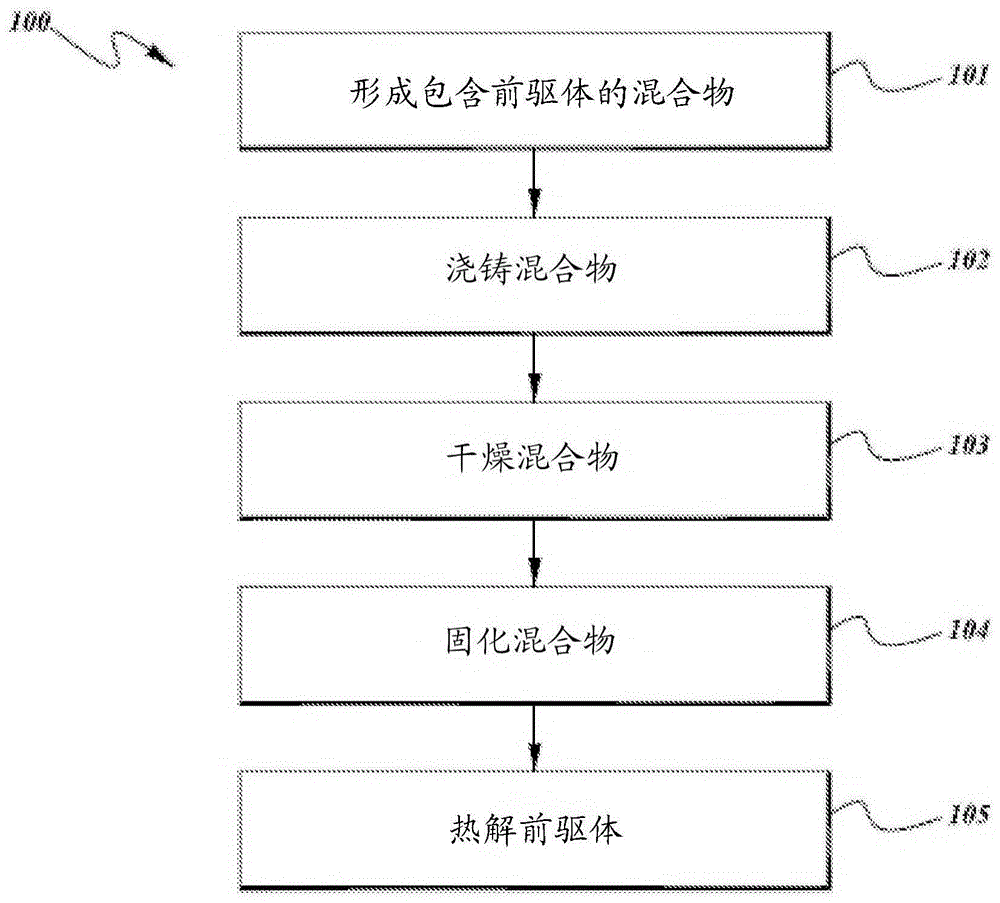
相关申请的交叉引用本申请要求于2017年12月7日提交的第62/596,071号美国临时申请的权益。以上援引的申请的全部内容通过援引并入本文。背景领域本申请总体上涉及硅颗粒。具体地,本申请涉及用于蓄电池电极中的硅颗粒以及包含硅颗粒的复合材料。相关技术描述锂离子蓄电池(battery)通常包括在阳极与阴极之间的分隔物和/或电解质。在一类蓄电池中,分隔物、阴极和阳极材料分别形成片或膜。将阴极、分隔物和阳极的片顺序地堆叠或轧制,使分隔物将阴极与阳极(例如,电极)分隔,以形成蓄电池。典型的电极包括在导电金属(例如,铝和铜)上的电化学活性材料层。可以将膜轧制或切割成块,然后将其层叠成堆叠体。堆叠体具有交替的电化学活性材料以及在它们之间的分隔物。技术实现要素:在某些实施方案中,提供硅颗粒。硅颗粒可以用于电化学电池中的电极中。硅颗粒可以具有提供小于约87.2°的平均接触角的表面。例如,平均接触角可以为约82°至约87.1°。硅颗粒还可以具有从表面延伸约20nm深度的外部区域。外部区域可以包含一定量的铝,使得整体测量的铝占硅颗粒的至少约0.01重量%。例如,整体测量的铝可以占硅颗粒的约0.01重量%至约1重量%。在一些情况下,整体测量的铝可以占硅颗粒的至少约0.05重量%。例如,整体测量的铝可以占硅颗粒的约0.05重量%至约1重量%。在一些情况下,整体测量的铝可以占硅颗粒的至少约0.1重量%。例如,整体测量的铝可以占硅颗粒的约0.1重量%至约1重量%。作为另一个实例,整体测量的铝可以占硅颗粒的约0.1重量%至约0.6重量%。一些硅颗粒中的外部区域可以包含氧化铝和/或硅化铝。在某些实施方案中,还提供用于包含硅颗粒的各种实施方案的电化学电池中的电极。在各种实施方案中,提供复合材料膜。复合材料膜可以包含大于0重量%且小于约99重量%的硅颗粒。例如,复合材料膜可以包含占复合材料膜的50重量%至99重量%的硅颗粒。作为另一个实例,复合材料膜可以包含占复合材料膜的70重量%至99重量%的硅颗粒。硅颗粒可以具有包含碳化硅或碳和碳化硅的混合物的表面涂层。硅颗粒可以具有从表面涂层延伸约20nm深度的区域。所述区域可以包含一定量的铝,使得整体测量的铝占硅颗粒的至少约0.01重量%。在一些情况下,整体测量的铝可以占硅颗粒的至少约0.1重量%。例如,整体测量的铝可以占硅颗粒的约0.1重量%至约1重量%。作为另一个实例,整体测量的铝可以占硅颗粒的约0.1重量%至约0.6重量%。一些硅颗粒中的区域可以包含氧化铝和/或硅化铝。复合材料膜可以还包含大于0重量%且小于约90重量%的一种或多种类型的碳相。一种或多种类型的碳相中的至少一种可以是基本上连续的相。在一些情况下,为基本上连续的相的一种或多种类型的碳相中的至少一种可以是电化学活性的和导电的。在复合材料膜的一些实施方案中,硅颗粒的平均粒度可以为约0.1μm至约40μm。例如,硅颗粒的平均粒度可以为约1μm至约20μm。在一些情况下,硅颗粒可以为约90%的纯硅至约99%的纯硅。表面涂层可以包含一氧化硅(sio)、二氧化硅(sio2)或硅氧化物(siox)。表面涂层可以是基本上连续的层。复合材料膜可以是自支撑的。在各种实施方案中,还提供包含复合材料膜的锂离子蓄电池电极。在某些实施方案中,提供形成复合材料的方法。方法可以包括提供包含前驱体和硅颗粒的混合物。方法还可以包括热解前驱体以将前驱体转化成一种或多种类型的碳相。方法还可以包括在硅颗粒的表面上形成碳化硅。硅颗粒可以具有从表面延伸约20nm深度的区域。所述区域可以包含一定量的铝,使得整体测量的铝占硅颗粒的至少约0.01重量%。在一些情况下,整体测量的铝可以占硅颗粒的至少约0.1重量%。例如,整体测量的铝可以占硅颗粒的约0.1重量%至约1重量%。作为另一个实例,整体测量的铝可以占硅颗粒的约0.1重量%至约0.6重量%。在一些情况下,硅颗粒可以包含氧化铝和/或硅化铝。在方法的一些实施方案中,硅颗粒的表面可以提供小于约87.2°的平均接触角。例如,平均接触角可以为约82°至约87.1°。在方法的一些情况中,提供混合物可以包括提供水分处理的硅颗粒。例如,水分处理的硅颗粒可以包括用水处理的硅颗粒、用醇处理的硅颗粒、液体煮沸的硅颗粒、液体倾析的硅颗粒、蒸制的硅颗粒、用水分热处理的硅颗粒和/或用氧化试剂处理的硅颗粒。氧化试剂可以包括氢氧化钾和/或过氧化氢。在方法的一些情况中,提供混合物可以包括向前驱体提供水分。前驱体可以包含聚合物和溶剂。向前驱体提供水分可以包括向聚合物提供水分和/或向溶剂提供水分。溶剂可以包括n-甲基-吡咯烷酮(nmp)和/或水。前驱体可以包含水溶性聚合物。在一些实施方案中,碳化硅和/或一种或多种类型的碳相中的一种可以在硅颗粒上形成基本上连续的层。形成碳化硅可以包括使一种或多种类型的碳相中的一种与硅颗粒反应。使一种或多种类型的碳相中的一种与硅颗粒反应可以包括使一种或多种类型的碳相与硅颗粒的自然硅氧化物层反应。热解前驱体可以包括将混合物加热至约500℃至约1300℃的温度。例如,热解前驱体可以包括将混合物加热至约800℃至约1200℃的温度。作为另一个实例,热解前驱体可以包括将混合物加热至约1175℃的温度。在一些情况下,热解可以包括向混合物提供水分。在方法的一些实施方案中,方法可以包括将混合物浇铸在衬底上、干燥混合物以形成膜、从衬底上移除膜以及将膜放置在热压机中。浇铸混合物可以包括向混合物提供水分。干燥混合物可以包括热处理具有水分的混合物。将膜放置在热压机中可以包括向膜提供水分。附图说明图1a示出了形成复合材料的方法的实施方案,所述方法包括形成包含前驱体的混合物、浇铸混合物、干燥混合物、固化混合物以及热解前驱体;图1b是在硅颗粒上形成碳化硅的示意图示;图2a和图2b是从较大的硅颗粒磨碎的微米尺寸的硅颗粒的一个实施方案的sem显微照片;图2c和图2d是在表面上具有纳米尺寸特征的微米尺寸的硅颗粒的一个实施方案的sem显微照片;图2e示出了形成复合材料的方法的示例性实施方案;图3a示意性地示出了示例性水分处理的硅颗粒;图3b示出了形成复合材料的方法的示例性实施方案;图4是在c/2.6的平均倍率下的放电容量的图绘;图5是在c/3的平均倍率下的放电容量的图绘;图6是在c/3.3的平均倍率下的放电容量的图绘;图7是在c/5的平均倍率下的放电容量的图绘;图8是在c/9的平均倍率下的放电容量的图绘;图9是放电容量的图绘;图10是在c/9的平均倍率下的放电容量的图绘;图11a和图11b是对于20重量%si的固定百分比,作为来自2611c的pi衍生的碳和石墨颗粒的各个重量百分比的函数的可逆容量和不可逆容量的图绘;图12是作为碳的重量百分比的函数的首次循环放电容量的图绘;图13是作为热解温度的函数的可逆(放电)容量和不可逆容量的图绘;图14是4.3cm×4.3cm的不含金属箔支撑层的复合阳极膜的照片;图15是复合阳极膜在循环之前的扫描电子显微镜(sem)显微照片(离焦部分为阳极底部部分,而聚焦部分是复合膜的裂开的边缘);图16是复合阳极膜在循环之前的另一个sem显微照片;图17是复合阳极膜在循环10次循环之后的sem显微照片;图18是复合阳极膜在循环10次循环之后的另一个sem显微照片;图19是复合阳极膜在循环300次循环之后的sem显微照片;图20包括复合阳极膜横截面的sem显微照片;图21是样品硅颗粒的x射线粉末衍射(xrd)图;图22是硅颗粒的一个实施方案的sem显微照片;图23是硅颗粒的一个实施方案的另一个sem显微照片;图24是硅颗粒的一个实施方案的sem显微照片;图25是硅颗粒的一个实施方案的sem显微照片;图26是样品硅颗粒的化学分析;图27a和图27b是两种具有纳米尺寸特征的微米尺寸的硅颗粒的示例粒度柱状图;图28是比较两种类型的示例性硅颗粒在电池循环期间的放电容量的图绘;图29示出了与未处理的硅颗粒相比,在示例性水分处理的硅颗粒中铝2p峰的x射线光电子能谱(xps)光谱;以及图30示出了与包含未处理的硅颗粒的蓄电池相比,包含水分处理的硅颗粒的蓄电池的容量保持率与循环数的图。具体实施方式本申请描述了可以用作电化学电池中的电极(例如,阳极和阴极)中的电化学活性材料的硅材料的某些实施方案。硅可以是每单位体积主体材料的潜在高能量,例如用于锂离子蓄电池。例如,与使用诸如石墨的其它活性材料的锂离子蓄电池相比,硅具有高的理论容量并且可以增加锂离子蓄电池的能量密度。然而,在锂嵌入时,硅可以膨胀超过300%。因此,与具有石墨阳极的蓄电池相比,具有硅阳极的蓄电池在循环时表现出更快的容量损失。在充电和放电期间硅颗粒的反复膨胀和收缩可以导致在循环期间阳极的机械失效。机械失效可以暴露硅的新表面,所述表面可以与电解质反应,在固体电解质界面/相间(sei)中不可逆地掺入锂离子,并且导致容量损失。本文描述的某些实施方案可以包括具有改性表面的硅材料,导致改善的循环性能。例如,一些实施方案可以提供具有增加的稳定性的sei(例如,在一些情况下基本上稳定的sei和/或稳定的sei),以改善容量保持率并且降低(例如,和/或在一些情况下防止)快衰落。典型的碳阳极电极包括诸如铜片的集流器。将碳连同非活性粘合剂材料一起沉积在收集器上。碳是常用的,因为碳具有优异的电化学性质并且还是导电的。如果去除了集流器层(例如,铜层),则碳可能不能机械地支撑其自身。因此,常规电极需要诸如收集器的支撑结构以能够起到电极的作用。在本申请中描述的电极(例如,阳极或阴极)组合可以产生自支撑的电极。由于导电碳化聚合物用于阳极结构中的电流收集以及用于机械支撑,对金属箔集流器的需要被消除或最小化。在移动产业的典型应用中,通常添加金属集流器以确保足够的倍率性能。与一类常规锂离子蓄电池电极中的悬浮于非导电粘合剂中的颗粒碳相反,碳化聚合物可以在整个电极中形成基本上连续的导电碳相。采用碳化聚合物的碳复合共混物的优点可以包括,例如,1)较高的容量,2)增强的过充电/放电保护,3)由于消除(或最小化)金属箔集流器而具有较低的不可逆容量,以及4)由于更简单的制造而潜在的成本节约。当前用于可再充电的锂离子电池的阳极电极通常具有约200毫安小时/克的比容量(包括金属箔集流器、导电添加剂、以及粘合剂材料)。用于大多数锂离子蓄电池阳极的活性材料石墨具有372毫安小时/克(mah/g)的理论能量密度。相比之下,硅具有4200mah/g的高的理论容量。为了增加锂离子蓄电池的体积能量密度和重量能量密度,硅可以用作阴极或阳极的活性材料。还报道了多种类型的硅材料(例如,硅纳米粉末、硅纳米纤维、多孔硅和经球磨的硅)作为负电极或正电极的活性材料的可行的候选者。小粒度(例如,纳米范围的尺寸)通常可以增加循环寿命性能。它们还可以表现出非常高的不可逆容量。然而,小粒度也可以导致非常低的体积能量密度(例如,对于整个电池堆叠体),这归因于包裹活性材料的困难。较大的粒度(例如,微米(micrometer)或微米(micron)范围的尺寸)通常可以导致较高密度阳极材料。然而,硅活性材料的膨胀可能由于颗粒破裂而导致差的循环寿命。例如,在锂嵌入时,硅可以膨胀超过300%。由于这种膨胀,包含硅的阳极应在保持硅颗粒之间的电接触的同时,允许膨胀。如本文中描述,以及在标题分别为“compositematerialsforelectrochemicalstorage”和“siliconparticlesforbatteryelectrodes”的第13/008,800号美国专利申请(第9,178,208号美国专利)和第13/601,976号美国专利申请(第2014/0170498号美国专利申请公开)(其全部内容通过援引并入本文)中描述,某些实施方案采用了使用碳化聚合物产生单片自支撑阳极的方法。因为聚合物转化成导电且电化学活性的基质,因此所得的电极是足够导电的,从而可以省略或最小化金属箔或网状集流器。转化的聚合物还可以用作循环期间硅颗粒的膨胀缓冲剂,使得可以实现高的循环寿命。在某些实施方案中,所得的电极是基本由活性材料构成的电极。在其它实施方案中,所得的电极基本上是活性材料。电极可以具有约500mah/g至约3500mah/g的高的能量密度,这可以归因于,例如,1)硅的使用,2)金属集流器的消除或大幅减少,以及3)完全或基本上完全由活性材料构成。如标题为“surfacemodificationofsiliconparticlesforelectrochemicalstorage”的第14/821,586号美国专利申请(第2017/0040598号美国专利申请公开)(其全部内容通过援引并入本文)描述,在某些实施方案中,碳化聚合物可以与硅颗粒上的自然硅氧化物表面层反应。在一些实施方案中,对颗粒的表面进行改性以在其上形成表面涂层,所述表面涂层可以进一步用作循环期间硅颗粒的膨胀缓冲剂。表面涂层可以包含碳化硅。本文描述的复合材料可以用作大多数常规锂离子蓄电池中的阳极;它们也可以与额外的添加剂一起用作一些电化学偶中的阴极。复合材料也可以用于二次蓄电池(例如,可再充电的)或一次蓄电池(例如,不可再充电的)。在一些实施方案中,复合材料是自支撑结构。在其它实施方案中,复合材料是自支撑单片结构。例如,收集器可以包括在由复合材料构成的电极中。在某些实施方案中,复合材料可以用于形成在标题为“carbonelectrodestructuresforbatteries”的第12/838,368号美国专利申请(第2011/0020701号美国专利申请公开)中讨论的碳结构,其全部内容通过援引并入本文。此外,本文描述的复合材料可以是例如硅复合材料、碳复合材料和/或硅-碳复合材料。如在标题为“siliconparticlesforbatteryelectrodes”的第13/799,405号美国专利申请(第9,553,303号美国专利)(其全部内容通过援引并入本文)中描述,某些实施方案可以进一步包括包含微米尺寸的硅颗粒的复合材料。例如,在一些实施方案中,微米尺寸的硅颗粒在表面上具有纳米尺寸特征。具有此类几何结构的硅颗粒可以具有微米尺寸的硅颗粒的益处(例如,高能量密度)和纳米尺寸的硅颗粒的益处(例如,良好的循环行为)两者。如本文使用,术语“硅颗粒”通常可以包括具有或不具有纳米尺寸特征的微米尺寸的硅颗粒。图1a示出了形成复合材料的方法100的一个实施方案。例如,形成复合材料的方法可以包括形成包含前驱体的混合物,方框101。方法还可以包括热解前驱体以将前驱体转化为碳相。前驱体混合物可以包含碳添加剂,例如石墨活性材料、切碎或研磨的碳纤维、碳纳米纤维、碳纳米管和/或其它碳。在前驱体被热解之后,所得的碳材料可以是自支撑的单片结构。在某些实施方案中,将一种或多种材料添加至混合物中以形成复合材料。例如,可以将硅颗粒添加至混合物中。碳化前驱体产生将复合材料保持在一起的电化学活性结构。例如,碳化前驱体可以是基本上连续的相。包括具有或不具有纳米尺寸特征的微米尺寸的硅颗粒的硅颗粒可以分布在整个复合材料中。有利地,碳化前驱体可以是结构材料以及电化学活性且导电的材料。在某些实施方案中,添加至混合物中的材料颗粒均匀地或基本上均匀地分布在整个复合材料中以形成均匀或基本上均匀的复合物。混合物可以包含多种不同的组分。混合物可以包含一种或多种前驱体。在某些实施方案中,前驱体是烃化合物。例如,前驱体可以包括聚酰胺酰亚胺、聚酰胺酸、聚酰亚胺等。其它前驱体包括酚醛树脂、环氧树脂和/或其它聚合物。混合物还可以包含溶剂。例如,溶剂可以是n-甲基-吡咯烷酮(nmp)。其它可能的溶剂包括丙酮、二乙醚、γ-丁内酯、异丙醇、碳酸二甲酯、碳酸乙酯、二甲氧基乙烷、乙醇、甲醇等。前驱体和溶剂溶液的实例包括pi-2611(hdmicrosystems)、pi-5878g(hdmicrosystems)和vtecpi-1388(rbi,inc.)。pi-2611由>60%的正甲基-2-吡咯烷酮和10%至30%的s-联苯二酐/对苯二胺构成。pi-5878g由>60%的正甲基吡咯烷酮、10%至30%的苯均四酸二酐/二氨基二苯醚的聚酰胺酸、10%至30%的含5%至10%的1,2,4-三甲苯的芳香烃(石油馏出物)构成。在某些实施方案中,在溶剂中的前驱体的量为约10wt.%至约30wt.%。额外的材料也可以包含在混合物中。例如,如先前讨论,可以将硅颗粒或碳颗粒添加至混合物中,所述碳颗粒包括石墨活性材料、切碎或研磨的碳纤维、碳纳米纤维、碳纳米管以及其它导电碳。另外,可以将混合物混合以均质化混合物。在某些实施方案中,将混合物浇铸在衬底上,图1a中的方框102。在一些实施方案中,浇铸包括使用间隙挤出、带式浇铸或叶片浇铸技术。叶片浇铸技术可以包括通过使用控制在衬底上方一定距离的平表面(例如,叶片)来将涂层应用至衬底。可以将液体或浆料应用至衬底,并且可以使叶片在液体上经过以使液体在衬底上铺展开。由于液体经过叶片与衬底之间的间隙,可以通过叶片与衬底之间的间隙来控制涂层的厚度。随着液体经过间隙,还可以刮除过量的液体。例如,可以将混合物浇铸在包括聚合物片、聚合物辊和/或由玻璃或金属制成的箔或辊的衬底上。然后可以将混合物干燥以去除溶剂,方框103。例如,聚酰胺酸和nmp溶液可以在约110℃下干燥约2小时,以去除nmp溶液。然后可以将干燥的混合物从衬底上去除。例如,可以用hcl蚀刻掉铝衬底。或者,可以通过剥离将混合物从衬底上去除,或者以其它方式机械地从衬底上去除干燥的混合物。在一些实施方案中,衬底包含聚对苯二甲酸乙二醇酯(pet),包括例如在某些实施方案中,干燥的混合物是膜或片。在一些实施方案中,任选地固化干燥的混合物,方框104。在一些实施方案中,干燥的混合物可以进一步干燥。例如,可以将干燥的混合物放置在热压机中(例如,在烘箱中的石墨板之间)。热压机可以用于进一步干燥和/或固化并且保持干燥的混合物平整。例如,来自聚酰胺酸和nmp溶液的干燥的混合物可以在约200℃下热压约8小时至16小时。或者,包括浇铸和干燥的整个过程可以以使用标准膜处理设备的辊对辊(roll-to-roll)过程完成。可以冲洗干燥的混合物,以去除可能残留的任何溶剂或蚀刻剂。例如,去离子(di)水可以用于冲洗干燥的混合物。在某些实施方案中,带式浇铸技术可以用于浇铸。在一些实施方案中,可以通过狭缝模具涂覆工艺将混合物涂覆在衬底上(例如,通过设定的或基本上设定的间隙来计量恒定或基本上恒定的重量和/或体积)。在一些其它实施方案中,没有用于浇铸的衬底,并且不需要从任何衬底上去除阳极膜。干燥的混合物可以切割或机械分割成较小的块。混合物进一步经历热解以将聚合物前驱体转化成碳,方框105。在某些实施方案中,混合物在还原气氛中热解。例如,可以使用惰性气氛,真空和/或流动的氩气、氮气或氦气。在一些实施方案中,将混合物加热至约900℃至约1350℃。例如,由聚酰胺酸形成的聚酰亚胺可以在约1175℃下碳化约一小时。在某些实施方案中,混合物的加热速率和/或冷却速率为约10℃/min。可以使用固定器以将混合物保持成特定的几何结构。固定器可以是石墨、金属等。在某些实施方案中,将混合物保持成平坦的。将混合物热解之后,可以将接片(tab)附接至热解的材料以形成电接触。例如,镍、铜或其合金可以用于接片。在某些实施方案中,本文描述的方法中的一种或多种可以以连续过程进行。在某些实施方案中,浇铸、干燥、可能的固化和热解可以以连续过程进行。例如,可以将混合物涂覆到玻璃或金属圆筒上。混合物可以在滚筒上旋转的同时干燥以产生膜。膜可以作为卷转移或剥离,并且供给进入另一机器用于其它加工。在热解步骤之前,也可以采用挤出和其它工业已知的膜制造技术。前驱体的热解产生碳材料(例如,至少一种碳相)。在某些实施方案中,碳材料是硬碳。在一些实施方案中,前驱体是可以热解以形成硬碳的任何材料。当除了碳化前驱体以外,混合物包含一种或多种额外的材料或相时,可以产生复合材料。特别地,混合物可以包含产生硅-碳复合材料(例如,至少一个包含硅的第一相和至少一个包含碳的第二相)或硅-碳-碳复合材料(例如,至少一个包含硅的第一相、至少一个包含碳的第二相和至少一个包含碳的第三相)的硅颗粒。硅颗粒可以增加复合材料的锂嵌入比容量(specificlithiuminsertioncapacity)。当硅吸收锂离子时,其以300+体积百分比的量级经历大幅的体积增加,这可以引起电极结构完整性问题。除了体积膨胀相关问题以外,硅并非是固有导电的,但当其与锂形成合金(例如,锂化)时变得导电。当硅去锂化时,硅的表面失去导电性。此外,当硅去锂化时,体积减小,这导致了硅颗粒失去与基质接触的可能性。体积的显著改变还导致了硅颗粒结构的机械失效,转而使其粉碎。粉碎和失去电接触使得使用硅作为锂离子蓄电池中的活性材料是有挑战性的。硅颗粒的初始尺寸的减小可以防止硅粉末的进一步粉碎,以及使表面导电性的损失最小化。此外,向复合物添加可以随着硅颗粒的体积改变而弹性变形的材料可以减少损失对硅表面的电接触的机会。例如,复合材料可以包含诸如石墨的碳,其有助于复合物吸收膨胀的能力,并且还能够嵌入锂离子以增大电极(例如,化学活性的)的储存容量。因此,复合材料可以包含一种或多种类型的碳相。在一些实施方案中,粒度(例如,硅颗粒的直径或最大尺寸)可以小于约50μm、小于约40μm、小于约30μm、小于约20μm、小于约10μm、小于约1μm、约10nm至约50μm、约10nm至约40μm、约10nm至约30μm、约10nm至约20μm、约0.1μm至约20μm、约0.5μm至约20μm、约1μm至约20μm、约1μm至约15μm、约1μm至约10μm、约10nm至约10μm、约10nm至约1μm、小于约500nm、小于约100nm、约100nm等。所有、基本上所有或至少一些的硅颗粒可以包括以上描述的粒度(例如,直径或最大尺寸)。例如,硅颗粒的平均粒度(例如,平均直径或平均最大尺寸)或中值粒度(或中值直径或中值最大尺寸)可以小于约50μm、小于约40μm、小于约30μm、小于约20μm、小于约10μm、小于约1μm、约10nm至约50μm、约10nm至约40μm、约10nm至约30μm、约10nm至约20μm、约0.1μm至约20μm、约0.5μm至约20μm、约1μm至约20μm、约1μm至约15μm、约1μm至约10μm、约10nm至约10μm、约10nm至约1μm、小于约500nm、小于约100nm、约100nm等。在一些实施方案中,硅颗粒可以具有粒度的分布。例如,至少约95%、至少约90%、至少约85%、至少约80%、至少约70%或至少约60%的颗粒可以具有本文描述的粒度。混合物中或复合材料中提供的硅的量可以大于混合物和/或复合材料的0重量%。在某些实施方案中,硅的量可以是复合材料的约0重量%至约99重量%,包括大于约0重量%至约99重量%、大于约0重量%至约95重量%、大于约0重量%至约90重量%、大于约0重量%至约35重量%、大于约0重量%至约25重量%、约10重量%至约35重量%、至少约30重量%、约30重量%至约99重量%、约30重量%至约95重量%、约30重量%至约90重量%、约30重量%至约80重量%、至少约50重量%、约50重量%至约99重量%、约50重量%至约95重量%、约50重量%至约90重量%、约50重量%至约80重量%、约50重量%至约70重量%、至少约60重量%、约60重量%至约99重量%、约60重量%至约95重量%、约60重量%至约90重量%、约60重量%至约80重量%、至少约70重量%、约70重量%至约99重量%、约70重量%至约95重量%、约70重量%至约90重量%等。此外,硅颗粒可以是或可以不是纯硅。例如,硅颗粒可以基本是硅,或者可以是硅合金。在一个实施方案中,硅合金包含作为主要成分的硅,连同一种或多种其它元素。如本文描述,在一些实施方案中,硅颗粒可以含有铝。如本文描述,微米尺寸的硅颗粒可以提供良好的体积能量密度和重量能量密度,连同良好的循环寿命。在某些实施方案中,为了得到微米尺寸的硅颗粒的益处(例如,高的能量密度)和纳米尺寸的硅颗粒的益处(例如,良好的循环行为),硅颗粒可以具有在微米范围内的平均粒度或中值粒度以及包括纳米尺寸特征的表面。在一些实施方案中,硅颗粒可以具有约0.1μm至约30μm或约0.1μm至高达约30μm的所有值的平均粒度(例如,平均直径或平均最大尺寸)或中值粒度(例如,中值直径或中值最大直径)。例如,硅颗粒可以具有以下的平均粒度或中值粒度:约0.1μm至约20μm、约0.5μm至约25μm、约0.5μm至约20μm、约0.5μm至约15μm、约0.5μm至约10μm、约0.5μm至约5μm、约0.5μm至约2μm、约1μm至约20μm、约1μm至约15μm、约1μm至约10μm、约5μm至约20μm等。因此,平均粒度或中值粒度可以是约0.1μm至约30μm的任何值,例如,0.1μm、0.5μm、1μm、5μm、6μm、7μm、8μm、9μm、10μm、15μm、20μm、25μm和30μm。纳米尺寸特征可以包括以下的平均特征尺寸(例如,平均直径或平均最大尺寸):约1nm至约1μm、约1nm至约750nm、约1nm至约500nm、约1nm至约250nm、约1nm至约100nm、约10nm至约500nm、约10nm至约250nm、约10nm至约100nm、约10nm至约75nm、或者约10nm至约50nm。特征可以包括硅。从前驱体获得的碳的量可以是聚酰胺酸的约50重量%。在某些实施方案中,从复合材料中的前驱体获得的碳的量可以大于0重量%至约95重量%,例如约1重量%至约95重量%、约1重量%至约90重量%、1重量%至约80重量%、约1重量%至约70重量%、约1重量%至约60重量%、约1重量%至约50重量%、约1重量%至约40重量%、约1重量%至约30重量%、约5重量%至约95重量%、约5重量%至约90重量%、约5重量%至约80重量%、约5重量%至约70重量%、约5重量%至约60重量%、约5重量%至约50重量%、约5重量%至约40重量%、约5重量%至约30重量%、约10重量%至约95重量%、约10重量%至约90重量%、约10重量%至约80重量%、约10重量%至约70重量%、约10重量%至约60重量%、约10重量%至约50重量%、约10重量%至约40重量%、约10重量%至约30重量%、约10重量%至约25重量%等。例如,从前驱体获得的碳的量可以是前驱体的约1重量%、约5重量%、约10重量%、约15重量%、约20重量%、约25重量%等。来自前驱体的碳可以是硬碳。硬碳可以是即使在超过2800摄氏度下加热也不转化成石墨的碳。在热解期间熔化或流动的前驱体在足够的温度和/或压力下转化成软碳和/或石墨。可以选择硬碳,因为软碳前驱体可以流动,并且软碳和石墨相比硬碳在机械上更弱。其它可能的硬碳前驱体可以包括酚醛树脂、环氧树脂、以及其它具有非常高的熔点或交联的聚合物。在一些实施方案中,在复合材料中的硬碳的量可以具有大于0重量%至约95重量%的值,例如约1重量%至约95重量%、约1重量%至约90重量%、约1重量%至约80重量%、约1重量%至约70重量%、约1重量%至约60重量%、约1重量%至约50重量%、约1重量%至约40重量%、约1重量%至约30重量%、约5重量%至约95重量%、约5重量%至约90重量%、约5重量%至约80重量%、约5重量%至约70重量%、约5重量%至约60重量%、约5重量%至约50重量%、约5重量%至约40重量%、约5重量%至约30重量%、约10重量%至约95重量%、约10重量%至约90重量%、约10重量%至约80重量%、约10重量%至约70重量%、约10重量%至约60重量%、约10重量%至约50重量%、约10重量%至约40重量%、约10重量%至约30重量%、约10重量%至约25重量%等。在一些实施方案中,在复合材料中的硬碳的量可以是约1重量%、约5重量%、约10重量%、约20重量%、约30重量%、约40重量%、约50重量%或大于约50重量%。在某些实施方案中,硬碳相是基本上无定形的。在其它实施方案中,硬碳相是基本上结晶的。在其它实施方案中,硬碳相包括无定形碳和结晶碳。硬碳相可以是复合材料中的基质相。硬碳也可以嵌入含硅的添加剂的孔中。硬碳可以与一些添加剂反应以在界面处产生一些材料。例如,在硅颗粒与硬碳之间可以存在碳化硅层。在某些实施方案中,将混合物加热至期望的热解温度可以进一步导致存在于混合物中的硅颗粒的表面改性。在一些实施方案中,混合物的热解可以导致在存在于混合物中的至少50%的硅颗粒上形成表面涂层。在一些实施方案中,混合物的热解可以导致在存在于混合物中的至少60%、70%、80%、90%或99%的硅颗粒上形成表面涂层。在一些实施方案中,表面涂层形成在硅颗粒上的基本上连续的层。在一些实施方案中,碳化的前驱体或树脂可以接触硅颗粒的表面。在某些实施方案中,与硅颗粒表面接触的碳化的前驱体可以是由前驱体的热解产生的一种或多种类型的碳相。与硅颗粒表面接触的碳化的前驱体的一种或多种类型的碳相可以在热解期间与硅颗粒反应,从而在硅颗粒表面上形成碳化硅。因此,在一些实施方案中,表面涂层可以包含碳、碳化硅和/或碳和碳化硅的混合物。在一些实施方案中,如以下进一步描述,存在于混合物中的硅颗粒可以包括自然硅氧化物(sio、sio2、siox)表面层。在某些实施方案中,与硅颗粒表面接触的碳化的前驱体可以与自然存在的自然硅氧化物表面层反应以形成碳化硅。在一些实施方案中,与硅颗粒表面接触的碳化的前驱体可以与基本上所有的自然硅氧化物层反应以形成碳化硅。因此,在一些实施方案中,硅颗粒上的表面涂层可以包含碳和碳化硅,其中表面涂层基本上不含硅氧化物。在一些实施方案中,表面涂层的第一部分可以包含碳化硅,而第二部分可以包含碳化硅和碳的混合物。在一些其它实施方案中,与硅颗粒表面接触的碳化的前驱体可以将自然硅氧化物层不完全地转化为碳化硅,并且所得的一个或多个表面涂层可以包含碳、碳化硅和一种或多种硅氧化物,例如sio、sio2和siox。在一些实施方案中,与硅颗粒表面接触的碳化的前驱体可以完全反应,得到包含碳化硅的表面涂层。在一些实施方案中,基本上所有的表面涂层可以包含碳化硅。在一些实施方案中,此类表面涂层可以基本上不含硅氧化物和/或碳。在某些实施方案中,热解的混合物可以包括产生硅-碳-碳化硅复合材料(例如,至少一个包含硅的第一相、至少一个包含碳的第二相和至少一个包含碳化硅的第三相)或硅-碳-碳-碳化硅复合材料(例如,至少一个包含硅的第一相、至少一个包含碳的第二相、至少一个包含碳的第三相和至少一个包含碳化硅的第四相)的具有碳和/或碳化硅表面涂层的硅颗粒。此外,本文描述的硅颗粒上的表面涂层可以有助于限制硅颗粒在锂化期间的向外膨胀。通过限制在锂化期间的向外颗粒膨胀,表面涂层可以有助于防止硅颗粒的机械失效并且确保良好的电接触。表面涂层可以进一步增强电极内的电荷转移。阳极中的硅颗粒的受控和优化的表面改性还可以显著改善在相关的蓄电池单元循环期间的容量保持率。此外,表面涂层基本上影响蓄电池内阳极材料与电解质之间发生的反应。表面涂层可以有助于减少不希望的反应。在高温热解期间,形成的表面涂层和经由转化成更稳定和无反应性的sic来去除不希望的自然氧化物(sio2)可以提供较高的可逆容量,最小化不可逆容量损失。不可逆容量损失可能是由于消耗锂的固体电解质界面(sei)层的形成和积累。对于硅颗粒,这变成更突出的问题,因为纳米级硅颗粒和微米级硅颗粒具有大的表面积,并且较大的硅颗粒在锂化和脱锂化期间倾向于粉碎,这可以引入额外的颗粒表面积。另外,不可逆容量损失可能是由于锂与不希望的自然硅氧化物的反应(反应式1),这在硅阳极材料的加工和储存期间是不可避免的。siox+yli+ye→si+liyox(反应式1)因此,通过碳和/或碳化硅对硅颗粒的表面改性可以有助于形成相对稳定的固体电解质界面层,并且可以减少或消除锂与si颗粒表面上的自然硅氧化物的不希望的反应(反应式1)。图1b是如以上描述的在硅颗粒上形成碳化硅的示意图。首先,在包含如以上描述的前驱体的混合物中提供包含自然硅氧化物表面层的硅颗粒。在一些实施方案中,混合物在还原气氛中热解。例如,可以使用还原气氛、真空和/或流动气体,包括h2、co或烃气体。在一些实施方案中,将混合物加热至约500℃至约1350℃。在一些实施方案中,将混合物加热至约800℃至约1200℃。在一些实施方案中,将混合物加热至约1175℃。与硅颗粒的表面接触的热解的前驱体与硅颗粒的自然硅氧化物层反应以形成碳化硅。与硅颗粒表面接触的碳化的前驱体在此被描述为连续且保形的,但在一些其它实施方案中可以不是连续或保形的。此外,在一些实施方案中,由自然硅氧化物层与接触硅颗粒表面的碳化前驱体之间的反应形成的碳化硅层可以采取复合阳极膜内的涂层或分散体的形式。如图1b中显示,在一些实施方案中,碳化硅在硅颗粒上可以不是连续或保形的,然而在一些其它实施方案中,碳化硅可以是连续和/或保形的涂层。在某些实施方案中,将石墨颗粒添加至混合物中。有利地,石墨可以是蓄电池中的电化学活性材料以及可以响应于硅颗粒的体积变化的弹性可变形材料。对于目前市场上某些类型的锂离子蓄电池,石墨是优选的活性阳极材料,因为它具有低的不可逆容量。另外,石墨比硬碳软,并且可以更好地吸收硅添加剂的体积膨胀。在某些实施方案中,石墨颗粒的粒度(例如,直径或最大尺寸)可以是约0.5微米至约20微米。所有、基本上所有或至少一些的石墨颗粒可以包括本文描述的粒度(例如,直径或最大尺寸)。在一些实施方案中,石墨颗粒的平均粒度或中值粒度(例如,直径或最大尺寸)可以是约0.5微米至约20微米。在一些实施方案中,石墨颗粒可以具有粒度的分布。例如,至少约95%、至少约90%、至少约85%、至少约80%、至少约70%或至少约60%的颗粒可以具有本文描述的粒度。在某些实施方案中,复合材料可以包括大于0重量%且小于约80重量%的量的石墨颗粒,包括约40重量%至约75重量%、约5重量%至约30重量%、约5重量%至约25重量%、约5重量%至约20重量%、约5重量%至约15重量%等。在某些实施方案中,将也可以是电化学活性的导电颗粒添加至混合物。此类颗粒能够实现更加导电的复合物以及更加机械可变形的复合物,其能够吸收在锂化和去锂化期间发生的大幅体积改变。在某些实施方案中,导电颗粒的粒度(例如,直径或最大尺寸)可以是约10纳米至约7微米。所有、基本上所有或至少一些的导电颗粒可以包括本文描述的粒度(例如,直径或最大尺寸)。在一些实施方案中,导电颗粒的平均粒度或中值粒度(例如,直径或最大尺寸)可以是约10nm至约7微米。在一些实施方案中,导电颗粒可以具有粒度的分布。例如,至少约95%、至少约90%、至少约85%、至少约80%、至少约70%或至少约60%的颗粒可以具有本文描述的粒度。在某些实施方案中,混合物可以包含大于0重量%至高达约80重量%的量的导电颗粒。在其它实施方案中,复合材料可以包含约45重量%至约80重量%。导电颗粒可以是导电碳,包括炭黑、碳纤维、碳纳米纤维、碳纳米管等。许多被认为是非电化学活性的导电添加剂的碳一旦在聚合物基质中热解则变得具有活性。或者,导电颗粒可以是金属或合金,包括铜、镍或不锈钢。在某些实施方案中,电极可以包含本文描述的复合材料。例如,复合材料可以形成自支撑的单片电极。复合材料的热解的碳相(例如,硬碳相)可以保持在一起并且结构上支撑添加至混合物中的颗粒。在某些实施方案中,自支撑的单片电极不包括单独的收集器层和/或其它支撑结构。在一些实施方案中,复合材料和/或电极不包含在前驱体热解之后残留的痕量以外的聚合物。在其它实施方案中,复合材料和/或电极不包含非导电粘合剂。复合材料也可以包括孔隙率,例如按体积孔隙率计约1%至约70%或约5%至约50%。例如,孔隙率可以是按体积孔隙率计约5%至约40%。复合材料也可以形成粉末。例如,可以将复合材料研磨成粉末。复合材料粉末可以用作电极的活性材料。例如,复合材料粉末可以以类似于制备常规电极结构的方式沉积在收集器上,如工业中已知的。在某些实施方案中,蓄电池或电化学电池中的电极可以包含复合材料,包括具有本文描述的硅颗粒的复合材料。例如,复合材料可以用于阳极和/或阴极。在某些实施方案中,蓄电池为锂离子蓄电池。在其它实施方案中,蓄电池为二次蓄电池,或者在其它实施方案中,蓄电池为一次蓄电池。此外,在蓄电池的使用期间,可以不采用复合材料的全部容量,以改善蓄电池的寿命(例如蓄电池失效或蓄电池性能下降至可用水平以下之前的充电和放电循环数)。例如,具有约70重量%的硅颗粒、约20重量%的来自前驱体的碳以及约10重量%的石墨的复合材料可以具有约3000mah/g的最大重量容量,而复合材料可以仅使用多至约550mah/g至约1500mah/g的重量容量。尽管可以不采用复合材料的最大重量容量,以较低容量使用复合材料仍然可以实现比某些锂离子蓄电池更高的容量。在某些实施方案中,以或仅以小于复合材料的最大重量容量的约70%的重量容量使用复合材料。例如,不以超过复合材料的最大重量容量的约70%的重量容量使用复合材料。在其它实施方案中,以或仅以小于复合材料的最大重量容量的约50%或者小于复合材料的最大重量容量的约30%的重量容量使用复合材料。硅颗粒本文描述的是用于蓄电池电极(例如,阳极和阴极)中的硅颗粒。当前用于可再充电的锂离子电池中的阳极电极通常具有约200毫安小时/克的比容量(包括金属箔集流器、导电添加剂、以及粘合剂材料)。用于大多数锂离子蓄电池阳极的活性材料石墨具有372毫安小时/克(mah/g)的理论能量密度。相比之下,硅具有4200mah/g的高的理论容量。然而,在锂嵌入时,硅膨胀超过300%。由于这种膨胀,包含硅的阳极应在允许硅保持与硅的电接触的同时能够膨胀。一些实施方案提供可以用作电极中的电化学活性材料的硅颗粒。除了硅颗粒以外,电极可以包含粘合剂和/或其它电化学活性材料。例如,本文描述的硅颗粒可以用作本文描述的复合材料中的硅颗粒。在另一个实例中,电极可以具有集流器上的电化学活性材料层,并且电化学活性材料层包含硅颗粒。电化学活性材料还可以包含一种或多种类型的碳。有利地,本文描述的硅颗粒可以改善电化学活性材料的性能,例如改善容量和/或循环性能。此外,具有此类硅颗粒的电化学活性材料可能不会由于硅颗粒的锂化而显著劣化。在某些实施方案中,如本文描述,硅颗粒可以具有约10nm至约40μm的平均粒度,例如平均直径或平均最大尺寸。其它实施方案可以包括约1μm至约15μm、约10nm至约1μm和约100nm至约10μm的平均粒度。可以通过各种方法分离各种尺寸的硅颗粒,例如通过风筛、筛分或其它筛选方法。例如,可以使用325的网目尺寸从粒度大于约44μm的颗粒中分离粒度小于约44μm的颗粒。此外,硅颗粒可以具有粒度的分布。例如,至少约90%的颗粒可以具有约10nm至约40μm、约1μm至约15μm、约10nm至约1μm和/或大于200nm的粒度,例如直径或最大尺寸。在一些实施方案中,硅颗粒可以具有以下的平均表面积/单位质量:约1m2/g至约100m2/g、约1m2/g至约80m2/g、约1m2/g至约60m2/g、约1m2/g至约50m2/g、约1m2/g至约30m2/g、约1m2/g至约10m2/g、约1m2/g至约5m2/g、约2m2/g至约4m2/g或小于约5m2/g。在某些实施方案中,硅颗粒是至少部分结晶的、基本结晶的和/或完全结晶的。此外,硅颗粒可以是基本纯的硅。与常规电极中使用的硅颗粒相比,本文关于一些实施方案描述的硅颗粒通常具有更大的平均粒度。在一些实施方案中,本文描述的硅颗粒的平均表面积通常较小。不受任何特定理论束缚,本文描述的硅颗粒的较小表面积可以有助于增强电化学单电池的性能。典型的锂离子类型的可再充电的蓄电池阳极将包含纳米尺寸的硅颗粒。为了进一步增加电池的容量,将更小的硅颗粒(例如在纳米尺寸范围内的硅颗粒)用于制备电极活性材料。在一些情况下,将硅颗粒研磨以减小颗粒的尺寸。有时研磨可以产生粗糙的或刮损的颗粒表面,其也增加了表面积。然而,硅颗粒的增加的表面积实际上可以有助于电解质的降解,这导致不可逆容量损失的增加。图2a和图2b是从较大的硅颗粒磨碎的硅颗粒的示例性实施方案的sem显微照片。如附图中显示,某些实施方案可以具有粗糙的表面。如本文描述,某些实施方案包括具有在纳米尺寸范围内的表面粗糙度的硅颗粒,例如在表面上具有纳米尺寸特征的微米尺寸的硅颗粒。图2c和图2d是此类硅颗粒的示例性实施方案的sem显微照片。各种此类硅颗粒可以具有在微米范围内(例如,如本文描述,约0.1μm至约30μm)的平均粒度(例如,平均直径或平均最大尺寸)和包括纳米尺寸特征(例如,如本文描述,约1nm至约1μm、约1nm至约750nm、约1nm至约500nm、约1nm至约250nm、约1nm至约100nm、约10nm至约500nm、约10nm至约250nm、约10nm至约100nm、约10nm至约75nm或约10nm至约50nm)的表面。特征可以包括硅。与图2a和图2b中显示的示例性实施方案相比,具有组合的微米/纳米尺寸几何结构(例如,图2c和图2d)的硅颗粒可以具有比磨碎的颗粒更高的表面积。因此,可以通过期望的应用和规格来确定待使用的硅颗粒。尽管某些实施方案的硅颗粒在表面上具有纳米尺寸特征,但所述颗粒的总表面积可能与与纳米尺寸的颗粒相比更类似于微米尺寸的颗粒。例如,微米尺寸的硅颗粒(例如,从大颗粒磨碎的硅)通常具有大于约0.5m2/g且小于约2m2/g的平均表面积/单位体积(例如,使用布鲁诺-埃梅特-特勒(bet)颗粒表面积测量),而纳米尺寸的硅颗粒通常具有大于约100m2/g且小于约500m2/g的平均表面积/单位质量。本文描述的某些实施方案可以具有以下的平均表面积/单位质量:约1m2/g至约30m2/g、约1m2/g至约25m2/g、约1m2/g至约20m2/g、约1m2/g至约10m2/g、约2m2/g至约30m2/g、约2m2/g至约25m2/g、约2m2/g至约20m2/g、约2m2/g至约10m2/g、约3m2/g至约30m2/g、约3m2/g至约25m2/g、约3m2/g至约20m2/g、约3m2/g至约10m2/g(例如、约3m2/g至约6m2/g)、约5m2/g至约30m2/g、约5m2/g至约25m2/g、约5m2/g至约20m2/g、约5m2/g至约15m2/g或约5m2/g至约10m2/g。具有纳米尺寸特征的微米尺寸的硅颗粒的各种实例可以用于形成如本文描述的复合材料的某些实施方案。例如,图2e例示形成某些实施方案的复合材料的示例方法200。方法200包括提供多个硅颗粒(例如,具有约0.1μm至约30μm的平均粒度和包括纳米尺寸特征的表面的硅颗粒),方框210。方法200还包括形成包含前驱体和多个硅颗粒的混合物,方框220。方法200还包括热解前驱体(方框230),以将前驱体转化成一种或多种类型的碳相,以形成复合材料。关于方法200的方框210,具有本文描述的特性的硅可以合成为流化床反应器(fbr)方法的产物或副产物。例如,在fbr方法中,有用的材料可以在硅晶种材料上生长。通常,可以通过重力从反应器中去除颗粒。一些细微粒的硅材料可以从反应器的顶部离开反应器或者可以沉积在反应器的壁上。离开反应器的顶部或沉积在反应器的壁上的材料(例如,副产物材料)可以具有在微米级颗粒上的纳米级特征。在一些此类方法中,气体(例如,氮载气)可以通过硅材料。例如,硅材料可以是多个粒状硅。气体可以以足够高的速度通过硅材料以悬浮固体硅材料并且使其表现得像流体一样。方法可以在惰性气氛下,例如在氮气或氩气下进行。在一些实施方案中,也可以使用硅烷气体,例如,以允许在硅颗粒的表面上生长金属硅。从气相中生长的方法可以赋予硅颗粒独特的表面特性,例如纳米尺寸特征。由于硅通常以平滑形状(例如像玻璃)裂开,因此使用fbr方法形成的硅颗粒的某些实施方案可以有利地获得小特征,例如在纳米尺寸范围内的的小特征,这在通过从较大硅颗粒研磨而形成硅颗粒的一些实施方案中可能不容易获得。此外,由于fbr方法可以处于惰性气氛下,可以获得非常高纯度的颗粒(例如,比99.9999%更高的纯度)。在一些实施方案中,可以获得约99.9999%至约99.999999%的纯度。在一些实施方案中,fbr方法可以与太阳能级多晶硅的生产中使用的方法相似,同时比传统siemens方法少用85%的能量,其中在1150℃下,可以随着三氯甲硅烷的分解并且在高纯度硅棒上沉积额外的硅材料而形成多晶硅。因为纳米尺寸的硅颗粒在电化学电池中已表现出增强循环寿命性能,因此微米尺寸的硅颗粒还没有被考虑用作电化学电池中的电化学活性材料。对于方法200中的方框220和方框230,形成包含前驱体和多个硅颗粒的混合物,方框220,以及热解前驱体,方框230,以将前驱体转变为一种或多种类型的碳相,以分别形成与本文描述的方法100中的方框101和方框105相似的复合材料。在一些实施方案中,在低于硅的熔点(例如,约1414℃)的温度下发生热解(例如,约900℃至1350℃),而不影响硅颗粒的纳米尺寸特征。根据本文描述的某些实施方案,某些具有纳米表面特征的微米尺寸的硅颗粒可以实现高的能量密度,并且可以用于电化学电池中的复合材料和/或电极,以改善电池循环期间的性能。硅颗粒的表面改性如本文描述,硅颗粒可以用作电极中的电化学活性材料。在一些实施方案中,硅颗粒可以包括表面涂层。表面涂层可以包含通过碳化的前驱体与硅颗粒上的硅氧化物表面层之间的反应形成的碳化硅。在一些实施方案中,包含碳化硅的表面涂层可以用作循环期间硅颗粒的膨胀缓冲剂。不受理论束缚,硅颗粒的表面性质(例如,氧化物层的性质)可以影响形成的碳化硅层。硅与氧反应以产生氧化物层。例如,暴露于空气的硅表面具有薄的自然氧化物层。硅也可以与水反应(例如,水分处理的硅)以产生氧化物层。与氧形成的氧化物层可以具有不同于与水形成的氧化物层的性质。使用在本文描述的电极和/或电化学电池的各种实施方案中的水分处理的硅颗粒可以提供含有具有改善的性质的碳化硅的表面涂层。在一些情况下,可以提供更稳定和/或基本上稳定的固体电解质界面/相间(sei),改善容量保持率和循环性能。图3a示意性地示出了示例性水分处理的硅颗粒300。为了简化,图3a中的硅颗粒300被示出为具有圆形横截面形状,例如球形或圆柱形颗粒。然而,应理解,本文描述的“硅颗粒”300可以具有任何规则或不规则的横截面形状,并且不限于球形或圆柱形颗粒。继续参考图3a,示例性硅颗粒300包括块体材料301和表面302。如本文描述,硅颗粒300还可以具有外部区域303。例如,外部区域303可以从表面302延伸进入颗粒300一定距离。在一些情况下,外部区域303可以不同于块体材料301的其余部分。例如,与块体材料301的其余部分相比,外部区域303可以包括与干氧化物相对的湿氧化物。作为另一个实例,外部区域303可以包括由于存在水分(例如,氢氧化物)而形成的一个或多个层。在一些实施方案中,外部区域303可以被限定为从表面延伸约25nm、约20nm或约15nm深。其它实例也是可能的。在各种实施方案中,可以通过将水分添加至用作硅颗粒300的前驱体的硅材料中来生产水分处理的硅颗粒。例如,添加水分可以包括润湿和干燥。在一些实施方案中,润湿可以将液体和/或氧化剂引入硅材料中。液体可以包括水,例如去离子水、蒸馏水、纯水、超纯水和/或醇等。氧化剂可以包括氢氧化钾,过氧化氢等。可以用作前驱体的硅材料包括如本文描述的各种类型的硅材料,包括但不限于硅粉末、硅纤维、多孔硅、球磨的硅等。在一些实施方案中,可以将硅粉末(或其它硅材料)浸入液体和/或氧化剂中。硅粉末与液体和/或氧化剂之间的重量比可以是约1:1至约1:6或者在上述范围内的范围内。例如,重量比可以是约1:1、约1:2、约1:3、约1:4、约1:5、约1:6等。其它比率也是可能的。可以搅拌混合物以允许硅表面的润湿。在一些情况下,可以彻底地或基本上彻底地搅拌混合物,以允许硅表面完全润湿或基本上完全润湿。干燥可以减少(例如,在一些情况下去除)来自硅粉末的液体和/或氧化剂的量,以形成水分处理的硅颗粒300。在一些实施方案中,硅粉末可以在空气中或惰性气氛中干燥。例如,硅粉末可以在以下的温度下干燥:至少约140℃、至少约145℃、至少约150℃、至少约155℃、至少约160℃、至少约165℃、至少约170℃、至少约175℃、至少约180℃等。在一些情况下,硅粉末可以在约140℃至约180℃或在该范围内的范围内(例如,约145℃至约180℃、约150℃至约180℃、约155℃至约180℃、约155℃至约175℃等)的温度下干燥。在一些实施方案中,硅粉末可以在约150℃、约155℃、约160℃、约165℃、约170℃、约175℃、约180℃等下干燥。硅粉末可以经受干燥温度直到已经去除足够量的水分。例如,硅颗粒可以干燥至少约20小时、至少约21小时、至少约22小时、至少约23小时、至少约24小时。在一些情况下,硅粉末可以干燥约20小时至约28小时或在该范围内的范围内(例如,约20小时至约27小时,约22小时至约26小时等)的时间量。在一些实施方案中,将硅粉末干燥约21小时、约22小时、约23小时、约24小时、约25小时、约26小时、约27小时等。继续参考图3a,除了减少和/或去除硅颗粒中的水分以外,干燥还可以促进与块体材料301的其余部分不同的外部区域303的转化。在一些实施方案中,硅颗粒的块体材料301可以包含铝。具有大于约0.01%、大于约0.02%、大于约0.03%、大于约0.04%、大于约0.05%等的铝的硅材料(例如,硅粉末)可以具有在水分处理之后改变的某些特点和/或性质。不受理论束缚,与没有水分处理相比,水分处理可以允许块体材料301中的铝更多地暴露在表面302上。例如,可以对表面302进行改性,使得更多的铝被暴露和/或更多的铝被溶解并且重新分布(例如,铝朝向表面重新分布)。在一些情况下,在外部区域303中暴露更多的铝。在一些情况下,更多的铝溶解并且重新分布在外部区域303中,同时一些铝可以保留在被外部区域303包围的块体材料301内。在一些其它情况下,所有或基本上所有的铝可以暴露和/或溶解并且重新分布在硅颗粒300的外部区域303中。因此,在各种实施方案中,与未处理的硅颗粒的外部区域相比,水分处理的硅颗粒300的外部区域303可以包含更多的铝。不受理论束缚,当用于本文描述的复合材料时,水分处理的硅颗粒300的外部区域303中的铝可以影响在复合材料中形成的碳化硅层,例如产生更稳定的sei层。在一些实施方案中,水分处理的硅颗粒300的外部区域303可以包含一定量的铝,使得整体测量的铝占硅颗粒300的至少约0.01重量%。例如,硅颗粒可以包括至少约0.01%、至少约0.02%、至少约0.03%、至少约0.04%、至少约0.05%、至少约0.06%、至少约0.07%、至少约0.08%、至少约0.09%、至少约0.1%等的整体测量的铝。在一些实施方案中,整体测量的铝可以为硅颗粒的约0.01重量%至约1重量%、约0.02重量%至约1重量%、约0.03重量%至约1重量%、约0.04重量%至约1重量%、约0.05重量%至约1重量%、约0.06重量%至约1重量%、约0.07重量%至约1重量%、约0.08重量%至约1重量%、约0.09重量%至约1重量%、约0.1重量%至约0.6重量%、约0.1重量%至约0.7重量%、约0.1重量%至约0.8重量%、约0.1重量%至约0.9重量%、约0.1重量%至约1重量%、约0.2重量%至约0.6重量%、约0.2重量%至约0.7重量%、约0.2重量%至约0.8重量%、约0.2重量%至约0.9重量%、约0.2重量%至约1重量%、约0.3重量%至约0.6重量%、约0.3重量%至约0.7重量%、约0.3重量%至约0.8重量%、约0.3重量%至约0.9重量%、约0.3重量%至约1重量%。其它实例也是可能的。在一些实施方案中,可以通过x射线光电子能谱(xps)测量整体测量的铝。在xps中,可以通过照射x射线并且测量从样品逸出的电子的动能和数量来测量样品的元素组成。测量可以是表面敏感的,并且由此测量至少存在于硅颗粒的表面处(例如,至少在外部区域303中)的铝的量。根据测量灵敏度,在一些情况下,整体测量的铝可以提供在硅颗粒300的外部区域303中的铝的量或在硅颗粒300的整个材料中的铝的量(例如,在块体材料301内的外部区域303和其它区域中的铝的量)。可以使用本领域已知的或待开发的其它方法来测量铝的量。例如,在一些情况下,可以使用包括电感耦合等离子体原子发射光谱(icp-aes)或电感耦合等离子体质谱(icp-ms)的电感耦合等离子体(icp)分析来测量铝的量。作为另一个实例,在一些情况下,能量色散x射线光谱(eds)可以用于测量铝的量。作为另一个实例,在一些情况下,x射线荧光(xrf)可以用于测量铝的量。在一些实施方案中,硅颗粒300的外部区域303可以包含硅颗粒的至少约0.001重量%的量的铝。例如,硅颗粒300可以在外部区域303包含至少约0.001%、至少约0.002%、至少约0.003%、至少约0.004%、至少约0.005%的量的铝。在一些实施方案中,在外部区域303中的铝的量可以为硅颗粒的约0.001重量%至约0.01重量%、约0.002重量%至约0.01重量%、约0.003重量%至约0.01重量%、约0.004重量%至约0.01重量%、约0.005重量%至约0.01重量%等。在一些情况下,硅颗粒300的外部区域303可以包含至少约0.01%、至少约0.02%、至少约0.03%、至少约0.04%、至少约0.05%、至少约0.06%、至少约0.07%、至少约0.08%、至少约0.09%、至少约0.1%等的量的铝。在一些实施方案中,在外部区域303中的铝的量可以为硅颗粒的约0.01重量%至约1重量%、约0.02重量%至约1重量%、约0.03重量%至约1重量%、约0.04重量%至约1重量%、约0.05重量%至约1重量%、约0.06重量%至约1重量%、约0.07重量%至约1重量%、约0.08重量%至约1重量%、约0.09重量%至约1重量%、约0.1重量%至约0.6重量%、约0.1重量%至约0.7重量%、约0.1重量%至约0.8重量%、约0.1重量%至约0.9重量%、约0.1重量%至约1重量%、约0.2重量%至约0.6重量%、约0.2重量%至约0.7重量%、约0.2重量%至约0.8重量%、约0.2重量%至约0.9重量%、约0.2重量%至约1重量%、约0.3重量%至约0.6重量%、约0.3重量%至约0.7重量%、约0.3重量%至约0.8重量%、约0.3重量%至约0.9重量%、约0.3重量%至约1重量%等。其它实例也是可能的。在各种实施方案中,在硅颗粒300的外部区域303中的铝可以包括氧化铝、硅化铝或氧化铝和硅化铝的组合。在一些实施方案中,水分处理的硅颗粒300可以具有表面302,其提供比未处理的硅颗粒的表面提供的接触角更低的接触角。水分处理的硅颗粒300的一些实施方案可以具有小于约87.3o、小于约87.2o、小于约87.1o、小于约87o、小于约86.9o、小于约86.8o、小于约86.7o、小于约86.6o、小于约86.5o等的平均接触角。例如,一些水分处理的硅颗粒可以具有约80o至约87.2o或在其间的范围内(例如,约80o至约87.1o、约80o至约87o、约80o至约86.9o、约81o至约87.1o、约81o至约87o、约81o至约86.9o、约82o至约87.1o、约82o至约87o、约82o至约86.9o等)的平均接触角。不受理论束缚,通过具有比未处理的硅颗粒的表面提供的接触角更低的接触角,水分处理的硅颗粒300的各种实施方案可以包括具有更高润湿性的表面,允许增加在浆料中的可混合性,例如在形成本文描述的复合材料的各种实施方案的混合物中。例如,水分处理的硅颗粒的各种实例可以用于形成如本文描述的复合材料的某些实施方案。例如,复合材料可以用于电化学电池的电极中。水分处理的硅颗粒可以具有如本文描述的可以改善容量保持率和循环性能的某些特点和/或性质。不受理论束缚,水分处理的硅颗粒具有可以提供更稳定和/或基本上稳定的sei的表面。某些实施方案可以包含复合材料膜。复合材料膜可以包括本文描述的复合材料膜的任何实例。例如,复合材料膜可以具有大于0重量%且小于约99重量%(例如,约50重量%至约99重量%、约60重量%至约99重量%、约70重量%至约99重量%、约75重量%至约99重量%、约80重量%至约99重量%等)的硅颗粒、或者大于0重量%且小于约95重量%(例如,约50重量%至约95重量%、约60重量%至约95重量%、约70重量%至约95重量%、约75重量%至约95重量%、约80重量%至约95重量%等)的硅颗粒。硅颗粒可以包括水分处理的硅颗粒和/或水分处理的硅颗粒和本文描述的其它硅颗粒的组合(例如,平均粒度为约0.1μm至约40μm的硅颗粒、平均粒度为约1μm至约20μm的硅颗粒、具有纳米尺寸特征的微米尺寸的硅颗粒等)。硅颗粒可以包含如本文描述的铝。硅颗粒可以是约90%至约99%的纯硅。如本文描述,硅颗粒可以具有包含碳化硅或碳和碳化硅的混合物的表面涂层,如图1b中显示。表面涂层可以是基本上连续的层。在一些实施方案中,表面涂层可以包含一氧化硅(sio)、二氧化硅(sio2)和/或硅氧化物(siox)。复合材料膜还可以具有大于0重量%且小于90重量%的一种或多种类型的碳相。一种或多种类型的碳相可以是基本上连续的相。在一些实施方案中,一种或多种类型的碳相可以是电化学活性的和/或导电的。在各种实施方案中,复合材料膜可以是自支撑的。图3b示出了形成复合材料的某些实施方案的示例性方法400。方法400可以包括提供包含碳前驱体和硅颗粒(例如,水分处理的硅颗粒)的混合物,方框410。方法400还可以包括热解前驱体以将前驱体转化成一种或多种类型的碳相,方框420。方法400还可以包括在硅颗粒的表面上形成碳化硅,方框430。关于方法400的方框410,可以通过使用水分处理的硅颗粒来提供具有如本文描述的特点和/或性质的硅颗粒。在一些实施方案中,水分处理的硅颗粒可以包括以多种方式中的一种或多种用液体和/或水分处理的硅材料。可以通过如本文描述的润湿和干燥来提供水分处理的硅颗粒。例如,可以在液体中加工硅材料。在一些实施方案中,液体可以包括水(例如,去离子水、蒸馏水、纯水,超纯水等)、醇和/或其它氧化剂,例如氢氧化钾或过氧化氢。硅材料可以在液体中煮沸以产生经液体煮沸的硅颗粒,在液体中倾析以产生经液体倾析的硅颗粒,和/或用液体蒸制以产生经液体蒸制的硅颗粒。如本文描述,可以将硅颗粒添加至包含碳前驱体的混合物中。在一些此类实施方案中,替代单独用水分处理硅材料或除了单独用水分处理硅材料以外,可以用存在于和/或添加至碳前驱体中的水分处理硅颗粒。例如,如本文描述,碳前驱体可以包含聚合物和溶剂。水分可以存在于聚合物中和/或添加至聚合物和/或溶剂中。聚合物和溶剂可以包括本文描述的任何聚合物和溶剂。作为一些实例,碳前驱体可以包括聚酰胺酰亚胺、聚酰胺酸、聚酰亚胺、酚醛树脂、环氧树脂等。溶剂可以包括n-甲基-吡咯烷酮(nmp)、丙酮、二乙醚、γ-丁内酯、异丙醇、碳酸二甲酯、碳酸乙酯、二甲氧基乙烷、乙醇、甲醇等。可以将水分添加至聚合物和/或溶剂中。在一些情况下,碳前驱体可以包括水溶性聚合物,并且溶剂可以包括水。硅材料可以单独或与混合物组合进行热处理以干燥颗粒。硅颗粒的润湿和干燥可以顺序地进行。然而,在一些实施方案中,可以同时进行硅颗粒的润湿和干燥。例如,可以将水分添加至干燥/加热室中,并且可以将硅材料单独或与混合物组合放置在加热室中。可以在如本文描述的温度和时间下进行热处理。如本文描述,方法400还可以包括各种步骤,例如将混合物浇铸在衬底上、干燥混合物以形成膜、从衬底上移除膜以及将膜放置在热压机中。可以在这些步骤中的任一个中将水分添加至混合物或膜中。替代将水分单独添加至硅材料中或除了将水分单独添加至硅材料中以外,可以将水分添加至混合物或膜中。关于方法400的方框420,可以如本文描述热解碳前驱体,以将前驱体转化成一种或多种类型的碳相。在一些实施方案中,可以在热解室中添加水分。替代将水分单独添加至硅材料中或除了将水分单独添加至硅材料中以外,替代将水分添加至混合物或膜中或除了将水分单独添加至硅材料中以外,和/或替代将水分添加进干燥室或除了将水分添加进干燥室以外,可以将水分添加在热解室中。关于方框430,可以在硅颗粒的表面上形成碳化硅。使用具有如本文描述的某些表面特点和性质的硅颗粒(例如,使用水分处理的硅颗粒)可以影响形成的碳化硅层并且形成更稳定的sei。如本文描述,水分处理的硅颗粒可以具有有益于生产用于电化学电池的电极中的复合材料的某些特点和性质。应理解,可以提供具有本文描述的期望的特点和性质而未经水分处理的硅颗粒。一些此类未经水分处理的硅颗粒也可以用于复合材料和/或用于形成复合材料的方法中。实施例以下用于阳极制造的示例性方法通常包括将组分混合在一起,将那些组分浇铸在可移除的衬底上,干燥、固化、移除衬底,然后热解得到的样品。通常,将n-甲基-2-吡咯烷酮(nmp)用作溶剂以改变任何混合物的粘度并且使其可使用刮片方法浇铸。实施例1在实施例1中,使用spex8000d机器,将聚酰亚胺液态前驱体(来自hdmicrosystemscorp.的pi2611)、石墨颗粒(来自timcalcorp.的slp30)、导电碳颗粒(来自timcalcorp.的superp)和硅颗粒(来自alfaaesarcorp.)以200:55:5:20的重量比一起混合5分钟。然后,将混合物浇铸在铝箔上并且使其在90℃的烘箱中干燥以去除溶剂,例如,nmp。其后在可忽略的压力下,在热压机中在200℃下进行固化步骤,持续至少12小时。然后,通过在12.5%的hcl溶液中蚀刻去除铝箔衬垫。然后,在di水中冲洗剩余的膜、干燥,然后在氩气流下在1175℃下热解约1小时。方法产生15.8重量%的pi2611衍生的碳、57.9重量%的石墨颗粒、5.3重量%的由superp产生的碳和21.1重量%的硅的组合物。然后,在袋式电池配置中相对于锂nmc氧化物阴极测试得到的电极。图4中显示典型的循环图。实施例2在实施例2中,首先使用turbula混合器将1:9重量比的硅颗粒(来自evnanoadvancedchemicalmaterialsco.,ltd.)与nmp混合1小时。然后,将聚酰亚胺液态前驱体(来自hdmicrosystemscorp.的pi2611)、石墨颗粒(来自timcalcorp.的slp30)和碳纳米纤维(来自pyrografcorp.的cnf)以200:55:5:200的重量比添加至si:nmp混合物中,并且涡旋约2分钟。然后,将混合物浇铸在覆盖有21μm厚的铜网的铝箔上。然后,使样品在90℃的烘箱中干燥以去除溶剂,例如,nmp。其后在可忽略的压力下,在热压机中在200℃下进行固化步骤,持续至少12小时。然后,通过在12.5%的hcl溶液中蚀刻去除铝箔衬垫。然后,在di水中冲洗剩余的膜、干燥,然后在氩气下在1000℃下热解约1小时。方法产生15.8重量%的pi2611衍生的碳、57.9重量%的石墨颗粒、5.3重量%的cnf和21.1重量%的硅的组合物。然后,在袋式电池配置中相对于锂nmc氧化物阴极测试得到的电极。图5中显示典型的循环图。实施例3在实施例3中,使用turbula混合器将聚酰亚胺液态前驱体(来自hdmicrosystemscorp.的pi2611)和325目的硅颗粒(来自alfaaesarcorp.)以40:1的重量比一起混合1小时的持续时间。然后,将混合物浇铸在铝箔上并且使其在90℃的烘箱中干燥以去除溶剂,例如,nmp。其后在可忽略的压力下,在热压机中在200℃下进行固化步骤,持续至少12小时。然后,通过在12.5%的hcl溶液中蚀刻去除铝箔衬垫。然后,在di水中冲洗剩余的膜、干燥,然后在氩气流下在1175℃下热解约1小时。方法产生75重量%的pi2611衍生的碳和25重量%的硅的组合物。然后,在袋式电池配置中相对于锂nmc氧化物阴极测试得到的电极。图6中显示典型的循环图。实施例4在实施例4中,使用涡旋仪,将硅微粒(来自alfaaesarcorp.)、聚酰亚胺液态前驱体(来自hdmicrosystemscorp.的pi2611)、石墨颗粒(来自timcalcorp.的slp30)、磨碎的碳纤维(来自fibreglastdevelopmentscorp.)、碳纳米纤维(来自pyrografcorp.的cnf)、碳纳米管(来自cnanotechnologylimited)、导电碳颗粒(来自timcalcorp.的superp)、导电石墨颗粒(来自timcacorp.的ks6)以20:200:30:8:4:2:1:15的重量比混合5分钟。然后,将混合物浇铸在铝箔上。然后,使样品在90℃的烘箱中干燥以去除溶剂,例如,nmp。其后在可忽略的压力下,在热压机中在200℃下进行固化步骤,持续至少12小时。然后,通过在12.5%的hcl溶液中蚀刻去除铝箔衬垫。然后,在di水中冲洗剩余的膜、干燥,然后在氩气下在1175℃下热解约1小时。方法产生与初始混合物类似的组合物,但具有为聚酰亚胺前驱体的初始重量的7.5%的pi2611衍生的碳部分。然后,在袋式电池配置中相对于锂nmc氧化物阴极测试得到的电极。图7中显示典型的循环图。实施例5在实施例5中,使用turbula混合器将聚酰亚胺液态前驱体(来自hdmicrosystemscorp.的pi2611)和硅微粒(来自alfaaesarcorp.)以4:1的重量比一起混合1小时的持续时间。然后,将混合物浇铸在覆盖有碳遮蔽物(来自fibreglastdevelopmentscorporation)铝箔上并且使其在90℃的烘箱中干燥以去除溶剂,例如,nmp。其后在可忽略的压力下,在热压机中在200℃下进行固化步骤,持续至少12小时。然后,通过在12.5%的hcl溶液中蚀刻去除铝箔衬垫。然后,在di水中冲洗剩余的膜、干燥,然后在氩气流下在1175℃下热解约1小时。方法产生约23重量%的pi2611衍生的碳、76重量%的硅的组合物,并且遮蔽物的重量是可忽略的。然后,在袋式电池配置中相对于锂镍锰钴氧化物(nmc)阴极测试得到的电极。图8中显示典型的循环图。实施例6在实施例6中,使用spex8000d机器将聚酰亚胺液态前驱体(来自hdmicrosystemscorp.的pi2611)、石墨颗粒(来自timcalcorp.的slp30)和硅微粒(来自alfaaesarcorp.)以为200:10:70重量比一起混合5分钟。然后,将混合物浇铸在铝箔上并且使其在90℃的烘箱中干燥以去除溶剂(例如,nmp)。在可忽略的压力下,在热压机中在200℃下进行固化步骤,持续至少12小时。然后,通过在12.5%的hcl溶液中蚀刻去除铝箔衬垫。然后,在di水中冲洗剩余的膜、干燥,然后在氩气流下在1175℃下热解约1小时。方法产生15.8重量%的pi2611衍生的碳、10.5重量%的石墨颗粒、73.7重量%的硅的组合物。然后,在袋式电池配置中相对于锂nmc氧化物阴极测试得到的电极。阳极被充电至各个循环600mah/g并且记录每循环的放电容量。图9中显示典型的循环图。实施例7在实施例7中,将pvdf和硅颗粒(来自evnanoadvancedchemicalmaterialsco)、导电碳颗粒(来自timcalcorp.的superp)、导电石墨颗粒(来自timcalcorp.的ks6)、石墨颗粒(来自timcalcorp.的slp30)和nmp以5:20:1:4:70:95的重量比混合。然后,将混合物浇铸在铝衬底上并且将其放置在90℃的烘箱中以去除溶剂,例如,nmp。然后,在袋式电池配置中相对于锂nmc氧化物阴极测试得到的电极。图10中显示典型的循环图。实施例8进行多个实验以获得以下条件的影响:改变聚酰亚胺衍生的碳(例如,2611c)的百分比,同时降低石墨颗粒(来自timcalcorp.的slp30)的百分比,并且将硅微粒(来自alfaaesarcorp.)的百分比保持在20wt.%。如图11a和图11b中显示,结果显示通过增加比容量同时降低不可逆容量,更多的石墨和更少的2611c有利于电池性能。最小化2611c不利地影响了得到的阳极的强度,因此在一个实施方案中,接近20wt.%的值可以优选作为折衷。实施例9与实施例8类似,如果将2611c保持在20wt.%,并且以石墨颗粒为代价来增加si的百分比,则得到的电极的首次循环放电容量增加。图12显示更高的硅含量能制备性能更好的阳极。实施例10根据实施例1中的程序热解并且测试1密耳厚的聚酰亚胺片。将可逆容量和不可逆容量作为热解温度的函数图绘。图13表明在一个实施方案中,优选在约1175℃下热解聚酰亚胺片(ubecorp的upilex)。附加实施例图14是4.3cm×4.3cm的不含金属箔支撑层的复合阳极膜的照片。复合阳极膜具有约30微米的厚度,并且具有约15.8重量%的pi2611衍生的碳、约10.5重量%的石墨颗粒和约73.7重量%的硅的组合物。图15至图20是复合阳极膜的扫描电子显微镜(sem)显微照片。复合阳极膜的组成为约15.8重量%的pi2611衍生的碳、约10.5重量%的石墨颗粒和约73.7重量%的硅。图15和图16显示在进行循环之前(离焦部分是阳极的底部部分并且聚焦部分是复合膜的裂开的边缘)。图17、图18和图19分别是在进行循环10次循环、10次循环和300次循环之后复合阳极膜的sem显微照片。sem显微照片显示硅没有任何显著的粉碎,并且阳极在循环之后不具有在其顶部上建立的固体电解质界面/相间(sei)的过度的层。图20是复合阳极膜横截面的sem显微照片。以下描述了示例性硅颗粒的测量性质。出于示例性目的讨论这些实施例,但这些实施例不应解释为限制公开的实施方案的范围。图21是样品硅颗粒的x射线粉末衍射(xrd)图。xrd图表明样品硅颗粒的性质基本上是晶体或多晶。图22至图25是样品硅颗粒的扫描电子显微镜(sem)显微照片。尽管sem显微照片似乎显示硅颗粒可以具有比测量的约300nm的平粒度更大的平均粒度,但不受理论束缚,颗粒被认为已经团聚在一起,表现为更大的颗粒。图26是样品硅颗粒的化学分析。化学分析表明硅颗粒基本上是纯硅。图27a和图27b是两个具有纳米尺寸特征的微米尺寸的硅颗粒的示例性粒度柱状图。通过fbr方法制备颗粒。示例性硅颗粒可以具有粒度分布。例如,至少90%的颗粒可以具有约5μm至约20μm(例如,约6μm至约19μm)的粒度,例如直径或最大尺寸。至少约50%的颗粒可以具有约1μm至约10μm(例如,约2μm和约9μm)的粒度。此外,至少约10%的颗粒可以具有约0.5μm至约2μm(例如,约0.9μm和1.1μm)的粒度。图28是对比两种类型的示例性硅颗粒在电池循环期间的放电容量的图绘。将通过fbr方法制备的四种硅颗粒(具有纳米尺寸特征的微米尺寸的颗粒)样品的性能与通过磨碎较大的硅颗粒而制备的五种硅颗粒样品的进行比较。因此,具有组合的微米/纳米几何结构(例如,通过fbr方法制备)的硅颗粒的某些实施方案可以具有相对于硅颗粒的各种其它实施方案(例如,通过磨碎较大的硅颗粒而制备的微米尺寸的硅颗粒)的增强的性能。可以针对预期或期望的应用和规格调整待使用的硅颗粒的类型。水分处理的硅颗粒的实例将硅粉末以1:4的重量比浸入去离子水中。将混合物彻底搅拌并且在160℃干燥24小时。图29示出了与未处理的硅颗粒相比,在示例性水分处理的硅颗粒中铝2p峰的x射线光电子能谱(xps)光谱。如图29中显示,水分处理的硅颗粒具有特征铝峰,表明在表面处存在铝。氧化铝和/或硅化铝以大于0.001%(例如,大于0.01%、大于0.1%等)的量存在于硅颗粒的外部区域(例如,约20nm的深度)中。不受理论束缚,水分处理可以允许在表面处有更多的铝。表i包括对于示例性水分处理的硅颗粒的不同样品的接触角(ca)测量。通过使用力张力计的washburn方法测量接触角(ca)。表i.样品1样品2ca-测量187.07284.821ca-测量282.90982.646ca-测量384.29485.104ca-平均值84.75884.190ca-标准偏差2.1201.345如表1中显示,样品的平均接触角为84.19°和84.76°。在水分处理之前测量的接触角高于(例如,大于87.2°)处理之后测量的接触角。将本文描述的样品与石墨、nmp和树脂混合。将混合物形成阳极前驱体(例如,涂覆在衬底上,干燥,并且从衬底上移除),并且将其热解以形成如本文描述的自支撑阳极膜。相对于基于锂钴氧化物(lco)的阴极构建样品阳极以形成蓄电池。图30示出了样品蓄电池的容量保持率与循环数的图。如图30中显示,与具有未处理的硅颗粒的蓄电池相比,具有水分处理的硅颗粒的蓄电池在400次循环时的容量保持率提高了30%。如本文描述,硅颗粒的水分处理可以提供相对简单和实用的方法来控制电极中的sei形成并且显著改善电化学电池性能。水分处理还可以提供减少电池间性能变化的方法,所述方法可以使产品更稳定并且更不依赖于方法变化。此外,硅颗粒的水分处理可以提供控制活性颗粒中的初始锂化水平的方法,所述方法可以允许更均匀的锂化和应力,并且减少可以加速衰落的局部反应和浓缩反应。此外,尽管本文描述的各种实施方案包括用于锂离子蓄电池的硅颗粒,但硅颗粒可以用于其它蓄电池系统,所述其它蓄电池系统涉及硅-金属合金化方法,例如钠或镁系统。以上已经描述了各种实施方案。尽管已经参考这些具体实施方案描述了本发明,但描述旨在是说明性的而不旨在限制。在不背离如所附权利要求中限定的本发明的真实主旨和范围的情况下,本领域技术人员可以进行各种修改和应用。当前第1页12