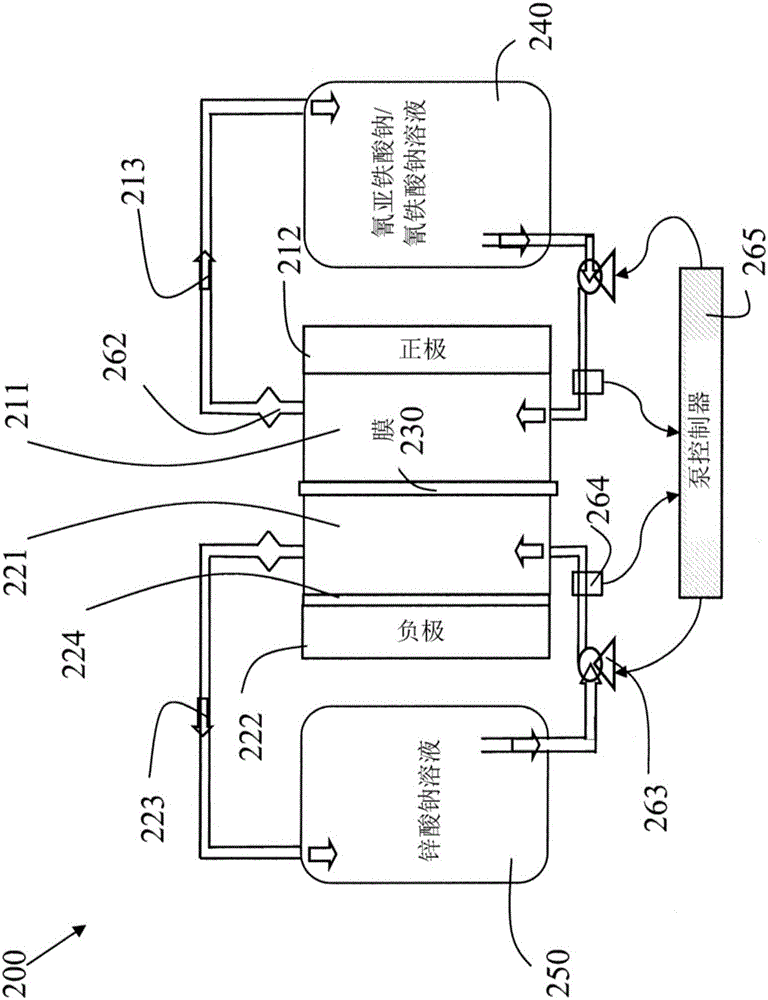
本申请是PCT申请第PCT/US2011/030613号于2012年9月28日进入中国国家阶段得到的、申请号为201180016873.6、申请日为2011年3月30日、发明名称为“高性能液流电池组”的发明专利申请的分案申请。相关申请案的交叉引用本申请案主张在2010年3月30日提交的美国临时申请案第61/319,248号和在2010年4月9日提交的美国临时申请案第61/322,780号的权益,所述美国临时申请案以引用方式全部并入本文。
技术领域:
本发明涉及高性能电化学电池和电池组,并且更特定来说涉及液流电池组。
背景技术:
:能量经济的“绿色化”、可再生能源(诸如,风能和太阳能)不断增长的需求和使用、以及(例如)插入式混合动力车辆和全电力车辆的预期激增日益使配电电网紧张。高容量电能存储技术(诸如,抽送水电技术)可在电网负荷平衡、自产生时间至使用高峰期的时移可再生能源中起着重要作用,然而,地理位置和成本限制所述高容量电能存储技术的使用,尤其是在地区水平上的使用。现有的高容量电池组技术(例如,液流电池组)对于广泛采用来说过于昂贵,因为输送的所得能量和/或功率的有效成本大大高于市场价格。因此存在对于低成本、高容量、高效率和高性能电池组技术的实质上未满足的需要。技术实现要素:本发明的实施例提供高性能液流电池组设备和用于增强、充电、操作和使用液流电池组的方法。本发明的各种实施例提供的高电流密度充电率和放电率处于近似70mA/cm2至400mA/cm2范围内,并且更特定来说处于100mA/cm2至250mA/cm2范围内。本发明的高性能、碱性锌/铁氰化亚铁可充电(“ZnFe”)液流电池组的实施例是基于对于现有技术的许多改善。这些实施例也适用于结合金属电镀来存储能量的其它液流电池组(诸如:ZnHBr;ZnBr;CeZn;和ZnCl)。第一,电池组设计具有电池堆叠,所述电池堆叠包含至少一个正的半电池中的低电阻正极和至少一个负的半电池中的低电阻负极,其中选择正极电阻和负极电阻以获得整个电池堆叠区域上的均匀高电流密度,即,使电极上的电阻足够低以确保整个电极上较小的电压变化,因此均匀电流流出电极之外并在整个电池堆叠上流动。第二,以高水平混合(本文也称为“高速率混合”和“高度混合”)流经接近沉积表面的Zn沉积区域中的至少一个负的半电池的电解液流(例如,ZnFe电池组中的锌物种),其中接近于沉积表面的电解液具有足够高的锌浓度,以在沉积表面上获得维持均匀高电流密度的沉积速率。负的半电池中电解液流和液流的混合经设计以提供足以支持高电流密度的传质系数并提供(例如)锌在电池的沉积表面上的实质上均匀沉积。此外,一些实施例已将液流设计成以小于极限电流的电流提供锌沉积,其中所沉积的锌具有密集、附着的非枝状形态。第三,锌电解液具有高浓度,并且在一些实施例中,锌电解液的浓度大于平衡饱和浓度,即,锌电解液的Zn离子超饱和。本发明的不同实施例组合这些改善中的一或更多个改善。高度混合流经电池的电解液流可能是由于平行板通道中较高的流体速度造成的。然而,液流中的混合可由诸如以下的结构诱导:导电网孔和非导电网孔;筛网;带;泡沫结构;圆锥体、圆柱体或角锥体的阵列;和线或管子的其它布置,上述结构可单独使用或与平坦电极表面组合使用。这类结构的使用可允许具有层流或具有湍流的电解液以较高的或较低的流体速度高度混合。此外,用于使湍流平静的结构可包括在紧接在电池之后的电解液流体管路中。根据本发明的实施例,用于操作液流电池组的方法可包括使以层流态或湍流态高度混合的电解液流经接近沉积表面的Zn沉积区域中的至少一个负的半电池。此外,一些实施例包括沉积具有密集、附着的非枝状形态的Zn。可在电池组电池的充电和/或放电期间利用高度混合液流。附图说明在结合附图审阅本发明的特定实施例的以下描述之后,本领域的一般技术人员将更加明白本发明的这些和其它方面和特征,其中:图1为锌氧化还原液流电池组的示意图;图2为根据本发明的一些实施例的锌氧化还原液流电池组的示意图;图3为根据本发明的一些实施例的液流电池的示意性透视图;图4为根据本发明的一些实施例,含在框架内的图3的电池的示意性透视图;图5为根据本发明的一些实施例,氧化还原液流电池组的电池配置的第一实例的示意性横截面图;图6为根据本发明的一些实施例,氧化还原液流电池组的电池配置的第二实例的示意性横截面图;图7为根据本发明的一些实施例,氧化还原液流电池组的电池配置的第三实例的示意性横截面图;图8为根据本发明的一些实施例,液流电池组电极的表面上的混合诱导编织线网孔特征的实例;图9为根据本发明的一些实施例,液流电池组电极的表面上的混合诱导非编织线网孔特征的实例;图10为根据本发明的一些实施例,液流电池组电极的表面上的混合诱导线/管子特征的实例;图11为根据本发明的一些实施例,液流电池组电极的表面上的混合诱导圆柱体阵列的实例;图12为根据本发明的一些实施例,液流电池组电极的表面上的混合诱导圆锥体阵列的实例;图13为根据本发明的一些实施例,液流电池组电极的表面上的混合诱导角锥体阵列的实例;和图14为根据本发明的一些实施例的液流层化特征的横截面图。具体实施方式现在将参照诸图详细描述本发明的实施例,所述图提供为本发明的一些实施例的说明性实例,以便使本领域的技术人员能够实践本发明。值得注意的,下文的图和实例并不意味着将本发明的范畴限于单个实施例,而是以互换所描述或图示元件中的一些或全部元件的方式的其它实施例是有可能的。此外,在可部分地或完全地使用已知组件来实施本发明的某些元件的情况下,将仅描述理解本发明所必需的这类已知组件的那些部分,并且将省略这类已知组件的其它部分的详细描述,以免使本发明模糊。在本说明书中,显示单个组件的实施例不应视为限制性的;相反地,本发明旨在涵盖包括多个相同组件的其它实施例,反之亦然,除非本文明确地表示并非如此。此外,除非同样地明确阐述,否则申请者并不旨在对说明书或权利要求书中的任何术语赋予不常见的或特殊的意义。此外,本发明涵盖现在和将来已知的等效物,所述等效物等效于本文以说明方式提及的已知组件。本发明的实施例提供高性能液流电池组设备和用于增强、充电、操作和使用液流电池组的方法。图1图示现有技术氧化还原液流电池组100的实例。例如,参见Wu等人的IndianJournalofTechnology,第24卷,1986年7月,第372-380页。液流电池组包含正的半电池110和负的半电池120,正的半电池110和负的半电池120分别由隔膜130分隔。半电池的电解液存储于槽140和槽150中并抽送通过半电池,如通过箭头所示。图1中所示的液流电池组为Zn/Fe氧化还原液流电池组;正极电解液为Fe复合物,并且负极电解液为锌酸盐。然而,现有技术液流电池组不能以足够高的电流密度操作并且效率不足够高来经济上可行地用于大规模能量存储。本发明提供对于液流电池组的改善,所述改善将允许低成本但具有高效率的高电流密度操作。例如,本发明的一些实施例将提供氧化还原液流电池组,所述氧化还原液流电池组的充电电流密度为70mA/cm2、80mA/cm2、90mA/cm2、100mA/cm2、125mA/cm2、150mA/cm2、200mA/cm2和甚至更高。本发明的一些实施例的碱性锌/铁氰化亚铁(“ZnFe”)可充电电池组系统旨在用于公用供电设施负荷平衡、负荷跟踪、区域调节服务、输配电延期应用、风能和太阳能整合应用等兆瓦特能量存储应用,所述应用的能量存储容量自数分钟(诸如,15分钟)至高达24小时持续时间和超过24小时持续时间。ZnFe电池组为混合氧化还原液流电池组,其中活性物质(氧化锌和氰亚铁酸钠)作为氢氧化钠电解液中的饱和溶液存储于电池外部的储存槽中并被送到电化学反应的位点。在充电期间,能量以沉积于锌电极基板上的锌金属的形式存储并存储为通过氰亚铁酸盐反应物的阳极氧化形成的氰铁酸盐。当负荷需要要求时,可通过阳极溶解锌以形成氧化锌同时将氰铁酸盐离子还原成氰亚铁酸盐,而自电池吸取能量。这些过程高度可逆并具选择性,从而使电池的操作具有以下优点:高循环效率、高电池电压、自负荷至隔离或自隔离至满负荷小于5ms的随机循环时间和切换时间。尤其当充电(沉积)期间的操作电流密度增加时,现有技术液流电池组,尤其是基于Zn的液流电池组具有枝状晶体生长的问题。例如,锌枝状晶体可能在沉积(充电)过程期间在基于锌的电池组中由于各种原因形成。锌枝状晶体可能在基于锌的电池组中产生问题,所述问题包括性能降低、电池短路和操作寿命减少,所有所述问题会增加有效操作成本。本发明的实施例将通过增加用于给电池充电和放电的可维持的操作电流密度,减少或最小化枝状晶体的生长,来提高锌液流电池组和其它液流电池组的性能(从而降低操作成本)。对于给定的液流电池组额定功率,本发明的尤其用于电网存储器应用的液流电池组实施例一般将具有近似处于自20kW至25MW和更大的范围内的功率输出和近似处于5kWh至600MWh范围内的能量输出或自5分钟至15分钟至24小时内的放电持续时间,但可使用更高和更低的功率输出和能量输出。大体充电时间和放电时间由特定液流电池组产品的市场应用界定。典型的放电时间为15分钟、1小时、2小时、4小时、8小时、12小时、16小时和24小时。充电时间与放电时间的比率一般处于2比1或1比1或1比2的范围内,其中近似1比1的充电与放电比率较为理想。本发明的高性能液流电池组(例如,ZnFe液流电池组)的实施例基于对于现有技术的许多改善,所述改善将允许以高电流密度操作和/或降低电池组整体操作成本。第一,电池组设计具有电池,所述电池包含至少一个正的半电池中的低电阻正极和至少一个负的半电池中的低电阻负极,其中选择正极电阻和负极电阻以获得电池堆叠区域上的均匀高电流密度,即,使电极上的电阻足够低以确保电极上较小的电压变化,因此均匀电流流出电极之外并在电池的至少一个区域上流动(例如,电压变化通常小于5mV至10mV,其中电池上的电阻在操作电流密度100mA/cm2下产生小于200mV的损失,对应于电流密度变化小于20%)。电池通常一起串联装配成电池堆叠,所述电池堆叠包括多个电池。电池堆叠中的电池之间的电气连接可呈双极电极或其它电极设计的形式,所述其它电极设计包括使用导线将电池串联和/或并联连接在一起,以制得电池堆叠。通常组合多个电池堆叠来制得电池组系统。第二,高速率混合的电解液(例如,ZnFe电池组中的锌物种)的流动速率通过接近沉积表面的Zn沉积区域中的至少一个负的半电池来诱导,其中电解液溶液具有足够高的锌浓度,以在沉积表面上获得维持电池上或电池堆叠中的实质上全部电池上的均匀高电流密度的沉积速率。负的半电池中的液流经设计以提供锌在沉积表面上的实质上均匀沉积。此外,一些实施例将液流设计成提供锌沉积,其中锌具有密集、附着的非枝状形态。液流可用混合元件层化,或可通过较高速度下的湍流或较低速度下的湍流,用向电池的流动通道添加的湍动元件实现混合。第三,锌电解液具有高浓度,并且在一些实施例中,锌电解液的浓度大于平衡饱和浓度,即,锌电解液的锌离子超饱和。本发明的不同实施例组合这些改善中的一或更多个改善。液流电池组操作电流密度为活性离子物种的浓度的函数。本发明的一些实施例提供超饱和电解液,以增加尤其在充电期间的离子浓度。可通过化学途径或电化学途径配制具有超饱和锌(Zn)离子的锌酸盐电解液。例如,可配制锌酸盐电解液具有近似~1摩尔至~1.9摩尔的锌离子,所述锌酸盐电解液保持稳定超过一天。参见Dirkse,JournaloftheElectrochemicalSociety,第128卷(第7号),1987年7月,第1412-1415页;Dirkse,JournaloftheElectrochemicalSociety,第134卷(第1号),1987年1月,第11-13页;和Debiemme-Chouvy&Vedel,JournaloftheElectrochemicalSociety,第138卷(第9号),1991年9月,第2538-2542页。应注意,可允许电解液中具有锌酸盐粒子,条件是粒度相对于电解液通道(即,电池的流动通道)的尺寸较小。此外,用于ZnFe液流电池组的电解液化学组成具有提供碱性(高pH)电解液的附加优点,所述碱性电解液化学组成比许多更具酸性的替代性电解液化学组成腐蚀性更小。碱性化学组成有利于液流电池组的组件的初始成本和寿命,所述组件诸如,用以输送电解液流往返于液流电池组的电池堆叠的管道装置和泵。电池沉积表面上和通过电池堆叠的高操作电流密度降低了电池组的每单位功率有效成本或能量输出并降低了整体操作成本。本发明的实施例将通过确保尤其在充电(沉积)期间避免或最小化枝状晶体生长,来提供可维持的较高操作电流密度。通过确保电池中的沉积表面上大体均匀的操作电流密度,并通过确保在电池沉积表面处或接近于电池沉积表面处的可用电解液中始终存在充分的、大体均匀和高浓度的离子,将避免或最小化枝状晶体生长,其中离子浓度与高操作电流密度一致并且足够或大于维持通过一或更多个沉积表面的电流密度所需要的浓度。在未充分混合的情况下,电解液的层流流经电池流动通道的高电流密度操作导致沉积表面处或接近于沉积表面处的扩散边界层中的离子浓度降低,所述离子浓度降低导致不均匀沉积和枝状晶体生长。以导致流经电池流动通道的电解液流中的混合(通过层流或者湍流)的电解液流流态操作电池,会增加传质系数并减小沉积表面处的扩散边界层厚度,所述传质系数增加和扩散边界层厚度减小又增加了用于沉积的离子的可得性。离子(例如,ZnFe电池组中锌酸盐中的锌离子浓度)的高可得性允许较高电流密度操作,而不会显著地耗尽一或更多个电池沉积表面的均匀区域中的电解液浓度,并因此几乎没有或没有枝状晶体生长。电解液中增加的锌酸盐离子浓度与沉积表面附近的电池流动通道中电解液的增加的混合两者(两者都相对于现有技术电池)的组合将减少或消除枝状晶体的形成。这样将允许可维持的增加的高电流密度操作并将产生较小尺寸的电池、较小的整体电池堆叠和较小的整体模组,因此将降低给定功率和/或电流输出的电池、堆叠和模组成本和整体操作成本。这些所得能力将提供更经济的电池组系统并将降低电池组系统的能量和功率输出的整体成本。通过设计电解液流和电池流动通道几何结构以产生足够的混合或湍动而减小沉积表面处的扩散边界层厚度,来增强电池性能。下文表1和表2显示根据本发明的实施例的电池流动通道中的液流的高操作电流密度以及相关联的平均传质系数(km)估计的说明性值。传质系数与传到电极表面的传质速率(mol/cm2.s)和本体溶液与电极表面处之间的浓度差(mol/cm3)有关。还可依据舍伍德(Sherwood)数或平均舍伍德数(Shm)来描述用于增加操作电流密度的电池流动通道中的混合,所述舍伍德数或平均舍伍德数定义为无因次传质系数,也定义为电解液中对流传送与扩散传送的离子的比率。应注意,基于流经3D湍流结构的液流的相关性计算下文表中舍伍德数的实例;然而,可在本发明的精神和范畴内使用其它计算方法。iL为极限电流密度,即电极表面(或电极固体界面)处零离子浓度下的以mA/cm2计的电流密度。iapp为有利的电池操作电流密度,出于表1中实例的目的定义为以mA/cm2计iL的近似~2/3倍(但本领域的技术人员应认识到,可在本发明的各种实施例的精神和范畴内使用其它值或定义)。v为流经电池流动通道的电解液的以cm/s计的平均流速。Cb为本体溶液浓度,即扩散边界层外部的活性离子浓度,以mol/l计。下文表1和表2也提供这些参数的说明性实例。尽管本领域的技术人员对这些参数和术语熟悉,但额外细节可见于书中,所述书诸如,L.GaryLeal的“AdvancedTransportPhenomenon:FluidMechanicsandConvectiveTransport”,第9章,由剑桥大学出版社出版于2007年,和WarrenL.McCabe、JulianC.Smith和PeterHarriot的“UnitOperationsofChemicalEngineering”,第21章,由McGrawHillInc出版(第V版,1993年)。iapp(mA/cm2)70100150200250400Cb(mol/L)0.250.250.250.250.250.25iL(mA/cm2)105150225300375600km(cm/s)2.3×10-33.1×10-34.6×10-36.2×10-37.8×10-312.4×10-3Shm6486129172215342表1.操作范围实例,其中Cb=0.25(mol/L)iapp(mA/cm2)70100150200250400Cb(mol/L)1.01.01.01.01.01.0iL(mA/cm2)105150225300375600km(cm/s)5.3×10-47.7×10-41.2×10-31.5×10-31.9×10-33×10-3Shm162132435486表2.操作范围实例,其中Cb=1(mol/L)对于处于70mA/cm2至400mA/cm2的近似范围内的电池操作来说,理想的传质系数介于近似5×10-4cm/s与1.24×10-2cm/s之间。对于处于70mA/cm2至400mA/cm2的近似范围内的电池操作来说,理想的平均舍伍德数介于近似15与350之间。表3中显示以下高电流密度的8小时充电操作的一或更多个电池沉积表面上的经计算的锌沉积厚度。电流密度(mA/cm2)100200400沉积物厚度(cm)0.170.340.68沉积物容量(mAh/cm2)8001,6003,200沉积物质量(g/cm2)0.9761.9513.902表3.8小时充电的近似锌沉积厚度应注意,这些厚度数字与电流密度和时间线性地成比例。例如,对于电流密度100mA/cm2,计算出生长速率近似0.21毫米/小时;对于电流密度200mA/cm2,计算出生长速率近似0.43毫米/小时;和对于电流密度400mA/cm2,计算出生长速率近似0.85毫米/小时。尽管本文提供的实例为ZnFe氧化还原液流电池组,但可使用本发明的教导和原理来制造其它氧化还原液流电池组。例如,可制造以下电池组:ZnHBr;ZnBr;CeZn;和ZnCl。图2图示根据本发明的一些实施例的液流电池组200的示意图。图2为ZnFe液流电池组的实例。液流电池组200具有正极212、负极222和膜210,负极222的表面上存在镀锌区域224,膜210分隔正极通道211与负极通道221。分别针对正极电解液管路和负极电解液管路,用箭头213和箭头223指示流经电池中分隔通道的电解液流和流经其余流体管路的电解液流。每一流体管路包括电池通道(211和221)、可选的液流平静特征262(诸如,图14中所示的液流平静特征)、电解液储存槽(240和250,电解液储存槽240在这个实例中含有正极电解液氰亚铁酸钠/氰铁酸钠溶液,电解液储存槽250在这种情况下含有负极电解液锌酸钠溶液)、泵263和一或更多个流量传感器264。泵263、传感器264和泵控制器265经配置以控制通过电池的电解液的流动,包括控制电池中的流态,即,流态可为贯穿本申请案描述的层流、混合流和/或湍流。通过计算电池通道体积、电解液流的速率和期望在电池出口腔室处的锌酸盐耗尽的量,来确定通过电化学电池每一侧抽送的电解液的量,其中考虑了能量存储持续时间和界定电解液存储槽尺寸的管道体积和管道段长度。针对每电池堆叠给定量的电解液,取决于用于电化学电池的电解液的性质,使用在强碱(例如,2至5NNaOH)或强酸条件下具有耐久性和长寿命的构造材料来选择泵尺寸。通常,对每一电池堆叠选择两个泵,每一电解液对应一个泵。构造的大体可接受材料包括聚丙烯、聚乙烯、氟化聚合物、聚醚酮、聚砜、聚苯硫醚等。各种传感器经选择以在存储槽、管道、泵、电池通道的入口点和出口点中的各个位置处测量流体速度、流体流动的方向、温度、压力和其它度量。来自每一传感器的各个数据信号通过信号线或通过无线传输器传输至数据控制系统。数据控制系统记录数据流并使用算法、设定点和控制输入,以将数据信号发送至风扇(在需要时用于冷却)、阀和发动机,以按照命令控制(例如,增加、减小或保持)发动机速度和阀位置,进而增加、减小、保持恒定或改变流体方向。数据控制系统可在某些条件下将警报信号和其它性能数据发送至远距离定位的控制室。往返于电池通道的管道经设计并经设计尺寸以最小化分路电流损失,并且取决于电解液的性质,针对在强碱或强酸条件下的耐久性选择构造的材料。电化学系统大体位于流体容纳系统内部,所述流体容纳系统包含适当的传感器和警报器,以指示任何电解液泄漏。图3图示电池300的示意性透视图。例如,电池300可为大致0.5cm厚,其中较大尺寸为大致30cm×30cm至高达132cm×67cm。在图7中图示截面X-X的横截面图。图3图示在两侧具有双极结构元件的电池300。电池具有正极通道211和负极通道221,正极通道211与负极通道221通过膜230分隔。通过负极通道抽送负极电解液,并且通过正极通道抽送正极电解液,如图所示;分别通过箭头213和箭头223显示正极电解液流体流和负极电解液流体流。上文参照图7提供电池的进一步细节。图4图示框架410中的图3的电池300。电池300由框架410围绕,框架410用来将膜(隔膜)和双极结构元件固定在适当位置,从而产生流动通道、密封流动通道的边缘、提供附接电解液流和回管的位置,并且电池300可选地可含有电解液分配岐管和液流平静特征。向电池300提供的进出框架的正极电解液流和负极电解液流分别通过箭头213和箭头223来指示。在图5至图7中提供根据本发明的一些实施例的电池的更详细的实例。例如,电池的大尺寸可为30cm×30cm、90cm×90cm、60cm×90cm、45cm×90cm或132cm×67cm。在图5至图7中提供电池的组件的横截面尺寸的实例。然而,本发明不限于这些电池尺寸,并且本发明可用于更小或更大尺寸的电池。以横截面图示电池,并且截面垂直于电池的较大表面。(例如,参见图3中的截面X-X。)功率密度为电池化学组成和电池电流密度的函数。例如,对于200mA/cm2下的ZnFe,放电功率密度为约0.3W/cm2。对于上文列出的电池尺寸,每电池所得功率将分别为近似274W、2.43kW、1.60kW、1.22kW和2.45kW。图5图示本发明的双极ZnFe氧化还原液流电池组电池的示意性横截面的第一实例。图示单个电池组电池,所述单个电池组电池包含负的半电池220、正的半电池210和双极结构元件270。双极结构元件270分隔相邻电池的正的半电池与负的半电池。(参见图6。)这个实例中的双极结构元件270为50%石墨纤维/PPS互连器,在所述互连器上存在镉金属发条(strike)271。(PPS为聚苯硫醚。可使用与导电填料组合的其它聚合物材料来代替双极结构元件的构造中的PPS,所述其它聚合物材料诸如,聚醚酮、聚砜、聚乙烯、聚丙烯等,所述导电填料诸如,石墨纤维或薄片、某些碳粉和碳黑、碳纳米管、导电金属粉末等。)正的半电池210包含多孔Ni网孔氧化还原电极,所述多孔Ni网孔氧化还原电极完全填充正极通道211,即,正极电解液流经多孔Ni网孔氧化还原电极。负的半电池220包括Cd金属发条271上的可变厚度的镀Zn区域224和负极电解液流动通道221。单独电池的正的半电池和负的半电池通过膜230与彼此分隔,膜230由诸如Nafion-114的材料或另一种隔膜材料制成。膜230保持锌酸盐与铁电解质分隔,但Na离子和水能够移动穿过膜。膜材料可为具有或不具有接枝离子化学物种的隔膜材料。为了以高电流密度(例如,充电电流密度200mA/cm2)操作图5的双极电池,在负极流动区域中产生较高传质速率。可通过将混合速率增加至现有技术电池的混合速率以上和/或通过将电解液流体流动速率增加至现有技术电池的电解液流体流动速率以上,来实现这一结果。可通过向电池通道添加混合元件、或通过增加速度而不达到湍流态、或通过增加速度直至实现湍流为止、或通过引入下文论述的湍动产生元件,来执行这一操作。应注意,锌沉积电流密度为流体(电解液)速度和雷诺数的函数。参见R.D.Naybour的“TheEffectofElectrolyteFlowontheMorphologyofZincElectrodepositedfromAqueousAlkalineSolutionContainingZincateIons”,J.Eletrochem.Soc.,第520-525页,1969年4月。应注意,沉积操作电流密度也为活性物种的浓度的函数。图6图示双极ZnFe氧化还原液流电池组电池的示意性横截面的第二实例。正极612包含多孔Ni网孔氧化还原电极,所述多孔Ni网孔氧化还原电极附接至双极Ni/Cu电极272,即,Ni网孔附接至双极电极的Ni面。正极电解液流动区域被多孔Ni网孔占据。负极622可包含涂覆Cd、Sn或Pb的高表面区域Cu或Ni网孔,所述高表面区域Cu或Ni网孔的孔隙率为(例如)60%至98%。被涂覆的Cu或Ni网孔附接至双极电极272的Cu面。被涂覆的Cu或Ni网孔占据负极电解液流动区域,并且网孔产生负极电解液流中的混合,而不需要较高流体速度。电池设置成使得被涂覆的Cu或Ni网孔可电镀有高达近似20%至70%体积的Zn。图6也图示双极电极272(或图5的双极结构元件270)如何分隔电池与相邻电池并有助于电池堆叠的有效率的和有成本效益的构造。在图6中图示相邻电池。图7图示双极ZnFe氧化还原液流电池组电池的示意性横截面的第三实例。(图7为图3中的截面X-X。)正极通道211包含多孔Ni网孔氧化还原电极,所述多孔Ni网孔氧化还原电极附接至双极Ni/Cu电极272,即,Ni网孔附接至双极电极的Ni面。正极电解液流动区域被多孔Ni网孔占据。负极通道221包括锌金属电镀区域224和特征280,特征280经配置以诱导高效的混合或湍动。特征280的实例图示于图8至图13中且在下文描述。(应注意,特征280可定位于沉积表面上方的流动通道中,如图7中所示,或在其它实施例中,特征280可直接定位于沉积表面上,如图11至图13中所示,而图8至图10图示可定位于沉积表面上或者沉积表面上方的结构。)这些特征经设计以产生液流的高速率混合,同时不一定需要高速度(因此会导致较高的抽送功率耗散)。将Zn金属电镀于双极电极272的Cu面上。Cu面可能替代性地还涂覆有Cd、Sn或Pb。应注意,图11至图13中所示的圆柱体、圆锥体和角锥体将由非导电材料制成并图示为具有尖锐的边缘和点。然而,如果希望由导电材料制成圆柱体、圆锥体和角锥体,那么所述圆柱体、圆锥体和角锥体应具有较钝的边缘和末端而非尖锐的边缘和点。(应注意,为了改善Zn电镀的均匀性,如果用以诱导混合和/或湍动的特征为导电的,则所述特征不应具有尖锐的点或边缘,尖锐的点和边缘为电场集中器并导致不理想的不均匀电镀并且甚至导致枝状晶体形成。)此外,特征不应占据过大体积而使得流经阳极通道的液流受到不适当的阻碍——参见下文以获得进一步细节。应注意,可针对特定通道几何结构,通过使用(例如)雷诺数方便地定义诱导湍流的条件。本领域的技术人员熟悉雷诺数的计算,包括针对含有特征(诸如,图8至图13中所示的那些特征)的通道的雷诺数的计算。大致上,对于图7中所示的具有实质上矩形通道的电池,至少近似大于1,300或优选为2,000的雷诺数可用以确保湍流,其中通过水力直径界定特征长度。较窄流动通道(L>>W)的水力直径为通道厚度的两倍,即2W,其中L和W为垂直于流体流动方向测量的流动通道的长度和宽度。(参见图3。)对于图7中所示的包含图8至图13中所示特征的电池,较低的雷诺数可足以确保有效率的混合或高速率混合,例如,至少近似8或更大的雷诺数可足以确保有效率的混合。然而,特定的雷诺数将随电池和流动通道设计和混合特征而变化。图8图示适合于在液流电池组电极表面上诱导电解液流中的混合或湍动的结构的实例。小区段的编织线网孔820图示为在电极810表面的一部分上。电解液流动方向通过箭头来指示;流动大体平行于电极810的表面。线网孔820中断流体流动,从而在电极表面上诱导层流、半湍流或者湍流中的所需混合。应注意,也可通过使网孔接近于电极810的表面而不一定在电极810的表面上,来实现类似效果。适合的线直径将介于通道厚度的20%与50%之间。在一些实施例中,线网孔为导电的并充当电极表面的一部分,从而增加总的电极表面面积(除充当混合元件的网孔之外)。在其它实施例中,网孔为非导电的并在平坦电极表面上混合液流。当非导电网孔夹在电极与膜之间时,非导电网孔还可用以确保指定的电极与膜间隔。在其它实施例中,可能存在若干层网孔,一些为导电的,并且一些为非导电的。在一个这类实例中,导电网孔邻近于电极,并且非导电网孔介于导电网孔与膜之间。非导电网孔充当间隔物以保持电镀表面远离膜,以及充当液流混合结构。非导电网孔可由塑料或其它非导电材料或低电导率材料制成。在进一步实施例中,可能存在具有变化的电导率的一系列相邻网孔。这种结构将确定局部电场,所述局部电场控制局部电流分配,因此控制电镀均匀性。图9图示适合于诱导层流电解液流或湍流电解液流中的混合的另一结构。小区段的非编织线网孔830图示为在电极810表面的一部分上。电解液流动方向通过箭头来指示;流动大体平行于电极810的表面。线网孔830中断流体流动,从而在电极表面上诱导层流或湍流中的所需混合。应注意,也可通过使网孔接近于电极810的表面而不一定在电极810的表面上,来实现类似效果。适合的线直径将介于通道厚度的10%与50%之间。在一些实施例中,可在电池通道上堆叠或间隔设置多个线,以进一步增强性能。图10图示适合于诱导层流电解液流或湍流电解液流中的混合的又一结构。平行线/管子840图示为在电极810表面的一部分上。电解液流动方向通过箭头来指示;流动大体平行于电极810的表面并垂直于线/管子的长轴。线/管子840中断流体流动,从而在电极表面上诱导理想的湍流(非层流)。应注意,也可通过使线/管子接近于电极810的表面而不一定在电极810的表面上,来实现类似效果。适合的线直径将介于通道厚度的10%与90%之间。图11图示用于诱导层流电解液流或湍流电解液流中的混合的特征阵列的一部分。圆柱体阵列850图示为在电极810表面的一部分上。电解液流动方向通过箭头来指示;流动大体平行于电极810的表面。圆柱体阵列850中断流体流动,从而在电极表面上诱导液流中的所需混合。所图示的圆柱体由非导电材料形成并且可具有尖锐的边缘。适合的圆柱体高度介于通道厚度的20%与100%之间。间隔和直径必须达到产生期望流动速率下的湍动的程度。图12图示用于诱导层流电解液流或湍流电解液流中的混合的另一特征阵列的一部分。圆锥体(或锥形圆柱体)阵列860图示为在电极810表面的一部分上。电解液流动方向通过箭头来指示;流动大体平行于电极810的表面。圆锥体阵列860中断流体流动,从而在电极表面上诱导层流或湍流中的理想混合。所图示的锥形圆柱体由非导电材料形成并且可具有尖锐的点。适合的圆柱体高度介于通道厚度的20%与100%之间。间隔和直径必须达到产生混合,同时不会随着Zn沉积物厚度增加时通道厚度的减小而不适当地增加流动阻力的程度。图13图示用于诱导电解液流中的混合的又一特征阵列的一部分。这是为了说明除圆柱体之外的形状也是适合的。角锥体阵列870图示为在电极810表面的一部分上。电解液流动方向通过箭头来指示;流动大体平行于电极810的表面。角锥体阵列870中断流体流动,从而在电极表面上诱导液流的所需混合。所图示的锥形特征由非导电材料形成并且可具有尖锐的边缘,并且所图示的锥形特征可具有其它横截面,例如,三角形的、其它多边形的或椭圆形的横截面。适合的特征高度介于通道厚度的20%与100%之间。间隔和直径必须达到产生期望流动速率下的混合的程度。锥形可经选择以维持高速率的混合,同时不会随着Zn沉积物厚度增加时通道厚度的减小而不适当地增加流动阻力。图8至图13提供可用以在电极表面上诱导电解液流中混合的特征的实例的范围。然而,这些实例并不旨在成为全面的清单,并且本领域的技术人员在阅读本揭示案之后将更加明白适合于诱导层流和/或湍流中混合的进一步特征。例如,进一步特征可包括:上文描述的特征的组合;导电网孔和非导电网孔;带;泡沫结构;和线或管子的其它布置。图11至图13中所示的阵列图示为特征的规则阵列;然而,这些阵列也可具有随机定位的特征或部分随机定位的特征。图8至图13的特征图示为在液流电池组电极的表面上。然而,这类特征可刚好在电解液在整个电极上流动之前替代性地或另外地位于电解液流中;所述特征可附接(例如)至将电解液输送至半电池中的管道装置的内表面。在商业液流电池组操作中,抽送系统所消耗的功率为最佳化电池组系统的整体生产率的重要因素。尽管较高的流体抽送速率诱导电池中较高混合程度,但较高的流体抽送速率还需要更多抽送功率,所述更多抽送功率最终减损电池组系统所输送的功率和能量。较高抽送速率还引起较高磨损,因此引起较频繁的预防性维护。在电池组设计中,可权衡考虑泵功率、混合和湍动。在电池内部与外部并流经管往返于电池的层流大体降低抽送功率要求。当以用于在电池的流动通道中混合电解液的湍动操作时,可(例如)通过允许较低速度区域来使湍动骤减,在所述较低速度区域中,(例如)使用诸如图示于图14中的结构来减小流速并恢复层流。确保电池的任何有意湍流区域外部的液流为层流或实质上层流减小了泵功率消耗。图14图示经修改的管在半电池的出口处的横截面,所述管经设计以在电解液移动穿过管道装置其余部分时使湍流平静并提供层流。湍动流动的电解液自半电池流动至管的第一段1410中。电解液随后进入管的第二段1420,在管的第二段1420中,管的横截面增加。随着管1420横截面增加,电解液的速度减小,并且湍流平静,从而产生层流。层流流动的电解液随后进入管的第三区段1430,在管的第三区段1430中,管的横截面减小,以便将平静后的电解液通过漏斗送至管道装置1440中,管道装置1440延续电解液管路。电解液流动的方向通过箭头来指示。可使流经电池流动通道的电解液流反向以改善混合、沉积的均匀性并避免耗尽沉积表面处的电解液。支架可用以支撑流动通道中的网孔(或筛网)混合元件,以避免所述网孔接触膜或电极并大体避免网孔由于高流动速率、湍动或温度变化而弯曲或屈曲。本领域的技术人员应知道湍动的许多定义和度量。在这种情境中的湍动大体意味着流速的变化(速度为矢量,并且变化包括速度的变化与流动方向的变化两者),所述流速的变化包括引起电解液流的混合,以避免在沉积(充电)期间耗尽或在放电期间移除沉积表面处或接近于沉积表面处的经沉积离子。在充电期间电池的沉积表面上实质上均匀沉积的定义意味着在充电期间沉积时未形成或较少形成枝状晶体。本领域的技术人员应认识到,沉积表面上和电池上(可能小于20%)沉积厚度的一些变化是固有的,尤其在以高电流密度和以电解液中高浓度的离子操作时。高速率的混合大体意味着层流或湍流中的混合,以避免或最小化尤其在沉积表面处或接近于沉积表面处的电镀离子耗尽。可如下实现用于各种实施例的高速率混合:(1)用通道和偏离沉积表面的混合装置;(2)用通道和沉积表面上的混合装置;(3)用通道和沉积表面上的混合装置与偏离沉积表面的混合装置两者;或(4)用通道、混合装置和较高的电解液速度。第一,在混合元件或装置位于距电极沉积表面的距离为扩散边界层厚度的至少近似两倍处,并且混合元件或装置的横截面面积为电池通道横截面面积的近似10%至80%,理想地自近似25%至60%时,可实现高速率的混合;或在混合装置位于距电极沉积表面的距离为至少近似125微米处,并且混合装置的横截面面积为电池通道横截面面积的近似10%至80%,优选为近似25%至60%时,可实现高速率的混合;或在混合元件或装置位于距电极沉积表面的距离为扩散边界层厚度的至少近似两倍处,并且混合元件或装置的横截面面积为电池通道横截面面积的近似10%至80%,优选为近似25%至60%,其中混合装置在电池通道宽度上和沿着电池通道长度具有重复特征(或近似重复特征)时,可实现高速率的混合;或在混合元件或装置位于距电极沉积表面的距离为扩散边界层厚度的至少近似两倍处,并且混合元件或装置的横截面面积为电池通道横截面面积的近似10%至80%,优选为近似25%至60%,其中混合装置在电池通道宽度上和沿着电池通道长度具有重复特征(或近似重复特征),并且沿着电池通道长度的重复特征的间距为通道宽度上的重复特征的间距的至少近似1.1倍时,可实现高速率的混合。第二,在一或更多个混合元件或装置附接至电极沉积表面,并且混合装置前边缘重复距离的比率为距电极沉积表面的混合装置高度的至少近似五倍,并且混合装置的形状可选自包含以下的群组:线、网孔、筛网、半球形、圆形、半圆形或矩形形状或其它形状或上述的组合时,可实现高速率的混合。第三,在一或更多个混合元件或装置附接至电极沉积表面,结合上位于距电极沉积表面的距离为扩散边界层厚度的至少近似两倍处的第二混合装置,并且第二混合装置的横截面面积为电池通道横截面面积的近似10%至80%,优选为近似25%至60%时,可实现良好速率的混合。第四,在混合元件或装置位于距电极沉积表面的距离为扩散边界层厚度的至少近似两倍处,并且混合元件或装置的横截面面积为电池通道横截面面积的近似10%至80%,优选为近似25%至60%,并且电解液流体速度为至少近似5cm/s,优选为至少近似25cm/s,并更优选为至少近似50cm/s时,可实现高速率的混合。在一些应用中,液流电池组(诸如,本发明的一些实施例)可用于频率调节。此外,本发明的一些实施例可用于其它较短持续时间功率需要(诸如,UPS(不可中断电力系统))或较短响应功率备用。对于较短持续时间功率需要,本发明的液流电池组的一些实施例可在较高的充电电流密度和放电电流密度(诸如,大于大致200mA/cm2)下操作。在其它实施例中,液流电池组可包括以下中的一或更多者:流动通道的雷诺数近似大于1300;流动通道的舍伍德数近似大于21;均匀的高电流密度>100mA/cm2;在流动通道中存在至少一个混合元件;在流动通道中存在至少一个湍动诱导元件;传质系数近似大于7.7×10-4m/s;和充电周期为至少5分钟的持续时间或为至少一个小时的持续时间。在一些实施例中,高性能液流电池组可包含电池堆叠,所述电池堆叠在>100mA/cm2的充电周期期间在电池堆叠中的电池区域中具有可维持的操作电流密度。在一些实施例中,高性能的基于锌的液流电池组可包含以大于每小时0.1mm的速率将锌沉积于电池组的电池中的沉积表面上,并且在其它实施例中,沉积速率大于每小时0.2mm。此外,在一些实施例中,给高性能ZnFe液流电池组充电的方法可包含:以大于每小时0.1mm的速率使锌生长于或将锌沉积于电池组中电池的沉积表面上,并且在其它实施例中,生长或沉积速率大于每小时0.2mm或大于每小时0.4mm。在另一实施例中,高性能氧化还原液流电池组包含至少一个电池,所述至少一个电池包含至少一个正的半电池中的低电阻正极和至少一个负的半电池中的低电阻负极,其中低电阻正极的电阻和低电阻负极的电阻足够小,以获得至少一个电池的沉积表面的区域上的均匀高电流密度,在接近沉积表面的沉积区域中以高速率混合流经至少一个半电池的流动通道的电解液流,其中电解液具有足够高的活性离子物种浓度,以在沉积表面上获得维持在充电周期期间通过沉积表面的均匀高电流密度的沉积速率,接近沉积表面的液流的传质系数至少足以维持接近沉积表面的足够电解液浓度,以获得沉积表面的区域中的实质上均匀沉积。在另一实施例中,给高性能液流电池组充电的方法包含:在比液流电池组的电压更高的电压下将足够的电能供应输送至液流电池组;在低电阻正极和低电阻负极上提供均匀高电流密度,所述高电流密度穿过液流电池组的至少一个半电池的沉积表面的区域;产生流经至少一个半电池的流动通道的电解液流,所述电解液流在接近沉积表面的沉积区域中以高速率混合,其中电解液具有足够高的活性离子物种浓度,以在沉积表面上获得维持在充电期间通过沉积表面的均匀高电流密度的沉积速率;维持接近沉积表面的液流的传质系数足够大,以维持接近沉积表面的足够的电解液浓度,从而获得沉积表面的区域中的实质上均匀沉积。液流可为层流或湍流。高速率的混合处于足以维持传质系数大于7.7×10-4cm/s的范围内。此外,本发明包括最佳化高性能氧化还原液流电池组的方法,所述方法包含:设计液流电池组的流动速率和流动通道,所述流动速率和流动通道经最佳化以确保满足以下参数中的一或更多者:在最佳流体速度下,沉积表面上有均匀传质速率;局部电流密度近似小于2/3xiL,但足够高以防止苔藓状沉积(换句话说,适合于提供密集、附着的非枝状形态的局部电流密度);和沿着流动通道(在Zn侧上)的浓度耗尽为入口浓度的近似<10%。实验证实:(1)锌在4NNaOH中的溶解度为0.73M和(2)在40℃,旋转速度120rpm下,这一溶液的极限电流密度(在旋转圆盘电极处)为121mA/cm2。超饱和锌电解液,即4NNaOH中的0.73MZn++制备如下。步骤1:通过将8.139gZnO(m.w81.39g/mol)与30gmNaOH球粒(m.w.40g/mol)组合并用D.I水在恒定搅拌下配制至100ml,来制备原液(5.5NNaOH中1MZn++)。所得溶液为1MZn+++5.5NNaOH。步骤2:通过取用100ml(5.5NNaOH中1MZn++)原液并用D.I水将所述原液配制至137.5ml,来将(1MZn++/5.5NNaOH)稀释至4NNaOH溶液,所得溶液为4NNaOH中的0.73MZn++。(应注意,所报告的4NNaOH中Zn++溶解度极限为0.37M。)应注意,发现NaOH浓度处于2N-4N范围内的电解液提供令人满意的锌酸盐离子浓度、可接受的亚铁离子浓度组合和可接受的溶液腐蚀性,而高于4N的NaOH浓度导致亚铁离子浓度迅速减少以及产生更具腐蚀性的电解液。实验证实,4NNaOH中0.73MZn++和2.2NNaOH中0.4MZn++稳定达至少四周。尽管已参照本发明的某些实施例特定描述本发明,但本领域的一般技术人员应容易地更加明白,可在不脱离本发明的精神和范畴的情况下进行形式和细节的改变和修改。当前第1页1 2 3