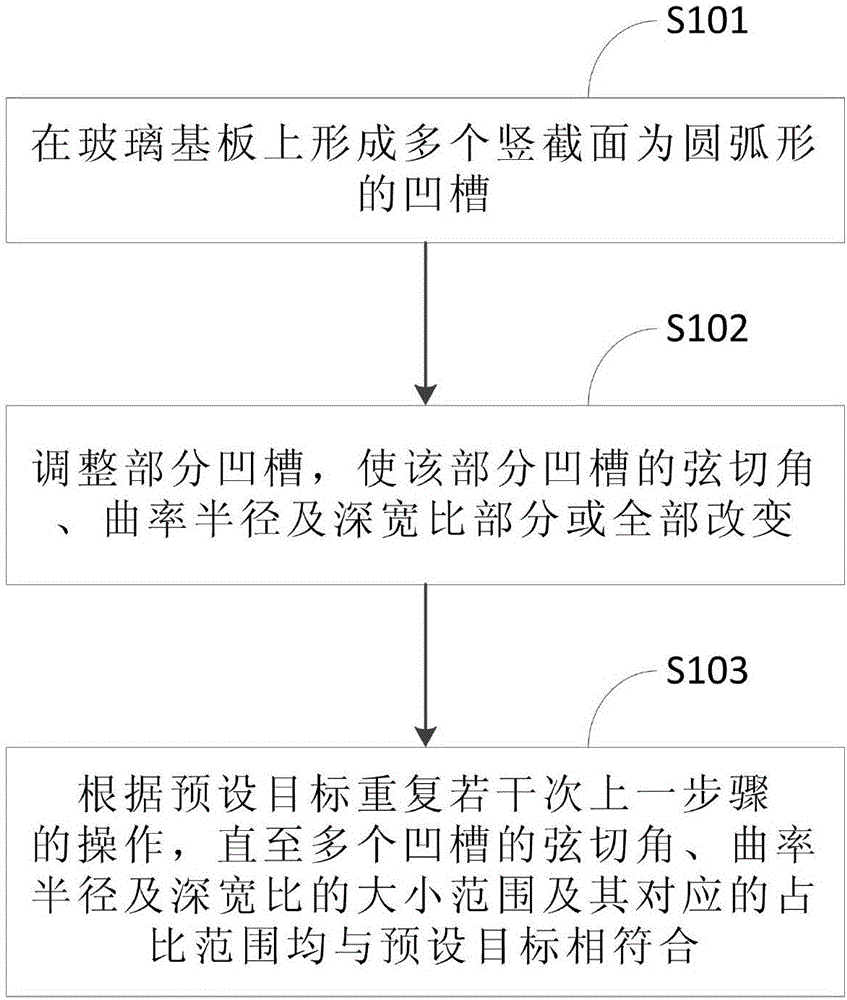
本发明涉及液晶显示领域,特别涉及一种抗闪光盖板的制造方法。
背景技术:
:液晶显示装置(LCD,LiquidCrystalDisplay)具有机身薄、省电、无辐射等众多优点,得到了广泛的应用。TFT-LCD在日常生活中已经很普及,如电视、电脑、手机等显示屏,该领域技术不断更新以更好的服务消费者。不断的产品升级使对TFT-LCD更高的要求,提出了更高的产品品质的要求。车载显示和小尺寸显示面板的抗眩功能越来越受到人们的关注,传统的抗眩结构的加工方法包括湿刻法和涂布法。湿刻法即采用酸液对盖板玻璃进行表面蚀刻处理,得到粗糙的表面结构。涂布方法即通过在盖板玻璃表面涂布有机或无机粒子的方式得到粗糙表面结构。然而,湿刻和涂布的方法工艺虽然简单,但是无法得到形貌可控的粗糙表面结构,无法控制盖板表面透射光或者反射光的光强空间分布和强度,这就会导致盖板表面发生闪光的现象,严重影响画面的品质。技术实现要素:本发明的目的在于提供一种抗闪光盖板的制造方法,以解决现有技术中,无法得到形貌可控的粗糙表面结构的盖板,无法控制盖板表面透射光或者反射光的光强空间分布和强度,这就会导致盖板表面发生闪光的现象,严重影响画面的品质的问题。本发明的技术方案如下:一种抗闪光盖板的制作方法,包括以下步骤:1)根据预设目标设定玻璃基板表面结构的不同结构参数的目标大小范围及其对应的目标占比范围;2)在所述玻璃基板上形成多个微结构,每个所述微结构的不同结构参数的绝对值大小均在其对应的所述目标大小范围之内,且所述目标大小范围划分为若干个设定范围,参数大小处于该若干个设定范围内的所述微结构的个数与所述微结构的总数的比例大小均在其对应的所述目标占比范围之内,以使所述抗闪光盖板具有抗闪光作用。优选地,在玻璃基板上形成多个微结构,包括以下步骤:1)在玻璃基板上形成多个竖截面为圆弧形的凹槽;2)调整部分所述凹槽,使该部分所述凹槽的弦切角、曲率半径及深宽比部分或全部改变;3)根据所述预设目标重复若干次所述步骤2)的操作,直至多个所述凹槽的弦切角、曲率半径及深宽比的大小范围及其对应的占比范围均与所述预设目标相符合。优选地,多个所述凹槽的大小相同,其相互连接并均匀分布排列。优选地,步骤1)具体包括:在所述玻璃基板表面的预设位置喷涂包括氢氟酸、磷酸及硫酸在内所组成的混酸溶液,并使所述混酸溶液在所述预设位置停留至预设时间长度,使其蚀刻出多个所述凹槽。优选地,步骤2)具体包括:在所述多个凹槽上涂布正光阻层,所述正光阻层覆盖多个所述凹槽;准备设定光罩并将其与所述正光阻层相对合,将紫外光线照射所述设定光罩,以得到曝光区小于未曝光区的光阻结构;在所述光阻结构的曝光区再次喷涂所述混酸溶液对所述玻璃基板进行蚀刻,以改变该曝光区部分的所述凹槽的弦切角、曲率半径及深宽比。优选地,所述预设目标具体为:弦切角大小的绝对值处于30°~40°、20°~30°、10°~20°的所述凹槽的个数占所述凹槽的总数的百分比分别为0~0.5%、0.5%~1.5%、7%~15%及85%~91%,多个所述凹槽的平均曲率半径范围为10~30um,且多个所述凹槽的平均深宽比范围为0.05~0.1。优选地,在玻璃基板上形成多个微结构,包括以下步骤:1)在玻璃基板上涂覆一透明有机层,所述透明有机层具有所述玻璃基板的光学性质;2)在所述透明有机层上涂覆一负光阻层,准备设定光罩并将紫外光线照射所述设定光罩,以对所述负光阻层进行曝光显影,得到所述负光阻层的光阻预设结构;3)对所述光阻预设结构及所述透明有机层进行蚀刻,以去除所述光阻预设结构,并得到所述透明有机层的透明有机结构,且所述透明有机结构的外型与所述光阻预设结构的外型相同,所述透明有机结构包括多个所述微结构;其中,所述设定光罩设有全曝光区、半曝光区及无曝光区,所述半曝光区位于所述全曝光区的两侧,所述无曝光区位于所述半曝光区的中部,多个所述透明微结构具有抗闪光作用。优选地,每个所述微结构的外型为中间厚两侧薄的底面横截面为圆弧形的凸包,所述凸包的中部对应所述无曝光区,所述凸包的两侧对应所述半曝光区。优选地,各个所述微结构的大小不完全相同,且相邻两个所述微结构之间设有间距,该间距区对应所述全曝光区。优选地,所述凸包的曲率半径范围为2~100um,相邻两个所述凸包之间的间隔范围为0.2~30um,所述凸包的高度范围为1~100um。本发明的有益效果:本发明的一种抗闪光盖板的制作方法,包括两种制作方式,其一是通过多次湿蚀刻,并辅助光罩的工艺方式在玻璃基板上制备多个微结构,通过对微结构的相关结构参数进行设计并优化,有效改善微结构在高解析度盖板上产生的闪光现象,使微结构盖板在增强面板户外可读性的同时也避免闪光现象,对于抗眩盖板在小尺寸显示面板上的实际应用起到很好的推动作用。其二是采用光刻的方式制备从圆弧状到球状的抗闪光结构,通过光罩工艺精确控制微结构周期大小、间距和高度,当微结构粒径大小为2~100um范围内,微结构间距为0.2~30um的范围内(间距为粒径大小的0.1~0.3倍),微结构高度为1~100um的范围内(高度为粒径大小的0.5~2倍),通过光学软件模拟进行验证,改善盖板表面的抗闪光效果。【附图说明】图1为本发明实施例一的抗闪光盖板的制造方法实施步骤流程图;图2为本发明实施例一的抗闪光盖板的制造方法实施步骤中,将玻璃基板清洗并烘干后的示意图;图3为本发明实施例一的抗闪光盖板的制造方法实施步骤中,在玻璃基板上形成多个竖截面为圆弧形的凹槽的示意图;图4为本发明实施例一的抗闪光盖板的制造方法实施步骤中,在透明有机层上涂覆一正光阻层的示意图;图5为本发明实施例一的抗闪光盖板的制造方法实施步骤中,将紫外光线照射所述设定光罩的示意图;图6为本发明实施例一的抗闪光盖板的制造方法实施步骤中,得到曝光区小于未曝光区的光阻结构的示意图;图7为本发明实施例一的抗闪光盖板的制造方法实施步骤中,改变该曝光区部分的所述凹槽的弦切角、曲率半径及深宽比的示意图;图8为本发明实施例一的凹槽的弦切角、曲率半径和深度的结构参数表达示意图;图9为本发明实施例二的抗闪光盖板的制造方法实施步骤流程图;图10为本发明实施例二的抗闪光盖板的制造方法实施步骤中,将玻璃基板清洗并烘干后的示意图;图11为本发明实施例二的抗闪光盖板的制造方法实施步骤中,在玻璃基板上涂覆一透明有机层的示意图;图12为本发明实施例二的抗闪光盖板的制造方法实施步骤中,在透明有机层上涂覆一负光阻层的示意图;图13为本发明实施例二的抗闪光盖板的制造方法实施步骤中,将紫外光线照射所述设定光罩,对所述负光阻层进行曝光显影的示意图;图14为本发明实施例二的抗闪光盖板的制造方法实施步骤中,得到负光阻层的光阻预设结构的示意图;图15为本发明实施例二的抗闪光盖板的制造方法实施步骤中,去除光阻预设结构,并得到透明有机层的透明有机结构的示意图;图16为本发明实施例二的抗闪光盖板的制造方法实施步骤中,得到的透明有机材料层形成的多个所述微结构的竖截面近似于圆弧状的示意图;图17为本发明实施例二的凸包的弦切角、曲率半径和深度的结构参数表达示意图。【具体实施方式】以下各实施例的说明是参考附加的图式,用以例示本发明可用以实施的特定实施例。本发明所提到的方向用语,例如「上」、「下」、「前」、「后」、「左」、「右」、「内」、「外」、「侧面」等,仅是参考附加图式的方向。因此,使用的方向用语是用以说明及理解本发明,而非用以限制本发明。在图中,结构相似的单元是以相同标号表示。实施例一总的来说,本发明的一种抗闪光盖板的制造方法包括以下两个步骤:第一,根据预设目标设定玻璃基板1表面结构的不同结构参数的目标大小范围及其对应的目标占比范围。第二,在所述玻璃基板1上形成多个微结构,每个所述微结构的不同结构参数的绝对值大小均在其对应的所述目标大小范围之内,且所述目标大小范围划分为若干个设定范围,参数大小处于该若干个设定范围内的所述微结构的个数与所述微结构的总数的比例大小均在其对应的所述目标占比范围之内,以使所述抗闪光盖板具有抗闪光作用。以下多本发明进行具体的说明。请参考图1,图1为本实施例的一种抗闪光盖板的制造方法实施步骤流程图。从图1可以看到,本发明的一种抗闪光盖板的制造方法包括以下步骤:步骤S101:在玻璃基板1上形成多个竖截面为圆弧形的凹槽2。本步骤优选多个所述凹槽2的大小相同,其相互连接并均匀分布排列。步骤S102:调整部分所述凹槽2,使该部分所述凹槽2的弦切角、曲率半径及深宽比部分或全部改变。步骤S103:根据所述预设目标重复若干次所述步骤S102的操作,直至多个所述凹槽2的弦切角、曲率半径及深宽比的大小范围及其对应的占比范围均与所述预设目标相符合。其中,相邻的两次重复步骤S102的操作中,后一次部分被调整的所述凹槽2与前一次不完全相同。在本实施例中,步骤S101具体包括:在所述玻璃基板1表面的预设位置喷涂包括氢氟酸、磷酸及硫酸在内所组成的混酸溶液,并使所述混酸溶液在所述预设位置停留至预设时间长度,使其蚀刻出多个所述凹槽2。在本实施例中,步骤S102具体包括:第一,在所述多个凹槽2上涂布正光阻层3,所述正光阻层3覆盖多个所述凹槽2。第二,准备设定光罩4并将其与所述正光阻层3相对合,将紫外光线5照射所述设定光罩4,以得到曝光区小于未曝光区的光阻结构。第三,在所述光阻结构的曝光区再次喷涂所述混酸溶液对所述玻璃基板1进行蚀刻,以改变该曝光区部分的所述凹槽2的弦切角、曲率半径及深宽比。在本实施例中,所述预设目标具体为:弦切角大小的绝对值处于30°~40°、20°~30°、10°~20°的所述凹槽2的个数占所述凹槽2的总数的百分比分别为0~0.5%、0.5%~1.5%、7%~15%及85%~91%,多个所述凹槽2的平均曲率半径范围为10~30um,且多个所述凹槽2的平均深宽比范围为0.05~0.1。请参考图2至图8,图2为本发明实施例一的抗闪光盖板的制造方法实施步骤中,将玻璃基板1清洗并烘干后的示意图。图3为本发明实施例一的抗闪光盖板的制造方法实施步骤中,在玻璃基板1上形成多个竖截面为圆弧形的凹槽2的示意图。图4为本发明实施例一的抗闪光盖板的制造方法实施步骤中,在透明有机层上涂覆一正光阻层3的示意图。图5为本发明实施例一的抗闪光盖板的制造方法实施步骤中,将紫外光线5照射所述设定光罩4的示意图。图6为本发明实施例一的抗闪光盖板的制造方法实施步骤中,得到曝光区小于未曝光区的光阻结构的示意图。图7为本发明实施例一的抗闪光盖板的制造方法实施步骤中,改变该曝光区部分的所述凹槽2的弦切角、曲率半径及深宽比的示意图。图8为本发明实施例一的凹槽2的弦切角、曲率半径和深度的结构参数表达示意图。本发明在所述玻璃基板1上形成多个微结构,使每个所述微结构的不同结构参数大小均符合其对应的所述目标大小范围,及使符合各种结构参数要求的所述微结构的个数占全部所述微结构的比例均符合其对应的所述目标占比范围,以使所述抗闪光盖板具有抗闪光作用。本发明的制作方法的具体实施步骤如下所述:本发明采用多次湿刻的工艺方式进行盖板表面微结构的制备,微结构主要的湿刻工艺结构参数如图8所示,其中r为曲率半径,h为凹槽2深度,β为弦切角,h/r为深宽比。具体工艺操作流程如图2至图7所示。首先将玻璃基板1清洗干净并烘干,如图2所示,在玻璃基板1表面第一次喷涂较低浓度的氢氟酸、磷酸及硫酸等组成的混酸溶液,并使混酸溶液在玻璃基板1表面停留一段时间,使得混酸溶液蚀刻出如图3所示的微结构,即多个竖截面为圆弧形的凹槽2。其中微结构的弦切角β的绝对值控制在0°~10°,平均曲率半径r的大小控制在30~50um,平均深宽比h/r控制在0.02~0.025,并再次将玻璃基板1洗净并烘干。其次在玻璃基板1的凹槽2上即湿刻表面涂布一层正光阻,采用曝光的方式将微结构表面留下少量曝光区,其中曝光区的面积大小远小于未曝光区,形成曝光区小于未曝光区的光阻结构。接着如上所述,在所述光阻结构的曝光区再次喷涂所述混酸溶液对所述玻璃基板1进行蚀刻,以改变该曝光区部分的所述凹槽2的弦切角、曲率半径及深宽比,即在玻璃基板1表面再次喷涂浓度稍高的氢氟酸、磷酸及硫酸的混酸溶液,使混酸溶液在基板表面暂留一段时间,湿刻出所需图案,以上工艺流程如图4~图7所示。其中每个凹槽2的弦切角β的绝对值在10°~20°之间的角度占比在2%~5%,平均曲率半径r控制在20~40um,平均深宽比h/r控制在0.03~0.04。接下来重复若干次图4~图7所示的操作过程,其中每次曝光显影区均与前几次不完全相同,最终在玻璃基板1的表面湿刻出多个不同弦切角、曲率半径和深宽比的凹槽2,其中弦切角呈现高斯分布的特性,满足绝对值在30°~40°占比0~0.5%,20°~30°占比0.5%~1.5%,10°~20°占比7%~15%,0°~10°占比85%~91%,平均曲率半径R控制在10~30um,平均深宽比h/R控制在0.05~0.1。表一和表二显示了不同湿刻工艺制备的抗闪光盖板的具体工艺参数情况。从表中数据可知,4#样品采用多次湿刻的工艺进行微结构制备,其弦切角分布呈现出一定分散的特性,绝对值在30°~40°的占比为0.1%,20°~30°的占比为0.7%,10°~20°的占比为8.8%,0°~10°的占比90.4%,平均曲率半径r为29um,平均深宽比h/r为0.05,其参数规格符合上述事实方案要求。将4种不同参数的微结构盖板放在同一解析度的显示面板上,通过实物照片结果可知闪光现象的严重程度为:4#<1#<2#<3#,3#和2#有明显的闪光现象,1#的闪光现象较为轻微,4#几乎看不到闪光现象,从而也进一步验证了通过多次湿刻工艺制备盖板表面抗眩微结构可以有效改善高解析度显示面板表面的闪光现象。表一不同湿刻工艺凹槽2弦切角的统计分布表二不同湿刻工艺凹槽2结构参数对比样品编号0°-10°占比10°-20°占比20°-30°占比30°-40°占比曲率半径/um深宽比1#97%2.70%0.20%-490.031#99.10%0.80%0.10%-850.0251#99.40%0.50%0.10%-1140.021#90.40%8.80%0.70%0.10%290.05本发明的一种抗闪光盖板的制作方法,通过多次湿蚀刻,并辅助光罩的工艺方式在玻璃基板1上制备多个微结构,通过对微结构的相关结构参数进行设计并优化,有效改善微结构在高解析度盖板上产生的闪光现象,使微结构盖板在增强面板户外可读性的同时也避免闪光现象,对于抗眩盖板在小尺寸显示面板上的实际应用起到很好的推动作用。实施例二总的来说,本发明的一种抗闪光盖板的制造方法包括以下两个步骤:第一,根据预设目标设定玻璃基板10表面结构的不同结构参数的目标大小范围及其对应的目标占比范围。第二,在所述玻璃基板10上形成多个微结构,每个所述微结构的不同结构参数的绝对值大小均在其对应的所述目标大小范围之内,且所述目标大小范围划分为若干个设定范围,参数大小处于该若干个设定范围内的所述微结构的个数与所述微结构的总数的比例大小均在其对应的所述目标占比范围之内,以使所述抗闪光盖板具有抗闪光作用。以下多本发明进行具体的说明。请参考图9,图9为本实施例的抗闪光盖板的制造方法实施步骤流程图,从图9可以看到,本发明的一种抗闪光盖板的制造方法,包括以下步骤:步骤S101:在玻璃基板10上涂覆一透明有机层20,所述透明有机层20具有所述玻璃基板10的光学性质。步骤S102:在所述透明有机层20上涂覆一负光阻层30,准备设定光罩并将紫外光线70照射所述设定光罩,以对所述负光阻层30进行曝光显影,得到所述负光阻层30的光阻预设结构。步骤S103:对所述光阻预设结构及所述透明有机层20进行蚀刻,以去除所述光阻预设结构,并得到所述透明有机层20的透明有机结构,且所述透明有机结构的外型与所述光阻预设结构的外型相同,所述透明有机结构包括多个所述微结构。其中,所述设定光罩设有全曝光区40、半曝光区50及无曝光区60,所述半曝光区50位于所述全曝光区40的两侧,所述无曝光区60位于所述半曝光区50的中部,多个所述透明微结构具有抗闪光作用。在本实施例中,每个所述微结构的外型为中间厚两侧薄的底面横截面为圆弧形的凸包,所述凸包的中部对应所述无曝光区60,所述凸包的两侧对应所述半曝光区50。在本实施例中,各个所述微结构的大小不完全相同,且相邻两个所述微结构之间设有间距,该间距区对应所述全曝光区40。在本实施例中,所述凸包的曲率半径范围为2~100um,相邻两个所述凸包之间的间隔范围为0.2~30um,所述凸包的高度范围为1~100um,所述间隔范围为所述曲率半径范围的0.1~0.3倍,所述高度范围为所述曲率半径范围的0.5~2倍。请参考图10至图17,图10为本实施例的抗闪光盖板的制造方法实施步骤中,将玻璃基板10清洗并烘干后的示意图。图11为本实施例的抗闪光盖板的制造方法实施步骤中,在玻璃基板10上涂覆一透明有机层20的示意图。图12为本实施例的抗闪光盖板的制造方法实施步骤中,在透明有机层20上涂覆一负光阻层30的示意图。图13为本实施例的抗闪光盖板的制造方法实施步骤中,将紫外光线70照射所述设定光罩,对所述负光阻层30进行曝光显影的示意图。图14为本实施例的抗闪光盖板的制造方法实施步骤中,得到负光阻层30的光阻预设结构的示意图。图15为本实施例的抗闪光盖板的制造方法实施步骤中,去除光阻预设结构,并得到透明有机层20的透明有机结构的示意图。图16为本实施例的抗闪光盖板的制造方法实施步骤中,得到的透明有机材料层形成的多个所述微结构的竖截面近似于圆弧状的示意图。图17为本实施例的凸包的弦切角、曲率半径和深度的结构参数表达示意图。本发明在所述玻璃基板10上形成多个微结构,使每个所述微结构的不同结构参数大小均符合其对应的所述目标大小范围,及使符合各种结构参数要求的所述微结构的个数占全部所述微结构的比例均符合其对应的所述目标占比范围,以使所述抗闪光盖板具有抗闪光作用。本发明的制作方法的具体实施步骤如下所述:本发明采用光刻的方法进行玻璃基板10表面微结构的制备,微结构主要的工艺结构参数如图17所示,其中r为凸包的曲率半径,h为凸包的高度,β为凸包的弦切角,h/r为高宽比。具体工艺操作流程如图10至图16所示。首先,将玻璃基板10清洗干净并烘干,如图10所示。然后在玻璃基板10表面涂布一层与玻璃基板10组分相近的材质以形成涂布层,该涂布层和玻璃基板10有很相近的物理性质,保证涂布层在玻璃基板10表面拥有良好的附着力,如图11所示。接着在涂布层的上方涂布一层负光阻层30,负光阻层30的涂布需要厚度合适且均匀,如图12所示。然后用光罩的方式在负光阻层30表面形成相应的图案,其中该光罩包括无曝光区60、全曝光和半曝光区50,如图13所示,经过使用紫外光线70曝光之后,负光阻层30无曝光区60的光阻被洗掉,全曝光区40的光阻完全保留,半曝光区50光阻被部分洗掉,如图14所示。接着利用干刻或湿刻的方式将中间位置的涂布层完全蚀刻掉,再利用光阻清洗剂将两侧光阻中的半曝光区50清洗掉,如图15所示。最后再次利用干刻或者蚀刻的方式进行将半曝光区50下方的涂布层进行部分蚀刻,并清洗掉涂布层上方的全部光阻,得到如图16所示的微结构类型。其中,光刻工艺加工产生的凸包的结构特征参数具体包括:凸包呈现出从球状到圆弧状的几何形貌,其曲率半径r的大小范围在2~100um之内,凸包之间的间隔大小范围在0.2~30um之内,其中凸包之间的间隔约为曲率半径r的0.1~0.3倍,凸包凸起高度h的大小范围在1~100um之内,其中凸包凸起高度h约为其曲率半径r的0.5~2倍。本发明采用光刻的方式制备从圆弧状到球状的抗闪光凸包结构,通过光罩工艺精确控制凸包周期大小、间距和高度,当凸包的曲率半径r大小在2~100um范围内,凸包间距在0.2~30um的范围内(间距为曲率半径r大小的0.1~0.3倍),凸包高度在1~100um的范围内(高度h为曲率半径r大小的0.5~2倍),通过光学软件模拟进行验证,本发明很好地改善了玻璃基板10表面的抗闪光效果。综上所述,虽然本发明已以优选实施例揭露如上,但上述优选实施例并非用以限制本发明,本领域的普通技术人员,在不脱离本发明的精神和范围内,均可作各种更动与润饰,因此本发明的保护范围以权利要求界定的范围为准。当前第1页1 2 3