽1043中。进一步的,在缓冲层1041受热分解的过程中,缓冲层1041分解产生的气体受热膨胀,会将石墨烯层102推离所述缓冲层1041与基底100,从而使得石墨烯层102更容易与缓冲层1041分离。由于石墨烯层102的存在,使外延层104与缓冲层1041之间的接触面积减小,从而减小了生长过程中外延层104与缓冲层1041之间的应力。因此,在激光照射去除基底100的过程中,使得缓冲层1041及基底100的剥离更加的容易,也减小了对外延层104的损伤。所述S15步骤结束后得到一具有微构造的外延结构体10,其包括一外延层104及一石墨烯层102,所述外延层104一表面具有多个凹槽1043,所述石墨烯层102设置于该外延层104的图案化的表面,并嵌入该外延层104的多个凹槽1043。如图10及图11所示,本发明进一步提供一种由上述方法制备的具有微构造的外延结构体10,所述具有微构造的外延结构体10包括一外延层104及一石墨烯层102,所述外延层104一表面具有多个凹槽1043及多个凸起1045以形成一图案化表面,所述石墨烯层102为具有多个开口105的连续的整体结构体,所述石墨烯层102设置于该外延层104的图案化的表面,并嵌入该外延层104的多个凹槽1043中,所述外延层104的多个凸起1045由所述石墨烯层102的多个开口105露出。所述具有微构造的外延结构体10是指所述外延层104表面具有由多个凹槽1043和多个凸起1045间隔形成的微结构,所述微结构是在外延层104生长过程中,外延层104从石墨烯层102中的开口位置生长,之后围绕石墨烯层102进行侧向外延生长所形成,将基底100剥离后,在所述外延层104的表面形成多个凹槽1043和多个凸起1045。本实施例提供的具有微构造的外延结构体,由于所述石墨烯层102直接暴露于外延层104的表面,因此所述石墨烯层102可以直接作为具有微构造的外延结构体10的大面积电极,从而可以改善具有微构造的外延结构体10中的电场分布及电流走向,进而提高具有微构造的外延结构体10的工作效率。本发明第二实施例提供另一种具有微构造的外延结构体10的制备方法,具体包括以下步骤:S21,提供一基底100,且该基底100具有一支持外延层104生长的外延生长面101;S22,在基底100的外延生长面101生长一缓冲层1041;S23,在所述缓冲层1041的远离基底100的表面平铺一石墨烯层102;S24,在设置有石墨烯层102的缓冲层1041表面生长外延层104;S25,将基底浸入腐蚀溶液中,剥离所述基底100,得到所述具有微构造的外延结构体10。本发明第二实施例的具有微构造的外延结构体10的制备方法与第一实施例的制备方法基本相同,其区别在于,本实施例中所述基底100的材料为SiC,外延生长面101上生长的缓冲层1041为AlN或TiN,外延层104为GaN,并且所述去除方法为腐蚀法。本发明第二实施例中采用单层石墨烯薄膜制备石墨烯层202制备石墨烯层102,其制备方法包括以下步骤。具体的,在步骤S23中,该石墨烯层102的制备方法包括以下步骤:首先,制备一单层石墨烯薄膜。本实施例中,采用CVD法制备单层石墨烯薄膜,具体包括以下步骤:(a1)提供一衬底;(b1)在衬底上沉积金属催化剂层;(c1)对金属催化剂层进行退火处理;以及(d1)在碳源气氛中生长单层石墨烯薄膜。所述步骤(a1)中,所述衬底可以为铜箔或Si/SiO2。本实施例中,所述衬底为Si/SiO2。所述Si层的厚度为300微米~1000微米,所述SiO2层的厚度为100纳米~500纳米。优选地,所述Si层的厚度为600微米,所述SiO2层的厚度为300纳米。所述步骤(b1)中,所述金属催化剂层的材料包括镍、铁、金等,所述金属催化剂层的厚度为100纳米~800纳米。所述金属催化剂层可以通过化学气相沉积(CVD)、物理气相沉积(PVD)、磁控溅射或电子束蒸镀等方法制备。本实施例中,采用电子束蒸镀法在SiO2层表面沉积一厚度为500纳米的金属镍。所述步骤(c1)中,所述退火温度为900℃~1000℃;所述退火的气氛为氩气和氢气混合气体,其中氩气的流量为600sccm,氢气的流量为500sccm;所述退火时间为10分钟~20分钟。所述步骤(d1)中,所述生长温度为900℃~1000℃;所述碳源气为甲烷;所述生长时间为5分钟~10分钟。其次,将该单层石墨烯薄膜转移至所述缓冲层1041的远离基底100的表面。本实施例中,具体包括以下步骤:(a2)在单层石墨烯薄膜表面涂覆有机胶体或聚合物作为支撑体;(b2)对涂覆有机胶体或聚合物的单层石墨烯薄膜烘烤坚膜;(c2)将坚膜后的单层石墨烯薄膜以及Si/SiO2衬底一起浸泡在去离子水中使金属催化剂层和SiO2层分离;(d2)将分离后的支撑体/单层石墨烯薄膜/金属催化剂层复合结构去除金属催化剂层;(e2)将支撑体/单层石墨烯薄膜复合结构设置在外延生长面101,并加热使单层石墨烯薄膜与所述缓冲层1041牢固结合;以及(f2)去除支撑体。所述步骤(a2)中,所述支撑体的材料为聚甲基丙烯酸甲酯(PMMA)、聚二甲基硅氧烷、光刻正胶9912、光刻胶AZ5206中的一种或多种。所述步骤(b2)中,所述烘烤的温度为100℃~185℃。所述步骤(c2)中,浸泡在去离子水中之后,对所述金属催化剂层和SiO2层进行超声处理。所述步骤(d2)中,通过化学液腐蚀去除金属催化剂层,该化学液可以为硝酸、盐酸、氯化铁(FeCl3)、硝酸铁(Fe(NO3)3)等。所述步骤(f2)中,去除支撑体的方法为先用丙酮和乙醇浸泡,然后在保护气体中加热到约400℃。最后,将该单层石墨烯薄膜图案化。所述将该单层石墨烯薄膜图案化方法包括光催化二氧化钛切割法、离子束刻蚀法、原子力显微镜刻蚀法、以及等离子体刻蚀法中的一种或多种。本实施例中,先将一阳极氧化铝模板(AnodicAluminumOxideTemplate)设置于该单层石墨烯薄膜表面,然后通过等离子体刻蚀法将该单层石墨烯薄膜图案化。其中,所述阳极氧化铝模板具有多个成阵列排布的微孔,与阳极氧化铝模板微孔对应处的单层石墨烯薄膜被等离子体刻蚀去除,从而得到的石墨烯层102为一具有多个微孔的连续单层石墨烯薄膜。在步骤S24中,将所述生长有外延层104的基底100浸入到相应的腐蚀溶液中,使得所述缓冲层1041在溶液中溶解,从而实现基底100的分离。所述溶液可根据缓冲层1041以及外延层104的材料进行选择,即所述溶液可溶解缓冲层1041而不能溶解外延层104。所述溶液可为NaOH溶液、KOH溶液、NH4OH溶液等,本实施例中,所述溶液为KOH溶液。所述KOH溶液的质量浓度可为30%~50%,浸入时间为2分钟~10分钟,使得KOH溶液浸入到外延层104的凹槽1043中,逐渐腐蚀掉AlN缓冲层,使得SiC基底脱落。由于石墨烯层102与凹槽1043部分接触,石墨烯具有较强的吸附作用,因此在缓冲层1041腐蚀的过程中,所述AlN逐渐在KOH溶液中溶解而从石墨烯层102表面脱离,从而使所述石墨烯层102吸附于凹槽1043中,得到所述具有微构造的外延结构体10。可以理解,所述缓冲层1041以及溶液的材料不限于以上所举,只要保证溶液能够溶解缓冲层1041而不能溶解外延层104即可。如当所述缓冲层为TiN时,所述溶液可为硝酸。进一步的,所述腐蚀法中,也可以直接将基底100溶解去除,从而在溶解的过程中,所述缓冲层1041以及基底100能够同时被溶解,使得石墨烯层102暴露于外延层104的表面。可以理解,如果直接将基底100溶解去除,也可以省去生长缓冲层的步骤。所述腐蚀法中,由于石墨烯层102的存在,石墨烯层102与缓冲层1041之间存在多个凹槽或间隙,从而能够使相应的溶液均匀的分散到缓冲层1041中将缓冲层1041溶解而实现快速的剥离,能够更好保持所述具有微构造的外延结构体的剥离表面的平整和光滑。请参阅图12及13,为本发明第二实施例制备获得的具有微构造的外延结构体10,其包括:一外延层104及一石墨烯层102。本发明第二实施例中的具有微构造的外延结构体10与第一实施例的其区别在于,本发明第二实施例的石墨烯层102为一图案化的单层石墨烯薄膜。本发明第三实施例提供一种具有微构造的外延结构体10的制备方法,具体包括一下步骤:S31,提供一基底100,且该基底100具有一支持外延层104生长的外延生长面101;S32,在基底100的外延生长面101生长一缓冲层1041;S33,在所述缓冲层1041的远离基底100的表面平铺一石墨烯层102;S34,在设置有石墨烯层102的缓冲层1041表面生长外延层104;S35,对所述生长有外延层104的基底100降温,剥离所述基底100,得到所述具有微构造的外延结构体10。本发明第三实施例的具有微构造的外延结构体10的制备方法与第一实施例的半导体层的制备方法基本相同,其区别在于,在步骤S33中,直接将石墨烯粉末分散在缓冲层1041表面。在步骤S35中,所述剥离方法为温差分离法。所述温差分离法为在高温生长GaN完成之后,将所述高温的基底100的温度在2min~20min的时间内,快速的降低到200℃以下,利用外延层104与基底100之间的由于热膨胀系数的不同而产生的应力将二者分离。可以理解,该方法中也可以通过给石墨烯层102通入电流的方式加热外延层104与基底100,再降温从而实现剥离。在剥离基底100的过程中,所述石墨烯层102吸附于凹槽1043中而不会脱落。这是因为一方面所述石墨烯层102为一整体结构,其与凹槽1043之间存在接触;另一方面,所述石墨烯层102嵌入外延层104中,凹槽1043将石墨烯层102半包围起来;第三,所述基底100可沿着平行于外延层104图案化表面的方向剥离,使得石墨烯层102保留于凹槽1043中。进一步的,在所述外延层104从基底100上分离之后,可包括一在外延层104的表面继续侧向生长外延层的步骤。所述进一步生长外延层的步骤可以减少在基底100分离的过程中,外延层104上产生裂纹。如图14所示,本发明第四实施例提供一种具有微构造的外延结构体20的制备方法,主要包括以下步骤:S41,提供一基底100,且该基底100具有一支持外延层204生长的外延生长面101;S42,在基底100的外延生长面101生长一缓冲层1041;S43,在所述缓冲层1041的远离基底100的表面平铺一第一石墨烯层202;S44,在设置有第一石墨烯层202的缓冲层1041表面生长第一外延层204;S45,在所述第一外延层204远离基底100的表面进一步设置一第二石墨烯层302;S46,在所述第一外延层204远离基底100的表面进一步生长一第二外延层304;S47,剥离所述基底100,得到所述具有微构造的外延结构体20。本发明第四实施例提供的具有微构造的外延结构体10的制备方法与第一实施例基本相同,其不同在于,在所述第一外延层204远离缓冲层1041的表面进一步铺设一第二石墨烯层302的步骤S45,以及进一步生长一第二外延层304的步骤S46。所述第二石墨烯层302与第一外延层204接触设置,并且所述第二外延层304覆盖所述第二石墨烯层302生长,将第二石墨烯层302夹持于第一外延层204以及第二外延层304之间,并使第二石墨烯层302嵌入所述第二外延层304中。由于第二石墨烯层302的存在,所述第二外延层304靠近第一外延层204的表面形成多个凹槽1043,所述第二石墨烯层302设置于该凹槽1043内。所述多个凹槽1043在第二外延层304的表面形成一“图案化”的结构,且所述第二外延层304的图案化表面与图案化第二石墨烯层302中的图案基本相同。所述第二石墨烯层302与第二外延层304分别与所述第一石墨烯层202以及第一外延层204的结构基本相同,所述第二外延层304的材料可以与第一外延层204相同或不同。可以理解,还可以在所述第二外延层304的表面继续设置石墨烯层,并进一步生长外延层,从而形成具有多个外延层以及多个石墨烯层的复合结构。所述多个外延层的材料可以相同也可以不同,且多个石墨烯层可以作为不同的电极,使所述具有微构造的外延结构体可以方便的应用于不同的电子器件。本发明采用一石墨烯层作为掩模设置于所述基底外延生长面生长外延层具有以下有以效果:第一,所述石墨烯层可直接铺设或转移在基底的外延生长面,相对于现有技术通过沉积后再光刻等工艺形成掩模,本发明工艺简单,成本低廉,有利于量产。第二,所述石墨烯层为图案化结构,其厚度、开口尺寸均可达到纳米级,所述衬底用来生长外延层时形成的异质外延晶粒具有更小的尺寸,有利于减少位错缺陷的产生,以获得高质量的异质外延层。第三,所述石墨烯层的开口尺寸为纳米级,所述外延层从与纳米级开口对应的暴露的外延生长面生长,使得生长的外延层与基底之间的接触面积减小,减小了生长过程中外延层与衬底之间的应力,从而可以生长厚度较大的异质外延层,可进一步提高异质外延层的质量;同时,由于石墨烯层具有多个开口,减小了外延层与缓冲层之间的接触面积,因此,在剥离基底的过程中,使得基底的剥离更加的容易,也减小了对外延层的损伤。另外,本领域技术人员还可在本发明精神内作其它变化,当然这些依据本发明精神所作的变化,都应包含在本发明所要求保护的范围内。