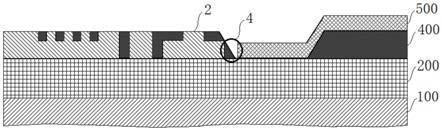
[0001]
本发明涉及双层硅基光子器件制造技术领域,具体涉及一种双层硅基光子器件的制作方法及双层硅基光子器件。
背景技术:[0002]
目前双层硅基光子器件的耦合方式通常是采用倒追耦合器或者光栅方式进行层间耦合,这种方式对层间介质厚度及均匀性要求很高,层间厚度越薄耦合效率越高但是层间串扰也越高,即耦合效率如串扰相互制约。
技术实现要素:[0003]
本发明的主要目的在于提供一种双层硅基光子器件的制作方法及双层硅基光子器件,采用各向同性腐蚀方法将非第一层波导结构的层间介质区域形成斜坡,使第二层波导材料与第一层波导结构的耦合区在同一层次实现耦合,增加耦合效率,降低层间串扰,以解决现有技术中双层硅基光子器件层间耦合存在层间串扰的技术问题。
[0004]
为了实现上述目的,根据本发明的第一方面,提供了一种双层硅基光子器件的制作方法。
[0005]
该双层硅基光子器件的制作方法包括以下步骤:
[0006]
该双层硅基光子器件的制作方法包括以下步骤:
[0007]
提供第一层波导结构绝缘体上硅(soi)衬底;
[0008]
在所述绝缘体上硅(soi)衬底上形成第一层波导结构;
[0009]
采用介质材料回填第一层;
[0010]
在非第一层波导结构的所述介质材料区域形成凹槽;
[0011]
采用各向同性腐蚀工艺腐蚀所述凹槽,以在所述凹槽上形成斜面;
[0012]
沉积第二层波导材料,所述第二层波导材料在所述凹槽处与所述第一层波导结构耦合。
[0013]
进一步的,所述绝缘体上硅(soi)衬底包括支撑衬底、位于所述支撑衬底上的氧化物埋层(box层)以及位于所述氧化物埋层上的硅层。
[0014]
进一步的,采用光刻工艺刻蚀所述硅层,以在所述硅层上形成所述第一层波导结构。
[0015]
进一步的,采用介质材料回填第一层包括:
[0016]
覆盖所述第一层波导结构以及所述氧化物埋层沉积介质材料,形成层间介质层;
[0017]
对所述层间介质层进行平坦化处理,以漏出所述第一层波导结构的上表面。
[0018]
进一步的,采用化学气相沉积(cvd)工艺沉积介质材料,以形成层间介质层。
[0019]
进一步的,所述平坦化处理采用化学机械抛光(cmp)工艺。
[0020]
进一步的,采用光刻工艺刻蚀所述层间介质层上的非第一层波导结构区域,以形成凹槽。
[0021]
进一步的,所述各向同性腐蚀采用湿法工艺;其中,腐蚀液为缓冲氧化物刻蚀液(boe)。
[0022]
进一步的,沉积第二层波导材料,所述第二层波导材料在所述凹槽处与所述第一层波导结构耦合包括:
[0023]
覆盖所述凹槽沉积第二层波导材料,形成第二波导层;
[0024]
采用光刻工艺刻蚀所述第二波导层,使得所述第二波导层在所述凹槽处与所述第一层波导结构形成耦合区。
[0025]
为了实现上述目的,根据本发明的第二方面,提供了一种双层硅基光子器件。
[0026]
根据上述的双层硅基光子器件的制作方法得到的双层硅基光子器件。
[0027]
在本发明实施例中,采用各向同性腐蚀方法将非第一层波导结构的层间介质区域形成斜坡,使第二层波导材料与第一层波导结构的耦合区在同一层次实现耦合,增加耦合效率,降低层间串扰。
附图说明
[0028]
通过阅读下文优选实施方式的详细描述,各种其他的优点和益处对于本领域普通技术人员将变得清楚明了。附图仅用于示出优选实施方式的目的,而并不认为是对本发明的限制。而且在整个附图中,用相同的参考符号表示相同的部件。在附图中:
[0029]
图1a~图1d为本发明实施例中双层硅基光子器件的制作方法的流程示意图。
[0030]
图中:
[0031]
1、soi衬底;2、第一层波导结构;3、凹槽;4、耦合区;
[0032]
100、支撑衬底;200、氧化物埋层;300、硅层;400、层间介质层;500、第二波导层。
具体实施方式
[0033]
下面将参照附图更详细地描述本公开的示例性实施方式。虽然附图中显示了本公开的示例性实施方式,然而应当理解,可以以各种形式实现本公开而不应被这里阐述的实施方式所限制。相反,提供这些实施方式是为了能够更透彻地理解本公开,并且能够将本公开的范围完整的传达给本领域的技术人员。
[0034]
本发明公开了一种双层硅基光子器件的制作方法,该双层硅基光子器件的制作方法包括以下步骤:
[0035]
提供绝缘体上硅(soi)衬底1,参考图1a所示,该soi衬底1包括支撑衬底100、位于支撑衬底100上的氧化物埋层200(box层)以及位于box层200上的硅层300。
[0036]
需要说明的是,支撑衬底100为si衬底,在本发明的实施例中,位于si衬底上的box层200的厚度为3μm,位于box层200上的硅层300的厚度为220nm。当然本领域技术人员可以根据实际需要设定box层200以及硅层300的厚度。
[0037]
继续参考图1a所示,采用光刻工艺刻蚀硅层300,以在硅层300上形成第一层波导结构2。需要说明的是,本领域技术人员可以根据实际需要设计第一层波导结构2的结构及图形。
[0038]
当然,本领域技术人员也可以采用常规的刻蚀工艺形成第一层波导结构2。
[0039]
参考图1b所示,覆盖第一层波导结构2以及box层200沉积介质材料,形成层间介质
层400。
[0040]
在本发明实施例中,采用化学气相沉积(cvd)工艺,如低压力化学气相沉积(lp cvd)、等离子体增强化学的气相沉积(pe cvd)沉积介质材料,以形成层间介质层400,介质材料可以为二氧化硅,并且层间介质层400的厚度大于第一层波导结构2的高度,以对第一层波导结构2形成有效覆盖。
[0041]
需要说明的是,本领域技术人员可以采用常规的cvd工艺以及合适的介质材料沉积形成层间介质层400。
[0042]
继续参考图1b所示,对层间介质层400进行平坦化处理,以漏出第一层波导结构2的上表面。
[0043]
在本发明实施例中,平坦化处理采用化学机械抛光(cmp)工艺。
[0044]
需要说明的是,本领域技术人员可以采用常规的cmp工艺对层间介质层400进行平坦化处理。
[0045]
参考图1c所示,采用光刻工艺刻蚀层间介质层400上的非第一层波导结构2区域,以形成凹槽3。
[0046]
在本发明实施例中,采用光刻工艺刻蚀层间介质层400上位于第一层波导结构2右侧的区域,以形成与第一层波导结构2邻近的凹槽3,并且凹槽3的底部侧面与形成有第一层波导结构2的硅层300的底面位于同一水平面上。
[0047]
需要说明的是,本领域技术人员可以采用常规的光刻工艺刻蚀层间介质层400以形成凹槽3。
[0048]
继续参考图1c所示,为了避免形成近似直角或直角,减轻漏光的发生,采用各向同性腐蚀工艺对凹槽3的侧壁进行腐蚀,以使凹槽3的侧壁所在的平面倾斜。
[0049]
在本发明实施例中,采用各向同性湿法腐蚀对凹槽3的相对两侧壁进行腐蚀,使得凹槽3相对两侧壁所在的平面均发生倾斜,采用的腐蚀液可以为缓冲氧化物刻蚀液(boe),并且凹槽3一侧壁邻近第一层波导结构2。
[0050]
需要说明的是,本领域技术人员可以根据实际需要选择合适的腐蚀液对凹槽3的侧壁进行各向同性湿法腐蚀。当然,本领域技术人员也可以采用常规各向同性干法腐蚀工艺腐蚀凹槽3的侧壁。
[0051]
参考图1d所示,覆盖凹槽3沉积第二层波导材料,形成第二波导层500。在本发明的实施例中,第二层波导材料可以为非晶硅或氮化硅。
[0052]
需要说明的是,本领域技术人员可以采用常规沉积工艺,并选择适宜的波导材料沉积形成第二波导层500,不作具体限定。
[0053]
继续参考图1d所示,采用光刻工艺刻蚀第二波导层500,使得第二波导层500在凹槽处与第一层波导结构2形成耦合区4,从而实现第一层波导结构2在同一层次与第二层波导材料耦合。
[0054]
在本发明的实施例中,采用光刻工艺刻蚀第二波导层500,使得位于凹槽3内的第二波导层500的高度小于等于第一层波导结构2的高度,并且由于第二波导层500与第一层波导结构2的底部位于同一水平面上,因而使得第一层波导结构2与第二层波导材料在同一层次耦合。
[0055]
需要说明的是,本领域技术人员可以根据实际需要设计第二波导层500的厚度,不
作具体限定。
[0056]
继续参考图1d所示,第二波导层500与层间介质层400之间在耦合区4内存在间隙。
[0057]
在本发明的实施例中,第二层波导材料与层间介质层400之间存在间隙,防止干扰,但是对间隙的宽度不作具体限定,可以根据实际需要设定。
[0058]
需要说明的是,本领域技术人员可以采用常规的光刻工艺刻蚀形成第二波导层500。
[0059]
以上所述,仅为本发明较佳的具体实施方式,但本发明的保护范围并不局限于此,任何熟悉本技术领域的技术人员在本发明揭露的技术范围内,可轻易想到的变化或替换,都应涵盖在本发明的保护范围之内。因此,本发明的保护范围应以所述权利要求的保护范围为准。