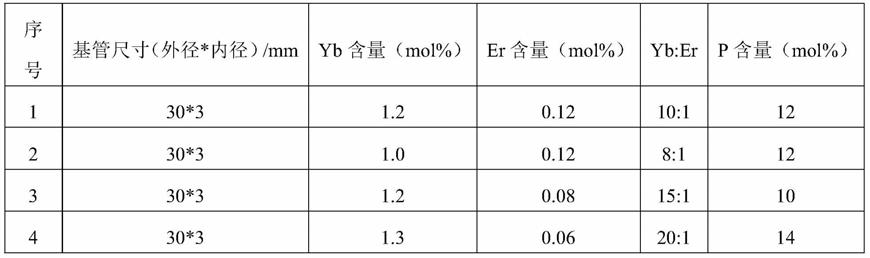
1.本发明涉及光纤及其制备方法,属于光学与激光光电子技术领域。
背景技术:2.近年来,高功率铒镱共掺光纤激光器因具有“人眼安全”和在光纤及大气中的低损耗特性,广泛用于光纤通信、激光雷达、卫星遥感和精密测量中。作为百瓦量级的1.5μm高功率光纤激光器的核心部件,铒镱共掺光纤的制备及优化升级越来越收到研究人的关注。
3.铒镱共掺光纤的难点在于如何实现高浓度的铒、镱离子的掺杂以及纤芯p2o5的高浓度掺入,同时又要保持光纤具有足够的光敏特性。目前,典型的铒镱共掺光纤普遍采用气相掺磷+液相掺稀土或者采用气相掺磷+螯合物掺稀土离子的方式进行,此种方式下掺磷,会造成纤芯中心凹陷明显,磷元素挥发严重,使光纤模式发生不可逆突变。同时,高浓度稀土元素掺杂,会普遍造成光纤析晶或浓度淬灭现象的发生,因此,亟需解决高浓度掺稀土下芯棒析晶的问题。
4.业内在制备铒镱共掺光纤时,普遍采用气相沉积+螯合物气相掺杂或气相沉积+液相掺杂的方式,且磷元素较难实现高浓度掺杂。中国专利文献202010477756.0公开了一种制备掺稀土光纤的气相
‑
液相复合掺杂方法,介绍了利用溶液掺杂的方法进行稀土离子的高浓度掺杂,但掺磷含量较低。中国专利文献200410029810.6公开了双包层掺稀土光纤及其制造方法,在实施例中提供一种铒镱共掺光纤的制备过程。
技术实现要素:5.针对目前铒镱共掺光纤在掺p工艺及铒镱共掺技术上的不足,本发明提供一种高功率用光敏型铒镱共掺光纤及其制备方法,光纤在芯层结构上设计为台阶式,两层芯层,第一芯层富含大量er、yb、p、f等元素,第二芯层富含大量ge、p元素,第一芯层和第二芯层分别的相对折射率采用台阶型设计,以此让光纤具有足够低的数值孔径,实现激光高光束质量输出。采用多步法掺p+气相掺稀土的掺杂工艺,可以实现p和稀土掺杂浓度的双提升,避免析晶及失透现象的出现,保证更高功率激光输出。
6.本发明所提供的的铒镱共掺光纤在1.5μm波段可以实现百瓦级平均光功率输出,同时由于较低的数值孔径,可实现优异的光束质量及光敏特性,工艺简单,可操作性强,有效降低生产制造成本,有利于1.5μm波段光纤激光器或光纤放大器在数据通信、激光雷达和激光医疗等领域的应用。
7.本发明解决上述问题所采用的技术方案为:一种高功率用光敏型铒镱共掺光纤,光纤截面结构由内到外依次包括同心设置的第一芯层、第二芯层、渐变层、第一包层、第二包层和外部涂层。
8.所述第一芯层为含有er、yb、p、f掺杂元素的石英,相对于纯石英的折射率差δ1为0.016~0.019;第一芯层直径d1:20~35μm,纤芯形状为圆形,其中er的摩尔百分比为0.1~0.2mol%,yb的摩尔百分比为1.3~2.0mol%,p的摩尔百分比为10~17mol%,f的摩尔百分
比为0.1~0.15mol%,纤芯中掺氟是为了改善疏松体流动性。
9.所述第二芯层为含有ge、p掺杂元素的石英,相对于纯石英的折射率差δ2为0.013~0.016;芯层形状为圆形,外径d2:45~60μm,其中ge的摩尔百分比为8~12mol%,p的摩尔百分比为0.5~1.0mol%。
10.所述第一芯层和第二芯层在折射率差上存在差值,该差值构成纤芯数值孔径na
芯
为0.06~0.09,na
芯
为第一芯层和第二芯层的折射率差的平方差的平方根。
11.所述渐变层为包含al、f掺杂元素的石英层,渐变层在光纤径向上折射率差由内向外逐渐降低,折射率差在0.008~0.013之间线性下滑,外径控制在55~90μm,渐变层中同时含有al和f,是为了均衡第二纤芯和第一外包层的折射率偏差值,实现折射率差的均衡过渡。
12.所述第一包层为纯石英层,含水量控制在1ppm以下,截面形状为圆形或多边形,例如正六边形或正八边形。
13.所述第二包层为低折射率涂料层,折射率绝对值在1.36~1.37,该低折涂层为含氟树脂,具有优异的耐水性和耐温性能。
14.所述外部涂层的涂布模量控制在1100mpa以上,可以采用高强度丙烯酸树脂涂层及其改性涂层。
15.本发明的另一目的是提供上述光纤的制备方法,主要包括如下步骤:
16.第一步:准备石英基管,将基管两端分别焊接头管和尾管,在距离基管一侧某一位置的头管处,通过火焰加热的方式挤出凹陷容器(不限于一个)用于盛放固相掺杂化合物,准备工作完成后,对基管进行刻蚀、抛光处理;
17.第二步:沉积渐变层,将al化合物固体导入凹陷容器中,在沉积sio2疏松体的过程中,在头管外侧加热凹陷容器,使al化合物的固相颗粒升华为气相,并通入o2作为载气,一边沉积疏松体一边掺杂al元素,al元素最终以al2o3的形式在疏松体中沉积;疏松体沉积的同时通入sf6气体实现f掺杂,sf6气体流量控制在5~10sccm,需要沉积5~6层疏松体,每层疏松体的沉积温度逐渐降低以对应获得孔隙率逐渐变小的疏松体,以此控制各层疏松体对掺杂元素al的吸收量,每层疏松体沉积时调节sf6气体流量以此控制各层疏松体对掺杂元素f的吸收量,以此实现通过控制沉积温度和sf6流量来控制渐变的折射率剖面,最后将沉积疏松体玻璃化即获得渐变层;
18.第三步:沉积第二芯层,向基管通入sicl4、o2,沉积温度控制在1500~1700℃,疏松体沉积完成后,通入o2、cl2对疏松体氧化、干燥,再进行玻璃化,玻璃化过程中掺入ge、p元素,玻璃化温度控制在1850~2000℃,重复以上步骤4~5遍,获得透明玻璃态的第二纤芯;
19.第四步:沉积第一芯层疏松体,在第三步的基础上向基管内通入sicl4、pocl3、o2、sf6气体,沉积一层含f、高含p的sio2疏松体,在一边沉积疏松体一边掺杂的过程中,采用反向掺杂的方式进行p2o5的高浓度掺杂(反向掺杂即火焰喷灯移动的方向与气体流动的方向相反),火焰喷灯移动的速度是100~140mm/min,温度控制在1450~1650℃,沉积完疏松体后,将yb、er的固态化合物颗粒装入到头管中的凹陷容器里,从头管外部加热凹陷容器使固体颗粒升华,在基管内通入o2作为载流气体,将蒸发的稀土化合物载入到疏松体内,载流过程中氢氧焰喷灯在基管下方沿来回移动加热基管,pocl3和稀土最终以氧化物的形式掺杂在疏松体内;
20.第五步:第一芯层玻璃化并塌缩,对第四步的疏松体进行玻璃化,玻璃化完成后基管呈现透明状态,玻璃化过程中向基管内通入pocl3和o2,pocl3最终以p2o5的形式掺杂于透明玻璃中;玻璃化后对基管进行塌缩,过程全部采用反向塌缩工艺,反向塌缩次数控制在4~5次,塌缩过程中同时通入pocl3;
21.第六步:对塌缩后的芯棒进行套管,芯棒直接穿过套管并进行塌缩,套管完成后,再对套管热抛处理;
22.第七步:根据需要对套管进行机械加工,形成第一包层,对光棒进行碱洗、水洗,处理后的光棒接好把手,准备拉丝;
23.第八步:将光棒放入拉丝炉内进行熔融拉丝,拉丝后对光纤进行内涂固化形成第二包层后,再对光纤进行外涂固化形成外部涂层。
24.步骤二中,将alcl3填放在凹陷容器中,对凹陷容器的加热温度控制在200~250℃,使alcl3挥发。
25.步骤二中,各层疏松体的沉积温度逐渐降低,每层沉积温度比上一层降低10~16℃,设计第一层疏松体的沉积温度为1615℃。
26.步骤三中,ge、p分别以gecl4、pocl3在疏松体玻璃化的时候掺入,gecl4的流量控制在150~200sccm,pocl3的流量控制在15~20sccm。
27.步骤四中,yb、er分别以ybcl3、ercl3的固体装填到所述凹槽容器中,对凹槽容器的加热温度控制在500~1000℃,氢氧焰喷灯的移动速度控制在50~80mm/min,载流o2的流量控制在100~150sccm。
28.步骤五中,玻璃化温度控制在1900~2000℃,玻璃化速率控制在120~140mm/min,pocl3流量控制在20~30sccm,o2流量控制在50~100sccm。
29.步骤五的塌缩过程中,第一次塌缩时pocl3流量控制在100~150sccm,第二次塌缩时pocl3流量控制在40~50sccm,第三次塌缩时pocl3流量控制在40~50sccm。
30.步骤六中塌缩温度控制在2200~2300℃,喷灯移动速度控制在0.5~1mm/min。
31.步骤八中,拉丝炉内温度控制在1600~1700℃,拉丝速度控制在50~60pmp(即m/min),拉丝张力控制在1.0n以上。
32.与现有技术相比,本发明的优点在于:
33.1、采用疏松体反向掺p+玻璃化掺p+塌缩补p的方式进行高浓度掺p,保证光纤具备足够浓度的p含量,能够最大程度上减小折射率中心凹陷值,达到平坦增益的目的。
34.2、通过固相高温升华为气相掺稀er、yb的方式,在疏松体中实现高浓度及均匀掺杂,使元素始终处于均匀分布的状态。同时,多步法掺磷工艺,有利于高浓度掺磷的实现,并有效防止高浓度稀土元素掺杂情况下所出现的团簇或析晶现象,从而提升整棒掺杂均匀性。
35.3、通过对光纤剖面进行台阶式设计,有效提高光纤围绕纤芯四周的包层折射率,在降低纤芯数值孔径的同时改善光束质量,并采用磷硅酸盐体系(磷硅酸盐体系是指以sio2为基质,内部含有较多的p2o5;同时,在第二纤芯中掺杂着少量的p,其掺杂方式是采用在疏松体中反向掺杂少量的pocl3和o2,最终p以p2o5的方式存在),使光纤光子暗化性能得到有效提升,同时含ge的第二纤芯层,使光纤具备较好的光敏性。
36.4、本工艺采用固相稀土化合物高温蒸发的方式进行稀土元素掺杂,既避免了螯合
物系统的复杂性,同时避免了液相掺杂下原料利用率低的问题,能够实现高浓度、高均匀性、高效率的掺杂。
附图说明
37.图1为本发明实施例光敏型铒镱共掺光纤制备工艺流程图;
38.图2为本发明第一包层为八边形的铒镱共掺光纤截面示意图;
39.图3为本发明铒镱共掺光纤折射率剖面示意图;
40.图4位基管凹陷容器的结构示意图;
41.图中,101
‑
第一芯层,102
‑
第二芯层,103
‑
渐变层,104
‑
第一包层,105
‑
第二包层,106
‑
外部涂层,107
‑
凹陷容器,108
‑
凹陷容器,109
‑
基管。
具体实施方式
42.以下结合附图对本发明作进一步详细描述,所述实施例是示例性的,旨在用于解释本发明,而不能理解为对本发明的限制。
43.光纤折射率剖面:光纤的折射率与其半径之间的关系曲线。
44.折射率差:δ
i
=(n
i2
‑
n
02
)/n
i2
*100%,其中n
i
为第i层光纤材料的折射率,i为整数;n0为纯石英折射率。
45.实施例1
46.本实施例中光敏型铒镱共掺光纤的制备过程如图1所示,为了便于理解,本实施案例以第一包层的横截面为八边形的光敏型铒镱共掺光纤的制备过程为例进行说明。
47.第一步:准备石英基管,基管尺寸为heraeus(20~30mm)*2mm*600mm(外径20~30mm,内径2mm,长度600mm),将基管两端分别焊接头管和尾管,在距离基管一侧20cm的头管处,通过火焰加热的方式挤出2个凹陷容器(107、108)(容器长度在80~100mm左右,深度在20~30mm左右),该凹陷容器用于盛放掺杂化合物的固相粒子,(氯化铒、氯化镱、氯化铝等),准备工作完成后,对基管进行大火焰刻蚀、抛光处理。
48.第二步:沉积渐变层,将5g重量的alcl3固体导入其中一个凹陷容器中,在沉积疏松体的过程中,在头管外对凹陷容器加热,让alcl3固体颗粒升华为气体,加热温度控制在200~250℃,在基管内通入o2作为气相alcl3的载气,一边沉积疏松体一边渗入al元素,o2流量控制在100~120sccm,同时通入适量的sf6气体,sf6气体流量控制在5~10sccm,每层疏松体沉积时调节sf6气体流量以此控制各层疏松体对掺杂元素f的吸收量,一共沉积5~6遍疏松体,第一层疏松体的沉积温度为1615℃,每层疏松体的沉积温度比上一层降低10℃,通过降低沉积温度缩小疏松体的孔隙率,这样疏松体所吸收的al的含量也会逐渐降低,以便形成折射率渐变层。
49.第三步:沉积ge层疏松体(第二芯层疏松体)并玻璃化,向基管通入sicl4、o2,sicl4沉积流量控制在150~160sccm,沉积温度控制在1500~1700℃,疏松体沉积完成后,通入o2、cl2进行3遍氧化和3遍干燥,以保证羟基含量足够低,再进行高温玻璃化,玻璃化过程中通入gecl4、pocl3气体,gecl4的流量控制在150~200sccm,pocl3的流量控制在15~20sccm,玻璃化温度控制在1850~2000℃,重复以上步骤4~5遍,获得预定设计的,玻璃化后的第二芯层为透明玻璃态。
50.第四步:沉积第一芯层疏松体,在第三步的基础上向基管内通入sicl4、pocl3、o2、sf6气体,沉积一层含f、高含p的sio2疏松体,sicl4沉积流量控制在300~305sccm,沉积温度控制在1500~1700℃,沉积完成一层含f的sio2疏松体后,在一边沉积疏松体一边掺杂的过程中,采用反向掺杂的方式进行p2o5的高浓度掺杂(反向掺杂即火焰喷灯移动的方向与气体流动的方向相反),火焰喷灯移动的速度是100~140mm/min,温度控制在1450~1650℃,沉积完疏松体后,将ybcl3(2.5g)、ercl3(1.0g)的固态颗粒装入到头管的凹陷容器里,在头管处放置加热器对凹陷容器的固体颗粒加热使升华,在基管内部通入o2作为载流气体,将掺杂物载入基管的疏松体内,载流过程中利用氢氧焰喷灯在基管下方来回移动,加热器温度控制在500~1000℃,氢氧焰喷灯的移动速度控制在50~80mm/min,载气o2的流量控制在100~150sccm。
51.第五步:第一芯层玻璃化并塌缩,对第四步的疏松体进行玻璃化,玻璃化温度控制在1900~2000℃,玻璃化速率控制在120~140mm/min,玻璃化完成后,基管呈现透明状态,玻璃化过程中,基管内通入少量pocl3和o2,pocl3流量控制在20~30sccm o2流量控制在50~100sccm,pocl3最终以p2o5的形势存在于透明玻璃中。玻璃化后对基管塌缩,塌缩过程全部采用反向塌缩工艺,以保证p含量的充足,反向塌缩次数控制在4~5次,塌缩过程中,第一遍塌缩时向基管中通入pocl3,流量控制在100~150sccm,第二遍塌缩pocl3的流量控制在40~50sccm,第三遍塌缩pocl3的流量控制在40~50sccm。
52.第六步:塌缩后的芯棒,直接进行套管,芯棒直接穿过套管,使用氢氧焰喷灯直接进行塌缩,塌缩温度控制在2200~2300℃,喷灯移动速度控制在0.5~1mm/min,套管完成后,再对套管棒进行大火焰热抛处理;
53.第七步:套管棒进行机械加工,将光棒加工为八边形,对光棒进行碱洗、水洗,碱洗时间控制在30min~60min,加工完成的异性光棒接好把手,准备拉丝;
54.第八步:将准备好的光棒放入拉丝炉内进行拉丝,高温炉内温度控制在1600~1700℃,拉丝速度控制在50~60pmp,拉丝张力控制在1.0n以上,涂覆装置先对光纤进行内涂固化形成第二包层,再对光纤进行外涂固化形成外包层。
55.由以上方法制备的光纤,其纤芯吸收能够达到90db/m,包层吸收能够达到2.9db/m,包层损耗能够达到3.8db/km。
56.光敏型铒镱共掺光纤的结构设计如表1所示,产品性能指标如表2所示。
57.表1
[0058][0059]
表2
[0060][0061]
除上述实施例外,本发明还包括有其他实施方式,凡采用等同变换或者等效替换方式形成的技术方案,均应落入本发明权利要求的保护范围之内。