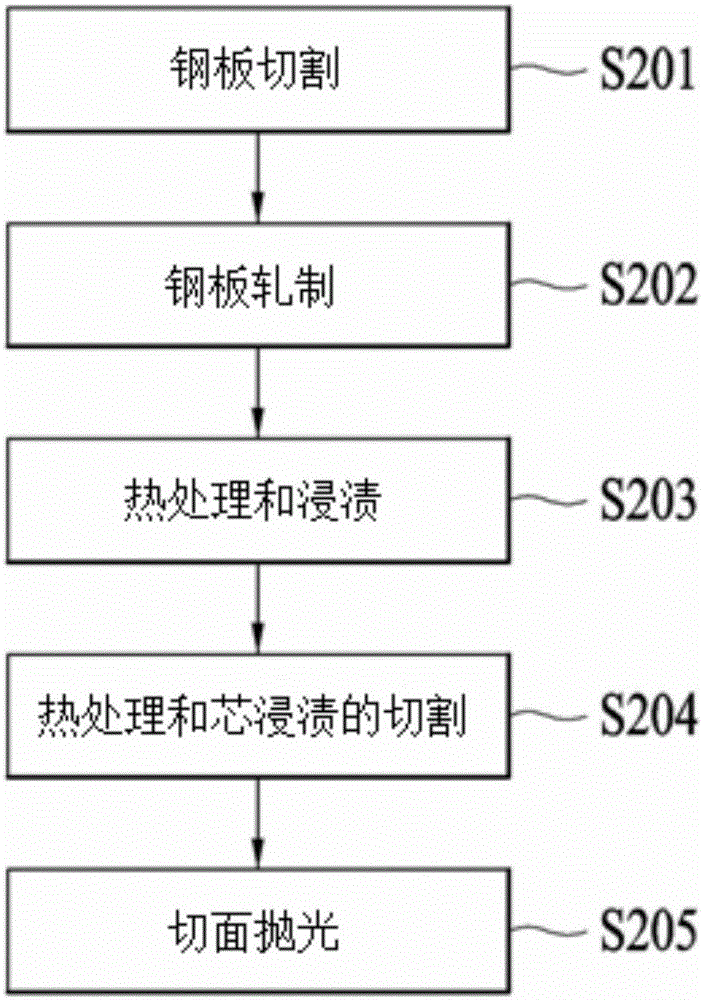
本发明涉及一种制造用于发电的可分离电磁感应装置的方法,尤其涉及一种通过缠绕和切割由非磁性材料(无钴材料)制成的磁芯来制造用于发电的低成本可分离电磁感应装置的方法,使得在可分离磁芯的制造过程中气隙最小化。
背景技术:
:现已经有种耦合装置被开发用来在衰减低频信号和改善高频信号特性,因为在电力系统中使用的耦合装置通常被用于阻断电力频率并且仅在高频带传送通信信号。此外,在电流互感器(CT)应用的情况下,CT已经在特别用于提高线性度的方向上开发,以获得理想的B-H特性。然而,当这些耦合装置用于发电时,这种耦合装置的特性变得无意义。此外,衰减电力频率特性对于发电可能是致命的。因此,功率CT应被配置为具有与现有CT相反的特性,如下所示:(1)电力频率特性应当最大化,并且其他高频信号应当最小化。也就是说,特性应该在低于120Hz的频率范围内最大化,该频率范围是60Hz的工频的倍频,并且在120Hz以上的频率范围内的特性应该尽可能低;(2)一般CT所需的线性B-H特性不是必需的;(3)不需要一般的高饱和特性,而是通过所需的功率能量相对较低的饱和特性更有效。(应当防止高功率线路电流中的无感应感应电压)(参见图1);(4)现有的CT制造工艺应该原样使用,并且甚至应该从低成本材料实现。然而,这样的条件相当适合用于制造具有此特点的功率CT。但是电感器、普通CT等所需的特性与之相反。因此普通电感或者CT的制造技术在用于制造功率CT需求的特性时,可能会招致很大的困难。也就是说,在电感器或CT应用中需要高饱和感应特性以增强线性并且提高在高频带中的信噪比。但是相反地,由于高饱和感应特性在高功率线路电流中产生不规则的高感应电压,可分离CT在处理用作电源的高感应电压时会引起许多问题。同时,由于功率CT在交流线路上运行,在一般磁线中出现的磁通密度的波形也看起来是正弦波波形。并且尽管时有发生,但磁饱和仅仅是暂时现象,在确保电源方面不涉及大的问题。而是相当高的磁饱和所产生的过高的感应电动势,则有可能对生产电能的管理产生困难。图1是功率CT的优选特性的B-H曲线的曲线图。如图1所示。与电感器或典型芯不同,当低电流通过功率线路时,功率CT表现出比典型芯更好的特性。并且当高电流通过电源功率时,功率CT应具有不高于电感器或典型芯的特性,以防止产生过大的感应电压。然而,当功率CT由用于如上所述的现有的普通电感器或CT的磁性合金制成时,将引起各种限制。技术实现要素:本发明所要解决的课题为了解决现有技术的限制,本发明提供了一种用于制造用于发电的可分离的电动感应装置的方法,该装置可以从低功率线路中生成必要的电力力并具有低磁饱和点。解决课题的方案本发明包括:将由轧制的非晶磁性合金构成的钢板卷绕成圆形以形成磁芯;热处理和浸渍缠绕的不添加钴的磁芯;在垂直于所述磁芯的卷绕方向的方向上切割所述热处理和浸渍的磁芯;抛光磁芯的切割表面,磁芯具有在固定状态中均匀排列的切面的三维表面。在一个实施例中,非晶磁性合金可以包括硅钢(SiSteel)。在一个实施方案中,浸渍可以包括真空浸渍。在一个实施例中,切割可以包括在固定于切割方向和与磁芯的切割方向正交的方向的状态下将磁芯切割成半圆形形状。在一个实施例中,抛光可以包括与抛光工艺同时施加冷却剂的抛光。有益效果根据本发明的用于制造用于发电的可分离电磁感应装置的方法,其可以通过非接触电磁感应方法从流过功率线路系统的电流产生电力,并且可以制造高效可分离的感应装置,当低电流流过功率线路时具有高饱和感应特性,并且当高电流流过功率线路时表现出非高饱和感应特性,以便可以容易地调整功率输出。此外,本发明使得可以制造可分离的感应装置,其可以防止由于非高饱和特性而产生过大的感应电压,并且因此可以向负载侧提供稳定的电源。此外,根据本发明,具有非高饱和感应特性并且适合于电能的可分离电磁感应装置可以通过现有的磁芯制造工艺由便宜的材料制造,而获得更廉价的成本,并无需在热处理过程中使用钴。附图说明图1是表示优选功率CT的特性的B-H曲线的曲线图。图2是根据本发明的实施例的用于制造可分离电磁感应装置的方法的流程图。图3是根据图2中的缠绕步骤缠绕的磁芯的透视图。图4是根据图2中的切割步骤切割的磁芯的透视图。图5是示出根据磁芯的切割的B-H特性的变化的曲线图。图6是示出执行图2所示的芯的切割的切割夹具的分解图。图7是表示进行图2所示的研磨工序的研磨夹具的动作状态的立体图。图8示出了比较样品(a)和实施例样品(b)的可分离磁芯的照片。图9是图8所示的各磁芯的输出比较图。具体实施方式下面将结合本实用新型实施例中的附图,对本实用新型实施例中的技术方案进行清楚、完整地描述,显然,所描述的实施例仅仅是本实用新型一部分实施例,而不是全部的实施例。基于本实用新型中的实施例,本领域普通技术人员在没有作出创造性劳动的前提下所获得的所有其他实施例,都属于本实用新型保护的范围。下面结合附图和具体实施例对本发明作进一步说明,但不作为本发明的限定。本发明涉及一种用于制造用于发电的电磁感应装置的方法,其用作是使用从功率线发生的磁场信号来产生功率的功率CT。根据本发明,用于发电的电磁感应装置被制造为可分离型,其在使用中可以容易地安装到电力线路和从电力线路移除,并且被切割成使得三维平面被均匀地平整的切割面,以便最小化从两个芯彼此耦合的表面泄漏的磁通量。此外,根据本发明,使用非钴硅钢来提高在低频带,特别是在120Hz以下的工频范围内的信号传递特性,在低功率线路电流中获得高感应功率,并且为了实现低成本制造以及维持高磁导率,通过使用钢板以减少的气隙效应的方式来制造磁芯。进一步地,通过本发明的方法制造的电磁感应装置可以在低功率线路电流中提供高输出,同时防止过高电压在高功率线路电流上感应,这是通过保持磁饱和点在一个相对于一般电感器或者CT较低的数值上来达到的。首先,图2描述了根据本发明的实施例的制造可分离电磁感应装置的方法。图2是根据本发明的实施例的制造电磁感应装置的方法的流程图。用于制造电磁感应装置的方法(200)包括:切割步骤(S201),切割构成磁芯的钢板;卷绕步骤(S202),以圆形形式卷绕切割的钢板;处理步骤S203),对卷绕的磁芯进行热处理和浸渍;切割步骤(S204),切割经热处理和浸渍的磁芯;以及切割表面处理步骤(S205),对磁芯的切割表面进行抛光。进一步地,首先,如图2所示,切割由轧制的非晶磁性合金制成的钢板(S201),用于制造磁芯。根据本发明的用于发电的电磁感应装置的材料具有最大磁通密度,高谐振频率,低电阻率,低磁芯损耗和不那么高的磁导率。这是因为磁饱和点不需要如上所述那么高,并且考虑了损耗因子和材料加工性。到目前为止还没有材料完全满足这样的条件。由于功率CT的工作频率在50-60Hz的功率频率范围内,所以不着重考虑电阻率指数。与这种条件最接近的材料是硅钢,其是具有低钴含量的金属材料。因此,使用非钴磁性材料或具有最小钴含量的磁性材料(例如硅钢)允许在低功率线路电流中获得高感应功率,并且同时减小磁饱和点。同时,涡流损耗是磁芯损耗的主要因素,但是当使用由具有不高磁导率的硅钢制成的薄钢板并通过轧制技术进行卷绕时,涡流损耗可大大降低。然后,通过轧制技术卷绕切割钢板,以形成圆形磁芯(S202)。在卷绕步骤中,多个芯层120堆叠以形成单个圆形芯。图3是根据图2中的缠绕步骤缠绕的磁芯的透视图。如图3所示,通过轧制技术将宽度为W,厚度为d的芯层110卷绕成总厚度为T。本发明采用轧制技术来卷绕钢板,以便使可能发生在芯层110之间的耦合表面上的气隙120最小化,并降低磁芯的磁导率。也就是说,当通过滚压技术制造圆形磁芯时,可以使芯层110之间的空气间隙12最小化,并且涡流损耗相应地减小,从而可以大大降低性能的劣化,特别是由气隙导致的磁导率的劣化。一般来说,考虑到制造工艺,在一些昂贵且高导磁率的材料中减小气隙是不容易的,因此尽管制造成本高,但是获得的导磁率低于预期,并且性能亦将低于预期。然后,对该圆形磁芯进行热处理和浸渍(S203)。在该步骤中,热处理和浸渍过程可以以任何顺序进行,例如,热处理可以在浸渍过程之后进行或之前进行,或者热处理和浸渍过程可以同时进行。热处理和浸渍的具体条件采用磁芯的一般处理方法,因此这里不进行详细描述。然而,本发明的热处理工艺在该工艺期间不进一步添加钴而进行,并且当通过热处理工艺使钢板本身的电阻含有最少量的钴时,可以保持均匀的密度和非高饱和感应特性。此外,浸渍工艺优选为真空浸渍工艺,并且真空浸渍工艺可以使圆形磁芯的气隙最小化。因此,如图1所示,根据本发明的磁芯与一般的磁芯或电感器相比改善了低功率配电线路电流中的特性,并且可以具有相对较低的饱和特性。然后,将经热处理和浸渍的磁芯切割以形成可分离磁芯(S204)。在该过程中,在与磁芯的卷绕方向正交的方向上切割磁芯。也就是说,在磁芯沿着切割方向和与磁芯100的切割方向正交的方向上被固定的状态下,磁芯被切割成具有半圆形形状。切割工艺是用于制造可分离磁芯的工艺,其可以安装到电源线路或从电源线路移除,而不管电源线路的状态如何,并且参考图4和图5进行详细描述。图4是在切割过程中切割的磁芯的透视图,图5是示出通过切割磁芯而变化的B-H特性的变化的曲线图。如上所述,可通过最小化冷轧磁性合金(例如镍-铁)中的钴含量而不在热处理工艺期间添加钴(Co)成分,以较低成本的方式提供非高饱和感应特性。然而,当切割磁芯以制造可分离磁芯时,由于切割表面之间的间隙而产生磁阻,导致磁通量泄漏。如图4所示,当两个磁芯联接在一起时,可以通过两个磁芯100a和100b的切割表面102之间的切割部分形成间隙。切割表面102之间的这种间隙对应于这样的效果,即,在电力线路中产生的磁场的环路根据尺寸而增加,以呈现与如图5所示的B-H特性的变化那样相同的效果。特别地,低功率线路电流中的特性降低,即,可以降低低功率线路电流中的发电。在本发明的实施例中,在磁芯沿切割方向和与磁芯的切割方向正交的方向上固定的状态下,将磁芯100切割成具有半圆形形状。也就是说,磁芯的切割表面102之间的间隙最小化,使得由间隙引起的磁阻可以减小。因此,可以保持磁芯的良好性能,而无需在间隙中添加另一磁性材料或氧化物,以最小化在切割表面102处泄漏的磁通量(参见图5A)这通过允许磁芯具有低电感而减小磁芯的谐振频率,但是不涉及严重的问题。因为功率CT的操作频率是电源频率,而且通过允许保持磁性物质的固有磁导率而在低功率线路中电流表现出更有效的特性。图6是详细描述切割处理的具体示例。图6是示出用于执行图2所示的切割处理的切割夹具的透视分解图。如图6所示,用于切割磁芯100的夹具通过使用螺栓和螺母40和50将圆形芯10组装并固定在导板30和固定板60之间而固定到基座20的顶表面。当圆形芯10处于如上所述的固定状态时,切割装置,例如插入到用于切割目的的槽30a或60a中的设置在引导板30或固定板60上的诸如电火花机的线路,切割磁芯朝向正交于磁芯的缠绕的方向移动。如上所述,在导向板30和固定板60中形成切割槽30a和60a,此外,分别形成用于安装磁芯的一个表面和另一个表面的其它的槽60b。因此,芯10插入设计成适合于芯的尺寸的安装槽60b中,并且通过诸如螺栓40和螺母50的固定装置组装,使得芯10完全固定在基部20的顶表面上。因为切割夹具被同时固定到X轴(切割方向)和Y轴(与切割方向正交的方向),所以目标芯10被切割成围绕预定中心的完全半圆形形状,以便在切割过程中强制的动力不平衡被最小化,并且可以保护芯部10免于变形。本发明不限于使用图6所示的切割夹具切割芯的方法。优选在切割方向和与切割方向正交的方向上切割磁芯固定的磁芯。再次参考图2,提供冷却剂的同时抛光磁芯100的切割表面102。抛光工艺是用于使磁芯100的切割表面102的间隙最小化以及使磁芯100的耦合表面相等的工艺,并且在磁芯的切割表面102的三维平面被固定以均匀地平整后,通过用磨石磨削切割表面来抛光切割表面102。参考图7更具体地描述这种抛光工艺的具体实例。图7是表示用于进行图2的研磨工序的研磨夹具的动作状态的立体图。如图7所示,用于抛光磁芯100的切割表面102的抛光夹具包括限定水平表面的基板20,安装成接触磁芯10的顶表面和底表面的一对顶部和底部固定板60在与磁芯10的轴线方向正交的方向上延伸,并且被安装为沿着磁芯的轴线方向移动,同时磁芯10的切割表面朝向上方向放置,并且其中固定板、侧板40与磁芯10的侧表面紧密接触并与基板20组装,以保持磁芯10的切割面(11)的水平性;中心板30,其设置在磁芯之间,以与一个磁芯的顶表面和另一磁芯10的底表面紧密接触,并安装在基板20的上表面上。该过程的顺序开始于将中心板30放置在适合于磁芯10的尺寸的位置,并且将穿过调节滑块23的槽22a的调节螺栓23旋拧到中心板30,以固定中心板。当将磁芯10放置在支撑基板21上时,调整侧板40的高度以适应磁芯10的尺寸,并且侧板通过拧紧螺栓25来固定,同时磁芯10的顶表面和底表面与中心板30的指针31接触,并且在支撑基板21上调节磁芯10,以确保磁芯的切割面11设置为平行于侧板40。然后,固定板60的指针61通过转动支撑杆50的手柄52而移动,以与磁芯10的顶表面和底表面紧密接触,以这种方式固定磁芯10。当磁芯10固定时,抛光过程开始。对于抛光工艺,基板20以电子方式或通过夹具固定到抛光装置,而磁芯10处于对夹具的固定状态。在这种状态下,磨石200向下移动以开始如图7所示的抛光过程。本发明不限于使用如图7所示的用于抛光的抛光夹具的方法。但是可以包括任何优选方法,由此在固定状态下抛光磁芯的切割表面使得切割表面的三维平面被均匀地平整。图8是根据比较样品(a)和实施例样品(b)的可分离磁芯的照片。比较例(a)和实施例样品(b)的磁芯通过相同的方法,用具有不同钴组分的不同硅钢板制造。以这种方式制造的磁芯在图8a和8b中示出,并且实施例样品(b)含有的钴量比对比样品(a)少约50%。比较例和实施例之间的输出特性示于图9中。图9是表示图8所示的磁芯的输出特性的比较图。如图9所示,具有低饱和特性的磁性材料制造的磁芯(b)在低功率线路电流中表现出高功率特性,并且由于磁饱和点低,在高电力线路电流中表现出相对低的输出值。该特性可以执行主要作用,以防止功率CT驱动比电子系统所需的更高的无保护功率。表一功率线路电流(毫安)比较例(瓦)实施例(瓦)100.010.23150.861.55202.33.35305.857.07401011.25013.6915.36017.117.7701818.5801920.7+9021231002224.3815026.326.8420027.828.325028.8729.130029.2329.14如图9和表1所示,通过本发明的实施例制造的磁芯与现有情况相比在低功率线路电流中具有更高的功率特性,并且由于其更快地达到磁饱和状态而呈现相对低的输出值。通过这种方法,可以制造具有容易调节的输出功率的高效率可分离电感装置,其具有在低功率线路电流中的高特性和在高功率线路电流中的饱和感应特性。此外,通过这种方法,在现有的磁芯制造过程中制造具有非高饱和特性的可分离电磁感应装置,该非高饱和特性防止发生不规则感应电压,从而向负载侧提供稳定的电力,并且具有可以在热处理工艺中不使用钴的情况下以廉价的成本制造适合于非高饱和特性电源的器件。以上仅为本发明较佳的实施例,并非因此限制本实发明的实施方式及保护范围,对于本领域技术人员而言,应当能够意识到凡运用本实用新型说明书及图示内容所作出的等同替换和显而易见的变化所得到的方案,均应当包含在本发明的保护范围内。当前第1页1 2 3