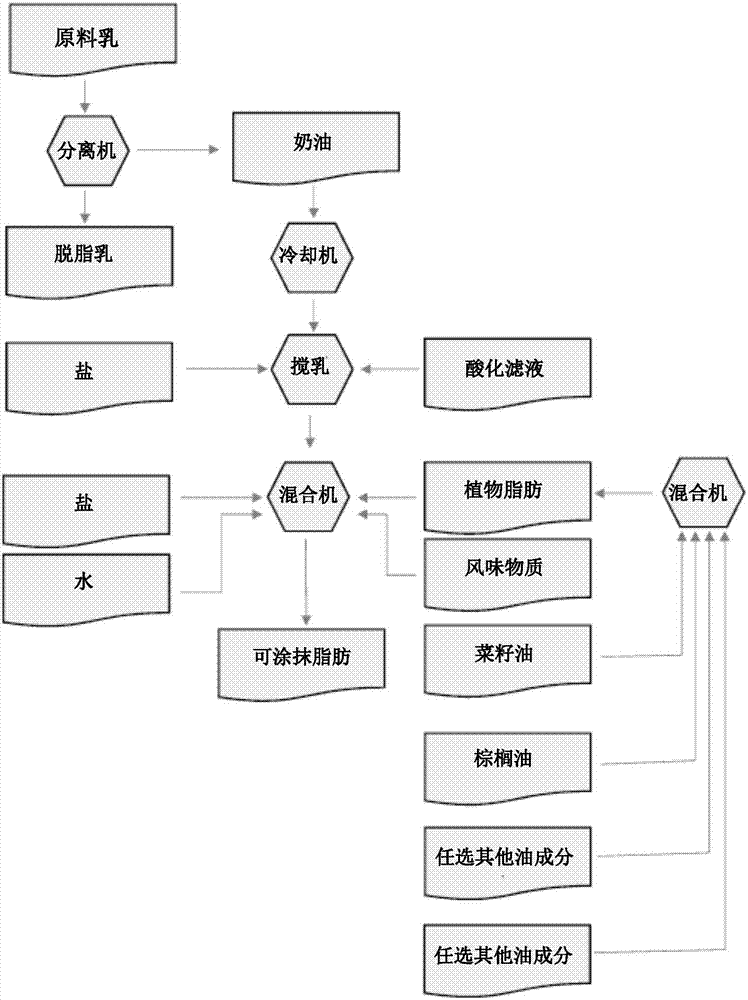
本发明属于黄油
技术领域:
并且涉及改进的可涂抹脂肪组合物,一种改进的制备方法,以及这种产品的用途。
背景技术:
脂肪,其用于营养目的并且在室温下保持为固态,但仍然可以涂抹,被称为可涂抹脂肪。实例是黄油或人造黄油,以及植物脂肪。从化学观点来看,可涂抹脂肪是以脂肪为主要成分的固态、塑化乳液。所有可涂抹脂肪必须适于人类食用。根据欧盟委员会的定义,可涂抹脂肪是“脂肪含量至少为10重量%并且至多为90重量%并且在20℃的温度下保持为固体的产品”。与之相反,根据该规定,“术语“黄油”和“人造黄油”仅用于脂肪含量至少80%的产品”。通过该规定,旨在保护消费者不会混淆黄油、人造黄油和其他具备不同脂肪含量的可涂抹脂肪(例如minarine)。根据理事会条例(ec)2991/94,可涂抹脂肪被分为以下三类:●乳脂:仅基于奶或特别是奶制品生产。它们包括:黄油、四分之三脂肪的黄油、半脂黄油和乳品涂抹脂肪。●脂肪:由固态或液态植物脂肪或动物脂肪(动物油)得到。它们含有至多3%乳脂。产品有:人造黄油、四分之三脂肪的人造黄油、半脂人造黄油、可涂抹脂肪。被称为植物脂肪的脂肪可以含有至多2%的动物源脂肪。●混合脂肪:其由固态或液态植物或动物产品,即其混合物制得。在混合脂肪中,乳脂含量可以为总脂肪含量的10%至80%。产品以混合脂肪、四分之三脂肪的混合脂肪、半脂混合脂肪或混合涂抹脂肪出售。过去这些年,除了黄油和人造黄油,含有乳脂成分和植物脂肪成分的可涂抹脂肪组合物确定了牢固的定位,因为它们像人造黄油一样从冰箱中拿出后直接可以涂抹,但是仍具备更让人联想起黄油的味道。现有技术,例如ep1279338a、wo1999043218a1、wo1999051105a1、us4,298,625、或us6,136,349,已知方法,根据其可由混合脂肪制造可涂抹脂肪组合物。dk171699b1公开了一种用于生产可涂抹脂肪的方法。底料包括含有80至83重量%植物油、水和盐的相,其中该相的部分被连续捏合为黄油相,另一部分在最后加入。特别地,ep1688044b1(dragsbaek)提出一种方法,其中结合三个成分流:在第一成分流中,将通过加热已经均质化的菜籽油和棕榈油的植物油混合物冷却,并与黄油混合,黄油的晶体结构必须被机械破坏以使其可以泵送。香料成分。其由脱脂乳粉末和盐的水性混合物组成,通过第三台泵加入。在结晶器中进行混合,随后加工得到最终的可涂抹脂肪,在该过程中,加入作为必要成分的乳酸菌以调节酸含量并从而调节产品味道。该方法有许多显著缺陷:菜籽油和棕榈油的混合物必须首先加热液化。随后再次冷却该混合物、结晶并与黄油相混合,然而黄油相以结晶形式存在,因此需要高的能量输入破坏其晶体结构,使其可以泵送和加入。此外,得到的产品没有充分均质化,因此需要乳化剂;为此,将脱脂乳粉末加入混合物。因此,该方法技术上复杂,并且包括高的能量成本。味道和涂抹性方面仍然有改进的空间。因此本发明的目的是改进现有技术从而消除乳脂部分晶体结构的机械破坏以及食品乳化剂的同时使用。同时,旨在改善产品的可涂抹性和味道性质。技术实现要素:本发明的第一个主题是可涂抹脂肪组合物,其可由此或由此得到:(a)提供含有至少40重量%脂肪和至少6重量%无脂肪干物质的奶油部分;(b)使奶油部分进行温度熟化,优选在12至14℃;(c)搅乳熟化的奶油部分,并分离酪乳;(d)向由此得到的黄油加入盐和酸化滤液;(e)在12至16℃下将酸化的黄油与在该温度下为液态的植物脂肪混合;(f)向该混合物加入水相,并且(g)在均质化和冷却后包装混合物。本发明方法的优势特别在于精确的温度控制使在奶油熟化步骤以及搅乳步骤后分别得到的乳脂仅不充分的结晶并因此仍然可以泵送和运输。以这种方式,避免了输入任何机械能量,节省了相关的高额成本。此外,不再需要使用脱脂奶粉,由于物质充分均质化,不需要任何乳化剂。使用酸化滤液在搅乳步骤已经导致得到具备显著黄油味道性能的可涂抹脂肪组合物。总之,产品的特征在于更好的可涂抹性,特别是在5至8℃的温度。本发明的组合物,优选含有至少40(“低脂”)或70重量%脂肪,特别是76至72重量%的脂肪。对于脂肪相,其还含有优选40至60重量%,并且特别是约50重量%的乳脂,以及任何情况下加至100重量%的植物脂肪。此外,对于脂肪相它们优选含有至少70重量%,并且特别是至少80重量%的脂肪,其在20℃下为固体,生产方法本发明的另一个主题涉及一种生产可涂抹脂肪组合物的方法,其包括或由以下一连串步骤组成:(a)提供含有至少40重量%脂肪和至少6重量%无脂肪干物质的奶油部分;(b)使奶油部分进行温度熟化,优选在12至14℃;(c)搅乳熟化的奶油部分,并分离酪乳;(d)向由此得到的黄油加入盐和酸化滤液;(e)在14至16℃下将酸化的黄油与在该温度下为液态的植物脂肪混合;(f)向该混合物加入水相,并且(g)均质化、冷却并包装混合物。附图说明图1显示根据本发明的生产可涂抹脂肪组合物的方法。具体实施方式奶油熟化上文提到的奶油部分通常通过原料乳脱脂得到。随后的热处理,被称为“奶油熟化”,对于该过程是决定性的。奶油熟化用于制备用于搅乳过程的奶油,其将物理式和生物化学式奶油熟化过程区分开来。在目前的物理式奶油熟化过程,离开分离机的温度约50℃的奶油部分被冷却至11至15℃的温度,并被保持在该温度约6至约18小时,优选约10至约15小时。优选地,在奶油熟化过程推荐根据冷/温/冷熟化的方法进行。冷/温/冷熟化为黄油稠度提供了最大的潜在影响。为此,将奶油多次短时加热至约20℃的温度并随后再次冷却。奶油熟化影响以下标准·稠度、硬度、可涂抹性●黄油的基础水含量(更长的保质期)·酪乳的脂肪含量·酸化、风味的形成·黄油产率在奶油熟化过程中,形成四种不同的脂肪球:类型1:具备薄外围晶体层和液体核的脂肪球类型2:具备薄外围晶体层和含有结晶团聚物和少量液态脂肪的核的脂肪球类型3:具备厚结晶壳和液态核的脂肪球类型4:具备厚结晶壳和含有结晶团聚物和少量液态脂肪的核的脂肪球搅乳熟化的奶油部分随后以常规方式进行搅乳,即,搅拌奶油,破坏乳脂的脂肪球。脂肪膜破开,所含脂肪漏出,并且脂肪求球相互粘合。部分脂肪膜、水和一些乳蛋白被封入。液态水包脂肪乳液成为固态脂肪包水乳液。到目前为止最大部分的无脂肪成分(乳清)作为酪乳漏出并分离。剩下的是黄油,通常含有82重量%脂肪,2重量%无脂肪干物质和16重量%水。本发明的另一个主要方面是搅乳步骤后,保持14至16℃的温度,将由此得到的黄油进一步加工。在这种条件下,黄油仅部分结晶并因此仍然塑性成形,因此仅需要一台搅拌罐式反应器或均质器与其他成分混合。以这种方式,与使用成品黄油—其在冷藏室储存并完全结晶—相反,避免了机械破坏晶体结构,从而节省了时间和能量。酸化随后,将盐和酸化滤液加入得到的黄油。需要这一步骤赋予可涂抹脂肪组合物黄油味道。令人惊讶地是,该方法示出在这步使用酸化滤液进行酸化比向成品中加入乳酸菌群—现有技术已知的酸化方法—产生更好的味道评估。酸化滤液的制备,例如,记载于de2652558c3(stichting)。根据该公开,用于制备风味物质的酸化过程最好在脱脂乳中使用形成风味物质,特别是双乙酰和α‐乙酰基乳酸的微生物进行。特别适用于此目的是那些含有乳脂明串珠菌(leuconostoccremoris,所谓的b发酵剂),并且特别是那些含有双乙酰乳酸链球菌(streptococcusdiacetilactis)特定菌株(所谓的d发酵剂)及其混合物(bd发酵剂)的发酵剂(starters)。酸或甜乳清,根据物理分离方法或由脱脂乳得到的其部分,以及其他已知的培养介质也适用于孵化形成风味的细菌。液体中基于乳清的乳酸菌的孵化(乳酸发酵剂)由nl‐os7205909已知。也已知保持菌群运动提高了那些风味发酵剂中的双乙酰含量。以这种方式氧化导致α‐乙酰基乳酸转化为双乙酰。然而,已经示出在将保持移动的发酵剂捏入通过搅乳非酸化奶油得到的黄油固体或黄油后,黄油熟化过程中双乙酰的形成比在通过搅乳酸奶油得到的黄油中或在由甜奶油—其通过加入化学上纯的乳酸溶液酸化—得到的黄油中更强。因此,通过捏合黄油直至干燥实现水分分布非常重要。越粗糙,随后形成越多双乙酰,由此使用更多或更少的有力的风味形成发酵剂或其混合物。风味发酵剂以其本身的形式,也可以在移除蛋白质后捏合,在后一种情况下,可以根据本身已知的方法进行风味物质的浓缩。根据上述条件之一,香气发酵剂可以任选作为用于产生大量乳酸的乳酸菌的培养介质使用。用于得到大量乳酸的酸化过程也可以在脱脂乳中进行;然而,优选地,使用基于奶的其他培养介质,只要他们相对于由于产生乳酸导致的ph值的降低用作足够有利的缓冲液,从而不必加入任何缓冲盐混合物。适当的培养介质是生产奶酪、夸克或松软干酪过程中得到的甜或酸乳清,特别是乳清母液,其已经用于生产乳糖,或得到的低乳糖乳清粉末溶液。优选上面提到的后两种培养介质,因为它们提供乳清蛋白量与乳糖量的比例有利于得到高乳酸含量以及得到的乳酸与未发酵乳糖的高比例。在这种情况下,随后的浓缩步骤在乳糖结晶后不应导致任何不透明。乳清蛋白的缓冲作用确保了乳酸的高含量,并且ph值将会低于乳酸菌代谢过程停滞的水平。在大多数乳酸菌培养物中,该数值为4.3至4.6。然而,优选使用乳酸菌,因为它们的代谢对于较低ph值不敏感。对于高酸度特别低的敏感性可见于瑞士乳杆菌(lactobacillushelveticus),其在低于3.3的ph值下仍然存活。使用这种特定菌种,特别在良好缓冲的培养介质中,得到例如20至25g/l的高乳酸含量。通过采用已知的浓缩方法该百分比甚至可以提高更多。此外,特别有利的是通过浓缩前的超滤将培养物分离为高蛋白滞留物和低蛋白滤液,特别是当使用低乳糖培养物时。滤液可以再次通过真空蒸发或膜过滤(反渗透),并且任选地随后蒸发浓缩。以这种方法,乳清蛋白与乳酸的比例可显著降低,例如从瑞士乳杆菌中的0.20降至滤液中的0.12,并且在反渗透步骤的滤液中小于0.07。如果蒸发上述最后一种滤液,非常容易得到高于35重量%的乳酸量。在将非常少量的这些强酸和成比例的低缓冲乳酸溶液捏合进由非酸化奶油制得的黄油中之后,可以将奶油乳清的ph值减小至低于5.3。使用1重量%的这种浓缩物和1重量%的风味发酵剂可以得到4.0的ph值。通常,想要的减小的ph值可以使用至多0.5重量%的浓缩物得到。为了得到上述高乳酸含量,推荐剧烈蒸发滤液,从而避免乳糖结晶。因此,用于孵化乳酸菌的培养介质应当优选地具备低含量的乳糖(低乳糖乳清)。为了清楚再次指出,由此得到的酸化滤液不含有任何活的细菌培养物。向熟化奶油部分添加的盐量通常在0.1至约4重量%的范围内,优选0.5至2重量%。加入的酸化滤液的量通常得到约4.0至约6.0,特别是约4.2至约5.0的ph值。添加植物脂肪加入黄油的适当的植物脂肪是液态的并且通常选自组包括棕榈油、新和老品种的菜籽油、红花油、橄榄油、葵花籽油、亚麻籽油及其混合物。问题是,例如棕榈油具备特别有利的味道,但其在20℃是固体,因此必须加热从而可以泵送。因此,证明有利的是加入棕榈油和其他在20℃为液态的植物脂肪,即植物油的混合物。考虑到熔点和味道,棕榈油和菜籽油的混合物被证明特别有利,特别是含有至多50重量%棕榈油的混合物在20℃下仍然是液体。通常,棕榈油和菜籽油的使用重量比为约40:60至约60:40,并且特别是约50:50。将混合物加入奶油,使得基于脂肪相存在40至60重量%的乳脂和加至100重量%的植物脂肪。添加水相原则上,可以与液态植物脂肪一起加入水相,在这种情况下仍然需要加入乳化剂。因此根据本发明的方法提供独立的添加。通常,用量为约10至50重量%,并且优选约15至25重量%,基于脂肪相,即乳脂和植物脂肪的总量。优选地,加入水性盐溶液,如果需要,也可以含有溶解状态的其他成分,例如水溶性风味物质。当物质充分均质化,可以直接装入最终包装。根据本发明的一种典型的可涂抹脂肪组合物,除非另外说明,通过在22℃的温度下,优选在室温下进行所有步骤得到,其具备以下组成:(a)约30至约40,优选约35重量%的乳脂;(b)约30至约40,并且优选约35重量%的植物脂肪,优选重量比为约40:60至约60:40的棕榈油和菜籽油;(c)0.5至约4,优选约1至约2重量%盐(食用)和/或风味物质,以及(d)加至100重量%的水。工业应用本发明的其他主题涉及新的可涂抹脂肪作为食物,特别是作为黄油替代物的用途。实施例___________________________________________________________________________实施例1将原料乳供应至分离器并分离为脱脂乳部分和奶油部分。奶油部分含有40重量%的脂肪和6重量%的无脂肪干物质。离开分离器后,将该部分由约50℃冷却至12℃,并在该温度下保持12小时,其中在约3小时的时间内加热至20℃。在熟化步骤结束后,将该部分结晶至62重量%,仍然维持塑形和可成型。将熟化奶油部分供应至搅乳器并搅拌至固体。原料黄油易于捏合,用水重复清洗,加入2重量%的食盐和一定量的酸化滤液,从而得到4.8的ph值。随后,将酸化黄油供应至14℃的混合机,在此向酸化黄油加入同样量的60重量%菜籽油和40重量%棕榈油的液态混合脂肪,其已经预热至室温。同时,将1重量%的食盐水溶液加入对应于约15重量%脂肪的量。将物质均质化并随后装入无菌容器和包装。对比实施例v1与ep1688044b1类似,将50重量%黄油,其已经通过引入机械能塑化,25重量%菜籽油和棕榈油的混合脂肪(60:40)和25重量%的水相,其含有14重量%脱脂乳粉末,3重量%食盐、5重量%乳酸菌和加至100重量%的水,在20℃下均质化60分钟。随后,将物质装入无菌容器和包装。评估两种产品将两种产品在5℃下储存3小时,在(由冷储存环境)拿出后和在室温放置10分钟后由5名测试者在(1)=固体至(5)=油体,或(1)=黄油味至(5)=无味的分数上评估可涂抹性和味道。结果在表1中总结,为平均值。表1可涂抹脂肪的评估根据实施例的产品1v1可涂抹性,由冷储存环境取出后4310分钟后的可涂抹性45味道23根据本发明的组合物一直表现出良好的可涂抹性,而对比产品给人留下更固态的印象,但是在10分钟后变得更软,在过程中漏出油滴。此外,根据本发明的产品也被评估为显著地“更黄油”。本发明通过实施例的方式在下图中解释(图1)。缩写具有以下含义:sep=分离机k=冷却机mix=混合机but=(黄油的)搅乳当前第1页12