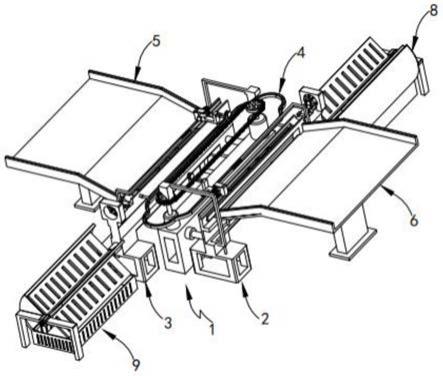
:
[0001]
本发明属于毛竹自动加工设备技术领域,更具体的说是涉及一种自动化加工切片设备。
背景技术::
[0002]
现有一些切片设备能够解决毛竹切片加工的问题,但是使用中还是存在效率低、需要人工搬运上料、切片不均匀以及危险系数高的弊端。
[0003]
公开号为cn111070353a的一篇中国发明专利,其公开了一种刀头可切换的竹子切片装置,属于竹子切片领域,包括底座,底座的底部设置有滚轮,底座的顶部设置有切片箱,切片箱的一侧贯穿有进料口,当需要将片更薄化时,工作人员对刀头进行更换,在更换时工作人员转动对第一刀头相对于的转舵,进而使得螺杆向上转动,从而使得连接板在滑槽内向上滑动,连接板向上滑动使得第一刀头向上运动,第一刀头缩回一组固定筒,然后工作人员再转动与第二刀头相对于的转舵,进而使得另一组螺杆向下运动,另一组螺杆向下运动推动连接板带动第二刀头伸出另一组固定筒,而第二刀头之间的间隙较小,从而使得竹条切出来的竹片更加薄化,该装置便于切换刀头,满足于不同的工艺效果,实用性强。
[0004]
但是其切片效率低,需要人工上料,存在安全隐患比较大。
技术实现要素::
[0005]
本发明的目的是针对现有技术的不足之处,提供一种竹子切片设备,通过设置驱动机构将上料机构将竹子推送至破片装置切刀处进行均分切片,解决了现有竹子切片设备效率低、需要人工上料、接料、切片不均匀以及危险系数高的问题。
[0006]
本发明的技术解决措施如下:
[0007]
一种双工位竹子自动破片设备,包括破片装置,所述破片装置包括第一破片机构、第二破片机构以及设置在第一破片机构与第二破片机构之间的驱动机构,所述驱动机构包括回转组件、导向组件、支撑组件以及设置在所述支撑组件上的定位组件,在第一破片机构和第二破片机构的一侧分别对应设置第一上料机构与第二上料机构,所述第一破片机构与第二破片机构均包括切割台、设置在所述切割台尾端的切刀以及所述切割台面上的支撑件,在所述第一破片机构与第二破片机构尾端分别对应设置有第一接料机构与第二接料机构,所述第一上料机构和第二上料机构用于往对应的第一破片机构与第二破片机构上供给毛竹,所述支撑组件在回转组件的带动下沿着导向组件的轨道移动,在移动的过程中将毛竹往第一破片机构和第二破片机构尾端推送进行破碎,在支撑组件支撑毛竹的初始阶段,定位组件对毛竹进行定位,在到达切刀破片之前,由支撑件配合定位组件进行辅助定位。
[0008]
作为一种优选,所述回转组件包括底座、设置在底座上的电机a、由该电机a带动下的转动链条以及设置在所述转动链条上的支撑块a。
[0009]
作为一种优选,所述导向组件由连接杆a与连接杆b分别与第一破片机构和第二破片机构固定连接,该导向组件包括进入段、平推段、退出段以及回转段。
[0010]
作为一种优选,所述支撑组件包括一端与回转组件上的支撑块a滑动连接的滑杆a、与所述滑杆a另一端固定连接的支撑杆a以及设置在所述支撑杆a上的支撑块b,支撑杆a沿着导向组件的轨道移动,在该支撑杆a的底部设置有滑块。
[0011]
作为一种优选,所述定位组件包括定位杆、与所述定位杆尾端固定链接的齿条a、设置在支撑组件中支撑杆a上的齿轮以及设置在定位组件移动路径上的齿条b和齿条c,所述齿条b通过支撑杆b固定在第一破片机构上,所述齿条c通过支撑杆c固定在第二破片机构上,所述定位杆与支撑组件中的支撑块b设置滑动连接,所述齿轮与支撑组件中支撑杆a设置转动连接。
[0012]
作为一种优选,所述第一上料机构与第二上料机构均包括挡板a、升降块、与所述升降块固定连接的支撑杆d、与所述支撑杆d一侧固定连接的推送杆、与所述支撑杆d另一侧固定连接的滑杆b、设置在第一破片机构与第二破片机构一侧的上料斜面、与所述上料斜面固定连接的储料平面、设置在所述上料斜面与储料平面两侧的挡板b,设置在所述储料平面下方的支撑柱、转动设置在支撑块a上的滚轮以及设置在切割台上的滑套,其中滑杆b与滑套之间滑动连接,挡板a可转动连接设置在切割台的内壁上,且所述挡板a与切割台之间还连接有弹簧a。
[0013]
作为一种优选,所述第一接料机构与第二接料机构均包括支撑杆e、设置在该支撑杆e上的电机b、由该电机b带动下的转动板、设置在所述转动板下方的接料篓以及设置在转动板一侧的挡板c。
[0014]
作为一种优选,所述第一破片机构与第二破片机构中切割台上的支撑件包括固定连接在切割台上的支撑块c和可转动设置在该支撑块c的支撑板,所述支撑板与切割台连接有弹簧b。
[0015]
作为又一种优选,在所述挡板a与推送杆对应的位置设置为镂空。
[0016]
本发明的有益效果在于:
[0017]
1.本发明中设置回转组件沿着导向组件带动支撑组件转动,并在转动路径上对竹子往切刀处推送进行切片、接料,实现了集上料、推送、破片以及接料自动化连续式工作,在应对人工上料的基础上提高了切片的效率,并且全程无人员参与,提高了工作中的安全性。
[0018]
2.本发明中在竹子刚接触到支撑组件时,由定位组件对毛竹进行定位推送,再到达切刀破片之前,由切割台上的支撑件辅助定位组件进行二次定位,确保对竹子均分破片,解决了现有设备切片不均匀的问题。
[0019]
3.本发明中设置自动上料机构,由回转组件上支撑块带动滚轮转动的过程中,沿着上料机构中的升降快斜面移动,在斜面路径上移动的同时,使得上料机构中的推送杆升起,将毛竹推送至切割台后,由弹簧将挡板复位的同时限位板限制挡板向下转动,防止竹子下落,在此期间,推送杆从挡板的镂空处下降进行复位,防止与挡板发生碰撞,其自动上料代替了人工上料,解决了人工上料时安全性差效率低的问题。
[0020]
4.本发明中在破片机构的尾端设置接料机构,可以将完成切片的竹材料通过重力下落至接料板然后落入接料篓中,省去了人工搬料的环节,提高了效率的同时还提升了整个切片过程中的安全性。
[0021]
综上所述,本发明具有切片效率快、避免人工上料、接料、安全系数高以及切片均匀的优点,适合竹子加工切片设备领域。
附图说明:
[0022]
下面结合附图对本发明做进一步的说明:
[0023]
图1为毛竹自动切片设备的结构示意图;
[0024]
图2为上料机构以及固定齿条的俯视示意图;
[0025]
图3为驱动机构的结构示意图;
[0026]
图4为上料机构与破片机构的结构示意图;
[0027]
图5为支撑组件与定位组件的结构示意图;
[0028]
图6为破片机构中支撑件的放大结构示意图;
[0029]
图7为上料机构中的挡板与推送杆的放大示意图;
[0030]
图8为上料机构中的挡板剖面示意图;
[0031]
图9为图2中a处放大示意图。
具体实施方式:
[0032]
下面结合附图对本发明实施例中的技术方案进行清楚、完整地说明。
[0033]
实施例一
[0034]
下面详细描述本发明的实施例,所述实施例的示例在附图中示出,其中自始至终相同或类似的标号表示相同或类似的元件或具有相同或类似功能的元件。下面通过参考附图描述的实施例是示例性的,旨在用于解释本发明,而不能理解为对本发明的限制。
[0035]
如图1至图8所示,一种双工位竹子自动破片设备,包括破片装置1,所述破片装置1包括第一破片机构2、第二破片机构3以及设置在第一破片机构2与第二破片机构3之间的驱动机构4,所述驱动机构4包括回转组件41、导向组件42、支撑组件43以及设置在所述支撑组件上的定位组件44,在第一破片机构2和第二破片机构3的一侧分别对应设置第一上料机构5与第二上料机构6,所述第一破片机构2与第二破片机构3均包括切割台100、设置在所述切割台100尾端的切刀101以及所述切割台100面上的支撑件102,在所述第一破片机构2与第二破片机构3尾端分别对应设置有第一接料机构8与第二接料机构9,所述第一上料机构5和第二上料机构6用于往对应的第一破片机构2与第二破片机构3上供给毛竹,所述支撑组件43在回转组件41的带动下沿着导向组件42的轨道移动,在移动的过程中将毛竹往第一破片机构2和第二破片机构3尾端推送进行破碎,在支撑组件43支撑毛竹的初始阶段,定位组件44对毛竹进行定位,在到达切刀101破片之前,由支撑件102配合定位组件44进行辅助定位。
[0036]
值得一提的是,该发明设置了自动上料机构,由驱动机构提供动力,再由推送杆将毛竹推送至切割台上,并设置与切割台内壁有弹簧连接的挡板防止毛竹下落,并在挡板上设置镂空,防止推送杆下落时与之碰撞,该机构代替现有的人工上料,实现了自动上料,解决了人工上料过程中的危险性大的问题。
[0037]
进一步地,所述回转组件41包括底座413、设置在底座413上的电机a414、由该电机a414带动下的转动链条411以及设置在所述转动链条411上的支撑块a412。
[0038]
进一步地,所述导向组件42由连接杆a245与连接杆b426分别与第一破片机构2和第二破片机构3固定连接,该导向组件42包括进入段421、平推段422、退出段423以及回转段424。
[0039]
进一步地,所述支撑组件43包括一端与回转组件41上的支撑块a412滑动连接的滑
杆a431、与所述滑杆a431另一端固定连接的支撑杆a432以及设置在所述支撑杆a432上的支撑块b434,支撑杆a432沿着导向组件42的轨道移动,在该支撑杆a432的底部设置有滑块435。
[0040]
进一步地,所述定位组件44包括定位杆441、与所述定位杆441尾端固定链接的齿条a442、设置在支撑组件43中支撑杆a432上的齿轮433以及设置在定位组件44移动路径上的齿条b429和齿条c430,所述齿条b429通过支撑杆b427固定在第一破片机构2上,所述齿条c430通过支撑杆c固定在第二破片机构3上,所述定位杆441与支撑组件43中的支撑块434设置滑动连接,所述齿轮433与支撑组件43中支撑杆a432设置转动连接。
[0041]
值得一提的是,本发明中在竹子刚接触到支撑组件时,由定位组件对毛竹进行定位推送,再到达切刀破片之前,由切割台上的支撑件辅助定位组件进行二次定位,确保对竹子均分破片,解决了现有设备切片不均匀的问题。
[0042]
进一步地,所述第一上料机构5与第二上料机构6均包括挡板a206、升降块201、与所述升降块201固定连接的支撑杆d202、与所述支撑杆d202一侧固定连接的推送杆203、与所述支撑杆d202另一侧固定连接的滑杆b204、设置在第一破片机构2与第二破片机构3一侧的上料斜面210、与所述上料斜面210固定连接的储料平面209、设置在所述上料斜面210与储料平面209两侧的挡板b211,设置在所述储料平面209下方的支撑柱212、转动设置在支撑块a412上的滚轮208以及设置在切割台100上的滑套205,其中滑杆b204与滑套205之间滑动连接,挡板a206可转动连接设置在切割台100的内壁上,且所述挡板a206与切割台100之间还连接有弹簧a213。
[0043]
此处,通过设置自动上料机构,由回转组件上支撑块带动滚轮转动的过程中,沿着上料机构中的升降快斜面移动,在斜面路径上移动的同时,使得上料机构中的推送杆升起,将毛竹推送至切割台后,由弹簧将挡板复位的同时限位板限制挡板向下转动,防止竹子下落,在此期间,推送杆从挡板的镂空处下降进行复位,防止与挡板发生碰撞,其自动上料代替了人工上料,解决了人工上料时安全性差效率低的问题。
[0044]
进一步地,所述第一破片机构2与第二破片机构3中切割台100上的支撑件102包括固定连接在切割台100上的支撑块c104和可转动设置在该支撑块c104的支撑板103,所述支撑板103与切割台连接有弹簧b105。
[0045]
更进一步地,在所述挡板a206与推送杆203对应的位置设置为镂空。
[0046]
实施例二
[0047]
如图2所示,其中与实施例一中相同或相应的部件采用与实施例一相应的附图标记,为简便起见,下文仅描述与实施例一的区别点;该实施例二与实施例一的不同之处在于:所述第一接料机构8与第二接料机构9均包括支撑杆e76、设置在该支撑杆e76上的电机b73、由该电机b73带动下的转动板71、设置在所述转动板71下方的接料篓72以及设置在转动板71一侧的挡板c75。
[0048]
值得一提的是,本实施例在破片机构的尾端设置接料机构,可以将完成切片的竹材料通过重力下落至接料板然后落入接料篓中,省去了人工搬料的环节,提高了效率的同时还提升了整个切片过程中的安全性。
[0049]
工作过程
[0050]
由回转组件41的转动下,转动链条中支撑块a412上的滚轮208经过上料机构升降
快201的斜面路径时,使得上料机构中的推送杆203上升,将竹子推送至切割台100上,再由设置在切割台100内壁上的挡板a206挡住竹子下落,并在挡板a206设置有镂空,防止与推送杆203发生碰撞;
[0051]
回转组件41还带动两个工位上的支撑组件43经过导向组件42的进入段421后,在平推段422移动,用于将竹子往第一破片机构2和第二破片机构3的切刀101处推送,在此过程中,支撑组件43上的定位组件44对竹子进行定位,双向移动的定位组件44在经过推送路径上的齿条b429和齿条c430后,在齿轮433与齿条a442的作用下缓缓退出定位;
[0052]
此外,回转组件41带动支撑组件43继续将竹子向切刀101推送,破片完成后的竹片下落至第一接料机构8与第二接料机构9中,随后回转组件41继续带动支撑组件43和定位组件44进行与之前相同的过程,支撑组件43与定位组件44在回转组件41及导向组件42的作用下循环往复,以达到自动上料、切片和接料的功能。
[0053]
以上结合附图所述的仅是本发明的优选实施方式,但本发明并不限于上述实施方式,应当指出,对于本领域的技术人员来说,在不脱离本发明结构的前提下,还可作出各种变形和改进,这些也应该视为本发明的保护范围,都不会影响本发明实施的效果和实用性。