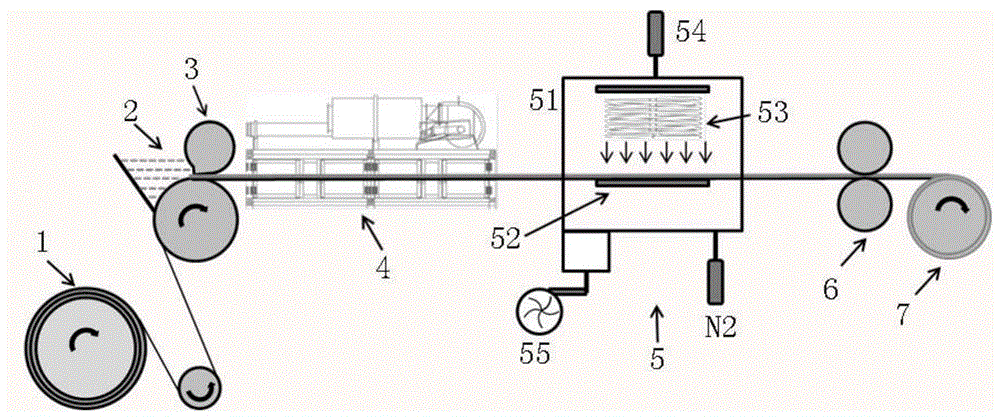
本发明属于锂离子电池
技术领域:
,尤其涉及一种锂离子电池极片及其制备方法和锂离子电池。
背景技术:
:锂离子电池作为一种化学电源,具有能量密度高、循环寿命长、无记忆效应等优点,在电动汽车及移动电子设备领域取得了广泛的应用。但是,锂离子电池往往充电时间较长,不能满足电动车辆及电子设备的快速充电要求,在很大程度上限制了锂离子电池的广泛应用。影响电池功率性能的一个重要因素就是正负极片中的导电剂。目前,常见的导电剂包括导电炭黑、石墨、碳纳米管以及石墨烯。其中石墨烯作为一种新型导电剂材料引起了广泛的关注,该材料具有比表面积大、电导率高、导热性好等优点。相关研究表明,二维结构的石墨烯和活性物质之间可以实现点-面接触,更利于建立导电网络,极片中仅需要极低的添加量就能满足电池快速充放电的电子导电需求。虽然就电子导电性而言,石墨烯相比于其他导电剂具有非常明显的优势。但是锂离子无法穿过石墨烯的二维平面,因此石墨烯的平面结构会对锂离子的传输产生位阻效应,以石墨烯为导电剂的电极片,锂离子的传导路径更曲折,离子导电能力比导电炭黑要差。尤其是在较大倍率充放电时,石墨烯的空间位阻效应会大大增加锂离子的传输难度,使电池的功率性能变差。技术实现要素:本发明针对上述技术问题,提出一种锂离子电池极片及其制备方法和锂离子电池。为了达到上述目的,本发明一方面提供一种锂离子电池极片的制备方法,包括以下步骤:(1)制备浆料:将电化学活性材料、石墨烯或石墨烯和炭黑、分散剂、粘结剂和溶剂混合,搅拌均匀形成浆料;(2)浆料涂布:将制备获得的浆料涂布到集流体上并对涂层进行干燥,得到干燥后的极片;(3)等离子体刻蚀:在室温下采用等离子体刻蚀设备对干燥后的极片进行刻蚀,等离子体刻蚀设备包括供气系统、刻蚀腔和真空系统;等离子体刻蚀包括以下步骤:将极片传送至刻蚀腔内并与刻蚀腔内的下电极接触,对刻蚀腔密封并进行抽真空;供气系统将刻蚀气体送入刻蚀腔内的耦合线圈,经过辉光放电形成等离子体;等离子体在电场作用下沿垂直于极片的方向对极片涂层进行轰击,在涂层中形成垂直于极片表面的孔洞;向刻蚀腔内通入惰性气体,将刻蚀完成的极片送出刻蚀腔,进行下一段极片的等离子体刻蚀处理;(4)完成刻蚀的极片经压延、收卷备用。作为优选,经步骤(3)等离子体刻蚀处理后,在极片涂层中所形成的孔洞的孔径范围为500~1000nm。作为优选,步骤(3)等离子体刻蚀过程中,设定icp射频功率≤200w,rf射频功率<60w,刻蚀时间<3min。作为优选,步骤(3)中,刻蚀气体为氧气和cf4的混合气体,氧气与cf4的体积比为(1~4):10,气体流速为10~30cm3/min。作为优选,所述锂离子电池极片为磷酸铁锂、三元材料、锰酸锂或钴酸锂正极极片,或者钛酸锂负极极片。作为优选,所述锂离子电池极片为磷酸铁锂正极极片,所述电化学活性材料为磷酸铁锂,所述分散剂为聚乙烯吡咯烷酮,所述粘结剂为聚偏氟乙烯,所述溶剂为n-甲基吡咯烷酮。作为优选,所述步骤(1)具体包括以下步骤:(1a)石墨烯预分散:将聚乙烯吡咯烷酮加入到n-甲基吡咯烷酮中搅拌至充分溶解,随后加入石墨烯,搅拌均匀,得石墨烯分散液;(1b)混合制浆:将聚偏氟乙烯加入到n-甲基吡咯烷酮中,以100~500rmp转速搅拌至充分溶解,向其中加入一半的石墨烯分散液,以100~500rmp转速搅拌10~30min,随后边搅拌边慢慢加入磷酸铁锂,待磷酸铁锂全部加入后继续搅拌30~60min,然后加入剩余的另一半石墨烯分散液,以1000~2500rmp转速高速搅拌1~5h,对体系抽真空并以100~500rmp转速搅拌30~60min以消除浆料中的气泡;(1c)检测:取出浆料,测定粘度后过筛备用。作为优选,按重量份数计,各组分的加入量为:步骤(1a)中所述聚乙烯吡咯烷酮为0.1~1份,所述n-甲基吡咯烷酮为10份,所述石墨烯为1~5份;步骤(1b)中所述聚偏氟乙烯为1~3份,所述n-甲基吡咯烷酮为30~50份,所述磷酸铁锂为45~55份。本发明另一方面提供一种根据上述任一项所述锂离子电池极片的制备方法制备获得的锂离子电池极片。本发明再一方面提供一种包括上述锂离子电池极片的锂离子电池。与现有技术相比,本发明的优点和积极效果在于:1、本发明所提供的锂离子电池极片的制备方法,通过采用等离子体刻蚀的方法,对极片内水平方向分布的石墨烯进行选择性刻蚀,有利于锂离子在极片中的传输,降低了石墨烯的位阻效应,大大增强了锂离子电池极片的离子导电能力。2、本发明所提供的锂离子电池极片和锂离子电池,具有高的电子导电率和离子导电率,功率性能好,可以进行大电流充放电。附图说明图1为本发明实施例所提供的锂离子电池极片制备方法的流程示意图;图2为本发明实施例所提供的等离子体刻蚀作用原理示意图;图3为等离子体刻蚀对电池高倍率放电性能影响的测试结果图;图4为电池循环寿命测试结果图;图中:1、集流体;2、浆料;3、自动涂布机;4、烘干机;5、等离子体刻蚀设备;51、刻蚀腔;52、下极板;53、耦合线圈;54、供气系统;55、真空系统;6、压延;7、收卷。具体实施方式下面将对本发明实施例中的技术方案进行清楚、完整地描述,显然,所描述的实施例仅仅是本发明一部分实施例,而不是全部的实施例。基于本发明中的实施例,本领域普通技术人员在没有做出创造性劳动前提下所获得的所有其他实施例,都属于本发明保护的范围。本发明实施例一方面提供一种锂离子电池极片的制备方法,图1为所述制备方法的流程示意图,包括以下步骤:(1)制备浆料2:将电化学活性材料、石墨烯或石墨烯和炭黑、分散剂、粘结剂和溶剂混合,搅拌均匀形成浆料2;(2)浆料涂布:将制备获得的浆料2涂布到集流体1上并对涂层进行干燥,得到干燥后的极片;(3)等离子体刻蚀:在室温下采用等离子体刻蚀设备5对干燥后的极片进行刻蚀,等离子体刻蚀设备包括供气系统54、刻蚀腔51和真空系统55;等离子体刻蚀包括以下步骤:将极片传送至刻蚀腔51内并与刻蚀腔51内的下电极52接触,对刻蚀腔51密封并进行抽真空;供气系统54将刻蚀气体送入刻蚀腔51内的耦合线圈53,经过辉光放电形成等离子体;等离子体在电场作用下沿垂直于极片的方向对极片涂层进行轰击,在涂层中形成垂直于极片表面的孔洞;向刻蚀腔51内通入惰性气体,将刻蚀完成的极片送出刻蚀腔51,进行下一段极片的等离子体刻蚀处理;(4)完成刻蚀的极片经压延6、收卷7备用。如图2所示,未经等离子体刻蚀的锂离子电池极片,在极片涂层内存在横向阻断锂离子传输的石墨烯片状结构,降低锂离子的传输效率,进而使得离子导电能力降低。本发明上述实施例制备获得的锂离子电池极片,针对加入石墨烯作为导电剂的锂离子电池,通过采用等离子体刻蚀的方法在极片涂层中沿垂直方向开孔,对极片内水平方向分布的石墨烯进行选择性刻蚀,既不影响极片涂层垂直方向的电子电导率,又能改善电极涂层的离子电导率,增加极片中与集流体平面垂直的通道,有利于锂离子在极片中的传输,降低了石墨烯的位阻效应,大大增强了锂离子电池极片的离子导电能力,有利于电极和电解液的浸润以及电池的大电流充放电。作为一可选实施例,在进行等离子体刻蚀初始时,对刻蚀腔51进行抽真空的操作可以选择通过真空泵进行抽真空至压强<0.5pa,但可以理解的是,还可以选择能实现抽真空效果的其它现有方式。作为一优选实施例,经步骤(3)等离子体刻蚀处理后,在极片涂层中所形成的孔洞的孔径范围为500~1000nm,进一步地,优选为500nm,孔径在该值左右时,极片的高倍率充放电性能最优。作为一优选实施例,步骤(3)中,等离子体刻蚀过程中设定icp射频功率≤200w,rf射频功率<60w,刻蚀时间<3min。其中,所述刻蚀时间是从等离子体开始轰击涂层开始起算至轰击结束终止。等离子体密度过高,会造成支撑涂层的集流体铝箔或铜箔被击穿,破坏涂层的稳定性,而等离子体密度过低,会使得开孔效果不好。本实施例通过优化选择合理的icf射频功率、rf射频功率并控制刻蚀时间,从而控制刻蚀腔51内等离子体的密度,使等离子体在强电场作用下加速,获得较高的动能,垂直向地轰击涂层,使得开孔效果最佳。作为一优选实施例,步骤(3)中,刻蚀气体为氧气和cf4的混合气体,氧气与cf4的体积比为(1~4):10,气体流速为10~30cm3/min。刻蚀气体经过辉光放电失去电子变成o、f、cfx等离子体。其中,氧等离子体会与石墨烯中的c原子反应,产生各向异性的刻蚀,只有与极片表面平行的石墨烯会被等离子体击穿,留下孔洞;氟等离子体会与极片涂层中的电化学活性材料或粘结剂发生较弱的物理刻蚀。涂层经过等离子体的轰击,产生均匀分布的与极片平面垂直的孔洞,可用于电解液中锂离子的传输,大大降低了电极涂层中石墨烯的空间位阻,且利于电解液和电极的浸润。在本实施例中,可以理解的是,氧气与cf4的体积比还可以为1:5、3:10、1:9等,气流流速还可以为15cm3/min、20cm3/min、25cm3/min等,本领域技术人员可以根据实际情况在上述范围内进行选择。本发明所提供的锂离子电池极片的制备方法可用于磷酸铁锂、三元材料、锰酸锂或钴酸锂正极极片,或者钛酸锂负极极片的制备,均可改善锂离子的传输,提高离子导电能力。以所制备的锂离子电池极片为磷酸铁锂正极极片为例。此时,作为优选,所述电化学活性材料为磷酸铁锂,所述分散剂为聚乙烯吡咯烷酮,所述粘结剂为聚偏氟乙烯,所述溶剂为n-甲基吡咯烷酮。采用以下优选实施例进行制备。所述步骤(1)制备浆料2具体包括以下步骤:(1a)石墨烯预分散:将聚乙烯吡咯烷酮(以下简称pvp)加入到n-甲基吡咯烷酮(以下简称nmp)中搅拌至充分溶解,随后加入石墨烯,搅拌均匀,得石墨烯分散液;(1b)混合制浆:将聚偏氟乙烯(以下简称pvdf)加入到nmp中,以100~500rmp转速搅拌至充分溶解,向其中加入通过步骤(1a)制备获得的一半的石墨烯分散液,以100~500rmp转速搅拌10~30min,随后边搅拌边慢慢加入磷酸铁锂,待磷酸铁锂全部加入后继续搅拌30~60min,然后加入剩余的另一半石墨烯分散液,以1000~2500rmp转速高速搅拌1~5h,对体系抽真空并以100~500rmp转速搅拌30~60min以消除浆料2中的气泡;(1c)检测:取出浆料2,测定粘度后过筛备用。在上述制备浆料2的实施例中,关于步骤(1a),需要说明的是,由于石墨烯用作导电剂是一种片状二维结构,比表面积大,不易分散,因此需要对石墨烯进行预分散处理;其中pvp作为分散剂可以防止石墨烯的团聚。搅拌可以选用高剪切力搅拌桨,以大于1000rmp的转速充分搅拌,或者采用超声分散仪超声30min,得到石墨烯分散液。通过上述实施例制备获得的磷酸铁锂正极极片用浆料2,使用分散剂对石墨烯进行预分散,并且将石墨烯分散液分批依次与活性材料等其它材料混合搅拌,石墨烯分散均匀且电子导电性极高,形成均匀的导电网络,有利于后续的浆料涂布以及获得高能量密度的电池。作为上述实施例的优选,按重量份数计,各组分的加入量为:步骤(1a)中所述pvp为0.1~1份,所述nmp为10份,所述石墨烯为1~5份;步骤(1b)中所述pvdf为1~3份,所述nmp为30~50份,所述磷酸铁锂为45~55份。对应上述制浆方法,优化各步骤中各组分的用量,在降低了石墨烯材料的用量的情况下,提高了导电性能。在步骤(2)浆料涂布的过程中,本实施例优选20μm厚的铝箔作为集流体1,将经步骤(1)制备获得的浆料2转移到自动涂布机3上,采用刮刀涂布或挤压式涂布的方式完成极片的涂布,并通过烘干机4采用80~120℃的温度对极片进行干燥。但可以理解的是,本领域技术人员还可以选用其它金属箔作为集流体1,如铜箔,并且集流体1的厚度可根据实际情况调整;还可以选用其它现有可实现涂布的方法,只要实现浆料的均匀涂布即可;干燥温度还可以在上述范围内选择90℃、100℃、110℃等。采用前述步骤(3)等离子体刻蚀的实施例对经步骤(1)和步骤(2)获得的极片进行刻蚀,最终制备获得具有纳米级孔洞的磷酸铁锂正极极片。本发明实施例的另一方面还提供一种根据上述任一实施例所述锂离子电池极片的制备方法制备获得的锂离子电池极片。本发明实施例的再一方面提供一种包括上述锂离子电池极片的锂离子电池。通过本发明实施例所获得的锂离子电池极片和锂离子电池,具有高的电子导电率和离子导电率,功率性能好,可以进行大电流充放电。为了更清楚详细地介绍本发明实施例所提供的锂离子电池极片的制备方法,下面将结合具体实施例进行描述。实施例1(1)制备浆料:将0.5gpvp加入到10gnmp中,搅拌至pvp充分溶解,随后加入1g石墨烯,搅拌均匀,得石墨烯分散液;将2gpvdf加入到40gnmp中,以100rmp转速低速搅拌30min至pvdp充分溶解,向其中加入一半的石墨烯分散液,以100rmp转速搅拌10min,随后边搅拌边慢慢加入46.5g磷酸铁锂,待磷酸铁锂全部加入后继续低速搅拌30min,然后加入剩余的另一半石墨烯分散液,以2000rmp转速高速搅拌2h;充分分散后,对体系抽真空并以100rmp转速低速搅拌30min以消除浆料中的气泡;取出浆料,测定粘度约为6000cp,过筛备用。(2)浆料涂布:将制备获得的浆料转移到自动涂布机上,选用20μm厚的铝箔作为集流体,采用刮刀涂布的方式完成极片的涂布,并对涂层进行干燥,干燥温度为80℃。(3)等离子体刻蚀:将干燥后的极片传送至刻蚀腔内并与刻蚀腔内的下电极接触,对刻蚀腔密封并进行抽真空使得压强<0.5pa;设置icf射频功率为200w,rf射频功率为50w,供气系统将体积比为1:9的氧气和cf4的混合气体送入刻蚀腔内的耦合线圈,气体流速为20cm3/min,经过辉光放电形成等离子体;等离子体在电场作用下沿垂直于极片的方向对极片涂层进行轰击,在涂层中形成垂直于极片表面的孔洞;刻蚀0.5min后,向刻蚀腔内通入氮气,将刻蚀完成的极片送出刻蚀腔,进行下一段极片的等离子体刻蚀处理;测得孔洞的平均孔径为500nm。(4)完成刻蚀的极片经压延、收卷备用。采用上述锂离子电池极片制作锂离子电池。实施例2(1)制备浆料:将1gpvp加入到10gnmp中,搅拌至pvp充分溶解,随后加入2g石墨烯,搅拌均匀,得石墨烯分散液;将2gpvdf加入到40gnmp中,以100rmp转速低速搅拌30min至pvdp充分溶解,向其中加入一半的石墨烯分散液,以100rmp转速搅拌10min,随后边搅拌边慢慢加入50g磷酸铁锂,待磷酸铁锂全部加入后继续低速搅拌30min,然后加入剩余的另一半石墨烯分散液,以2000rmp转速高速搅拌2h;充分分散后,对体系抽真空并以100rmp转速低速搅拌30min以消除浆料中的气泡;取出浆料,测定粘度为7000cp,过筛备用。(2)浆料涂布:将制备获得的浆料转移到自动涂布机上,选用20μm厚的铝箔作为集流体,采用刮刀涂布的方式完成极片的涂布,并对涂层进行干燥,干燥温度为100℃。(3)等离子体刻蚀:将干燥后的极片传送至刻蚀腔内并与刻蚀腔内的下电极接触,对刻蚀腔密封并进行抽真空使得压强<0.5pa;设置icf射频功率为200w,rf射频功率为50w,供气系统将体积比为1:9的氧气和cf4的混合气体送入刻蚀腔内的耦合线圈,气体流速为20cm3/min,经过辉光放电形成等离子体;等离子体在电场作用下沿垂直于极片的方向对极片涂层进行轰击,在涂层中形成垂直于极片表面的孔洞;刻蚀0.5min后,向刻蚀腔内通入氮气,将刻蚀完成的极片送出刻蚀腔,进行下一段极片的等离子体刻蚀处理;测得孔洞的平均孔径为500nm。(4)完成刻蚀的极片经压延、收卷备用。采用上述锂离子电池极片制作锂离子电池。实施例3(1)制备浆料:将0.5gpvp加入到10gnmp中,搅拌至pvp充分溶解,随后加入1g石墨烯,搅拌均匀,得石墨烯分散液;将2gpvdf加入到40gnmp中,以100rmp转速低速搅拌30min至pvdp充分溶解,向其中加入一半的石墨烯分散液,以100rmp转速搅拌10min,随后边搅拌边慢慢加入46.5g磷酸铁锂,待磷酸铁锂全部加入后继续低速搅拌30min,然后加入剩余的另一半石墨烯分散液,以2000rmp转速高速搅拌2h;充分分散后,对体系抽真空并以100rmp转速低速搅拌30min以消除浆料中的气泡;取出浆料,测定粘度约为6000cp,过筛备用。(2)浆料涂布:将制备获得的浆料转移到自动涂布机上,选用20μm厚的铝箔作为集流体,采用刮刀涂布的方式完成极片的涂布,并对涂层进行干燥,干燥温度为80℃。(3)等离子体刻蚀:将干燥后的极片传送至刻蚀腔内并与刻蚀腔内的下电极接触,对刻蚀腔密封并进行抽真空使得压强<0.5pa;设置icf射频功率为300w,rf射频功率为100w,供气系统将体积比为1:9的氧气和cf4的混合气体送入刻蚀腔内的耦合线圈,气体流速为40cm3/min,经过辉光放电形成等离子体;等离子体在电场作用下沿垂直于极片的方向对极片涂层进行轰击,在涂层中形成垂直于极片表面的孔洞;刻蚀2min后,向刻蚀腔内通入氮气,将刻蚀完成的极片送出刻蚀腔,进行下一段极片的等离子体刻蚀处理;测得孔洞的平均孔径约为1000nm,部分开孔将铝箔击穿,电极有轻微掉粉现象。(4)完成刻蚀的极片经压延、收卷备用。采用上述锂离子电池极片制作锂离子电池。实施例4(1)制备浆料:将0.5gpvp加入到10gnmp中,搅拌至pvp充分溶解,随后加入1g石墨烯,搅拌均匀,得石墨烯分散液;将2gpvdf加入到40gnmp中,以100rmp转速低速搅拌30min至pvdp充分溶解,向其中加入一半的石墨烯分散液,以100rmp转速搅拌10min,随后边搅拌边慢慢加入46.5g磷酸铁锂,待磷酸铁锂全部加入后继续低速搅拌30min,然后加入剩余的另一半石墨烯分散液,以2000rmp转速高速搅拌2h;充分分散后,对体系抽真空并以100rmp转速低速搅拌30min以消除浆料中的气泡;取出浆料,测定粘度约为6000cp,过筛备用。(2)浆料涂布:将制备获得的浆料转移到自动涂布机上,选用20μm厚的铝箔作为集流体,采用刮刀涂布的方式完成极片的涂布,并对涂层进行干燥,干燥温度为80℃。(3)等离子体刻蚀:将干燥后的极片传送至刻蚀腔内并与刻蚀腔内的下电极接触,对刻蚀腔密封并进行抽真空使得压强<0.5pa;设置icf射频功率为200w,rf射频功率为50w,供气系统将刻蚀气体cf4送入刻蚀腔内的耦合线圈,气体流速为30cm3/min,经过辉光放电形成等离子体;等离子体在电场作用下沿垂直于极片的方向对极片涂层进行轰击,在涂层中形成垂直于极片表面的孔洞;刻蚀1min后,向刻蚀腔内通入氮气,将刻蚀完成的极片送出刻蚀腔,进行下一段极片的等离子体刻蚀处理;测得孔洞的平均孔径为400nm。(4)完成刻蚀的极片经压延、收卷备用。采用上述锂离子电池极片制作锂离子电池。对比例1(1)制备浆料:将0.5gpvp加入到10gnmp中,搅拌至pvp充分溶解,随后加入1g石墨烯,搅拌均匀,得石墨烯分散液;将2gpvdf加入到40gnmp中,以100rmp转速低速搅拌30min至pvdp充分溶解,向其中加入一半的石墨烯分散液,以100rmp转速搅拌10min,随后边搅拌边慢慢加入磷酸铁锂,待磷酸铁锂全部加入后继续低速搅拌30min,然后加入剩余的另一半石墨烯分散液,以2000rmp转速高速搅拌2h;充分分散后,对体系抽真空并以100rmp转速低速搅拌30min以消除浆料中的气泡;取出浆料,测定粘度约为6000cp,过筛备用。(2)浆料涂布:将制备获得的浆料转移到自动涂布机上,选用20μm厚的铝箔作为集流体,采用刮刀涂布的方式完成极片的涂布,并对涂层进行干燥,干燥温度为80℃。(3)将干燥后的极片经压延、收卷备用。采用上述锂离子电池极片制作锂离子电池。对比例2(1)制备浆料:将0.5gpvp加入到10gnmp中,搅拌至pvp充分溶解,随后加入2g炭黑,搅拌均匀,得炭黑分散液;将2gpvdf加入到40gnmp中,以100rmp转速低速搅拌30min至pvdp充分溶解,向其中加入一半的炭黑分散液,以100rmp转速搅拌10min,随后边搅拌边慢慢加入磷酸铁锂,待磷酸铁锂全部加入后继续低速搅拌30min,然后加入剩余的另一半炭黑分散液,以100rmp转速高速搅拌2h;充分分散后,对体系抽真空并以100rmp转速低速搅拌30min以消除浆料中的气泡;取出浆料,测定粘度约为5000cp,过筛备用。(2)浆料涂布:将制备获得的浆料转移到自动涂布机上,选用30μm厚的铝箔作为集流体,采用刮刀涂布的方式完成极片的涂布,并对涂层进行干燥,干燥温度为120℃。(3)等离子体刻蚀:将干燥后的极片传送至刻蚀腔内并与刻蚀腔内的下电极接触,对刻蚀腔密封并进行抽真空使得压强<0.5pa;设置icf射频功率为200w,rf射频功率为50w,供气系统将体积比为1:9的氧气和cf4的混合气体送入刻蚀腔内的耦合线圈,气体流速为20cm3/min,经过辉光放电形成等离子体;等离子体在电场作用下沿垂直于极片的方向对极片涂层进行轰击,在涂层中形成垂直于极片表面的孔洞;刻蚀0.5min后,向刻蚀腔内通入氮气,将刻蚀完成的极片送出刻蚀腔,进行下一段极片的等离子体刻蚀处理;测得孔洞的平均孔径为500nm。(4)完成刻蚀的极片经压延、收卷备用。采用上述锂离子电池极片制作锂离子电池。性能测试(1)电池容量和内阻测试分别采用通过实施例1-4以及对比例1-2生产的电极制备相同规格的电池。测量电池的容量和内阻,见表1。表1电池的容量和内阻测量结果序号电池容量/ah交流内阻/mω直流内阻/mω实施例120.011.102.71实施例220.001.072.78实施例319.981.122.89实施例420.021.093.12对比例120.051.143.62对比例219.951.213.31由表1的测量结果可知,本发明实施例1-4所提供的电池的容量值和内阻值接近,其中,综合比较,实施例1所制备的电池的容量较大,内阻较小,离子导电能力和电子导电能力好,大电流充放电性能好。未经等离子体刻蚀的对比例1以及以炭黑作为导电剂的对比例2的电池的内阻较大,不利于大电流充放电。(2)放电性能测试对实施例1和对比例1制备的电池进行不同倍率的放电性能测试,测试结果如图3所示。经过刻蚀处理的电池在高倍率放电时的容量更高,更有利于大功率放电。(3)循环寿命测试对实施例1、实施例3和对比例1三种方案制备的电池进行循环寿命测试,测试结果如图4所示。实施例1经等离子体刻蚀处理的电池循环性能优于未经过等离子体刻蚀的对比例1的电池,而实施例3由于刻蚀程度过大,损坏了作为承载介质的集流体,对电池循环寿命产生了一定影响。当前第1页12