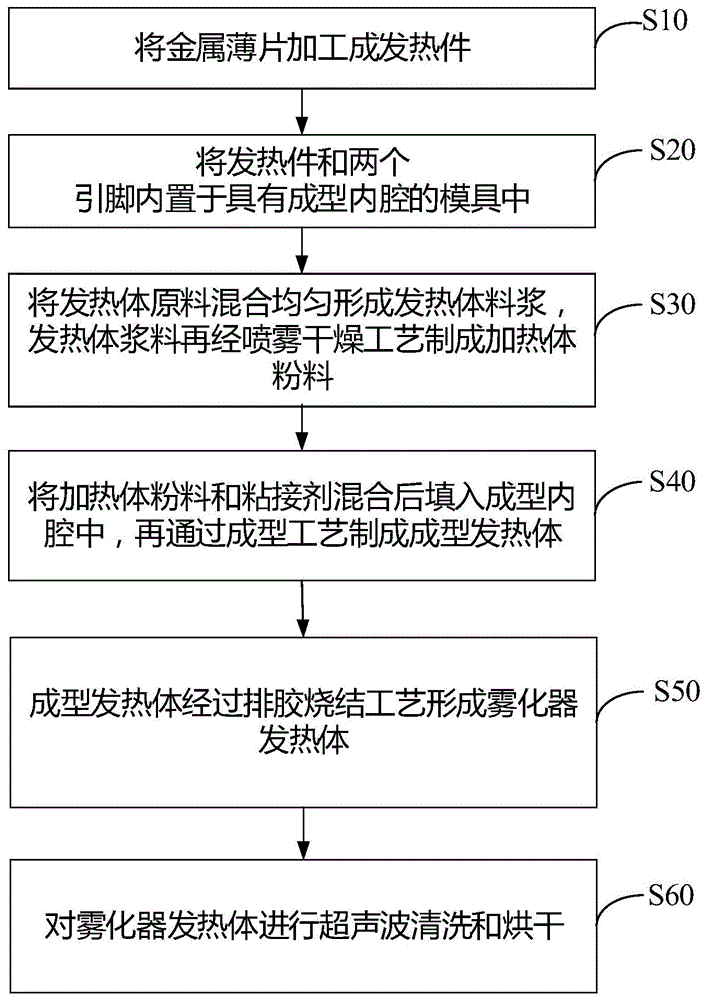
本发明属于电子雾化
技术领域:
,尤其涉及一种雾化器发热体和雾化器发热体的制作方法。
背景技术:
:电子雾化器是一种采用电加热雾化技术将雾化液经多孔材料雾化后产生烟雾的装置,其核心的部件包括发热件。发热件包括多孔陶瓷以及加热丝,多孔陶瓷的外侧面直接与雾化液接触,然后通过多孔陶瓷的微孔的毛细作用将雾化液吸附进入多孔陶瓷内部,然后经发热丝加热达到液体沸点产生雾化而形成雾化效果。然而,在目前市面上常见的电子雾化器中,多孔陶瓷大多呈中空筒状设置,发热丝呈螺旋形并部分嵌置在多孔陶瓷的内壁面,另一部分暴露于空气中,此时,由于陶瓷的导热系数大于空气的导热系数,且螺旋形的发热丝的散热方向为立体空间,故在加热时,就会导致加热丝凸出于多孔陶瓷的部分会过热,从而导致多孔陶瓷加热时温度场梯度大,使得液体受热不充分不均匀,进而导致挥发过程中成份变化,影响口感。技术实现要素:本发明的目的在于克服上述现有技术的不足,提供了一种雾化器发热体,其旨在解决现有的雾化器发热体加热时温度场梯度大的问题。本发明是这样实现的:一种雾化器发热体,包括多孔陶瓷块、发热件以及两个引脚;所述多孔陶瓷块呈多孔隙的实体块状设置,所述发热件由含钛的合金制成,并内嵌在所述多孔陶瓷块中,两个所述引脚分别与所述发热件的两自由端连接,两个所述引脚远离所述发热件的自由端均伸出所述多孔陶瓷块。可选地,所述发热件内埋在所述多孔陶瓷块中,或者,所述发热件内嵌在所述多孔陶瓷块的表面,且所述发热件与所述多孔陶瓷块的表面平齐。可选地,所述发热件呈网状,由在同一平面上多次弯折但不相交的金属丝形成,且所述引脚呈长片状设置。可选地,所述发热件内嵌在所述多孔陶瓷的上端端面。可选地,所述引脚的材质与所述发热件的材质不同或者相同,且所述引脚的宽度大于制成所述发热件的金属丝的宽度。可选地,所述多孔陶瓷块为圆柱形,两所述引脚均同向弯折至与所述发热件所在的平面之间具有夹角;或者,所述多孔陶瓷块为矩形块状,两所述引脚均与所述发热件所在的平面平行向外伸出。可选地,所述发热件的材质为含有银铜钛的合金。本发明还提出一种雾化器发热体的制作方法,该雾化器发热体的制作方法用于制作前述的雾化器发热体,包括以下步骤:s10、将金属薄片加工成发热件;s20、将所述发热件和两个引脚内置于具有成型内腔的模具中;s30、将发热体原料混合均匀形成发热体料浆,所述发热体浆料再经喷雾干燥工艺制成加热体粉料;s40、将所述加热体粉料和粘接剂混合后填入所述成型内腔中,再通过成型工艺制成成型发热体;s50、所述成型发热体经过排胶烧结工艺形成雾化器发热体。可选地,在所述步骤s10中,所述金属薄片通过蚀刻加工工艺或激光切割工艺制成所述发热件。可选地,在所述步骤s20中,所述模具上设有供两所述引脚插置的预留孔位。可选地,在所述步骤s40中,所述成型工艺包括注塑工艺或者热压铸工艺。可选地,所述步骤s50包括:s51、将所述成型发热体移入匣钵,并用氧化铝粉将所述成型发热体埋没;s52、将装有所述成型发热体和所述氧化铝粉的匣钵放置于箱式炉中,并升温至预设温度以加热预设时间;s53、加热完成后,将装有所述成型发热体和所述氧化铝粉的匣钵经随炉冷却后取出,所述成型发热体经排胶烧结形成所述雾化器发热体。可选地,在所述步骤s52中,所述箱式炉的升温速度≤1℃/min。可选地,在所述步骤s50之后,还包括以下步骤:s60、对所述雾化器发热体进行超声波清洗和烘干。在本发明的技术方案中,通过前述的雾化器发热体的制作方法制成的雾化器发热体,由于其发热件嵌置于多孔陶瓷块中,这样,发热件发出的热量就会绝大部分被多孔陶瓷块吸收,同时,由于发热件由含钛合金制成,故在烧结制作过程中,内含的钛元素可在高温下与多孔陶瓷块的陶瓷基体发生反应,产生钛氧化物的过渡连接层,该过渡连接层不但可以进一步增强发热件和陶瓷基体之间的结合强度,还具有更好的导电性能,并能产生更多热量,同时,由于该过渡连接层的导热系数介于陶瓷基体和金属之间,故发热件的热量传导至多孔陶瓷时,其热传导过程会更加平稳,从而使得本雾化器发热体加热时的温度梯度更小,加热温度更加均匀,进而使得雾化液受热更充分均匀,用户吸食的口感更佳。附图说明为了更清楚地说明本发明实施例中的技术方案,下面将对实施例中所需要使用的附图作简单地介绍,显而易见地,下面描述中的附图仅仅是本发明的一些实施例,对于本领域普通技术人员来讲,在不付出创造性劳动的前提下,还可以根据这些附图获得其他的附图。图1是本发明实施例提供的雾化器发热体的制作方法的流程图;图2是本发明实施例提供的雾化器发热体的制作方法的步骤s50的细化流程图;图3是本发明实施例提供的雾化器发热体的一实施例的结构示意图;图4是本发明实施例提供的雾化器发热体的另一实施例的结构示意图。附图标号说明:标号名称标号名称110发热件100雾化器发热体120多孔陶瓷块130引脚具体实施方式为了使本发明的目的、技术方案及优点更加清楚明白,以下结合附图及实施例,对本发明进行进一步详细说明。应当理解,此处所描述的具体实施例仅用以解释本发明,并不用于限定本发明。需要说明的是,当元件被称为“固定于”或“设置于”另一个元件,它可以直接在另一个元件上或者间接在该另一个元件上。当一个元件被称为是“连接于”另一个元件,它可以是直接连接到另一个元件或间接连接至该另一个元件上。下面详细描述本发明的实施例,所述实施例的示例在附图中示出,其中自始至终相同或类似的标号表示相同或类似的元件或具有相同或类似功能的元件。下面通过参考附图描述的实施例是示例性的,旨在用于解释本发明,而不能理解为对本发明的限制。在本发明的描述中,需要理解的是,术语“长度”、“宽度”、“上”、“下”、“前”、“后”、“左”、“右”、“竖直”、“水平”、“顶”、“底”“内”和“外”等指示的方位或位置关系为基于附图所示的方位或位置关系,仅是为了便于描述本发明和简化描述,而不是指示或暗示所指的装置或元件必须具有特定的方位、以特定的方位构造和操作,因此不能理解为对本发明的限制。在本发明中,除非另有明确的规定和限定,术语“安装”、“相连”、“连接”、“固定”等术语应做广义理解,例如,可以是固定连接,也可以是可拆卸连接,或成一体;可以是机械连接,也可以是电连接;可以是直接相连,也可以通过中间媒介间接相连,可以是两个元件内部的连通或两个元件的相互作用关系。对于本领域的普通技术人员而言,可以根据具体情况理解上述术语在本发明中的具体含义。本发明实施例提供一种雾化器发热体。请参阅图3,雾化器发热体100包括多孔陶瓷块120、发热件110以及两个引脚130;多孔陶瓷块120呈多孔隙的实体块状设置,发热件110由含钛的合金制成,并内嵌在多孔陶瓷块120中,两个引脚130分别与发热件110的两自由端连接,两个引脚130远离发热件110的自由端均伸出多孔陶瓷块120。在此需说明的是,本雾化器发热体100主要应用于电子雾化器中。通常电子雾化器包括吸嘴(未图示)、电池部(未图示)和雾化部(未图示),雾化部包括用于容纳雾化液的容器(未图示)、用于雾化液雾化的雾化器发热体100,雾化器发热体100内置于容器中,两引脚130分别与电池部的正负两极连接。具体地,发热件110内埋在多孔陶瓷块120中,或者,在如图3所示的一实施例中,发热件110内嵌在多孔陶瓷块120的表面,且发热件110与多孔陶瓷块120的表面平齐。优选地,发热件110内嵌在多孔陶瓷的上端端面,以方便制作过程中对发热件110定位。进一步地,如图3和图4所示,发热件110呈网状,由在同一平面上多次弯折但不相交的金属丝形成,且引脚130呈长片状设置,当然,于其他实施例中,发热件还可以呈其他形状设置。具体地,发热件110的图案,可以是如图3所示一实施例的多次弯折后盘成的o形图案,也可以是如图4所示的另一实施例的沿长度方向迂回弯折的s形图案。可以理解,这种金属丝在同一平面上多次弯折但不相交的图案设置可使得在有限的面积上尽可能地使用于加热的金属丝更长更多,从而有利于提高本雾化器发热体100的加热性能和加热效率。可选地,引脚130的材质与发热件110的材质不同或者相同,且引脚130的宽度大于制成发热件110的金属丝的宽度。例如,引脚130的材质与发热件110的材质相同时,引脚130和发热件110可以一体制成,若引脚130的材质与发热件110的材质不同时,可以在分别制作好引脚130和发热件110后,将引脚130通过焊接等方式与发热件110连接。在此需特别说明的是,为适应不同的产品结构要求,本雾化器发热体100的具有多种形状。例如,在如图3所示的一实施例中,多孔陶瓷块120为圆柱形,两引脚130均同向弯折至与发热件110所在的平面之间具有夹角,该夹角可以是任何角度,但优选为直角即两引脚130与发热件110所在的平面垂直,以方便后续装配;或者,在如图3所示的一实施例中,多孔陶瓷块120为矩形块状,两引脚130均与发热件110所在的平面平行向外伸出,当然,两引脚130也可以均与发热件110所在的平面之间具有夹角。此外,由于在发热过程中,越细的金属丝会越先发热,故本实施例中引脚130的宽度大于发热件110的金属丝的宽度的设置,不但有利于引脚130与其他部件的连接便利,还能确保发热件110先于引脚130发热,以尽量减少热量浪费。在本实施例中,金属薄片优选含有银铜钛的合金,其厚度范围优选为0.1mm-0.5mm,相应地,发热件110的材质也是优选为含有银铜钛的合金。本发明实施例还提供一种雾化器发热体的制作方法。请参阅图1和图3,该雾化器发热体的制作方法包括以下步骤:s10、将金属薄片加工成发热件110;s20、将发热件110和两个引脚130内置于具有成型内腔的模具中;s30、将发热体原料混合均匀形成发热体料浆,发热体浆料再经喷雾干燥工艺制成加热体粉料;s40、将加热体粉料和粘接剂混合后填入成型内腔中,再通过成型工艺制成成型发热体;s50、成型发热体经过排胶烧结工艺形成雾化器发热体100。在本发明的技术方案中,通过前述的雾化器发热体的制作方法制成的雾化器发热体100,由于其发热件110嵌置于多孔陶瓷块120中,且两引脚130凸出于多孔陶瓷后能与电池部的正负两极连接,这样,发热件110发出的热量就会绝大部分被多孔陶瓷块120吸收,同时,由于发热件110由含钛合金制成,故在烧结制作过程中,内含的钛元素可在高温下与多孔陶瓷块的陶瓷基体发生反应,产生钛氧化物的过渡连接层,该过渡连接层不但可以进一步增强发热件110和陶瓷基体之间的结合强度,还具有更好的导电性能,并能产生更多热量,同时,由于该过渡连接层的导热系数介于陶瓷基体和金属之间,故发热件110的热量传导至多孔陶瓷120时,其热传导过程会更加平稳,从而使得本雾化器发热体100加热时的温度梯度更小,加热温度更加均匀,进而使得雾化液受热更充分均匀,用户吸食的口感更佳。具体地,在步骤s10中,金属薄片通过蚀刻加工工艺或激光切割工艺制成发热件110。当然,于其他实施例中,发热件110还可以通过但不限于使用刀具裁剪形成,但本实施例中选用蚀刻加工工艺或激光切割工艺制成发热件110具有加工效率高,形状稳定,适于大规模生产的优势。进一步地,在步骤s20中,可以按照产品的设计要求先制作好模具,且模具上设有供两引脚130插置的预留孔位,即在模具制作完成后,可将引脚130插入该预留孔位中,以完成模具的组装。由于发热件110的厚度较薄,而为了实现将发热件110嵌置在多孔陶瓷块120中,发热件110的定位应依靠模具实现。具体地,在步骤s30中,发热体原料包括石英砂、刚玉砂、造孔剂等,其配方可沿用通常的多孔陶瓷配方设计,其中,造孔剂可优选为碳粉。将各种发热体原料按配方称取后,就可以投入到研磨装置,例如但不限于球磨机中边研磨边混合均匀形成加热体浆料。在球磨完成后,这些加热体浆料就可以直接经过喷雾干燥的工艺制作成加热体粉料。进一步地,在步骤s40中,成型工艺包括注塑工艺或者热压铸工艺。然本设计不限与此,于其他实施例中,本雾化器发热体100还可以采用但不限于干压成型等其他成型工艺。在本步骤中,粘结剂可以但不限于是石蜡等,主要用于与加热体粉料混合,以助其成型,且粘接剂会在后续的步骤s50排胶烧结工序中去除。进一步地,步骤s50包括:s51、将成型发热体移入匣钵,并用氧化铝粉将成型发热体埋没;s52、将装有成型发热体和氧化铝粉的匣钵放置于箱式炉中,并升温至预设温度以加热预设时间;s53、加热完成后,将装有成型发热体和氧化铝粉的匣钵经随炉冷却后取出,成型发热体经排胶烧结形成雾化器发热体100。步骤s50为排胶烧结的工序,具体采用的是埋烧方式,即使用氧化铝粉将成型发热体埋没后进行烧结。在此,氧化铝粉除了起到导热和保护内埋的成型发热体,以防止成型发热体在烧结过程中变形的作用之外,其粉状颗粒之间形成的毛细作用,还具有促使成型发热体中的粘接剂和有机物排除的效果,从而可进一步避免有害物质残留的问题。在步骤s52中,预设温度范围优选为800-900℃,加热预设时间范围优选为15-20小时,如此,就能更好地将成型发热体中的粘接剂以及其他有机物通过加热挥发排出,并在多孔陶瓷块120中形成孔隙合适的多孔结构。且进一步地,在步骤s52中,箱式炉的升温速度优选≤1℃/min,以防止升温速度过快时,会成型发热体导致开裂或排胶不完全的情况发生。进一步地,在步骤s50之后,还包括以下步骤:s60、对雾化器发热体100进行超声波清洗和烘干。可以理解,由于在s50的步骤中采用的是埋烧方式,故在烧结完成后,雾化器发热体100的表面会轻微粘结氧化铝粉,这些杂质需放在水中经超声波清洗后才能去除,然后,将清洗干净但带水的雾化器发热体100装入烘箱中烘干后,即可得到最终成品的雾化器发热体100。以上所述仅为本发明的较佳实施例而已,并不用以限制本发明,凡在本发明的精神和原则之内所作的任何修改、等同替换或改进等,均应包含在本发明的保护范围之内。当前第1页12