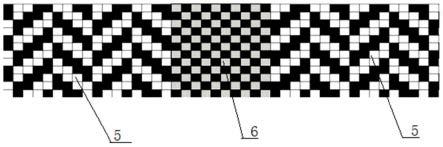
1.本发明涉及车内安全设备技术领域,特别是涉及一种耐用性发光汽车安全带及其生产工艺。
背景技术:2.汽车安全带是为了在碰撞时对乘员进行约束以及避免碰撞时乘员与方向盘及仪表板等发生二次碰撞或避免碰撞时冲出车外导致死伤的安全装置。汽车安全带又可以称之为座椅安全带,是乘员约束装置的一种,当车辆紧急制动或撞车时,能限制佩带者的身体移动,以防止或减轻佩戴者受到伤害。
3.汽车安全带产品在初始强度、耐久性强度、宽度方面的性能要求是法规强制的要求,所以汽车安全带的设计首先应满足严苛的国标要求。统计资料表明,使用安全带可以把严重受伤的概率降低50%,驾驶人未系安全带死亡率是系安全带的37.7倍。
4.由于安全带能大幅度减少严重受伤的概率,我国于80年代末提出使用安全带,90年代初国家交通部规定所有汽车的驾驶座和小车前座必须装上安全带。但有些乘客还是心存侥幸,通过及时拉安全带覆盖身体来蒙蔽交警执法。
5.目前,公开号为cn107433925a的中国专利公开了一种汽车安全带,包括:锁扣、收带器、设于所述锁扣、收带器之间的织带、套设于所述织带上的胸部护带、套设于所述织带上的腰部护带、设于所述胸部护带相连的心率传感器和血压传感器、以及设于所述胸部护带上的与所述心率传感器和血压传感器电性连接的震动器;所述胸部护带和腰部护带均包括衬底层、分别设于所述衬底层的两侧的两蜂窝吸能层、以及分别设于两蜂窝吸能层的两侧的外套层。
6.该种汽车安全带虽然扩展了汽车安全带的安全保护功能,但本身颜色为纯色,一般为纯黑色,且纹路几乎只有五条纹、七条纹、无条纹、碎花纹,一方面纯色的安全带较难吸引乘客注意,容易造成乘客忘记佩戴安全带的情况;另一方面纯色尤其是纯黑色的安全带,在乘车人员心存侥幸想要蒙蔽执法时,较容易由背包等背带混淆,交警执法或外部监测时容易忽略,造成乘车人员的安全隐患。
技术实现要素:7.本发明针对上述技术问题,克服现有技术的缺点,提供一种耐用性发光汽车安全带及其生产工艺。
8.技术效果:利用了合理的织物组织设计纹理,织造出个性度强且耐久度高的发光织带作为安全带,能够吸引乘客尤其是小孩的眼球,引导乘客主动佩戴安全带;同时通过安全带的发光也能够便于交警或外部监测乘车人员是否有效佩戴安全带,提升安全带的佩戴率;本发明的织造工艺设计、定型工艺设计使光导纤维在满足法律法规的要求下合理在汽车安全带上应用,提高了产品使用寿命,赋予安全带个性化有更高的辨识度,从而为汽车的内饰加分,也主动吸引提高乘坐人员的佩戴意识,保障交通安全。
9.本发明进一步限定的技术方案是,一种耐用性发光汽车安全带生产工艺,包括如下步骤:
10.s1,织造,取光导纤维和涤纶色纱,相互交织得到安全带织带,光导纤维位于安全带织带的正中心,并采用一上一下的组织方式织造;
11.s2,预烘,将织带至于烘箱中预热,预热温度为60~100℃;
12.s3,热定型,将预热完成后的织带至于烘箱中进行热定型,并完成伸长率、产品宽厚度的微调;
13.s4,喷淋,在热定型完成后的织带表面用水喷洗1~5s;
14.s5,还原水洗,用含有还原清洗剂的溶液对织带进行浸轧,使织带湿润并含带还原清洗剂;
15.s6,气蒸,将湿润后的织带至于气蒸箱中使用蒸汽蒸3~5min,气蒸温度为80~90℃;
16.s7,热水洗,将气蒸后的织带至于60~80℃的热水中,用柠檬酸调节热水的ph值,将热水调节为弱酸性,并将织带浸泡处理3~5min;
17.s8,中间烘干,将热水洗后的织带取出并送入烘箱烘干,烘干温度为100~140℃;
18.s9,降温,将织带置于通风冷却架上冷却1~2min,至织带表面温度降低至60℃以下;
19.s10,涂层,取定量涂层液,织带表面施加压力,将涂层液浸轧至织带内,将织带中的带液率控制在10~25%之间;
20.s11,最终烘干,将织带至于烘箱中烘干2~5min,烘干温度为120~140℃,制得织带成品。
21.进一步的,步骤s2中,热定型温度在120~160℃之间,以避免破坏光导纤维。
22.前所述的一种耐用性发光汽车安全带生产工艺,涂层液的制备包括如下步骤:
23.s6-1,取定量改性聚二甲基硅氧烷乳液和脂肪族聚氨酯乳液,以0.75:1的比例复配得到功能整理剂;
24.s6-2,将所述功能整理剂用温度低于35℃的水稀释,稀释后的浓度为2~15%,得到稀释液;
25.s6-3,在稀释液中加入醋酸或柠檬酸,将ph值调节至中性,得到涂层液。
26.前所述的一种耐用性发光汽车安全带生产工艺,步骤s6中,对织带的浸轧方法为:将涂层液倒入轧槽内,再将织带浸入轧槽,采用一浸一轧的方式以胶轮对织布浸轧,保证织带的带液率在15~20%之间,胶轮压力为3~5bar。
27.前所述的一种耐用性发光汽车安全带生产工艺,步骤s1中,光导纤维部分的带宽小于安全带织带总带宽的1/5。
28.本发明还提供一种耐用性发光汽车安全带,包括相互交织的涤纶胚带和光导纤维胚带,光导纤维胚带位于安全带织带的中线上,沿安全带织带的长度方向分布,光导纤维胚带为1/1平纹结构,涤纶胚带为2/2斜纹结构,且安全带织带整体由权利要求1~5中任意一种耐用性发光汽车安全带生产工艺制得。
29.前所述的一种耐用性发光汽车安全带,涤纶胚带由涤纶色纱织造而成,其规格为1000d或1500d。
30.前所述的一种耐用性发光汽车安全带,光导纤维由软质pcv材料制成,其直径小于1.5mm。
31.本发明的有益效果是:
32.(1)本发明中,制备的汽车安全带上设置光导纤维,能够使安全带具备发光性能,应用在汽车内时,可以吸引乘客,尤其是儿童乘客的眼球,提升汽车安全带的自主佩戴率;另外在光导纤维应用在安全带上后,也能够便于外界对于乘车人员佩戴安全带的监控,以提高安全带的强制佩戴率;另外设置光导纤维还能提升安全带的个性程度,使安全带的设计更加个性化;本发明将光纤与纺织、安全带相结合开发了新的生产工艺和表现手法,设计出兼具安全性和功能性的产品,使得安全带向着更加智能化、时尚化的方向发展;
33.(2)本发明中,相对于安全带用的纱线来说,光导纤维的力学强度低,弹性、透气性较差,脆性大、钩接强度低,因此需要对其进行处理,保证安全带整体的机械性能不会因为加入光导纤维而大幅度降低;本发明通过特殊的安全带生产工艺,一方面将安全带中光导纤维的宽度占比控制在总宽度的1/5以下,另一方面通过各步骤对安全带的处理,提升对光导纤维的各方面性能,保证了安全带整体机械性能符合相关规定;
34.(3)本发明中,通过本织造工艺设计、定型工艺设计使光导纤维在满足法律法规的要求下合理地在汽车安全带上应用,提高了安全带整体使用寿命,赋予安全带个性化有更高的辨识度,从而为汽车的内饰加分,也主动吸引提高乘坐人员的佩戴意识,保障交通安全;
35.(4)本发明中,利用了合理的织物组织设计纹理,织造出个性度强且耐久度高的发光织带作为安全带,能够吸引乘客尤其是小孩的眼球,引导乘客主动佩戴安全带;同时通过安全带的发光也能够便于交警或外部监测乘车人员是否有效佩戴安全带,提升安全带的佩戴率;同时将光导纤维应用在安全带上,也提升了安全带的智能性,助力安全带在保证应用安全的情况下朝向差别化、高性能化、复合化和时尚化方向发展。
附图说明
36.图1是实施例1的应用效果示意图:
37.图2是实施例1中材料应用分布图:
38.图3是实施例1的应用组织图:
39.图4是实施例1中光导纤维侧面剖视图
40.图5是实施例1中织带局部穿综效果图。
41.其中:1、汽车安全带;2、座椅;3、涤纶色纱;4、光导纤维;5涤纶胚带;6、光导纤维胚带。
具体实施方式
42.为使本发明的目的、技术方案和优点更加清楚,下面结合附图及具体实施方式做详细的说明。在下面的描述中阐述了很多具体细节以便于充分理解本发明。但是本发明能够以很多不同于在此描述的其他方式来实施,本领域技术人员可以在不违背本发明内涵的情况下做类似改进,因此本发明不受下面公开的具体实施的限制。
43.除非另有定义,本文所使用的所有的技术和科学术语与属于本发明的技术领域的
技术人员通常理解的含义相同。本文中在本发明的说明书中所使用的术语只是为了描述具体的实施例的目的,不是旨在于限制本发明。
44.本实施例提供的一种耐用性发光汽车安全带,结构如图1和图2所示,该安全带应用在汽车座椅2上。该汽车安全带1包括相互交织的涤纶胚带5和光导纤维胚带6,光导纤维胚带6位于整个汽车安全带的正中间位置,并且沿着安全带的长度方向分布,在佩戴使用时,安全带中间部分能够发出光线,以提升安全带的辨识度。
45.如图2至图3所示,光导纤维胚带6整体为1/1平纹结构,即由一上一下的方式织造而成;而涤纶胚带5则为2/2斜纹结构,即由二上二下斜纹织造的方式织成。涤纶胚带5位于光导纤维胚带的两侧。安全带织造完成后,局部的穿综效果如图5所示,斜纹结构的涤纶胚带5,相对于平纹结构的光导纤维胚带6,能够进一步提升视觉效果,提高中间位置的醒目程度。
46.本发明中采用的涤纶胚带5由涤纶色纱3织造而成,其规格为1000d或1500d;采用的光导纤维4则选用软质通体pvc材料,直径小于1.5mm。另外,本发明中安全带整体宽度应介于46~50mm之间,而光导纤维胚带6的宽度则需要在安全带整体宽度的1/5以下,以保证安全带整体的力学性能复合相关标准。
47.本发明还提供一种耐用性发光汽车安全带生产工艺,其包括如下步骤:
48.s1,织造,取光导纤维和涤纶色纱,相互交织得到安全带织带,光导纤维位于安全带织带的正中心,并采用一上一下的组织方式织造,且光导纤维部分的带宽小于安全带织带总带宽的1/5;
49.s2,预烘,将织带至于烘箱中预热,预热温度为60~100℃;
50.s3,热定型,将预热完成后的织带至于烘箱中进行热定型,并完成伸长率、产品宽厚度的微调,热定型温度在120~160℃之间,以避免破坏光导纤维;
51.s4,喷淋,在热定型完成后的织带表面用水喷洗1~5s;
52.s5,还原水洗,用含有还原清洗剂的溶液对织带进行浸轧,使织带湿润并含带还原清洗剂;
53.s6,气蒸,将湿润后的织带至于气蒸箱中使用蒸汽蒸3~5min,气蒸温度为80~90℃;
54.s7,热水洗,将气蒸后的织带至于60~80℃的热水中,用柠檬酸调节热水的ph值,将热水调节为弱酸性,并将织带浸泡处理3~5min;
55.s8,中间烘干,将热水洗后的织带取出并送入烘箱烘干,烘干温度为100~140℃;
56.s9,降温,将织带置于通风冷却架上冷却1~2min,至织带表面温度降低至60℃以下;
57.s10,涂层,取定量涂层液,织带表面施加压力,将涂层液浸轧至织带内,将织带中的带液率控制在10~25%之间;
58.s11,最终烘干,将织带至于烘箱中烘干2~5min,烘干温度为120~140℃,制得织带成品。
59.在步骤s6中,对织带的浸轧方法为:将涂层液倒入轧槽内,再将织带浸入轧槽,采用一浸一轧的方式以胶轮对织布浸轧,保证织带的带液率在15~20%之间,胶轮压力为3~5bar。
60.另外,涂层液的制备方法包括如下步骤:
61.s6-1,取定量改性聚二甲基硅氧烷乳液和脂肪族聚氨酯乳液,以0.75:1的比例复配得到功能整理剂;
62.s6-2,将所述功能整理剂用温度低于35℃的水稀释,稀释后的浓度为2~15%,得到稀释液;
63.s6-3,在稀释液中加入醋酸或柠檬酸,将ph值调节至中性,得到涂层液。
64.由于在涤纶胚带之间加入了光导纤维胚带,因此整个安全带织带的强度势必会受到影响,为尽量减少对安全带织带造成的强度影响,本发明一方面控制光导纤维胚带的宽度,使其宽度小于安全带整体宽度的1/5;另一方面也通过上述步骤的处理提升安全带织带的性能。
65.提升安全带强度的主要步骤为:气蒸、热水洗、中间烘干和降温步骤。气蒸的步骤能够将涤纶胚带和光导纤维进行初步软化,提升安全带整体的柔韧度;气蒸后通过酸性溶液能够进一步软化光导纤维部分,降低光导纤维的脆性,提升安全带的弹性和钩接强度,提高光导纤维的弯曲性能;通过中间烘干的步骤能够将安全带上述弯曲性能、钩接强度、弹性和柔韧度进行进一步加深和固化,最后由降温步骤将上述性能固化在安全带上,保证安全带整体性能指标符合相关规定的标准。
66.本发明针对制备所得的安全带织带的性能进行了测试,测试的主要参考标准为:qc/t 946-2013汽车安全带织带性能要求和试验方法和gb14166-2013织带的断裂强度试验,本发明设置了若干个实施例,测试不同生产条件下安全带织带的静态强度,得到的承载力值如表2所示。
67.具体实施例中发光安全带的制备步骤如下所示。
68.前提条件为,1、光导纤维位于织带的正中心,带宽设计应小于10mm,采用1上1下的组织方式进行织造;
69.2、光导纤维选用软质通体pvc材料,直径小于1.5mm;
70.3、安全带宽度设计50mm,剩余经纱应选用涤纶色纱,规格为1000d或1500d,采用2上2下的组织方式进行织造;
71.4、采用如图5所示的穿综纹路进行织造。
72.各实施例中制备条件如表1所示。
73.表1各实施例安全带织带制备条件表
[0074][0075]
表2各实施例制得安全带织带承载力值表
[0076][0077][0078]
由表2可知,实施例6制备得到的安全带承载力值最大,具有最佳的性能效果,且通过本方法制备的安全带,其承载力值均满足有关标准的参考值。因此本发明生产的安全带能够在保证性能的基础上实现发光功能。
[0079]
本发明利用了合理的织物组织设计纹理,织造出个性度强且耐久度高的发光织带作为安全带,能够吸引乘客尤其是小孩的眼球,引导乘客主动佩戴安全带;同时通过安全带的发光也能够便于交警或外部监测乘车人员是否有效佩戴安全带,提升安全带的佩戴率;同时将光导纤维应用在安全带上,也提升了安全带的智能性,助力安全带在保证应用安全的情况下朝向差别化、高性能化、复合化和时尚化方向发展。
[0080]
除上述实施例外,本发明还可以有其他实施方式。凡采用等同替换或等效变换形成的技术方案,均落在本发明要求的保护范围。